In today’s rapidly evolving technological landscape, the battery pack manufacturer stands at the forefront of innovation, powering everything from consumer gadgets to cutting-edge electric vehicles. But what exactly does it take to design, assemble, and deliver these essential energy systems? Join us as we explore the intricate world of battery pack manufacturing, uncovering the processes, challenges, and advancements that drive this critical industry forward.
What is a Battery Pack Manufacturer?
A battery pack manufacturer specializes in designing, assembling, and distributing battery packs tailored for various applications, from consumer electronics to electric vehicles and industrial machinery. These manufacturers combine individual battery cells, typically lithium-ion, into cohesive systems that deliver reliable power, safety, and efficiency. Their expertise lies in integrating cells with battery management systems (BMS), thermal management solutions, and protective enclosures to meet specific performance requirements. By collaborating with industries like automotive, renewable energy, and aerospace, battery pack manufacturers play a critical role in advancing sustainable energy solutions.
How is a Battery Pack Manufactured? A Step-by-Step Guide
The battery pack manufacturing process is a complex, highly controlled procedure that ensures safety, performance, and durability. Below is a step-by-step breakdown of how battery packs are created:
-
Step 1: Cell Selection and Testing
Manufacturers source high-quality battery cells, such as lithium-ion or nickel-metal hydride, from trusted suppliers. Each cell undergoes rigorous testing for capacity, voltage, and internal resistance to ensure consistency and reliability. -
Step 2: Design and Engineering
Engineers design the battery pack layout, incorporating the battery management system (BMS), thermal management, and structural components. This stage involves simulations to optimize performance and safety under various conditions. -
Step 3: Assembly
Cells are arranged in series or parallel configurations, connected via welding or soldering. The BMS is integrated to monitor voltage, temperature, and state of charge. Protective casings are added to shield the pack from environmental factors. -
Step 4: Quality Control and Testing
The assembled pack undergoes stress tests, including charge-discharge cycles, thermal exposure, and vibration tests, to verify performance and safety standards. -
Step 5: Packaging and Distribution
Once approved, the battery pack is packaged with clear labeling and shipped to clients or integrated into final products.
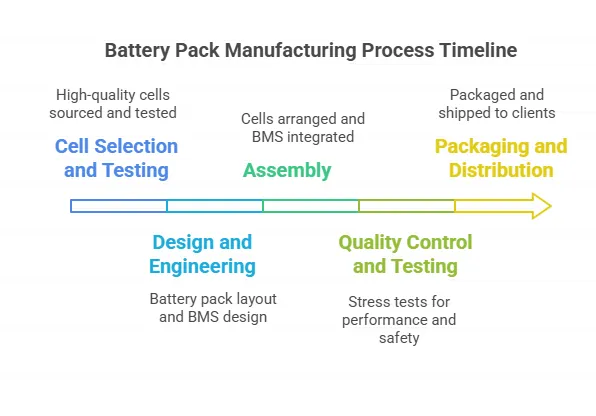
This meticulous process ensures that battery packs meet industry standards and customer expectations for performance and longevity.
How Does a Battery Pack Work? From Cells to Complete System
A battery pack is more than just a collection of cells; it’s a sophisticated system that delivers power efficiently and safely. Here’s how it functions:
- Battery Cells: The core of the pack, these store and release energy through electrochemical reactions. Lithium-ion cells are common due to their high energy density.
- Battery Management System (BMS): The BMS acts as the brain, monitoring cell health, balancing charge, and preventing overcharging or overheating.
- Thermal Management: Cooling systems, such as liquid or air cooling, regulate temperature to maintain performance and prevent thermal runaway.
- Enclosure: A durable casing protects the cells and electronics from physical damage, moisture, and other environmental factors.
When connected to a device, the pack delivers a steady flow of electricity, with the BMS ensuring optimal performance. This integrated approach makes battery packs versatile for applications ranging from smartphones to electric vehicles.
How to Choose the Right Battery Pack for Industrial Equipment
Selecting the ideal battery pack for industrial equipment requires careful consideration of performance, durability, and compatibility. Here are key factors to guide your decision:
- Energy Requirements: Assess the equipment’s voltage and capacity needs. For example, heavy machinery may require high-capacity packs to sustain long operating hours.
- Environmental Conditions: Consider the operating environment. Equipment in extreme temperatures or high humidity needs packs with robust thermal management and IP-rated enclosures.
- Cycle Life and Durability: Choose packs with a high cycle life to minimize replacement costs. Look for cells with proven longevity, such as lithium iron phosphate (LiFePO4).
- Safety Certifications: Ensure the pack meets industry standards, such as UL, CE, or IEC, to guarantee safe operation.
- Customization Options: Some manufacturers offer tailored solutions, adjusting pack size, shape, or BMS settings to match specific equipment.
By aligning these factors with your equipment’s needs, you can select a battery pack that enhances efficiency and reliability in industrial applications.
What Are the Key Considerations for Setting Up a Battery Pack Manufacturing Facility?
Establishing a battery pack manufacturing facility is a significant undertaking that demands strategic planning and investment. Below are critical considerations to ensure success:
-
Location and Infrastructure:
Choose a site with access to reliable power, transportation, and skilled labor. The facility must include clean rooms for cell assembly and advanced ventilation to handle chemical processes safely. -
Equipment and Technology:
Invest in automated assembly lines, precision welding machines, and testing equipment to ensure high-quality output. Software for BMS programming and quality control is also essential. -
Regulatory Compliance:
Adhere to local and international regulations, including safety standards (e.g., ISO 9001, UL) and environmental guidelines for handling hazardous materials like lithium. -
Supply Chain Management:
Build relationships with reputable cell suppliers and component manufacturers to ensure a steady supply of high-quality materials. Diversifying suppliers mitigates risks of shortages. -
Skilled Workforce:
Hire engineers, technicians, and quality control specialists with expertise in electrochemistry, electronics, and manufacturing processes. Ongoing training keeps staff updated on industry advancements.
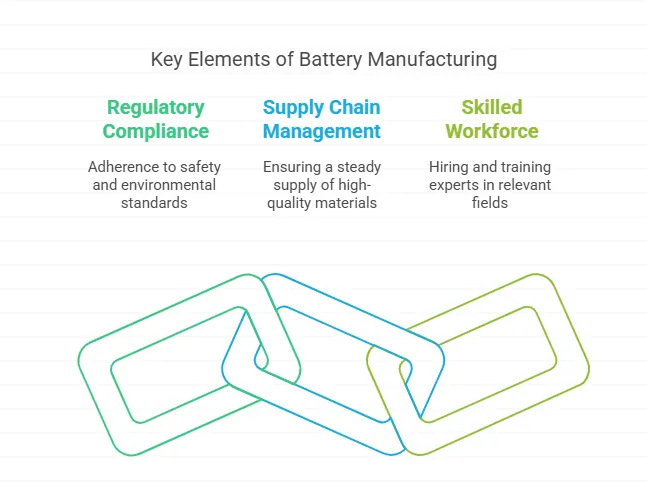
By addressing these considerations, a new facility can produce reliable, high-performance battery packs while maintaining cost-efficiency and compliance.
How Are Battery Packs Tested for Safety and Performance?
Battery pack manufacturers implement rigorous testing protocols to ensure their products are safe, reliable, and high-performing. These tests simulate real-world conditions and stress scenarios to verify that the pack meets industry standards. Here’s an overview of the testing process:
- Electrical Performance Testing: Measures capacity, voltage stability, and discharge rates to confirm the pack delivers consistent power.
- Thermal Testing: Exposes the pack to extreme temperatures to evaluate thermal management systems and prevent risks like overheating or thermal runaway.
- Mechanical Stress Testing: Subjects the pack to vibration, shock, and drop tests to ensure durability in rugged environments.
- Safety Testing: Includes short-circuit, overcharge, and puncture tests to verify the pack’s resilience against potential hazards.
- Environmental Testing: Assesses performance in humid, dusty, or corrosive conditions, ensuring reliability in diverse applications.
These tests, often guided by standards like UL 2054 or IEC 62133, ensure battery packs are safe and effective for consumer electronics, electric vehicles, or industrial use.
What Are the Safety Guidelines for Handling Lithium Battery Packs?
Lithium battery packs are powerful but require careful handling to prevent accidents. Following strict safety guidelines protects users and prolongs pack life. Below are key practices:
- Store Properly: Keep battery packs in a cool, dry place, ideally at 15-25°C, away from flammable materials.
- Avoid Physical Damage: Do not drop, crush, or puncture the pack, as this can cause internal short circuits or leaks.
- Use Compatible Chargers: Only use manufacturer-approved chargers to prevent overcharging or voltage mismatches.
- Inspect Regularly: Check for signs of swelling, leakage, or corrosion, and stop using the pack if damage is detected.
- Dispose Responsibly: Recycle used or damaged packs at certified facilities to avoid environmental hazards.
By adhering to these guidelines, users can minimize risks like fires or chemical leaks while ensuring safe operation in devices like laptops, e-bikes, or power tools.
When and How to Replace Your Battery Pack Safely
Battery packs degrade over time, losing capacity and efficiency. Knowing when and how to replace them ensures optimal device performance and safety. Here’s a step-by-step guide:
-
Step 1: Recognize Replacement Signs
Look for reduced runtime, slow charging, or overheating during use. If the pack swells or leaks, replace it immediately. -
Step 2: Verify Compatibility
Check the device manual or consult the manufacturer to confirm the replacement pack’s voltage, capacity, and connector type. -
Step 3: Power Down and Disconnect
Turn off the device, unplug it, and remove the old pack carefully, following the manufacturer’s instructions. -
Step 4: Install the New Pack
Insert the new battery pack, ensuring secure connections. Avoid forcing components to prevent damage. -
Step 5: Test and Recycle
Power on the device to verify functionality. Dispose of the old pack at a certified recycling center, never in regular trash.
Replacing a battery pack promptly and correctly extends device life and maintains safety, especially in high-demand applications like medical equipment or electric vehicles.
Why Choose Custom vs. Off-the-Shelf Battery Packs?
Choosing between custom and off-the-shelf battery packs depends on your application’s needs, budget, and timeline. Here’s a comparison to guide your decision:
-
Custom Battery Packs:
-
Pros:
- Tailored to specific voltage, capacity, or size requirements.
- Optimized for unique applications, like specialized medical devices or drones.
- Can include advanced features, such as proprietary BMS or enhanced thermal management.
-
Cons:
- Higher upfront costs due to design and engineering.
- Longer lead times for development and testing.
-
Pros:
-
Off-the-Shelf Battery Packs:
-
Pros:
- Cost-effective and readily available for immediate use.
- Standardized designs meet common industry needs, like consumer electronics.
- Pre-tested for reliability and compliance with safety standards.
-
Cons:
- Limited flexibility in size, shape, or performance.
- May not fully optimize device efficiency for niche applications.
-
Pros:
For standard devices, off-the-shelf packs offer convenience and affordability. However, custom packs are ideal for industries like aerospace or robotics, where precise specifications enhance performance and safety.
This in-depth guide provides a comprehensive look at the role of the battery pack manufacturer in shaping modern energy solutions. We begin by defining what a battery pack manufacturer does, highlighting their expertise in integrating individual cells with advanced battery management systems (BMS) and thermal management solutions to deliver reliable power. The manufacturing process is then broken down step-by-step, from cell selection and rigorous testing to final assembly, quality control, and distribution.
We also delve into the inner workings of a battery pack, explaining how the combination of battery cells, BMS, thermal management, and protective enclosures ensures efficient and safe performance. For those seeking industrial applications, we outline key considerations for choosing the right battery pack, including energy requirements, environmental resilience, and safety certifications. Additionally, we explore the critical factors for setting up a battery pack manufacturing facility, from location and infrastructure to regulatory compliance and workforce training.
Safety is a top priority, so we cover the rigorous testing protocols used by manufacturers to ensure their products meet industry standards. We also provide essential handling guidelines for lithium battery packs and offer advice on when and how to replace a battery pack safely. Finally, we compare custom and off-the-shelf battery packs, helping you decide which option best suits your needs. This guide is your ultimate resource for understanding the dynamic world of battery pack manufacturing.