一个软包电池是指使用铝塑膜作为其包装材料的电芯。软包电池的制造工艺与方形电池不同,主要从卷绕阶段开始。制造过程的初始阶段通常相似。在锂离子电池封装方面,主要有两大类:软包电芯和金属壳电芯。金属外壳电池包括钢壳和铝壳,近年来,一些电池一直使用塑料外壳,也可以归类为这一类。
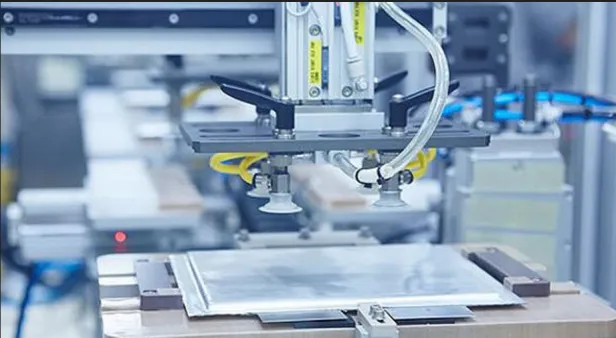
不同的外壳材料决定了包装方法。软包电池使用热包装,而金属外壳电池通常使用焊接(激光焊接).软包电池之所以能进行热封,是因为它们使用铝塑包装膜。
铝塑包装薄膜由横截面的三层组成:尼龙层、铝层和聚丙烯(PP)层。这三个层中的每一个都有自己的角色。首先,尼龙层保证了铝塑薄膜的形状,保证了薄膜在制造成锂离子电池之前不会变形。金属铝层用于防止水渗透。锂离子电池非常怕水。一般要求电极的水分含量在10-6左右,因此包装膜必须能够阻挡水蒸气的渗透。尼龙不防水,无法提供保护。金属铝在常温下与空气中的氧气反应,形成致密的氧化膜,防止水蒸气渗透,保护果冻卷内部。金属铝层还为铝塑料薄膜形成时的冲压提供了可塑性。PP的特点是在100摄氏度以上的温度下熔化并且具有粘性。因此,电池的热封主要依赖于PP层在封头加热的作用下熔融粘合在一起。然后取下密封头,降低温度以凝固和粘合。下图是铝塑包装膜的结构示意图。
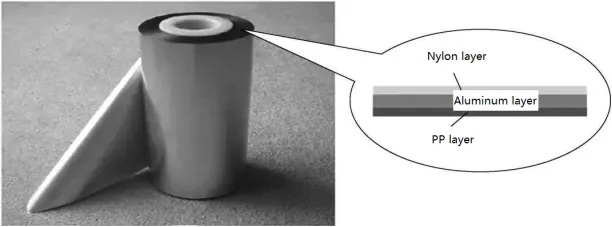
铝塑膜看起来很简单,但在实际操作中,要将三层材料均匀牢固地结合在一起并不是那么容易。不幸的是,优质的铝塑薄膜基本上是从日本进口的。国内的没有,但质量仍然需要提高。
- 冲孔
铝塑膜成型工艺是软包电池生产中的一种特殊制造技术。软包电池可根据客户要求设计成不同的尺寸。一旦确定了外部尺寸,就需要开发相应的模具来塑造铝塑薄膜。这种成型过程也称为“冲孔”,这意味着使用成型模具在加热的铝塑料薄膜上创建一个可以容纳果冻卷的空腔。下图说明了冲孔的概念。
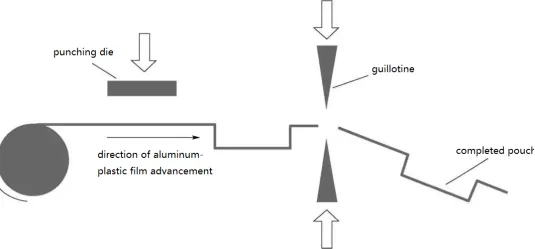
铝塑膜经过冲孔和切割成型后,通常称为“袋”。当电芯相对较薄时,通常会打出单腔,而当电芯较厚时,通常会打出双腔。这是因为一侧的过度变形会超过铝塑膜的变形极限,从而导致破裂。
- 顶部和侧面密封工艺
顶部密封工艺是袋装锂离子电池制造的第一步。顶部密封过程实际上包括两个步骤:顶部密封和侧面密封。首先,将果冻卷放入冲孔袋中。然后,将包装膜沿虚线位置折叠。下图说明了顶部密封的概念。
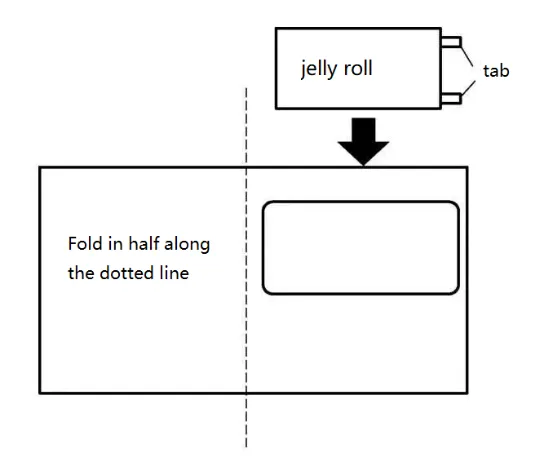
铝塑膜装入芯体后,需要对几个位置进行密封,包括顶部封口区、侧封区、第一封口区和第二封口区。下图是打包位置的示意图。
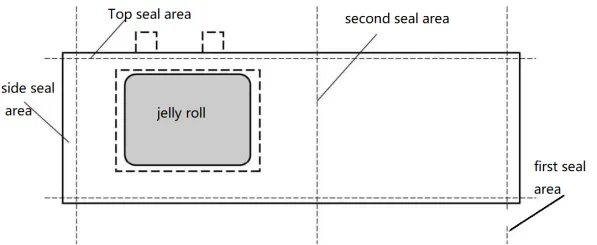
将果冻卷放入口袋后,将整个铝塑膜放入夹具中,并在顶部封口机中进行顶部封口和侧封。图6显示了该型号的顶部封口机,它配备了四个夹具。左侧工作站用于顶部密封,而右侧工作站用于侧面密封。在两个金属密封头下方,还有另一个底部密封头。在密封过程中,两个密封头被加热到一定温度(通常在180°C左右)并压在铝塑薄膜上。薄膜的PP层熔化并粘合在一起,完成密封过程。
对于顶部密封,目标是密封由金属制成的集流体(铝用于正极,镍用于负极)。如何用PP薄膜密封它们?这是通过集流体上称为“集流体胶粘剂”的小组件实现的。在密封过程中,集流体胶粘剂的PP层熔化并与铝塑薄膜的PP层粘合,形成有效的密封结构。下图说明了密封结构。
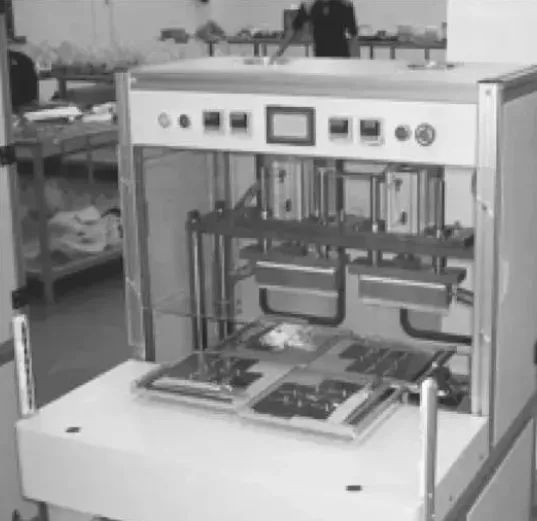
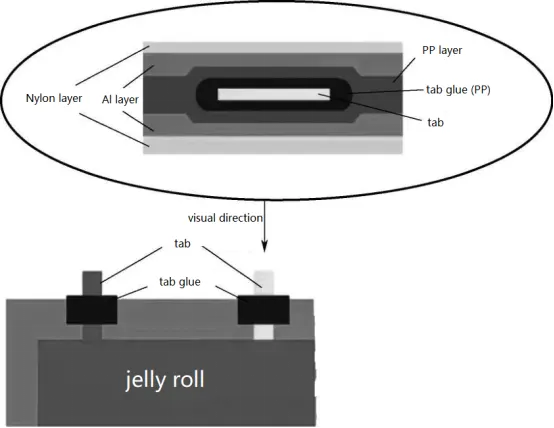
- 注射和预密封工艺
顶部密封过程后,软包电池需要进行X射线检查,以检查其果冻卷的平行度。然后,它进入干燥室去除水分。在干燥室中放置一段时间后,进入注射和预密封过程。
电池的顶部密封完成后,安全气囊侧只剩下一个开口。这个开口用于注射。在注射完成后,需要立即对安全气囊侧进行预密封,也称为“一次密封”。一旦完成第一次密封,理论上,电池的内部就与外部环境完全隔离。首封的密封原理与顶部密封相同。
- 静置、成型和夹具成型工艺
在注入和第一次密封过程之后,电池芯需要处于静态状态。根据具体的制造工艺,它可以进行高温静态存储或室温静态存储。静电储存的目的是让注入的电解质完全渗透到电极片中。静电存储后,电池单元可以形成。Formation是指电池的初始充电,但没有充电到最高工作电压,充电电流很低。形成的目的是在电极表面建立稳定的固体电解质界面(SEI)膜,相当于“活化”电池芯。在此过程中,会产生一定量的气体,这就是为什么在铝塑膜中预留了安全气囊的原因。一些制造工艺在化成过程中可能会使用固定装置,其中电池单元被夹在固定装置中(有时使用玻璃板和钢夹),然后放置在机柜中进行化成。这使得产生的气体可以完全挤压到相邻的安全气囊中,同时还可以改善形成后的电极界面。形成后,一些电池芯,尤其是较厚的电池芯,可能会因内应力而变形。因此,某些工厂在形成后可能会有夹具成型工艺,也称为夹具烘烤。
- 第二次密封过程
在形成过程中,会产生气体,因此有必要在进行第二次密封之前提取气体。在一些公司中,这个过程分为两个步骤:气体排放和二次密封。还有一个后续步骤,即切割安全气囊,但在这里我们将所有这些步骤统称为第二次密封。
在第二次密封过程中,使用分切刀刺穿安全气囊,同时产生真空。这允许提取安全气囊内的气体和一小部分电解液。然后,立即在第二个密封区域,使用密封头密封电池,确保其气密性。最后,切割密封电池以去除安全气囊,基本上形成一个袋状电池。第二次密封是锂离子电池的最终密封过程。
- 后续流程
在第二次密封过程中切割安全气囊后,电池进行修边和折叠。这包括将第一个密封件和第二个密封件边缘修剪成适当的宽度并折叠它们以确保电池的宽度不超过规定的限制。折叠过程后,电池可以进行容量分级,这本质上是确定电池是否满足最低要求容量的容量测试。原则上,所有电池在出厂前都需要进行容量分级,以确保容量不足的电池不会交付给客户。但是,在大批量电池生产中,一些公司可能会进行部分容量分级,以统计评估该批次的容量合格率。
容量分级后,容量合格的电池进行后续过程,包括目视检查、标签应用、边缘电压测试和极耳焊接等。这些流程可以根据客户要求进行调整。最后,电池经过出厂质量控制(OQC)并包装发货。