La máquina de soldadura láser para baterías de iones de litio se ha convertido en una tecnología fundamental en la industria de fabricación de baterías. A medida que la demanda de baterías de iones de litio fiables y de alto rendimiento sigue aumentando en sectores como los vehículos eléctricos, la electrónica de consumo y el almacenamiento de energía, la precisión y la eficiencia que ofrecen estas máquinas no tienen parangón. Esta publicación de blog explorará los componentes esenciales y las ventajas de las máquinas de soldadura láser, su papel en diferentes formatos de batería y los factores críticos que garantizan su rendimiento y seguridad óptimos. Tanto si es un profesional del sector como si simplemente está interesado en la tecnología que hay detrás de las baterías modernas, este artículo le proporcionará una visión completa de cómo las máquinas de soldadura láser están dando forma al futuro del almacenamiento de energía.
¿Qué es una máquina de soldadura láser para baterías de iones de litio?
Una máquina de soldadura láser para baterías de iones de litio es una herramienta de precisión que utiliza rayos láser enfocados para unir los componentes de la batería con alta precisión. Garantiza soldaduras fuertes y libres de contaminación, críticas para el rendimiento y la seguridad de la batería. Estas máquinas son ampliamente utilizadas en el ensamblaje de celdas de baterías, pestañas y barras colectoras debido a su capacidad para trabajar con materiales sensibles al calor como el cobre, el aluminio y el níquel.
Las principales ventajas son:
- Zona mínima afectada por el calor (ZAT) – Evita daños a los materiales de la batería cercanos.
- Proceso sin contacto – Reduce la tensión mecánica en componentes delicados.
- Alta repetibilidad – Asegura soldaduras uniformes para la producción en masa.
Industrias como los vehículos eléctricos (VE), la electrónica de consumo y el almacenamiento de energía confían en esta tecnología para la fabricación de baterías eficiente y de alta calidad.
¿Cuáles son los componentes principales de una máquina de soldadura láser?
Una máquina de soldadura láser consta de varias partes críticas que garantizan un funcionamiento preciso y eficiente:
- Fuente láser – Genera el rayo láser (fibra, CO₂ o Nd:YAG).
- Sistema óptico – Incluye lentes y espejos para enfocar y dirigir el láser.
- Plataforma de movimiento – Controla el movimiento del cabezal láser o de la pieza de trabajo (por ejemplo, etapas CNC, brazos robóticos).
- Sistema de enfriamiento – Mantiene la temperatura óptima para la fuente láser.
- Control Software – Programa los parámetros de soldadura (potencia, velocidad, frecuencia de pulso).
- Sensores de monitoreo – Detecta la calidad de la soldadura en tiempo real (por ejemplo, cámaras CCD, pirómetros).
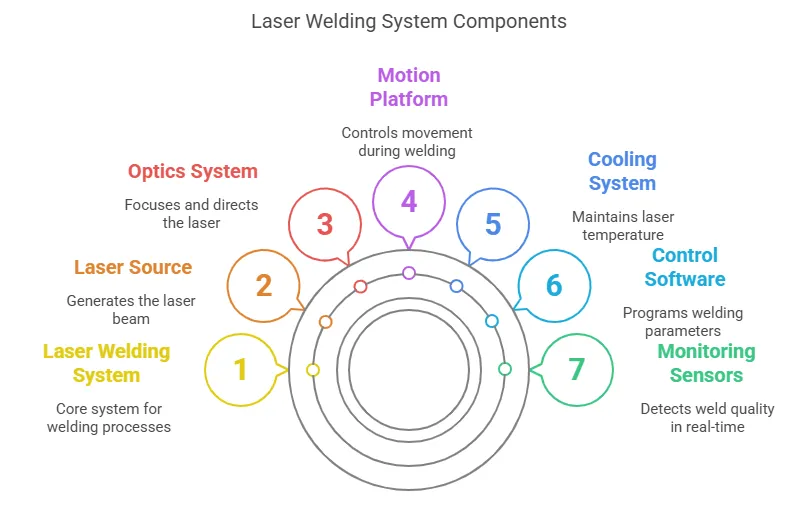
Cada componente desempeña un papel vital en el logro de una soldadura consistente y de alta velocidad para la producción de baterías de iones de litio.
¿Por qué los láseres de fibra son los más utilizados para la soldadura de baterías de iones de litio?
Los láseres de fibra dominan la soldadura de baterías de iones de litio debido a su rendimiento superior en comparación con los láseres de CO₂ o Nd:YAG. He aquí por qué:
- Mayor eficiencia – Convierte el 30-50% de la energía eléctrica en luz láser (láseres de CO₂: ~10%).
- Precisión – Proporciona un punto focal más pequeño (10-50 μm) para la soldadura fina de láminas delgadas de baterías.
- Flexibilidad – Compatible con metales reflectantes como el cobre y el aluminio.
- Bajo mantenimiento – El diseño de estado sólido sin partes móviles reduce el tiempo de inactividad.
Además, los láseres de fibra admiten:
✔ Modos de onda pulsada o continua (CW) para diversas aplicaciones.
✔ Soldadura de alta velocidad (hasta 100 mm / s) para producción en serie.
¿Cómo se utiliza la soldadura láser en el ensamblaje de celdas cilíndricas, de bolsas y prismáticas?
La soldadura láser se adapta a diferentes formatos de baterías de iones de litio con enfoques personalizados:
Celdas cilíndricas (p. ej., 18650, 21700)
-
Proceso paso a paso:
- Soldar las lengüetas del cátodo/ánodo a los terminales de la celda.
- Uniendo el colector de corriente a la tapa de la batería.
- Sellado de la carcasa con soldaduras herméticas.
Celdas de bolsa
- Las láminas ultrafinas requieren pulsos de baja potencia para evitar perforaciones.
- La soldadura con lengüetas (Al/Cu) debe evitar la fuga de electrolitos.
Células prismáticas
- Las barras colectoras soldadas con láser conectan varias celdas en módulos.
- Las robustas soldaduras de la carcasa garantizan la integridad estructural.
Cada formato exige parámetros láser específicos (longitud de onda, duración del pulso) para evitar el sobrecalentamiento o la deformación.
¿Cuáles son los requisitos de la sala limpia para la soldadura láser de baterías de litio?
Las baterías de iones de litio de soldadura láser a menudo ocurren en entornos controlados para evitar la contaminación. Los requisitos críticos incluyen:
- Salas limpias ISO Clase 5–8 – Filtra partículas >0,3–0,5 μm.
- Control de temperatura/humedad – Mantiene una variación de 20-25 °C y <1% de HR.
- Blindaje de gas inerte – El argón/nitrógeno evita la oxidación durante la soldadura.
Por qué es importante:
- El polvo o la humedad pueden causar soldaduras débiles o cortocircuitos.
- Las condiciones estables garantizan una calidad de soldadura repetible.
¿Cuáles son los métodos de inspección comunes para las baterías de iones de litio soldadas con láser?
La inspección de calidad garantiza soldaduras fiables en la producción de baterías de iones de litio. Se utilizan tres métodos clave:
-
Prueba de tracción
- Mide la resistencia de la soldadura aplicando fuerza de tracción hasta la falla
- Requisitos mínimos: 50 N para las lengüetas de cobre, 30 N para el aluminio
- Por qué es importante: Identifica las articulaciones débiles que podrían fallar durante el uso
-
Análisis de sección transversal
- Proceso paso a paso:
- Corte a través de la unión soldada
- Muestra de pulido
- Examinar bajo el microscopio
- Revela: Profundidad de penetración, formación de poros, zona afectada por el calor
- Proceso paso a paso:
-
Tomografía computarizada de rayos X
- Imágenes 3D no destructivas de la estructura interna de la soldadura
- Detecta: Huecos, grietas y desalineaciones invisibles para la inspección de superficies
- Resolución típica: 5-20 micras para aplicaciones de batería
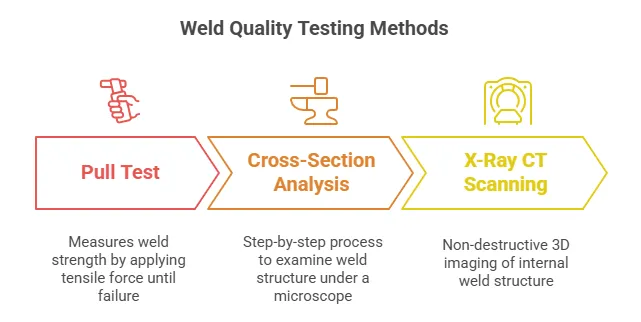
Cómo garantizar la seguridad del operador al usar máquinas de soldadura láser
La soldadura láser presenta varios peligros que requieren estrictas medidas de seguridad:
Equipo de seguridad esencial:
- Gafas láser con clasificación OD4+ para longitudes de onda específicas
- Ropa ignífuga para la protección contra chispas
- Extractores de humos para eliminar los vapores metálicos
Características de seguridad de la máquina:
✔ Enclavamientos que desactivan el láser cuando se abren las puertas
✔ Botones de parada de emergencia al alcance de la mano
✔ Cortinas de luz que detienen el funcionamiento cuando se rompen
✔ Sistemas de aviso sonoro/visual antes de disparar
Por qué son importantes:
- Los láseres de clase 4 pueden causar daño ocular permanente en milisegundos
- Los metales reflectantes aumentan el riesgo de peligros de haces parásitos
- Una formación adecuada reduce el 90% de los posibles accidentes
¿Qué debe incluirse en un programa de mantenimiento de rutina?
El mantenimiento regular evita costosos tiempos de inactividad y garantiza la calidad de la soldadura:
Tareas diarias:
- Óptica limpia con toallitas sin pelusa y disolvente aprobado
- Verifique la presión del suministro de gas (generalmente 10-20 psi)
- Verificar el funcionamiento del sistema de refrigeración
Tareas semanales:
- Realizar la calibración de la potencia del láser
- Inspeccione la lente de enfoque en busca de daños
- Pruebe los enclavamientos de seguridad
Tareas mensuales:
- Alineación de ruta óptica completa
- Lubricación del sistema de movimiento
- Configuración de parámetros de copia de seguridad
Signos críticos que requieren atención inmediata:
- Caída del 10% en la potencia de salida del láser
- Aumento de las salpicaduras durante la soldadura
- Perfil de viga irregular
Cómo integrar la soldadura láser con el apilamiento de celdas de batería y las líneas automatizadas
La producción moderna de baterías requiere una integración perfecta:
Puntos clave de integración:
-
Manejo de materiales
- Alimentadores automáticos para las pastillas de la batería
- Robots guiados por visión para una colocación precisa de las piezas
-
Sincronización de procesos
- Disparadores láser sincronizados con la máquina apiladora
- Retroalimentación de calidad en tiempo real para ajustar los parámetros
-
Seguimiento de datos
- Registros de soldadura para cada celda de la batería (tiempo, potencia, ubicación)
- Trazabilidad a través de sistemas de código QR/MES
Por qué es importante la integración:
- Reduce la manipulación manual en un 70%
- Aumenta la velocidad de producción a 1-2 celdas por segundo
- Ilumina el 100% de la inspección de soldaduras a través de cámaras en línea
Este artículo ofrece un examen detallado de la máquina de soldadura láser para baterías de iones de litio, una herramienta crucial en la fabricación contemporánea de baterías. Desglosamos los componentes clave de estas máquinas, como la fuente láser, el sistema óptico, la plataforma de movimiento, el sistema de refrigeración, el software de control y los sensores de monitoreo, y explicamos cómo funcionan juntos para lograr una soldadura precisa y eficiente. El artículo también destaca por qué los láseres de fibra son la opción preferida de la industria, gracias a su alta eficiencia, precisión, flexibilidad y bajo mantenimiento. Además, exploramos cómo se adapta la soldadura láser para el ensamblaje de celdas cilíndricas, de bolsa y prismáticas, analizamos los requisitos de las salas limpias y describimos los métodos de inspección comunes. También se cubren las medidas de seguridad y los consejos de mantenimiento de rutina, junto con la integración de la soldadura láser con líneas de producción automatizadas. En general, este artículo subraya el papel vital de la máquina de soldadura láser para baterías de iones de litio para garantizar la calidad, la seguridad y la escalabilidad de la producción moderna de baterías.