Microscopic Mechanism of Viscosity in Lithium Slurry
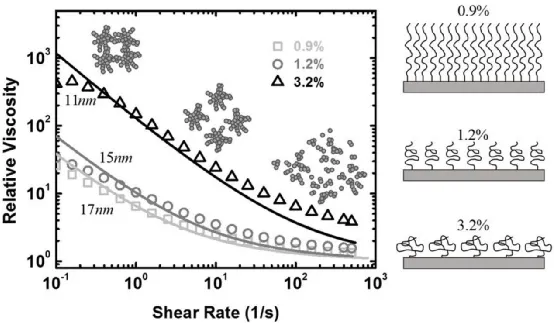

Follow me on:
Viscosity is the degree of resistance to flow within a fluid, and its definition formula is: viscosity η = shear force τ / shear rate γ.

The shear force τ is the force per unit area experienced by a fluid along a tangent in shear flow, as shown in the figure. Its definition formula is:

Where F represents the shear force and A represents the area over which the shear force is applied.
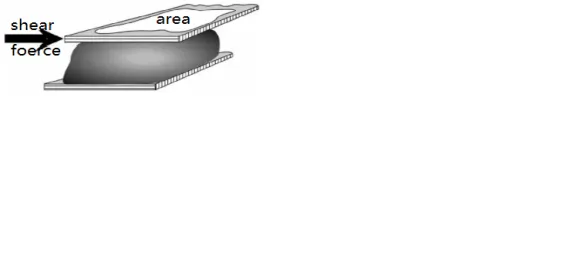
The shear rate γ is the velocity gradient between fluid layers and represents the speed of fluid motion. Under the action of shear force, the fluid flows along the x-axis, and the velocity distribution between the layers is shown in the figure. The shear rate γ is defined as:

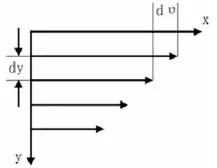
The most common type is Newtonian fluid (such as water, most organic solvents, etc.), which is characterized by a linear positive correlation between shear force and shear rate. The viscosity of a Newtonian fluid remains constant with respect to shear rate at a given temperature. The viscosity of non-Newtonian fluids is influenced by shear rate. Pseudoplastic (shear-thinning) fluids exhibit a decrease in viscosity with increasing shear rate (referred to as shear thinning). Dilatant (shear-thickening) fluids, on the other hand, show an increase in viscosity with increasing shear rate (referred to as shear thickening).
Lithium battery slurry is a shear-thinning non-Newtonian fluid, where viscosity decreases with increasing shear rate. Therefore, when referring to the viscosity of slurry, it is generally necessary to specify the shear rate conditions. The viscosity that actually affects the coating performance is the viscosity value at the actual shear rate during the coating process.
From a microscopic perspective, viscosity is determined by the interactions between particles in a suspension. Typical electrode slurry consists of active materials, carbon black additives, polymer binders, and solvents. The colloidal interactions between particles play a crucial role in particle self-assembly and overall rheological properties. The colloidal interactions between large polymer molecules and carbon black conductor particles lead to particle aggregation and cluster formation, which dominate the rheological behavior. This article takes the negative electrode slurry composed of graphite, carbon black conductor additive particles, PVDF polymer binder, and NMP solvent as an example to illustrate the microscopic mechanisms of viscosity.
As shown in the figure, the main colloidal interactions between particles include van der Waals forces, polymer steric hindrance, electrostatic repulsion, hydrodynamic interactions, and dissipative interactions. Colloidal interactions primarily occur between particles ranging in size from hundreds of nanometers to several micrometers. PVDF is physically absorbed onto the surface of carbon black particles, reducing the high surface tension between carbon black particles and NMP. The length of the PVDF coating layer is closely related to solvent properties, particle surface morphology, particle-polymer ratio, and polymer molecular weight. The PVDF coating layer gives rise to electrostatic repulsion and steric hindrance between PVDF-coated carbon black particles, as shown in Figure b. The dispersed carbon black particles in NMP have a very low zeta potential (measured to be approximately -10 mV using a zeta potential analyzer), hence electrostatic repulsion can be neglected, and the dominant colloidal interaction arises from steric hindrance. The colloidal forces exert a much stronger effect on carbon black particles compared to graphite particles, as shown in Figure d. Due to weak attractive forces, carbon black particles assemble into highly branched aggregates or flocculent structures (Figure c). In contrast, the relatively larger graphite particles do not form interconnected fractal structures.
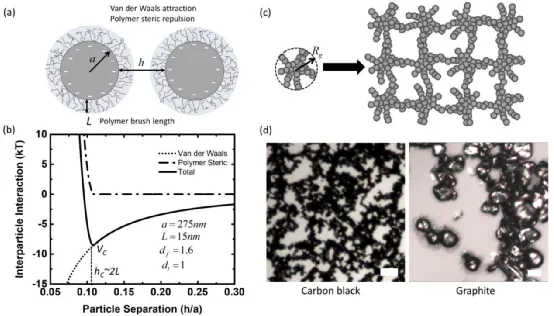
(a) A schematic diagram illustrating the polymer coating on carbon black particles and the colloidal interactions between particles.
(b) Typical inter-particle forces between two carbon black particles coated with PVDF.
(c) Schematic diagram of primary carbon black particles assembling into secondary aggregates, which are interconnected to form a network.
(d) Optical images of carbon black (left) and graphite (right) particles.
First, let’s study the viscosity of carbon black and polymer suspensions. In the suspension of carbon black and PVDF polymer, the amount of PVDF remains constant while the amount of carbon black increases, resulting in a variation of particle volume fraction from 0.9% to 3.2%. The experimental results are shown in Figure 4. The carbon black and polymer suspension exhibit shear thinning behavior, where the viscosity decreases with increasing shear rate.
At low shear rates, colloidal interactions between particles dominate, and the network of fractal aggregates formed by carbon black interconnections fills the entire slurry. Due to strong inter-particle forces and a high volume fraction of carbon black aggregates, the relative viscosity is high.
At moderate shear rates, when the fluid dynamic shear forces become slightly stronger than or comparable to the maximum bond strength between carbon black particles, the carbon black network or large clusters of carbon black particles break down into smaller aggregates. As the shear rate further increases, the fluid dynamic interactions become stronger, causing the larger aggregates to further break down into smaller aggregates or even individual particles, resulting in lower viscosity of the carbon black suspension.
The breaking and reformation of the carbon black network are reversible processes. When the shear rate is reduced, the carbon black particles reassemble into an interconnected network, leading to an increase in viscosity.
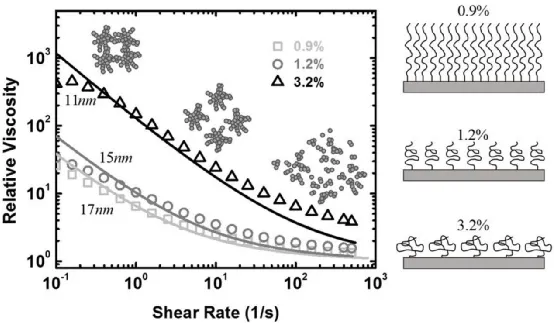
The experimental results for the viscosity of carbon black and PVDF slurries at three different particle concentrations are shown below. The schematic on the right illustrates the morphology of PVDF on the surface of carbon black at three different particle volume fractions.
The morphology of the polymer absorbed on the surface of carbon black particles varies with the available surface space of the particles. When the volume fraction of carbon black is low, there is less total surface area of the particles, resulting in more polymer being adsorbed on the surface and the polymer chains being stretched and opened. However, when the volume fraction of carbon black is high, such as 3.2%, there is sufficient space on the carbon black surface to accommodate PVDF, allowing the PVDF polymer chains to remain in a coiled conformation. The PVDF polymer adopts a “relaxed” structure, and higher concentrations of carbon black particles lead to shorter polymer lengths.
The maximum attractive force between two carbon black particles depends on the thickness of the adsorbed polymer layer because when the surface-to-surface distance between the particles reaches 2L, the strong polymer steric hindrance exceeds the van der Waals attraction and becomes dominant. For smaller polymer layer thicknesses, the two particles come closer together, resulting in stronger van der Waals attraction between the particles. Therefore, as the volume fraction of carbon black particles increases from 0.9% to 3.2%, the viscosity increases sharply.
Continuing with the addition of graphite particles with a volume fraction of 26% to the carbon black suspension, the carbon black particles still form a network, and the graphite particles are embedded within the carbon black network. As colloidal interactions primarily occur between particles ranging in size from hundreds of nanometers to several micrometers, at lower shear rates, the viscosity of the entire graphite slurry is similar to that of the carbon black and polymer solution, with a relatively small impact from the graphite particles.
However, as the shear rate increases, the fluid dynamic interactions become stronger, and the shear forces between the graphite particles start to dominate the viscosity. In summary, nano-sized particles such as carbon black and CNTs have a greater impact on viscosity due to their strong interactions.
The microscale mechanism for the graphite, CMC, and water system is similar. As shown in the figure, when the CMC concentration is low (lower part of the figure) and the graphite concentration is low, an adequate amount of CMC is adsorbed on the particle surfaces, inhibiting the aggregation of graphite particles. With increasing graphite concentration, the amount of CMC adsorbed on each graphite particle decreases (lower center of the figure), weakening the interactions between particles. This results in a decrease in viscosity in the low shear rate region and the emergence of shear thinning in the high shear rate region.
Further increasing the graphite concentration causes a further reduction in the amount of CMC adsorbed on each particle, weakening the interactions between graphite particles and leading to aggregation (lower right corner of the figure). This results in an increase in viscosity and data fluctuations. When the CMC concentration is increased (upper part of the figure), even at higher graphite concentrations, there is enough CMC adsorbed on the graphite surface to disperse the graphite particles. Therefore, the viscosity does not increase significantly, and shear thickening is also suppressed in the high shear rate range.
The CMC with the highest molecular weight provides stronger steric hindrance interactions, thus exerting a greater influence on viscosity and shear thickening.
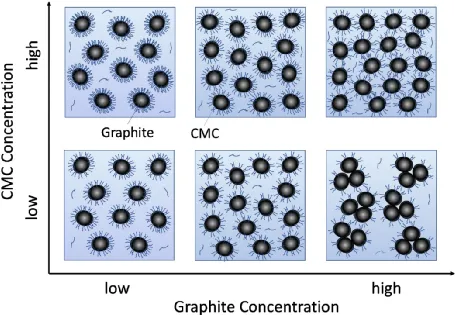
In addition to encapsulation (a), the interactions between polymers and particles also include (b) the formation of a three-dimensional network structure with the binder, where steric hindrance prevents particle aggregation, and (c) bonding between the binder and the surface of active particles, connecting the particles together. This results in the formation of a gel structure in the slurry, leading to higher viscosity.
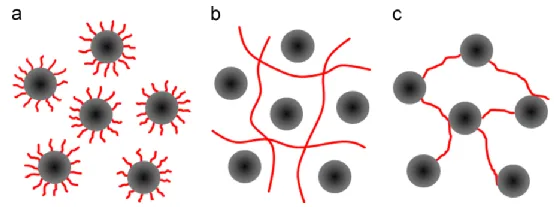
For high nickel materials, when PVDF binder is used, the presence of residual alkali groups on the material surface can lead to dehydrofluorination reaction of PVDF, resulting in the formation of carbon-carbon double bonds (C=C) in the polymer. These C=C double bond structures further promote cross-linking between PVDF chains, forming a gel network throughout the electrode slurry. This cross-linking is an irreversible reaction, making it difficult to reduce the viscosity of the gel-like slurry by means such as adding solvents.
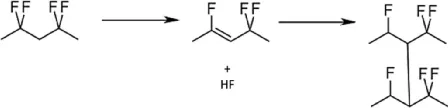
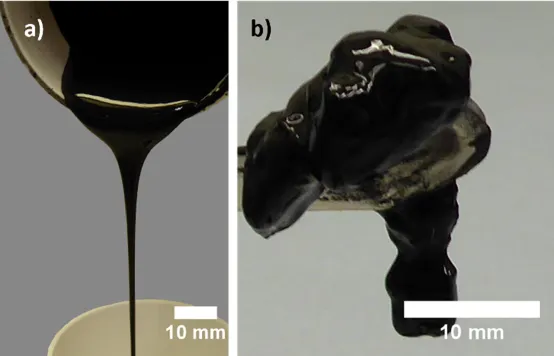