コーティング技術は、流体特性の研究に基づくプロセスであり、基板上に1層または複数の液体を塗布します。基板は通常、柔軟なフィルムまたは紙です。その後、液状コーティングをオーブン乾燥などの方法で乾燥または硬化させ、リチウムイオン電池の電極コーティングのように特殊な機能を持つ層を形成します。現在、リチウムイオン電池電極の主なコーティング方法は、コンマロール転写コーティングとスロットダイ押出コーティングです。
01コーティング機の原理と分類
電極コーティング装置の原理は、正極または負極の配合に必要な材料を均一に混合し、その後、アルミ箔または銅箔の表面と裏面に塗布またはラミネートすることを含みます。必要に応じて、電気機械式統合デバイスを使用して、エネルギー伝導によってスラリーから溶媒を蒸発させることにより、顧客の技術要件を達成できます。
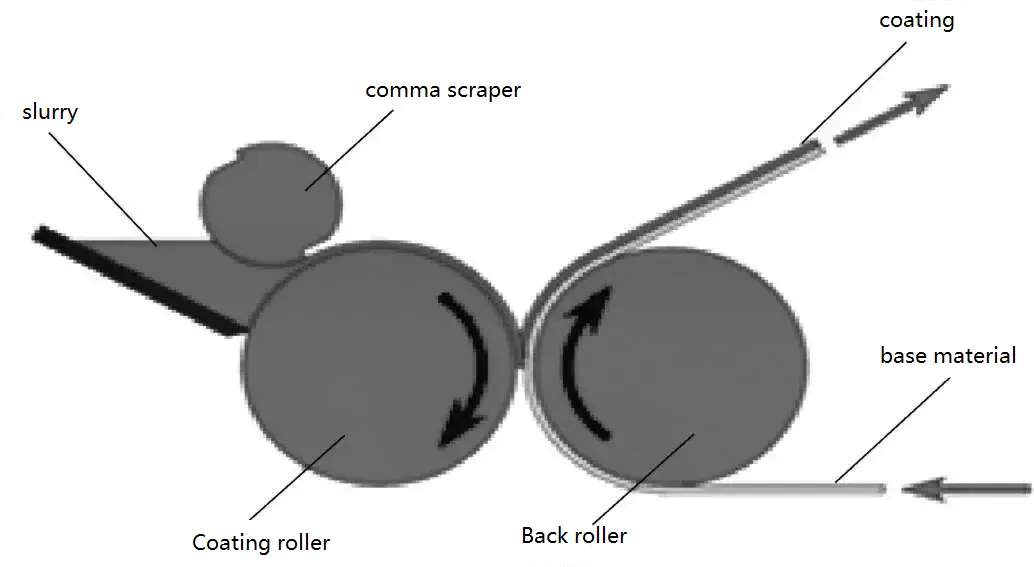
コーティングローラーとコンマブレードの間のギャップを調整することにより、スラリーはコーティングローラーに計量されます。次に、バックローラーとコーティングローラーの隙間を調整することにより、コーティングローラー上の計量スラリー全体がホイルに転写されます。
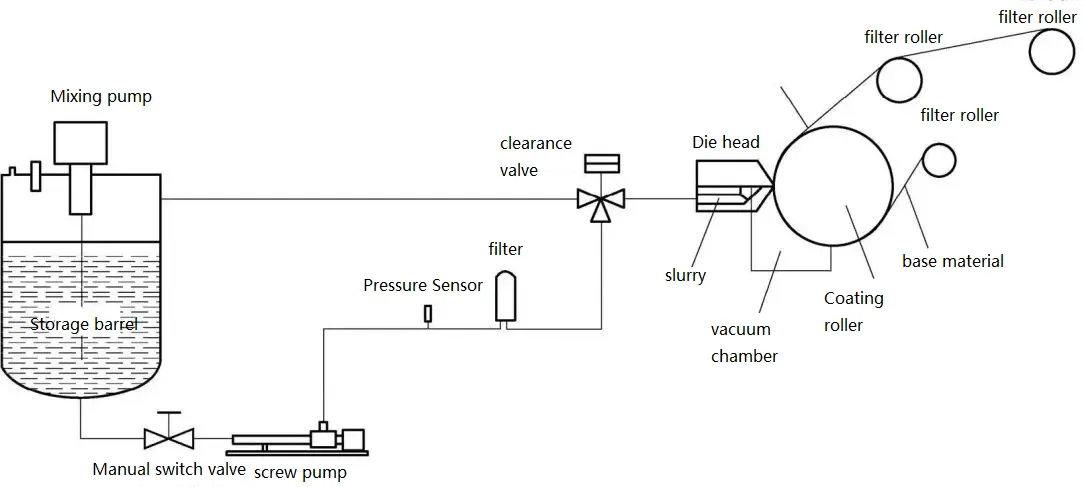
ニュートン流体スラリーや非ニュートン流体スラリーを、計量ポンプとスロットダイにより基板表面に均一に塗布する高精度定量膜装置です。コーティングの厚さを計算する式は次のとおりです。
コーティング厚さ=定量ポンプ流量/(コーティング幅×コーティング速度)
また、ダイはスロットダイのコーティング法の重要な構成要素であり、コーティング精度を決定する重要な要素の1つです。塗装速度の高速化に伴い、高速塗装工程での塗装品質を確保するために、真空チャンバーの仕組みを採用しているお客様もいらっしゃいます。通常、コーティング速度が≥30m/minの場合、この負圧チャンバーの構造を考慮する必要があります。
ダイの設計では、次の要素を考慮する必要があります。
スラリーのレオロジーパラメータに基づく流路キャビティの計算とシミュレーション。
上部と下部のダイリップの平坦度と真直度の要件。
ダイの材料選択、できればステンレス鋼を使用。
使用中の金属異物の発生防止やむを得ない場合は、異物がスラリーに入るのを防ぐために、適切な保護を実施する必要があります。
分解と清掃の容易さ。
乾式電極調製の原理(図を参照):
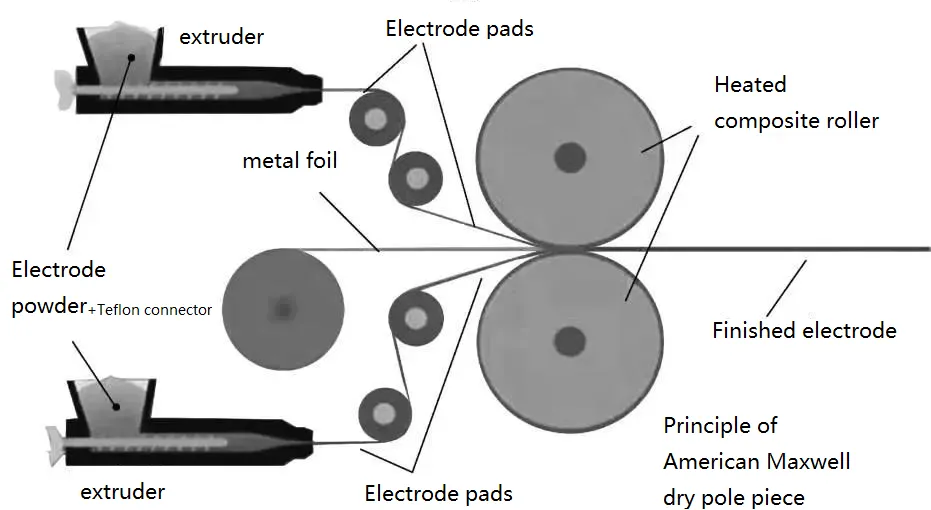
コーティング技術は、特に全固体電池技術と組み合わせることで、将来の高度なリチウム電池のニーズを満たすための破壊的なイノベーションとなる可能性を秘めています。例えば、硫化物固体電解質と乾式電極技術の組み合わせは、大きな期待が寄せられています。このテクノロジーの利点は次のとおりです。
ヨーロッパの厳しい環境要件を満たすことができ、生産プロセスを環境に優しいものにします。
これにより、生産中の安全性が確保されます。従来のリチウム電池カソードコーティングスラリーは、溶媒としてNMP(N-メチル-2-ピロリドン)を使用しており、安全性が劣ります。
設備投資コストは低く、環境湿度要件の低減により、設置面積を小さくする必要があります。
これにより、より厚い電極フィルムの製造が可能になり、同じ体積エネルギー容量を確保しながら、箔とセパレータの材料を節約できます。これにより、部品表(BOM)コストの面で大きなメリットが得られます。
02設備構成と主要構成
装置は、巻出ユニット、コーティングユニット(供給システムを含む)、乾燥ユニット、排出ユニット、巻取ユニットの5つの主要部分で構成されています。塗装機ユニットの構成は図の通りです。
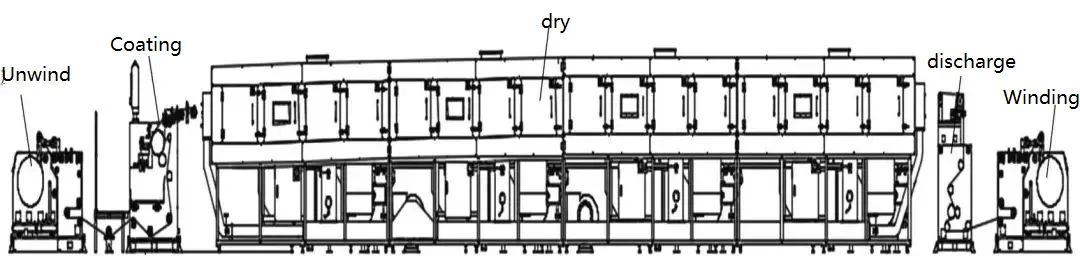
2.1巻き戻しユニット
巻き戻しには、自動テープスプライシングと手動テープスプライシングの2つがあります。手動テープスプライシングおよび巻き戻しユニットを図に示します。

処理する材料は巻出シャフトに取り付けられ、エッジアライメントとテンション制御を受けた後、コーティングセクションに導かれます。デバイスの主な制御ポイントは、巻き戻しエッジの位置合わせと張力制御です。
エッジアライメントは、専用のエッジポジションコントロール(EPC)ユニットによって実現されます。超音波位置検出センサー(透明フィルムを検出可能)は、材料の端の位置を連続的に監視します。巻き戻し装置は、モーターによって駆動されて左右に移動し、材料の端と端の位置合わせセンサーとの間の相対的な位置が一定になります。
エッジアライメントには3つのモードがあります:全自動、電源投入時にシステムが自動的にエッジアライメントを行います(モーターを駆動するためのセンサーのフィードバックに基づく)。半自動、システムは自動運転(コーティングとトラクション)中にエッジアライメントを行い、停止時には手動エッジアライメントを行います。手動モードでは、システムのステータスに関係なく、エッジアライメントメカニズムを手動でのみ操作できます。
張力制御は、フローティングローラー位置制御と実際の張力検出制御の2つの部分で構成されています。フローティングローラーの位置制御の原理は次のとおりです:自動運転中、PLCコントローラーは、ポテンショメータからのリアルタイムフィードバック信号(0%〜100%)に基づいてPIDアルゴリズムを使用して巻き戻しシャフトモーターの速度を調整し、一定のフローティングローラー位置(デフォルト位置は50%に設定されています)を維持することを目指します。
2.2コーティングユニットと供給および間欠バルブシステム
(1)コーティングユニット
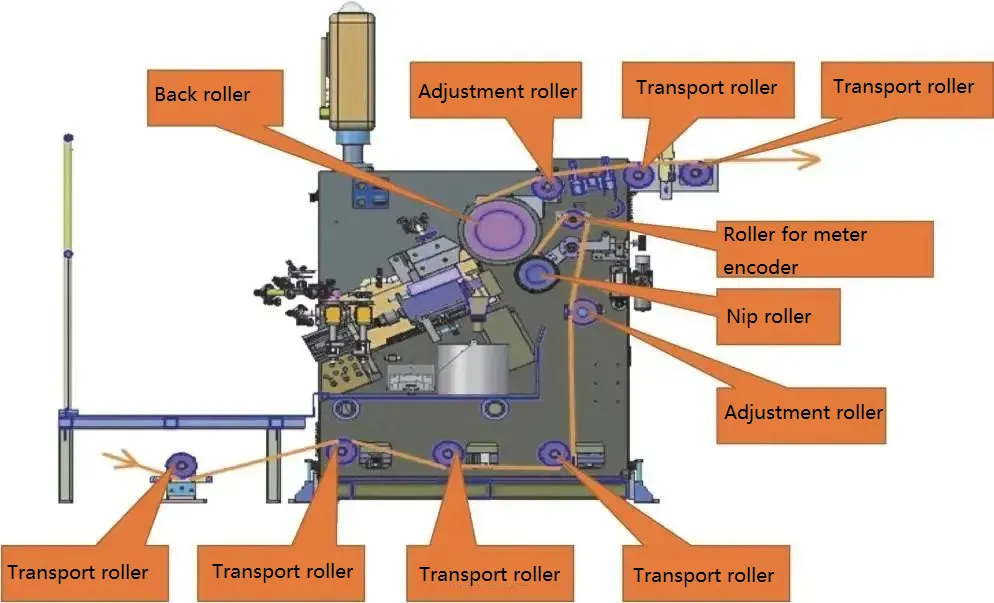
材料は、巻き戻しユニットからコーティングローラーに供給された後、張力分離(巻き戻しと排出の間の張力を分離する)のための供給圧力ローラーを通過し、次にコーティングローラーを通過してから乾燥炉に導かれます。この装置の主な制御点は、機械全体の速度の安定性と、ダイとバッキングローラーの間のギャップ値です。
ダイとバッキングローラの間の変位は、2つの部分によって駆動されます。大規模な移動はシリンダー(前進と後退)を介して達成され、正確な位置決めは左右のサーボモーターによって駆動されます(実際の変位は0.1μmの分解能を持つ高精度リニアエンコーダーによって検出されます)。
(2)給餌システム
供給システムには、材料貯蔵タンク、計量ポンプ、鉄除去器、フィルター、および接続されたパイプが含まれます。最初に、スラリーは貯蔵タンクに追加されます。コーティングが開始されると、貯蔵タンク内のスラリーは、接続されたパイプ、鉄除去器、およびフィルターを介してスロットダイにポンプで送られ、コーティングされます。レベルセンサーが貯蔵タンク内のスラリーが指定されたレベルに達したことを検出すると、貯蔵タンクへの供給が開始されます。スラリーが指定されたレベルに達すると、レベルセンサーは貯蔵タンクへの供給を停止するコマンドを送信します。
2.1乾燥ユニット
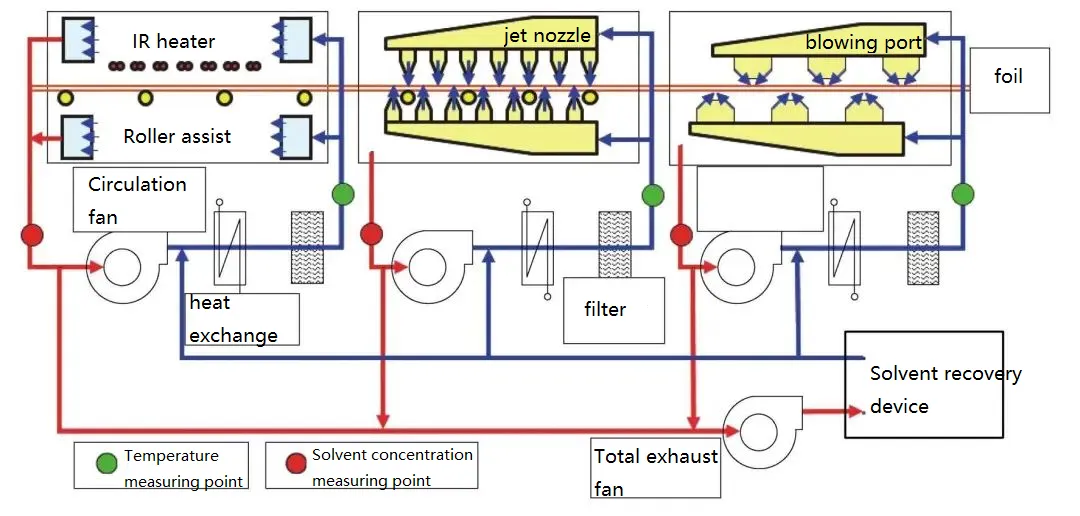
乾燥原理の概略図を図に示します
コーティングユニットによって生成された液体溶剤成分を含むスラリーは、フィルムとともに乾燥炉に入ります。溶剤を安全かつ効果的に蒸発させるためには、乾燥炉の各部の温度、空気供給、排気量などの制御が必要です。シングルセクション温度制御システムは、発熱体と循環ファンで構成されています。ファンは可変周波数モーターによって駆動され、周波数(周波数に正比例)を設定することで風量と速度を調整できます。センサーで検出した温度制御点の温度変化を一定に制御することで、加熱温度を維持し、乾燥プロセスの品質を確保しています。
2.2排出ユニット
乾燥後、フィルムは放電装置に入ります。排出装置は、乾燥炉内のフィルムの張力とエッジ位置を制御します。この装置の主な制御点は、乾燥エリアのエッジアライメントと張力制御です。
エッジアライメントは巻き戻しユニットと似ており、専用のエッジポジションコントロール(EPC)システムを利用しています。エッジ位置検出センサーは、フィルムのエッジの位置を連続的に監視し、放電デバイスは、フィルムのエッジとエッジアライメントセンサーとの間の相対位置を一定に保つために、その位置を調整します。
2.3巻き戻しユニット
巻き方には、自動巻きと手巻きの2つの方法があります。
生産完了後、完成したフィルムはエッジアライメントとテンションコントロールを経て、巻線シャフトに導かれます。この装置の主な制御点は、巻き戻しユニットと同様の巻き取りプロセス中のエッジアライメントと張力制御です。
巻線プロセス中、層間の滑りを防ぎ、過度の締め付けやコアの引っ張りを避けるために、巻線テンションテーパーを調整する必要があります。
03機材選び
3.1機器選択の原則
(1)安全第一:
当社のコーティング機にはNMP有機溶剤が存在するため、業界標準の「リチウムイオン電池工場の設計基準」(GB 51377-2019)に従って、厳格な防爆要件を満たす必要があります。
(2)バッテリーの安全性確保と異物混入の防止
リチウムイオン電池の製造工程では、異物金属粒子の侵入を防ぐことが重要です。したがって、スラリーや電極シートと接触する部品や、それらに近接する部品は、銅、亜鉛、または錫で作ってはいけません。
(3)機器とパラメータの選択:
現在、スロットダイコーティング法が主に使用されています。
(4)コーティングダイの選定:
(1)電池スラリーは非ニュートン流体であるため、レオロジーパラメータ試験が必要です。通常、これらのパラメータを決定するために、特殊なレオメータが使用されます。コーティングダイの流路形状は、計算されたレオロジーパラメータとシミュレーション結果に基づいて設計し、コーティング精度を確保する必要があります。
(2)コーティングダイは25°の上向きの角度で取り付けることをお勧めします。これにより、ダイ洗浄後のパイプラインやキャビティからの迅速なエア放出が可能になり、エア排気機能の代わりとなるダイリターンフローパイプの使用を防ぐことができます。
(3)フィードポンプの選択:
通常、高精度の定量スクリューポンプが使用されます。ポンプの仕様とモデルは、必要な流量に基づいて選択されます。ポンピング精度を向上させるためには、脈動を減らし、高精度を確保するデュアルポンプ構造が推奨されます。
(4)乾燥炉の選定
(1)各セクションの全長と長さ:
まず、乾燥炉の各セクションの長さを決定します。各セクションの長さは4m以上にすることをお勧めします。乾燥速度が速いほど、断面の長さは長くする必要があります。ただし、輸送と組み立ての実現可能性を考慮する必要があります。各セクションの最大長は5mを超えないようにすることをお勧めします。乾燥炉の全長の決定は、乾燥プロセスとコーティング速度のパラメータに基づいており、これらは通常、ユーザーによって提供されます。その後、機器メーカーはこれらのプロセス要件を満たします。
(2)炉内での乾燥温度範囲:
推奨温度範囲は室温から140°Cまでです。特定のプロセス要件がある場合は、カスタマイズを検討できます。一般的に、最高温度は160°Cを超えてはなりません。
(3)炉内の乾燥空気速度の範囲:
5〜20m / sの範囲が推奨され、ノズル精度は±20%以内です。
(5)乾燥炉内の基板輸送:
(1)厚さが6〜10μmを超える銅/アルミホイル基板の場合、アクティブガイドローラーとフローティング乾燥炉の組み合わせを使用することをお勧めします。
(2)厚さが6〜10μm未満の銅/アルミホイル基板の場合、引張強度が低下するため、アクティブガイドローラーの使用をお勧めします。
巻線径の選択:
巻き戻しの直径は、入ってくる材料の直径に基づいて一致するため、ここでは詳しく説明しません。ただし、巻線径を選択するための手法があります。スリット加工や型抜き加工で得られた個々の電極シートの累積長さから大型ロールの長さを決定し、巻径に変換することをお勧めします。計算式は次のとおりです。
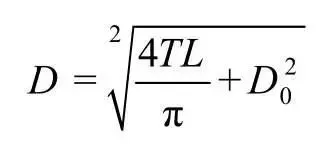
式では、Dはコイルの直径です。D0 は下部の円柱の直径です。Tは電極シートの厚さです。Lは電極シートの長さです。
このようにしてのみ、材料の利用率を高め、廃棄物を減らし、コストを削減することができます。自動化の進歩により、式によれば、下部シリンダーの直径を大きくすると、電極シートのロール全体の長さをより長くすると同時に、下部電極シートの圧力を下げることができることがわかります。巻線品質を向上させます。