あるパウチセルは、アルミニウムプラスチックフィルムを包装材料として使用するバッテリーセルを指します。パウチ電池の製造工程は角型電池とは異なり、主に巻線段階から始まります。製造プロセスの初期段階は一般的に似ています。リチウムイオン電池のパッケージには、パウチセルと金属シェルセルの2つの主要なカテゴリがあります。金属シェルセルには、スチールシェルとアルミニウムシェルがあり、近年ではプラスチックシェルを使用しているセルもあり、これもこのカテゴリに分類できます。
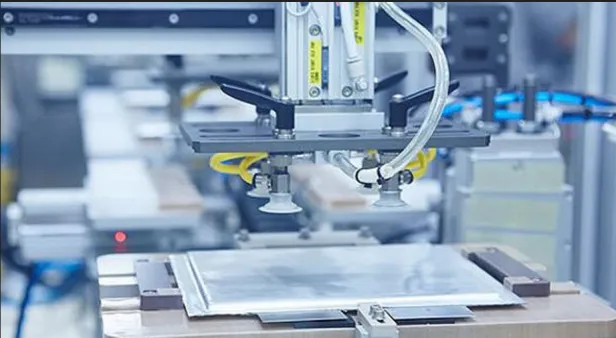
さまざまなシェル材料によって、パッケージング方法が決まります。ポーチ電池はサーマルパッケージを使用していますが、金属ケースの電池は一般的に溶接(レーザー溶接).パウチ電池を熱密封できる理由は、アルミニウムプラスチック包装フィルムを使用しているためです。
アルミニウムプラスチック包装フィルムは、断面からナイロン層、アルミニウム層、ポリプロピレン(PP)層の3つの層で構成されています。3 つのレイヤーにはそれぞれ独自の役割があります。まず、ナイロン層は、アルミニウムプラスチックフィルムの形状を確保し、フィルムがリチウムイオン電池に製造される前にフィルムが変形しないようにします。金属製のアルミニウム層は、水が浸透するのを防ぐために使用されています。リチウムイオン電池は水を非常に恐れています。一般に、電極の含水率は10〜6のオーダーである必要があるため、包装フィルムは水蒸気の浸透をブロックできなければなりません。ナイロンは防水性がなく、保護を提供することはできません。金属アルミニウムは、室温で空気中の酸素と反応して緻密な酸化膜を形成するため、水蒸気の浸透を防ぎ、ゼリーロールの内部を保護します。金属アルミニウム層は、アルミニウムプラスチックフィルムが形成されたときにパンチングするための可塑性も提供します。PPの特徴は、100°C以上の温度で溶けて粘り気がある点です。したがって、バッテリーのサーマルシールは、主にシーリングヘッドの加熱の作用下でPP層が溶融して結合されることに依存しています。次に、シーリングヘッドを取り外し、温度を下げて固化して接着します。下の写真は、アルミニウムプラスチック包装フィルムの構造の概略図です。
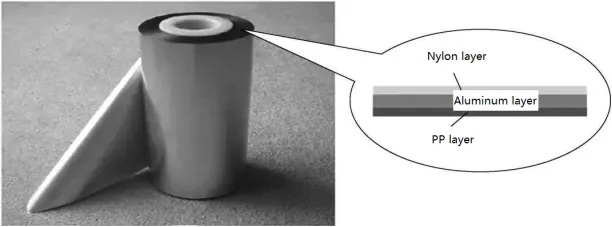
アルミプラスチックフィルムは一見シンプルに見えますが、実際には3層の素材を均一にしっかりと組み合わせるのはそう簡単ではありません。残念ながら、良質なアルミプラスチックフィルムは基本的に日本から輸入しています。国産のものはありませんが、まだ品質を向上させる必要があります。
- パンチ穴
アルミニウムプラスチックフィルム形成プロセスは、パウチ電池の製造における特別な製造技術です。パウチセルは、お客様の要件に応じてさまざまなサイズで設計できます。外形寸法が決定されたら、アルミニウムプラスチックフィルムを成形するための対応する金型を開発する必要があります。この成形プロセスは「パンチングホール」とも呼ばれ、成形金型を使用して、ゼリーロールを収容できる加熱されたアルミニウムプラスチックフィルムにキャビティを作成することを意味します。次の図は、パンチ穴の概念を示しています。
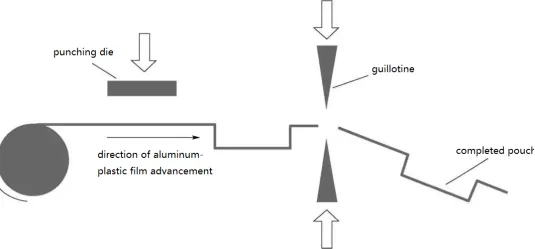
アルミプラスチックフィルムに穴を開けて形にした後、一般的に「ポーチ」と呼ばれます。セルが比較的薄い場合は、通常、シングルポケットが打ち抜かれ、セルが厚い場合はダブルポケットが打ち抜かれます。これは、片面の過度の変形がアルミニウムプラスチックフィルムの変形限界を超え、破裂につながる可能性があるためです。
- トップとサイドのシーリングプロセス
トップシールプロセスは、パウチリチウムイオン電池の製造における最初のパッケージングステップです。トップシーリングプロセスは、実際にはトップシーリングとサイドシーリングの2つのステップで構成されています。まず、ゼリーロールをパンチポケットに入れます。次に、包装フィルムを点線の位置に沿って折ります。次の図は、トップシーリングの概念を示しています。
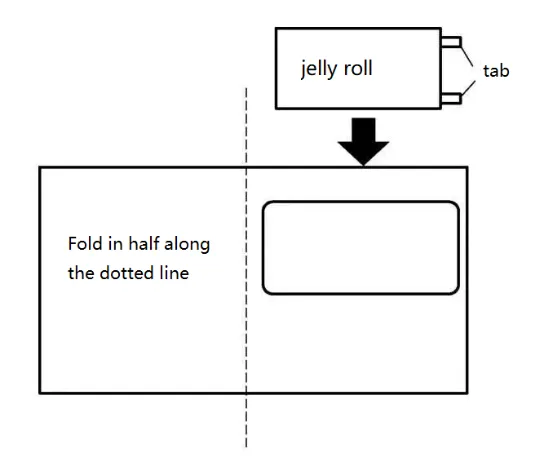
アルミニウムプラスチックフィルムがコアに装填された後、上部シール領域、サイドシール領域、第1シール領域、第2シール領域など、いくつかの場所をシールする必要があります。下の図は、パッケージ位置の概略図です。
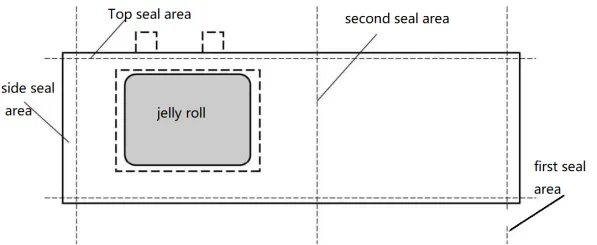
ゼリーロールをポケットに入れた後、アルミニウムプラスチックフィルム全体を固定具に入れ、トップシール機でトップシールとサイドシールを行います。図6は、4つの固定具が装備されているこのモデルのトップシール機を示しています。左のワークステーションはトップシール用で、右のワークステーションはサイドシール用です。2つの金属製シーリングヘッドの下には、別のボトムシーリングヘッドがあります。シーリングプロセスでは、2つのシーリングヘッドが特定の温度(通常は約180°C)に加熱され、アルミニウムプラスチックフィルムに押し付けられます。フィルムのPP層が溶融して結合し、シーリングプロセスが完了します。
トップシーリングの場合、目標は、金属(正極はアルミニウム、負極はニッケル)でできている集電体をシールすることです。PPフィルムでどのように密封できますか?これは、「集電体接着剤」と呼ばれる集電体上の小さなコンポーネントによって実現されます。シーリングプロセス中に、集電体接着剤のPP層が溶融してアルミニウムプラスチックフィルムのPP層と結合し、効果的なシーリング構造を形成します。次の図は、シーリング構造を示しています。
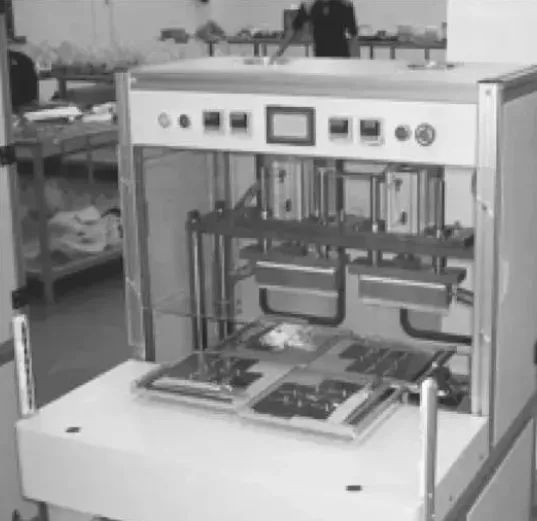
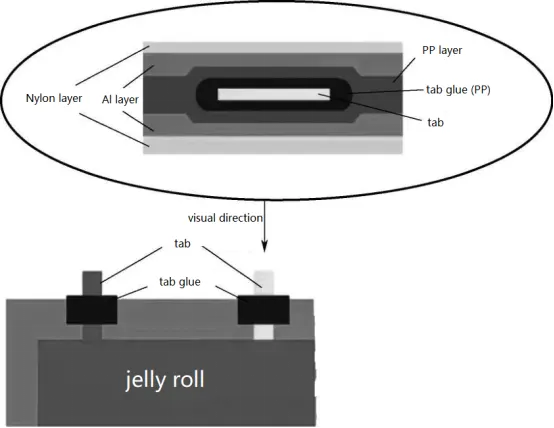
- インジェクションおよびプレシールプロセス
トップシールプロセスの後、ポーチバッテリーはゼリーロールの平行度を確認するためにX線検査を受ける必要があります。その後、乾燥チャンバーに入り、水分を逃がします。乾燥チャンバー内で一定時間経過した後、注入およびプレシールプロセスに進みます。
バッテリーの上部のシーリングが完了すると、エアバッグ側に残る開口部は1つだけです。この開口部は注射に使用されます。その後注射完了すると、エアバッグ側の即時の事前シーリングが必要であり、これは「ワンシーリング」とも呼ばれます。最初のシーリングが完了すると、理論的には、バッテリーの内部部分は外部環境から完全に隔離されます。最初のシーリングのシーリング原理は、トップシーリングの原理と同じです。
- 休息、成形、および固定具の成形プロセス
注入と最初のシーリングプロセスの後、バッテリーセルを静止状態に置く必要があります。特定のものに応じて製造プロセス、高温静的保存または室温静的保存のいずれかを行うことができます。静的保存の目的は、注入された電解質が電極シートに完全に浸透できるようにすることです。静的な貯蔵の後、バッテリーセルは形成を受けることができます。フォーメーションとは、バッテリーの初期充電を指しますが、最高の動作電圧まで充電されておらず、充電電流は非常に低くなっています。形成の目的は、電極表面に安定した固体電解質界面(SEI)膜を確立することであり、これは電池セルを「活性化」することに相当します。この過程で、一定量のガスが発生するため、アルミニウムプラスチックフィルムにエアバッグが予約されています。一部の製造プロセスでは、形成時に固定具を使用する場合があり、バッテリーセルを固定具に固定し(ガラス板やスチールクランプを使用する場合もあります)、キャビネットに配置して形成します。これにより、発生したガスを隣接するエアバッグに完全に押し込むことができ、形成後の電極界面も改善されます。形成後、一部のバッテリーセル、特に厚いバッテリーセルは、内部応力により変形する可能性があります。したがって、特定の工場では、形成後にフィクスチャの成形プロセス(フィクスチャベーキングとも呼ばれる)が行われる場合があります。
- セカンドシールプロセス
形成過程ではガスが発生するため、2回目のシールを進める前にガスを抽出する必要があります。一部の企業では、このプロセスはガスベントとセカンドシーリングの2つのステップに分かれています。エアバッグを切断する後続のステップもありますが、ここではこれらすべてのステップをまとめてセカンドシーリングと呼びます。
2回目のシーリングでは、スリッターナイフを使用してエアバッグに穴を開けると同時に、真空を作り出します。これにより、エアバッグ内のガスと電解液のごく一部を取り出すことができます。次に、すぐに2番目のシーリングエリアで、シーリングヘッドを使用してバッテリーをシールし、気密性を確保します。最後に、密閉されたバッテリーを切断してエアバッグを取り外し、基本的にポーチバッテリーを形成します。2番目のシーリングは、リチウムイオン電池の最終的なシーリングプロセスです。
- 後続プロセス
2回目のシール工程でエアバッグを切断した後、バッテリーはエッジトリミングと折り畳みを行います。これには、第1シールと第2シールの端を適切な幅にトリミングし、バッテリーの幅が指定された制限を超えないように折りたたむことが含まれます。折り畳みプロセスの後、バッテリーは容量グレーディングの準備ができており、これは基本的にバッテリーが最低限必要な容量を満たしているかどうかを判断するための容量テストです。原則として、すべてのバッテリーは、容量が不足しているバッテリーが顧客に配送されないように、工場を出る前に容量の等級付けを受ける必要があります。ただし、バッテリーの大量生産では、一部の企業は、バッチの容量認定率を統計的に評価するために、部分的な容量評価を実行する場合があります。
容量の等級付け後、認定容量のバッテリーは、目視検査、ラベル貼付、エッジ電圧テスト、タブ溶接などの後続のプロセスに進みます。これらのプロセスは、お客様の要件に基づいて調整できます。最後に、バッテリーは出荷品質管理(OQC)を受け、出荷用に梱包されます。