Inconsistency among individual batteries often leads to problems such as rapid capacity decay and shorter lifespan in battery packs during cycling processes. Selecting batteries with as consistent performance as possible for grouping is of great significance for the widespread application of lithium-ion batteries in electric vehicles.
This article analyzes the manifestations and causes of inconsistency in lithium-ion batteries, summarizes methods for improving their consistency, and provides an overview of existing battery grouping schemes.
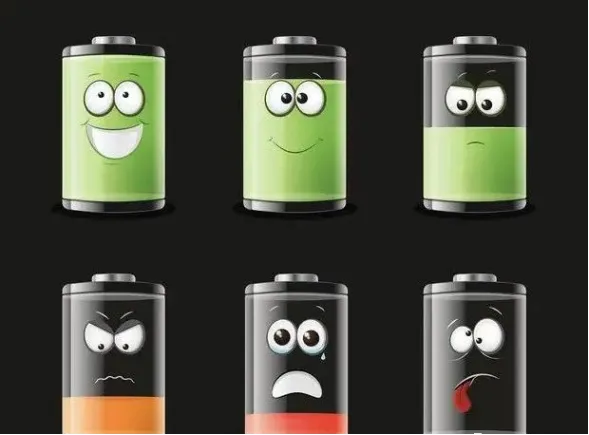
- Inconsistency analysis
1.1 Definition of inconsistency
Inconsistency in lithium-ion battery packs refers to the differences in parameters such as voltage, capacity, internal resistance, lifespan, temperature impact, and self-discharge rate among individual batteries of the same specifications and models when they are assembled into a battery pack.
After manufacturing, individual batteries inherently have some initial performance variations. As batteries are used, these performance differences accumulate over time. Additionally, the usage environment within the battery pack is not identical for each individual battery, which further amplifies the inconsistency among them. This progressive inconsistency accelerates the degradation of battery performance and eventually leads to premature failure of the battery pack.
1.2 Manifestations of inconsistency
The inconsistency in lithium-ion batteries manifests primarily in two aspects: differences in performance parameters (such as capacity, internal resistance, and self-discharge rate) and differences in state of charge (SOC) among battery cells.
Research by Dai Haifeng et al. has found that the distribution of capacity differences among battery cells approximates a Weibull distribution, while the dispersion of internal resistance is more significant than that of capacity. The internal resistance of batteries from the same batch generally follows a normal distribution, and the self-discharge rate also exhibits an approximate normal distribution. SOC represents the charge state of the battery and is the ratio of the remaining capacity to the rated capacity. Due to the inconsistency of batteries, the capacity degradation rate varies, resulting in differences in the maximum available capacity among batteries. Batteries with smaller capacity experience faster SOC changes compared to those with larger capacity, reaching the cutoff voltage more quickly during charging and discharging processes.
1.3 Causes of inconsistency
There are various reasons for the occurrence of inconsistency in lithium-ion batteries, primarily arising from the manufacturing and usage processes. Each stage of the manufacturing process, such as the uniformity of the slurry during material mixing and the control of coating density and surface tension during coating, can result in performance variations among individual battery cells.
Research conducted by Luo Yu et al. has examined the influence of production processes on battery consistency, with a particular focus on the impact of water-based binder systems in lithium-ion battery manufacturing. In the usage process of batteries, Xie Jiao et al. suggest that connection methods, structural components/devices, operating conditions, and environmental factors all have an impact on battery pack consistency. The energy consumption at each connection point is not consistent, and the performance and aging rate of each component or structural part are also inconsistent, leading to varying effects on the battery. Additionally, as each individual battery cell in a battery pack occupies a different position and experiences different temperatures, the performance degradation also differs, further amplifying the inconsistency among battery cells.
2. Methods to improve battery consistency
2.1 Control of production process
The control of the production process primarily involves two aspects: raw materials and manufacturing techniques. In terms of raw materials, efforts are made to select materials from the same batch to ensure consistency in particle size and performance. In the production process, strict control is applied, including ensuring uniform mixing of the slurry and avoiding prolonged storage, controlling the speed of the coating machine to ensure thickness and uniformity of the coating, conducting visual inspections and weight sorting of electrode sheets, controlling the injection volume, and managing formation, capacity-sorting, and storage conditions.
Through research on the preparation techniques of lithium-ion batteries, Luo Yu has identified key processes that significantly impact battery consistency, including material mixing, coating, calendaring, winding/stacking, injection, and formation. In-depth research and analysis have been conducted on the relationship between these key process parameters and battery performance.
2.2 Control of the grouping process
The control of the battery grouping process mainly involves sorting the batteries. The battery pack uses batteries of the same specifications and models, and the voltage, capacity, internal resistance, and other parameters of the batteries are measured to ensure consistency in their initial performance.
According to the research conducted by Xu Haitao et al., during the battery grouping process, voltage differences among individual batteries are a crucial factor affecting the consistency of the battery pack during charging and discharging, while differences in internal resistance among individual batteries result in significant voltage variations among them during the charging and discharging process. Wang Linxia et al. analyzed the impact of the main influencing factor, DCR, on the battery pack in parallel combination lithium-ion batteries, as well as the impact of the main influencing factor, capacity, on the battery pack in series combination lithium-ion batteries, providing necessary guidelines for the combination battery pack. Chen Ping et al. studied the effect of discharge rate on battery grouping consistency and found that as the discharge rate increases, the inconsistency of the batteries is amplified, achieving the effect of eliminating defective batteries.
2.3 Control of use and maintenance processes
Real-time monitoring of batteries is essential. Conducting consistency screening during battery grouping ensures initial consistency in the battery pack’s usage. Real-time monitoring of batteries during usage allows for the observation of consistency issues that may arise. However, when inconsistency is detected, the monitoring circuit may disconnect the charging and discharging circuit, leading to performance degradation. Therefore, a balance must be struck between monitoring and performance. Additionally, real-time monitoring enables timely adjustment or replacement of batteries with extreme parameters, ensuring that inconsistency in the battery pack does not amplify over time.
Implementing a balancing management system is crucial. Intelligent management of batteries can be achieved through appropriate balancing strategies and circuits. Common balancing strategies include voltage-based, state of charge (SOC)-based, and capacity-based strategies. Balancing circuits can be categorized into passive and active balancing circuits based on energy consumption methods. Active balancing enables efficient energy flow between batteries and has been a focus of research both domestically and internationally. Common methods for active balancing include bypassing, switch capacitor, switch inductor, and DC/DC conversion.
Thermal management of batteries is important. Besides maintaining the working temperature of the battery pack within an optimal range, it is essential to ensure consistent temperature conditions among batteries to ensure performance consistency. Adopting appropriate control strategies is crucial. Within the allowable output power range, minimizing the depth of discharge and avoiding overcharging can prolong the cycle life of the battery pack. Strengthening maintenance of the battery pack involves periodic low-current maintenance charging and ensuring cleanliness.
3. Power lithium-ion battery grouping method
3.1 Voltage grouping method
The voltage grouping method can be divided into static voltage grouping and dynamic voltage grouping. Static voltage grouping, also known as open-circuit grouping, is performed without a load and only considers the battery itself. It measures the self-discharge rate of the selected individual battery after being stored in a fully charged state for several days and the open-circuit voltage of the battery at different storage periods in a fully charged state. This method is the simplest to operate but is not very accurate. Dynamic voltage grouping examines the voltage under a load, but it does not take into account factors such as load variations, so it is also not very accurate.
3.2 Static capacity grouping method
One method for battery grouping is to charge and discharge the batteries under specified conditions, calculate their capacity based on the discharge current and discharge time, and group the batteries according to their capacity. This method is simple and practical, but it can only reflect that the batteries have the same capacity under specific conditions and does not fully represent the complete working characteristics of the batteries. Therefore, it has certain limitations.
3.3 Internal resistance grouping method
The main consideration is the internal resistance of individual batteries. This method enables rapid measurement. However, since the internal resistance of batteries can change during the discharge process, accurately determining the internal resistance poses certain difficulties.
3.4 Multi-parameter grouping method
Considering multiple external conditions such as capacity, internal resistance, voltage, self-discharge rate, etc., in the comprehensive assessment of batteries, it is possible to select battery groups with better consistency. However, the prerequisite for this method is that the accurate sorting based on individual parameters requires a long time to complete.
3.5 Dynamic characteristic grouping method
The dynamic characteristic grouping method involves using the charge and discharge characteristic curves of batteries to sort and group them. The charge and discharge curves can reflect most of the battery’s characteristics. By using the dynamic characteristic grouping method, the consistency of various performance indicators of the batteries can be ensured. This method involves a large amount of data and is typically implemented using computer programs. However, this approach leads to lower utilization of the batteries for grouping, which is not conducive to reducing the cost of the battery pack. Another challenge in implementing this method is determining the standard or reference curves.
4. Conclusion
(1) The causes of battery inconsistency mainly lie in the manufacturing and usage aspects of batteries.
(2) Measures to improve battery consistency can be divided into three main aspects:
Strict control of the production process from raw materials and manufacturing techniques.
Adoption of more scientific sorting methods, selecting batteries with consistent initial performance for grouping as much as possible.
Real-time monitoring of batteries during usage, implementation of a balancing management system, adoption of reasonable control strategies, thermal management of batteries, and strengthening maintenance of the battery pack.
(3) When it comes to battery grouping, single-parameter grouping methods have limited practical value due to considering too few factors. Multi-parameter grouping methods and dynamic characteristic grouping methods are relatively comprehensive. Additionally, methods such as electrochemical impedance spectroscopy have also made certain progress.