1.負極コーティングにピンホールができる理由は何ですか?材料がうまく分散していないからでしょうか?材料の粒度分布が良くない可能性はありますか?
負極コーティングのピンホールの発生は、いくつかの要因に起因する可能性があります。
1.1ホイル表面の不純物。
1.2導電剤の分散不良。
1.3負極活物質の不適切な分散。
1.4製剤の特定の成分中の不純物。
1.5導電剤粒子の不均一な分布と難解な分散。
1.6負極粒子の不均一な分布と分散の難しさ。
1.7製剤材料自体の品質問題。
1.8不完全な洗浄による混合タンク内の残留乾燥粉末。
具体的な原因を特定するためには、プロセスの監視と分析を行う必要があります。セパレーターの黒い斑点の問題については、何年も前に遭遇しました。まず、簡単な答えをします。間違っていたら訂正してください。これは、バッテリー動作中の分極放電によるセパレーター内の局所的な高温によってもたらされます。この分極放電は、材料やプロセスに関連する要因の結果であり、活物質粒子がゼリーロールに付着し、バッテリー充電中に分極放電を引き起こします。これらの問題を回避するためには、活物質と集電体との間の接着に対処するための適切なスラリープロセスを採用することが重要です。また、電極製造や電池の組み立て時には、粉体が剥がれないように注意が必要です。コーティングプロセス中に、バッテリーの性能に影響を与えない特定の添加剤を追加すると、電極の特定の特性を改善できます。これらの添加剤を電解液に配合することで、圧密効果を出すこともできます。セパレータ内の局所的な高温は、電極の不均一性によって実際に引き起こされ、これはマイクロ短絡の一種と見なすことができます。マイクロ短絡は、局所的な高温と負極粉末の電位的剥離につながる可能性があります。
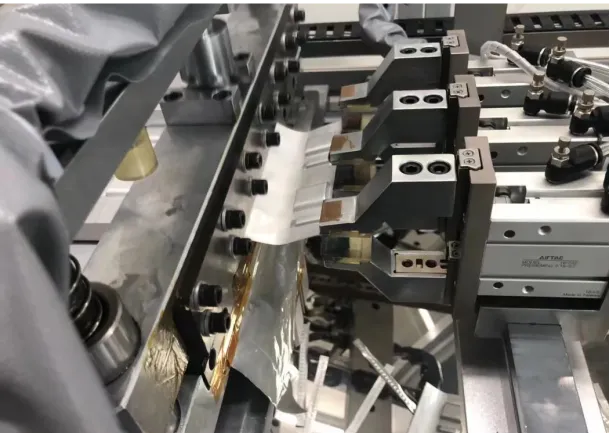
2.バッテリーの内部抵抗が過剰になる原因は何ですか?
プロセス要因に関しては、次のようになります。
2.1正極製剤の導電剤が不十分です(コバルトリチウム自体の導電率が非常に低いため、材料間の導電率が不十分です)。
2.2正極配合の過剰なバインダー(バインダーは一般に強力な絶縁特性を持つポリマー材料です)。
2.3負極配合の過剰なバインダー(バインダーは一般に強力な絶縁特性を持つポリマー材料です)。
2.4成分の不均一な分散。
2.5成分混合中のバインダーの不完全な溶媒溶解(NMPまたは水に完全に溶解することはできません)。
2.6過剰なコーティングとスラリーの表面密度(イオン移動距離の増加)。
2.7過度の圧縮密度、カレンダー加工中の過圧(カレンダー加工圧力が高すぎると、活物質の構造が損傷する可能性があります)。
2.8弱い溶接正極タブの、仮想溶接をもたらします。
2.9負極タブの弱い溶接またはリベット留めにより、仮想溶接または剥離が発生します。
2.10巻線が緩く、巻線セルが緩んでいる(正極シートと負極シートの間の距離が長くなっている)。
2.11正極タブのケーシングへの弱溶接。
2.12負極タブの電極カラムへの弱溶接。
2.13 バッテリーのベーキング温度が高すぎると、セパレーターが収縮します(細孔サイズが小さくなります)。
2.14電解質注入が不十分である(導電率の低下、サイクリング後の内部抵抗の増加)。
2.15電解液注入後の不十分な立位時間、不完全な電解質浸潤。
2.16 フォーメーション中の不完全な活性化。
2.17形成過程での過剰な電解液の漏れ。
2.18製造中の水分管理が不十分で、バッテリーの膨張を引き起こします。
2.19過度の充電ボリュームtage設定、原因過充電.
2.20 バッテリーの保管環境が不適切です。
重要な要因について:
2.21正極材料の高抵抗(リン酸鉄リチウムなどの導電性が低い)。
2.22セパレーター材料の影響(厚さ、低気孔率、小孔サイズ)。
2.23電解質材料の影響(低導電率、高粘度)。
2.24正極におけるPVDFバインダー材料の影響(過剰量または高分子量)。
2.25正極の導電剤材料の影響(導電率が低く、抵抗が高い)。
2.26正と負の電極タブ材料の影響(薄い厚さ、導電率の悪さ、厚さの不均一、材料の純度の悪さ)。
2.27銅箔またはアルミ箔材料の導電性が低い、または表面酸化物の存在。
2.28カバープレートと電極カラムのリベット留めにおける高い接触抵抗。
2.29負極材料の高抵抗。
その他の要因:
2.30内部抵抗試験装置の偏差。
2.31.操作における人為的ミス。
3.電極シートは不均一にコーティングされています。どのような問題に注意を払うべきですか?
この問題は非常に一般的であり、比較的簡単に解決できます。しかし、多くのコーティングオペレーターは要約するのが苦手であり、特定の既存の問題を正常で避けられない現象と見なすことにつながっています。まず、問題を効果的に解決するためには、コーティング表面密度に影響を与える要因と、表面密度の安定値に影響を与える要因を理解することが重要です。コーティング表面密度に影響を与える要因には、次のものがあります。
3.1材料要因
3.2 フォーミュレーション
3.3 ミキシングとブレンディング
3.4 コーティング環境
3.5 ドクターブレード
3.6 スラリー粘度
3.7電極シートの速度
3.8表面の平坦度
3.9 コーティング機の精度
3.10 オーブンの空気の流れ
3.11 コーティングテンションなど
電極シートの均一性に影響を与える要因には、次のものがあります。
3.12 スラリーの品質
3.13 スラリー粘度
3.14電極シートの速度
3.15 ホイルテンション
3.16 テンションバランス法
3.17 コーティングプルの長さ
3.18 ノイズ
3.19表面の平坦度
3.20 ドクターブレードの均一性
3.21箔の均一性など
これらはリストされている要因のほんの一部であり、特定の状況を分析し、異常な表面密度を引き起こす要因を体系的に排除する必要があります。
4.正極と負極の集電体がそれぞれアルミ箔と銅箔でできているのには特別な理由がありますか?逆の使い方に問題はありますか?Mステンレス鋼メッシュを直接使用するドキュメント。何か違いはありますか?
4.1集電体として銅とアルミニウムを使用するという選択は、主に、それらの優れた導電性、柔らかい質感(接着を容易にする)、相対的な共通性、および費用対効果によるものです。さらに、銅とアルミニウムの両方が、その表面に保護酸化物層を形成することができます。
4.2銅の表面にある酸化物層は半導体であり、電子伝導を可能にします。酸化物層が厚すぎると、インピーダンスが増加します。一方、酸化アルミニウムと呼ばれるアルミニウム上の酸化膜は絶縁体であり、電気を通しません。しかし、その薄さゆえに、トンネル効果によって電子伝導が起こることがあります。アルミニウムの酸化物層が厚すぎると、導電性が不均一になったり、絶縁性が均一になったりする可能性があります。一般的には、使用前に集電体の表面を清掃し、油や厚い酸化物層を除去することをお勧めします。
4.3正極は電位が高く、アルミニウムの薄い酸化物層は非常に密度が高いため、集電体の酸化を防ぐのに役立ちます。対照的に、銅の酸化物層は比較的多孔質です。酸化を防ぐためには、電位を低く抑える方が良いでしょう。さらに、リチウムは低電位でリチウム-銅合金を形成するのが困難です。ただし、銅表面にかなりの量の酸化がある場合、リチウムは酸化銅と反応して、わずかに高い電位でリチウム-銅合金を形成する可能性があります。アルミ箔は、リチウムと合金化して低電位でLiAl合金を形成する可能性があるため、負極として使用しないでください。
4.4集電体が純粋な組成を持つことが重要です。アルミニウム中の不純物は、非緻密な表面膜の形成や局所的な腐食につながる可能性があり、深刻な場合には、表面膜の損傷によるLiAl合金の形成につながる可能性があります。銅メッシュは、ベーキングする前にバイサルフェートで洗浄し、脱イオン水ですすいでください。一方、アルミニウムメッシュは、ベーキングする前にアンモニウム塩で洗浄し、脱イオン水ですすいでください。この調製は、メッシュコーティング時に良好な導電性を達成するのに役立ちます。
5.巻線ゼリーロールの短絡を測定するとき、使用されるバッテリー短絡テスターは、どの電圧で短絡セルを正確にテストできます。また、短絡テスターの高電圧ブレークダウン原理は何ですか?
バッテリーセルの短絡をテストするために使用される電圧は、次のようないくつかの要因によって異なります。
5.1会社の製造プロセスと専門知識:会社によって、専門知識のレベルに基づいて電圧試験の基準と慣行が異なる場合があります。
5.2バッテリー自体の構造設計:バッテリーの内部コンポーネントと構造は、短絡のテストに必要な電圧に影響を与える可能性があります。
5.3バッテリーに使用されるメンブレン(セパレーター)材料:メンブレン材料の特性は、必要なボリュームに影響を与える可能性がありますtage短絡テスティング。
5.4バッテリーの使用目的:アプリケーションごとに異なるボリュームが必要になる場合がありますtage短絡テストのレベル。
これらの要因は、1 > 4 > 3 > 2 のように重要度の順にランク付けできます。これは、同社の製造プロセスと専門知識が、短絡テストの電圧の決定に最も大きな影響を与えることを意味します。
簡単に言えば、ブレークダウンの原理は、電極シートとセパレーターの間にほこり、粒子、大きな膜の細孔、バリなどの潜在的な弱点がある場合、これらの弱点が正極と負極の間の内部抵抗を低くする可能性があるということです。固定された高電圧の下では、これらの弱点は空気のイオン化を促進し、電気アークの発生につながる可能性があります。あるいは、正極と負極がすでに短絡していて、接点が小さい場合、これらの小さな接点に大電流が瞬時に流れ、電気エネルギーが熱エネルギーに変換され、膜が溶けたり、瞬間的に故障したりする可能性があります。
6. 材料の粒度は放電電流にどのような影響を与えますか?
簡単に言えば、粒子サイズが小さいほど一般に導電率が高くなり、粒子サイズが大きいほど導電率が悪くなります。その結果、高速材料は、多くの場合、導電性の高い小さな粒子で構成されています。しかし、この分析は理論的には成り立つものの、小さな粒子サイズの材料で高い導電性を達成するための実用化は、特にナノスケールの材料にとって困難な課題です。さらに、粒子サイズが小さい材料は圧縮密度が低くなる傾向があり、これは体積容量が小さくなることを意味します。
7.正極と負極を転がした後、12時間焼いて1日保存した後、10um跳ね返りました。なぜこれほど大きな反発があるのですか?
材料とプロセスという2つの基本的な影響要因があります。
7.1材料:材料の特性によって反発係数が決まります。材料が異なれば、反発係数も異なります。同じ材料でも、配合が異なると、リバウンド係数が異なる可能性があります。さらに、同じ材料と配合の場合、プレスされたシートの厚さを変えると、リバウンド係数も異なる可能性があります。
7.2プロセス:不十分なプロセス制御もリバウンドの一因となる可能性があります。保管時間、温度、圧力、湿度などの要素、スタッキング方法、内部応力、機器などがリバウンドに影響を与える可能性があります。
8.円筒形電池の漏れ問題を解決する方法は?
電解液後の円筒形電池のシール注射は、シーリングプロセスの難しい側面です。現在、円筒形電池のシールにはいくつかの方法が使用されています。
8.1 レーザー溶接シーリング
8.2 ガスケットまたはOリングによるシーリング
8.3接着剤のシーリング
8.4超音波振動シーリング
8.5上記のシール方法の2つ以上の組み合わせ
8.6 その他のシール方法
密閉された円筒形電池の液漏れを引き起こす可能性のあるいくつかの要因があります。
8.7不十分なシーリング:これは、シーリング領域の変形または汚染が原因で発生し、シーリングが不十分になる可能性があります。
8.8シーリングの安定性:最初のシールが満足のいくものであっても、後でシーリング領域が損傷しやすいと、液漏れにつながる可能性があります。
8.9形成または試験中のガス発生:形成プロセス中にガスが生成され、シールが耐えられる最大応力に達すると、シールに衝撃を与え、液漏れを引き起こす可能性があります。これは2点目と異なり、シールの欠陥ではなく、過剰な内圧によるシールの損傷です。
8.10 その他の漏れ経路:液体の漏れに寄与する追加の要因または経路が存在する可能性があります。
液漏れに対処するには、根本的な原因を特定することが重要です。根本原因が特定されると、適切な解決策を見つけることが容易になります。ただし、円筒形電池のシール効果を評価することは難しく、多くの場合、破壊的なテストやランダムなサンプリングが必要になるため、原因を特定することが課題となります。
9.実験中、電解質が過剰でした。オーバーフローしないと、過剰な電解液がバッテリーの性能に影響を与えますか?
電解液がオーバーフローしないいくつかの状況があります:1.電解液はちょうどいい2。電解液がわずかに過剰です 3.電解液が大きすぎるが、限界4に達していない。電解液が大きすぎて限界5に近い。電解液が限界まで満たされている、OKシーリングの最初の状況は理想的な状況であり、問題はありません。2番目のケースでは、わずかな過剰が精度の問題である場合もあれば、設計上の問題である場合もあります。一般的に、デザインは過剰です。3番目のケースでは、問題はなく、コストの無駄です。4番目の状況は少し危険です。バッテリーの使用またはテスト中に、さまざまな理由があるためです:電解質が分解してガスを生成します。バッテリーが熱くなり、熱膨張が発生します。上記の2つの状況では、バッテリーシェルが膨らんだり(変形とも呼ばれます)、漏れたりする可能性があります。液体は、バッテリーの安全上の問題を高めます。5番目の状況は、実際には4番目の状況の拡張バージョンであり、さらに危険です。もっと大げさに言うと、液体も電池になることがあります。つまり、電解液を多量に含んだ容器(500MLビーカーなど)に正極と負極を同時に挿入します。このとき、正極と負極を充電および放電できます。電池でもあるので、ここの余分な電解液はほんの少しだけではありません。電解質は電気を通す媒体にすぎません。ただし、バッテリーの容量には限りがあります。限られたボリュームの中で、スペースの利用と変形の問題を考えるのは自然なことです。
10.注入する液体の量が少なすぎると、バッテリーを分割した後にドラムシェルが発生しますか?
確実ではないとしか言いようがありませんが、注入量がどれだけ小さいかによります。1.バッテリーセルに電解液が完全に浸透しているが、残留物がない場合、ボリュームを分割してもバッテリーは膨らみません。2.バッテリーセルに電解液が完全に浸透している場合、少量の残留物がありますが、それはあなたの会社の要件よりも液体です。量は少なくする必要があります(もちろん、この要件は必ずしも最適値ではなく、わずかな偏差があります)そして、容量分割されたバッテリーはこの時点で膨らみません。3.バッテリーセルが電解液に完全に浸されている場合、大量の電解液残留物が発生しますが、あなたの会社の液体注入量の要件は実際の量よりも高くなります。現時点では、いわゆる不十分な液体注入量は単なる企業の概念であり、バッテリーの実際の液体注入量の適切性を真に反映しているわけではありません。容量の異なるバッテリーには膨らんだシェルがありません;4。実質的な注入量が不十分です。これも程度によります。電解液がバッテリーセルにかろうじて浸透できる場合、ボリュームを分割した後にシェルが膨らむ場合と膨らまない場合がありますが、ボリュームを分割した後にバッテリーシェルが膨らむ可能性が高くなります。バッテリーセルに注入される液体の量が著しく不足している場合、バッテリーが形成されますこの時点での電気エネルギーは化学エネルギーに変換できません。このとき、分割容量のバッテリーセルのドラムシェルの確率はほぼ100%です。次に、次の要約を作成できます:バッテリーの実際の最適な液体注入量はMgであると仮定します。液体注入量が小さすぎる場合は、次の状況に分けることができます:1.液体注入量= M:バッテリーは正常です2。液体注入量がMよりわずかに少ない:バッテリー容量が膨らんでいません。容量は正常である場合もあれば、設計値よりわずかに低い場合もあります。循環膨張の可能性が高まり、サイクル性能が悪化します。3.液体注入量がMよりはるかに少ない:バッテリー容量の膨らみ率はかなり高いです。、バッテリーの容量は少なく、サイクルの安定性が非常に劣っています。一般的に、容量は数十週間で80%未満です。4.M = 0、バッテリーには膨らんだシェルや容量がありません。