The spot welding machine for lithium battery assembly is a game-changer in the energy storage industry. This specialized tool provides a precise, efficient, and reliable method to join battery cells and nickel strips without causing thermal damage to sensitive components. In this article, we will explore the essential features, working principles, and best practices for using a spot welding machine in lithium battery manufacturing. Whether you are a professional engineer or a DIY enthusiast, understanding how to leverage this technology can significantly enhance the safety, performance, and longevity of your battery packs.
What Is a Spot Welding Machine for Lithium Batteries?
A spot welding machine for lithium batteries is a specialized device that joins battery cells/nickel strips using controlled heat and pressure without filler materials. Unlike traditional welding, it minimizes thermal damage to sensitive lithium-ion components.
Key Features:
- Precision Current Control: Adjustable amperage (typically 100-2,000A) for不同 cell thicknesses (0.1mm to 0.5mm nickel strips).
- Pulse Duration: Short pulses (1-10ms) prevent electrolyte overheating.
- Electrode Materials: Copper-tungsten alloys ensure conductivity and durability.
Why Lithium Batteries Require It:
Lithium cells degrade if exposed to prolonged heat. Spot welding’s localized energy input preserves cell integrity, avoiding leaks or thermal runaway.
How Does a Spot Welding Machine Work in Lithium Battery Pack Assembly?
Step-by-Step Process:
-
Cell Preparation:
- Clean cell terminals (e.g., 18650 anode/cathode) with alcohol wipes.
- Align nickel strips for series/parallel connections.
-
Machine Setup:
- Set parameters: 300A for 0.15mm nickel, 3ms pulse (prismatic cells).
- Test weld on scrap material to verify bond strength.
-
Welding Execution:
- Position electrodes perpendicular to the strip.
- Apply firm pressure (5-10kg/cm²) before triggering.
-
Quality Check:
- Peel test: Weld should withstand 90° bending without detachment.
- Measure resistance (<2mΩ per joint).
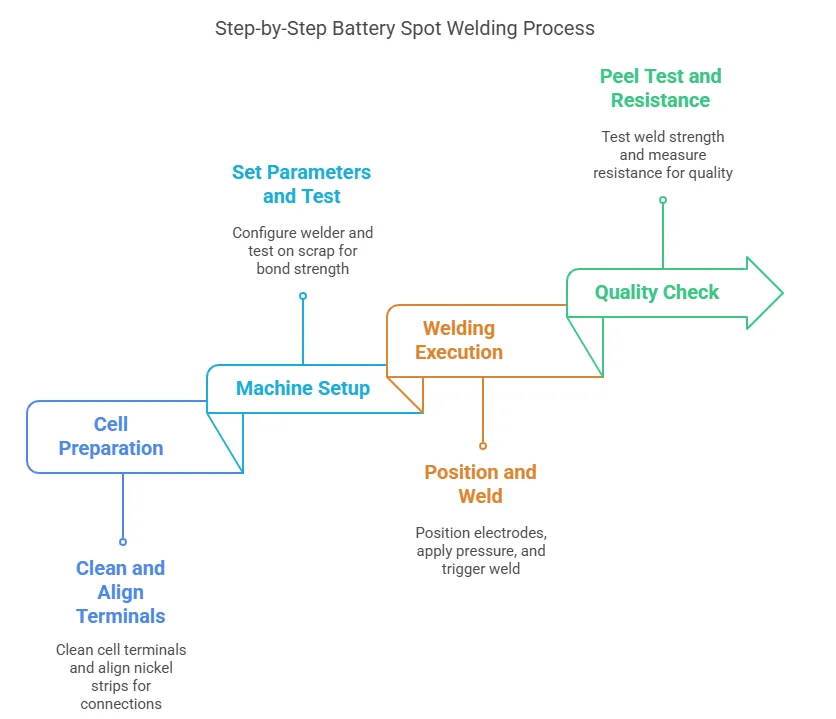
Critical Parameters Table:
Cell Type | Current (A) | Pulse Width (ms) |
---|---|---|
Cylindrical | 200-500 | 2-5 |
Pouch | 100-300 | 1-3 |
Why Understanding the Working Principle Matters for Lithium Battery Spot Welding
The machine transforms AC power into low-voltage, high-current DC pulses via a transformer. When electrodes contact the nickel strip:
- Resistance Heating: Contact resistance at the strip-cell interface generates heat (Q=I²Rt).
- Nugget Formation: Metal melts locally, fusing strip to cell terminal.
- Rapid Cooling: Electrodes absorb residual heat, solidifying the joint in milliseconds.
Safety Mechanisms:
- Overcurrent Protection: Prevents cell damage from excessive I²R losses.
- Auto Shutoff: Stops welding if electrode misalignment is detected.
How to Choose Between Cylindrical, Prismatic, and Pouch Cell Spot Welding
Equipment Differences:
Cylindrical Cells (e.g., 18650):
- Challenges: Curved surface requires pointed electrodes.
- Settings: Higher current (400A+) due to thicker terminals.
Prismatic Cells:
- Flat Surface: Use rectangular electrodes for even pressure.
- Thermal Management: Longer cooling intervals between welds.
Pouch Cells:
- Precision Needed: <100A current to avoid piercing foil.
- Electrode Shape: Flat, wide tips distribute force.
Comparison Table:
Feature | Cylindrical | Pouch |
---|---|---|
Electrode Type | Pointed | Flat |
Risk Factor | Overheating | Foil Tear |
What Environmental Conditions Ensure Optimal Spot Welder Performance?
Ideal Operating Conditions:
- Temperature: 15-25°C (extreme heat/cold affects transformer efficiency).
- Humidity: <60% RH to prevent arcing between electrodes.
- Ventilation: Fume extraction for ozone generated during welding.
Step-by-Step Workspace Setup:
- Grounding: Install copper grounding rods (<4Ω resistance).
- Power Stability: Use voltage regulators (±5% tolerance).
- Static Control: Anti-static mats/wrist straps when handling cells.
Hazard Prevention:
- Fire Safety: Keep Class D extinguishers nearby for lithium fires.
- Ventilation: 10-15 air changes/hour in confined spaces.
How to Test Spot Weld Strength in Lithium Battery Cells
Why Testing Matters:
Weak welds increase resistance, causing overheating in battery packs. Reliable testing ensures safety and longevity.
Step-by-Step Methods:
-
Peel Test (Destructive):
- Grip nickel strip with pliers and bend at 90°.
- Weld leaves material on both cell terminal and strip (no clean separation).
-
Resistance Measurement (Non-Destructive):
- Use a micro-ohmmeter across the weld joint.
- Acceptable range: <2mΩ for 0.2mm nickel strips.
-
Shear Force Test:
- Apply force parallel to the weld until failure.
- Minimum requirement: 50N for EV battery applications.
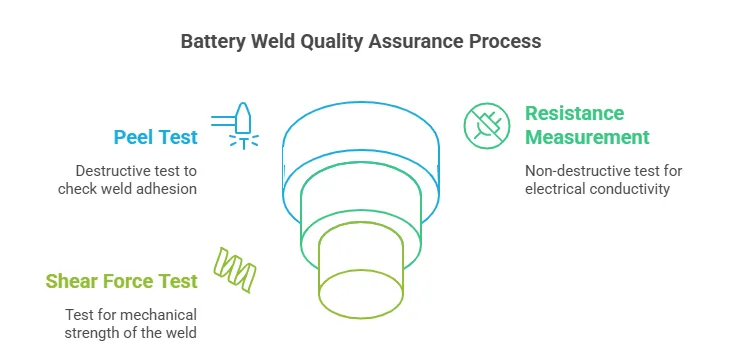
Common Failure Signs:
- Discoloration (indicates excessive heat)
- Partial adhesion (peels like a sticker)
Key Precautions When Using a Lithium Battery Spot Welding Machine
What to Avoid for Safety & Quality:
Electrical Safety:
- Always disconnect power before replacing electrodes.
- Use insulated gloves when adjusting transformer settings.
Material Handling:
- Never weld cells below 2.7V or above 4.25V (risk of thermal runaway).
- Store nickel strips in sealed containers to prevent oxidation.
Machine Operation:
- Electrode Alignment: Misaligned electrodes cause uneven pressure → weak welds.
- Cooling Intervals: Wait 10 seconds between welds at >500A to prevent overheating.
Critical Checks Before Welding:
✔ Verify electrode cleanliness (clean with brass brush every 50 welds).
✔ Confirm pressure gauge reads 5-8kg/cm² for 18650 cells.
How to Replace Electrodes and Maintain Consistent Weld Pressure
Step-by-Step Electrode Replacement:
- Power Off: Unplug the machine.
-
Remove Old Electrodes:
- Loosen set screws using a hex key.
- Inspect for wear (replace if diameter shrinks >10%).
-
Install New Electrodes:
- Use copper-chromium alloy tips for high conductivity.
- Tighten screws to 0.5Nm torque (prevents arcing).
Pressure Calibration:
- Place a 0.1mm shim between electrodes.
- Adjust spring tension until the gauge shows 3kg/cm² (for pouch cells).
- Verify with a force meter monthly.
Maintenance Schedule:
Task | Frequency |
---|---|
Electrode Polishing | Every 200 welds |
Pressure Check | Weekly |
How to Choose the Right Spot Welding Machine for Your Battery Line
Decision Factors:
1. Battery Type:
- Thin-Film (Pouch): Low-current machines (50-150A) with microsecond control.
- High-Capacity (EV): 1,500A+ machines with water-cooled electrodes.
2. Production Volume:
- Prototyping: Manual pen welders (200−200−500).
- Mass Production: Automated systems with vision alignment ($15k+).
3. Key Features Checklist:
✔ Pulse customization (1-20ms range)
✔ Real-time resistance monitoring
✔ OSHA-compliant safety interlocks
Cost vs. Performance Trade-Offs:
- Cheap machines often lack thermal overload protection → risky for Li-ion.
- Over-spec’ing amperage wastes energy for small cells.
The Future of Spot Welding in Lithium Battery Manufacturing
Emerging Innovations:
1. Adaptive AI Welding:
- Cameras + machine learning adjust current/pressure in real-time based on strip thickness variations.
2. Solid-State Welding:
- Ultrasonic and laser alternatives eliminate thermal stress for solid-state batteries.
3. Sustainability Trends:
- Recyclable electrode materials (e.g., graphene-coated copper).
- Energy recovery systems that feed wasted heat back into the grid.
Industry Challenges Ahead:
- Welding thicker tabs for 4680 cells requires 3,000A+ machines.
- Reducing argon gas usage in dry room welding environments.
This article offers an in-depth look at the spot welding machine for lithium battery assembly, covering its key features such as precision current control, pulse duration, and electrode materials. It walks through the step-by-step process of using the machine, from cell preparation and parameter settings to welding execution and quality checks. The importance of understanding the working principles, including resistance heating and rapid cooling, is also emphasized. Additionally, the article provides practical advice on choosing the right machine for different battery types (cylindrical, prismatic, and pouch), maintaining optimal environmental conditions, and ensuring safety during operation. Future innovations and industry trends are also discussed, making this a comprehensive resource for anyone involved in lithium battery manufacturing or assembly.