電極シートのコーティングとは、一般に、よく混合されたスラリーを集電体に均一に塗布し、スラリー中に存在する有機溶剤を乾燥させるプロセスを指します。コーティングの品質は、バッテリー容量、内部抵抗、サイクル寿命、および安全性に大きな影響を与えます。電極シートの均一なコーティングを確保することは非常に重要です。コーティング方法の選択と制御パラメータは、リチウムイオン電池の性能に重要な役割を果たします。これは主に次の側面に反映されます。
1)コーティング乾燥温度制御:コーティング中の乾燥温度が低すぎる場合(関連マシン)、電極シートが完全に乾燥していることを保証することはできません。温度が高すぎると、電極シート内の有機溶剤が急速に蒸発し、電極シートの表面コーティングにカメが現れたり、ひび割れたり、脱落したりする可能性があります。
2)コーティング表面密度:コーティング表面密度が小さすぎると、バッテリー容量が公称容量に達しない場合があります。コーティング表面密度が高すぎると、材料の無駄遣いが発生しやすくなります。深刻な場合、リチウムによる正極容量が過剰になると、降水量はリチウム樹状突起を形成し、バッテリーセパレーターを貫通して短絡を引き起こし、安全上の問題を引き起こします。
3)コーティングサイズ:コーティングサイズが小さすぎるか大きすぎると、バッテリー内部の正極が負極で完全に覆われていない可能性があります。充電プロセス中、リチウムイオンは正極から埋め込まれ、負極で完全に覆われていない電解質に移動します。中程度、正極シートの実際の容量を効率的に使用することはできません。ひどい場合、バッテリー内部にリチウム樹状突起が形成され、セパレーターを簡単に貫通してバッテリーの内部回路を引き起こす可能性があります。
4)コーティングの厚さ:コーティングの厚さが薄すぎたり厚すぎたりすると、その後の電極シートの圧延プロセスに影響を与え、バッテリー電極シートの性能の一貫性を保証することはできません。
さらに、電極シートコーティングは、バッテリーの安全性にとって非常に重要です。コーティングの前に、コーティングプロセス中に粒子、破片、ほこりなどが電極シートに混入しないように、5S作業を行う必要があります。ゴミが混入するとバッテリー内部で微小なショートが発生し、ひどい場合にはバッテリーが発火して爆発する恐れがあります。
1. 塗装設備と塗装プロセスの選択
一般的なコーティングプロセスには、巻き戻し→スプライシング→引っ張り→張力制御→コーティング→乾燥→アライメント補正→張力制御→偏差補正→巻線およびその他のプロセスが含まれます。コーティングプロセスは複雑であり、コーティング効果に影響を与える多くの要因があります:コーティング装置の製造精度、装置操作の滑らかさ、コーティングプロセス中の動的張力の制御、乾燥プロセス中の空気量、および温度制御曲線はコーティング効果に影響を与えます。 したがって、適切なコーティングプロセスを選択することが非常に重要です。
一般に、コーティング方法を選択する際には、コーティング層の数、ウェットコーティングの厚さ、コーティング液のレオロジー特性、必要なコーティング精度、コーティングサポートまたは基材、布の速度などを考慮する必要があります。
上記の要素に加えて、電極シートコーティングの特定の条件と特性も組み合わせる必要があります。リチウムイオン電池電極シートのコーティング特性は次のとおりです:(1)両面単層コーティング。(2)スラリーウェットコーティングは厚い(100~300μm)。(3)スラリーは非ニュートン高粘度流体です。(4)電極シートのコーティング精度要件は高く、フィルムコーティング精度と同様です。(5)コーティングサポートは、厚さ10〜20μmのアルミホイルと銅ホイルです。(6)フィルムコーティング速度と比較して、電極シートのコーティング速度は高くありません。上記の要素を考慮すると、一般的な実験装置はスクレーパータイプを使用することが多く、民生用リチウムイオン電池は主にローラーコーティング転写タイプを使用し、パワーバッテリーは主にスリット押出法を使用します。
Sクラッパーコーティング:動作原理を図1に示します。ホイル基材はコーティングローラーを通過し、スラリートラフと直接接触します。過剰なスラリーがホイル基材に塗布されます。基板がコーティングローラーとスクレーパーの間を通過すると、スクレーパーと基板の間のギャップがコーティングの厚さを決定し、同時に余分なスラリーが削り取られてリフローされるため、基板の表面に均一なコーティングが形成されます。スクレーパータイプ メインコンマスクレーパー。コンマスクレーパーは、コーティングヘッドの主要コンポーネントの1つです。これは一般に、バスラインに沿った丸いローラーの表面でコンマのような刃先に加工されます。強度・硬度が高く、コーティング量やコーティング精度のコントロールが容易なスクレーパーです。高固形分および高粘度スラリーに適しています。
ローラーコーティング転写式:コーティングローラーの回転がスラリーを駆動し、スラリーの移動量はコンマスクレーパーギャップを介して調整され、バックローラーとコーティングローラーの回転を使用してスラリーを基板に移送します。このプロセスを図2 に示します。ローラートランスファーコーティングは、2つの基本的なプロセスで構成されています:(1)コーティングローラーの回転は、計量ローラーのギャップを介してスラリーを駆動し、特定の厚さのスラリー層を形成します。(2)ある特定の厚さのスラリーの層はコーティングのローラーの反対方向を通り、裏付けのローラーの回転はコーティングを形作るためにホイルにスラリーを移します。
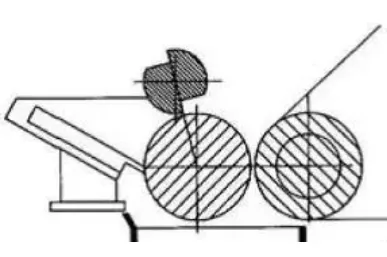
ローラーコーティングブレード転写コーティングプロセスの概略図
スロットダイコーティング:精密なウェットコーティング技術として、スロットダイコーティングは図3に示すように機能します。動作原理は、特定の圧力と流量でスロットダイの隙間からコーティング液を押し出し、それを基板上に転写することを含みます。他のコーティング方法と比較して、スロットダイコーティングには、高いコーティング速度、高精度、均一な湿った厚さなど、いくつかの利点があります。コーティングシステムは密閉されているため、コーティングプロセス中に汚染物質が侵入するのを防ぎ、スラリーの使用率が高く、安定したスラリー特性が維持されます。これにより、同時多層コーティングが可能になります。さらに、スロットダイコーティングは、幅広いスラリー粘度と固形分に対応できるため、トランスファーコーティングプロセスと比較して適応性が高くなります。
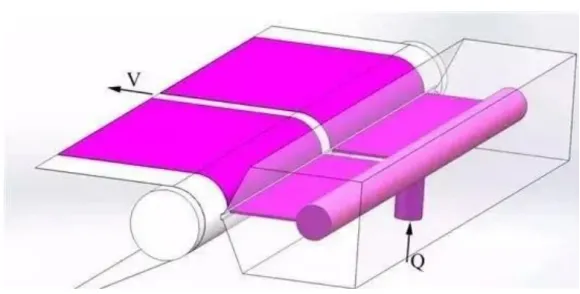
2. コーティングの欠陥と影響要因
コーティングの欠陥を減らし、コーティングの品質と歩留まりを向上させ、コストを削減することは、コーティングプロセスの研究において考慮すべき重要な側面です。コーティングプロセス中によく発生する一般的な問題には、ヘッドの厚い尾の薄い、両側の厚いエッジ、スペックル欠陥、表面粗さ、ホイルの露出などがあります。
ヘッドとテールの厚さは、コーティングバルブまたは間欠バルブの開閉時間を制御することで調整できます。エッジが厚いという問題は、スラリーの特性、コーティングギャップ、およびスラリーの流量を調整することで改善できます。表面の粗さや凹凸、縞模様は、箔素材を安定させ、速度を落とし、エアナイフの角度を調整することで対処できます。
基材-スラリー
スラリーとコーティングの基本的な物理的特性の関係:実際のプロセスでは、スラリーの粘度がコーティング効果に一定の影響を与えます。電極原料、スラリーの割合、および調製されたスラリーの粘度も、バインダーの種類を選択すると異なります。異。スラリーの粘度が高すぎると、コーティングを連続的かつ安定して行うことができないことが多く、コーティング効果にも影響します。
コーティング液の均一性、安定性、エッジおよび表面効果は、コーティング液のレオロジー特性の影響を受け、コーティングの品質を直接決定します。理論解析、コーティング実験技術、流体力学有限要素技術などの研究方法を使用して、コーティングウィンドウを研究することができます。コーティングウィンドウは、安定したコーティングを実現し、均一なコーティングを得ることができるプロセス動作範囲です。
基板–銅箔とアルミ箔
表面張力:銅アルミ箔の表面張力は、コーティングされた溶液の表面張力よりも高くなければならない、そうしないと溶液が基板上に滑らかに広がるのが難しくなり、コーティング品質が低下します。従う必要がある1つの原則は、コーティングする溶液の表面張力を基板の表面張力よりも5ダイン/cm低くする必要があるということです。もちろん、これは大まかなものにすぎません。溶液と基板の表面張力は、基板の処方または表面処理を調整することで調整できます。両方の表面張力測定は、品質管理試験項目としても使用する必要があります。
均一な厚さ:ブレードコーティングと同様のプロセスでは、基板の厚さが幅全体で不均一になり、コーティングの厚さが不均一になります。コーティングプロセスでは、コーティングの厚さはスクレーパーと基板の間のギャップによって制御されるためです。基板の横方向に基板の厚さが比較的低い場所がある場合、その場所を通過する溶液が多くなり、コーティングの厚さが厚くなり、その逆も同様です。厚さ計から母材の次の厚さ変動を見ると、最終的なコーティング厚さの変動も同じ偏差を示します。さらに、横方向の厚さの偏差も巻線の欠陥につながる可能性があります。したがって、この欠陥を回避するためには、原材料の厚さ制御が非常に重要です。
静電気:コーティングラインでは、コーティングがほどけてローラーを通過する際に、基板表面に多くの静電気が発生します。発生した静電気は、ローラー上の空気や灰層を吸収しやすく、コーティング欠陥の原因となります。静電気の放電過程では、コーティング表面に静電気のような外観欠陥も発生し、より深刻な場合は火災を引き起こす可能性さえあります。冬場の湿度が低いと、コーティングラインの静電気問題が深刻になります。このような欠陥を減らす最も効果的な方法は、周囲の湿度をできるだけ高く保ち、コーティングラインを接地し、帯電防止装置を設置することです。
清潔:基板表面の不純物は、突起物、汚れなどの物理的な欠陥を引き起こします。したがって、基材の製造工程では、原材料の清浄度をより適切に制御する必要があります。オンラインフィルムクリーニングローラーは、基板の不純物を除去するより効果的な方法です。メンブレン上のすべての不純物を除去することはできませんが、原材料の品質を効果的に向上させ、損失を減らすことができます。
3.リチウム電池電極シート欠陥マップ
- リチウムイオン電池負極コーティングの気泡欠陥
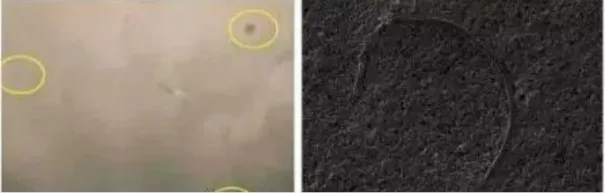
左の写真は気泡の入った負極板、右の写真は走査型電子顕微鏡の倍率を200倍にしたものです。スラリーの混合、移送、コーティングのプロセスでは、ほこりや長い糸くずなどの異物がコーティング液に混入したり、濡れたコーティングの表面に落下したりして、コーティングの表面張力が外力の影響を受け、分子間力が発生します。変化が起こり、スラリーはわずかに移動し、乾燥後、薄い中央で円形の痕跡が形成されます。
- ピンホール
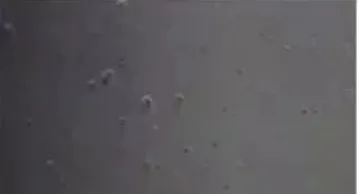
1つは気泡の発生です(攪拌プロセス、輸送プロセス、コーティングプロセス)。気泡によるピンホール欠陥は比較的理解しやすいです。ウェットフィルム中の気泡は、内層からフィルム表面に移動し、フィルム表面で破裂してピンホール欠陥を形成します。気泡は主に、攪拌、コーティング液の輸送、およびコーティングプロセス中の塗料の流動性とレベリングの悪さ、および塗料からの気泡放出の悪さから発生します。
- 傷
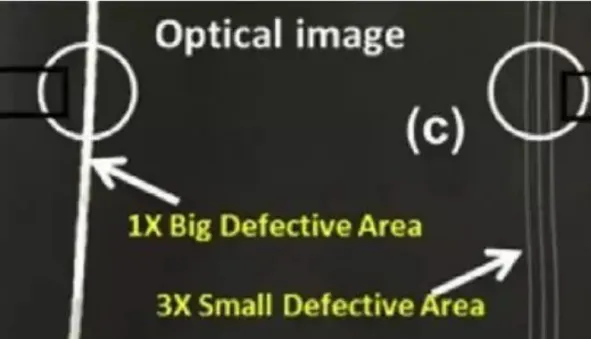
- 太いエッジ
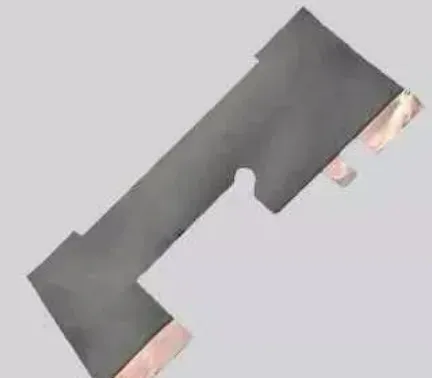
エッジが厚い理由は、スラリーの表面張力により、スラリーが電極シートの端のコーティングされていない領域に移動し、乾燥後に厚いエッジを形成するためです。
- 負の表面凝集粒子
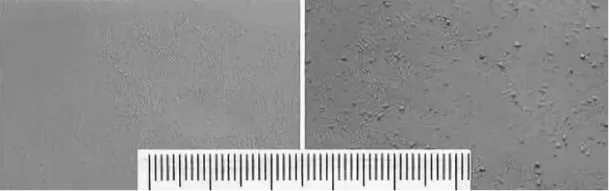
処方:球状グラファイト+ SUPER C65 + CMC +蒸留水
異なる混合プロセスを使用した2つの異なる電極フィルムの巨視的な外観:滑らかな表面(左)と多数の小さな粒子を含む表面(右)。
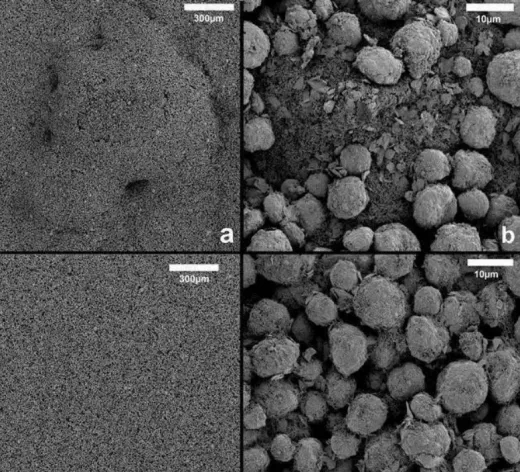
処方:球状グラファイト+ SUPER C65 + CMC / SBR +蒸留水
微粒子電極膜表面の拡大形態(a、b):導電性添加剤の凝集、不完全分散
滑らかな表面電極フィルムの拡大形態:導電性添加剤はよく分散し、均一に分布しています。
- 正極表面凝集粒子
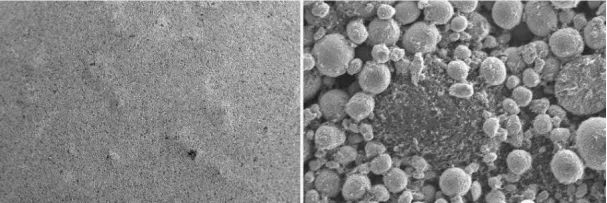
処方:NCA +アセチレンブラック+ PVDF + NMP
攪拌プロセス中、周囲の湿度が高すぎるため、スラリーがゼリー状態になり、導電剤が完全に分散しておらず、圧延後の電極シートの表面に多数の粒子が存在していました。
- 水系電極シートの亀裂
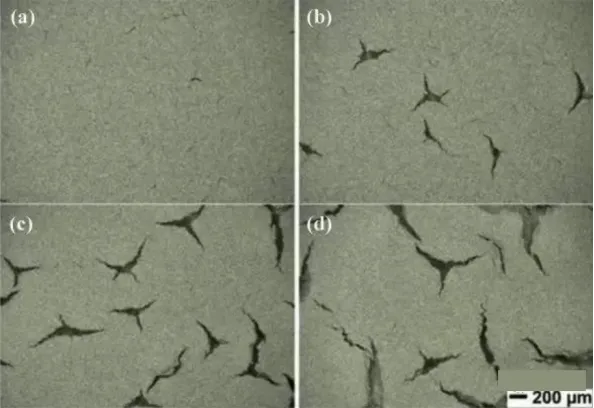
処方:NMC532/カーボンブラック/バインダー=90/5/5重量%、水/イソプロピルアルコール(IPA)溶剤。
(a)15 mg/cm2、(b)17.5 mg/cm2、(c)20 mg/cm2、(d)25 mg/cm2 の異なるコーティング面密度での電極フィルム表面の亀裂の光学写真。電極フィルムが厚いほど、ひび割れやすくなります。
- 電極シート表面の収縮キャビティ
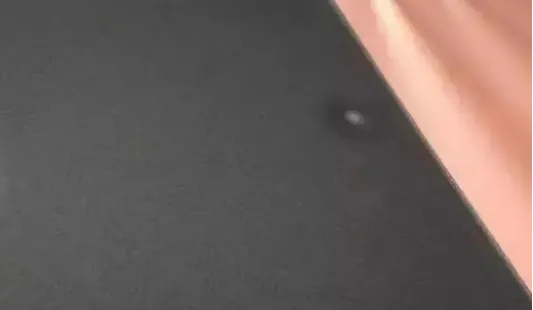
配合:フレークグラファイト+ SP + CMC / SBR +蒸留水
ホイルの表面には汚染物質粒子があり、粒子の表面のウェットフィルムには低い表面張力領域があります。液膜は粒子の周りを放射状に移動し、収縮点の欠陥を形成します。
- 電極シート表面の傷

製剤:NMC532 + SP + PVdF + NMP
スリット押出コーティングプロセス中、刃先に大きな粒子が存在すると、電極シートの表面にホイルの傷がつきます。
- 垂直ストリップのコーティング
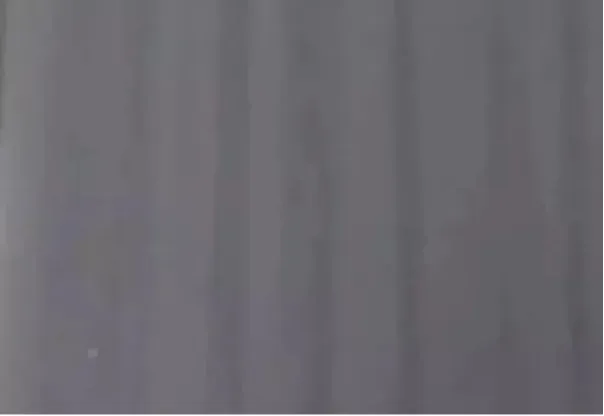
製剤:NCA+SP + PVdF+NMP
転写コーティングの後期段階では、スラリーは吸水により粘度が上昇します。コーティングプロセスはコーティングウィンドウの上限に近づき、スラリーのレベリングが不十分になり、垂直の縞が形成されます。
- 電極シートの濡れた部分の転がり亀裂
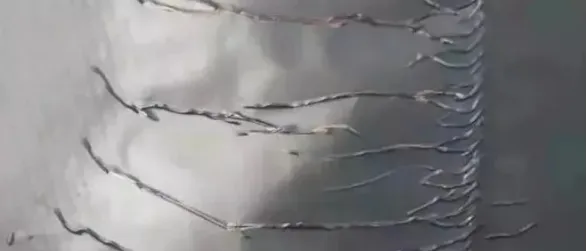
配合:フレークグラファイト+ SP + CMC / SBR +蒸留水
コーティング中、電極シートの中央部分が完全に乾燥していなかったため、圧延中にコーティングが移動し、ストリップ状の亀裂が形成されました。
- 電極シートロールエッジシワ
コーティング中に厚いエッジが形成されます。ローリングタイプは、コーティングの端にしわを引き起こします。
- 負極スリットコーティングは箔から分離されています
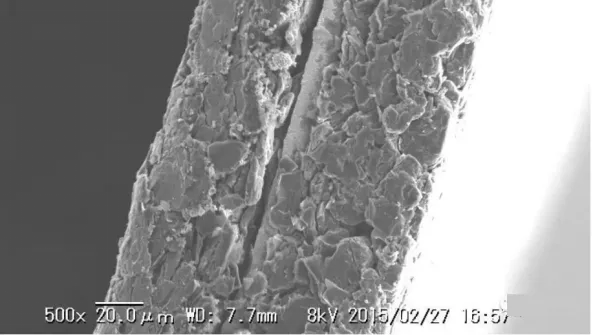
処方:天然グラファイト+アセチレンブラック+ CMC / SBR +蒸留水、活性物質比率96%
電極シートディスクにスリットを入れると、コーティングが箔から分離します。
- 電極シートスリットバリ
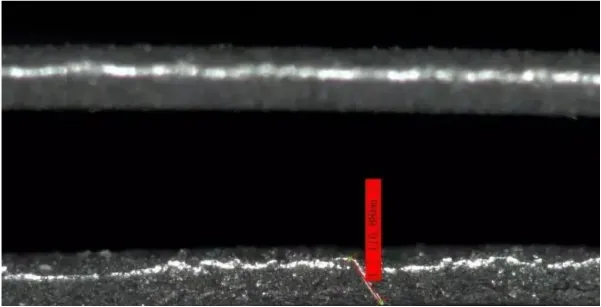
正極ディスクにスリットを入れると、不安定なテンションコントロールにより、二次切断により箔バリが発生します。
- 電極シートスリット波状エッジ
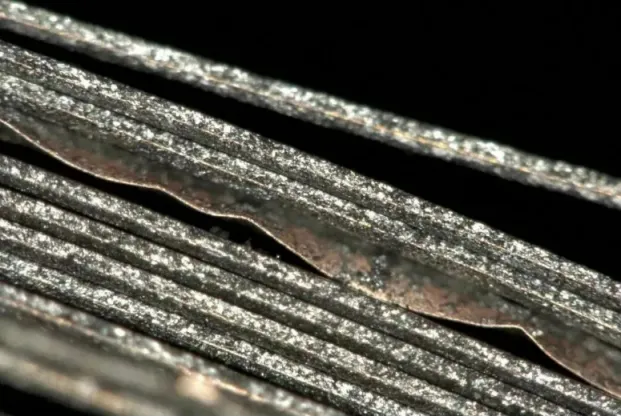
負極ディスクを切断すると、カッターの不適切な重なりと圧力により、波状のエッジが形成され、切断のコーティングが剥がれます。
- その他の一般的なコーティングの欠陥には、空気の浸透、横波、垂直流、リヴレット、膨張、水の波紋などがあります。
欠陥は、コーティングの配合、基材の準備、コーティング操作領域、乾燥ゾーン、切断、スリット、カレンダー加工プロセスなど、処理のさまざまな段階で発生する可能性があります。障害を解決するための一般的な論理的アプローチは次のとおりです。
パイロットスケールから生産まで、製品の配合、コーティング、乾燥プロセスを最適化します。パラメータと変数を調整することにより、最適またはより広いプロセスウィンドウを見つけます。
製品の品質を管理するための品質管理手段と統計ツール(統計的プロセス管理、SPCなど)を実装します。オンライン監視システムを利用して安定したコーティング厚さを確保するか、外観検査システム(Visual Systems)を使用して表面欠陥を検出します。
欠陥が発生した場合は、プロセスをタイムリーに調整して、欠陥の再発を回避します。根本原因を特定し、プロセス変数を分析し、それに応じてパラメーターを変更して問題を修正します。
4. コーティングの均一性
「コーティングの均一性」という用語は、コーティング領域内のコーティングの厚さまたは接着剤の分布の一貫性を指します。コーティングの厚さまたは接着剤の分布の一貫性が優れているほど、コーティングの均一性は高くなり、その逆も同様です。コーティングの均一性に関する標準化された指標はありませんが、特定の領域内のさまざまなポイントでのコーティングの厚さまたは接着剤量の偏差またはパーセンテージの偏差によって測定できます。また、一定領域内の最大コーティング厚さと最小コーティング厚さまたは接着剤量の差によって測定することもできます。コーティングの厚さは通常、マイクロメートル(μm)で表されます。
コーティングの均一性は、特定の領域内の全体的なコーティング品質を評価するために使用されます。しかし、実際の生産では、通常、基板の横方向(クロスマシン)と縦方向(マシン方向)の均一性に関心があります。横方向の均一性は、コーティングの幅方向(または機械方向)の均一性を指し、縦方向の均一性は、コーティングの長さ方向(または基板の進行方向)の均一性を指します。
横方向と縦方向のコーティング誤差の大きさ、影響要因、および制御方法は大きく異なります。一般に、基材(またはコーティング)の幅が広いほど、横方向の均一性を制御するのが難しくなります。コーティング作業における長年の実務経験に基づいて、基板幅が800mm未満の場合、通常、横方向の均一性を確保することは比較的容易です。基板幅が1300mmから1800mmの範囲の場合、横方向の均一性はよく制御できますが、かなりの専門知識が必要です。しかし、基板幅が2000mmを超えると、横方向の均一性を実現することは非常に難しく、それを効果的に扱えるメーカーはごくわずかです。一方、生産バッチサイズ(つまり、コーティング長)が大きくなると、縦方向の均一性は横方向の均一性と比較してより大きな課題または困難になる可能性があります。