L’un des processus clés de la commercialisation des batteries lithium-ion secondaires est l’utilisation d’électrolytes liquides, ce qui rend le processus d’injection essentiel. Le processus d’injection fait référence à la procédure d’injection d’électrolyte à l’intérieur de la cellule de batterie et de scellement à l’aide d’un équipement d’injection.
01.Vue d’ensemble du matériel d’injection
1.1 Importance du matériel d’injection
Dans le processus de fabrication des batteries lithium-ion secondaires, le rôle de l’électrolyte est de faciliter la conduction des ions entre les électrodes positives et négatives. Il agit comme un moyen pour le transport des ions lithium, de la même manière que le sang dans nos poumons facilite l’échange d’oxygène et de dioxyde de carbone. Cela souligne l’importance de l’électrolyte dans l’ensemble du système de batterie.
En règle générale, l’électrolyte d’une batterie lithium-ion se compose d’un électrolyte de sel de lithium inorganique, de solvants carbonatés organiques et d’additifs. En tant que moyen de migration et de transfert de charge au lithium-ion, l’électrolyte est un composant indispensable et crucial d’une batterie lithium-ion. Il constitue la base de la batterie pour obtenir des avantages tels qu’une tension élevée, une densité d’énergie élevée et des performances de cyclage élevées.
Les paramètres les plus critiques pour évaluer l’injection de la batterie sont le volume d’injection, l’effet de mouillage (complet et uniforme) et la précision de l’injection. Ces trois aspects sont réalisés grâce aux performances de l’équipement d’injection. Par conséquent, l’équipement d’injection est crucial dans le processus de production des batteries lithium-ion car il a un impact direct sur les performances de la batterie. Les principaux paramètres de l’équipement sont décrits comme suit :
(1) Volume d’injection : Il est nécessaire d’envisager de répondre aux exigences de conception de la batterie et de s’assurer que la quantité spécifiée d’électrolyte est entièrement injectée dans la batterie. Le volume d’injection doit être contrôlé avec précision pour s’assurer que la quantité d’électrolyte à l’intérieur de chaque cellule de batterie répond aux exigences.
(2) Effet mouillant : L’effet mouillant fait référence à l’infiltration uniforme de l’électrolyte à l’intérieur des électrodes de la batterie, permettant aux électrodes de présenter des performances électrochimiques optimales. Un mouillage incomplet peut nuire à la constance des performances de la batterie. Obtenir le meilleur effet mouillant dans les plus brefs délais est un aspect crucial de la capacité de traitement de l’équipement d’injection.
(3) Précision de l’injection : La précision de l’injection reflète la constance de la quantité d’électrolyte dans la batterie, ce qui affecte à son tour la constance des performances de la batterie. Il reflète également les performances et les capacités de l’équipement d’injection.
En plus de remplir les trois points susmentionnés pour répondre aux exigences, l’équipement d’injection doit également envisager d’utiliser le processus d’injection optimal pour obtenir le résultat souhaité dans les plus brefs délais, avec des cycles d’injection minimaux, des exigences d’espace minimales, une intervention manuelle minimale et des coûts minimaux.
1.2 Principe du matériel d’injection
Le principe du matériel d’injection consiste à injecter l’électrolyte dans la cavité interne limitée de la batterie (qui comprend la cellule et l’espace non rempli) en utilisant un processus spécifique (tel que le vide, la pression et le temps). Une partie de l’électrolyte s’infiltre dans la cellule de la batterie (composée de feuilles d’électrodes positives et négatives et d’un séparateur), tandis qu’une autre partie occupe l’espace non rempli. La quantité totale d’électrolyte injectée est appelée volume d’injection. Plus l’effet de mouillage est bon, plus l’électrolyte s’infiltre dans la cellule de la batterie. Plus le temps nécessaire pour infiltrer l’électrolyte dans la cellule de la batterie est court, meilleure est la capacité de traitement de l’équipement d’injection.
L’écart entre le volume d’injection réel et le volume d’injection réglé pour une batterie spécifique représente la précision de l’injection. Pour un lot de batteries, meilleure est la consistance du volume d’injection et plus le volume d’injection est concentré, indiqué par une valeur CPK plus élevée du poids d’injection, meilleures sont les performances globales de l’équipement d’injection.
1.3 Types de matériel d’injection
1. Basé sur les types de batteries
(1) Matériel d’injection en poche.
(2) Matériel d’injection à coque dure, y compris le matériel d’injection de batterie cylindrique et le matériel d’injection de batterie prismatique.
2. Basé sur les types de structures
(1)Équipement d’injection linéaire, y compris une structure alternative.
(2) Équipement d’injection rotative.
Basé sur des procédés d’injection
(1) L’équipement d’injection sous vide, qui fait généralement référence à la méthode d’infiltration par respiration sous vide et à pression atmosphérique.
(2) Équipement d’injection à basse pression, qui implique généralement une pression inférieure à 0,3 MPa pendant la pressurisation et l’infiltration cyclique avec alternance de vide et de pression.
(3)Équipement d’injection à haute pression, qui implique généralement une pression comprise entre 0,5 et 0,8 MPa lors de la pressurisation et de l’infiltration cyclique avec vide et alternance de pression. La haute pression permet de meilleurs effets d’injection et de mouillage, ce qui en fait la direction de développement actuelle de l’équipement d’injection. Actuellement, une partie importante des batteries cylindriques et des batteries à coque prismatique en aluminium (avec le soutien de la pression isostatique) utilisent l’injection à haute pression. Cependant, l’injection à haute pression n’a pas été largement adoptée pour les batteries de type poche.
(4) Équipement d’injection à ultra-haute pression : Actuellement, il n’existe pas d’équipement d’injection à ultra-haute pression clairement produit en série sur le marché. À l’avenir, il pourrait y avoir des équipements d’injection avec une pression statique plus élevée. Les équipements d’injection fonctionnant avec une pression comprise entre 1 et 2 MPa peuvent être appelés équipements d’injection à ultra-haute pression. Pour les batteries à plus forte densité d’énergie à l’avenir, il est possible d’utiliser un équipement d’injection à ultra-haute pression, ce qui réduirait potentiellement le temps de stabilisation post-injection requis.
4) Basé sur la méthode de pressurisation
(1) Équipement d’injection à pression différentielle : Il s’agit généralement d’appliquer une pression positive uniquement à la cavité interne de la batterie pendant la pressurisation et la décantation statique. Il y a une différence de pression entre la cavité interne de la batterie et la coque externe, d’où le terme d’injection « pression différentielle » ou de stabilisation de la pression différentielle. Il convient de noter que pour les batteries prismatiques à coque dure, en raison de la présence de membranes antidéflagrantes et de la tendance de la coque prismatique à se déformer, l’équipement d’injection à pression différentielle est généralement de type basse pression. Pour les batteries cylindriques telles que les batteries à coque en acier 18650/26650, l’équipement d’injection à pression différentielle peut être à basse pression ou à haute pression. Le schéma ci-dessous illustre le principe de l’injection cyclique sous vide à haute pression.
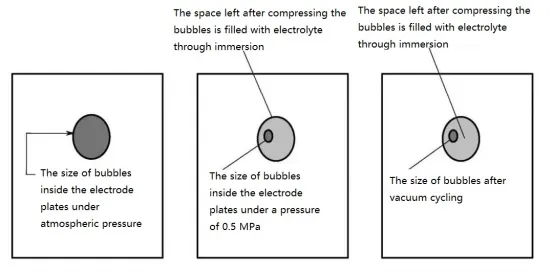
(2) L’équipement d’injection isostatique fait généralement référence à l’application d’une pression positive égale à la fois à la cavité interne de la batterie et à la coque externe pendant la pressurisation et la décantation statique. Il n’y a que peu ou pas de différence de pression entre la cavité interne de la batterie et la coque externe, d’où le terme d’injection « isostatique » ou de décantation isostatique. En termes de relation logique, la haute pression est l’objectif, et la pression isostatique est le moyen d’atteindre une pression élevée. Sans la présence de pression, la pression isostatique n’a aucun sens. L’équipement d’injection isostatique permet aux batteries prismatiques à coque en aluminium de réaliser une injection à haute pression. Les batteries à poche peuvent également utiliser l’injection isostatique à haute pression. Le diagramme illustre le schéma de l’injection cyclique sous pression atmosphérique et sous vide.
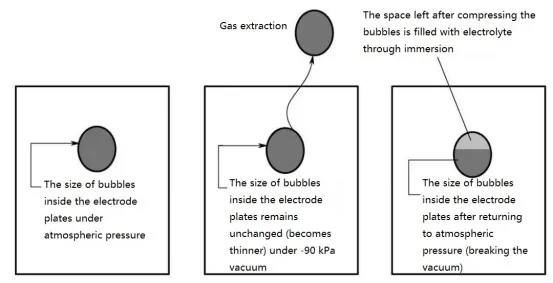
1.4 Fonctions de la machine d’injection
(1) Une machine à injection unique pour batteries prismatiques à coque en aluminium comprend les fonctions suivantes :
a. Chargement du matériau : Fonctionnement manuel ou fonctionnement automatique par un bras robotisé.
b. Lecture de code : Codes-barres ou codes QR.
c. Pré-pesée : Liaison des codes-barres avec poids, avec données enregistrées dans le système MES.
d. Placement des plateaux : Placer les batteries dans les plateaux et positionner les plateaux.
e. Test d’étanchéité : Vérification de l’étanchéité de la buse d’injection.
f. injection : à l’aide d’une pompe d’injection.
g. Modes de décantation, de vide et de cycle de pression : mode haute pression, mode basse pression et mode isostatique.
h. Déchargement des plateaux : Retrait des piles des plateaux.
i. Post-pesée : Liaison des codes-barres avec poids, avec données enregistrées dans le système MES.
j. Scellement des trous d’injection : Insertion de goupilles adhésives pendant le processus d’insertion.
k. Décharge de matière.
(2) Une machine d’injection secondaire pour batteries prismatiques à coque en aluminium comprend les fonctions suivantes :
a. Chargement du matériau : Fonctionnement manuel ou fonctionnement automatique par un bras robotisé.
b. Lecture de code : Codes-barres ou codes QR.
c. Pré-pesée : Liaison des codes-barres avec poids, avec des données enregistrées dans le système MES pour calculer la quantité d’injection secondaire (injection variable).
d. Placement des plateaux : Placer les batteries dans les plateaux et positionner les plateaux.
e. Test d’étanchéité : Vérification de l’étanchéité de la buse d’injection.
f. injection : Réalisation d’une injection variable à l’aide d’une pompe à injection variable.
g. Modes de décantation, de vide et de cycle de pression : mode haute pression, mode basse pression et mode isostatique.
h. Déchargement des plateaux : Retrait des piles des plateaux.
i. Post-pesée : Liaison des codes-barres avec poids, avec données enregistrées dans le système MES.
j. Extraction sous vide et remblayage à l’hélium : Extraction par pression négative et remblayage à l’hélium, à l’aide de goupilles adhésives.
k. Scellement des trous d’injection : Insertion de goupilles adhésives pendant le processus d’insertion.
l. Décharge de matière.
(3) Les machines d’injection pour batteries cylindriques 18650/21700/26650 (injection de liquide avant de sceller le bouchon) comprennent généralement les fonctions suivantes :
a. Chargement des matériaux : Méthode de chargement généralement automatisée.
b. Pré-pesée : Liaison des codes-barres avec poids, avec enregistrement des données dans le système MES pour calculer la quantité d’injection secondaire (injection variable).
c. Placement des plateaux : Placer les batteries dans les plateaux et positionner les plateaux.
d. Test d’étanchéité : Vérification de l’étanchéité de la buse d’injection.
e. injection : à l’aide d’une pompe d’injection.
f. Modes de décantation, de vide et de cycle de pression : mode haute pression, mode basse pression et mode isostatique.
g. Déchargement des plateaux : Retrait des piles des plateaux.
h. Post-pesée : les unités NG (non conformes) sont déchargées.
i. Décharge de matières.
(4) Les machines d’injection pour batteries cylindriques 18650/21700/26650 (scellant le bouchon avant l’injection de liquide) comprennent généralement les fonctions suivantes :
a. Chargement des matériaux : Méthode de chargement généralement automatisée.
b. Orientation du capuchon : Déterminer l’orientation correcte du capuchon.
c. Pré-pesée : Liaison des codes-barres avec poids, avec des données enregistrées dans le système MES pour calculer la quantité d’injection secondaire (injection variable).
d. Placement des plateaux : Placer les batteries dans les plateaux et positionner les plateaux.
e. Injection séquentielle : À l’aide d’une pompe d’injection, généralement en 5 à 6 étapes d’injection.
f. Modes séquentiels de décantation, de vide et de cycle de pression : mode haute pression, mode basse pression et mode vide.
g. Déchargement des plateaux : Retrait des piles des plateaux.
h. Post-pesée : les unités NG (non conformes) sont déchargées.
i. Orientation du capuchon et pliage de la languette : Déterminer l’orientation correcte du capuchon et plier la languette.
j. Aplatir le capuchon : Aplatir le capuchon.
k. Décharge de matière.
(5) Les machines d’injection pour batteries de poche comprennent généralement les fonctions suivantes :
a. Chargement du matériau : Fonctionnement manuel ou fonctionnement automatique par un bras robotisé.
b. Lecture de code : Codes-barres ou codes QR.
c. Pré-pesée : Liaison des codes-barres avec poids, avec données enregistrées dans le système MES.
d. Placement des plateaux : Placer les batteries dans les plateaux et positionner les plateaux.
e. Test d’étanchéité : Vérification de l’étanchéité de la buse d’injection.
f. injection : à l’aide d’une pompe d’injection.
g. Débourbage : Implique généralement des cycles de décantation sous vide et à pression atmosphérique.
h. Déchargement des plateaux : Retrait des piles des plateaux.
i. Post-pesée : Liaison des codes-barres avec poids, avec données enregistrées dans le système MES.
j. Etanchéité des trous d’injection : Utilisation d’une méthode de thermoscellage.
k. Décharge de matière.
(6) Les machines d’injection à passage unique pour les batteries à coque cylindrique en aluminium de grande taille comprennent généralement les fonctions suivantes :
a. Chargement du matériau : Fonctionnement manuel ou fonctionnement automatique par un bras robotisé.
b. Lecture de code : Codes-barres ou codes QR.
c. Pré-pesée : Liaison des codes-barres avec poids, avec données enregistrées dans le système MES.
d. Alignement rotationnel des trous d’injection : Généralement réalisé par reconnaissance CCD.
e. Placement du plateau : Placer les batteries dans des plateaux et positionner les plateaux.
f. Test d’étanchéité : Vérification de l’étanchéité de la buse d’injection.
g. injection : à l’aide d’une pompe d’injection.
h. Modes de décantation, de vide et de cycle de pression : mode haute pression, mode isostatique.
i. Déchargement des plateaux : Retrait des piles des plateaux.
j. Post-pesée : Liaison des codes-barres avec poids, avec enregistrement des données dans le système MES.
k. Scellement des trous d’injection : Insertion de goupilles adhésives pendant le processus d’insertion.
l. Décharge de matière.
1.5 Indicateurs de rendement
1. Efficacité de l’injection
(1) Efficacité des machines d’injection de batterie cylindrique :
un. Efficacité pour les accus 18650/21700/26650 (scellant le capuchon avant d’injecter du liquide) : les options disponibles incluent 80 PPM, 120 PPM, 200 PPM et 300 PPM.
b. Efficacité pour les accus 18650/21700/26650 (injection de liquide avant de sceller le bouchon) : Les options disponibles incluent 80PPM et 120PPM.
c. Efficacité pour les grandes batteries cylindriques à coque en aluminium (diamètre extérieur 32-50 mm, hauteur 80-273 mm) : Actuellement en production à 50 PPM et 72 PPM, avec des options futures potentielles atteignant 100 PPM ou plus.
d. Efficacité pour les grandes batteries cylindriques à coque en acier (diamètre extérieur 32-26 mm, hauteur 80-160 mm) : Actuellement en production à 60 PPM et 120 PPM, avec des options futures potentielles atteignant 200 PPM ou plus. Pour la batterie 46800 avec une structure de coque en acier ouverte, l’efficacité de la ligne de production peut être considérée dans la plage de 80 PPM, 120 PPM, 160 PPM et 200 PPM par incréments progressifs.
(2) Efficacité des machines d’injection de batterie pour les batteries de puissance avec des coques en aluminium :
un. Efficacité des batteries 26148 : Généralement dans la plage de 12 à 24 PPM, avec des options futures potentielles dans la plage de 24 à 60 PPM.
b. Efficacité des batteries 50160 : Généralement dans la gamme de 12-24 PPM, avec des options futures potentielles dans la gamme de 24-60 PPM.
c. Efficacité des batteries 33230 : Généralement dans la gamme de 12 à 24 PPM, avec des options futures potentielles dans la plage de 24 à 48 PPM.
(3) Efficacité des machines d’injection pour les batteries à poche :
Efficacité des batteries de poche : Généralement dans la plage de 6 à 24 PPM.
(4) machines d’injection pour batteries de poche 3C :
Efficacité des piles Pouch 3C : Généralement dans la plage de 12 à 24 PPM pour les petites pochettes.
1. Précision d’injection
un. Précision d’injection pour les batteries de poche : Généralement autour de 0,5 %.
b. Précision d’injection pour les accus 18650 : généralement autour de ±0,1 g, compte tenu de l’écart du système de pesage lui-même, avec un écart défini du logiciel de pesage généralement autour de ±0,15 g.
c. Précision d’injection pour les batteries 26650 : généralement autour de ±0,12 g, compte tenu de l’écart du système de pesage lui-même, avec un écart défini du logiciel de pesage généralement autour de ±0,18 g.
d. Précision d’injection pour les accus 32130 à grande coque cylindrique en aluminium (première injection) : généralement autour de ±1g.
e. Précision d’injection pour les accus 32130 à grande coque cylindrique en aluminium (injection secondaire) : Généralement autour de ±1g.
f. Précision d’injection pour les batteries prismatiques (première injection) : Généralement autour de 0,5% à 1%.
g. Précision d’injection pour les batteries prismatiques (injection secondaire) : généralement autour de 0,5 % à 1 %.
02 Composition de l’équipement et structures clés
2.1 Boîtier extérieur
(1) Type de boîte à gants : Généralement utilisé uniquement dans les laboratoires ou pour la production à petite échelle. Il peut être équipé d’un déshumidificateur intégré ou connecté à une source de gaz sec pour contrôler la teneur en humidité à l’intérieur. La boîte à gants d’un seul poste de travail est illustrée dans la figure ci-dessous.
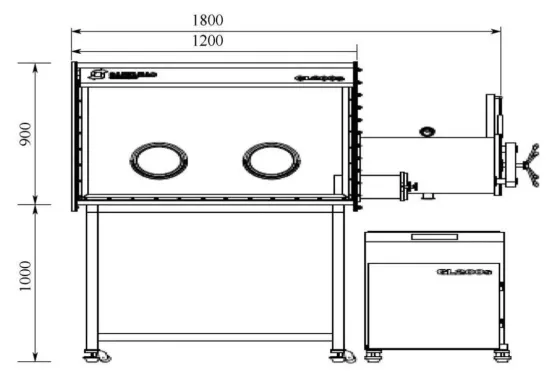
(2) Boîtier en tôle avec une certaine fonction d’étanchéité. Il est connecté à une source de gaz sec et peut être utilisé à l’intérieur d’une pièce sèche ou dans une pièce ordinaire avec une pièce de transition. La structure du boîtier en tôle est illustrée dans la figure ci-dessous.
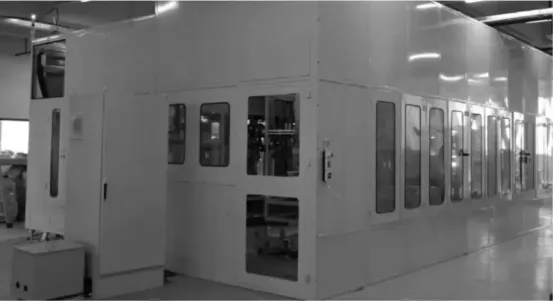
(3) Boîtier de cadre en alliage d’aluminium. Il est utilisé à l’intérieur d’une pièce sèche et fournit une certaine barrière contre l’humidité, assurant la sécurité de l’équipement et du personnel. La structure du boîtier du cadre en alliage d’aluminium est illustrée dans la figure ci-dessous.
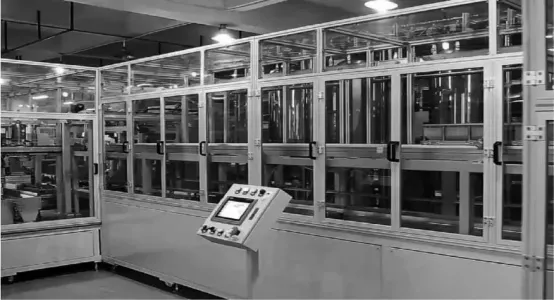
2.2 Pompe à vide
(1) Généralement, les pompes à vis sont couramment utilisées.
(2) Le placement de la pompe à vide à côté de la machine d’injection garantit une efficacité d’utilisation du vide élevée et des économies d’énergie.
(3) Si la pompe à vide est placée loin, il faudra des canalisations pour la relier. Dans ce cas, la perte de vide due aux canalisations doit être prise en compte. Plus les conduites sont longues et étroites, plus la perte de débit et de niveau de vide est importante.
2.3 Pompe d’injection
(1) De nos jours, les pompes électriques sont couramment utilisées avec des têtes de pompe en céramique, au lieu des pompes d’injection Hibar qui étaient couramment utilisées avant 2010.
(2) Les pompes électriques sont disponibles en types manuels et variables intelligents, ces derniers étant souvent appelés pompes variables.
(3) La précision des pompes électriques pour l’injection d’électrolyte est généralement d’environ 0,25%.
(4) Il est important d’éviter l’encrassement de la pompe pendant la production réelle lors de l’utilisation de la pompe d’injection.
2.4 Réservoir de transfert d’électrolytes
(1) L’objectif principal du réservoir de transfert d’électrolyte est de fournir de l’électrolyte (à la coupelle d’injection) à la pression atmosphérique et de maintenir un niveau constant dans une petite plage.
(2) L’électrolyte dans le réservoir de transfert est pressurisé à environ 0,2 MPa en raison de la présence d’azote gazeux comme gaz protecteur, mais la pression diminue pendant l’utilisation.
(3) Si nécessaire, une structure à deux couches ou à double réservoir peut être utilisée pour le réservoir de transfert d’électrolyte. Cela permet le dégazage du réservoir supérieur pour améliorer la consistance et la précision du volume injecté.
(4) La filtration de l’électrolyte peut être effectuée si nécessaire.
(5) Si nécessaire, un transmetteur de pression différentielle peut être installé pour surveiller le filtre.
2.5 Système de lecture de codes-barres
(1) Les lecteurs de codes-barres sont utilisés pour identifier et lire les codes-barres ou les codes QR.
(2) Les informations numérisées sont liées aux données de poids et forment une base de données dans le système MES.
2.6 Système de pesage
(1) Il comprend des composants tels que des bras robotiques, des pinces robotiques et des balances électroniques.
(2) Les balances électroniques se composent généralement de capteurs de pesage et d’amplificateurs séparés pour gagner de la place.
(3) Les performances de résistance à la corrosion des capteurs de pesage doivent être prises en compte.
2.7 Système MES
(1) Le système MES comprend principalement des codes-barres de batterie, une pré-pesée, une post-pesée et la vérification de l’écart de la quantité d’injection pour la qualification.
(2) Le système MES permet la connexion entre la première et la deuxième injection, ainsi que l’interconnexion de l’ensemble de l’usine.
2.8 Système d’essai d’étanchéité
(1) Parfois, il est nécessaire de vérifier l’étanchéité de la buse d’étanchéité et de la batterie. Les batteries dont l’étanchéité est défectueuse ne sont pas soumises à l’injection.
(2) Des méthodes de maintien sous vide ou sous pression sont utilisées pour la détection des fuites.
2.9 Système d’alimentation en liquide
(1) Il comprend la pompe d’injection, la vanne et la canalisation.
(2) Certains systèmes sont équipés de gobelets de stockage temporaires pour améliorer l’efficacité.
(3) Certains systèmes utilisent une méthode d’injection à aiguille mobile pour injecter du liquide dans plusieurs tasses à l’aide d’un nombre réduit de pompes.
2.10 Luminaire/Palette
(1) Utilisés pour le positionnement des batteries, les luminaires ou les palettes sont conçus en fonction de différentes structures de batterie et des exigences d’efficacité.
(2) Il existe des luminaires à positions fixes et des palettes à configurations mobiles.
2.11 Mécanisme de décantation
(1) Le mécanisme de décantation comprend des coupelles d’injection, des buses d’étanchéité, des plateaux de batterie, des mécanismes de compression, une soupape de pression et de vide et des systèmes de canalisations, etc.
(2) Il existe plusieurs types de méthodes de décantation :
· Les batteries à poche souple utilisent généralement une méthode de décantation cyclique à pression atmosphérique sous vide.
· Les batteries Hardshell utilisent généralement une méthode de décantation cyclique sous vide, pression atmosphérique, pression positive, pression atmosphérique.
· Le décantation sous pression peut être classée en décantation à haute pression et décantation à basse pression. Le tassement à haute pression fait référence à une pression supérieure à 0,5 MPa, tandis que le tassement à basse pression fait référence à une pression inférieure à 0,3 MPa. Pour les batteries prismatiques, en particulier celles dotées de membranes antidéflagrantes, une méthode de décantation isobare est nécessaire lors de l’utilisation d’un décantage à haute pression.
· Le mécanisme de décantation en forme de dôme est illustré sur la figure. L’unité de décantation du chargeur de plateaux est illustrée sur la figure.
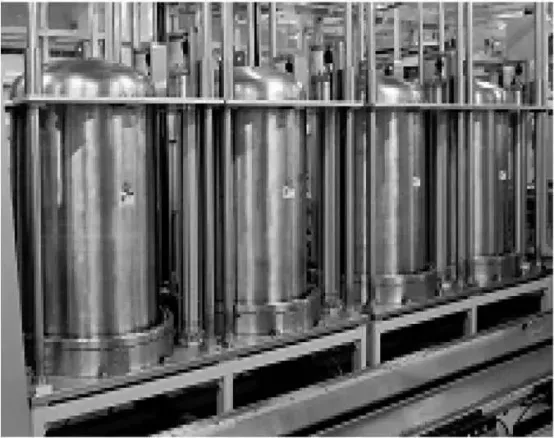
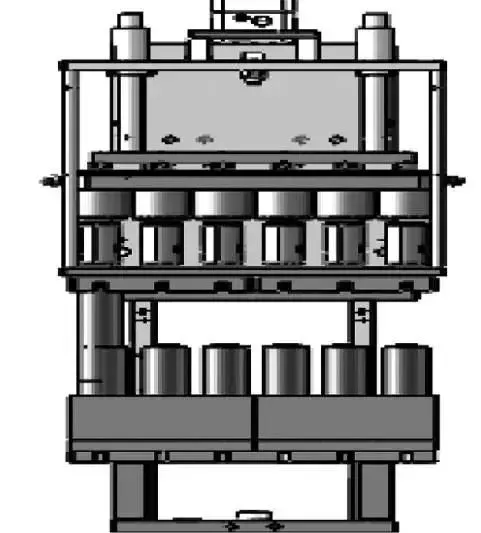
2.12 Bande transporteuse de matériaux
La bande transporteuse de matériaux est un mécanisme de connexion automatisé pour le transport des batteries dans et hors de la machine d’injection dans le processus ultérieur.
03 Sélection de l’équipement et Application Exemples
3.1 Choix des méthodes de décantation
(1) Compte tenu de la situation actuelle des machines d’injection traditionnelles, la sélection de l’équipement implique principalement le choix de différentes méthodes de décantation, notamment la décantation sous vide, la décantation à basse pression et la décantation à haute pression.
(2) Pour les machines d’injection de cellules de poche, la pratique actuelle est principalement basée sur la méthode cyclique de décantation sous vide. À l’avenir, il pourrait être possible d’adopter une méthode de décantation isobare à haute pression. D’une part, il peut fournir de meilleurs effets d’imprégnation, et d’autre part, on suppose qu’il pourrait économiser le temps de séjour ultérieur.
(3) Considérations de référence pour la sélection de l’équipement des batteries d’alimentation prismatiques à coque en aluminium :
un. Pour un temps de décantation par injection dans les 10 minutes : Il est recommandé de choisir un décantation à basse pression (méthode à pression différentielle).
b. Pour un temps de décantation par injection supérieur à 10 minutes : Il est recommandé de choisir un décantation isobare à haute pression.
c. Pour une efficacité supérieure à 20 PPM et un temps de décantation supérieur à 10 minutes : Il est fortement recommandé de choisir un décantation à haute pression.
(4) Pour les batteries cylindriques à coque en acier (18650, 21700, 26650, 32650, 32130, 46800) :
un. Pour les batteries à faible rendement, telles que 60 PPM pour 18650 et 30 PPM pour 32650, 46800, l’injection haute pression avec méthode de pression différentielle peut être sélectionnée.
b. Pour les batteries à rendement plus élevé, telles que 120 PPM ou 200 PPM pour 18650, 60 PPM et plus pour 32650, ainsi que les futures séries 46800, il est fortement recommandé d’utiliser l’injection isobare haute pression.
c. Pour la série 32130 avec des coques en acier, où la hauteur de la batterie est plus élevée et l’imprégnation de l’électrolyte plus difficile, il est fortement recommandé d’utiliser l’injection isobare à haute pression.
(5) Batteries cylindriques en aluminium de la série 32130 :
un. Pour les batteries à faible rendement ou pour l’injection secondaire, la méthode de pression différentielle peut être choisie.
b. Pour les lignes de production à haut rendement, telles que celles dont le rendement dépasse 30 PPM, il est fortement recommandé d’utiliser l’injection isobare à haute pression, à moins que l’injection de cette batterie ne soit particulièrement facile et n’ait un temps d’imprégnation très court.
3.2 Sélection des modes structurels
(1) La structure des machines d’injection comprend généralement des modes rotatif, linéaire et en zigzag (qui est un type de linéaire), chacun avec quelques différences.
(2) Le mode linéaire est ensuite divisé en modes parallèle et en mode série. En mode parallèle, tout le temps de décantation est effectué sur la même station de décantation, tandis qu’en mode série, la batterie du plateau passe par toutes les stations de décantation pour terminer tout le temps de décantation. Le mode parallèle a une efficacité d’utilisation du temps plus élevée par rapport au mode série.
(3) Le mode rotatif et le mode linéaire parallèle sont essentiellement les mêmes, tandis que le mode zigzag est généralement un mode série. Les principes du mode linéaire en série et du mode zigzag sont fondamentalement les mêmes.
(4) Quel que soit le mode, la clé est le flux des batteries, le flux des plateaux de batteries et la circulation de leur utilisation.
(5) Le grand équipement d’injection peut être une combinaison de modes rotatif et linéaire.
(6) Pour les machines d’injection de cellules de poche, les modes rotatifs ou linéaires sont généralement utilisés.
(7) Les machines d’injection isobares à haute pression en forme de dôme sont généralement des machines d’injection linéaires parallèles.
04 Utilisation et entretien de l’équipement
(1) Par rapport à d’autres équipements automatisés, la plus grande caractéristique d’une machine d’injection est que l’électrolyte est corrosif, nécessitant une attention particulière lors de l’utilisation et de la maintenance.
(2) Le nylon (PA66), le Delrin (POM), les tubes en PU et la feuille acrylique (plexiglas) ne résistent pas à la corrosion par électrolyte et doivent être évités pour l’utilisation.
(3) L’électrolyte est sujet à la cristallisation. Avant un arrêt à long terme, la pompe d’injection, en particulier la tête de pompe en céramique, doit être démontée pour le nettoyage afin d’éviter que la cristallisation n’obstrue la pompe.
(4) Évitez d’avoir des circuits électriques à proximité de l’électrolyte, en particulier en dessous de celui-ci.
(5) Les rails de guidage et les glissières doivent être protégés de la corrosion par l’électrolyte.
(6) Si possible, ne coupez pas l’alimentation en air sec pendant les arrêts de production.