- Vue d’ensemble de la batterie 18650
L’accu 18650 est uncylindriqueBatterie lithium-ion nommée d’après ses dimensions de 18 millimètres de diamètre et 65 millimètres de hauteur. Ce type de batterie offre des avantages tels qu’une densité d’énergie élevée, une longue durée de vie et d’excellentes performances de sécurité. Il est largement utilisé dans les véhicules électriques, les appareils électroniques, les systèmes de stockage d’énergie et d’autres domaines.
- 18650 matières premières de batterie
Matériau de l’électrode positive : Le matériau de l’électrode positive est un composant important de la batterie 18650 et est généralement composé de nitrures de métaux de transition au lithium tels que le NCA (nickel-cobalt-aluminium) et le NMC (nickel-manganèse-cobalt). Ces matériaux offrent des avantages tels qu’une densité d’énergie élevée et d’excellentes performances électrochimiques.
Matériau de l’électrode négative : Le matériau de l’électrode négative est généralement composé de graphite ou de titanate de lithium. Le graphite présente des avantages tels qu’une capacité élevée et de bonnes performances de cyclage, tandis que le titanate de lithium offre des avantages tels qu’une sécurité élevée et une longue durée de vie.
Électrolyte : L’électrolyte est le milieu conducteur de la batterie 18650 et se compose généralement de solvants organiques et de sels de lithium. Les performances de l’électrolyte ont un impact significatif sur les performances électrochimiques et la sécurité de la batterie.
Séparateur : Le séparateur est un composant important de la batterie 18650 et est utilisé pour isoler les électrodes positive et négative afin d’éviter les courts-circuits. Les séparateurs sont généralement fabriqués à partir de matériaux polyoléfines et possèdent d’excellentes propriétés mécaniques et une stabilité chimique.
- Processus de production de la batterie 18650
Fabrication de feuilles d’électrodes : La fabrication de feuilles d’électrodes est la première étape de la production d’une batterie 18650 et implique généralement des processus tels que le mélange, le revêtement, le séchage et le calandrage. Au cours du processus de revêtement, des paramètres tels que l’épaisseur et l’uniformité du revêtement doivent être contrôlés pour garantir la structure et les performances optimales de la feuille d’électrode.
Enroulement : Le bobinage est une étape cruciale dans la fabrication d’une batterie 18650, où les feuilles d’électrodes positives et négatives, ainsi que le séparateur, sont enroulées dans une cellule. Des paramètres tels que la pression et la vitesse d’enroulement doivent être contrôlés pendant le processus d’enroulement pour garantir la structure et les performances optimales de la cellule.
Injection : L’injection fait référence au processus d’injection d’électrolyte dans la cellule, généralement effectué après le processus d’enroulement. Des paramètres tels que le volume et la vitesse d’injection doivent être contrôlés pendant le processus d’injection pour assurer une distribution uniforme de l’électrolyte et éviter la formation de bulles.
Encapsulation : L’encapsulation consiste à loger la cellule dans un boîtier en aluminium ou en acier pour assurer la sécurité et la fiabilité de la batterie.
Test de qualité : Les tests de qualité consistent à effectuer des tests de performance et de sécurité sur la batterie 18650 terminée. Cela comprend des tests de capacité, des tests de durée de vie, des tests de performance en matière de sécurité, etc., pour s’assurer que la batterie répond aux exigences de qualité et de performance attendues.
- Méthodes d’emballage des batteries et contrôle de la qualité
Emballage : L’emballage des batteries 18650 implique généralement l’utilisation de boîtiers en aluminium ou en acier, ainsi que des mesures telles que l’étanchéité à l’humidité et la protection antistatique, pour assurer la sécurité et la stabilité des batteries pendant l’utilisation.
Contrôle de la qualité : Un contrôle de qualité strict est mis en œuvre à chaque étape du processus de production des batteries 18650. Cela comprend le contrôle de la qualité des matières premières, le contrôle du processus pendant la fabrication et les tests de qualité des produits finis. Ce n’est que grâce à un contrôle de qualité rigoureux que la qualité et les performances des produits peuvent être garanties pour atteindre leur état optimal.
- Difficultés et technologies de base dans la fabrication des batteries 18650
Formulation des matériaux : La formulation des matériaux est l’une des technologies clés dans la fabrication des batteries 18650, affectant directement les performances et la sécurité des batteries. Le développement de formulations de matériaux nécessite des tests itératifs et une optimisation pour obtenir les meilleures performances et stabilité.
Contrôle de précision : Le contrôle de précision est une technologie essentielle dans la fabrication des batteries 18650, y compris le contrôle de paramètres tels que l’épaisseur du revêtement, la pression d’enroulement et le volume d’injection. Le contrôle de précision s’appuie sur des équipements de pointe et un contrôle strict des processus pour garantir que la qualité et les performances des produits atteignent leur état optimal.
- Comment garantir l’uniformité des performances des produits
Dans le processus de fabrication des batteries 18650, chaque étape a ses points de contrôle qualité spécifiques pour garantir des performances constantes du produit. Voici une analyse des points de contrôle de la qualité pour chaque étape et de la manière d’assurer des performances constantes du produit :
Préparation du matériau de l’électrode positive et négative : Les points de contrôle de la qualité à cette étape comprennent la taille des particules de matériau, la pureté, la structure de surface, etc. Pour garantir des performances constantes du produit, il est nécessaire de contrôler strictement la provenance et le traitement des matières premières et d’effectuer des inspections de qualité rigoureuses pour chaque lot de matériaux.
Fabrication de la feuille d’électrode : Les points de contrôle de la qualité à cette étape comprennent l’épaisseur du revêtement, l’uniformité, la température de séchage, etc. Pour garantir des performances constantes du produit, des équipements de revêtement avancés doivent être utilisés, une surveillance et un ajustement en temps réel du processus de revêtement doivent être mis en œuvre, et des inspections de qualité strictes pour l’épaisseur et l’uniformité de la feuille d’électrode doivent être effectuées.
Enroulement : Les points de contrôle de la qualité dans cette étape comprennent la pression d’enroulement, la vitesse d’enroulement, le positionnement de la membrane, etc. Pour garantir des performances constantes du produit, un équipement d’enroulement de précision doit être utilisé, une surveillance et un ajustement en temps réel du processus d’enroulement doivent être mis en œuvre, et la précision structurelle et dimensionnelle de chaque cellule doit être assurée.
Injection : Les points de contrôle de la qualité à cette étape comprennent la pureté de l’électrolyte,injectionvolume, vitesse d’injection, etc. Pour garantir des performances constantes du produit,Matériel d’injectionUne surveillance et un ajustement en temps réel du processus d’injection doivent être effectués, et des inspections de qualité strictes pour la pureté de l’électrolyte et le volume d’injection doivent être effectuées.
Encapsulation : Les points de contrôle de la qualité dans cette étape comprennent la qualité du boîtier, la stabilité des circuits de protection, etc. Pour garantir des performances constantes du produit, il convient d’utiliser un équipement d’encapsulation fiable, de mettre en œuvre une surveillance et un ajustement en temps réel du processus d’encapsulation, et d’assurer la stabilité structurelle et les performances de chaque batterie.
À chaque étape du contrôle de la qualité, il est également important de se concentrer sur l’analyse des données et la tenue de registres pour l’amélioration continue et l’optimisation des performances des produits. De plus, tout problème de qualité qui se pose doit être analysé et résolu rapidement pour s’assurer que la qualité et les performances des produits répondent aux exigences attendues.
- Difficultés et technologies de base en 18650Fabrication de batteries
Les défis de la fabrication des batteries 18650 résident principalement dans la formulation des matériaux, le contrôle de précision et la sécurité. La formulation des matériaux est l’un des aspects cruciaux qui ont un impact direct sur les performances et la sécurité de la batterie. De même, le contrôle de précision est une technologie importante dans le processus de fabrication, où des paramètres tels que le revêtement (Équipement connexe) l’épaisseur, la pression d’enroulement et le volume d’injection doivent répondre à des exigences de précision spécifiques. De plus, en raison des exigences de sécurité élevées des batteries, de multiples mesures doivent être prises au cours du processus de fabrication pour garantir leurs performances en matière de sécurité.
En réponse à ces défis et à ces technologies de base, de nombreuses entreprises recherchent et explorent en permanence de nouvelles solutions. Par exemple, ils améliorent la formulation des matériaux et le flux de processus pour améliorer la densité énergétique et la durée de vie de la batterie. Des techniques de contrôle de précision avancées sont adoptées pour améliorer l’efficacité de la fabrication et la qualité des produits. La conception et les tests de sécurité sont renforcés pour garantir les performances de sécurité de la batterie.
- Dans l’attente des tendances de développement et des orientations d’innovation des batteries 18650
Avec le développement continu dans des domaines tels que les véhicules électriques et les appareils électroniques, la demande de batteries 18650 ne cesse d’augmenter. À l’avenir, les batteries 18650 évolueront vers une capacité plus élevée, une charge rapide, la durabilité et le respect de l’environnement. Une capacité élevée améliorera l’autonomie de la batterie, la technologie de charge rapide réduira le temps de charge, et les exigences en matière de durabilité et d’environnement minimiseront l’impact sur l’environnement.
Pour atteindre ces objectifs, il y aura davantage d’innovation technologique et d’activités de recherche et développement à l’avenir. Par exemple, l’amélioration de la formulation des matériaux et du flux de processus pour améliorer la densité énergétique et la durée de vie de la batterie, l’adoption de nouveaux matériaux d’électrolyte et de séparateur pour améliorer les performances de sécurité de la batterie et la recherche de nouvelles technologies de charge rapide pour réduire le temps de charge.
- Si l’on prend l’exemple de la société XX, sa ligne de production de batteries 18650 présente les caractéristiques d’un haut degré d’automatisation et d’intégration intelligente.
Préparation des matières premières : Les systèmes de dosage automatiques sont utilisés pour peser avec précision diverses matières premières en fonction de formulations spécifiques.
Préparation du lisier : Les matières premières sont mélangées uniformément à l’aide de mélangeurs efficaces pour former des boues d’électrodes.
Procédé de revêtement : Double facemachines d’enductionsont utilisés pour enrober uniformément la boue sur des feuilles métalliques, suivi d’un durcissement préliminaire dans des fours de séchage infrarouges.
Calandre et découpe : Les feuilles d’électrodes sont compactées à l’aide de machines à calandrer pour assurer une structure étanche. Ensuite, ils sont coupés dans les tailles appropriées en vue du remontage.
Enroulement et assemblage : Des machines d’enroulement automatiques sont utilisées pour enrouler les feuilles d’électrodes positives et négatives avec un séparateur, formant la cellule. L’assemblage de la cellule est effectué dans un environnement propre.
Injection et scellement : Dans des conditions environnementales strictement contrôlées, les cellules sont injectées d’électrolytes et la technologie de soudage au laser est utilisée pour les sceller.
Tests de formation et de capacité : Les batteries sont activées par un processus de formation, suivi d’un test de capacité pour s’assurer que chaque batterie répond aux normes de performance requises.
Vieillissement et tests : Après une période de vieillissement spécifique, les batteries sont soumises à de multiples tests de performance de sécurité pour garantir leur fiabilité et leur qualité.
- Similitudes et différences dans les processus de fabrication des batteries et les points de contrôle de la qualité des différentes entreprises
Sélection des matériaux : Alors que la plupart des entreprises choisissent des matières premières de haute qualité, certaines entreprises privilégient les matériaux provenant de sources durables.
Niveau d’automatisation : Certaines entreprises ont atteint une production entièrement automatisée, tandis que d’autres s’appuient encore sur la semi-automatisation ou les opérations manuelles. Le niveau d’automatisation affecte l’efficacité de la production et le contrôle des coûts.
Technologie de contrôle de précision : Différentes entreprises utilisent différentes technologies de contrôle de précision dans des processus clés tels que l’enroulement et l’injection. Par exemple, certaines entreprises utilisent une technologie de mesure laser avancée pour la surveillance dimensionnelle.
Stratégies de sécurité : Toutes les entreprises privilégient la sécurité des batteries, mais les mesures de protection et les méthodes de détection spécifiques peuvent varier. Par exemple, certaines entreprises utilisent la thermographie infrarouge pour surveiller les changements de température en temps réel dans les batteries.
Mesures environnementales : Avec une prise de conscience environnementale croissante, de nombreuses entreprises ont mis en œuvre des mesures d’économie d’énergie et de réduction des émissions dans le processus de fabrication. Cependant, les pratiques peuvent différer d’une entreprise à l’autre en matière de gestion des déchets et d’utilisation de l’énergie.
En conclusion, la fabrication des batteries 18650 n’est pas seulement un processus technique ; c’est aussi un art. Différentes entreprises ont leurs propres approches dans le processus de fabrication, mais l’objectif ultime est de produire des produits de batterie performants et fiables. En tant que consommateurs ou partenaires, comprendre les processus de fabrication sous-jacents et les principaux points de contrôle de la qualité peut aider à faire des choix plus éclairés.
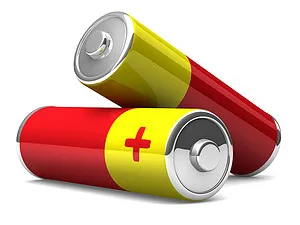