电极片的涂覆通常是指将充分混合的浆料均匀地涂在集流体上并干燥浆料中存在的有机溶剂的过程。涂层质量对电池容量、内阻、循环寿命和安全性有重大影响。确保电极片的均匀涂层至关重要。涂布法的选择和控制参数对锂离子电池的性能起着重要作用。这主要体现在以下几个方面:
1)衣干燥温度控制:涂布时干燥温度过低(相关机器),不能保证电极片完全干燥。如果温度过高,电极片内部的有机溶剂可能会蒸发得太快,导致电极片表面涂层上出现龟块、开裂、脱落等;
2)涂层表面密度:如果涂层表面密度太小,电池容量可能无法达到标称容量。如果涂层表面密度太高,很容易造成成分的浪费。严重时,如果正极容量过大,由于锂的沉淀形成锂枝晶,刺穿电池隔膜,造成短路,造成安全隐患;
3)涂层尺寸:如果涂层尺寸太小或太大,电池内部的正极可能无法被负极完全覆盖。在充电过程中,锂离子从正极嵌入并移动到未被负极完全覆盖的电解液中。介质,正极片的实际容量无法有效利用。严重时,电池内部会形成锂枝晶,很容易刺穿隔板,造成电池内部电路;
4)涂层厚度:涂层厚度太薄或太厚都会对后续的电极片轧制过程产生影响,无法保证电池电极片的性能一致性。
此外,电极片涂层对电池的安全具有重要意义。涂布前,必须做好5S工作,确保在涂布过程中没有颗粒、碎屑、灰尘等混入电极片。如果混入杂物,会导致电池内部发生微短路,严重时,电池可能会着火爆炸。
1. 涂装设备和涂装工艺选择
广义涂布工艺包括:放卷→拼接→拉→张力控制→涂布→干燥→对中→张力控制→纠偏→收卷等工序。涂布工艺复杂,影响涂布效果的因素很多,如:涂布设备的制造精度、设备运行的流畅性、涂布过程中动态张力的控制、干燥过程中的风量、温度控制曲线都会影响涂布效果,因此,选择合适的涂层工艺非常重要。
通常,在选择涂布方法时需要考虑以下几个方面,包括:涂布层数、湿涂布的厚度、涂布液的流变特性、所需的涂布精度、涂布支撑或基材、布料速度等。
除了上述因素外,还必须结合电极片涂层的具体条件和特性。锂离子电池电极片的涂层特性是:(1)双面单层涂层;(2)浆料湿涂较厚(100~300μm);(3)浆料为非牛顿高粘度流体;(4)对电极片的涂布精度要求高,与薄膜涂布精度相似;(5)涂层支撑为厚度为10至20 μm的铝箔和铜箔;(6)与薄膜涂布速度相比,电极片涂布速度不高。考虑到以上因素,一般实验室设备常采用刮刀式,消费类锂离子电池多采用辊涂转移式,动力电池多采用狭缝挤出法。
SCraper涂层工作原理如图1所示。铝箔基材通过涂布辊并与浆料槽直接接触。过量的浆料被施加到铝箔基材上。当基材通过涂布辊和刮刀之间时,刮刀和基材之间的间隙决定了涂层的厚度,同时,多余的浆料被刮掉并回流,从而在基材表面形成均匀的涂层。刮刀类型主逗号刮刀。逗号刮刀是涂布头中的关键部件之一。一般沿母线在圆辊表面加工成逗号状的切削刃。该刮刀具有高强度和硬度,易于控制涂布量和涂布精度。适用于高固含量、高粘度的浆料。
辊涂转移式:涂布辊的旋转驱动浆料,通过逗号刮刀间隙调节浆料转移量,利用后辊和涂布辊的旋转将浆料转移到基材上。该过程如图2所示。辊道转移涂布由两个基本过程组成:(1)涂布辊的旋转带动浆料通过计量辊间隙,形成一定厚度的浆料层;(2)一定厚度的浆料层通过与涂布辊的相反方向,在背衬辊的旋转下,将浆料转移到箔上,形成涂层。
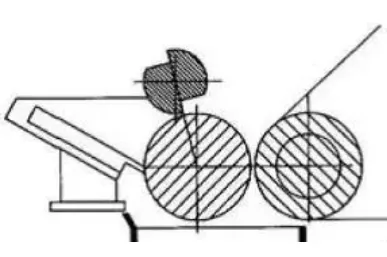
辊涂刀片转移涂布工艺示意图
狭缝模头涂布:作为一种精确的湿法涂布技术,狭缝模头涂布的工作原理如图3所示。其工作原理是以特定压力和流速将涂布液通过狭缝模头的间隙挤出,并将其转移到基材上。与其他涂层方法相比,狭缝模头涂层具有多种优点,例如涂层速度快、精度高和湿厚度均匀。涂层系统是封闭的,可防止污染物在涂层过程中进入,从而提高浆料的利用率并保持稳定的浆料性能。它允许同时进行多层涂层。此外,狭缝模头涂布可以适应各种浆料粘度和固体含量,与转移涂布工艺相比,其适应性更强。
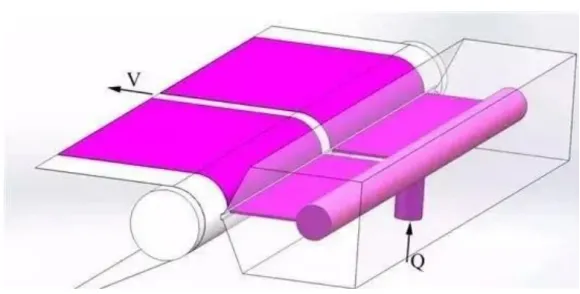
2. 涂层缺陷及影响因素
减少涂层缺陷、提高涂层质量和产量以及降低成本是研究涂层工艺时需要考虑的重要方面。涂布过程中经常出现的常见问题包括头部粗尾薄、两侧厚边、斑点缺陷、表面粗糙度和箔片暴露。
头尾厚度可以通过控制涂布阀或间歇阀的打开和关闭时间来调整。通过调整浆料特性、涂层间隙和浆料流速,可以改善厚边的问题。表面粗糙、不平整和划线可以通过稳定铝箔材料、降低速度和调整气刀的角度来解决。
基材-浆料
浆料基本物理性能与涂层的关系:在实际过程中,浆料的粘度对涂层效果有一定的影响。当选择粘合剂类型时,电极原材料、浆料比例和制备浆料的粘度也会发生变化。不同。当浆料的粘度过高时,涂布往往不能连续稳定地进行,涂布效果也受到影响。
涂布液的均匀性、稳定性、边缘和表面效果受涂布液流变性能的影响,流变性能直接决定涂层的质量。可采用理论分析、涂层实验技术、流体力学有限元技术等研究方法对涂层窗口进行研究。镀膜窗口是可以实现稳定镀膜并获得均匀镀膜的工艺操作范围。
基材–铜箔和铝箔
表面张力:铜铝箔的表面张力必须高于涂层溶液的表面张力,否则溶液将难以在基材上顺利铺展,导致涂层质量不佳。需要遵循的一个原则是,待涂溶液的表面张力应比基材的表面张力低5达因/厘米。当然,这只是粗略的。溶液和基材的表面张力可以通过调整基材的配方或表面处理来调节。两者的表面张力测量也应作为质量控制测试项目。
厚度均匀:在类似于刀片涂层的过程中,基材的厚度在整个宽度上不均匀,这将导致涂层厚度不均匀。因为在涂层过程中,涂层厚度由刮刀和基材之间的间隙控制。如果在基材的横向上有一个地方的基材厚度相对较低,则更多的溶液会通过该地方,涂层厚度会更厚,反之亦然。如果从测厚仪上看到基材的以下厚度波动,则最终涂层厚度波动也将显示相同的偏差。此外,横向厚度偏差也会导致绕组缺陷。所以为了避免这种缺陷,原材料的厚度控制非常重要。
静电:在涂装线上,当涂布展开并通过辊筒时,基材表面会产生大量静电。产生的静电很容易吸收空气和辊子上的灰层,造成涂层缺陷。在静电放电过程中,还会造成涂层表面出现类似静电的外观缺陷,更严重的情况下甚至可能引起火灾。如果冬天湿度低,涂装线上的静电问题会更加严重。减少此类缺陷的最有效方法是保持尽可能高的环境湿度,将涂装线接地,并安装一些防静电装置。
清洁:基板表面的杂质会导致一些物理缺陷,如突起、污垢等。因此,在基材的生产过程中,需要更好地控制原材料的清洁度。在线薄膜清洁辊是去除基材杂质的更有效方法。虽然不能去除膜上的所有杂质,但能有效提高原料质量,减少损失。
3.锂电池电极片缺陷图
- 锂离子电池负极涂层中的气泡缺陷
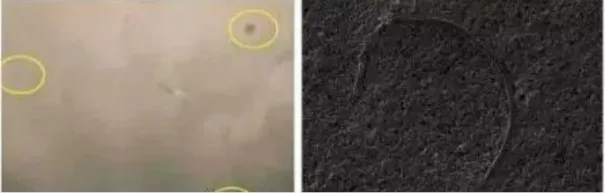
左图是带有气泡的负极板,右图是扫描电子显微镜的200倍放大倍率。在浆料混合、转移和涂布过程中,灰尘或长绒毛等异物混入涂布液中或落在湿涂层表面,涂层的表面张力受外力影响,产生分子间作用力。发生变化,浆料略微转移,干燥后形成中间较薄的圆形痕迹。
- 针孔
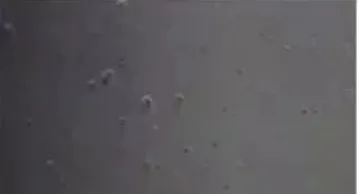
一是气泡的产生(搅拌过程、运输过程、涂层过程);气泡引起的针孔缺陷相对容易理解。湿膜中的气泡从内层迁移到薄膜表面,并在薄膜表面爆裂,形成针孔缺陷。气泡主要来自搅拌、涂装液体运输和涂装过程中涂料流动性差和流平性差,以及涂料中气泡释放不良。
- 划痕
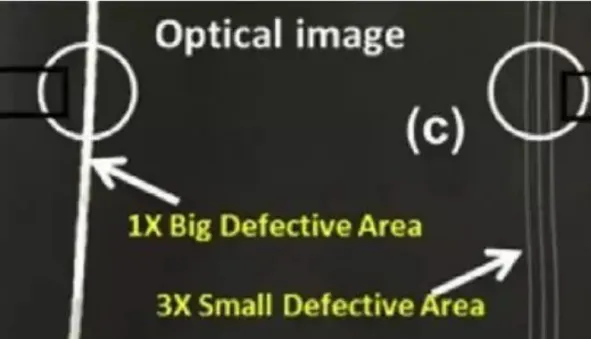
- 厚边
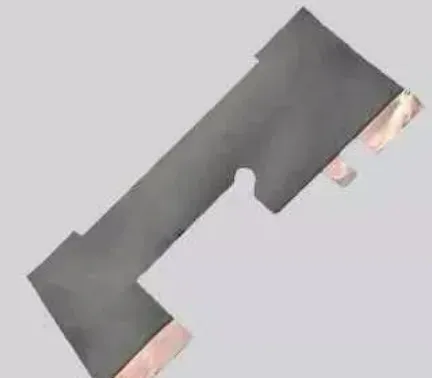
之所以出现厚边,是因为浆料的表面张力使浆料迁移到电极片边缘的未涂层区域,干燥后形成厚边。
- 负表面聚集体颗粒
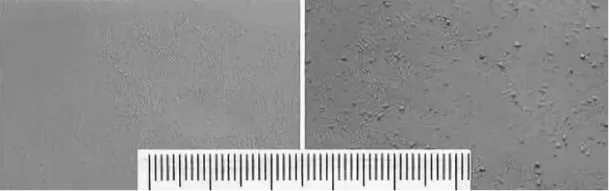
配方:球形石墨+ SUPER C65 + CMC +蒸馏水
使用不同混合工艺的两种不同电极膜的宏观外观:光滑的表面(左)和带有大量小颗粒的表面(右)。
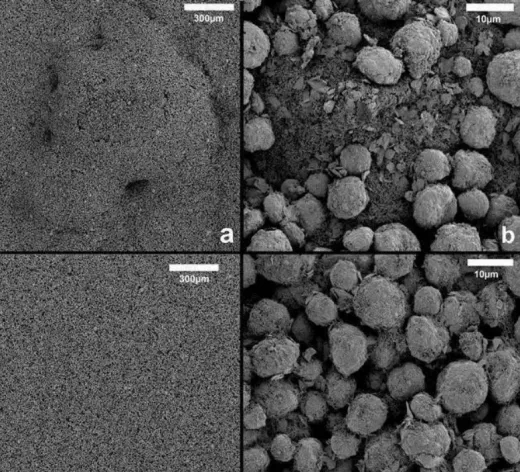
配方:球形石墨+超级C65 + CMC/SBR +蒸馏水
带有小颗粒(a和b)的电极膜表面的放大形态:导电添加剂的聚集,不完全分散。
光滑表面电极膜的放大形貌:导电添加剂分散良好且分布均匀。
- 正极表面聚集体颗粒
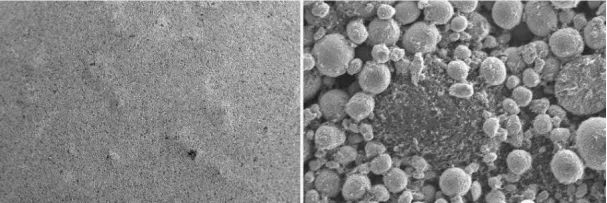
配方:NCA +乙炔黑+ PVDF+ NMP
在搅拌过程中,环境湿度过高,导致浆料呈果冻状,导电剂未完全分散,轧制后电极片表面有大量颗粒。
- 水系统电极片裂纹
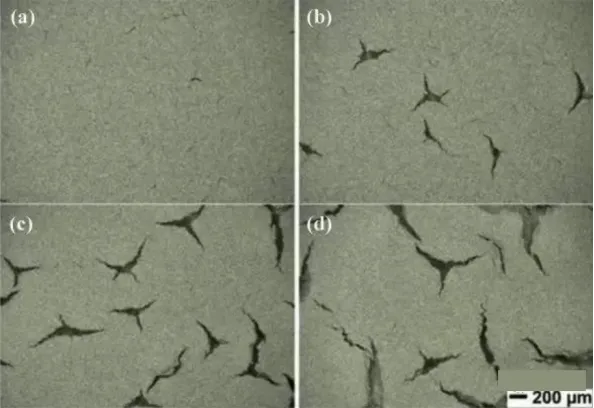
配方:NMC532/炭黑/粘合剂= 90/5/5 wt%,水/异丙醇(IPA)溶剂。
不同涂层面密度下电极膜表面裂纹的光学照片:(a) 15 mg/cm2、(b) 17.5 mg/cm2、(c) 20 mg/cm2和(d) 25 mg/cm2。较厚的电极膜更容易开裂。
- 电极片表面的缩孔
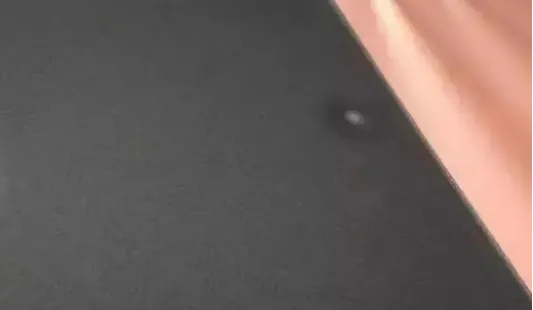
配方:片状石墨+ SP + CMC / SBR +蒸馏水
箔表面有污染物颗粒,颗粒表面湿膜中有低表面张力区。液膜在颗粒周围径向迁移,形成收缩点缺陷。
- 电极片表面有划痕

配方:NMC532 + SP + PVdF + NMP
在狭缝挤出涂布过程中,切削刃上存在大颗粒会导致电极片表面出现箔划痕。
- 涂层垂直条
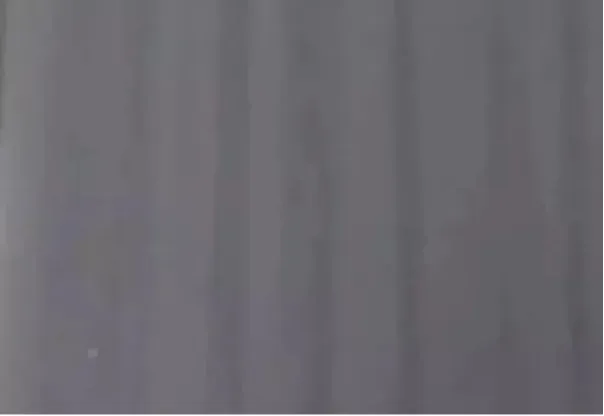
配方:NCA + SP + PVdF + NMP
在转移涂层的后期阶段,由于吸水,浆料的粘度增加。涂布过程接近涂布窗口的上限,导致浆料流平不良并形成垂直条纹。
- 电极片潮湿区域的滚动裂纹
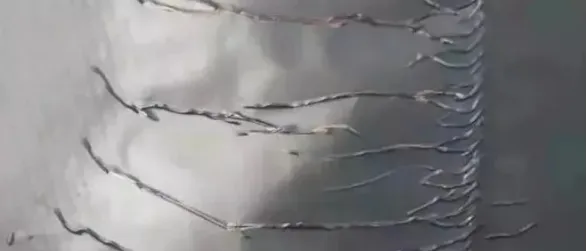
配方:片状石墨+ SP + CMC / SBR +蒸馏水
涂布时,电极片的中间区域没有完全干燥,涂层在轧制过程中迁移,形成条状裂纹。
- 电极片卷边皱纹
涂层过程中会形成厚边。轧制型会在涂层边缘产生皱纹。
- 负极分切涂层与箔分离
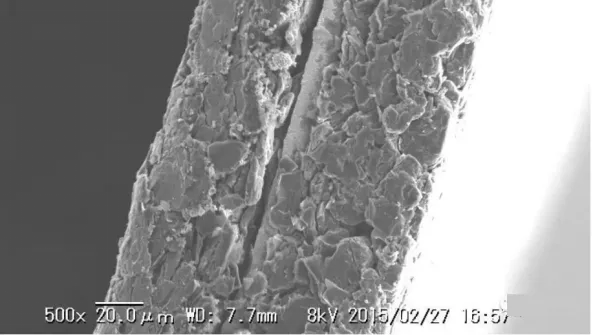
配方:天然石墨+乙炔黑+ CMC/SBR +蒸馏水,活性物质比例96%
当电极片盘被切开时,涂层与箔分离。
- 电极片分切毛刺
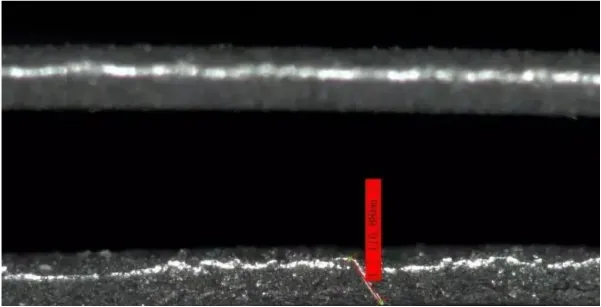
当正极盘被切开时,不稳定的张力控制会导致二次切割形成箔毛刺。
- 电极片狭缝波浪边
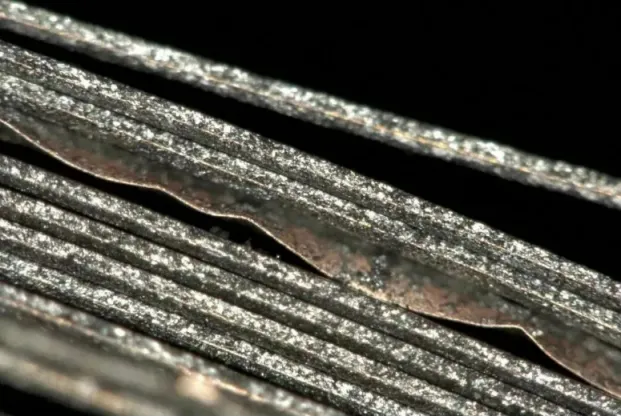
当切割负极盘时,由于刀具的重叠和压力不当,会形成波浪形边缘,并且切口的涂层会剥落。
- 其他常见的涂层缺陷包括:空气渗透、横波、垂直流、渗流、膨胀、水波纹等。
缺陷可能发生在加工的各个阶段:涂层的配方、基材的准备、涂层操作区域、干燥区、切割、分切、压延过程等。解决缺陷的一般逻辑方法如下:
优化从中试规模到生产的产品配方、涂层和干燥工艺。通过调整参数和变量找到最佳或更宽的工艺窗口。
实施质量控制措施和统计工具(例如统计过程控制,SPC)来控制产品质量。利用在线监控系统来确保稳定的涂层厚度,或采用视觉检查系统(Visual Systems)来检测表面缺陷。
当出现缺陷时,及时调整流程,避免缺陷再次发生。确定根本原因,分析流程变量,并相应地修改参数以纠正问题。
4. 涂层的均匀性
术语“涂层均匀性”是指涂层区域内涂层厚度或胶粘剂分布的一致性。涂层厚度或胶粘剂分布的一致性越好,涂层均匀性就越高,反之亦然。涂层均匀性没有标准化的指标,但可以通过涂层厚度或胶粘剂量在一定区域内各个点相对于该区域的平均涂层厚度或胶粘剂量的偏差或百分比偏差来衡量。它也可以通过一定区域内的最大和最小涂层厚度或粘合剂量之间的差异来衡量。涂层厚度通常以微米(μm)表示。
涂层均匀性用于评估特定区域内的整体涂层质量。然而,在实际生产中,我们通常更关心基材的横向(横机)和纵向(机方向)的均匀性。横向均匀性是指涂层宽度方向(或机器方向)的均匀性,而纵向均匀性是指涂层长度方向(或基材行进方向)的均匀性。
横向和纵向涂层误差的幅度、影响因素和控制方法存在显著差异。通常,基材(或涂层)宽度越宽,控制横向均匀性就越具有挑战性。根据多年的涂布操作实践经验,当基板宽度低于800mm时,通常比较容易保证横向均匀性。当基板宽度范围为1300毫米至1800毫米时,横向均匀性通常可以得到很好的控制,但需要相当水平的专业知识。然而,当基板宽度超过2000mm时,实现横向均匀性变得极具挑战性,只有少数制造商能够有效处理。另一方面,随着生产批量(即涂层长度)的增加,与横向均匀性相比,纵向均匀性可能成为更大的挑战或困难。