リチウムイオン電池用のレーザー溶接機は、電池製造業界の基礎となる技術として浮上しています。高性能で信頼性の高いリチウムイオン電池の需要が電気自動車、家電製品、エネルギー貯蔵などのセクターで急増し続ける中、これらの機械が提供する精度と効率は比類のないものです。このブログ投稿では、レーザー溶接機の基本的なコンポーネントと利点、さまざまなバッテリー形式での役割、および最適なパフォーマンスと安全性を確保するための重要な要素について説明します。業界の専門家であろうと、単に最新のバッテリーの背後にある技術に興味があるかどうか、この記事では、レーザー溶接機がエネルギー貯蔵の未来をどのように形作っているかを包括的に見ていきます。
リチウムイオン電池用レーザー溶接機とは?
リチウムイオン電池用のレーザー溶接機は、集束レーザービームを使用してバッテリー部品を高精度で接合する精密工具です。これにより、バッテリーの性能と安全性に不可欠な強力で汚染のない溶接が保証されます。これらの機械は、銅、アルミニウム、ニッケルなどの熱に弱い材料を取り扱うことができるため、バッテリーセル、タブ、バスバーの組み立てに広く使用されています。
主な利点は次のとおりです。
- 最小熱影響部(HAZ)–近くのバッテリー材料の損傷を防ぎます。
- 非接触プロセス– デリケートな部品への機械的ストレスを軽減します。
- 高い再現性–大量生産のための均一な溶接を保証します。
電気自動車(EV)、家電製品、エネルギー貯蔵などの業界では、効率的で高品質なバッテリー製造のためにこの技術が利用されています。
レーザー溶接機の主なコンポーネントは何ですか?
レーザー溶接機は、正確で効率的な操作を保証するいくつかの重要な部品で構成されています。
- レーザー光源・レーザービーム(ファイバー、CO₂、Nd:YAG)を発生させます。
- オプティクスシステム–レーザーを焦点を合わせて方向付けるためのレンズとミラーが含まれています。
- モーションプラットフォーム–レーザーヘッドまたはワークピース(CNCステージ、ロボットアームなど)の動きを制御します。
- 冷却システム–レーザー光源に最適な温度を維持します。
- 制御ソフトウェア–溶接パラメータ(電力、速度、パルス周波数)をプログラムします。
- 監視センサー–溶接品質をリアルタイムで検出します(CCDカメラ、パイロメーターなど)。
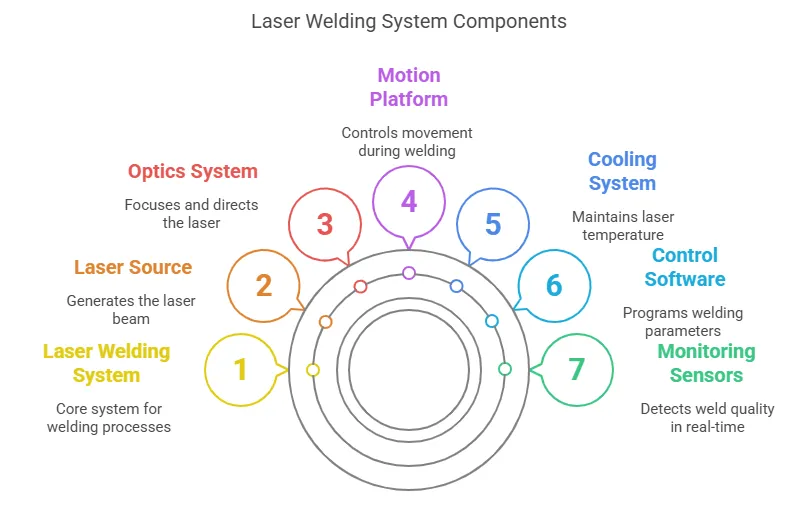
各コンポーネントは、リチウムイオン電池製造の一貫した高速溶接を実現するために重要な役割を果たします。
ファイバーレーザーがリチウムイオン電池の溶接に最も使用されているのはなぜですか?
ファイバーレーザーは、CO₂レーザーやNd:YAGレーザーと比較して優れた性能を発揮するため、リチウムイオン電池の溶接を支配しています。理由は次のとおりです。
- より高い効率・電気エネルギーの30〜50%をレーザー光に変換します(CO₂レーザー:~10%)。
- 精度–薄いバッテリー箔の微細な溶接のために、より小さな焦点(10〜50μm)を提供します。
- 柔軟性–銅やアルミニウムなどの反射金属と互換性があります。
- 低メンテナンス–可動部品のないソリッドステート設計により、ダウンタイムが短縮されます。
さらに、ファイバーレーザーは以下をサポートします。
✔ パルスモードまたは連続波(CW)モードにより、さまざまなアプリケーションに対応
✔大量生産のための高速溶接(最大数十00mm/s)。
レーザー溶接は、円筒形、ポーチ、および角形セルアセンブリでどのように使用されますか?
レーザー溶接は、カスタマイズされたアプローチでさまざまなリチウムイオン電池形式に適応します。
円筒形セル(例:18650、21700)
-
ステップバイステップのプロセス:
- カソード/アノードタブをセル端子に溶接します。
- 集電体をバッテリーキャップに結合します。
- 気密溶接でケーシングをシールします。
パウチセル
- 極薄箔は、ピアシングを避けるために低電力パルスを必要とします。
- タブ溶接(Al/Cu)は、電解液の漏れを防ぐ必要があります。
プリズムセル
- レーザー溶接されたバスバーは、モジュール内の複数のセルを接続します。
- 堅牢なケーシング溶接により、構造的な完全性が確保されます。
各フォーマットでは、過熱や変形を防ぐために、特定のレーザーパラメータ(波長、パルス幅)が必要です。
レーザー溶接リチウム電池のクリーンルーム要件は何ですか?
レーザー溶接リチウムイオン電池は、汚染を避けるために制御された環境で行われることがよくあります。重要な要件は次のとおりです。
- ISOクラス5–8クリーンルーム–粒子>0.3〜0.5μmをろ過します。
- 温湿度制御– 20〜25°C、<1%のRH変動を維持します。
- 不活性ガスシールド– アルゴン/窒素は溶接中の酸化を防ぎます。
なぜそれが重要なのか:
- ほこりや湿気は、溶接部が弱くなったり、短絡したりする可能性があります。
- 安定した条件により、再現性のある溶接品質が保証されます。
レーザー溶接リチウムイオン電池の一般的な検査方法は何ですか?
品質検査により、リチウムイオン電池の製造における信頼性の高い溶接が保証されます。次の3つの主要な方法が使用されます。
-
プルテスト
- 破損するまで引張力を加えることで溶接強度を測定
- 最小要件:銅タブの場合は50N、アルミニウムの場合は30N
- なぜ重要なのか:使用中に故障する可能性のある弱いジョイントを特定
-
クロスセクション分析
- ステップバイステップのプロセス:
- 溶接ジョイントの切断
- ポーランド語サンプル
- 顕微鏡で調べる
- 明らかになる:浸透深さ、細孔形成、熱影響部
- ステップバイステップのプロセス:
-
X線CTスキャン
- 内部溶接構造の非破壊3Dイメージング
- 検出:表面検査では見えないボイド、亀裂、ミスアライメント
- 一般的な解像度:バッテリーアプリケーション用の5〜20ミクロン
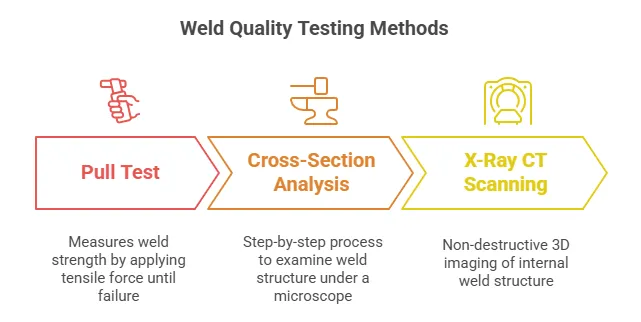
レーザー溶接機を使用する際にオペレーターの安全を確保する方法
レーザー溶接には、厳格な安全対策が必要ないくつかの危険があります。
必須の安全装置:
- レーザーゴーグル特定の波長のOD4+定格付き
- 耐火服火花に対する保護のため
- ヒュームエクストラクター金属蒸気を除去する
機械安全機能:
✔ ドアが開いたときにレーザーを無効にするインターロック
✔手の届くところに非常停止ボタン
✔違反すると動作を停止するライトカーテン
✔発砲前の可聴/視覚警告システム
なぜこれらが重要なのか:
- クラス4レーザーは、ミリ秒単位で永久的な眼の損傷を引き起こす可能性があります
- 反射性金属は、漂遊ビームの危険性を高めます
- 適切なトレーニングにより、潜在的な事故の90%が減少します
定期メンテナンススケジュールには何を含めるべきですか?
定期的なメンテナンスにより、コストのかかるダウンタイムを防ぎ、溶接品質を確保します。
デイリータスク:
- 糸くずの出ないワイプと承認された溶剤で光学部品を清掃
- ガス供給圧力(通常は10〜20 psi)を確認します
- 冷却システムの動作確認
ウィークリータスク:
- レーザー出力キャリブレーションの実行
- フォーカスレンズに損傷がないか調べます
- 安全インターロックのテスト
月間タスク:
- フル光路アライメント
- モーションシステム潤滑
- バックアップパラメータの設定
早急な対応が必要な重大な兆候:
- レーザー出力が10%低下
- 溶接中のスパッタの増加
- 不規則なビームプロファイル
レーザー溶接をバッテリーセルのスタッキングおよび自動化ラインと統合する方法
現代のバッテリー生産には、シームレスな統合が必要です。
主な統合ポイント:
-
マテリアルハンドリング
- バッテリータブの自動フィーダー
- 正確な部品配置のためのビジョンガイドロボット
-
プロセスの同期
- スタッキングマシンと同期したレーザートリガー
- パラメータを調整するためのリアルタイムの品質フィードバック
-
データトラッキング
- 各バッテリーセルの溶接ログ(時間、電力、場所)
- QRコード/MESシステムによるトレーサビリティ
統合が重要な理由:
- 手作業による取り扱いを70%削減
- 生産速度を毎秒1〜2セルに向上
- インラインカメラによる100%溶接検査を実現
この記事では、現代のバッテリー製造における重要なツールであるリチウムイオン電池用のレーザー溶接機について詳しく説明します。レーザー光源、光学システム、モーションプラットフォーム、冷却システム、制御ソフトウェア、監視センサーなど、これらの機械の主要コンポーネントを分解し、それらがどのように連携して正確で効率的な溶接を実現するかを説明します。また、この記事では、ファイバーレーザーが、その高効率、精度、柔軟性、および低メンテナンスのおかげで、業界で好まれる選択肢である理由も強調しています。さらに、レーザー溶接が円筒形、ポーチ、および角形のセルアセンブリにどのように適合しているかを探り、クリーンルームの要件について説明し、一般的な検査方法について概説します。安全対策と定期的なメンテナンスのヒント、およびレーザー溶接と自動生産ラインの統合についても説明します。全体として、この記事では、最新のバッテリー製造の品質、安全性、およびスケーラビリティを確保する上で、リチウムイオン電池用のレーザー溶接機の重要な役割を強調しています。