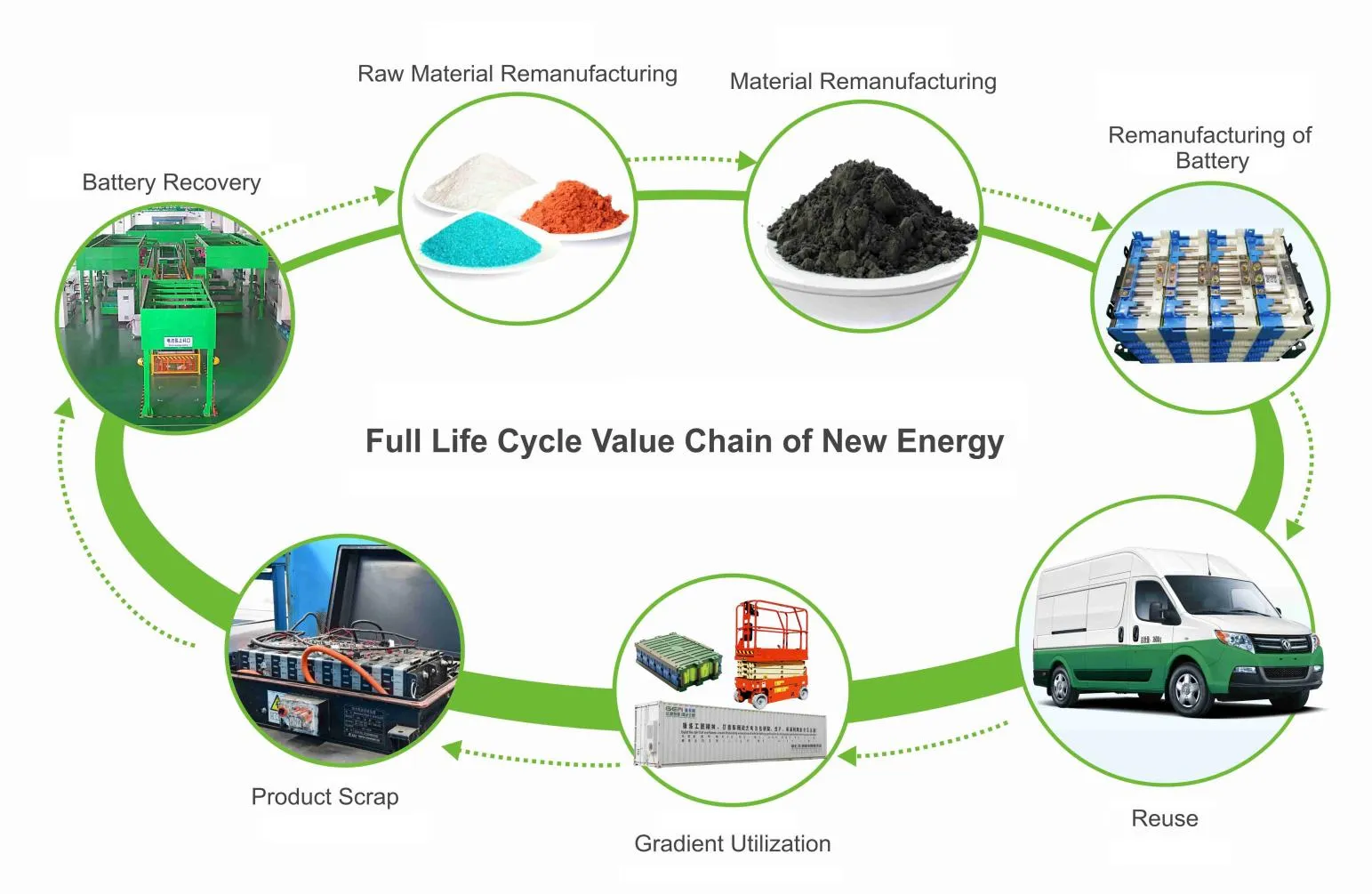
The recycling process of used lithium-ion batteries mainly includes pretreatment, secondary treatment and advanced treatment. Since there is still some electricity left in the used batteries, the pretreatment process includes deep discharge, crushing, and physical sorting; The purpose of the secondary treatment is to realize the complete separation of the positive and negative active materials from the substrate. Heat treatment, organic solvent dissolution, lye dissolution and electrolysis are commonly used to achieve complete separation of the two; The advanced treatment mainly includes two processes of leaching and separation and purification to extract valuable metal materials. According to the classification of extraction process, lithium battery recycling methods can be mainly divided into three categories: dry recycling, wet recycling and biological recycling.
1. Dry recycling: refers to the recycling of materials or valuable metals directly without using a medium such as a solution. Among them, the important methods used are physical separation method and high temperature pyrolysis method.
(1) Physical separation method: refers to dismantling and separating the battery, crushing, sieving, magnetic separation, fine crushing and classification of battery components such as electrode active materials, current collectors and battery casings, so as to obtain valuable high content of substances. The physical separation method is relatively simple to operate, but it is not easy to completely separate lithium-ion batteries, and there is a certain loss during screening and magnetic separation, so it is difficult to achieve complete separation and recovery of metals.
(2) High-temperature pyrolysis method: refers to decomposing physically crushed lithium-ion battery materials at high temperature, removing organic binders, and separating the constituent materials of lithium-ion batteries. At the same time, the metals and their compounds in lithium-ion batteries can be oxidized, reduced and decomposed, volatilized in the form of steam, and then collected by condensation and other methods.
The technology of this lithium battery recycling method is simple, easy to operate, fast in high temperature environment, high in efficiency, and can effectively remove binder; and this method does not have high requirements on the composition of raw materials, and is more suitable for processing a large number of or more complex batteries. However, this method have high requirements on equipment; during the treatment process, the organic matter of the battery will decompose and generate harmful gases, so it is necessary to add purification and recovery equipment to absorb and purify harmful gases and prevent secondary pollution.
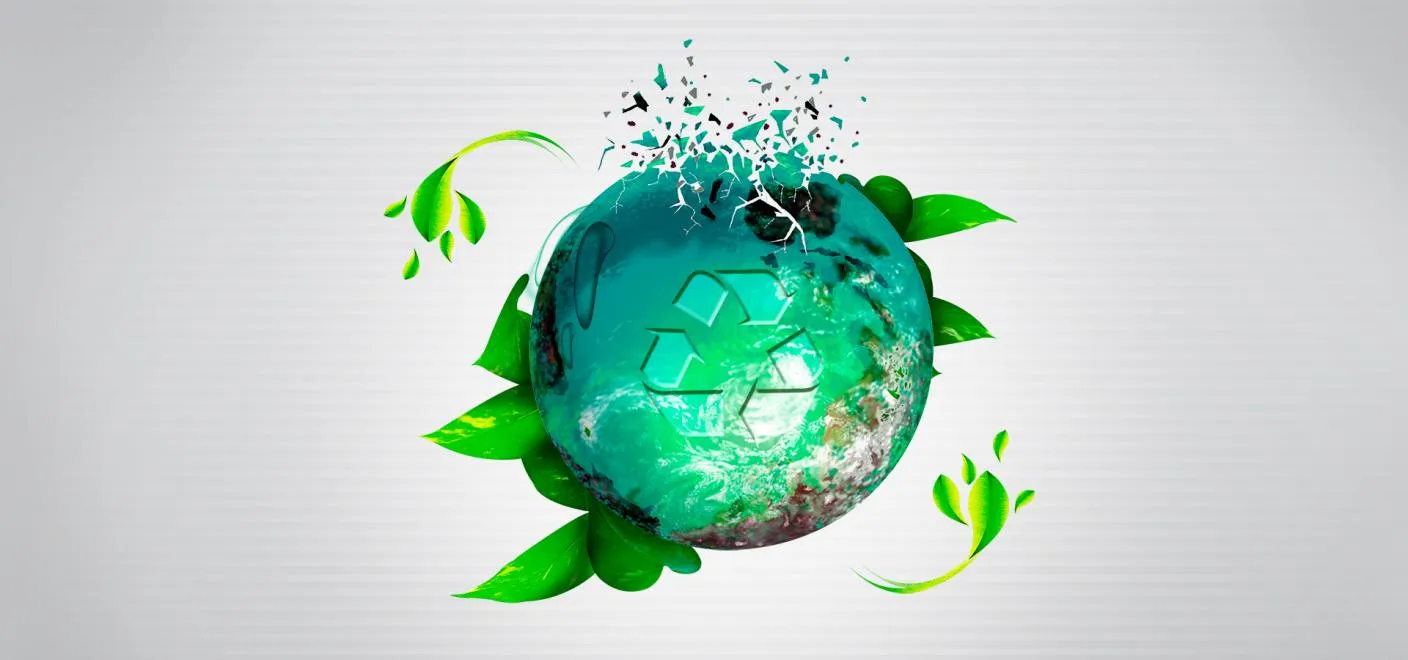
2.Wet recycling: the waste battery is crushed and dissolved, and then the metal elements in the leaching solution are selectively separated using appropriate chemical reagents to produce high-grade cobalt metal or lithium carbonate, etc., which can be directly recycled. Wet recycling is more suitable for the recovery of waste lithium-ion batteries with a relatively single chemical composition, and its equipment cost is lower, which is suitable for the recovery of small and medium-sized waste lithium-ion batteries.
(1)Alkali-acid leaching method: Since the positive electrode material of lithium-ion batteries will not dissolve in lye, and the base aluminum foil will dissolve in lye, this method is often used to separate aluminum foil. However, the alkaline leaching method cannot completely remove PVDF, which has adverse effects on subsequent leaching.
(2) Organic solvent extraction method: using the principle of similarity and compatibility, using a suitable organic solvent to physically dissolve the organic binder, thereby weakening the adhesion between the material and the foil, and separating the two. The experimental conditions of using organic solvent extraction to separate materials and foils are relatively mild, but organic solvents are toxic to a certain extent and may be harmful to the health of operators. At the same time, because different manufacturers have different processes for making lithium-ion batteries, the binders they choose are different. Therefore, for different manufacturing processes, manufacturers must choose different organic solvents when recycling waste lithium-ion batteries. In addition, cost is also an important consideration with regard to large-scale recycling operations at an industrial level. Therefore, it is very important to choose a solvent with wide sources, reasonable price, low toxicity and harmlessness, and wide applicability.
3.Biological recycling: It is a technology that uses microorganisms to convert useful components in the system into soluble compounds and selectively dissolve them to obtain a metal-containing solution, to achieve separation of target components from impurity components, and to finally recover useful metals; and compared with traditional battery recycling technologies, biological recycling has the advantages of less infrastructure investment, lower operating costs, and less environmental pollution; however, this is a relatively new topic, and there are still many problems to be solved, such as the selection and cultivation of strains , control of leaching conditions, metal bioleaching mechanism, etc.
The bioleaching method has low cost, high recovery efficiency, less pollution and consumption, less impact on the environment, and microorganisms can be reused; However, the cultivation of high-efficiency microbial fungi is difficult, the treatment period is long, and the control of leaching conditions are several major problems required by this lithium battery recycling method.
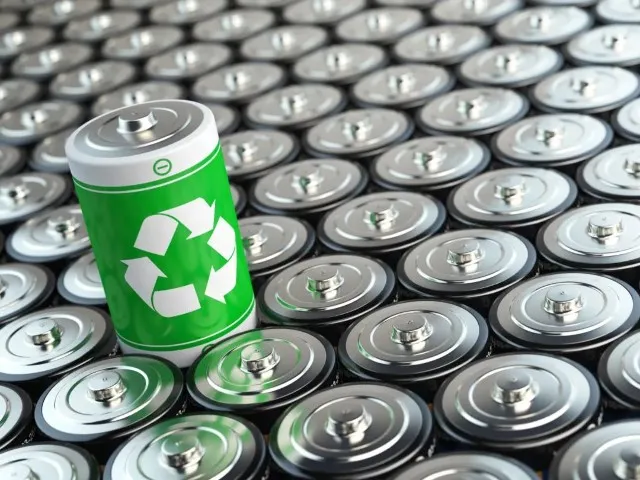