Battery coating is a critical process in enhancing the performance, safety, and longevity of batteries, particularly in industries such as electric vehicles (EVs), consumer electronics, and renewable energy storage. The process involves applying a thin layer of materials like conductive agents and binders to the electrodes of a battery. These coatings not only improve electrical conductivity but also ensure the structural stability of the battery over time. As technology advances, various coating methods, such as slot-die and spray coating, are being used to achieve uniformity and optimize battery efficiency. Testing and quality control processes are essential to ensure the consistency of the coatings, and innovative materials like graphene and nanocomposites are paving the way for next-generation batteries. Additionally, the sustainability of the battery coating process is being addressed by shifting towards eco-friendly solvents and recycling materials to reduce environmental impact. The development of advanced coating techniques is shaping the future of battery technology, making energy storage safer, more reliable, and more efficient.
What is Battery Coating?
Battery coating refers to the process of applying a thin layer of material onto the electrodes of a battery. This coating is crucial for enhancing the performance, safety, and longevity of the battery. The materials used for coating can vary, but they often include conductive agents, binders, and solvents that help improve the electrical conductivity and stability of the electrodes. The coating process is a critical step in the manufacturing of lithium-ion batteries, as it directly impacts the battery’s capacity, charge/discharge rates, and overall efficiency.
How Does the Battery Coating Process Flow Work?
The battery coating process involves several key steps to ensure that the electrode materials are uniformly coated and dried. Here’s a step-by-step breakdown of the process:
- Preparation of the Slurry: The first step involves mixing the active materials, conductive agents, binders, and solvents to form a homogeneous slurry. This slurry is then degassed to remove any air bubbles that could affect the coating quality.
- Coating Application: The slurry is then applied to the current collector (usually made of aluminum for the cathode and copper for the anode) using a coating machine. The coating can be done using various methods such as slot-die coating, roller coating, or spray coating.
- Drying: After the slurry is applied, the coated electrode is passed through a drying oven to evaporate the solvents. This step is crucial to ensure that the coating adheres properly to the current collector and to prevent any defects.
- Calendering: The dried electrode is then compressed using a calendering machine to achieve the desired thickness and density. This step improves the electrode’s conductivity and energy density.
- Slitting and Cutting: Finally, the coated and calendered electrode is slit into the required width and cut into the desired length for battery assembly.
What is the Working Principle of Battery Coating?
The working principle of battery coating revolves around the idea of creating a uniform and stable layer on the electrode surface. This layer serves multiple purposes:
- Enhanced Conductivity: The coating materials, often including conductive agents like carbon black, improve the electrical conductivity of the electrodes, allowing for more efficient charge and discharge cycles.
- Improved Stability: The binder materials in the coating help to hold the active materials together, preventing them from detaching during the battery’s operation. This enhances the battery’s cycle life and safety.
- Optimized Performance: By controlling the thickness and uniformity of the coating, manufacturers can optimize the battery’s performance parameters such as capacity, energy density, and charge/discharge rates.
What are the Applications of Battery Coatings in Different Industries?
Battery coatings are used in a wide range of industries, each with its own specific requirements and challenges. Here are some key applications:
- Electric Vehicles (EVs): In the EV industry, battery coatings are critical for improving the energy density and safety of lithium-ion batteries. The coatings help to enhance the battery’s performance under high-stress conditions, such as rapid charging and discharging.
- Consumer Electronics: In devices like smartphones, laptops, and tablets, battery coatings are used to extend battery life and improve safety. The coatings help to prevent issues like overheating and short-circuiting, which are common in high-performance electronic devices.
- Renewable Energy Storage: Battery coatings are also used in energy storage systems for renewable energy sources like solar and wind. These coatings help to improve the efficiency and lifespan of the batteries used in these systems, making them more cost-effective and reliable.
- Medical Devices: In the medical industry, battery coatings are used in devices like pacemakers and portable medical equipment. The coatings help to ensure that these devices operate safely and reliably, even under demanding conditions.
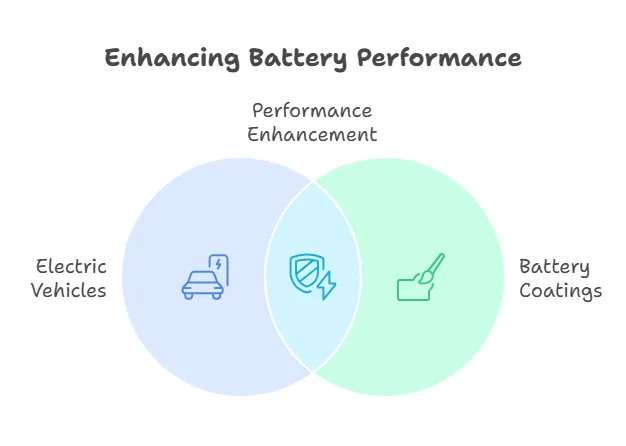
What are the Challenges in Battery Coating Technologies?
Despite the many advantages of battery coatings, there are several challenges that manufacturers face:
- Uniformity and Consistency: Achieving a uniform and consistent coating thickness is critical for battery performance. Any variations in the coating can lead to issues like uneven charge/discharge rates and reduced battery life.
- Material Compatibility: The materials used in the coating must be compatible with the electrode materials and the electrolyte. Incompatibility can lead to issues like poor adhesion, reduced conductivity, and even safety hazards.
- Cost and Scalability: The materials and processes used in battery coating can be expensive, especially when scaling up for mass production. Manufacturers need to find ways to reduce costs without compromising on quality.
- Environmental Concerns: The solvents and chemicals used in the coating process can be harmful to the environment. Manufacturers are increasingly looking for eco-friendly alternatives that can provide the same performance benefits without the environmental impact.
How to Overcome Challenges in Battery Coating Technologies?
To address the challenges in battery coating technologies, manufacturers are exploring several innovative solutions:
- Advanced Coating Techniques: Techniques like slot-die coating and precision spray coating are being developed to achieve more uniform and consistent coatings. These methods allow for better control over the coating thickness and distribution.
- New Materials: Researchers are constantly developing new materials that offer better compatibility with electrode materials and electrolytes. These materials can improve the performance and safety of the battery while reducing costs.
- Automation and AI: Automation and AI technologies are being used to optimize the coating process. These technologies can help to monitor and control the coating process in real-time, ensuring consistent quality and reducing waste.
- Sustainable Practices: Manufacturers are increasingly adopting sustainable practices, such as using water-based solvents and recycling waste materials. These practices not only reduce the environmental impact but also help to lower production costs.
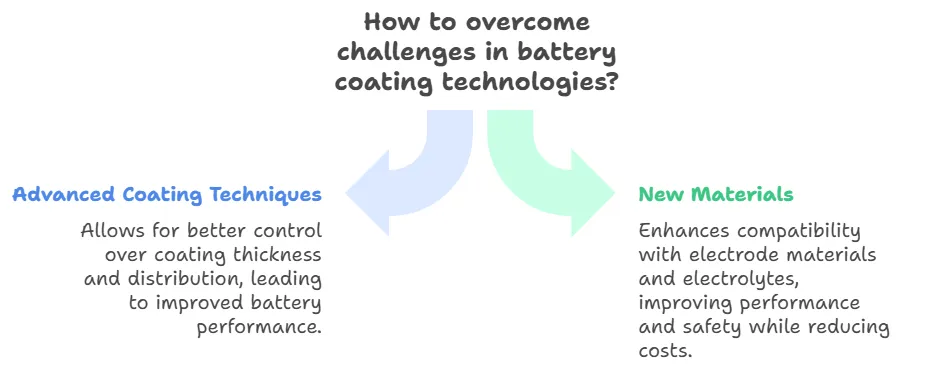
By addressing these challenges, manufacturers can continue to improve the performance and reliability of battery coatings, making them an essential component in the development of next-generation batteries.
What is Testing and Quality Control in Battery Coating?
Testing and quality control in battery coating are critical processes to ensure the performance, safety, and reliability of coated electrodes. These processes involve rigorous checks at various stages of the coating process to detect defects, measure uniformity, and verify adherence to specifications. Quality control ensures that the final product meets industry standards and performs optimally in real-world applications.
Key Steps in Testing and Quality Control:
- Visual Inspection: The coated electrodes are visually inspected for defects such as cracks, bubbles, or uneven coating. This is the first line of defense against quality issues.
- Thickness Measurement: Tools like micrometers or laser scanners are used to measure the thickness of the coating. Uniform thickness is essential for consistent battery performance.
- Adhesion Testing: The adhesion of the coating to the current collector is tested to ensure it can withstand mechanical stress during battery operation.
- Electrical Conductivity Testing: The coated electrodes are tested for electrical conductivity to ensure efficient charge and discharge cycles.
- Environmental Testing: The electrodes are subjected to conditions like high temperature, humidity, and mechanical stress to evaluate their durability and safety.
Why is Maintenance and Care of Battery Coating Equipment Important?
Proper maintenance and care of battery coating equipment are essential to ensure consistent coating quality, extend equipment lifespan, and reduce downtime. Neglecting maintenance can lead to defects in the coating, increased production costs, and safety hazards.
How to Maintain Battery Coating Equipment:
- Regular Cleaning: Residue from slurry and solvents can accumulate on coating machines, leading to defects. Regular cleaning prevents contamination and ensures smooth operation.
- Lubrication of Moving Parts: Lubricating rollers, conveyors, and other moving parts reduces wear and tear, preventing breakdowns.
- Calibration of Sensors and Controls: Sensors and control systems must be calibrated regularly to ensure accurate coating application and drying.
- Inspection of Wear Parts: Components like coating heads and drying ovens should be inspected for wear and replaced as needed.
- Training for Operators: Proper training ensures that operators can identify and address issues before they escalate.
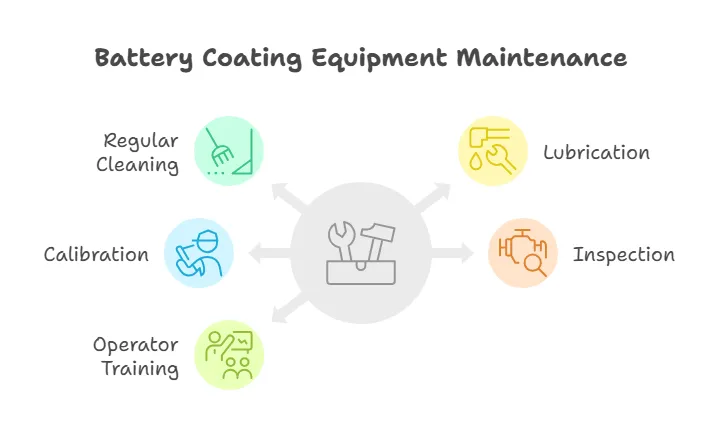
What are the Environmental Considerations in Battery Coating?
Environmental considerations in battery coating focus on reducing the ecological impact of the coating process. This includes minimizing waste, using eco-friendly materials, and adopting sustainable practices.
Key Environmental Challenges and Solutions:
- Solvent Emissions: Traditional solvents used in coating slurries can release volatile organic compounds (VOCs) into the atmosphere. Switching to water-based solvents or closed-loop systems can mitigate this issue.
- Waste Management: Slurry waste and defective coatings must be disposed of responsibly. Recycling and reusing materials can reduce waste.
- Energy Consumption: The drying process consumes significant energy. Using energy-efficient ovens or alternative drying methods can lower the carbon footprint.
- Material Sourcing: Sourcing raw materials from sustainable suppliers and using recyclable materials can further reduce environmental impact.
What are the Advances in Battery Coating Materials?
Advances in battery coating materials are driving improvements in battery performance, safety, and sustainability. Researchers are developing new materials that offer better conductivity, stability, and environmental compatibility.
Recent Innovations in Coating Materials:
- Graphene-Based Coatings: Graphene offers exceptional electrical conductivity and mechanical strength, making it an ideal material for enhancing electrode performance.
- Solid-State Electrolytes: Solid-state coatings can replace liquid electrolytes, improving safety and energy density.
- Nanocomposite Materials: Nanocomposites combine multiple materials at the nanoscale to create coatings with superior properties, such as higher conductivity and thermal stability.
- Biodegradable Binders: Researchers are developing binders made from biodegradable materials to reduce environmental impact.
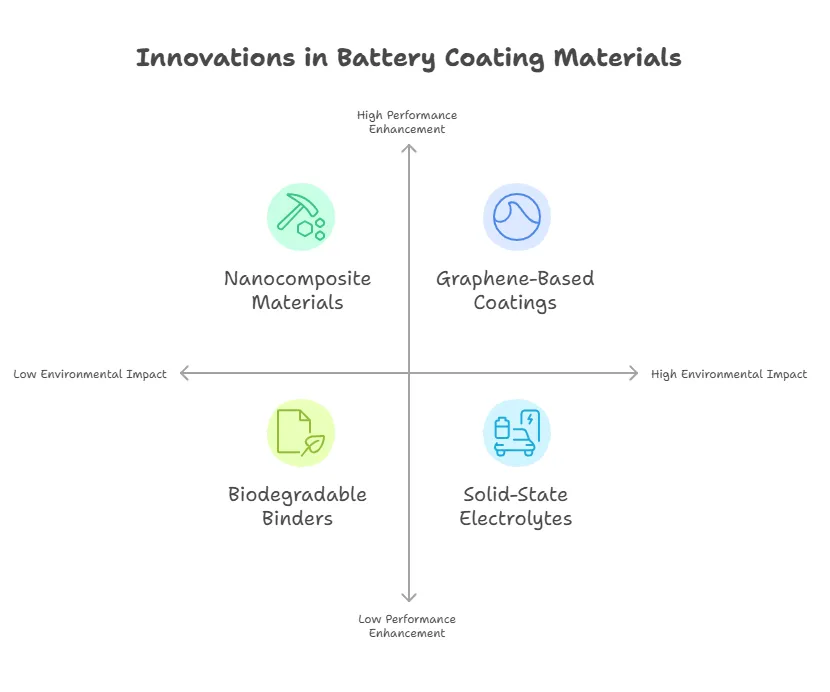
How are Innovative Coating Techniques Transforming Battery Manufacturing?
Innovative coating techniques are revolutionizing battery manufacturing by improving precision, efficiency, and scalability. These techniques enable manufacturers to produce high-quality coatings at a lower cost.
Step-by-Step Overview of Innovative Techniques:
-
Slot-Die Coating: This technique uses a precision slot-die head to apply a uniform layer of slurry onto the current collector. It offers excellent control over coating thickness and is highly scalable.
- Step 1: Prepare the slurry and load it into the slot-die coating machine.
- Step 2: Adjust the coating head to the desired gap width for precise thickness control.
- Step 3: Apply the slurry to the current collector in a continuous, uniform layer.
- Step 4: Dry the coated electrode in a controlled environment.
-
Electrospray Coating: This method uses an electric field to create fine droplets of slurry, which are then deposited onto the electrode. It allows for ultra-thin and uniform coatings.
- Step 1: Charge the slurry and pass it through a nozzle under high voltage.
- Step 2: Use the electric field to direct the droplets onto the current collector.
- Step 3: Dry the coating to form a thin, uniform layer.
-
Atomic Layer Deposition (ALD): ALD is used to apply ultra-thin coatings at the atomic level. It is ideal for creating precise, defect-free layers on electrodes.
- Step 1: Introduce precursor gases into the coating chamber.
- Step 2: Allow the gases to react and form a thin layer on the electrode surface.
- Step 3: Repeat the process to achieve the desired thickness.
By adopting these innovative techniques, manufacturers can produce batteries with higher performance, longer lifespans, and reduced environmental impact.
Battery coating is a vital step in the production of high-performance batteries used in various applications, including electric vehicles, consumer electronics, and energy storage systems. This process enhances battery efficiency by improving conductivity and ensuring structural integrity. As manufacturing techniques evolve, advanced methods like slot-die and atomic layer deposition are being explored for greater precision and scalability. The use of new materials, such as graphene and biodegradable binders, is also helping to improve battery performance while minimizing environmental impact. Quality control remains a cornerstone of the process, ensuring that coatings are consistent and reliable. Ultimately, as manufacturers continue to innovate, battery coatings will play an increasingly important role in the development of next-generation energy storage technologies.