La chaîne d’assemblage de batteries à sachets est un élément crucial des processus de fabrication de batteries au lithium. Il est principalement responsable de la manipulation des cellules nues assemblées ou enroulées et de l’exécution d’opérations telles que le soudage des languettes, le collage de rubans, le tubage des cellules et l’étanchéité de la face supérieure. Le principe de conception de la chaîne de montage est basé sur le processus de production des batteries au lithium, en tenant compte de facteurs tels que la taille des cellules, la structure et l’efficacité de production souhaitée.
1.Vue d’ensemble debourse Ligne d’assemblage d’emballes
1.1 Principes de conception et principes de la chaîne de montage
Le choix de la forme de la chaîne d’assemblage des batteries Pouch est principalement déterminé par les spécifications de taille des cellules. Pour les cellules d’une longueur inférieure à 390 mm, la machine à souder les onglets, la machine d’emballage et la section suivante de la machine d’emballage adoptent généralement une structure de plaque tournante entraînée par un séparateur à cames. Cette disposition structurelle est compacte et occupe une petite surface au sol. Cependant, il est limité par la précision de la platine vinyle. Plus le plateau tournant est grand, plus la précision d’assemblage des cellules est faible. De plus, l’augmentation de la charge affecte également la difficulté et l’efficacité du démarrage et de l’arrêt de la plaque tournante.
Pour les spécifications de cellule d’une longueur supérieure à 390 mm, la machine à souder les onglets, la machine d’emballage et la section suivante de la machine d’emballage adoptent généralement une structure linéaire. Cette disposition permet un positionnement précis lors de la commutation de station pour les batteries de grande taille et offre une efficacité élevée dans la commutation de station, offrant un meilleur potentiel d’amélioration de l’efficacité de la production. Cependant, cette disposition présente l’inconvénient d’occuper une surface au sol relativement étroite, et le mécanisme d’entraînement pour la commutation de station est plus complexe, ce qui entraîne des coûts relativement plus élevés. La disposition d’une ligne d’assemblage linéaire est illustrée dans le schéma ci-dessous.
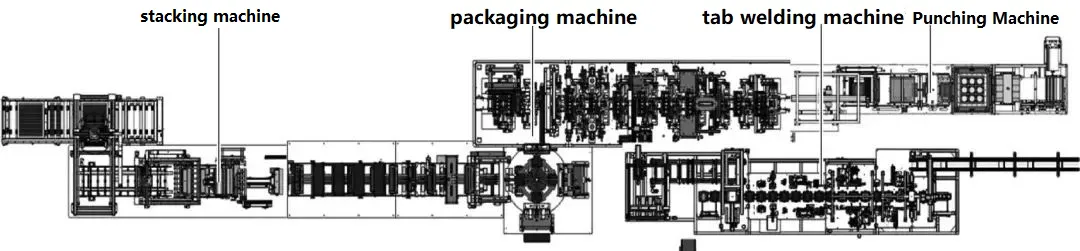
1.2Assemblée ligneefficacité distribution
Dans le processus de conception de la ligne de construction, le contrôle du rythme dépend principalement des limites de la station de goulot d’étranglement de chaque station de production. Par exemple, l’exigence de capacité de production réelle est de 8PPM. En ce qui concerne la capacité de production globale de l’équipement, la conception réelle est généralement basée sur 10PPM, et la limite de travail est de Les positions seront effectuées de manière multi-stations, telles que le mécanisme d’alimentation de la feuille de protection dans le pré-soudage de la languette de la section de la machine à souder, le mécanisme d’alimentation des languettes dans le soudage des onglets, le temps d’emballage de l’étanchéité supérieure et inférieure, le temps d’emballage de l’étanchéité latérale dans la machine d’emballage, etc. Après avoir comparé les besoins en capacité de production, calculez le temps de traitement nécessaire pour chaque station. S’il n’est pas respecté, une conception à plusieurs stations est requise. Par exemple, lorsque l’exigence d’efficacité de l’équipement est de 12 PPM, le temps de traitement et le temps de production de chaque cellule de batterie sont de 5 secondes. Les exigences de temps d’emballage de certains clients atteignent 4 à 5 secondes, plus le temps de commutation de la station de cellules de batterie et le temps d’action du mécanisme d’emballage. , ne peut pas répondre aux exigences d’efficacité de la production, il est donc nécessaire de concevoir un poste de travail double de cette station pour répondre aux exigences d’efficacité de la production. La répartition des battements des autres stations de travail est la même.
1.3 Méthodes logistiques
Lorsque les batteries sont assemblées, la logistique doit être utilisée pour le transfert et la commutation entre les postes de travail. Par conséquent, des méthodes logistiques raisonnables doivent être sélectionnées pour les batteries dans différents états.
(1) Pour les cellules nues déchargées de la machine d’empilage, afin d’assurer l’efficacité du transport des cellules et de protéger la sécurité des cellules, la méthode de la chaîne à double vitesse + pince de cellule est généralement utilisée. La chaîne à double vitesse a une efficacité de transport élevée et convient à la production à long terme. Il présente les avantages du transport longue distance, de la charge importante, de l’entretien simple, etc., et le profil de chaîne à double vitesse offre une grande flexibilité pour le réglage des butées et d’autres installations et ajustements de structures auxiliaires. L’inconvénient est que la chaîne à double vitesse est sujette aux frottements et génère de la poussière. Afin d’éviter l’impact de la poussière sur les noyaux des batteries, certains fabricants utilisent des lignes de convoyeurs à lévitation magnétique pour transporter les batteries nues, mais cela coûte cher.
(2) Les noyaux électriques sont transportés de la machine d’empilage à la machine à souder. Chaque station de la machine à souder a des exigences élevées en matière de précision de positionnement des noyaux électriques. Les noyaux électriques sont chargés dans le dispositif de soudage et adoptent une méthode de transport étape par étape. Afin d’assurer la précision Selon les exigences, l’entraînement adopte la structure de circulation du servomoteur + fourche de changement de vitesse.
(3) Une fois les noyaux de batterie déchargés de la machine à souder, la méthode de transport par servomoteur + courroie synchrone est généralement utilisée. Cela permet d’assurer l’espacement égal du transport du noyau de la batterie et de faciliter la précision des positions de déchargement et de saisie du robot. De même, la même méthode est adoptée après la machine d’emballage, qui est économique et efficace.
1.4 Méthodes et principes de positionnement des cellules
Sur la chaîne d’assemblage de cellules de batterie, le fabricant de la batterie a certaines exigences de précision dimensionnelle pour les cellules de batterie en termes de processus. Par conséquent, les cellules de la batterie doivent être positionnées avant que la batterie n’entre dans la chaîne de montage. Les cellules de la batterie sont positionnées sur la même base. Chaque poste de travail suivant Le réglage est également basé sur cela pour assurer la cohérence de l’assemblage de la batterie.
La forme du corps du noyau de la batterie est rectangulaire, donc en termes de positionnement, deux côtés sont généralement utilisés comme référence de positionnement, et les deux autres côtés sont utilisés pour positionner le noyau de la batterie en poussant. Vous pouvez également utiliser la méthode de positionnement central du corps de la batterie pour pousser le corps de la batterie vers l’avant, l’arrière, la gauche et la droite en même temps. Le choix de la méthode de positionnement dépend généralement des exigences de taille du processus du cœur de la batterie et de la commodité de la conception structurelle, tant que la référence est cohérente.
1.5 Contrôle de la poussière
Dans le processus de production de batteries, le danger le plus mortel est que de la poussière métallique pénètre dans le corps de la batterie, provoquant une série de problèmes, tels qu’un court-circuit de la batterie et un incendie. Afin d’éviter que cette situation ne se produise, il est nécessaire de contrôler strictement les sources de poussière dans la chaîne de montage et de les éliminer autant que possible. Pour contrôler la poussière, il faut d’abord déterminer la source de la poussière, puis prendre des mesures ciblées.
(1) Ligne de convoyeur de machine de laminage (chaîne à double vitesse). Pendant le processus de transport, la chaîne à double vitesse frottera contre le profil de la chaîne à double vitesse pour générer beaucoup de poussière. Pour ce type de poussière, il est nécessaire d’installer une plaque anti-poussière sur le corps de la chaîne à double vitesse pour éviter que la poussière ne tombe sur le noyau de la batterie. Dans le même temps, la pince du noyau de la batterie doit être aussi petite que possible. Le convoyeur est transporté par serrage supérieur et inférieur, et les dispositifs vides sur la ligne de retour sont dépoussiérés en des points fixes. La méthode de dépoussiérage s’effectue par soufflage + aspiration. Comme la ligne est relativement longue, la fréquence des nettoyages manuels doit être augmentée pour éviter l’accumulation de poussière, etc.
(2) Ligne d’assemblage. Lorsque les batteries circulent dans la chaîne de montage, certains postes de travail eux-mêmes peuvent générer de la poussière, comme les stations de pré-brasage, de découpe, de soudage par languette et d’emboutissage de soudure des languettes. Tant qu’il y a un poste de découpe ou de soudage, ils seront installés. Un mécanisme spécial de dépoussiérage effectue un dépoussiérage ininterrompu. L’image ci-dessous montre la carte de la station de dépoussiérage.
1.6 Contrôle de la qualité
Afin d’assurer la stabilité et la constance de la qualité de la production de batteries, il y aura des capteurs de détection correspondants pour le contrôle de la qualité dans tous les aspects de la production de batteries. Pour la chaîne de montage, les manifestations spécifiques sont les suivantes :
(1) Le capteur de couleur est utilisé pour détecter la polarité du noyau de batterie entrant, principalement pour empêcher la batterie d’être déchargée à l’envers après une intervention manuelle.
(2) Scannez le code de la batterie pour vous assurer que les informations de la batterie sont téléchargées sur le système MES en temps opportun, ce qui facilite le suivi des informations de production de la batterie.
(3)L’inspection par rayons X du noyau de la batterie est utilisée pour détecter l’alignement du noyau de la batterie afin d’éviter la production ultérieure de batteries gravement désalignées.
(4) Détection de polarité de languette et détection positive et négative pour éviter les erreurs de soudage.
(5) Détection de colle après le soudage Tab pour éviter le contact direct de l’impression de soudure avec le film aluminium-plastique lors de l’emballage ultérieur.
(6) Inspection de la taille CCD après soudage à languette pour assurer la cohérence de la taille de la production de noyaux de batterie.
(7) Après le soudage, le test Hi-pot est effectué sur la cellule de la batterie pour s’assurer qu’il n’y a pas de conductivité entre les bornes positive et négative de la cellule soudée.
(8) Contrôle de déviation du film plastique en aluminium pour assurer le taux de rendement de poinçonnage du film plastique en aluminium.
(9) Détection de la taille de la batterie par CCD après l’emballage pour assurer la cohérence de l’apparence et de la taille de la batterie.
(10) Après l’encapsulation, le test Hi-pot est effectué sur la batterie pour s’assurer qu’il n’y a pas de conductivité entre les bornes positive et négative de la cellule encapsulée.
(11)Le test d’isolation de la batterie après encapsulation est effectué pour s’assurer qu’il n’y a pas de conductivité entre les bornes positive et négative de la pile encapsulée et le film aluminium-plastique.
(12) Testez l’épaisseur du joint de la batterie après l’emballage pour vous assurer de la consistance du joint de la batterie après l’emballage.
Grâce à la série de méthodes et de points de contrôle mentionnés ci-dessus, la qualité de la batterie sur l’ensemble de la chaîne de montage peut être contrôlée efficacement.
2. Fonctions principales et description de l’équipement
Les batteries au lithium sont un type de batterie qui utilise du lithium métal ou un alliage de lithium comme matériau d’électrode négative et utilise une solution électrolytique non aqueuse. Les principaux composants des batteries au lithium sont les électrodes positives et négatives, les électrolytes, les séparateurs et les boîtiers. Les batteries au lithium Pouch-Pack sont des batteries avec une coque en polymère placée sur une batterie lithium-ion liquide et emballée dans un film composite aluminium-plastique. Par rapport aux batteries cylindriques et aux batteries à coque en aluminium, la composition de la batterie est la même, mais la forme de l’emballage et la structure physique de la batterie sont différentes, ce qui conduit à ce que la forme d’assemblage et le processus de production de la batterie pouch soient différents. La structure est illustrée sur la figure.
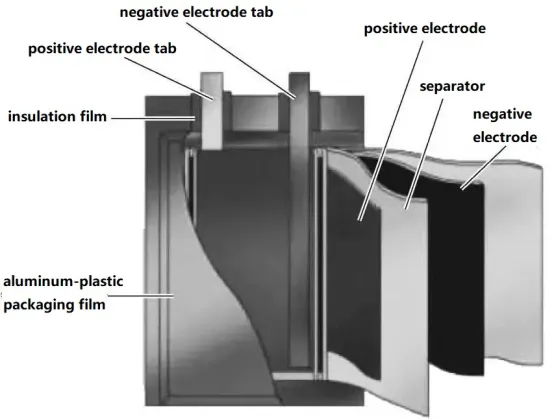
Structure cellulaire de poche
Le processus de production de la ligne d’assemblage de batteries de poche peut être divisé en trois parties : la première partie est la partie de soudage de languette, la deuxième partie est la partie de machine d’emballage et la troisième partie est la partie de poinçonneuse de fosse
Les principaux indicateurs techniques d’une ligne d’assemblage de cellules de poche sont les suivants :
(1) Taux de qualification du produit : ≥99%.
(2) Efficacité de production globale de la ligne : En fonction des exigences de la ligne de production.
(3) Nombre d’opérateurs nécessaires à la ligne de production : 2 personnes.
(4) Taux d’utilisation global de l’équipement : ≥98% [Formule de calcul : (24h – temps d’arrêt – temps d’alarme)/24 × 100%].
(5) Taux de qualification des équipements d’emballage : ≥98,8 %.
3.Composition de l’équipement et structures clés
La ligne d’assemblage de cellules de poche se compose principalement d’une machine à souder les languettes d’électrodes, d’une machine d’emballage et d’une machine de post-emballage.
3.1 Machine à souder les onglets
La machine à souder les languettes est chargée de plier et de pré-souder les languettes en cuivre ou en aluminium des cellules nues reçues de la machine à empiler. Il effectue des processus tels que le soudage final par ultrasons des languettes, l’aplatissement des empreintes de soudure, le dépoussiérage et l’application d’adhésif pour préparer l’encapsulation ultérieure dans les poches de film aluminium-plastique. Les structures clés de la machine à souder les languettes d’électrode comprennent le pré-soudage des languettes de cellule, la découpe des languettes, le soudage final des languettes de cellule, l’aplatissement de l’empreinte de soudure et le dépoussiérage, et l’application d’adhésif.
La machine à souder les languettes effectue le pré-soudage et le soudage final des languettes des cellules nues reçues de la machine à empiler. Ses structures clés comprennent la découpe de languettes, le pré-soudage de languettes, le soudage de languette à languette et le dépoussiérage d’empreintes de soudures.
Le pré-soudage des languettes consiste à plier et à souder les languettes de cuivre ou d’aluminium de la cellule, les préparant ainsi au processus de soudage final. Les composants de cette structure comprennent une machine de pré-soudage, une base de machine à souder, un mécanisme de pliage et un mécanisme de dépoussiérage. La structure du pré-soudage des languettes est illustrée dans le schéma.
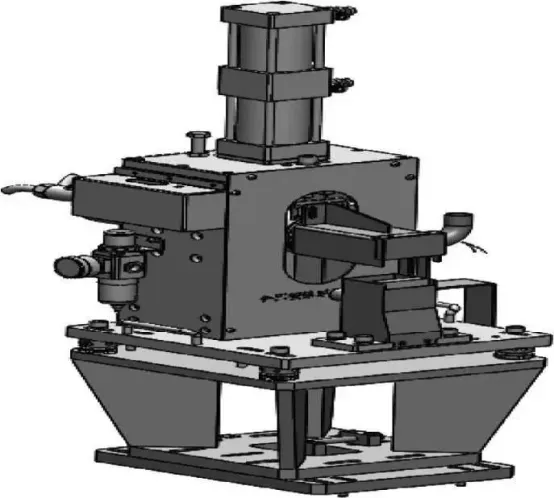
1) Pré-soudure des languettes
La fonction et l’action de cette structure sont utilisées pour réaliser le pré-soudage par ultrasons des languettes. La tête de soudage sous la machine à souder est fixe (la conception de la tête de soudage, de la base de soudage et de la base doit être communiquée au client). Une fois les languettes de cellule en place, le cylindre est enfoncé La pince à palette atteint la hauteur de travail de pré-soudage et la poussière est collectée pendant le soudage ; et les languettes sont rassemblées pendant le soudage. Il y a un dispositif de protection sur le noyau de la batterie soudé pour empêcher les scories de soudure de tomber dans le noyau de la batterie. La tête de soudage inférieure a un couvercle anti-poussière, et il y a un dispositif d’adsorption de poussière à l’intérieur du couvercle anti-poussière, y compris un dispositif de soufflage et un dispositif d’adsorption de poussière pour garantir que la poussière de soudage peut être absorbée proprement ; La vitesse du vent d’aspiration des poussières doit être de ≥15 m/s.
Pour la précision de la position de soudage de la pré-soudure de la languette, l’écart dans les directions haut et bas doit être de ≤±0,2 mm et l’écart dans les directions gauche et droite est de ≤±0,2 mm.
Remarques : La ligne d’emballage de soudage doit être connectée aux données en fonction de la machine à souder et peut collecter les paramètres de soudage clés (les paramètres de soudage comprennent l’énergie, la puissance, le temps, la pression, etc.), et peut recevoir des informations anormales de soudage pertinentes, effectuer des alarmes anormales et décharger la cellule NG.
2) Coupe de languette
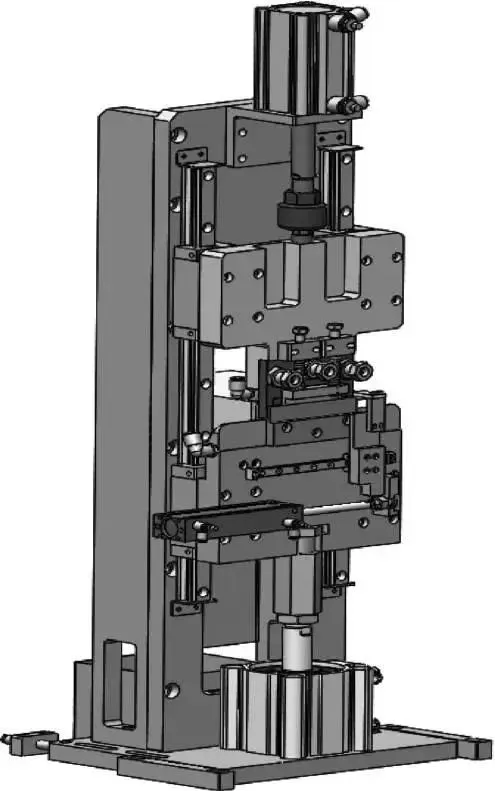
La structure de coupe des languettes est principalement utilisée pour couper soigneusement les languettes de cuivre et d’aluminium pré-soudées. Il se compose de lames de coupe supérieures et inférieures, de mécanismes de guidage de lames de coupe supérieures et inférieures, d’un mécanisme de dépoussiérage, d’une goulotte de guidage des déchets, d’un cylindre supérieur, d’un cylindre inférieur et d’autres composants. La structure de la coupe de la languette d’électrode est illustrée à la figure.
Cette structure est utilisée pour réaliser la découpe automatique des languettes d’électrodes positives après le pré-soudage. Les outils de coupe utilisent SKD11 avec un revêtement en carbone de type diamant pour éviter l’adhérence. Les outils de secours sont utilisés dans le cadre d’une approche individuelle, et le traitement au carbure de tungstène peut être appliqué au SKD11 selon les exigences du client. Il y a un micromètre numérique pour régler la position de coupe, ce qui facilite le réglage manuel, et la lame de coupe coupe sur l’empreinte de soudure de pré-soudage. La plage de réglage de la longueur de la languette de coupe est de 0 à 10 mm, avec une précision de coupe de ±0,1 mm. La durée de vie de la lame de coupe est qu’elle peut être utilisée au moins 300 000 fois (avec un rappel pour l’affûtage toutes les 200 000 fois), et qu’elle peut être réaffûtée plus de 10 fois. Il y a un capot étanche à la poussière au niveau de la lame de coupe, isolant le mécanisme de coupe de l’environnement extérieur. La hotte étanche à la poussière est dotée d’un dispositif d’adsorption de la poussière pour assurer la propreté en adsorbant les déchets de coupe et la poussière. La vitesse d’écoulement d’air requise pour l’extraction de la poussière est de ≥15 m/s. Il y a une boîte de réception à l’intérieur du mécanisme de coupe pour collecter le matériau de la feuille coupée. La plaque de coupe a une conception convexe et la force du ressort est réglable. Avant la découpe, le film protecteur des deux côtés est pressé pour éviter que le film protecteur ne se déforme et n’affecte les processus ultérieurs.
3.Soudage final de la languette
Le processus de soudage final des languettes se compose du mécanisme d’alimentation des languettes positives/négatives et du processus de soudage principal des languettes d’électrodes positives/négatives.
(1) Mécanisme d’alimentation de languette positive/négative : Le mécanisme d’alimentation de languette positive/négative se compose d’un mécanisme d’alimentation de type magasin de languettes, d’un dispositif de levage servo, d’un mécanisme d’aspiration de languette, d’un mécanisme de positionnement secondaire, d’un capteur de détection de mécanisme de chargeur, etc. Il est utilisé pour réaliser l’alimentation automatique des languettes positives et négatives.
La fonction principale du mécanisme d’alimentation des languettes positives/négatives est le processus critique de soudage de la poignée conductrice des languettes et des languettes positives/négatives prédécoupées ensemble. Dans la production réelle, les languettes doivent être alimentées en continu. Pour assurer un changement de matériau ininterrompu sans arrêter la machine, un mécanisme de tampon à languettes doit être conçu dans le mécanisme. Le robot de récupération d’onglets doit disposer d’une fonction de rotation pour éviter les erreurs d’orientation des onglets. La détection de polarité des languettes consiste à détecter la polarité des languettes positives et négatives afin d’éviter un placement incorrect par les humains. Le mécanisme de positionnement des languettes est nécessaire en raison de la précision de position entre les languettes de cellule et les languettes pendant le soudage. Les points de référence de positionnement peuvent être les côtés des languettes et l’adhésif PP ou l’environnement des languettes, selon les besoins du client. Le mécanisme d’alimentation des languettes maintient en toute sécurité les languettes correctement positionnées et les dépose à la position prédéterminée pour le soudage final. En raison des exigences de précision de position, le mécanisme d’entraînement est une combinaison d’un servomoteur et d’une vis à billes pour assurer la précision. Le mécanisme d’alimentation par languette positive/négative est illustré dans la figure ci-jointe.
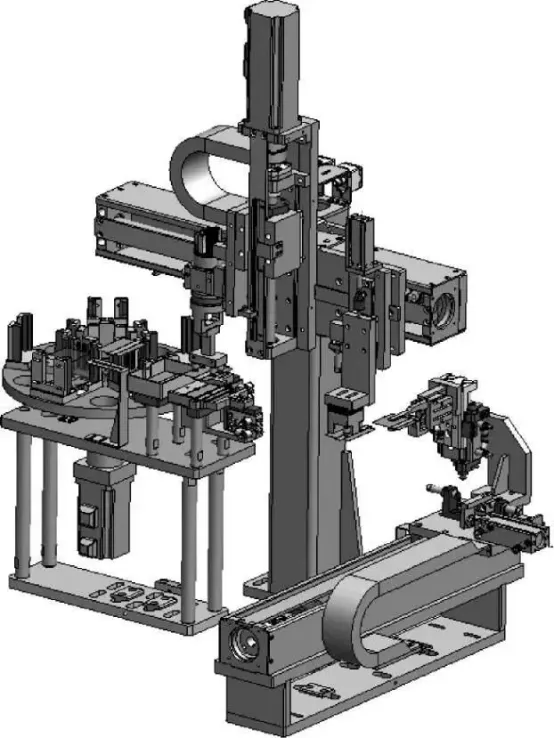
Les fonctions et actions du mécanisme de chargement d’onglets positif/négatif sont les suivantes :
un. Il y a un total de 5 chargeurs sur le mécanisme du chargeur. Les magazines positifs et négatifs se distinguent par des couleurs et des marquages. Un chargeur peut contenir 200 onglets à la fois, et il peut fonctionner en continu pendant plus de 2 heures avec une seule alimentation.
Précision dimensionnelle de b.Tab pour les matériaux entrants : Les languettes sont placées manuellement dans le clip lors de la réception du matériau. La batterie utilise des procédures de brossage, de soufflage d’air et de secousses électriques pour éviter plusieurs pièces, assurant ainsi un taux de qualification de 100 %. La détection de la position de la poignée conductrice permet d’identifier les côtés positifs et négatifs. Les bornes positives et négatives se distinguent par leur couleur. Le transfert de 6 magasins est effectué par des servos, et il y a des capteurs sur la position de chargement du matériau pour détecter la présence de matériaux. La servo-rotation est adoptée pour éviter un décalage de positionnement excessif, ce qui peut provoquer une distorsion des oreilles de la languette.
c. Le positionnement de la languette utilise le positionnement mécanique pour positionner le côté court du clip conducteur et la colle de la languette.
d. Pour le serrage et le chargement, un cylindre à doigts est utilisé pour serrer la poignée conductrice dans la plus grande zone afin d’éviter le glissement de la poignée conductrice. La méthode de transfert servo permet une alimentation précise et la précision de positionnement de la languette est de ±0,2 mm.
(2) Soudure principale des languettes d’électrode positive/négative. Les principaux composants du soudage principal des languettes positives / négatives sont la machine à souder par ultrasons, le mécanisme de positionnement, le système de détection, le système de dépoussiérage, etc. La soudure principale des languettes positives/négatives est comme indiqué sur la figure.
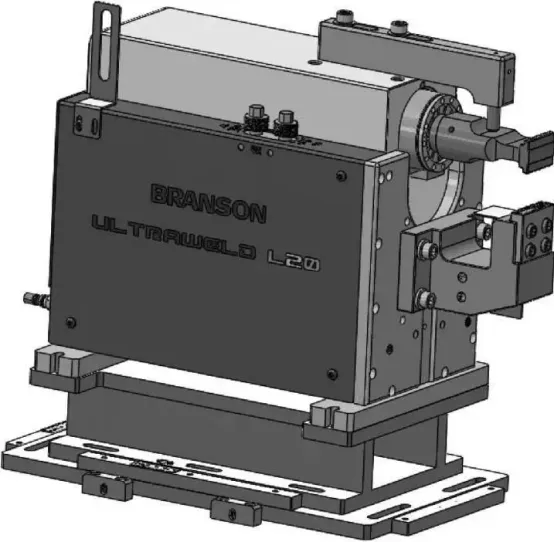
Le soudage principal des languettes positives/négatives est utilisé pour réaliser le soudage par ultrasons des languettes positives et négatives. La tête de soudage inférieure de ce mécanisme est fixe et les languettes sont soudées au-dessus des languettes de la batterie. L’ensemble de la machine à souder peut être réglé horizontalement pour s’adapter aux exigences du processus.
Les caractéristiques techniques du soudage principal à languette positive/négative sont les suivantes :
a.La durée de vie à usage unique de la pointe de soudage/matrice inférieure est de ≥ 50 000 fois et elle peut être réaffûtée plus de 5 fois sur une seule surface. La compatibilité de la pointe de soudage/matrice inférieure avec le nombre de couches de soudage par languette est de ≤50 couches. La conception de la pointe de soudage/matrice inférieure et de la base doit être communiquée à la partie A.
b.Après le soudage, il existe un dispositif pour détecter si la languette est soudée à la poignée conductrice. Le système générera une alarme et déclenchera l’appareil NG (non bon) en cas de problème avec la batterie.
c. Les paramètres clés du soudage (les paramètres de soudage comprennent l’énergie, la puissance, le temps, la pression, etc.) peuvent être définis avec des limites supérieures et inférieures. Il a les fonctions de détection en ligne, d’alarme anormale, d’exclusion de cellule NG et de poignée conductrice réservée pour le soudage vers le haut et vers le bas.
d. Traitement de dépoussiérage : Il y a un dispositif de protection sur le côté du noyau de batterie soudé pour empêcher les scories de soudure de tomber dans le noyau de la batterie. Faites un couvercle anti-poussière pour suivre le mouvement de la tête de soudage, et allumez la poussière pendant le soudage par ultrasons. La vitesse du vent d’aspiration de la poussière est de 20 m / s, ce qui peut aspirer efficacement la poussière métallique.
e. Précision : La précision de positionnement de la languette est de ±0,2 mm ; La précision de la position de soudage est de ±0,2 mm de haut en bas, et de ±0,2 mm à gauche et à droite.
f. Les paramètres de soudage ont un stockage local et ont la fonction d’interface pour se connecter avec MES. Un port de dépoussiérage manuel est ajouté, et le poste de soudage a pour fonction de vérifier si la languette de soudage est présente et de détecter la languette après le soudage.
4) Dépoussiérage de la soudure à languette
Le dépoussiérage des marques de soudure de la languette est crucial pour le taux de rendement et les performances de sécurité du noyau de la batterie. La raison principale est que le processus de soudage par ultrasons est un soudage par friction mécanique, qui produira beaucoup de poussière métallique, et de nombreuses bavures pointues tomberont sur les marques de soudage. Parfois, il peut également devenir une source de poussière métallique. Une fois que cette poussière métallique a pénétré dans le corps de la batterie, elle percera le séparateur entre les électrodes positive et négative, provoquant un court-circuit de la batterie et provoquant des accidents dangereux tels qu’un incendie.
Le dépoussiérage de la languette est divisé en deux parties : le mécanisme d’aplatissement de l’estampage par soudage et le mécanisme de dépoussiérage secondaire par emboutissage par soudage.
(1) Mécanisme de soudage et d’aplatissement. L’aplatissement du tampon de soudage consiste à estampiller et à aplatir le tampon de soudure après le soudage final de la pièce Tab. Son objectif principal est d’aplatir ou d’enlever les bavures du tampon à souder à la surface de la languette après le soudage par ultrasons, afin de faciliter le dépoussiérage secondaire du tampon à souder. Il est facile de se préparer pour le travail. Il y a également un orifice d’aspiration de la poussière sur ce mécanisme pour éliminer la poussière du laitier de soudage qui est directement pressée et facile à aspirer.
Le mécanisme d’emboutissage et d’aplatissement de soudage se compose d’un mécanisme de déplacement du cylindre supérieur, d’un mécanisme de levage inférieur, d’un bloc de pressage, d’un couvercle à vide, etc. Il est principalement utilisé pour réaliser le façonnage après soudage des languettes, la pression de façonnage est de ≥500N et le matériau de la plaque de pression est PEEK. Il n’y a pas de gauchissement après le façonnage, la position de mise en forme est réglable et le mécanisme de soudage et d’aplatissement est comme indiqué sur la figure.
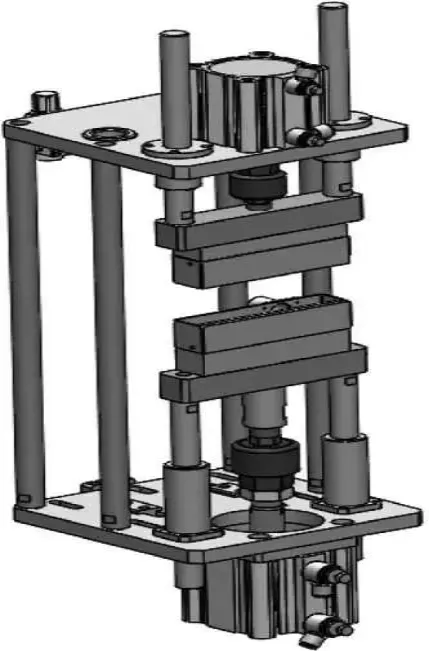
(2) Empreinte de soudure Mécanisme secondaire de dépoussiérage. Le but du dépoussiérage secondaire de l’empreinte de soudage est d’éliminer indépendamment la poussière de l’empreinte de soudure, en nettoyant soigneusement la poussière métallique qui n’a pas été éliminée par le mécanisme d’aplatissement.
Le mécanisme secondaire de dépoussiérage se compose principalement d’un mécanisme de mouvement de cylindre, d’une chambre scellée, d’un mécanisme de brosse, etc. Sa fonction et ses actions sont les suivantes : utilisation d’un dispositif de nettoyage pour nettoyer la zone de soudage, en s’assurant qu’il n’y a pas de particules étrangères de plus de 50 μm après le nettoyage. Il dispose également d’un dispositif d’adsorption de la poussière pour assurer un nettoyage en profondeur de la poussière, avec une vitesse de flux d’air d’extraction de poussière de ≥20m/s. Le processus de nettoyage ne doit pas provoquer de contamination secondaire de la cellule de la batterie et ne doit pas endommager les languettes d’électrode. Le mécanisme secondaire de dépoussiérage de l’empreinte de soudage est illustré dans la figure ci-jointe.
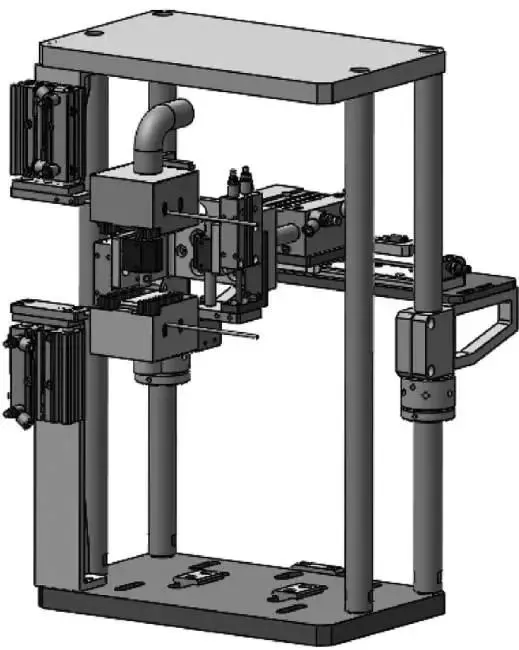
Le mécanisme d’aplatissement des empreintes de soudage et le mécanisme de dépoussiérage secondaire assurent la fluidité des processus ultérieurs tels que l’application de la colle et l’emballage, ainsi que la fusion de l’air chaud.
5.Collage et inspection d’onglets
Le collage des empreintes d’onglets est réalisé en appliquant du ruban adhésif pour s’assurer que lors de l’emballage ultérieur, la surface inégale des empreintes n’entre pas en contact direct avec le film aluminium-plastique, évitant ainsi le risque de perforation de l’adhésif PP et de contact direct avec la couche d’aluminium.
Le processus de collage et d’inspection des onglets se compose de deux parties : le mécanisme de collage des onglets et le mécanisme d’inspection du collage des onglets.
(1) Mécanisme de collage de languette : Le mécanisme de collage de languette se compose d’un mécanisme d’alimentation en ruban adhésif, d’un mécanisme de tension, d’un mécanisme de guidage, d’un mécanisme de coupe automatique, d’un mécanisme d’aspiration d’adhésif, etc. Le processus de collage implique des mécanismes de collage supérieurs et inférieurs séparés. Le mécanisme de collage est divisé en mécanisme de collage supérieur et en mécanisme de collage inférieur, qui fonctionnent tous deux de la même manière. La longueur du ruban adhésif est compatible avec ≤100 mm et la largeur est de ≤25 mm. Il garantit que le ruban adhésif bleu recouvre complètement l’empreinte et les bords inférieurs de la languette, avec un collage soigné et sans appuyer sur l’adhésif PP sur la poignée conductrice. Dans le mécanisme de collage, la tension du ruban adhésif bleu pendant le processus de traction est contrôlée par la tension du ressort pour garantir que le ruban adhésif bleu ne rebondit pas, ne se froisse pas ou ne se détache pas après le collage, ce qui permet une adhérence complète et correcte. Le matériau de la tête d’aspiration adhésive est anodisé dur A6061, ce qui n’endommage pas la languette. Il peut atteindre une précision de position de collage de ±0,2 mm, une précision d’alignement vertical de ±0,2 mm et une précision de coupe de ±0,2 mm. Le schéma du mécanisme de collage des onglets est illustré dans la figure ci-jointe.
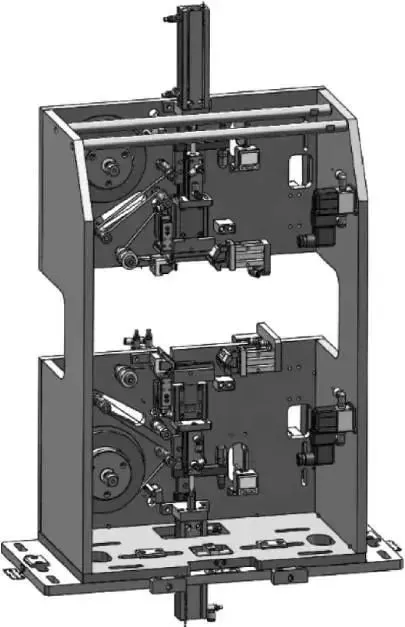
(2) Mécanisme d’inspection de collage de languettes. L’objectif principal du mécanisme d’inspection du collage des languettes est de détecter la présence de ruban adhésif au niveau des empreintes de languette de la cellule de batterie et d’aplatir le ruban adhésif.
Le mécanisme d’inspection du collage se compose principalement de cylindres, de blocs de pression, de sondes et d’autres composants. Le mécanisme d’inspection du collage des empreintes de languettes est illustré dans la figure ci-jointe.
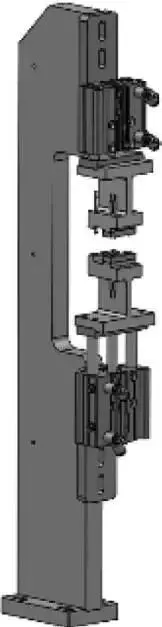
Après le traitement du mécanisme de collage des languettes et du mécanisme d’inspection du collage, l’impact des empreintes de soudure sur l’emballage du film aluminium-plastique est efficacement évité.
(2) Poinçonneuse de film aluminium-plastique
La poinçonneuse à film aluminium-plastique déroule activement la bobine de film aluminium-plastique et perfore les poches de film aluminium-plastique de manière séquentielle pour répondre aux exigences de taille de la batterie. Les structures clés de la poinçonneuse de film aluminium-plastique comprennent principalement le mécanisme de déroulement et de correction, le mécanisme de refendage, le mécanisme de poinçonnage, le mécanisme de coupe, etc.
(1) Mécanisme de déroulement et de correction : Le mécanisme de déroulement et de correction est la section avant de la poinçonneuse à film aluminium-plastique. Il est responsable du chargement, du changement et du déroulement du film aluminium-plastique, ainsi que de la correction en temps réel du film aluminium-plastique pendant le fonctionnement normal.
Le mécanisme de déroulement et de correction se compose d’un arbre d’expansion d’air, d’un mécanisme de positionnement du film aluminium-plastique, d’un mécanisme de déroulement actif (y compris moteur, réducteur, etc.), d’un système de contrôle de la tension, d’une plate-forme de réception du matériau, d’un système de correction, etc. Ses fonctions et actions sont les suivantes : chargement manuel, positionnement du cylindre du rouleau de matériau, détection par capteur photoélectrique de la présence du matériau, plate-forme d’alimentation manuelle de la bande avec couteau de découpe de film aluminium-plastique et plaque de pressage de la bande, et un dispositif d’aspiration de poussière à pression négative sous la plate-forme d’alimentation de la bande. La tension du film aluminium-plastique est ajustée par un contrôleur de tension et un frein à poudre magnétique pour maintenir une tension constante et une direction d’alimentation constante. Il dispose d’une double structure de déroulement pour assurer un fonctionnement rapide et l’efficacité de l’ensemble de la chaîne de production. Le mécanisme de déroulement et de correction est illustré sur la figure ci-jointe.
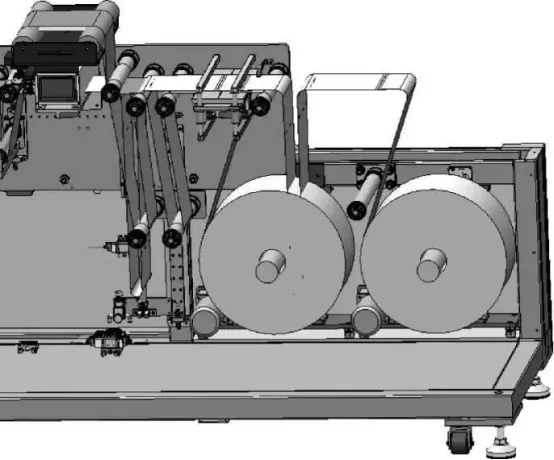
Les paramètres de précision pertinents du mécanisme de déroulement et de correction sont les suivants :
Plage de tension : 0-100N
Précision du contrôle de la tension : ±3N
Détection du diamètre du rouleau : Portée de détection ≥ 400 mm, précision de détection requise ±0,1 mm
Pour s’assurer que le film aluminium-plastique n’est pas endommagé pendant le transport, un traitement et un traitement spéciaux ont été appliqués aux rouleaux de guidage. Le galet de guidage est fabriqué en alliage d’aluminium anodisé dur noir A6061, avec une épaisseur de revêtement supérieure à 4 μm et une rugosité de surface de Ra0,8. La durée de vie peut dépasser 3 ans (tout en assurant l’efficacité de l’équipement, le taux d’utilisation et le taux de qualification du produit). Des roulements à faible frottement sont utilisés pour l’arbre à rouleaux afin de minimiser la résistance à la rotation.
(2) Mécanisme de refendage : Le mécanisme de refendage se compose principalement de roulements linéaires, de colonnes, de cylindres, de lames de coupe et de plaques de fixation de lame. Ses principales fonctions et actions sont les suivantes : avant de perforer les poches, il est utilisé pour relâcher les contraintes en le fendant entre les deux couches de film aluminium-plastique. La lame de coupe utilise une lame de couteau artistique pour faciliter l’approvisionnement et la préparation. Lorsque le matériau est en place, l’aspiration sous vide de la plate-forme est activée et le cylindre supérieur entraîne le mécanisme de coupe pour fendre le film. Le mécanisme de coupe est doté d’un couvercle d’aspiration de poussière, qui peut aspirer négativement la poussière générée pendant le processus de coupe, garantissant ainsi que les déchets de coupe et la poussière sont efficacement éliminés. La vitesse de débit d’air d’aspiration requise est de ≥15 m/s. La précision de la position de pré-coupe est de 0,3 mm et la plage de réglage de la longueur de coupe peut être sélectionnée selon les besoins. Le mécanisme de refendage est illustré dans la figure ci-jointe.
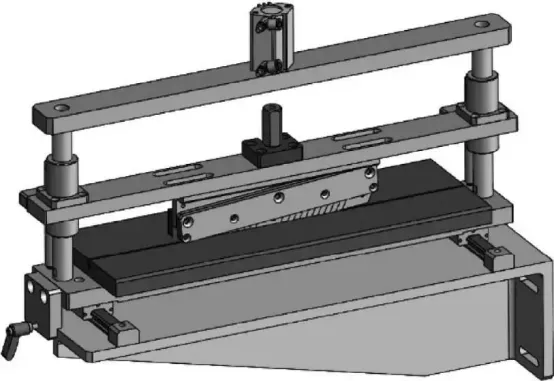
Le mécanisme de refendage prépare le poinçonnage du film aluminium-plastique en découpant des fentes sur le film aluminium-plastique.
(3) Mécanisme de poinçonnage de la fosse. Le mécanisme de poinçonnage est principalement composé d’un moule de poinçonnage de coque, d’un servomoteur, d’un réducteur, d’une vis à billes, d’un cylindre, d’un arbre de guidage, etc.
Le mécanisme de poinçonnage de la fosse utilise plusieurs cylindres pour comprimer le film aluminium-plastique, et un servomoteur entraîne la vis à billes pour perforer la fosse. La profondeur peut être réglée librement à l’aide d’une pochette de 2 à 12 mm. La force de pression du film aluminium-plastique est ajustée par le servo. Le moule a pour fonction de perforer les trous de positionnement. Il utilise une méthode de poinçonnage à double fosse. La précision dimensionnelle de la coquille de poinçonnage peut être contrôlée à ±0,1 mm. Les trous de goupille de positionnement sont poinçonnés par un cylindre et la précision de poinçonnage est élevée. ±0,1 mm, les déchets de trou d’épingle sont évacués des deux côtés de la plaque inférieure du moule. Les deux côtés du moule de poinçonnage de l’équipement sont équipés de caillebotis (perpendiculaires à la direction de transport de la bande). Lorsqu’un corps étranger est détecté, l’alarme émet un bip et la machine s’arrête. La maintenance est équipée de fonctions de protection de sécurité pour éviter que le personnel de maintenance ne soit piégé par le moule. mal.
Le mécanisme de poinçonnage a des exigences de changement de moule, de sorte que chaque poinçonneuse est équipée d’un chariot de moule pour faciliter le changement de moule.
Le mécanisme de poinçonnage est utilisé à de nombreuses reprises, le choix des matériaux est donc très important. Il existe principalement les types de matériaux suivants : plaque inférieure 45 # trempée + nickelage, plaque supérieure 45 # trempée + nickelée, colonne principale 45 # trempée + chromée, modèle supérieur SKD11 + trempe + nitruration, moule concave SKD11 + trempe + nitruration, poinçon KD11 + trempe + nitruration, plaque fixe de poinçon 45 # + nickelage. Le mécanisme de poinçonnage est illustré à la figure.
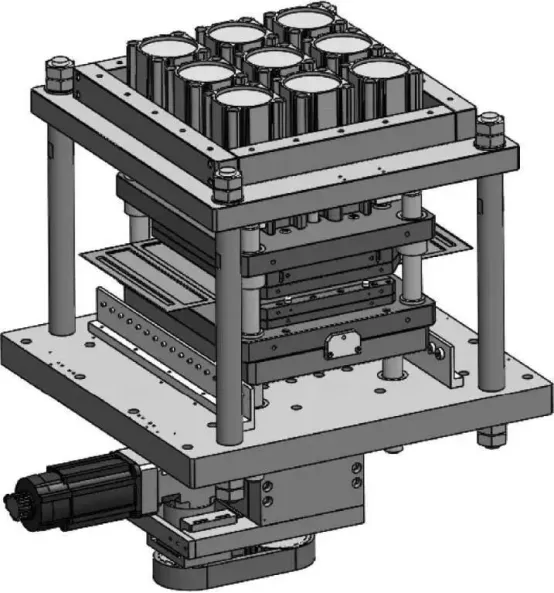
(4) Mécanisme de coupe. Le mécanisme de coupe se compose principalement de tiges de guidage, de lames de coupe, de sièges de fixation de lame, de cylindres supérieurs, de cylindres inférieurs, d’un mécanisme de dépoussiérage, etc. Sa fonction et son action sont de couper le film aluminium-plastique en longueurs fixes, avec un dispositif de dépoussiérage pendant la coupe. La lame de coupe a généralement une durée de vie de 300 000 à 500 000 coupes (avec une alarme de rappel de durée de vie) et peut être affûtée plus de 10 fois. Le tranchant est équipé d’un système d’aspiration de la poussière pendant la coupe. La vitesse de débit d’air d’aspiration requise est de ≥20 m/s et la précision de coupe de la coque en aluminium-plastique est de ±0,2 mm. Le mécanisme de coupe est illustré dans la figure ci-jointe.
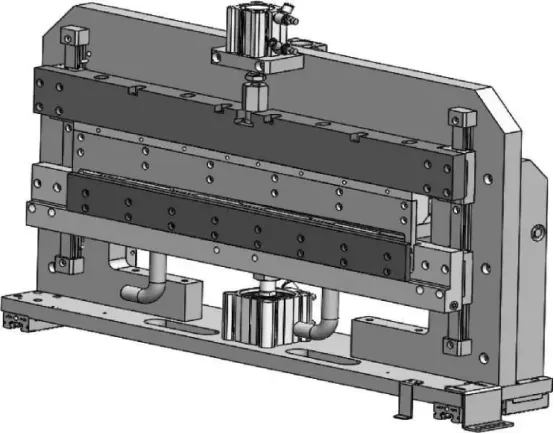
(3)Machine d’emballage
La machine d’emballage assemble le noyau de batterie soudé par la machine à souder les languettes et le film aluminium-plastique estampé par la poinçonneuse en une forme de batterie préliminaire. Les structures clés de la machine d’emballage comprennent principalement la pince de la machine d’emballage, le mécanisme de pliage, le mécanisme de coupe, le mécanisme de scellage supérieur/latéral, etc.
(1) Dispositif de machine d’emballage. Le dispositif de la machine d’emballage est un support important pour l’assemblage de films aluminium-plastique et de cellules de batterie pour réaliser divers processus. Il se compose de crémaillères, de roulements angulaires, de cavité supérieure, de cavité inférieure, de ventouses, de blocs de positionnement, etc. Son principe de fonctionnement est que la cavité inférieure est fixée sur le support et que les ventouses à vide sont raisonnablement réparties ; la cavité supérieure est retournée par le mécanisme de retournement de l’appareil à travers la crémaillère et le pignon, ce qui peut atteindre les trois exigences de position d’ouverture, de fermeture et de maintenance, et les ventouses à vide sont raisonnablement réparties ; film d’aluminium Après avoir été placé dans la cavité du moule, la ventouse à vide travaille pour déterminer la position du film d’aluminium, et la position du film d’aluminium reste inchangée pendant le flux de chaque station. Étant donné que le film aluminium-plastique est un corps de poche, afin d’assurer la position de taille relative entre la fosse du film aluminium-plastique et le noyau de la batterie, les cavités supérieure et inférieure sont traitées en copiant les dimensions extérieures du noyau de la batterie, et la précision de traitement peut atteindre ±0,2 mm, afin de rendre la pince aussi légère que possible et d’assurer les exigences de résistance, le matériau est généralement A6061 et oxydé en surface, ce qui est durable. Après pliage, l’alignement des bords du film d’aluminium est de ±0,2 mm. Dispositif de la machine d’emballage comme indiqué sur la figure.
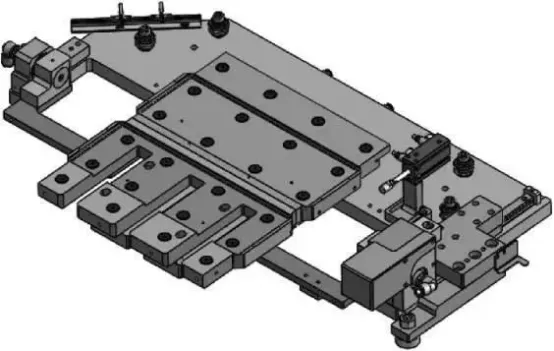
Le mécanisme de pliage se compose principalement de cylindres de levage, de cylindres d’avancement/rétraction, de guides linéaires, de plaques de pliage, etc. Sa fonction principale et son action sont les suivantes : le cylindre de levage reste en position supérieure et le servo d’avancement/rétraction pousse la plaque pliante à la position directement au-dessus de la ligne de pliage du film d’aluminium. Le cylindre de levage se déplace ensuite vers le bas pour appuyer sur le film d’aluminium, en alignant le bord de la plaque de pliage avec la ligne de pliage du film. Le dispositif rotatif se ferme, et le cylindre d’avancement/rétraction retire la plaque de pliage, replie complètement le film d’aluminium, et se déplace vers le poste de travail suivant. À ce stade, il n’y a pas de cellules de batterie à l’intérieur du film aluminium-plastique. La précision globale du mécanisme de pliage peut atteindre ±0,2 mm. Le mécanisme de pliage est illustré dans la figure ci-jointe.
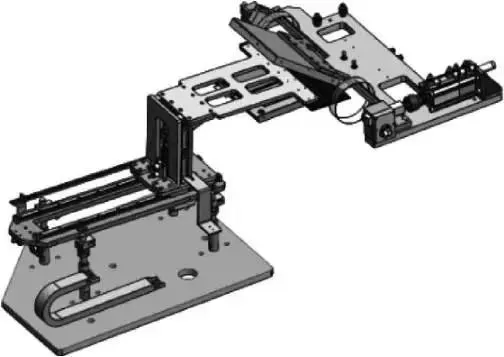
(3) Mécanisme de coupe. Le mécanisme de coupe est principalement utilisé pour couper le film aluminium-plastique sur la machine d’emballage. Il est principalement composé d’un cylindre d’entraînement de coupe supérieur, d’un cylindre d’entraînement de coupe inférieur, d’un couteau supérieur, d’un couteau inférieur, d’un mécanisme de pressage, d’un rail de guidage linéaire, d’un mécanisme de dépoussiérage et d’un régulateur de pression. Il est composé de soupapes, etc., et il y a un micromètre à la position de coupe pour faciliter le réglage manuel. La fonction et l’action sont les suivantes : la plaque tournante tourne d’une station, le cylindre inférieur se déplace, le couteau inférieur se soulève, le cylindre supérieur se déplace, la plaque de pression du ressort entre en contact avec le film aluminium-plastique, puis coupe le film aluminium-plastique, et le cylindre se réinitialise en même temps. Le mécanisme de coupe est illustré sur la figure.
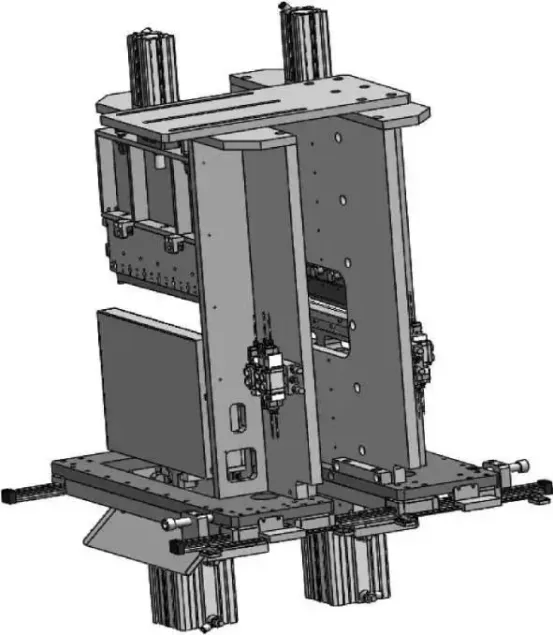
Le mécanisme de coupe inférieur du mécanisme de coupe comprend une boîte de réception de matériau pour collecter le film aluminium-plastique coupé. Le mécanisme de coupe est équipé d’un couvercle étanche à la poussière qui isole la zone de coupe de l’environnement extérieur pendant le processus de coupe. Le couvercle étanche à la poussière contient un dispositif de dépoussiérage, y compris un dispositif de soufflage et un dispositif de dépoussiérage à pression négative, garantissant que les déchets de coupe et la poussière peuvent être collectés efficacement. La vitesse de débit d’air d’aspiration de poussière requise est de ≥20 m/s. La précision de coupe du bord supérieur est de ≤0,2 mm et la précision d’alignement du bord supérieur après la coupe est également de ≤0,2 mm. La lame de coupe a une durée de vie de 300 000 à 500 000 coupes (avec un rappel pour l’affûtage de la lame), et elle peut être affûtée plus de 10 fois. Un micromètre numérique est utilisé pour assurer une précision de réglage de 0,01 mm.
(4) Mécanisme d’étanchéité supérieur/latéral. Le mécanisme d’étanchéité supérieur/latéral est principalement utilisé pour l’étanchéité supérieure ou latérale des batteries. Il se compose principalement d’un servomoteur, d’une vis à billes, d’un guide linéaire, d’un mécanisme de tamponnage, d’un mécanisme de positionnement de languette, d’un mécanisme de réglage fin, d’une tête d’étanchéité NAK80, d’un régulateur de température, d’un tube chauffant, d’un thermocouple et d’autres composants. La fonction et l’action sont les suivantes : la tête de soudure est chauffée à l’aide d’un chauffage électrique et la température de la tête de soudure peut être réglée de la température ambiante à 250°C. Pendant le fonctionnement de l’équipement, l’écart de température global de la tête d’étanchéité est inférieur à ±3°C. La puissance du tube chauffant est de 1500W et sa durée de vie est d’un an. La précision du contrôle de la température est de ≤5°C. Il faut moins de 10 minutes pour chauffer de la température ambiante à 200°C. Le siège chauffant de la tête d’étanchéité est conçu avec une plaque d’isolation thermique pour la compensation de la température, garantissant que la température reste dans la plage requise lors de l’étanchéité à grande vitesse. Une fois que la batterie tourne vers ce poste de travail, les servomoteurs supérieur et inférieur entraînent simultanément la vis à billes pour fermer les têtes d’étanchéité supérieure et inférieure pour l’étanchéité thermique. La plage de réglage de la pression d’étanchéité est de 0 à 20 kgf/cm2. La tête d’étanchéité est conçue avec des fentes de languette. L’écart entre le corps de la batterie et la tête d’étanchéité est réglable, et il y a un micromètre numérique pour le réglage. Le temps de soudure est réglable de 0 à 8 secondes avec une précision de réglage de 0,1 seconde. La précision de scellage dans la zone de la languette est de ±20 μm, tandis que dans la zone sans languette, elle est de ±15 μm. Le mécanisme d’étanchéité supérieur/latéral est illustré sur la figure ci-jointe.
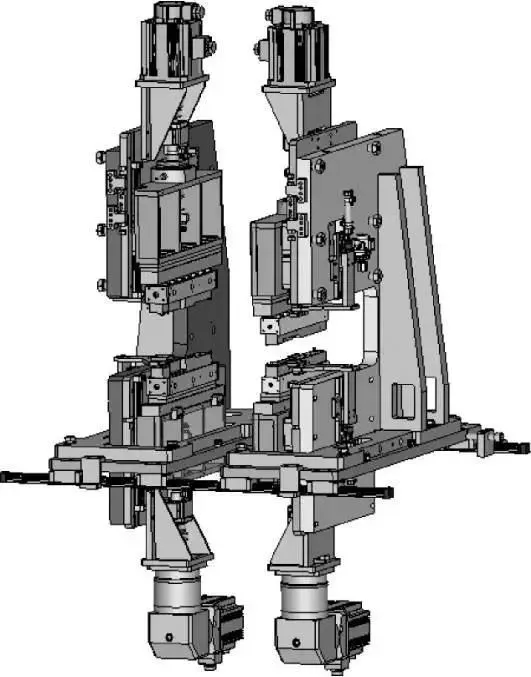