- Overview of 18650 battery
The 18650 battery is a common cylindrical lithium-ion battery named after its dimensions of 18 millimeters in diameter and 65 millimeters in height. This type of battery offers advantages such as high energy density, long cycle life, and excellent safety performance. It is widely used in electric vehicles, electronic devices, energy storage systems, and other fields.
- 18650 battery raw materials
Positive electrode material: The positive electrode material is an important component of the 18650 battery and is typically made of lithium transition metal nitrides such as NCA (nickel-cobalt-aluminum) and NMC (nickel-manganese-cobalt). These materials offer advantages such as high energy density and excellent electrochemical performance.
Negative electrode material: The negative electrode material is usually made of graphite or lithium titanate. Graphite has advantages such as high capacity and good cycling performance, while lithium titanate offers benefits such as high safety and long lifespan.
Electrolyte: The electrolyte is the conductive medium in the 18650 battery and typically consists of organic solvents and lithium salts. The performance of the electrolyte has a significant impact on the electrochemical performance and safety of the battery.
Separator: The separator is an important component of the 18650 battery and is used to isolate the positive and negative electrodes to prevent short circuits. Separators are typically made of polyolefin materials and possess excellent mechanical properties and chemical stability.
- 18650 battery production process
Electrode sheet fabrication: Electrode sheet fabrication is the first step in the production of an 18650 battery and typically involves processes such as mixing, coating, drying, and calendaring. During the coating process, parameters such as coating thickness and uniformity need to be controlled to ensure the optimal structure and performance of the electrode sheet.
Winding: Winding is a crucial step in the manufacturing of an 18650 battery, where the positive and negative electrode sheets, along with the separator, are wound into a cell. Parameters such as winding pressure and speed need to be controlled during the winding process to ensure the optimal structure and performance of the cell.
Injection: Injection refers to the process of injecting electrolyte into the cell, typically carried out after the winding process. Parameters such as injection volume and speed need to be controlled during the injection process to ensure even distribution of the electrolyte and prevent the formation of bubbles.
Encapsulation: Encapsulation involves housing the cell in an aluminum or steel casing to ensure battery safety and reliability.
Quality testing: Quality testing involves performing performance and safety tests on the completed 18650 battery. This includes capacity testing, cycle life testing, safety performance testing, etc., to ensure that the battery meets the expected quality and performance requirements.
- Battery packaging methods and quality control
Packaging: The packaging of 18650 batteries typically involves using aluminum or steel casings, along with measures such as moisture-proofing and anti-static protection, to ensure the safety and stability of the batteries during use.
Quality control: Strict quality control is implemented at every stage of the production process for 18650 batteries. This includes quality control of raw materials, process control during manufacturing, and quality testing of finished products. Only through rigorous quality control can the quality and performance of the products be ensured to reach their optimal state.
- Difficulties and core technologies in 18650 battery manufacturing
Material formulation: Material formulation is one of the key technologies in the manufacturing of 18650 batteries, directly affecting the performance and safety of the batteries. The development of material formulations requires iterative testing and optimization to achieve the best performance and stability.
Precision control: Precision control is a critical technology in the manufacturing of 18650 batteries, including the control of parameters such as coating thickness, winding pressure, and injection volume. Precision control relies on advanced equipment and strict process control to ensure that the quality and performance of the products reach their optimal state.
- How to ensure product performance consistency
In the manufacturing process of 18650 batteries, each stage has its specific quality control points to ensure consistent product performance. The following is an analysis of the quality control points for each stage and how to ensure consistent product performance:
Positive and negative electrode material preparation: Quality control points in this stage include material particle size, purity, surface structure, etc. To ensure consistent product performance, it is necessary to strictly control the source and processing of raw materials and conduct rigorous quality inspections for each batch of materials.
Electrode sheet fabrication: Quality control points in this stage include coating thickness, uniformity, drying temperature, etc. To ensure consistent product performance, advanced coating equipment should be used, real-time monitoring and adjustment of the coating process should be implemented, and strict quality inspections for electrode sheet thickness and uniformity should be carried out.
Winding: Quality control points in this stage include winding pressure, winding speed, membrane positioning, etc. To ensure consistent product performance, precision winding equipment should be used, real-time monitoring and adjustment of the winding process should be implemented, and the structural and dimensional accuracy of each cell should be ensured.
Injection: Quality control points in this stage include electrolyte purity, injection volume, injection speed, etc. To ensure consistent product performance, advanced injection equipment should be used, real-time monitoring and adjustment of the injection process should be carried out, and strict quality inspections for electrolyte purity and injection volume should be conducted.
Encapsulation: Quality control points in this stage include casing quality, stability of protection circuits, etc. To ensure consistent product performance, reliable encapsulation equipment should be used, real-time monitoring and adjustment of the encapsulation process should be implemented, and the structural and performance stability of each battery should be ensured.
In each stage of quality control, it is also important to focus on data analysis and record-keeping for continuous improvement and optimization of product performance. Additionally, any quality issues that arise should be analyzed and resolved promptly to ensure that the quality and performance of the products meet the expected requirements.
- Difficulties and core technologies in 18650 battery manufacturing
The challenges in the manufacturing of 18650 batteries primarily lie in material formulation, precision control, and safety. Material formulation is one of the crucial aspects that directly impact the battery’s performance and safety. Similarly, precision control is an important technology in the manufacturing process, where parameters such as coating(related equipment) thickness, winding pressure, and injection volume need to meet specific accuracy requirements. Additionally, due to the high safety requirements of batteries, multiple measures need to be taken during the manufacturing process to ensure their safety performance.
In response to these challenges and core technologies, many companies are continuously researching and exploring new solutions. For example, they are improving material formulation and process flow to enhance the battery’s energy density and cycle life. Advanced precision control techniques are being adopted to improve manufacturing efficiency and product quality. Safety design and testing are being strengthened to ensure the battery’s safety performance.
- Looking forward to the development trends and innovation directions of 18650 batteries
With the continuous development in fields such as electric vehicles and electronic devices, the demand for 18650 batteries is steadily increasing. In the future, 18650 batteries will evolve towards higher capacity, fast charging, sustainability, and environmental friendliness. High capacity will enhance the battery’s range, fast charging technology will reduce charging time, and sustainability and environmental requirements will minimize the impact on the environment.
To achieve these goals, there will be more technological innovation and research and development activities in the future. For example, improving material formulation and process flow to enhance the battery’s energy density and cycle life, adopting new electrolyte and separator materials to enhance battery safety performance, and researching new fast charging technologies to reduce charging time.
- Taking XX Company as an example, its 18650 battery production line demonstrates the characteristics of a high degree of automation and intelligent integration.
Raw Material Preparation: Automatic batching systems are used to accurately weigh various raw materials according to specific formulations.
Slurry Preparation: The raw materials are mixed uniformly using efficient mixers to form electrode slurries.
Coating Process: Double-sided coating machines are used to evenly coat the slurry onto metal foils, followed by preliminary curing in infrared drying ovens.
Calendering and Cutting: The electrode sheets are compacted using calendering machines to ensure a tight structure. Then, they are cut into appropriate sizes in preparation for winding.
Winding and Assembly: Automatic winding machines are used to wind the positive and negative electrode sheets together with a separator, forming the cell. The assembly of the cell is completed in a clean environment.
Injection and Sealing: Under strictly controlled environmental conditions, the cells are injected with electrolytes, and laser welding technology is used to seal them.
Formation and Capacity Testing: The batteries are activated through a formation process, followed by capacity testing to ensure that each battery meets the required performance standards.
Aging and Testing: After a specific aging period, the batteries undergo multiple safety performance tests to ensure their reliability and quality.
- Similarities and differences in battery manufacturing processes and quality control points of different companies
Material Selection: While most companies choose high-quality raw materials, some companies prioritize materials from sustainable sources.
Automation Level: Some companies have achieved fully automated production, while others still rely on semi-automation or manual operations. The level of automation affects production efficiency and cost control.
Precision Control Technology: Different companies employ varying precision control technologies in key processes such as winding and injection. For example, some companies use advanced laser measurement technology for dimensional monitoring.
Safety Strategies: All companies prioritize battery safety, but specific protective measures and detection methods may vary. For instance, some companies use infrared thermography to monitor real-time temperature changes in batteries.
Environmental Measures: With increasing environmental awareness, many companies have implemented energy-saving and emission-reducing measures in the manufacturing process. However, practices may differ among companies regarding waste management and energy utilization.
In conclusion, the manufacturing of 18650 batteries is not just a technical process; it is also an art. Different companies have their unique approaches in the manufacturing process, but the ultimate goal is to produce high-performance and reliable battery products. As consumers or partners, understanding the underlying manufacturing processes and key quality control points can help make more informed choices.
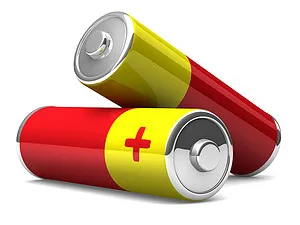