1. ¿Cuál es la razón de los agujeros en el recubrimiento del electrodo negativo? ¿Es porque los materiales no están bien dispersos? ¿Es posible que la distribución del tamaño de partícula del material no sea buena?
La aparición de agujeros en el recubrimiento del electrodo negativo se puede atribuir a varios factores:
1.1 Impurezas en la superficie de la lámina.
1.2 Mala dispersión del agente conductor.
1.3 Dispersión inadecuada del material activo del electrodo negativo.
1.4 Impurezas en ciertos componentes de la formulación.
1.5 Distribución no uniforme y difícil dispersión de las partículas del agente conductor.
1.6 Distribución no uniforme y difícil dispersión de las partículas negativas del electrodo.
1.7 Problemas de calidad con los propios materiales de formulación.
1.8 Polvo seco residual en el tanque de mezcla debido a una limpieza incompleta.
Para determinar las causas específicas, es necesario realizar un seguimiento y análisis del proceso. Con respecto al tema de las manchas negras en el separador, me lo encontré hace muchos años. Primero daré una breve respuesta. Por favor, corríjame si me equivoco. De hecho, es causado por una alta temperatura localizada en el separador debido a la descarga de polarización durante el funcionamiento de la batería. Esta descarga de polarización es el resultado de los materiales y factores relacionados con el proceso, donde las partículas de material activo se adhieren al rollo de gelatina y causan una descarga de polarización durante la carga de la batería. Para evitar estos problemas, es importante adoptar procesos de lodo adecuados para abordar la adhesión entre el material activo y el colector actual. Además, se debe tener cuidado durante la fabricación de los electrodos y el montaje de la batería para evitar que el polvo se desprenda. La adición de ciertos aditivos durante el proceso de recubrimiento, que no afectan el rendimiento de la batería, puede mejorar las propiedades específicas del electrodo. Estos aditivos también se pueden incluir en el electrolito para lograr efectos de consolidación. La alta temperatura localizada en el separador es causada por la falta de uniformidad del electrodo, lo que puede considerarse una forma de microcortocircuito. Los microcortocircuitos pueden provocar una alta temperatura localizada y un posible desprendimiento del polvo del electrodo negativo.
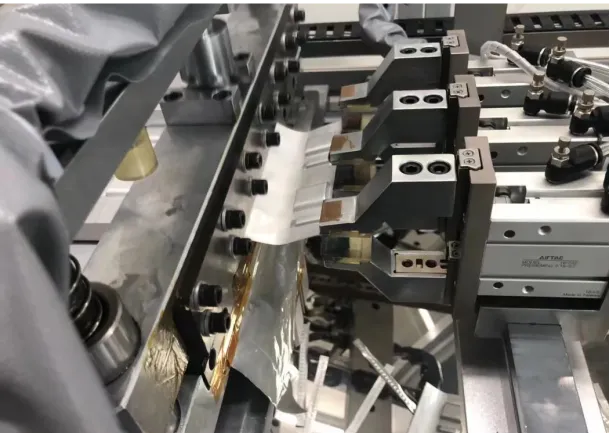
2. ¿Cuáles son las causas de la resistencia interna excesiva de la batería?
En cuanto a los factores del proceso:
2.1 Agente conductor insuficiente en la formulación de electrodos positivos (mala conductividad entre materiales, ya que el cobalto de litio en sí mismo tiene una conductividad muy pobre).
2.2 Exceso de aglutinante en la formulación de electrodos positivos (los aglutinantes son generalmente materiales poliméricos con fuertes propiedades aislantes).
2.3 Exceso de aglutinante en la formulación de electrodos negativos (los aglutinantes son generalmente materiales poliméricos con fuertes propiedades aislantes).
2.4 Dispersión no uniforme de los ingredientes.
2.5 Disolución incompleta de disolventes de aglutinantes durante la mezcla de ingredientes (no se puede disolver completamente en NMP o agua).
2.6 Exceso de densidad superficial de recubrimiento y lechada (aumento de la distancia de migración de iones).
2.7 Densidad de compactación excesiva, sobrepresión durante el calandrado (una presión excesiva del calandrado puede dañar la estructura de los materiales activos).
2.8 Débilsoldadurade lengüetas de electrodos positivos, lo que da como resultado una soldadura virtual.
2.9 Soldadura o remachado débil de las lengüetas de los electrodos negativos, lo que resulta en una soldadura o desprendimiento virtual.
2.10 Bobinado suelto, celda de bobinado relajado (mayor distancia entre las láminas de electrodos positivo y negativo).
2.11 Soldadura débil de las lengüetas de electrodos positivos a la carcasa.
2.12 Soldadura débil de las lengüetas negativas del electrodo a la columna del electrodo.
2.13 Temperatura de horneado excesiva para las baterías, lo que provoca la contracción del separador (reduciendo el tamaño de los poros).
2.14 Inyección insuficiente de electrolito (conductividad reducida, aumento de la resistencia interna después del ciclo).
2.15 Tiempo de reposo insuficiente después de la inyección de electrolito, infiltración incompleta de electrolito.
2.16 Activación incompleta durante la formación.
2.17 Fuga excesiva de electrolito durante el proceso de formación.
2.18 Control inadecuado de la humedad durante la producción, lo que provoca la hinchazón de la batería.
2.19 Ajuste excesivo de la tensión de carga, queSobrecarga.
2.20 Entorno de almacenamiento inadecuado para las baterías.
En cuanto a los factores materiales:
2.21 Alta resistencia del material del electrodo positivo (mala conductividad, como el fosfato de hierro y litio).
2.22 Influencia del material separador (espesor, baja porosidad, tamaño de poro pequeño).
2.23 Influencia del material electrolítico (baja conductividad, alta viscosidad).
2.24 Influencia del material aglutinante PVDF en el electrodo positivo (cantidad excesiva o alto peso molecular).
2.25 Influencia del material del agente conductor en el electrodo positivo (mala conductividad, alta resistencia).
2.26 Influencia de los materiales de las lengüetas de electrodos positivos y negativos (espesor delgado, conductividad deficiente, espesor desigual, pureza del material pobre).
2.27 Mala conductividad del material de papel de cobre o papel de aluminio, o presencia de óxidos superficiales.
2.28 Alta resistencia de contacto en el remachado de la placa de cubierta y la columna de electrodos.
2.29 Alta resistencia del material del electrodo negativo.
Otros factores:
2.30 Desviación en el equipo de prueba de resistencia interna.
2.31. Error humano en las operaciones.
3.Las láminas de electrodos están recubiertas de manera desigual. ¿A qué cuestiones debemos prestar atención?
Este problema es bastante común y es relativamente fácil de resolver. Sin embargo, muchos operadores de recubrimientos no son buenos para resumir, lo que lleva a considerar ciertos problemas existentes como fenómenos normales e inevitables. Primero, es importante comprender los factores que afectan la densidad de la superficie del recubrimiento y los factores que influyen en el valor estable de la densidad de la superficie para resolver el problema de manera efectiva. Los factores que influyen en la densidad de la superficie del recubrimiento incluyen:
3.1 Factores materiales
3.2 Formulación
3.3 Mezclar y mezclar
3.4 Entorno de recubrimiento
3.5 Rasqueta
3.6 Viscosidad de la suspensión
3.7 Velocidad de la lámina de electrodos
3.8 Planitud de la superficie
3.9 Precisión de la máquina de recubrimiento
3.10 Flujo de aire del horno
3.11 Tensión del recubrimiento, etc.
Los factores que afectan la uniformidad de la lámina de electrodos incluyen:
3.12 Calidad de la lechada
3.13 Viscosidad de la suspensión
3.14 Velocidad de la lámina de electrodos
3.15 Tensión de la lámina
3.16 Método de equilibrio de tensión
3.17 Longitud de tracción del recubrimiento
3.18 Ruido
3.19 Planitud de la superficie
3.20 Uniformidad de la rasqueta
3.21 Uniformidad de la lámina, etc.
Estos son solo algunos de los factores enumerados, y es necesario analizar la situación específica y eliminar sistemáticamente los factores que causan una densidad superficial anormal.
4.¿Hay alguna razón especial por la que los colectores de corriente de los electrodos positivo y negativo estén hechos de papel de aluminio y papel de cobre respectivamente? ¿Hay algún problema con usarlo al revés?Mcualquier documento que utilice directamente la malla de acero inoxidable. ¿Hay alguna diferencia?
4.1 La elección de utilizar cobre y aluminio como colectores de corriente se debe principalmente a su buena conductividad, textura suave (que puede facilitar la unión), relativa comunalidad y rentabilidad. Además, tanto el cobre como el aluminio pueden formar una capa protectora de óxido en sus superficies.
4.2 La capa de óxido en la superficie del cobre es un semiconductor y permite la conducción de electrones. Si la capa de óxido es demasiado gruesa, aumenta la impedancia. Por otro lado, la capa de óxido sobre aluminio, conocida como óxido de aluminio, es un aislante y no conduce la electricidad. Sin embargo, debido a su delgadez, la conducción de electrones puede ocurrir a través de efectos de túnel. Si la capa de óxido del aluminio es demasiado gruesa, puede dar lugar a una conductividad desigual o incluso a un aislamiento. Por lo general, se recomienda limpiar las superficies de los colectores actuales antes de su uso para eliminar las capas gruesas de aceite y óxido.
4.3 El electrodo positivo tiene un potencial más alto y la fina capa de óxido del aluminio es muy densa, lo que ayuda a prevenir la oxidación del colector de corriente. Por el contrario, la capa de óxido sobre el cobre es relativamente porosa. Para evitar la oxidación, es mejor mantener el potencial más bajo. Además, el litio tiene dificultades para formar aleaciones de litio y cobre a bajos potenciales. Sin embargo, si hay una cantidad significativa de oxidación en la superficie del cobre, el litio puede reaccionar con el óxido de cobre para formar aleaciones de litio-cobre a potenciales ligeramente más altos. Las láminas de aluminio no deben usarse como electrodos negativos, ya que pueden someterse a una aleación con litio para formar aleaciones de LiAl a bajas potencialidades.
4.4 Es importante que los coleccionistas actuales tengan composiciones puras. Las impurezas en el aluminio pueden provocar la formación de películas superficiales no densas y corrosión localizada y, en casos graves, la formación de aleaciones de LiAl debido al daño de la película superficial. Las mallas de cobre deben limpiarse con bisulfato y enjuagarse con agua desionizada antes de hornear, mientras que las mallas de aluminio deben limpiarse con sales de amonio y enjuagarse con agua desionizada antes de hornear. Esta preparación ayuda a lograr una buena conductividad sobre el recubrimiento de malla.
5. Al medir el cortocircuito del rodillo de gelatina del devanado, el probador de cortocircuito de la batería utilizado puede probar con precisión la celda de cortocircuito a qué voltaje. Además, ¿cuál es el principio de ruptura de alto voltaje del probador de cortocircuito?
El voltaje utilizado para probar cortocircuitos en las celdas de la batería depende de varios factores, entre ellos:
5.1 El proceso de fabricación y la experiencia de la empresa: Diferentes empresas pueden tener diferentes estándares y prácticas para las pruebas de voltaje en función de su nivel de experiencia.
5.2 El diseño estructural de la batería en sí: Los componentes internos y la construcción de la batería pueden influir en el voltaje requerido para probar los cortocircuitos.
5.3 El material de la membrana (separador) utilizado en la batería: Las propiedades del material de la membrana pueden afectar el voltaje necesario paracortocircuitoensayo.
5.4 El uso previsto de la batería: Diferentes aplicaciones pueden requerir diferentes niveles de voltaje para las pruebas de cortocircuito.
Estos factores se pueden clasificar en orden de importancia de la siguiente manera: 1 > 4 > 3 > 2. Esto significa que el proceso de fabricación y la experiencia de la empresa tienen la mayor influencia en la determinación del voltaje para las pruebas de cortocircuito.
En términos simples, el principio de ruptura es que si hay puntos débiles potenciales como polvo, partículas, poros de membrana más grandes o rebabas entre las láminas de electrodos y el separador, estos puntos débiles pueden crear una resistencia interna más baja entre los electrodos positivo y negativo. Bajo un voltaje fijo más alto, estos puntos débiles pueden facilitar la ionización del aire, lo que lleva a la generación de un arco eléctrico. Alternativamente, si los electrodos positivo y negativo ya están en cortocircuito y hay un pequeño punto de contacto, una corriente alta puede pasar a través de estos pequeños puntos de contacto instantáneamente, convirtiendo la energía eléctrica en energía térmica, lo que resulta en la fusión de la membrana o la ruptura instantánea.
6. ¿Cuál es el impacto del tamaño de partícula del material en la corriente de descarga?
En términos simples, un tamaño de partícula más pequeño generalmente conduce a una mejor conductividad, mientras que un tamaño de partícula más grande da como resultado una conductividad más pobre. En consecuencia, los materiales de alta velocidad a menudo consisten en partículas pequeñas con alta conductividad. Sin embargo, si bien este análisis es cierto en teoría, la implementación práctica de lograr una alta conductividad en materiales de tamaño de partícula pequeño es una tarea desafiante, especialmente para materiales a nanoescala. Además, los materiales con tamaños de partícula pequeños tienden a tener una densidad de compactación más baja, lo que se traduce en capacidades de volumen más pequeñas.
7. Después de enrollar los electrodos positivo y negativo, rebotaron 10um después de hornearse durante 12 horas y almacenarse durante un día. ¿Por qué hay un rebote tan grande?
Hay dos factores fundamentales que influyen: el material y el proceso.
7.1 Material: Las propiedades del material determinan el coeficiente de rebote. Diferentes materiales tienen diferentes coeficientes de rebote. Para el mismo material, diferentes formulaciones pueden dar lugar a diferentes coeficientes de rebote. Además, para el mismo material y formulación, variar el grosor de la lámina prensada también puede dar lugar a diferentes coeficientes de rebote.
7.2 Proceso: Un mal control del proceso también puede contribuir al rebote. Factores como el tiempo de almacenamiento, la temperatura, la presión, la humedad,apilamiento El método, la tensión interna, el equipo y más pueden influir en el rebote.
8.¿Cómo resolver el problema de fugas de las baterías cilíndricas?
Sellado de baterías cilíndricas después del electrolitoinyecciónes un aspecto desafiante del proceso de sellado. Actualmente, existen varios métodos utilizados para sellar baterías cilíndricas:
8.1 Sellado por soldadura láser
8.2 Sellado con junta o junta tórica
8.3 Sellado adhesivo
8.4 Sellado por vibración ultrasónica
8.5 Combinaciones de dos o más de los métodos de sellado anteriores
8.6 Otros métodos de sellado
Hay varios factores que pueden causar fugas de líquido en las baterías cilíndricas selladas:
8.7 Sellado insuficiente: Esto puede ocurrir debido a la deformación o contaminación en el área de sellado, lo que resulta en un sellado deficiente.
8.8 Estabilidad del sellado: Incluso si el sellado inicial es satisfactorio, si el área de sellado se daña fácilmente después, puede provocar fugas de líquido.
8.9 Generación de gas durante la formación o prueba: Si se produce gas durante el proceso de formación y alcanza la tensión máxima que el sello puede soportar, puede causar un impacto en el sello, lo que provoca fugas de líquido. Esto es diferente del segundo punto porque no se trata de un defecto en el sello, sino de una presión interna excesiva que causa daños en el sello.
8.10 Otras vías de fuga: Puede haber factores o vías adicionales que contribuyan a la fuga de líquido.
Para hacer frente a las fugas de líquido, es crucial identificar las causas subyacentes. Una vez que se identifican las causas raíz, es más fácil encontrar soluciones adecuadas. Sin embargo, el desafío radica en identificar las causas, ya que evaluar la efectividad del sellado de las baterías cilíndricas es difícil, a menudo requiere pruebas destructivas o muestreo aleatorio.
9.Durante el experimento, el electrolito era excesivo. Sin desbordarse, ¿afectará el exceso de electrolito al rendimiento de la batería?
Hay varias situaciones en las que el electrolito no se desborda: 1. El electrolito es el adecuado 2. El electrolito es ligeramente excesivo 3. El electrolito es excesivamente grande, pero no alcanza el límite 4. El electrolito es excesivamente grande y está cerca del límite 5. El electrolito está lleno hasta el límite, OK La primera situación de sellado es la situación ideal y no hay problema. En el segundo caso, un ligero exceso es a veces un problema de precisión, y a veces es un problema de diseño. Generalmente, el diseño es excesivo. En el tercer caso, no hay problema, es solo una pérdida de costos. La cuarta situación es un poco peligrosa. Porque durante el uso o prueba de la batería, habrá varias razones: el electrolito se descompondrá y producirá algo de gas; la batería se calentará y producirá expansión térmica; Las dos situaciones anteriores pueden hacer que la carcasa de la batería se abulte fácilmente (también llamada deformación) o tenga fugas. fluido, lo que aumenta el peligro de seguridad de la batería. La quinta situación es en realidad una versión mejorada de la cuarta situación y es aún más peligrosa. Para ser más exagerados, los líquidos también pueden convertirse en baterías. Es decir, los electrodos positivo y negativo se insertan en un recipiente que contiene una gran cantidad de electrolito al mismo tiempo (como un vaso de precipitados de 500 ml). En este momento, los electrodos positivo y negativo se pueden cargar y descargar. También es una batería, por lo que el exceso de electrolito aquí no es solo un poco. El electrolito es solo un medio que conduce la electricidad. Sin embargo, el volumen de la batería es limitado. Dentro del volumen limitado, es natural considerar los problemas de la utilización y la deformación del espacio.
10.Si la cantidad de líquido inyectado es demasiado pequeña, ¿causará una carcasa de tambor después de que se divida la batería?
Solo puedo decir que no es seguro, depende de qué tan pequeño sea el volumen de inyección. 1. Si la celda de la batería está completamente infiltrada por el electrolito, pero no hay residuos, la batería no se hinchará después de dividir el volumen; 2. Si la celda de la batería está completamente infiltrada por el electrolito, hay una pequeña cantidad de residuo, pero es más líquido que los requisitos de su empresa. La cantidad debe ser menor (por supuesto, este requisito no es necesariamente el valor óptimo, hay una ligera desviación) y la batería de capacidad dividida no se abultará en este momento; 3. Si la celda de la batería está completamente empapada por el electrolito, habrá una gran cantidad de residuos de electrolito, pero su empresa El requisito de la cantidad de inyección de líquido es mayor que la cantidad real. En este momento, la llamada cantidad insuficiente de inyección de líquido es solo un concepto de la empresa y no refleja realmente la idoneidad de la cantidad real de inyección de líquido de la batería. La batería con diferente capacidad no tiene una carcasa abultada;4. El volumen sustancial de inyección es insuficiente. Esto también depende del grado. Si el electrolito apenas puede infiltrarse en la celda de la batería, la carcasa puede o no abultarse después de dividir el volumen, pero la probabilidad de que la carcasa de la batería se abulte después de dividir el volumen es mayor; Si la cantidad de líquido inyectado en la celda de la batería es muy insuficiente, entonces la batería se formará La energía eléctrica en este momento no se puede convertir en energía química. En este momento, la probabilidad de que la carcasa del tambor de la celda de batería de capacidad dividida sea casi del 100%. Entonces, podemos hacer el siguiente resumen: Supongamos que el volumen óptimo real de inyección de líquido de la batería es Mg. Si el volumen de inyección de líquido es demasiado pequeño, se puede dividir en las siguientes situaciones: 1. Volumen de inyección de líquido = M: la batería es normal 2. El volumen de inyección de líquido es ligeramente inferior a M: La capacidad de la batería no está abultada. La capacidad puede ser normal o ligeramente inferior al valor de diseño. La probabilidad de abultamiento circulatorio aumenta y el rendimiento del ciclo empeora. 3. El volumen de inyección de líquido es mucho menor que M: la tasa de abultamiento de la capacidad de la batería es bastante alta. , la batería tiene baja capacidad y una estabilidad de ciclo extremadamente pobre. Generalmente, la capacidad es inferior al 80% en docenas de semanas. 4. M = 0, la batería no tiene carcasa abultada ni capacidad.