Lithium Battery Top 10 Key Equipment – pulp-making machine
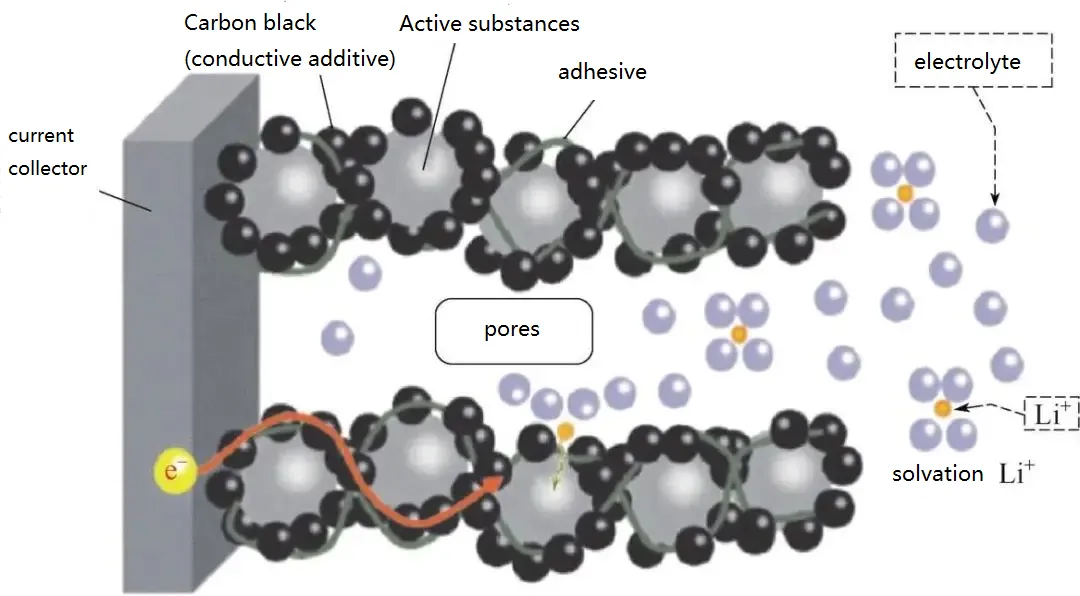

Follow me on:
from LIDIANBIJI
01 Introduction to pulping process
1.1 The Importance of the Pulp-making Process
The performance limit of lithium-ion batteries is determined by the chemical system used, including the active materials for the cathode and anode, as well as the electrolyte. However, the actual performance depends crucially on the microstructure of the electrode, which is primarily determined by the microstructure of the slurry and the coating process. In this context, the microstructure of the slurry plays a dominant role. Therefore, there is a widely recognized claim that the influence of the manufacturing process on the performance of lithium-ion batteries is at least 70% in the early-stage processes, and within these processes, the impact of the pulp-making process alone accounts for at least 70%. In other words, the pulp-making process contributes to approximately half of the overall influence.
1.2 Composition of Slurry and Ideal Dispersed State of Each Component
The electrode materials of lithium-ion batteries consist of three main components: active materials, conductive additives, and binders. Among them, the active material constitutes the vast majority of the total weight, generally ranging from 90% to 98%, while the proportions of conductive additives and binders are relatively small, usually between 1% and 5%. These main components differ significantly in their physical properties and sizes. The particles of the active material typically range from 1 to 20 μm, while the majority of conductive additives are nanocarbon materials. For example, commonly used carbon black has primary particle diameters in the range of tens of nanometers, and carbon nanotubes have diameters generally below 30 nm. The binder is a polymer material that can dissolve in solvents or form microemulsions in solvents.
The electrode of a lithium-ion battery needs to achieve good electron and ion transport, which requires the distribution state of the active material, conductive additives, and binders to meet certain requirements. The ideal distribution state of each material in the electrode is illustrated in the figure, where the active material is fully dispersed, the conductive additives are fully dispersed and in sufficient contact with the active material, forming a good electronic conductive network, and the binder is uniformly distributed in the electrode, bonding the active material and conductive additives together to form a cohesive electrode.
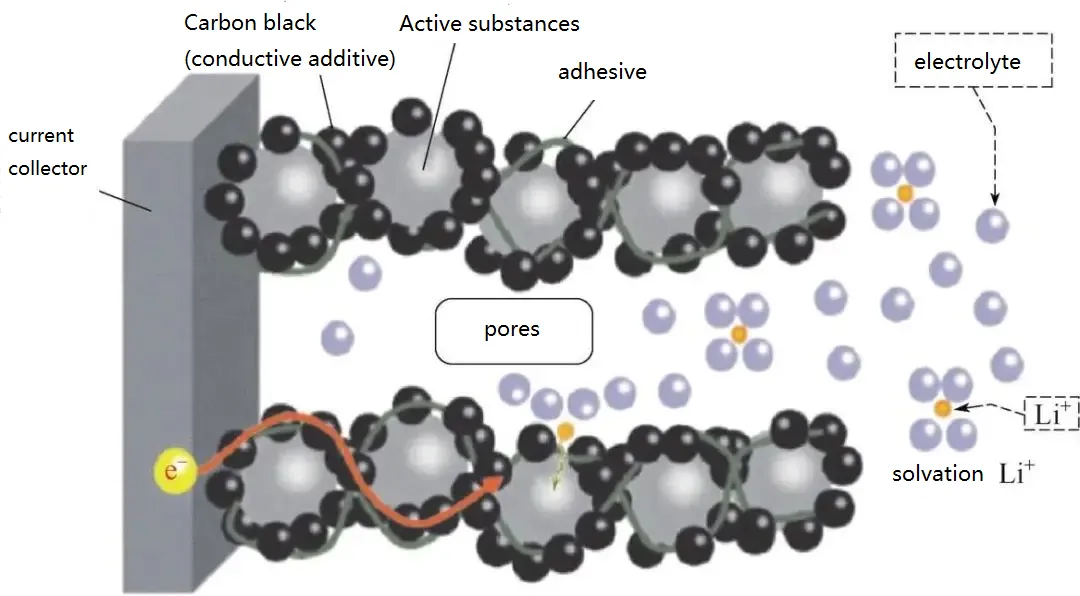
In order to achieve the desired microstructure of the electrode, it is necessary to obtain a slurry with the corresponding microstructure during the pulp-making process. This means that the active material, conductive additives, and binders in the slurry must be fully dispersed, and there should be good bonding between the conductive additives and the active material, as well as between the binder and the conductive additives/active material. Furthermore, the dispersion state of each component in the slurry must be stable. The slurry is essentially a suspension where solid particles are dispersed in a liquid. Various forces act between the particles in the suspension, and the attractive forces between particles formed by van der Waals interactions are the main cause of particle aggregation. To prevent this aggregation, it is necessary to have a certain level of repulsion between the particles. Common types of repulsion include electrostatic repulsion and steric hindrance caused by polymer chains. The DLVO theory (Deryaguin-Landau-Verwey-Overbeek theory) is a classic theory used to describe the stability of colloidal dispersions. It considers the combined effects of electrostatic repulsion and van der Waals attraction. As shown in the figure, the total energy formed by electrostatic repulsion and van der Waals forces reaches a maximum value (Gmax) at a certain distance. This maximum value forms an energy barrier, preventing particles from further approaching and forming gprimary.
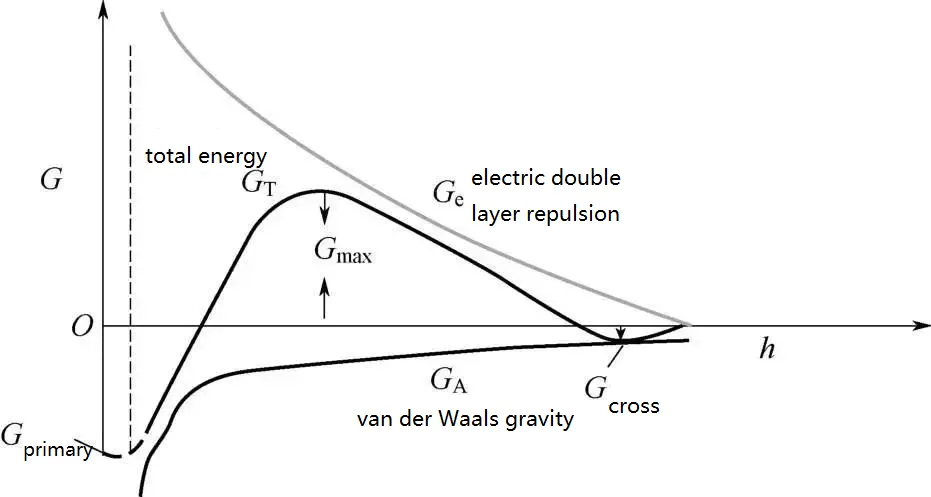
In the slurry of lithium-ion batteries, the steric hindrance formed by the adsorption of binder polymer chains on the particle surfaces plays a crucial role in the stability of the slurry. When binder molecules adsorb on the particle surfaces to form an adsorption layer, the adsorption layers on two particle surfaces come close to each other. Due to steric hindrance, an interaction energy is generated. The steric hindrance force, along with the electrostatic repulsion and van der Waals attraction, constitutes the total interaction energy between the particles, as shown in the figure.
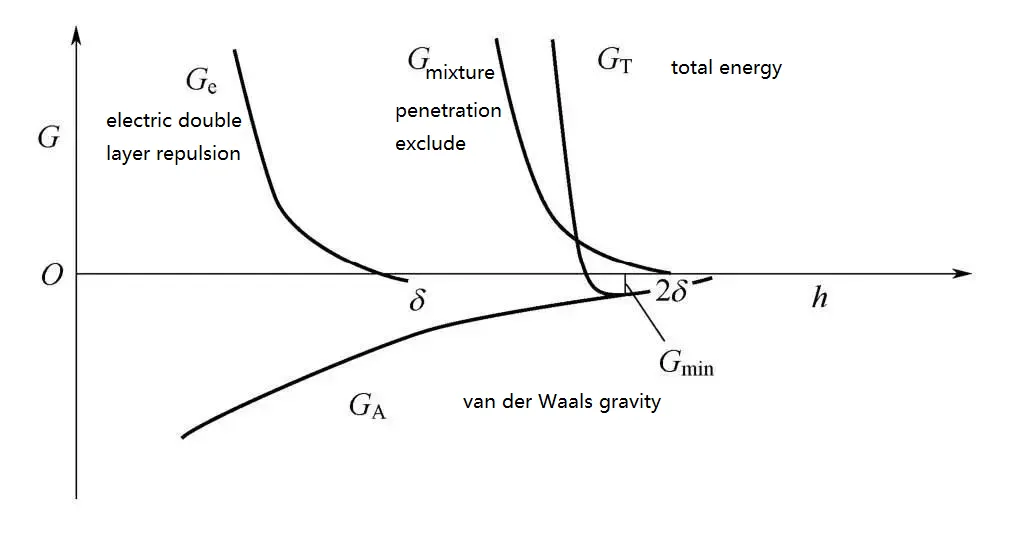
Therefore, to prevent particle aggregation in the slurry, it is necessary for the polymer chains of the binder to adsorb onto the particle surfaces, creating a certain level of steric hindrance. This allows the dispersion state of the slurry to remain stable for an extended period of time.
1.3 The Microscopic Process of Pulp-Making
The pulp-making process in lithium-ion battery manufacturing involves the uniform dispersion of active materials and conductive additives in a solvent, forming a stable slurry under the influence of binder polymer chains. From a microscopic perspective, this process typically includes three main stages: wetting, dispersion, and stabilization, as illustrated in the figure.
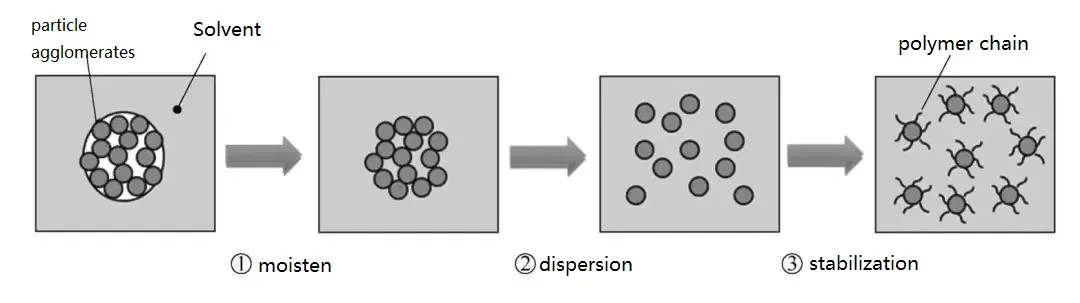
The wetting stage is the process of achieving sufficient contact between the solvent and the particle surfaces. It involves displacing air from the particle agglomerates and replacing it with the solvent. The speed and effectiveness of this stage depend on the affinity between the particle surfaces and the solvent, as well as the pulp-making equipment and process.
The dispersion stage is the process of breaking up particle agglomerates. The speed and effectiveness of this stage are influenced by material characteristics such as particle size, specific surface area, and interparticle forces. Additionally, the dispersion intensity and dispersion process are closely related to the efficiency of this stage.
The stabilization stage involves the adsorption of polymer chains onto the particle surfaces to prevent re-aggregation between particles. The speed and effectiveness of this stage depend on the material characteristics, formulation, as well as the pulp-making equipment and process.
It should be noted that not all materials undergo the three stages simultaneously throughout the entire pulp-making process. Different parts of the slurry may be at different stages. For example, some portions of the slurry may have entered the stabilization stage, while others are still in the wetting stage. This situation is quite common and contributes to the complexity and difficulty in controlling the pulp-making process.
1.4 Dispersion Equipment and Processes for Slurries
The equipment used for slurry dispersion can be broadly categorized into two types. The first type involves devices that utilize shear forces generated by fluid motion to disperse particle agglomerates. This includes various types of mixers and kneaders equipped with different types of stirring blades. It also includes three-axis milling machines and disc mills. The second type involves equipment that uses grinding beads to impact particle agglomerates and achieve dispersion, such as stirred mills. Additionally, there are some specialized dispersion devices, such as ultrasonic dispersers, which utilize cavitation and instantaneous micro-jets generated by ultrasound to disperse particle agglomerates. These different types of dispersion equipment are illustrated in the figure.
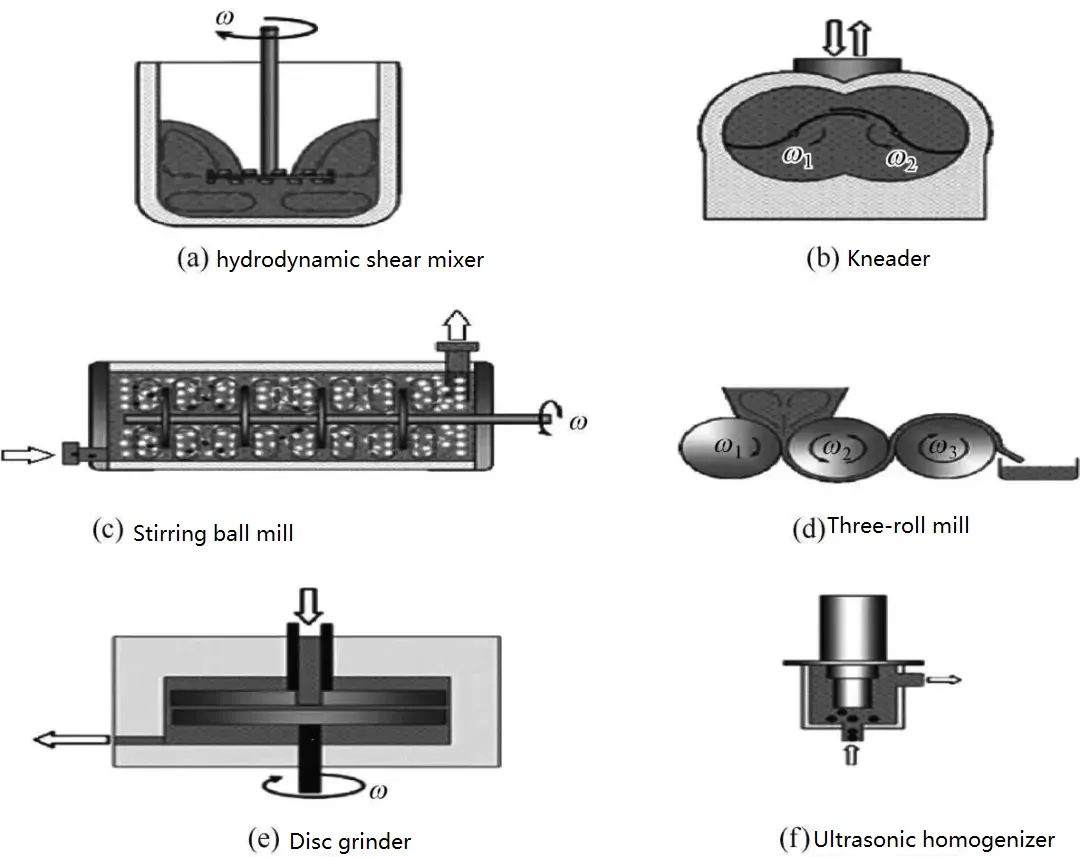
Not all of the aforementioned dispersion equipment is suitable for slurry production in lithium-ion batteries. For example, the use of grinding beads in stirred mills generates significant impact forces, which can damage the surface coating of some active materials and even result in their fragmentation. As a result, stirred mills are rarely used in slurry production for lithium-ion batteries. Ultrasonic dispersion devices are also not suitable for high-solid-content and high-viscosity slurries. However, slurry for lithium-ion batteries typically has high solid content (60% to 80% for positive electrode slurry, 40% to 60% for negative electrode slurry) and high viscosity (20 to 200 Pa·s), making them unsuitable for dispersion using ultrasonic dispersers.
In practice, the equipment used for slurry production in lithium-ion batteries relies on shear forces generated by fluid motion for dispersion. This includes mixers, kneaders, and the most typical equipment, the Twin planet mixer, which will be detailed in Section 2. The slurry production process also has a significant impact on the properties of lithium-ion battery slurries. For example, the slurry properties can vary greatly depending on the order of adding different materials. Literature reports have shown that using two different feeding sequences to prepare slurries for nickel-cobalt-manganese ternary positive electrode materials results in significant differences in slurry characteristics and electrode performance. The second feeding sequence produces a higher solid content slurry, with much higher peel strength and conductivity of the electrode. This is because pre-mixing the conductive additives with the main material allows the conductive additives to coat the surface of the main material, reducing the free conductive additives. This, in turn, reduces the viscosity of the slurry and minimizes the aggregation of the conductive additives during drying, facilitating the formation of a good conductive network.
Currently, there are two main types of slurry production processes commonly used in the lithium battery industry, known as wet process and dry process. The main difference between them lies in the initial solid content of the slurry. The wet process involves a lower initial solid content of the slurry, while the dry process involves a higher initial solid content of the slurry.
The process flow for wet slurry production involves first mixing and dispersing the conductive additives and binders. After achieving thorough dispersion, the active materials are added and further mixed and dispersed. Finally, an appropriate amount of solvent is added to adjust the viscosity for coating purposes. The binder can exist in either powdered or liquid form. Preparing the binder as a solution facilitates its effectiveness, although some companies directly use powdered binders as well. It should be noted that when the binder has a high molecular weight and large particle size, it may take a longer time for the binder to dissolve. In such cases, preparing the binder as a solution is necessary.
The process flow for dry slurry production involves first pre-mixing powdered materials such as active materials and conductive additives. Then, a portion of the binder solution or solvent is added, and the mixture is stirred or kneaded under high-solid-content and high-viscosity conditions. Subsequently, the remaining binder solution or solvent is gradually added for dilution and dispersion. Finally, an appropriate amount of solvent is added to adjust the viscosity for coating purposes.
The characteristic of the dry slurry production process is that in the initial stage, the mixing and dispersion (kneading) are performed under high-solid-content and high-viscosity conditions. At this stage, the material is in a thick and pasty slurry state, and the mechanical force applied by the stirring paddle is strong. Moreover, there is significant internal friction between the particles, which promotes wetting and dispersion, resulting in a high degree of dispersion. Therefore, the dry slurry production process can shorten the slurry production time, and the obtained slurry has lower viscosity, allowing for higher solid content compared to the wet slurry production process.
However, it is challenging to control the optimal state of the material in the dry slurry production process. When there are changes in the particle size, specific surface area, and other physical properties of the raw materials, it is necessary to adjust process parameters such as the intermediate solid content to achieve the optimal dispersion state. This may impact production efficiency and batch-to-batch consistency.
02 Current status of pulping equipment
2.1 Traditional pulping equipment – Twin planet mixer
Currently, both domestic and international lithium-ion battery production commonly employ traditional stirring processes for slurry production, often utilizing twin planet mixer. The working principle of a twin planet mixer involves the combined motion of 2 to 3 slow-speed stirring blades, which rotate and revolve simultaneously. This movement allows the blades to cover the entire space within the mixing drum, as shown in the diagram.
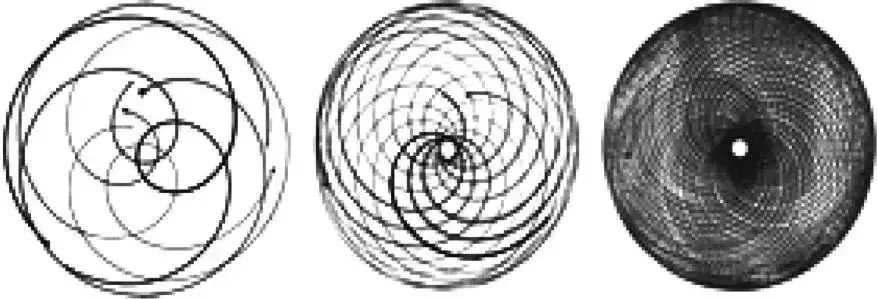
With technological advancements, there have been further improvements in slurry production equipment. In addition to the existing slow-speed stirring blades, high-speed dispersing blades have been added. These high-speed dispersing blades utilize the rapid rotation of the toothed disk to generate strong shear forces. This allows for further dispersion of the pre-mixed slurry, as shown in the diagram.
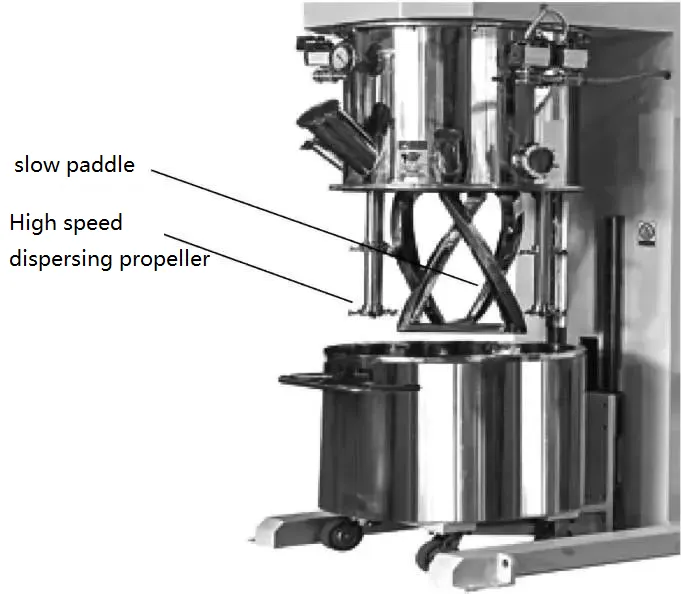
The twin planet mixer has the prominent advantage of easily adjusting process parameters such as feeding sequence, speed, and time to accommodate different material characteristics. It also allows for easy rework when the slurry properties do not meet the requirements, exhibiting strong adaptability and flexibility. Furthermore, during product changeovers, especially for small-scale mixers, cleaning is relatively simple.
In the twin planet mixer, the material’s interaction with the stirring blades follows a probability distribution, requiring a long mixing time to ensure thorough blending and dispersion of all materials. In the early stages, slurry preparation could take over 10 hours. With continuous process improvements, especially the introduction of dry slurry production techniques, the production time has been shortened to 3-4 hours. However, due to inherent limitations, it is challenging to further reduce the slurry production time with twin planet mixer. The efficiency of slurry production is relatively low, and the energy consumption per unit is higher.
As the volume of the mixing drum increases, it becomes more difficult to achieve uniform dispersion. Currently, the maximum volume of twin planet mixers used for lithium-ion battery slurry production does not exceed 2000 liters, with a maximum batch size of approximately 1200 liters of slurry.
The main manufacturers of twin planet mixers include Ross from the United States, Asada Iron Works and Inoue Mfg. from Japan, and Hongyun Mixing Equipment from China. The technology of twin planet mixer is highly mature.
2.2 The thin-film high-speed disperser, a new type of slurry dispersion equipment, is introduced to complement the limited dispersing capacity of the dual-planetary mixer. When dealing with difficult-to-disperse materials such as small particle-sized lithium iron phosphate and high-specific-surface-area conductive carbon black, the dual-planetary mixer may struggle to achieve effective dispersion. Therefore, more efficient dispersing equipment is required, and the thin-film high-speed disperser, developed by PRIMIX in Japan, is an excellent choice for slurry dispersion.
The working principle of the thin-film high-speed disperser is as follows: the slurry enters the dispersing vessel from the bottom and rotates at high speed along with the dispersing wheel. Under the centrifugal force, the slurry is thrown against the inner wall of the dispersing vessel, forming a slurry ring. Additionally, the slurry, influenced by the centrifugal force, rapidly separates from the outer wall of the dispersing wheel and impacts the walls of the dispersing vessel. Simultaneously, a momentary vacuum is formed on the surface of the wheel, facilitating the slurry to pass through the dispersing holes on the wheel, resulting in the trajectory shown in the diagram.
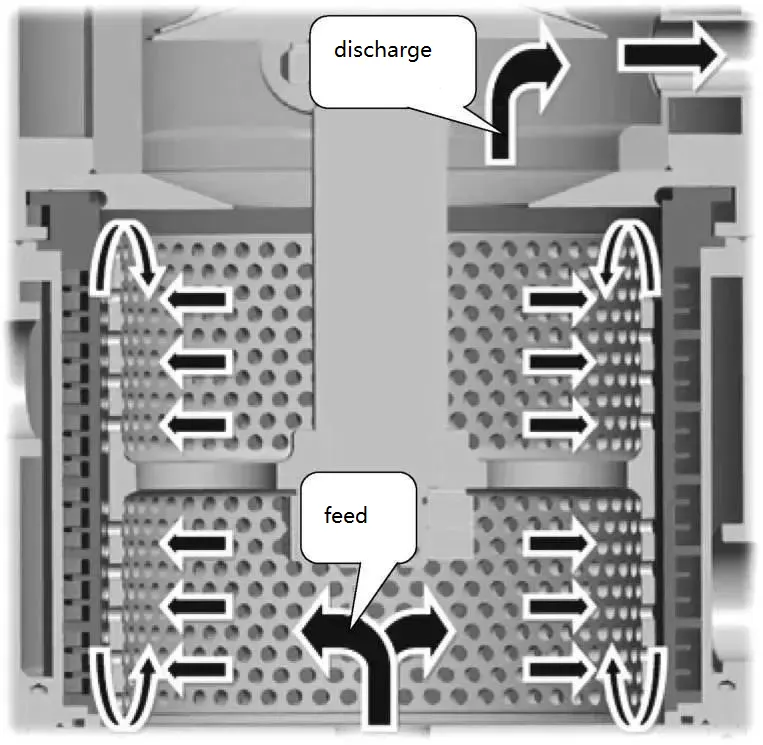
Moreover, due to the narrow gap of only 2mm between the dispersing wheel and the vessel wall, when the dispersing wheel rotates at high speed (with a linear velocity of up to 30-50m/s), the slurry experiences uniform and intense shear forces within this small gap. The slurry has a residence time of approximately 30 seconds inside the disperser. During this time, the slurry undergoes continuous circulation and shear dispersion within the disperser, resulting in an ideal dispersion effect. The diagram illustrates a comparison of the intensity and frequency of shear forces acting on the slurry in both the twin planet mixer and the thin-film high-speed disperser, obtained through simulation calculations. From the diagram, it is evident that in twin planet mixer, the slurry only experiences strong shear forces in the end region of the stirring blades, resulting in a low frequency of high shear action on the slurry. In contrast, in the thin-film high-speed disperser, the slurry experiences strong shear forces throughout the entire region, leading to a high frequency of high shear action on the slurry. This significantly improves the dispersion effect and efficiency of the slurry.
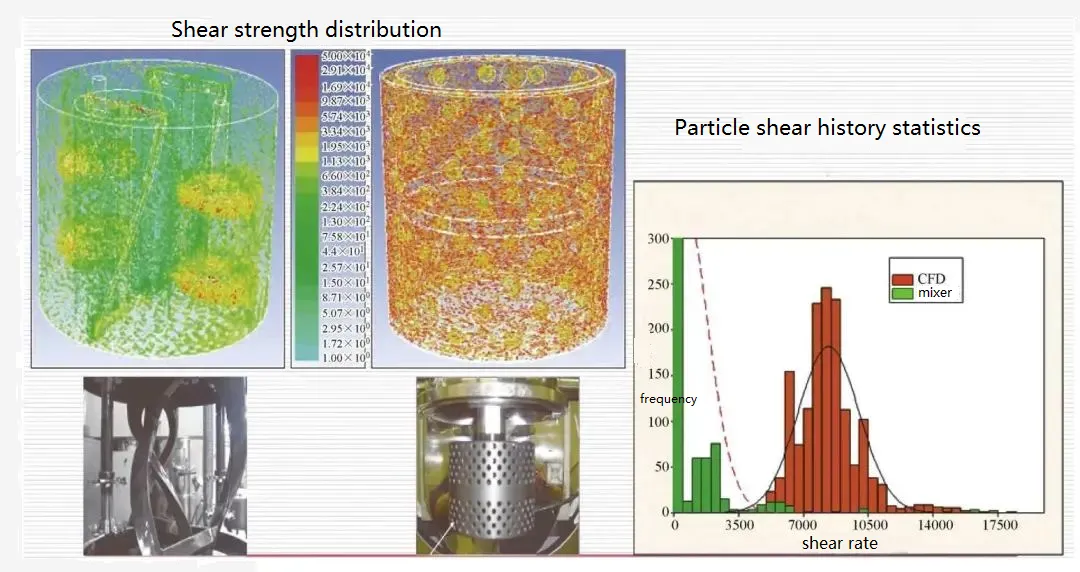
The thin-film high-speed disperser, pioneered by PRIMIX in Japan, has been adopted by some lithium-ion battery manufacturers in South Korea and China. SHANGSHUI was the first to introduce it domestically, and their product performance has reached the same level as PRIMIX’s products. It should be noted that this thin-film high-speed disperser cannot be used independently for slurry production. It requires pre-mixing of powdered and liquid materials to form a slurry using equipment such as a Twin planet mixer before further dispersion using the thin-film high-speed disperser. Therefore, the application of this equipment has certain limitations and is typically used in conjunction with twin planet mixers for the production of difficult-to-disperse materials.
2.3 New pulping equipment – twin-screw pulping machine
To address the issue of low efficiency in twin planet mixers, some manufacturers have introduced new slurry production processes and equipment. One such development that has garnered significant attention is the continuous pulping system, which features a twin-screw extruder as the core equipment. Brueckner from Germany is one of the companies that has introduced this system, which has been widely adopted.
Originally used in industries such as plastics processing, the twin-screw extruder is suitable for mixing and dispersing high-viscosity materials. Brueckner has introduced this equipment into the field of lithium-ion battery slurry production. The system enables the continuous preparation of slurry by introducing powder and liquid at different positions along the screws.
The specific process is as follows: the powder of active materials and conductive agents is first introduced at the front end of the screws. As the screws convey the materials towards the rear end, solvents or adhesives are sequentially added at different sections of the screws. Various screw elements are utilized to achieve processes such as kneading, dilution, dispersion, and deaeration. At the very end of the screws, the output is the finished slurry.
In the twin-screw pulping machine, the dispersion of the slurry primarily occurs during the kneading stage. During this stage, the slurry has high viscosity, and intense shear forces are generated by the action of the screw elements. This enables efficient dispersion of the slurry.。
The pulping process in the double-screw machine involves the continuous mixing of powdered and liquid raw materials, significantly improving the efficiency of macroscopic blending. Additionally, the kneading elements in the machine provide high-intensity shear dispersion for high solids content and high-viscosity slurries, greatly enhancing the dispersion efficiency. As a result, the double-screw pulping machine offers notable advantages such as high efficiency and low energy consumption.
However, the use of twin-screw pulping machines for lithium-ion battery slurry production also has some notable shortcomings. Firstly, due to the long length of the screws in the twin-screw pulping machine and the need to reduce wear and prolong residence time, the rotational speed cannot be too high. Typically, the linear speed at the end of the screw elements is between 2 and 3 m/s. Generating strong shear forces at such a low linear speed requires minimizing the minimum clearances between screw elements and between screw elements and the barrel wall. Currently, the minimum clearance in twin-screw pulping machines is around 0.2 to 0.3 mm. Such a small clearance requires high precision in processing and installation, and it can lead to wear of the screw elements. The resulting worn metal particles may pose serious safety hazards to lithium-ion battery products.
Secondly, the continuous pulping mode of the twin-screw machine requires precise dynamic metering of powdered and liquid raw materials to ensure accurate and stable feed rates for all materials. Any fluctuation in the feed rate of a particular material can cause fluctuations in the ingredient ratio of the slurry. If these fluctuations exceed the acceptable range, it can result in the rejection of a portion of the slurry or even cause unforeseen losses in subsequent processes. Therefore, this continuous pulping system must be equipped with a highly accurate raw material metering and feeding system, which significantly increases the overall system cost. In practical production, to prevent fluctuations in feed rates from causing abnormalities, a large buffer tank with stirring is often installed after the twin-screw extruder. The slurry produced by the extruder is partially homogenized in the buffer tank to eliminate the impact of instantaneous fluctuations in feed rates. However, this approach makes the system somewhat resemble a batch pulping system.
Furthermore, the twin-screw pulping machine is sensitive to fluctuations in raw material quality. If the slurry parameters become non-compliant due to fluctuations in raw material quality, rework is not possible. Additionally, when switching between different product variants, it may be necessary to change some screw elements to accommodate new materials and formulations, resulting in poor adaptability.
Currently, the primary supplier of twin-screw pulping machines is Brueckner from Germany. Some domestic manufacturers in China also offer similar equipment. This continuous pulping system has been adopted by domestic power battery factories in China.
2.4 New pulping equipment – circulating pulping machine
Given the strengths and weaknesses of continuous pulping systems, some manufacturers have introduced semi-continuous pulping systems. Shangshui Intelligent, for instance, has developed a circulating high-efficiency pulping machine that combines the advantages of continuous and batch pulping systems. This system utilizes batch metering, continuous feeding for pulping, and circulating dispersion to achieve efficient preparation of the slurry and uniform dispersion of the entire batch. It has been adopted by high-end domestic power battery factories. The basic structure of Shangshui Intelligent’s circulating pulping machine is shown in Figure 14.
The basic working principle involves first mixing the powder and continuously feeding it into the pulping machine through the powder feeding module at a predetermined flow rate. Under the negative pressure formed during the discharge of the pulping machine, the powder releases some gas and is dispersed into a smoke-like state by the high-speed rotating powder dispersing device. It is then drawn into the fast-flowing liquid, immersed, and dispersed into the liquid. As the slurry flows downward into the dispersion module below the impeller, it undergoes intense shear forces from the high-speed rotating impeller and the stator fixed in the chamber, forming a rotor-stator structure. This achieves a good dispersion state, and the slurry is accelerated by the impeller and discharged through the tangential outlet.
03 Future development trends of pulping equipment
The traditional mixer is still the mainstream pulping equipment so far, and its advantage lies in its strong adaptability, particularly suitable for the production of lithium-ion batteries with frequent variety changes and small batch sizes. However, in the field of power battery manufacturing with less frequent variety changes and larger batch sizes, the disadvantages of low single-machine capacity and high energy consumption of mixers make them gradually replaced by new pulping equipment with higher dispersion efficiency. For example, SHANGSHUI’s circulating pulping machine has been gradually accepted and adopted by high-end power battery manufacturers in China.
Furthermore, researching new dispersants and reducing reliance on high-intensity dispersion equipment is also one of the future development directions in the industry.