In-depth introduction to sodium-ion batteries(Ⅱ)
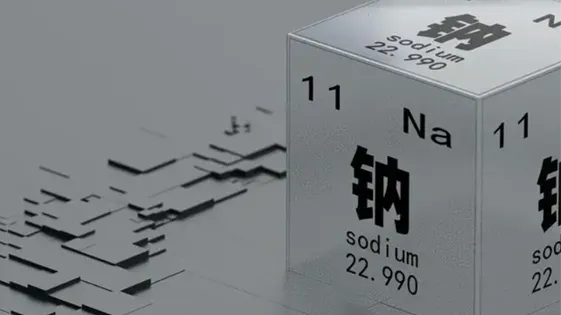

Follow me on:
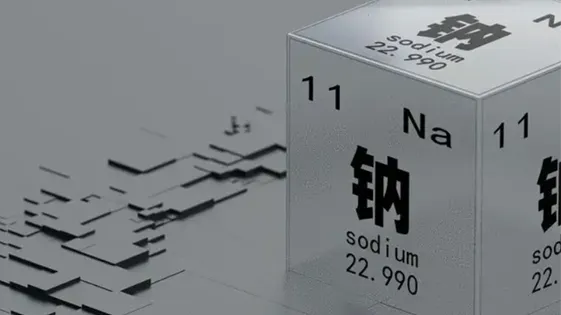
3.Sodium Ion Battery Cathode Materials
Sodium ion battery cathode materials can be classified based on their crystal structures into oxide-based materials (layered and tunnel structures), Prussian blue analogs, phosphate fluorides, phosphates, sulfates, and others. Among them, layered oxides, polyanion compounds, and Prussian blue analogs are the three mainstream cathode routes. Currently, each of these three approaches has its own advantages and disadvantages, and it is expected that there will continue to be diversified development in the short term.
3-1.Layered Oxides (Sodium Iron Manganese Oxide, Sodium Titanium Iron Oxide, etc.)
The structure of layered oxides, such as sodium iron manganese oxide and sodium titanium iron oxide, is similar to that of ternary materials in lithium-ion batteries, offering excellent energy density advantages but slightly lower cycling lifespan. Prussian blue compounds are advantageous due to their low cost, but suffer from poor conductivity and cycling lifespan. Polyanion compounds have outstanding cycling lifespan and high voltage, but lower specific capacity and some configurations involve the high cost of adding vanadium elements.
Layered oxides have a relatively high level of maturity and exhibit excellent overall performance. Both layered oxides and ternary materials in lithium-ion batteries are types of intercalation compounds, allowing for shared production processes and production lines, resulting in a relatively high degree of process maturity. Additionally, layered oxides have advantages in terms of high specific capacity and high packing density. However, due to the large size of sodium ions, irreversible structural changes occur during insertion and extraction processes, leading to reduced material cycling lifespan. Furthermore, the flexibility of sodium ions in the two-dimensional structure makes layered oxides highly reactive with substances such as water and carbon dioxide in the air, leading to the formation of byproducts on the crystal surface.
The chemical formula for layered oxides is NaxMO2 (M represents transition metal elements such as nickel, cobalt, manganese, iron, etc.). Depending on the coordination environment of sodium ions and the arrangement of oxygen, they can be categorized as O3, P3, P2, O2, etc., with O3 and P2 being the main configurations. The O3 configuration (e.g., NaNiO2, NaFeO2, NaCrO2, etc.) has a higher sodium content and energy density, but due to the narrow tetrahedral positions that sodium ions must traverse during migration, diffusion barriers are high, leading to poor cycling lifespan. The P2 configuration (e.g., Na2/3Ni1/3Mn2/3O2, Na2/3Fe1/2Mn1/2O2, etc.) offers better cycling lifespan and higher air stability, but slightly lower specific capacity. To address phase transition issues during the deintercalation process of layered oxides, the introduction of elements like manganese, iron, and copper is commonly used to achieve a stable crystal structure.
3-2.Polyanion Materials
Polyanion materials exhibit stable structures and long cycling lifespans; however, they are associated with higher costs and lower energy density performance. The chemical formula for polyanion materials is NaxMy[(XOm)n-]z (where M represents variable-valence metal ions, and X represents elements such as phosphorus, sulfur, silicon, etc.). The oxygen polyhedra of metal ions form a stable framework structure, contributing to these materials’ good cycling lifespan and safety. Due to the presence of larger anionic groups, the materials have lower conductivity and specific capacity. To address the suboptimal rate performance and energy density resulting from poor conductivity, modifications can be achieved through methods such as carbon coating or the addition of conductive agents.
Common polyanion materials include sodium iron sulfate, sodium iron phosphate, sodium vanadium phosphate, sodium vanadium fluorophosphate, and composite polyanion compounds involving pyrophosphate, among others. Sulfate anions have higher electronegativity and voltage compared to phosphate anions. Sulfate-based materials have the advantage of lower cost, but their susceptibility to moisture absorption and decomposition leads to poorer cycling lifespan and relatively lower theoretical capacity. Vanadium-based polyanion materials offer higher operating voltages (3.4-3.8V) and theoretical specific capacities. However, the higher cost and toxicity of vanadium weaken its cost-effectiveness as a sodium-ion battery material.
3-3.Prussian Blue Materials
The primary advantages of Prussian blue materials lie in their low cost and good energy density performance. However, they suffer from poor conductivity, cycling lifespan, and potential cyanide toxicity. Prussian blue compounds possess a perovskite-like structure with a face-centered cubic arrangement, and their chemical formula is NaxMa[Mb(CN)6] (where Ma and Mb are primarily transition metal elements). Prussian blue materials feature an open three-dimensional channel (framework structure) that enables rapid sodium ion migration within the tunnel. As a result, they exhibit favorable structural stability and exceptional rate performance. Prussian blue compounds are typically synthesized in aqueous solutions, which may contain trace lattice water. This lattice water could be released during cycling, posing a risk of short-circuiting or reacting with the electrolyte to corrode the material.
In 2015, Goodenough developed Prussian white, a sodium-ion battery cathode material variant of Prussian blue, which exhibits higher sodium content and consequently superior energy density compared to regular Prussian blue. Currently, common methods for preparing Prussian blue compounds include coprecipitation and hydrothermal synthesis. To address issues such as crystal water content and poor conductivity, coating, doping, and high-temperature drying treatments are often employed to enhance their performance.
4.Sodium Ion Battery Anode Materials: Mainly Hard Carbon Materials
Sodium-ion battery anode materials primarily utilize hard carbon, distinguishing them from the graphite materials used in lithium-ion batteries. This is due to the fact that sodium ions have three times the molar mass of lithium ions and are 1.3 times larger in diameter, preventing sodium ions from reversibly intercalating and de-intercalating within the graphite layers within an effective potential window. Additionally, the sodium-ion-graphite intercalation compounds are thermodynamically unstable and can easily form NaC64.
Currently, there are four main categories of materials that can be used: carbon-based materials (soft carbon/hard carbon, etc.), transition metal compounds, alloy-type anodes, and organic compounds. Among these, transition metal compounds achieve sodium storage through conversion reactions and alloying reactions. However, they often experience significant volume expansion during cycling, leading to electrode material pulverization and collapse, which poses safety concerns. Transition metal compounds also have relatively lower specific capacities, and organic materials suffer from low Coulombic efficiency.
In comparison to soft carbon materials such as graphite, hard carbon materials cannot graphitize and have lower structural regularity in terms of carbon layer alignment. They exhibit numerous micropores between layers, facilitating the intercalation and de-intercalation of sodium ions. Furthermore, hard carbon materials offer advantages such as high sodium storage specific capacity, lower sodium storage voltage, and cycling stability. As a result, they are currently the preferred choice for anode materials.
5.Sodium Ion Electrolyte
The composition of sodium-ion batteries is similar to that of lithium-ion batteries, consisting of solvent, solute, and additives. However, there are differences in the solute component. Currently, commonly used sodium salts in sodium-ion batteries include:
NaPF6 (Sodium Hexafluorophosphate): It exhibits better electrochemical stability compared to lithium hexafluorophosphate and has the highest conductivity in PC-based (propylene carbonate) electrolytes. However, its higher cost and slight toxicity affect its practical application.
NaClO4 (Sodium Perchlorate): It offers advantages such as fast ion migration, good compatibility, and low cost. However, its drawbacks include high water content, susceptibility to explosion, and high toxicity, which hinder its practical use.
6.Collector: Primarily Aluminum Foil
The current collector plays a crucial role in batteries by carrying the active materials and conducting electric current. In lithium-ion batteries, the lower negative electrode potential makes aluminum foil more susceptible to alloying reactions with lithium. As a result, aluminum foil cannot be used as the negative electrode current collector; copper foil is preferred instead. In sodium-ion batteries, sodium does not readily undergo alloying reactions with aluminum, making aluminum foil a common choice for the negative electrode current collector.
Compared to traditional aluminum foil, battery-grade aluminum foil has higher requirements for cleanliness, uniformity of plate shape, mechanical properties, and surface wetting ability. The use of aluminum foil in sodium-ion batteries does not exhibit significant differences from its use in lithium-ion batteries.
7.Sodium Ion Battery Related Companies
In Chinese companies, Hina, LiFun, CATL have achieved mass production of sodium-ion batteries. Traditional lithium-ion battery companies like Svolt, Gotion, EVE., CATL, Sunwoda, and Pylon are also strategically positioning themselves in the sodium-ion battery technology landscape. On the international front, UK-based Faradion has a long history and deep expertise in sodium-ion battery technology. Companies such as Natron Energy in the USA and Altris in Sweden are accelerating their efforts towards mass production.
Regarding the layout of sodium-ion battery cathode materials, Ronbay has achieved initial mass production capabilities. ZEC is commencing relevant capacity construction. Companies like EASPRING, GEM, Bangpu have patent layouts and are actively promoting industrialization.
In the anode material layout, Chinese companies like Hina utilize anthracite coal to prepare soft carbon materials. CATL has developed hard carbon materials with unique pore structures. BTR has achieved mass production of both hard and soft carbon materials. PTL and Xiangfenghua are currently conducting pilot testing. On the international stage, Japanese companies KUREHA, Mitsubishi, and Panasonic are involved in the research and production of sodium-ion battery anode materials.
In terms of electrolyte layout, Natrium has a production capacity of 5,000 tons of electrolyte, with plans to establish an electrolyte production line for 80,000 tons of positive electrode materials in the next 3-5 years. DuFluoride Chemicals Co., Ltd. (DFD) already has a production capacity of one thousand tons for sodium hexafluorosilicate (NaFSI), and it has successfully developed NaFSI. Tianci, CAPCHEM, Shenghua, and YongTai are making progress in this area.
Both the positive and negative current collectors for sodium-ion batteries are expected to use relatively inexpensive aluminum foil. Therefore, sodium-ion batteries are expected to increase aluminum foil usage per GWh by nearly twice that of lithium-ion batteries. In the domestic aluminum foil market, the battery application accounted for only 3.1% of total demand in 2021, with a total shipment volume of approximately 130,000 tons.
In 2021, DSXC, North China Aluminum, and Yongjie Aluminum are the top three players in the domestic market, with a combined market share of nearly 75%. DSXC began producing and researching battery-grade aluminum foil in 2015 and has established close collaborations with customers such as CATL, BYD, Tesla, Gotion, and LG. The company’s current capacity for battery-grade aluminum foil exceeds 100,000 tons, with an expected expansion to 150,000 tons by the end of 2022 and a potential breakthrough of 200,000 tons in 2023.
8.Risk Alerts
Lower-than-expected downstream demand: The advancement of sodium-ion battery industrialization relies on key steps such as 1) material development, 2) cost reduction, 3) product qualification, and successful customer validation. Any issues arising in these steps could impede the progress of industrialization.
Energy storage aspect: Currently, many countries primarily drive the economic viability of energy storage through subsidies. If subsidy policies and electricity market reforms fall short of expectations, the market dynamics for sodium-ion batteries might weaken. In sectors like low-speed vehicles, two-wheelers, and commercial vehicles, lithium-ion batteries are more commonly used. Consequently, weak demand for sodium-ion batteries in these downstream areas could pose potential risks to the sodium-ion battery industry.
Intensified product competition: In addition to competition from lithium-ion batteries, the industry is also witnessing the promotion of new battery technologies like vanadium batteries. If product competition intensifies, it could have adverse effects on the sodium-ion battery industry.