Lithium-ion battery assembly is the backbone of modern technology, driving everything from our smartphones to electric vehicles. But what exactly does this assembly process entail, and why is it so crucial? In this blog, we’ll explore the fundamentals of lithium-ion battery assembly, from its step-by-step construction to its far-reaching impact on various industries. We’ll also uncover how proper assembly ensures safety, performance, and sustainability, making it a vital component in our increasingly electrified world. Join us as we dive deep into the science and significance of lithium-ion battery assembly.
1. What Is Lithium-Ion Battery Assembly and Why Is It Important?
Lithium-ion battery assembly refers to the process of constructing rechargeable batteries by combining key components like anodes, cathodes, separators, and electrolytes. These batteries power modern devices due to their high energy density, lightweight design, and long cycle life.
Why Is It Important?
- Versatility: Used in smartphones, EVs, and renewable energy storage.
- Efficiency: Offers better charge retention compared to lead-acid batteries.
- Sustainability: Enables clean energy solutions when paired with solar/wind power.
- Economic Impact: Drives industries like electric vehicles (EVs) and consumer electronics.
Proper assembly ensures performance, safety, and compliance with international standards (e.g., UN38.3).
2. Step-by-Step Process of Lithium-Ion Battery Assembly
How Are Lithium-Ion Batteries Assembled?
A structured workflow ensures quality and safety:
-
Electrode Preparation
- Coat anode (graphite) and cathode (lithium metal oxide) with slurry.
- Dry and compress sheets into thin foils.
-
Stacking or Winding
- Layer electrodes with separators (for prismatic/pouch cells).
- Wind them into a “jelly roll” (for cylindrical cells).
-
Cell Housing
- Insert the stack into aluminum (pouch) or steel (cylindrical) casings.
-
Electrolyte Filling
- Inject liquid electrolyte to facilitate ion movement.
-
Sealing & Formation
- Seal the cell and charge/discharge to stabilize performance.
-
Testing & Grading
- Check capacity, voltage, and internal resistance.
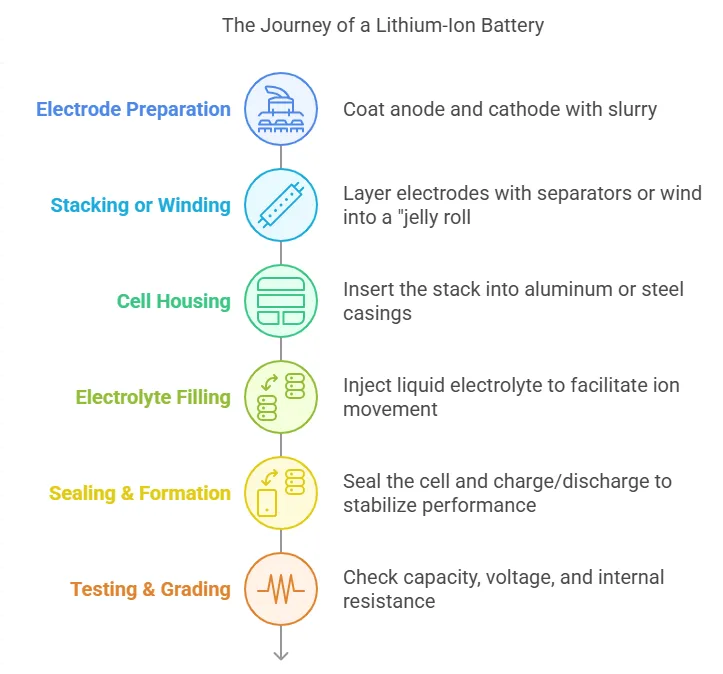
3. How Do Lithium-Ion Batteries Work Once Assembled?
The Science Behind Charging/Discharging
- Discharging: Lithium ions move from the anode to the cathode via the electrolyte, releasing electrons (energy) to power devices.
- Charging: An external current forces ions back to the anode, storing energy.
Key Components’ Roles
- Anode (Graphite): Hosts lithium ions during charging.
- Cathode (LiCoO₂/NMC): Accepts ions during discharge.
- Separator: Prevents short circuits.
- Electrolyte: Medium for ion transport.
This reversible reaction enables 300–1,000+ cycles per battery.
4. High-Demand Applications: E-Bikes, Drones, Power Banks
Where Are Assembled Li-Ion Batteries Used?
- E-Bikes: Lightweight cells provide 40–100 km per charge.
- Drones: High energy density extends flight time.
- Power Banks: Compact size with fast recharge capability.
- EVs: Tesla and BYD use NMC/NCA batteries for longer range.
- Medical Devices: Reliable power for portable equipment.
Demand grows 15% annually due to eco-friendly tech adoption.
5. Safety Protocols in Battery Assembly Workshops
How to Mitigate Risks During Production?
-
Thermal Runaway Prevention
- Use flame-retardant separators.
- Install temperature sensors in cells.
-
Workshop Measures
- Humidity control (<1% moisture).
- Anti-static flooring and equipment.
- PPE (fireproof gloves, goggles).
-
Compliance
- Follow IEC 62133 and UL 2054 standards.
- Conduct mandatory stress tests (crush, overcharge).
6. What Are the Essential Quality Control Procedures in Battery Assembly?
Quality control (QC) is critical in lithium-ion battery assembly to ensure safety, performance, and compliance with industry standards.
Key QC Procedures:
-
Raw Material Inspection
- Verify purity of lithium, cobalt, nickel, and graphite.
- Check separator thickness (typically 20–25 µm) for consistency.
-
In-Process Testing
- Electrode Coating Uniformity: Measure via X-ray diffraction.
- Moisture Levels: Keep <50 ppm to prevent electrolyte degradation.
-
Post-Assembly Checks
- Capacity Testing: Discharge cells at 0.5C rate to confirm rated mAh.
- Leak Detection: Submerge pouches in helium for seal integrity.
-
Safety Validation
- Nail Penetration Test: Ensures no thermal runaway below 130°C.
- Overcharge Protection: Verify BMS triggers at 4.25V±0.05V.
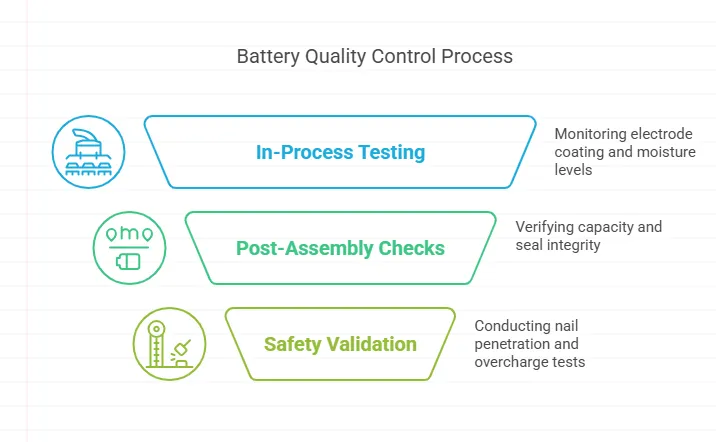
Non-compliant batches are scrapped to avoid recalls.
7. Why Does Improper Battery Assembly Cause Common Issues?
Faulty assembly leads to performance failures and hazards:
Common Problems & Root Causes
-
Swelling/Explosion
- Cause: Moisture contamination → gas formation.
- Fix: Dry room assembly (dew point <-40°C).
-
Capacity Fade
- Cause: Misaligned electrodes → lithium plating.
- Fix: Laser-guided winding tension control.
-
Short Circuits
- Cause: Burr on anode/cathode tabs piercing separator.
- Fix: Automated optical inspection (AOI) pre-assembly.
-
High Internal Resistance
- Cause: Poor electrolyte wetting.
- Fix: Vacuum filling with 30-minute soak time.
Defects increase warranty claims by 300% in uncertified factories.
8. How to Maintain Battery Pack Performance After Assembly?
Best Practices for Longevity
-
Storage Conditions
- Store at 50% SoC (3.7V–3.8V) in 15–25°C environments.
- Avoid >60% humidity to prevent corrosion.
-
Cycling Habits
- Limit discharges below 20% to reduce stress.
- Use partial cycles (e.g., 40%–80%) for grid storage packs.
-
Thermal Management
- Active cooling (liquid/air) for >2C continuous discharge.
- Maintain cell温差 <5°C in multi-module packs.
-
Firmware Updates
- Calibrate BMS annually to correct SoC drift.
Packs maintained properly retain >80% capacity after 1,000 cycles.
9. What Is the Environmental Impact of Lithium-Ion Battery Pack Assembly?
Production Footprint & Mitigation
-
Resource Extraction
- Issue: 500,000L water used per ton of lithium (Salar de Atacama).
- Solution: Direct lithium extraction (DLE) cuts water by 70%.
-
Energy Use
- Data: 60–100 kWh/kg CO₂ emitted during cell production.
- Fix: Renewable-powered gigafactories (e.g., Tesla Berlin).
-
Waste Streams
- Hazard: NMP solvent (cathode coating) requires incineration.
- Alternative: Water-based binders like PVDF.
-
Recycling
- Current recovery: <5% of global Li-ion waste.
- Emerging tech: Hydrometallurgy recovers 95% Co/Ni.
This article provides an in-depth look at the critical process of lithium-ion battery assembly. It begins by defining the assembly process and its importance in powering modern devices and driving industries like electric vehicles and consumer electronics. The article then details the step-by-step assembly process, from electrode preparation to testing and grading, emphasizing the importance of precision and quality control. It also explains how lithium-ion batteries work once assembled, highlighting the roles of key components like anodes, cathodes, separators, and electrolytes. Additionally, the article explores high-demand applications such as e-bikes, drones, power banks, and electric vehicles, and discusses safety protocols and quality control measures necessary to mitigate risks. Finally, it addresses the environmental impact of battery assembly and the importance of sustainable practices.