Uncellule de poche Fait référence à une cellule de batterie qui utilise un film aluminium-plastique comme matériau d’emballage. Le processus de fabrication des batteries de poche diffère de celui des batteries prismatiques, principalement à partir de l’étape de bobinage. Les premières étapes du processus de fabrication sont généralement similaires. En termes d’emballage de batteries lithium-ion, il existe deux catégories principales : les cellules de poche et les cellules à coquille métallique. Les cellules à coquille métallique comprennent les coquilles en acier et en aluminium, et ces dernières années, certaines cellules ont utilisé des coquilles en plastique, qui peuvent également être classées dans cette catégorie.
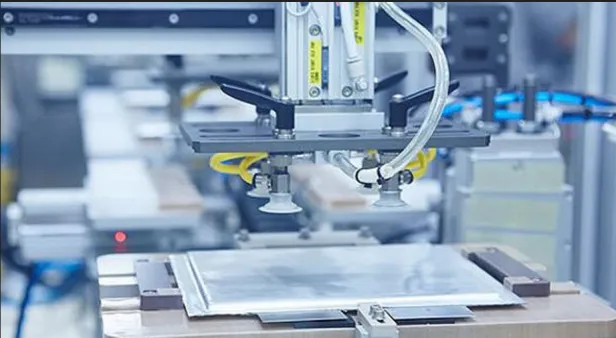
Différents matériaux de coque déterminent les méthodes d’emballage. Les batteries à pochette utilisent un emballage thermique, tandis que les batteries à boîtier métallique utilisent généralement des applications de soudage (Soudage au laser). La raison pour laquelle les batteries de poche peuvent être scellées thermiquement est qu’elles utilisent un film d’emballage en aluminium-plastique.
Le film d’emballage aluminium-plastique est composé de trois couches d’une section transversale : une couche de nylon, une couche d’aluminium et une couche de polypropylène (PP). Chacune des trois couches a son propre rôle. Tout d’abord, la couche de nylon assure la forme du film aluminium-plastique et garantit que le film ne se déformera pas avant d’être transformé en batterie lithium-ion. La couche métallique d’aluminium est utilisée pour empêcher l’eau de pénétrer. Les batteries lithium-ion ont très peur de l’eau. Généralement, la teneur en humidité de l’électrode doit être de l’ordre de 10-6, de sorte que le film d’emballage doit être capable de bloquer la pénétration de la vapeur d’eau. Le nylon n’est pas imperméable et ne peut pas fournir de protection. L’aluminium métallique réagit avec l’oxygène de l’air à température ambiante pour former un film d’oxyde dense, qui empêche la vapeur d’eau de pénétrer et protège l’intérieur du rouleau de gelée. La couche d’aluminium métallique fournit également la plasticité nécessaire au poinçonnage lorsque le film plastique d’aluminium est formé. La caractéristique du PP est qu’il fond à des températures de plus de 100 degrés Celsius et qu’il est collant. Par conséquent, l’étanchéité thermique des batteries repose principalement sur la fusion et le collage de la couche de PP sous l’action de chauffage de la tête d’étanchéité. Ensuite, la tête d’étanchéité est retirée et la température est réduite pour se solidifier et se lier. L’image ci-dessous est un schéma de la structure d’un film d’emballage en aluminium-plastique.
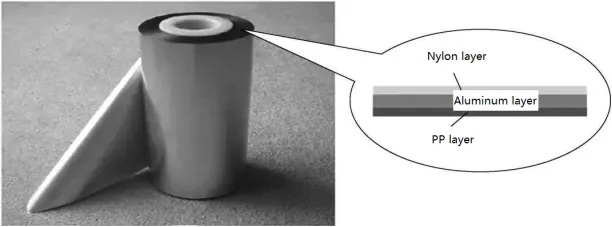
Le film plastique en aluminium semble très simple, mais dans la pratique, il n’est pas si facile de combiner les trois couches de matériaux uniformément et fermement ensemble. Malheureusement, les films aluminium-plastique de bonne qualité sont essentiellement importés du Japon. Les appareils nationaux ne sont pas disponibles, mais la qualité doit encore être améliorée.
- perforations
Le procédé de formage de film aluminium-plastique est une technique de fabrication spéciale dans la production de batteries à poche. Les cellules de poche peuvent être conçues en différentes tailles selon les exigences du client. Une fois les dimensions extérieures déterminées, des moules correspondants doivent être développés pour façonner le film aluminium-plastique. Ce processus de formage est également connu sous le nom de « trous de perforation », ce qui signifie utiliser le moule de formage pour créer une cavité sur le film aluminium-plastique chauffé qui peut accueillir le rouleau de gelée. Le schéma suivant illustre le concept des trous de perforation.
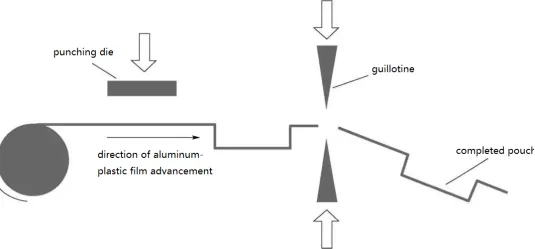
Une fois que le film aluminium-plastique est perforé et découpé en forme, il est généralement appelé « sachet ». Lorsque la cellule est relativement mince, une seule poche est généralement perforée, tandis que lorsque la cellule est plus épaisse, une double poche est perforée. En effet, une déformation excessive d’un côté peut dépasser la limite de déformation du film aluminium-plastique, entraînant une rupture.
- Procédé de scellage supérieur et latéral
Le processus de scellage par le haut est la première étape d’emballage dans la fabrication des batteries lithium-ion en poche. Le processus de scellement supérieur se compose en fait de deux étapes : le scellement supérieur et le scellement latéral. Tout d’abord, le rouleau de gelée est placé dans la poche perforée. Ensuite, le film d’emballage est plié le long de la position de la ligne pointillée. Le schéma suivant illustre le concept de l’étanchéité par le haut.
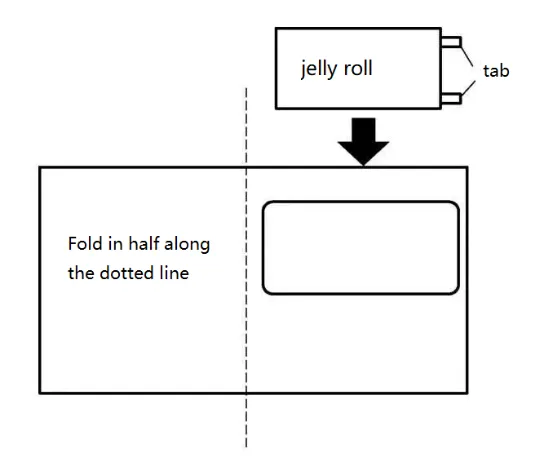
Une fois le film plastique d’aluminium chargé dans le noyau, plusieurs endroits doivent être scellés, notamment la zone d’étanchéité supérieure, la zone d’étanchéité latérale, la première zone d’étanchéité et la deuxième zone d’étanchéité. La figure ci-dessous est un schéma de l’emplacement de l’emballage.
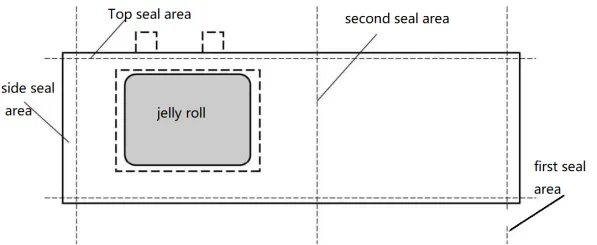
Après avoir placé le rouleau de gelée dans la poche, l’ensemble du film aluminium-plastique est placé dans un luminaire et soumis à un scellement supérieur et latéral dans une machine à sceller le dessus. La figure 6 montre une machine à sceller le haut de ce modèle, qui est équipée de quatre fixations. Le poste de travail gauche est destiné à l’étanchéité supérieure, tandis que le poste de travail droit est destiné à l’étanchéité latérale. Sous les deux têtes d’étanchéité métalliques, il y a une autre tête d’étanchéité inférieure. Pendant le processus de scellage, les deux têtes de soudure sont chauffées à une certaine température (généralement autour de 180°C) et pressées sur le film aluminium-plastique. La couche PP du film fond et se lie, complétant ainsi le processus d’étanchéité.
Pour l’étanchéité par le haut, l’objectif est d’assurer l’étanchéité des collecteurs de courant, qui sont en métal (aluminium pour l’électrode positive et nickel pour l’électrode négative). Comment peuvent-ils être scellés avec le film PP ? Ceci est réalisé grâce à un petit composant sur les collecteurs de courant appelé « adhésif de collecteur de courant ». Au cours du processus d’étanchéité, la couche PP de l’adhésif collecteur actuel fond et se lie à la couche PP du film aluminium-plastique, formant une structure d’étanchéité efficace. Le schéma suivant illustre la structure d’étanchéité.
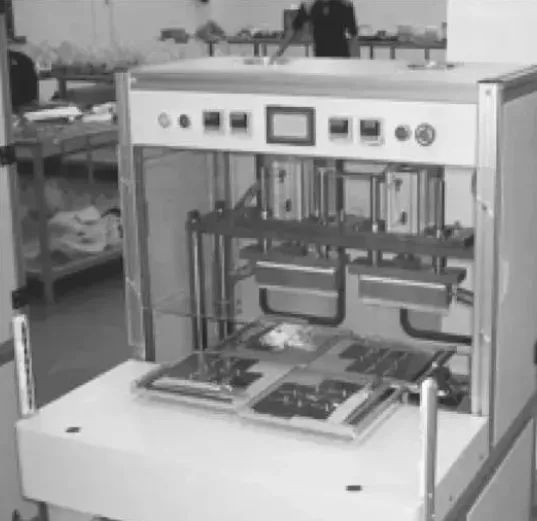
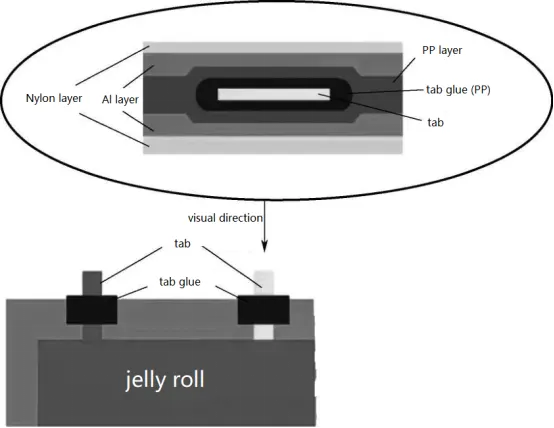
- Procédé d’injection et de pré-scellage
Après le processus de scellage supérieur, la batterie du sachet doit subir une inspection par rayons X pour vérifier le parallélisme de son rouleau de gelée. Ensuite, il entre dans la chambre de séchage pour l’élimination de l’humidité. Après un certain temps dans la chambre de séchage, il passe au processus d’injection et de pré-scellage.
Une fois l’étanchéité supérieure de la batterie terminée, il ne reste plus qu’une seule ouverture du côté de l’airbag. Cette ouverture est utilisée pour l’injection. Après leinjectionune fois terminé, une pré-étanchéité immédiate du côté de l’airbag est requise, également connue sous le nom de « scellement unique ». Une fois la première étanchéité terminée, théoriquement, la partie interne de la batterie est complètement isolée de l’environnement extérieur. Le principe d’étanchéité de la première étanchéité est le même que celui de l’étanchéité supérieure.
- Procédés de repos, de formage et de mise en forme des fixations
Après l’injection et le premier processus d’étanchéité, la cellule de la batterie doit être placée dans un état statique. En fonction de laProcessus de fabrication, il peut être soumis à un stockage statique à haute température ou à un stockage statique à température ambiante. Le but du stockage statique est de permettre à l’électrolyte injecté de pénétrer complètement dans les feuilles d’électrodes. Après le stockage statique, la cellule de batterie peut subir une formation. La formation fait référence à la charge initiale de la batterie, mais elle n’est pas chargée à la tension de fonctionnement la plus élevée et le courant de charge est très faible. Le but de la formation est d’établir un film d’interface électrolytique solide (SEI) stable à la surface de l’électrode, ce qui équivaut à « activer » la cellule de la batterie. Au cours de ce processus, une certaine quantité de gaz est générée, c’est pourquoi un airbag est réservé dans le film aluminium-plastique. Certains procédés de fabrication peuvent utiliser des montages lors de la formation, où la cellule de batterie est fixée dans un dispositif (parfois à l’aide de plaques de verre et de pinces en acier), puis placée dans une armoire pour la formation. Cela permet au gaz généré d’être entièrement compressé dans l’airbag adjacent, tout en améliorant l’interface des électrodes après la formation. Après la formation, certaines cellules de batterie, en particulier les plus épaisses, peuvent subir une déformation due à des contraintes internes. Par conséquent, certaines usines peuvent avoir un processus de mise en forme des appareils après la formation, également connu sous le nom de cuisson des appareils.
- Deuxième processus de scellage
Au cours du processus de formation, du gaz est généré, il est donc nécessaire d’extraire le gaz avant de procéder à la deuxième étanchéité. Dans certaines entreprises, ce processus est divisé en deux étapes : l’évacuation du gaz et la seconde étanchéité. Il y a aussi une étape ultérieure de coupe de l’airbag, mais ici, nous nous référerons à toutes ces étapes collectivement comme la deuxième étanchéité.
Lors de la deuxième étanchéité, un couteau à refendre est utilisé pour percer l’airbag, tout en créant simultanément un vide. Cela permet d’extraire le gaz et une petite partie de l’électrolyte à l’intérieur de l’airbag. Ensuite, immédiatement dans la deuxième zone d’étanchéité, la tête d’étanchéité est utilisée pour sceller la batterie, assurant ainsi son étanchéité à l’air. Enfin, la batterie scellée est coupée pour retirer l’airbag, et une batterie de poche est essentiellement formée. La deuxième étanchéité est le processus d’étanchéité final des batteries lithium-ion.
- Processus ultérieurs
Après avoir coupé l’airbag lors du deuxième processus de scellage, la batterie subit un découpage et un pliage des bords. Cela implique de couper le premier joint et les bords du deuxième joint à une largeur appropriée et de les plier pour s’assurer que la largeur de la batterie ne dépasse pas la limite spécifiée. Après le processus de pliage, la batterie est prête pour l’étalonnage de capacité, qui est essentiellement un test de capacité pour déterminer si la batterie répond à la capacité minimale requise. En principe, toutes les batteries doivent subir un calibrage de capacité avant de quitter l’usine afin de s’assurer que les batteries de capacité insuffisante ne sont pas livrées aux clients. Cependant, dans la production de batteries à grand volume, certaines entreprises peuvent effectuer un classement partiel de la capacité pour évaluer statistiquement le taux de qualification de capacité du lot.
Après le calibrage de capacité, les batteries de capacité qualifiée passent aux processus ultérieurs, notamment l’inspection visuelle, l’application d’étiquettes, les tests de tension de bord et le soudage par languette, entre autres. Ces processus peuvent être adaptés en fonction des besoins du client. Enfin, les batteries sont soumises à un contrôle de qualité sortant (OQC) et sont emballées pour l’expédition.