La tecnología de recubrimiento es un proceso basado en el estudio de las propiedades de los fluidos, que consiste en aplicar una o varias capas de líquido sobre un sustrato. El sustrato suele ser una película o papel flexible. A continuación, el recubrimiento líquido se seca o cura mediante métodos como el secado en horno para formar una capa con una funcionalidad especial, como en el caso del recubrimiento de electrodos de batería de iones de litio. Actualmente, los principales métodos para recubrir los electrodos de las baterías de iones de litio son el recubrimiento de transferencia de rodillo de coma y el recubrimiento de extrusión de matriz de ranura.
01 Principio y clasificación de la máquina de recubrimiento
El principio del equipo de recubrimiento de electrodos implica la mezcla uniforme de los materiales necesarios para la formulación del electrodo positivo o negativo, seguida de la aplicación o laminación en el anverso y el reverso de papel de aluminio o papel de cobre. Si es necesario, se puede utilizar un dispositivo electromecánico integrado para cumplir con los requisitos técnicos del cliente mediante la evaporación del solvente de la suspensión mediante la conducción de energía.
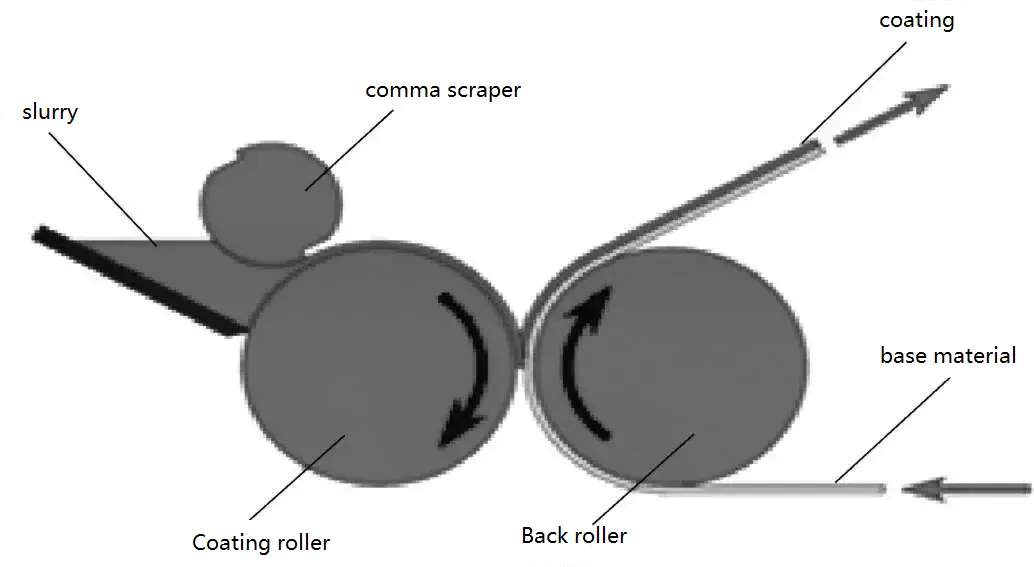
Al ajustar el espacio entre el rodillo de recubrimiento y la cuchilla de coma, la lechada se dosifica en el rodillo de recubrimiento. A continuación, ajustando el espacio entre el rodillo trasero y el rodillo de recubrimiento, toda la lechada dosificada en el rodillo de recubrimiento se transfiere a la lámina.
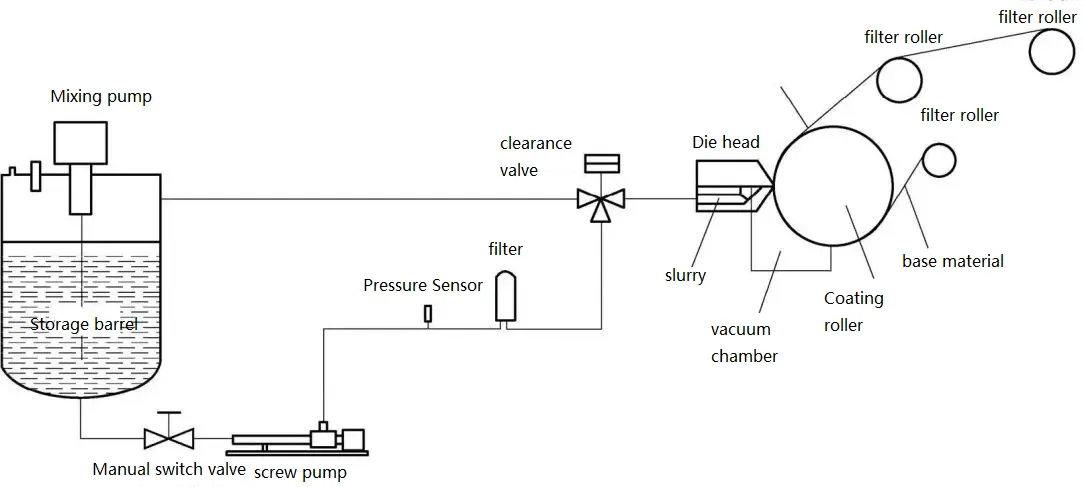
Este es un dispositivo para recubrimiento dosificado de alta precisión, que aplica uniformemente lodos fluidos newtonianos o no newtonianos sobre la superficie de un sustrato a través de una bomba dosificadora y una matriz de ranura. La fórmula para calcular el espesor del recubrimiento es la siguiente:
Espesor del recubrimiento = caudal de la bomba dosificadora / (ancho del recubrimiento * velocidad del recubrimiento)
Además, el troquel es un componente crucial del método de recubrimiento del troquel de ranura y es uno de los factores clave que determinan la precisión del recubrimiento. A medida que aumentan las velocidades de recubrimiento, algunos clientes ahora utilizan mecanismos de cámara de vacío para garantizar la calidad del recubrimiento durante los procesos de recubrimiento de alta velocidad. Por lo general, cuando la velocidad de recubrimiento es de ≥30 m / min, se debe considerar la estructura de esta cámara de presión negativa.
El diseño del troquel debe tener en cuenta los siguientes factores:
Cálculo y simulación de la cavidad del canal de flujo en base a los parámetros reológicos del purín.
Requisitos para la planitud y rectitud de los labios superiores e inferiores del troquel.
Selección del material para el troquel, preferiblemente de acero inoxidable.
Prevención de la generación de partículas extrañas metálicas durante su uso. Si es inevitable, se debe implementar una protección adecuada para evitar que entren partículas extrañas en el lodo.
Facilidad de desmontaje y limpieza.
Principio de la preparación de electrodos por método seco (como se muestra en el diagrama):
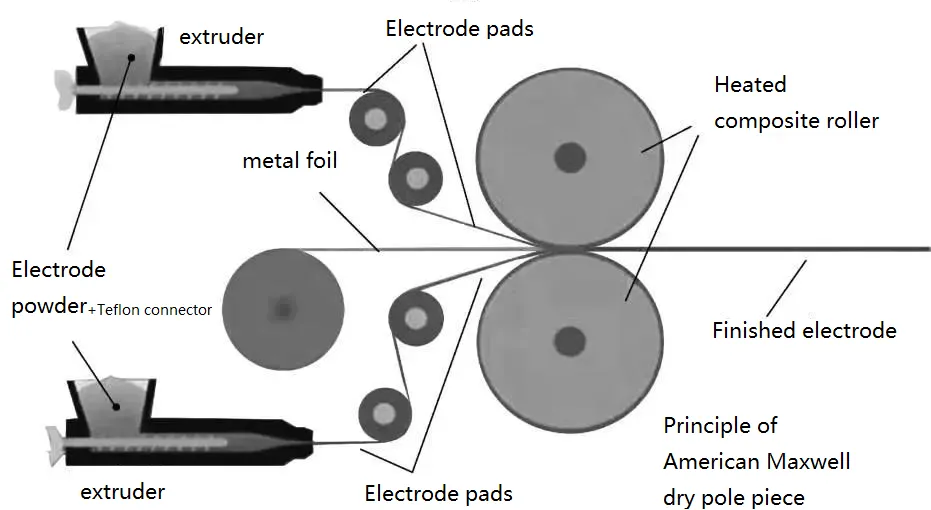
La tecnología de recubrimiento tiene el potencial de ser una innovación disruptiva, especialmente cuando se combina con la tecnología de baterías de estado sólido, para satisfacer las necesidades de las futuras baterías de litio avanzadas. Por ejemplo, la combinación de electrolitos de estado sólido de sulfuro y tecnología de electrodos de método seco es muy prometedora. Las ventajas de esta tecnología son las siguientes:
Puede cumplir con los estrictos requisitos ambientales en Europa, lo que hace que el proceso de producción sea respetuoso con el medio ambiente.
Garantiza la seguridad durante la producción. Los lodos de recubrimiento de cátodos de baterías de litio tradicionales utilizan NMP (N-metil-2-pirrolidona) como solvente, que tiene características de seguridad deficientes.
El costo de inversión en el equipo es bajo y requiere una huella más pequeña con requisitos de humedad ambiental reducidos.
Permite la producción de películas de electrodos más gruesas, lo que permite la misma capacidad de energía volumétrica al tiempo que ahorra en materiales de lámina y separador. Esto proporciona ventajas significativas en términos de costo de la lista de materiales (BOM).
02 Composición del equipo y estructura clave
El equipo consta de cinco partes principales: unidad de desenrollado, unidad de recubrimiento (incluido el sistema de alimentación), unidad de secado, unidad de descarga y unidad de bobinado. La configuración de la unidad de la máquina de recubrimiento es la que se muestra en el diagrama.
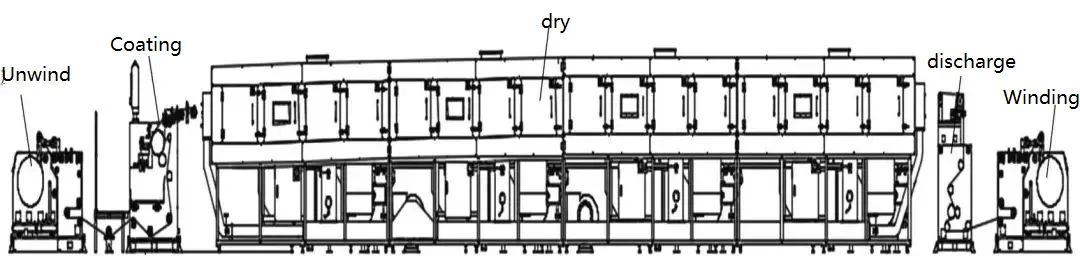
2.1 Unidad de desbobinado
Hay dos métodos de desenrollado: empalme automático de cinta y empalme manual de cinta. La unidad manual de empalme y desenrollado de cinta se muestra en la figura.

El material a procesar se instala en el eje de desenrollado y se guía hacia la sección de recubrimiento después de someterse a la alineación de los bordes y al control de tensión. Los principales puntos de control del dispositivo son el desenrollado, la alineación de los bordes y el control de la tensión.
La alineación de bordes se logra mediante una unidad de control de posición de bordes (EPC) dedicada. Un sensor ultrasónico de detección de posición (capaz de detectar películas transparentes) monitorea continuamente la posición del borde del material. El dispositivo de desenrollado es accionado por un motor para moverse hacia la izquierda o hacia la derecha, lo que garantiza una posición relativa constante entre el borde del material y el sensor de alineación de bordes.
Hay tres modos de alineación de bordes: totalmente automático, donde el sistema activa automáticamente la alineación de bordes al encenderse (en función de la retroalimentación del sensor para impulsar el motor); semiautomático, en el que el sistema activa la alineación de los bordes durante el funcionamiento automático (recubrimiento y tracción) y la alineación manual de los bordes durante la parada; y el modo manual, en el que el mecanismo de alineación de bordes solo puede accionarse manualmente independientemente del estado del sistema.
El control de tensión consta de dos partes: control de posición del rodillo flotante y control de detección de tensión real. El principio del control de la posición del rodillo flotante es el siguiente: durante el funcionamiento automático, el controlador PLC ajusta la velocidad del motor del eje de desenrollado utilizando un algoritmo PID basado en la señal de retroalimentación en tiempo real (0% a 100%) del potenciómetro, con el objetivo de mantener una posición constante del rodillo flotante (la posición predeterminada se establece en 50%).
2.2 Unidad de recubrimiento y sistema de válvulas de alimentación e intermitentes
(1) Unidad de recubrimiento
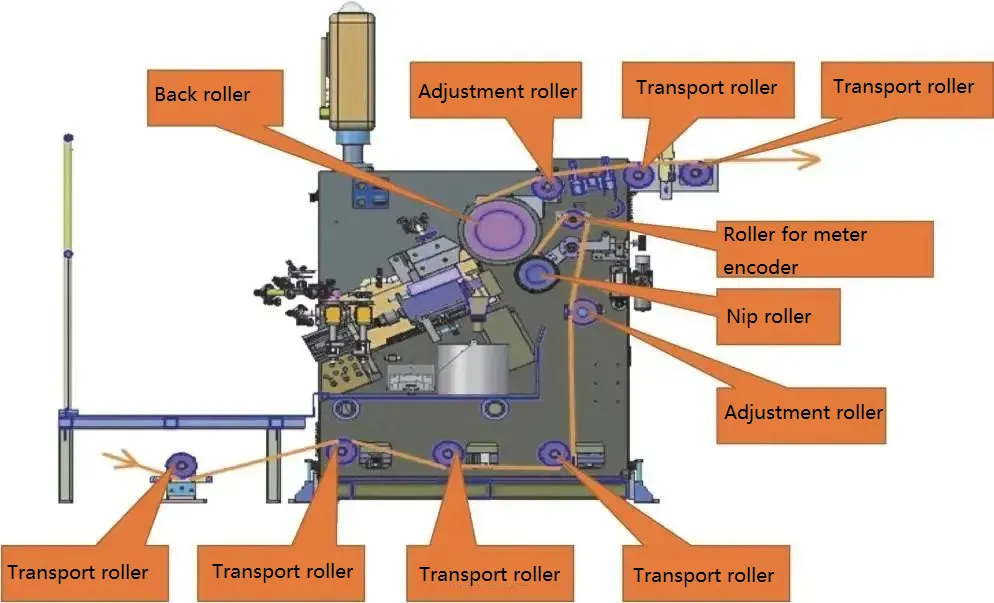
Después de que el material se introduce en el rodillo de recubrimiento desde la unidad de desenrollado, pasa a través del rodillo de presión de alimentación para el aislamiento de la tensión (separando la tensión entre el desenrollado y la descarga) y luego pasa a través del rodillo de recubrimiento antes de ser guiado al horno de secado. Los principales puntos de control de este dispositivo son la estabilidad de la velocidad total de la máquina y el valor del espacio entre el troquel y el rodillo de respaldo.
El desplazamiento entre el troquel y el rodillo de apoyo es accionado por dos partes. El movimiento a gran escala se logra a través de cilindros (hacia adelante y hacia atrás), mientras que el posicionamiento preciso es impulsado por servomotores en los lados izquierdo y derecho (desplazamiento real detectado por codificadores lineales de alta precisión con una resolución de 0,1 μm).
(2) Sistema de alimentación
El sistema de alimentación incluye un tanque de almacenamiento de material, una bomba dosificadora, un removedor de hierro, un filtro y tuberías conectadas. Inicialmente, el lodo se agrega al tanque de almacenamiento. Una vez que comienza el recubrimiento, la lechada en el tanque de almacenamiento se bombea a través de las tuberías conectadas, el removedor de hierro y el filtro en el troquel de ranura para el recubrimiento. Cuando el sensor de nivel detecta que el lodo en el tanque de almacenamiento alcanza el nivel especificado, comienza la alimentación al tanque de almacenamiento. Cuando el lodo alcanza el nivel designado, el sensor de nivel envía un comando para detener la alimentación del tanque de almacenamiento.
2.1 Unidad de secado
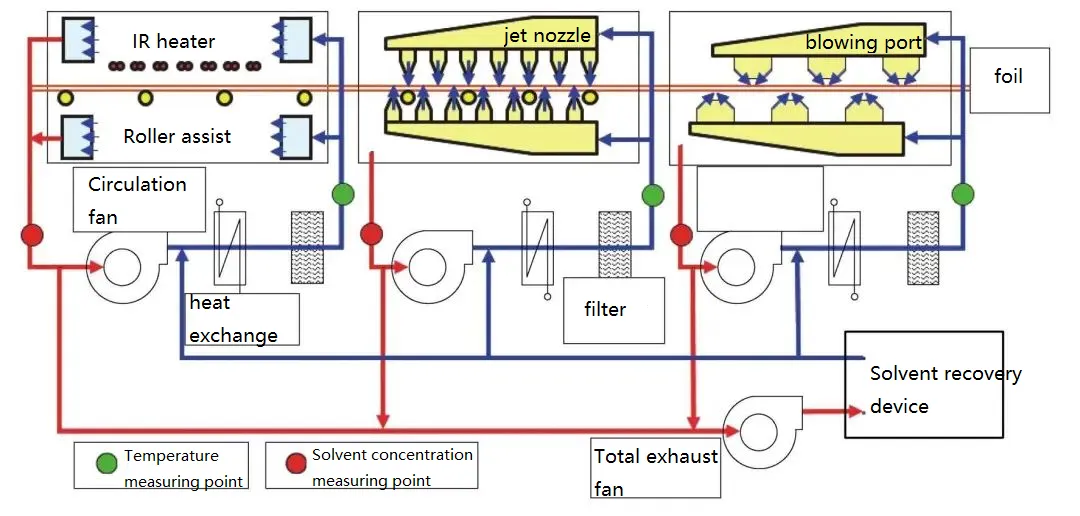
El diagrama esquemático del principio de secado se muestra en la figura
La lechada que contiene componentes solventes líquidos, producidos por la unidad de recubrimiento, ingresa al horno de secado junto con la película. Para evaporar el solvente de manera segura y efectiva, es necesario controlar la temperatura, el suministro de aire, el volumen de escape y otros parámetros en cada sección del horno de secado. El sistema de control de temperatura de una sola sección consta de elementos calefactores y ventiladores circulantes. Los ventiladores son accionados por motores de frecuencia variable, y el volumen y la velocidad del aire se pueden ajustar ajustando la frecuencia (que es directamente proporcional a la frecuencia). La temperatura de calentamiento se mantiene a través de un control constante basado en cambios de temperatura en puntos de control de temperatura detectados por sensores, lo que garantiza la calidad del proceso de secado.
2.2 Unidad de descarga
Después del secado, la película ingresa al dispositivo de descarga. El dispositivo de descarga controla la tensión y la posición del borde de la película dentro del horno de secado. Los principales puntos de control de este dispositivo son la alineación de los bordes y el control de la tensión en el área de secado.
La alineación de bordes es similar a la unidad de desenrollado, utilizando un sistema de control de posición de bordes (EPC) dedicado. Un sensor de detección de posición de bordes monitorea continuamente la posición del borde de la película, y el dispositivo de descarga ajusta su posición para mantener una posición relativa constante entre el borde de la película y el sensor de alineación de bordes.
2.3 Unidad de rebobinado
Hay dos métodos de bobinado: bobinado automático y bobinado manual.
Una vez finalizada la producción, la película terminada pasa por la alineación de los bordes y el control de tensión antes de ser guiada al eje de bobinado. Los principales puntos de control de este dispositivo son la alineación de los bordes y el control de la tensión durante el proceso de bobinado, que son similares a la unidad de desenrollado.
Durante el proceso de bobinado, para evitar el deslizamiento entre capas y evitar una tensión excesiva o la tracción del núcleo, es necesario ajustar el cono de tensión del devanado.
03 Selección de equipos
3.1 Principios de selección de equipos
(1) La seguridad es lo primero:
Debido a la presencia de solvente orgánico NMP en nuestra máquina de recubrimiento, se deben cumplir estrictos requisitos a prueba de explosiones, de acuerdo con el estándar de la industria "Estándar de diseño para fábricas de baterías de iones de litio" (GB 51377-2019).
(2) Garantizar la seguridad de la batería y prevenir la contaminación por metales extraños:
Durante el proceso de producción de baterías de iones de litio, es crucial evitar la introducción de partículas metálicas extrañas. Por lo tanto, los componentes que entran en contacto con la lechada y las láminas de electrodos o que están muy cerca de ellos no deben estar hechos de cobre, zinc o estaño.
(3) Selección de equipos y parámetros:
Actualmente, se utiliza principalmente el método de recubrimiento de matriz de ranura.
(4) Selección de la matriz de recubrimiento:
(1) Dado que la lechada de la batería es un fluido no newtoniano, es necesario realizar pruebas de parámetros reológicos. Por lo general, se utilizan reómetros especializados para determinar estos parámetros. La forma del canal de flujo del troquel de recubrimiento debe diseñarse en función de los parámetros reológicos calculados y los resultados de la simulación para garantizar la precisión del recubrimiento.
(2) Se recomienda instalar el troquel de recubrimiento en un ángulo ascendente de 25 °. Esto permite una rápida liberación de aire de las tuberías y cavidades después de limpiar el troquel y evita el uso de un tubo de flujo de retorno del troquel como sustituto de la función de escape de aire.
(3) Selección de la bomba de alimentación:
Por lo general, se utiliza una bomba de tornillo dosificador de alta precisión. Las especificaciones y el modelo de la bomba se seleccionan en función del caudal requerido. Para mejorar la precisión del bombeo, se recomienda una estructura de doble bomba, que reduce las pulsaciones y garantiza una alta precisión.
(4) Selección del horno de secado:
(1) Longitud total y longitud de cada sección:
Primero, determine la longitud de cada sección del horno de secado. Se recomienda que la longitud de cada sección no sea inferior a 4 m. Cuanto más rápida sea la velocidad de secado, mayor debe ser la longitud de la sección. Sin embargo, se debe tener en cuenta la viabilidad del transporte y el montaje. Se recomienda que la longitud máxima de cada tramo no supere los 5 m. La determinación de la longitud total del horno de secado se basa en el proceso de secado y los parámetros de velocidad de recubrimiento, que suelen ser proporcionados por el usuario. A continuación, el fabricante del equipo cumple con estos requisitos del proceso.
(2) Rango de temperatura para el secado en el horno:
El rango de temperatura recomendado es desde temperatura ambiente hasta 140 °C. Si hay requisitos específicos del proceso, se puede considerar la personalización. En general, la temperatura máxima no debe superar los 160 °C.
(3) Rango de velocidad del aire de secado en el horno:
Se recomienda un rango de 5 a 20 m/s, con una precisión de la boquilla del ±20%.
(5) Transporte de sustrato en el horno de secado:
(1) Para sustratos de papel de cobre/aluminio con un espesor superior a 6-10 μm, se recomienda utilizar una combinación de rodillos guía activos y un horno de secado flotante.
(2) Para sustratos de papel de cobre / aluminio con un espesor inferior a 6-10 μm, debido a la resistencia a la tracción reducida, se recomienda utilizar rodillos guía activos.
Selección del diámetro del devanado:
Dado que el diámetro de desenrollado coincide con el diámetro del material entrante, no proporcionaré una explicación detallada aquí. Sin embargo, existen técnicas para seleccionar el diámetro del devanado. Se recomienda determinar la longitud del rollo grande en función de la longitud acumulada de las láminas de electrodos individuales obtenidas del corte longitudinal o troquelado, y luego convertirlo en un diámetro de bobinado. La fórmula de cálculo es la siguiente:
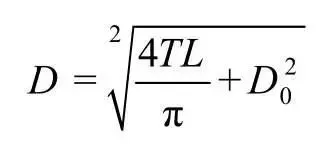
En la fórmula, D es el diámetro de la bobina; D0 es el diámetro del cilindro inferior; T es el espesor de la lámina del electrodo; L es la longitud de la lámina del electrodo.
Solo de esta manera se puede aumentar la tasa de utilización de materiales, reducir los desperdicios y reducir los costos. Debido a la mejora en la automatización, de acuerdo con la fórmula, se puede ver que aumentar el diámetro del cilindro inferior puede aumentar mejor la longitud de todo el rollo de lámina de electrodo y, al mismo tiempo, reducir la presión de la lámina de electrodo inferior. Mejorar la calidad del bobinado.