In the complex charging and discharging conditions of lithium-ion batteries during actual operation, although the battery management system can help achieve normal operation as much as possible, mechanical abuse, electrical abuse, and thermal abuse can still occur during overcharging, overdischarging, overtemperature, and other special situations. These abuses can lead to rapid degradation of battery performance, resulting in internal short circuits and ultimately causing thermal runaway safety issues.
This article conducts a systematic study on the internal short circuit of lithium-ion batteries, focusing on four aspects: internal short circuit principles, induced experimental methods, internal short circuit identification methods, and preventive measures.
By conducting research in these areas, this article provides insights into the identification methods and preventive measures for internal short circuits in lithium-ion batteries. This information can be valuable for the safety protection and application of lithium-ion batteries.
1 Research on internal short circuit mechanism
The triggering conditions for internal short circuits can be classified into three categories: mechanical abuse, electrical abuse, and thermal abuse. Mechanical abuse involves actions such as needle puncture and compression, which cause mechanical deformation of the battery and partial rupture of the separator, leading to an internal short circuit. Electrical abuse results in lithium plating and dendrite growth, which bridge the gaps in the separator and create a connection between the positive and negative electrodes, causing an internal short circuit. Thermal abuse occurs when high temperatures cause significant shrinkage and collapse of the separator, leading to an internal short circuit. When an internal short circuit occurs in a lithium-ion battery, it generates high current and a significant amount of localized heat, ultimately resulting in thermal runaway.
Internal short circuits can occur throughout the entire lifecycle of a battery, and their development and evolution can be divided into three stages: early stage, middle stage, and late stage, as shown in Table 1.
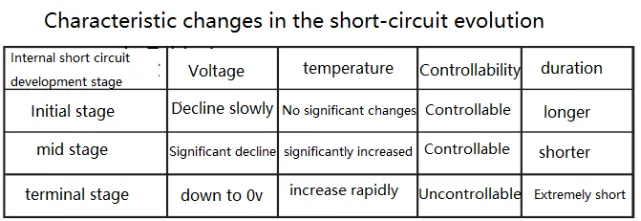
During the early stage of an internal short circuit, the voltage drop caused by the short circuit is relatively slow, and the heat generated is minimal, which can be dissipated by the cooling system. As a result, there is no significant change in battery temperature during this stage. The early stage can last for a long time and is difficult to detect.In the middle stage of an internal short circuit, the voltage drop becomes significant, and the heat generated accumulates due to inadequate dissipation. This leads to a noticeable increase in battery temperature. The middle stage is relatively short in duration, but its characteristics are more pronounced, making it easier to identify.In the late stage of an internal short circuit, the battery experiences a widespread short circuit, causing the voltage to drop to 0V. A large amount of heat is generated instantaneously, resulting in thermal runaway of the battery. The late stage is very short in duration and cannot be interrupted once it occurs.The characteristic changes during the evolution of an internal short circuit are summarized in Table 1.
2. Analysis of internal short circuit identification method
To prevent the development of internal short circuits in lithium-ion batteries to the late stage where they become uncontrollable and result in thermal runaway, researchers have long been devoted to the study of accurate methods for identifying internal short circuits during the early stages. Currently, the methods for identifying internal short circuits can be categorized into the following five types:
- Deviation identification based on measured data: This method requires the establishment of a reliable battery state prediction model. Real-time measured values of parameters such as voltage and temperature during battery charging and discharging are compared and analyzed with the predicted values from the model. If the calculated deviation exceeds the allowable range of error, it is determined that an internal short circuit has occurred. However, since the changes in characteristic parameters such as battery voltage and temperature are not significant during the early stage of an internal short circuit, this method has limited effectiveness in identifying early-stage internal short circuits and cannot identify internal short circuits in parallel battery packs.
- Voltage signal anomaly identification method: This method is based on the principle that ceramic separator-based batteries experience an abnormal voltage drop and recovery phenomenon during an internal short circuit. By detecting whether the battery voltage signal exhibits abnormal voltage drop and recovery during the battery charging and discharging process, the occurrence of an internal short circuit can be determined. However, this method can only identify internal short circuits in specific types of batteries, specifically those with porous protective material-coated separators. Therefore, it has limitations and can only be applied to the identification of internal short circuits in series-connected battery packs of specific battery types.
- Battery self-discharge identification method: An internal short circuit in a battery inevitably leads to abnormal self-discharge processes that exceed the normal range. By comparing the voltage before and after a period of battery rest or using methods such as benchmark constant voltage sources, the presence of abnormal self-discharge processes can be detected. If such processes are detected, it is determined that an internal short circuit has occurred. However, since this method requires the battery to be at rest and in a non-operational state, it cannot be used for real-time identification during battery operation or for identifying internal short circuits in parallel battery packs.
- Battery consistency identification method: Based on the assumption that battery cells within a battery pack exhibit consistency, this method involves monitoring parameters such as voltage, capacity, and remaining charge of individual battery cells within the same battery pack. If a certain battery cell’s parameters deviate significantly from the normal parameters of other cells, thereby disrupting the overall consistency of the battery pack, it is determined that the battery cell has experienced an internal short circuit. However, since the changes in characteristic parameters such as battery voltage and capacity are not significant during the early stage of an internal short circuit, this method has limited effectiveness in identifying early-stage internal short circuits and cannot identify internal short circuits in parallel battery packs.
- Special circuit identification method: This method involves detecting parameters such as voltage and current in a symmetric ring circuit topology. If any changes in the symmetry of the circuit parameters are observed, the location of the battery cell experiencing an internal short circuit can be accurately determined. This method addresses the high-precision identification of internal short circuits in parallel battery packs and enables estimation of the internal resistance. However, it has drawbacks such as high equipment cost and potential impact on the dynamic consistency of the battery pack.
3. Internal short circuit suppression measures
The factors that can cause internal short circuits in batteries can be broadly categorized into two types: battery materials and manufacturing processes, and battery design and usage. Here is a summary of methods to inhibit and prevent the occurrence of internal short circuits from these two aspects:
3.1 Battery materials and processes
The methods to inhibit and prevent internal short circuits can primarily be achieved through several aspects, including improvements in separator materials, electrolyte materials, electrode coatings, and production processes to reduce manufacturing defects.
By using high-temperature-resistant and low self-discharge rate ceramic separators, as well as flame-retardant electrolytes or ionic liquid electrolytes, it is possible to effectively inhibit dendrite growth and reduce the risk of internal short circuits. By applying low-conductivity coatings or materials with a positive temperature coefficient to the current collectors or electrodes of battery cells, it is possible to effectively reduce the internal short circuit current and heat generation during an internal short circuit, thereby lowering the probability of battery thermal runaway. Optimizing the production processes for battery cells, separators, and other materials, including impurity removal processes, can help filter out metallic impurities, prevent irreversible side reactions between metallic impurities and the electrolyte, and reduce the risk of metal particles puncturing the separator and causing internal short circuits. Additionally, employing advanced detection techniques to assess the integrity of the internal structure, manufacturing precision, and electrode alignment within the battery can help mitigate potential risks of internal short circuits.
3.2 Battery design and use
In terms of battery software design, implementing a Battery Management System (BMS) with appropriate battery warning and safety control strategies allows for real-time monitoring of individual battery cell states. This enables timely detection of the location of internal short circuits and prompt mitigation of any safety hazards. Reducing the risk of internal short circuits caused by high battery loads can be achieved through the design of cell redundancy and balancing during charging and discharging processes.
Regarding battery hardware design, the implementation of layered fuses such as cell fuses, module fuses, battery pack fuses, and vehicle load fuses allows for timely disconnection of the circuit affected by an internal short circuit. This helps prevent the further development of an internal short circuit. Additionally, a well-designed internal cooling system enhances heat dissipation capability, thereby preventing thermal runaway caused by excessive heat that can lead to electrode, electrolyte, and separator decomposition reactions. Furthermore, a properly designed internal heating system can preheat the battery to an appropriate operating temperature during low-temperature charging, avoiding the risk of thermal runaway caused by dendrite penetration through the separator during low-temperature charging.