A pouch cell refers to a battery cell that uses aluminum-plastic film as its packaging material. The manufacturing process for pouch batteries differs from that of prismatic batteries, primarily starting from the winding stage. The initial stages of the manufacturing process are generally similar. In terms of lithium-ion battery packaging, there are two main categories: pouch cells and metal shell cells. Metal shell cells include steel and aluminum shells, and in recent years, some cells have been using plastic shells, which can also be classified under this category.
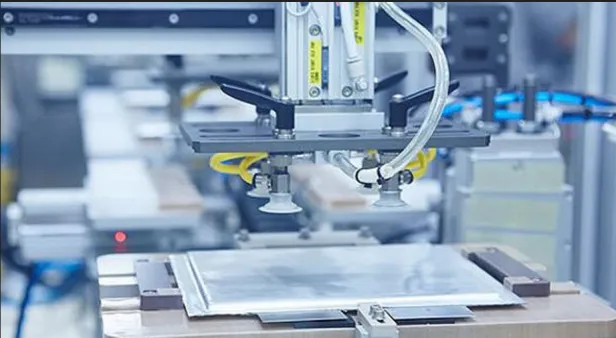
Different shell materials determine the packaging methods. Pouch batteries use thermal packaging, while metal-cased batteries generally use welding (laser welding). The reason why pouch batteries can be thermally sealed is that they use aluminum-plastic packaging film.
Aluminum-plastic packaging film is composed of three layers from a cross-section: nylon layer, aluminum layer and polypropylene (PP) layer. Each of the three layers has its own role. First, the nylon layer ensures the shape of the aluminum-plastic film and ensures that the film will not deform before it is manufactured into a lithium-ion battery. The metal aluminum layer is used to prevent water from penetrating. Lithium-ion batteries are very afraid of water. Generally, the moisture content of the electrode is required to be on the order of 10-6, so the packaging film must be able to block the penetration of water vapor. Nylon is not waterproof and cannot provide protection. Metal aluminum reacts with oxygen in the air at room temperature to form a dense oxide film, which prevents water vapor from penetrating and protects the inside of the jelly roll. The metal aluminum layer also provides the plasticity for punching when the aluminum plastic film is formed. The characteristic of PP is that it melts at temperatures of more than 100 degrees Celsius and is sticky. Therefore, the thermal sealing of batteries mainly relies on the PP layer being melted and bonded together under the action of heating of the sealing head. Then the sealing head is removed and the temperature is reduced to solidify and bond. The picture below is a schematic diagram of the structure of aluminum-plastic packaging film.
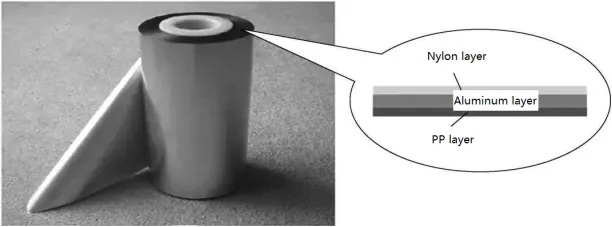
Aluminum plastic film looks very simple, but in actual practice, it is not that easy to combine the three layers of materials evenly and firmly together. Unfortunately, good-quality aluminum-plastic films are basically imported from Japan. Domestic ones are not available, but the quality still needs to be improved.
- punching holes
The aluminum-plastic film forming process is a special manufacturing technique in the production of pouch batteries. Pouch cells can be designed in different sizes according to customer requirements. Once the external dimensions are determined, corresponding molds need to be developed to shape the aluminum-plastic film. This forming process is also known as “punching holes,” which means using the forming mold to create a cavity on the heated aluminum-plastic film that can accommodate the jelly roll. The following diagram illustrates the concept of punching holes.
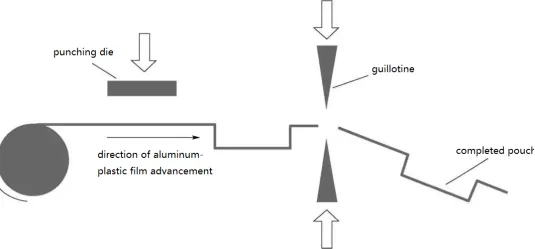
After the aluminum-plastic film is punched and cut into shape, it is generally referred to as a “pouch.” When the cell is relatively thin, a single pocket is usually punched, while when the cell is thicker, a double pocket is punched. This is because excessive deformation on one side can exceed the deformation limit of the aluminum-plastic film, leading to rupture.
- Top and side sealing process
The top sealing process is the first packaging step in the manufacturing of pouch lithium-ion batteries. The top sealing process actually consists of two steps: top sealing and side sealing. Firstly, the jelly roll is placed into the punched pocket. Then, the packaging film is folded along the dotted line position. The following diagram illustrates the concept of top sealing.
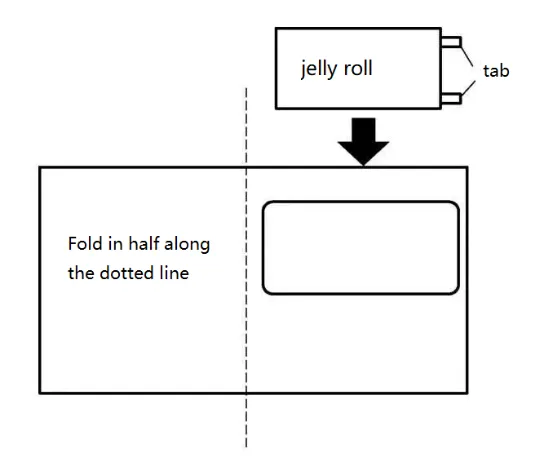
After the aluminum plastic film is loaded into the core, several locations need to be sealed, including the top sealing area, side sealing area, first sealing area and second sealing area. The figure below is a schematic diagram of the packaging location.
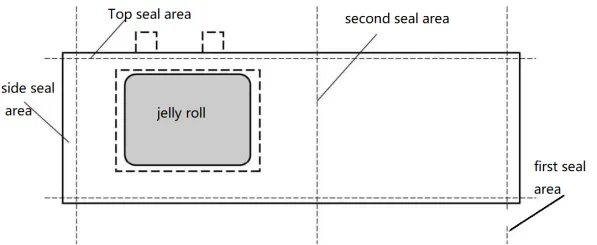
After placing the jelly roll into the pocket, the entire aluminum-plastic film is placed into a fixture and subjected to top sealing and side sealing in a top sealing machine. Figure 6 shows a top sealing machine of this model, which is equipped with four fixtures. The left workstation is for top sealing, while the right workstation is for side sealing. Underneath the two metal sealing heads, there is another bottom sealing head. During the sealing process, the two sealing heads are heated to a certain temperature (usually around 180°C) and pressed onto the aluminum-plastic film. The PP layer of the film melts and bonds together, completing the sealing process.
For top sealing, the goal is to seal the current collectors, which are made of metal (aluminum for the positive electrode and nickel for the negative electrode). How can they be sealed with the PP film? This is achieved through a small component on the current collectors called “current collector adhesive.” During the sealing process, the PP layer of the current collector adhesive melts and bonds with the PP layer of the aluminum-plastic film, forming an effective sealing structure. The following diagram illustrates the sealing structure.
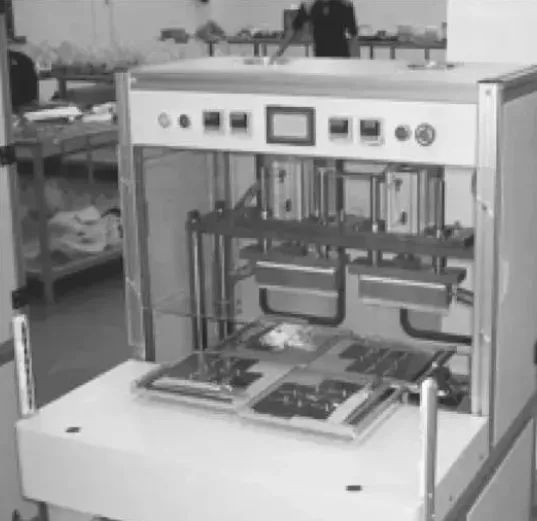
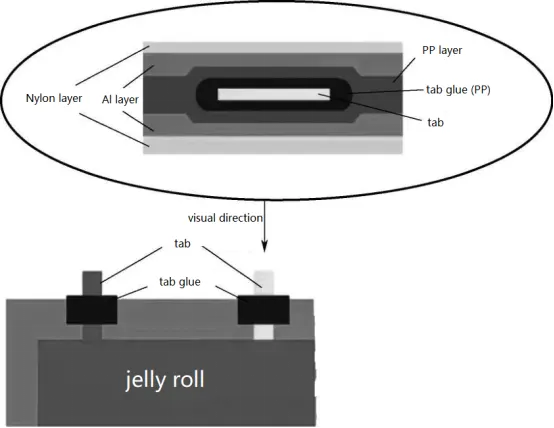
- Injection and pre-sealing process
After the top sealing process, the pouch battery needs to undergo X-ray inspection to check the parallelism of its jelly roll. Then, it enters the drying chamber for moisture removal. After a certain period of time in the drying chamber, it proceeds to the injection and pre-sealing process.
Once the top sealing of the battery is completed, there is only one opening left on the airbag side. This opening is used for injection. After the injection is completed, immediate pre-sealing of the airbag side is required, also known as “one sealing.” Once the first sealing is completed, theoretically, the internal part of the battery is completely isolated from the external environment. The sealing principle of first sealing is the same as that of top sealing.
- Resting, forming, and fixture shaping processes
After the injection and first sealing process, the battery cell needs to be placed in a static state. Depending on the specific manufacturing process, it can be subjected to either high-temperature static storage or room-temperature static storage. The purpose of static storage is to allow the injected electrolyte to fully penetrate the electrode sheets. After the static storage, the battery cell can undergo formation. Formation refers to the initial charging of the battery, but it is not charged to the highest operating voltage, and the charging current is very low. The purpose of formation is to establish a stable solid electrolyte interface (SEI) film on the electrode surface, which is equivalent to “activating” the battery cell. During this process, a certain amount of gas is generated, which is why there is an airbag reserved in the aluminum-plastic film. Some manufacturing processes may use fixtures during formation, where the battery cell is clamped in a fixture (sometimes using glass plates and steel clamps) and then placed in a cabinet for formation. This allows the generated gas to be fully squeezed into the adjacent airbag, while also improving the electrode interface after formation. After formation, some battery cells, especially thicker ones, may experience deformation due to internal stresses. Therefore, certain factories may have a fixture shaping process after formation, also known as fixture baking.
- Second sealing process
During the formation process, gas is generated, so it is necessary to extract the gas before proceeding with the second sealing. In some companies, this process is divided into two steps: gas venting and second sealing. There is also a subsequent step of cutting the airbag, but here we will refer to all of these steps collectively as the second sealing.
During the second sealing, a slitting knife is used to puncture the airbag, while simultaneously creating a vacuum. This allows the gas and a small portion of the electrolyte inside the airbag to be extracted. Then, immediately in the second sealing area, the sealing head is used to seal the battery, ensuring its air-tightness. Finally, the sealed battery is cut to remove the airbag, and a pouch battery is essentially formed. The second sealing is the final sealing process for lithium-ion batteries.
- Subsequent processes
After cutting the airbag in the second sealing process, the battery undergoes edge trimming and folding. This involves trimming the first seal and second seal edges to an appropriate width and folding them to ensure that the battery’s width does not exceed the specified limit. After the folding process, the battery is ready for capacity grading, which is essentially a capacity test to determine if the battery meets the minimum required capacity. In principle, all batteries need to undergo capacity grading before leaving the factory to ensure that batteries with insufficient capacity are not delivered to customers. However, in high-volume battery production, some companies may perform partial capacity grading to statistically assess the batch’s capacity qualification rate.
After capacity grading, batteries with qualified capacity proceed to subsequent processes, including visual inspection, label application, edge voltage testing, and tab welding, among others. These processes can be adjusted based on customer requirements. Finally, the batteries undergo outgoing quality control (OQC) and are packaged for shipment.