锂沉淀、电极表面钝化膜增厚、可逆锂的损失以及活性材料结构的降解都会导致锂离子电池的使用寿命缩短。其中,负极是导致电池容量衰减的主要因素。本文总结了电池使用过程中负极衰减的主要原理,并提出了几种减少容量退化的方法。
电池容量退化的机制已被广泛研究和报道。影响电池容量退化的主要因素包括:主要因素是电极表面侧反应引起的可逆锂量减少。次要因素包括活性材料的减少,例如金属溶解、结构损伤和材料相变,以及电池阻抗的增加。负极与这些降解机制中的许多影响因素有关。
1.负极衰变机理研究进展
碳材料,尤其是石墨,是锂离子电池中使用最广泛的负极材料。虽然其他负极材料,如合金材料和硬碳材料也被广泛研究,但研究重点主要是控制活性材料的形态和改善性能,而较少强调分析容量衰减的机制。因此,负极衰变机理的研究主要集中在石墨材料上。
电池容量的衰减包括存储引起的衰减和使用过程中的衰减。存储诱导的衰变通常与电阻化学性能参数(如阻抗)的变化有关。在使用过程中,除了电化学性能的变化外,还存在机械应力变化和析锂现象。
1.1负极/电解质界面的变化
对于锂离子电池,电极/电解质界面的变化被认为是负极衰减的主要原因之一。在初始充电过程中,电解液在负极表面减少,形成稳定的保护性钝化膜,称为固体电解质界面(SEI)膜。然而,在锂离子电池的后续储存和使用过程中,负极/电解质界面可能会发生变化,从而导致性能下降。
1.1.1 SEI薄膜的增厚/成分变化
电池使用过程中电源性能的逐渐下降主要与电极阻抗的增加有关。电极阻抗的增加主要是由于固体电解质界面(SEI)膜的增厚及其成分和结构的变化引起的。
由于SEI膜不具备真正固态电解质的特性,溶剂化锂离子仍可通过电解质中存在的其他阳离子、阴离子、杂质和溶剂分子在SEI膜中迁移。因此,在长时间循环或储存过程中,电解液仍可在负极表面发生分解反应,导致SEI膜增厚。
同时,当负极在循环过程中发生膨胀和收缩时,表面SEI薄膜可能会破裂并产生新的界面。这些新界面继续与溶剂分子和锂离子反应,从而形成新的SEI膜。随着这些表面反应的进行,负极表面会形成电化学惰性表面层,将一部分负极材料与整个电极隔离开来,并导致容量损失。
如图1所示,长时间循环后,负极表面的SEI膜明显增厚。
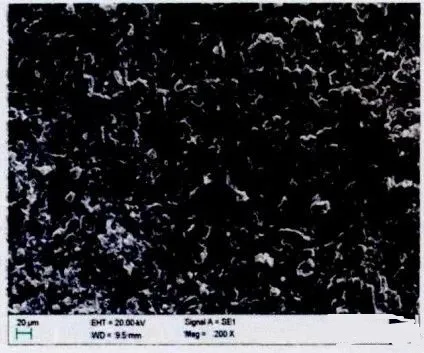
SEI薄膜的成分在热力学上不稳定,并在电池系统内发生溶解和再沉积的动态变化。在某些条件下,例如高温、暴露于HF或薄膜中存在金属杂质,SEI薄膜的溶解和再生会加速,从而导致电池中的容量损失。特别是在高温下,SEI薄膜内的有机成分可以转化为更稳定的无机成分(如Li2CO3和LiF),从而导致SEI薄膜的离子电导率降低。
研究发现,不同类型的石墨材料表现出不同的储存性能,合成石墨在高温下的性能优于天然石墨。随着储存时间的增加,合成石墨中的锂含量保持稳定,而天然石墨中的锂含量呈线性下降趋势。通过使用SEM和傅里叶变换红外光谱(FTIR)进行分析,观察到在高温储存过程中,随着储存时间的延长,天然石墨表面的Li2CO3和LiOCOOR含量显着增加。SEI膜的增厚主要是由于电解质相互作用在负极表面发生的副反应引起的。另一方面,合成石墨的表面结构和形貌相对保持不变。
1.1.2电解质分解和沉积
电解质减少包括溶剂减少、电解质减少和杂质减少。电解液中的常见杂质包括氧、水和二氧化碳。在电池的充放电过程中,电解液在负极表面发生分解反应。这些反应的主要产物包括碳酸锂、氟化物和其他化合物。随着循环次数的增加,分解产物积累并覆盖负极表面,阻碍了锂离子的插层和脱嵌,导致负极的阻抗增加。
1.1.3锂沉淀
由于石墨基材料与锂的紧密插层电位,如果在充电过程中发生金属锂的沉积或锂枝晶的生长,锂与电解液之间的后续反应将加速电池性能的下降。大量的锂沉淀会导致内部短路和热失控。增加锂沉淀风险的因素包括低温充电、负极相对于正极的过量较低、电极尺寸不匹配(正极与负极边缘重叠)和电位效应(局部极化、电极厚度和孔隙率的差异)。
石墨材料内部的无序程度和电流分布的不均匀性都会影响负极表面的锂沉淀。在石墨嵌入锂的第三和第四阶段,材料的无序导致电极内电荷分布不均匀,从而导致树枝状沉积物的形成。隔膜和负极之间沉积物的增长与温度和电流密度密切相关。随着温度的升高和充电速率的加快,反应速率加快,金属锂沉积在负极上。通过观察电池放电曲线中的电压平台和库仑效率的降低,可以确定锂沉淀的发生。
目前,研究主要集中在通过各种方法提高负极的性能,例如改进负极系统和通过加入添加剂来优化电解质系统以抑制锂沉淀。在石墨表面涂覆Sn和碳可以提高负极的电化学循环性能。石墨表面Sn的存在降低了SEI膜的内阻和低温下的电极极化。此外,还可以通过修改负极材料的表面来提高性能。在空气中氧化石墨会增加表面积和活性边缘位点的数量,导致孔隙率增加和粒径减小,从而减少因电荷分布不均匀而导致的锂沉淀的发生。
AsF6的添加提高了负极在高温下的稳定性,抑制了金属锂的形成,并阻止了LiPF6的分解。此外,负极片制备阶段的机械辊压可以减小孔径,减少电荷分布的不均匀性,增强电池的可逆容量。
1.2负极活性材料的变化
在电池性能逐渐恶化的过程中,石墨的有序结构逐渐被破坏。在锂离子电池中,高速率循环会产生锂离子的浓度梯度,导致材料内产生机械应力场。结果,负极的晶格发生变化,负极的初始层状结构逐渐变得无序。然而,这些结构性变化并不是电池性能下降的主要原因。降解可以表现为锂沉淀或SEI膜的变化。然而,在此过程中,负极的粒径和晶格参数不会发生显着变化。
石墨颗粒的可逆能力受其取向和形态的影响。例如,由于无序颗粒之间存在新的界面,可能会发生锂离子/电解质反应,从而使锂离子更难插层。因此,无序石墨颗粒具有较低的可逆能力。与球形颗粒相比,鳞片石墨在高速率下表现出更高的比容量。尽管负极结构在降解过程中不会改变,但菱面体/六边形结构的比例可以变化。六边形结构的增加降低了第一级和第三级锂离子插层的法拉第效率,从而降低了负极的可逆容量。因此,提高菱面体/六边形结构的比例可以增强可逆能力。
1.3负极结构的变化
石墨材料的粒度对负极的性能有重大影响。较小的粒径可以缩短石墨颗粒之间的扩散路径,有利于高倍率充放电。然而,小尺寸材料具有较大的比表面积,这可能导致高温下的锂消耗量增加,从而导致负极的不可逆容量增加。因此,石墨电极的热稳定性主要与石墨材料的粒度有关。
石墨电极片的孔隙率与负极的可逆容量有关。孔隙率的增加导致石墨和电解质之间的接触面积变大,从而导致界面反应增加和可逆容量降低。在电池的长期循环过程中,石墨电极的压实密度会影响性能退化。高压实密度可以降低电极的孔隙率,减少石墨与电解质的接触面积,从而提高可逆容量。此外,在120°C以上的温度下,由于SEI薄膜的热分解,高密度负极材料会产生更多的热量。