Brief Introduction of 4680 Cylindrical Cell (Ⅱ)
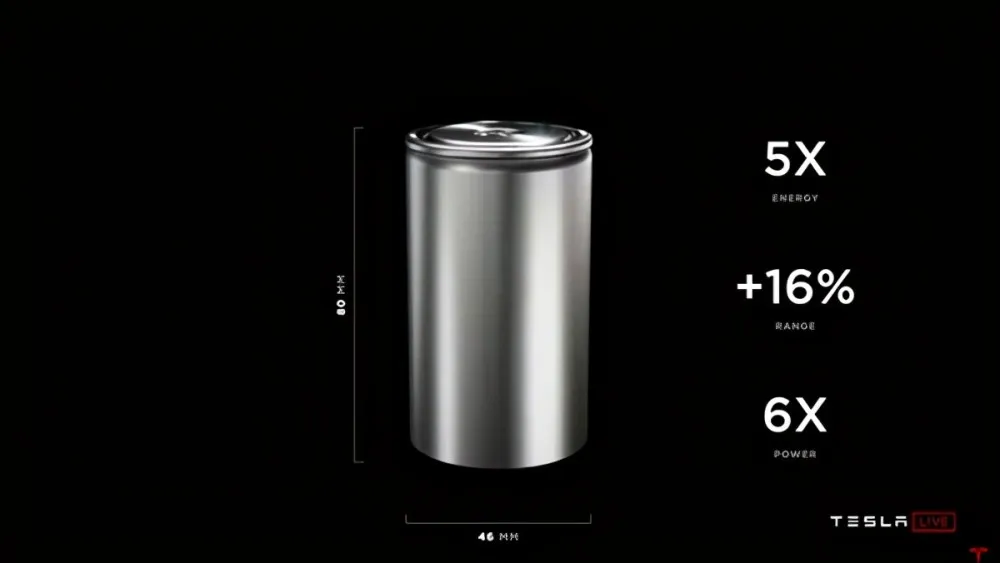

Follow me on:
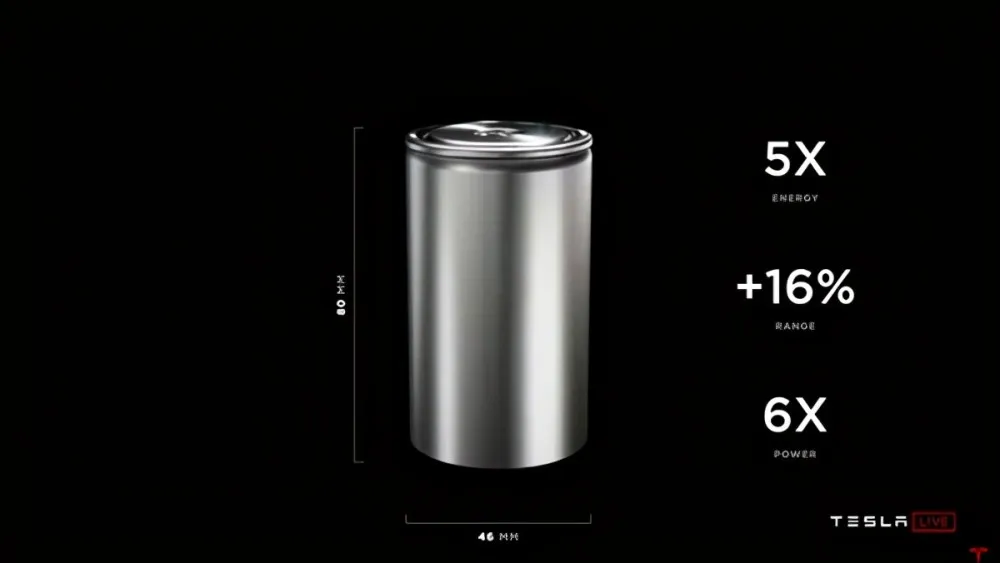
3. Dry electrode technology: This technology can be used on both positive and negative electrode.
Traditional wet process:
The material needs to be placed in a solution, then dried and pressed into a film: use a solvent with a binder material, of which NMP is one of the common solvents. After mixing the solvent with the binder with the negative electrode or positive electrode powder, the slurry is coated on the electrode collector and dried, wherein the solvent is toxic and needs to be recovered, purified and reused. This process needs a large, expensive and complex coating machines.
Dry electrode technology:
The dry electrode process saves the step of adding a solution, which saves the complicated coating and drying steps and greatly simplifies the production process. Mix the active positive and negative particles with PTFE to make it fibrous, then roll the powder directly into a film and pressed onto aluminum or copper foil to prepare positive and negative electrodes.
Advantages of dry electrode technology:
- No solvent is used, expensive coating machines are saved, so the process is simplified, a lot of space and costs are saved.
- Increased productivity: Dry electrode technology enables 7 times faster production.
- Increase battery energy density: In the presence of solvents, lithium and carbon mixed with lithium cannot be well integrated with each other, and there is a problem of first-cycle capacity lossing. Dry electrode technology will greatly improve this problem, thereby increasing battery energy density. At the same time, the thickness of the positive electrode material is increased from 55 μm to 60 μm, and the active electrode material ratio is increased to increase the energy density by 5%, while ensuring the power density.
Difficulties in dry electrode process: the current process is immature, the electrode sheet is thick, and there is a risk of cracking when rolled up.
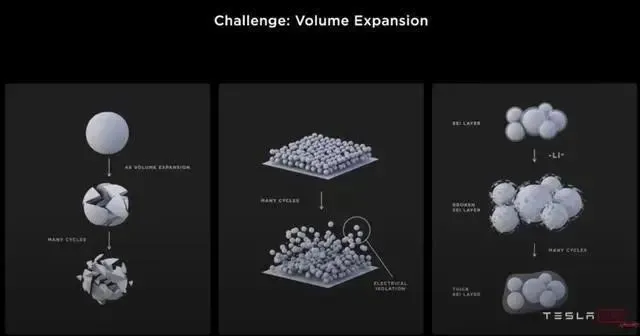
4. Silicon anode
Advantages of silicon anode:
- Theoretical energy density is higher: the theoretical maximum battery capacity of graphite negative electrode is 372Wh/kg, and the theoretical maximum battery capacity of silicon negative electrode can reach 4200Wh/kg.
- Better safety: the voltage system of silicon is higher than that of graphite, and now the negative electrode graphite will produce lithium dendrites, because their voltage system is close to the precipitation potential of lithium, dendrites will pierce the separator, and the positive and negative electrodes will short circuit, which seriously threatens the battery safety.
- Lower cost: silicon material has a wide source, abundant reserves, low production cost, and is environmentally friendly. The mass energy density of lithium-ion cells using silicon anode materials can be increased by more than 8%, the volumetric energy density can be increased by more than 10%, and the cost per KWH of cells can be reduced by at least 3%.
Disadvantages of silicon anode:
- Poor cycle performance: the volume expands after lithium intercalation, graphite has no obvious volume expansion after lithium ion intercalation, but the volume of silicon expands more than four times after lithium ion intercalation, and the battery is scrapped after many times of expansion and contraction.
- Poor conductivity: The low conductivity of silicon limits the full utilization of its capacity and the rate performance of silicon electrode materials; the volume change makes the contact between the active material and the conductive agent binder poor, and the conductivity decreases; the SEI film on the silicon surface is thick and uneven, affects the conductivity and the overall specific energy of the battery.
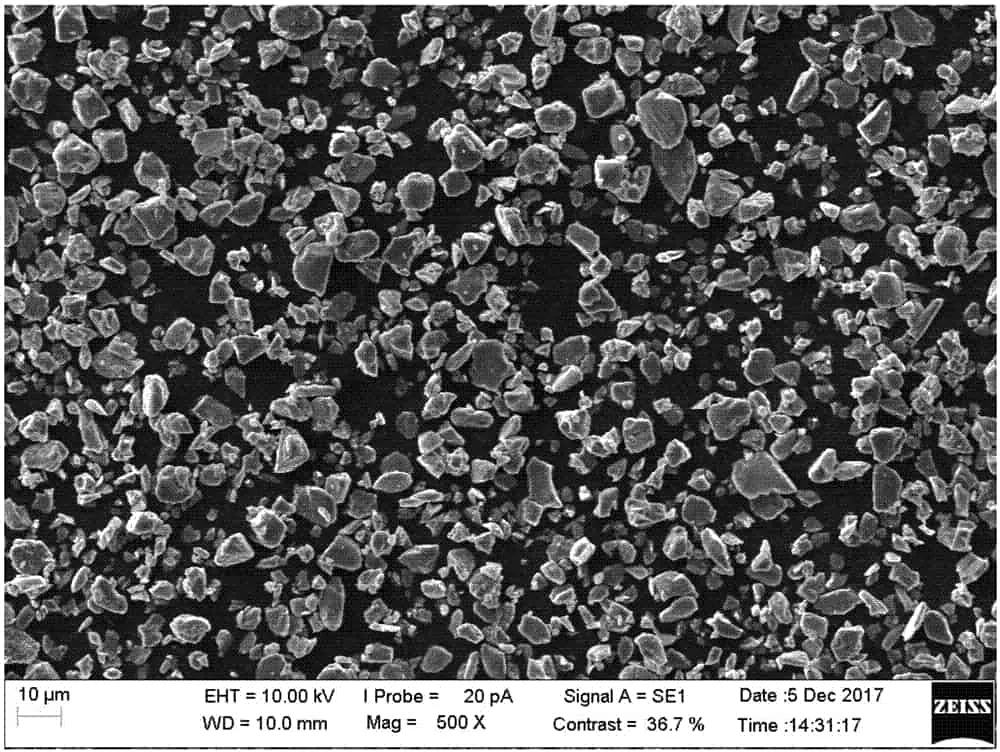
Battery companies are actively applying silicon-carbon anodes, which is the development direction of silicon-carbon anodes. Silicon-carbon anodes are currently mainly used in cylindrical batteries. In the high-capacity battery solutions of power battery manufacturers such as CATL, LISHEN, GOTION, and PRIDE, silicon-carbon anodes have clearly developed direction.
Acceleration of R&D and production of silicon-carbon anodes: foreign silicon-carbon industrialization is relatively leading, and Chinese manufacturers are actively catching up. At present, China’s anode manufacturers have increased their investment in silicon-carbon anodes, and BTR, SHANSHAN, GOTION, and ZET can achieve mass production. And, the BTR silicon carbon anode supplies Panasonic power batteries and enters the Tesla supply chain. Some battery companies such as CATL, BYD, GOTION, BAK and LISHEN are actively deploying silicon carbon materials.
Silicon carbon batteries are an inevitable trend in the development of high energy density. With the overcoming of technical bottlenecks and the improvement of end customer acceptance, silicon carbon will reduce costs and achieve mass production. CNCET predicts that the production and consumption of silicon-carbon anode materials in China will reach 60,000 tons in 2023, and the future market prospect of silicon-carbon anodes is huge.