1.负极涂层出现针孔的原因是什么?是因为物料分散不好吗?有没有可能材料的粒度分布不好?
负极涂层中出现针孔可归因于以下几个因素:
1.1铝箔表面有杂质。
1.2导电剂的分散性差。
1.3负极活性物质分散不充分。
1.4配方中某些成分中的杂质。
1.5导电剂颗粒分布不均匀,分散困难。
1.6负极颗粒分布不均匀,分散困难。
1.7配方材料本身的质量问题。
1.8由于清洗不彻底,混合罐内残留干粉。
要确定具体原因,有必要进行过程监控和分析。关于隔板黑点的问题,我多年前就遇到过。我先简单回答一下。如果我错了,请纠正我。确实是电池运行过程中由于极化放电导致隔膜内局部高温引起的。这种极化放电是材料和工艺相关因素的结果,其中活性材料颗粒附着在果冻卷上,并在电池充电过程中导致极化放电。为避免这些问题,采用适当的浆料工艺来解决活性材料和集流体之间的粘附问题非常重要。此外,在电极制造和电池组装过程中应小心,以防止粉末脱落。在涂覆过程中添加某些不影响电池性能的添加剂,可以提高电极的特定性能。这些添加剂也可以包含在电解液中,以达到固结效果。隔膜中的局部高温确实是电极不均匀引起的,可以认为是微短路的一种形式。微短路会导致局部高温和负极粉末可能脱落。
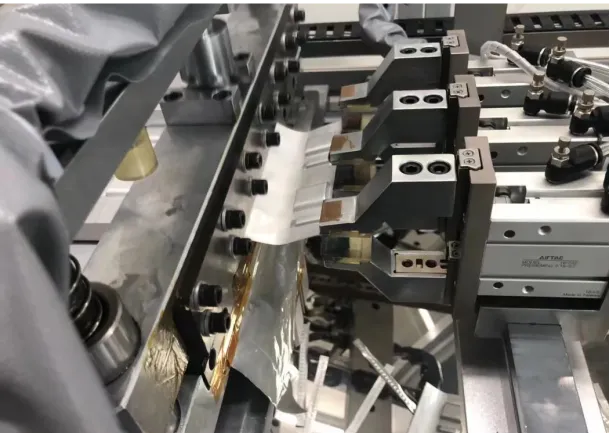
2.电池内阻过大的原因有哪些?
在工艺因素方面:
2.1正极配方中的导电剂不足(材料之间的导电性差,因为钴锂本身的导电性很差)。
2.2正极配方中粘结剂过量(粘结剂一般是具有较强绝缘性能的高分子材料)。
2.3负极配方中粘结剂过多(粘结剂一般是绝缘性能强的高分子材料)。
2.4成分分散不均匀。
2.5成分混合过程中粘合剂的溶剂溶解不完全(不能完全溶解在NMP或水中)。
2.6涂层和浆料表面密度过高(离子迁移距离增加)。
2.7压延密度过大,压延时压制过紧(压延压力过大可能会损坏活性材料的结构)。
2.8弱焊接的正极片,从而产生虚拟焊接。
2.9负极极耳焊接或铆接不牢固,导致虚焊或脱落。
2.10松散的绕组、松弛的绕组单元(增加正负极片之间的距离)。
2.11正极极耳与外壳的弱焊接。
2.12负极极片与电极柱的弱焊接。
2.13电池烘烤温度过高,导致隔膜收缩(减小孔径)。
2.14电解液注入不足(电导率降低,循环后内阻增加!
2.15电解质注射后静置时间不足,电解质浸润不完全。
2.16形成过程中的不完全活化。
2.17形成过程中电解液泄漏过多。
2.18生产过程中对水分控制不当,造成电池膨胀。
2.19充电电压设置过大,导致滥.
2.20电池存放环境不当。
关于材料因素:
2.21正极材料电阻高(导电性差,如磷酸铁锂)。
2.22隔膜材料的影响(厚度、低孔隙率、小孔径)。
2.23电解质材料的影响(低电导率、高粘度)。
2.24 PVDF粘合剂材料对正极的影响(数量过量或分子量高)。
2.25导电剂材料对正极的影响(导电性差,电阻大)。
2.26正负极极片材料的影响(厚度薄、导电性差、厚度不均匀、材料纯度差)。
2.27铜箔或铝箔材料的导电性差,或存在表面氧化物。
2.28盖板和电极柱铆接时接触电阻高。
2.29负极材料的高电阻。
其他因素:
2.30内阻检测设备偏差。
2.31.操作中的人为错误。
3.电极片涂层不均匀。我们应该注意哪些问题?
这个问题很常见,而且相对容易解决。然而,许多涂层操作者不善于总结,这导致将某些存在的问题视为正常且不可避免的现象。首先,重要的是要了解影响涂层表面密度的因素以及影响表面密度稳定值的因素,以便有效地解决问题。影响涂层表面密度的因素包括:
3.1材料因素
3.2配方
3.3混合和混合
3.4涂层环境
3.5刮刀
3.6浆料粘度
3.7电极片的速度
3.8表面平整度
3.9涂布机精度
3.10烤箱气流
3.11涂布张力等
影响电极片均匀性的因素包括:
3.12浆料质量
3.13浆料粘度
3.14电极片的速度
3.15箔片张力
3.16张力平衡法
3.17涂层拉长
3.18噪声
3.19表面平整度
3.20刮刀平整度
3.21箔片均匀度等
这些只是列出的一些因素,有必要分析具体情况,系统地消除导致表面密度异常的因素。
4.正负极的集流体分别由铝箔和铜箔制成,有什么特殊的原因吗?反过来使用它有什么问题吗?M任何文件直接使用不锈钢网。有什么区别吗?
4.1选择使用铜和铝作为集流体主要是因为它们具有良好的导电性、柔软的质地(可以促进键合)、相对通用性和成本效益。此外,铜和铝都可以在其表面形成保护性氧化层。
4.2铜表面的氧化层是半导体,允许电子传导。如果氧化层太厚,则会增加阻抗。另一方面,铝上的氧化层,称为氧化铝,是绝缘体,不导电。然而,由于其薄,电子传导可以通过隧穿效应发生。如果铝上的氧化层太厚,会导致导电性不均匀甚至绝缘。通常建议在使用前清洁集流体表面,以去除油和厚厚的氧化层。
4.3正极具有较高的电位,铝的薄氧化层密度高,有助于防止集流体氧化。相比之下,铜上的氧化层相对多孔。为了防止氧化,最好保持较低的电位。此外,锂难以在低电位下形成锂铜合金。但是,如果铜表面有大量的氧化,锂可以与氧化铜反应,形成电位略高的锂铜合金。铝箔不应用作负极,因为它们可以与锂发生合金化,形成低电位的LiAl合金。
4.4集流器具有纯成分很重要。铝中的杂质会导致形成不致密的表面膜和局部腐蚀,在严重的情况下,由于表面膜的损坏而形成LiAl合金。铜网应在烘烤前用硫酸氢盐清洗并用去离子水冲洗,而铝网应用铵盐清洗并在烘烤前用去离子水冲洗。这种制剂有助于在网状涂层上实现良好的导电性。
5、在测量绕组果冻卷短路时,使用的电池短路测试仪可以准确测试短路电芯在什么电压下。另外,短路测试仪的高压击穿原理是什么?
用于测试电池单元短路的电压取决于几个因素,包括:
5.1公司的制造工艺和专业知识:根据其专业水平,不同的公司可能有不同的电压测试标准和实践。
5.2电池本身的结构设计:电池的内部元件和结构会影响测试短路所需的电压。
5.3电池中使用的膜(隔膜)材料:膜材料的特性会影响所需的电压短路测试。
5.4电池的预期用途:不同的应用可能需要不同的电压水平进行短路测试。
这些因素可以按重要性顺序排序如下:1 > 4 > 3 > 2。这意味着公司的制造工艺和专业知识对确定短路测试的电压影响最大。
简单来说,击穿原理是,如果电极片和隔膜之间有潜在的薄弱点,如灰尘、颗粒、较大的膜孔或毛刺,这些薄弱点可以在正极和负极之间产生较低的内阻。在固定的较高电压下,这些弱点会促进空气的电离,从而导致电弧的产生。或者,如果正负极已经短路并且有一个小的接触点,则大电流可以立即通过这些小接触点,将电能转化为热能,导致膜熔化或瞬时击穿。
6. 材料粒度对放电电流有什么影响?
简单来说,较小的粒径通常会导致更好的电导率,而较大的粒径会导致较差的电导率。因此,高倍率材料通常由具有高导电性的小颗粒组成。然而,虽然这种分析在理论上是正确的,但在小粒径材料中实现高导电性的实际实施是一项具有挑战性的任务,尤其是对于纳米级材料。此外,小粒径的材料往往具有较低的压实密度,这意味着体积容量较小。
7、正负极轧制后,烘烤12小时,存放1天后反弹10um。为什么会出现这么大的反弹?
有两个基本影响因素:材料和工艺。
7.1材料:材料的性能决定了回弹系数。不同的材料具有不同的回弹系数。对于相同的材料,不同的配方会导致不同的回弹系数。此外,对于相同的材料和配方,改变压制板的厚度也会导致不同的回弹系数。
7.2过程:过程控制不佳也会导致反弹。储存时间、温度、压力、湿度等因素,堆垛方法、内应力、设备等都会影响反弹。
8.圆柱电池漏液问题怎么解决?
电解液后的圆柱形电池密封注射是密封过程中一个具有挑战性的方面。目前,有几种方法可用于密封圆柱形电池:
8.1激光焊接密封
8.2用垫圈或O形圈密封
8.3胶粘剂密封
8.4超声波振动密封
8.5上述两种或两种以上密封方法的组合
8.6其他密封方法
有几个因素会导致密封的圆柱形电池漏液:
8.7密封不足:这可能是由于密封区域的变形或污染而发生的,从而导致密封不良。
8.8密封稳定性:即使初封令人满意,如果之后密封区域容易损坏,也可能导致漏液。
8.9在形成或测试过程中产生气体:如果在形成过程中产生气体并达到密封件可以承受的最大应力,则会对密封件造成冲击,导致液体泄漏。这与第二点不同,因为它不是密封缺陷,而是内部压力过大导致密封损坏。
8.10其他泄漏途径:可能还有其他因素或途径导致液体泄漏。
为了解决液体泄漏问题,确定根本原因至关重要。一旦确定了根本原因,就更容易找到合适的解决方案。然而,挑战在于确定原因,因为评估圆柱形电池的密封效果很困难,通常需要破坏性测试或随机采样。
9.在实验过程中,电解质过多。不溢出,多余的电解液会影响电池性能吗?
电解液不溢出的情况有几种: 1.电解液刚刚好2.电解质略微过多3.电解液过大,但未达到极限4.电解质过大,接近极限5。电解液满到极限,OK密封的第一种情况是理想的情况,没有问题。在第二种情况下,轻微超额有时是精度问题,有时是设计问题。一般来说,设计是过度的。第三种情况,没有问题,只是浪费成本。第四种情况有点危险。因为在电池的使用或测试过程中,会有各种原因:电解液会分解并产生一些气体;电池会发热并产生热膨胀;以上两种情况很容易导致电池外壳鼓包(也称为变形)或漏液。液体,这增加了电池的安全隐患。第五种情况实际上是第四种情况的加强版,更加危险。更夸张地说,液体也可以变成电池。即将正负极同时插入装有大量电解液的容器中(如500ML烧杯)。此时,正负极可以充电和放电。它也是电池,所以这里多余的电解液不只是一点点。电解质只是一种导电的介质。但是,电池的容量是有限的。在有限的体积内,自然会考虑空间利用率和变形的问题。
10.如果注入的液体量太少,分电池后会不会造成桶壳?
我只能说不确定,这取决于注射量有多小。1、如果电芯被电解液完全渗入,但没有残留物,则分体积后电池不会鼓起;2.如果电芯完全被电解液渗透,会有少量残留物,但流动性比贵公司要求要多。用量要少一些(当然,这个要求不一定是最优值,会有一点点偏差),此时分容量的电池不会鼓鼓的;3、如果电芯被电解液完全浸泡,会有大量的电解液残留,但贵公司对注液量的要求高于实际量。这时候,所谓的注液量不足只是一个公司的概念,并没有真正反映电池实际注液量的适当性。不同容量的电池没有鼓起的外壳;4.大量的注射量不足。这也取决于学位。如果电解液勉强能渗入电芯,分体积后外壳可能会鼓起,也可能不会鼓包,但分体积后电池壳鼓包的概率更大;如果注入电芯的液体量严重不足,那么电池此时会形成电能,不能转化为化学能。此时,分体式容量电芯的鼓壳概率几乎是100%。那么,我们可以做以下总结:假设电池的实际最佳注液量为Mg。如果注液量太小,可分为以下几种情况: 1.注液量= M:电池正常2.注液量略小于M:电池容量未鼓起。容量可能正常或略低于设计值。循环鼓胀的可能性增加,周期表现变差。3、注液量远小于M:电池容量鼓包率相当高。,电池容量低,循环稳定性极差。通常,数十周的容量小于80%。4.M=0,电池无鼓壳,无容量。