パウチパック電池組立ラインは、リチウム電池製造の中期から後期のプロセスの重要な部分です。主に、組み立てられた、または巻かれたベアセルの取り扱いと、タブ溶接、テーピング、セルケーシング、上面シーリングなどの操作の実行を担当します。組立ラインの設計原理は、セルのサイズ、構造、望ましい生産効率などの要素を考慮に入れた、リチウム電池の製造プロセスに基づいています。
1.概要ポーチパック組立ライン
1.1設計原則と組立ラインの原則
パウチパックバッテリーの組立ラインの形状の選択は、主にセルのサイズ仕様によって決まります。長さが390mm未満のセルの場合、タブ溶接機、包装機、および包装機の後段は、一般的にカムスプリッターによって駆動されるターンテーブル構造を採用しています。この構造レイアウトはコンパクトで、床面積が小さくなっています。ただし、ターンテーブルの精度には制限があります。ターンテーブルが大きいほど、セルの組み立て精度は低下します。さらに、負荷の増加は、ターンテーブルの始動と停止の難しさと効率にも影響します。
長さが390mmを超えるセル仕様の場合、タブ溶接機、包装機、および包装機の後続セクションは、一般に線形構造を採用しています。このレイアウトにより、大型バッテリーのステーション切り替え時に正確な位置決めが可能になり、ステーション切り替えの効率が高くなり、生産効率を向上させる可能性が高くなります。しかし、このレイアウトは床面積が比較的狭いという欠点があり、駅切替の駆動機構が複雑で、コストが比較的高くなってしまいます。線形組立ラインのレイアウトを下の図に示します。
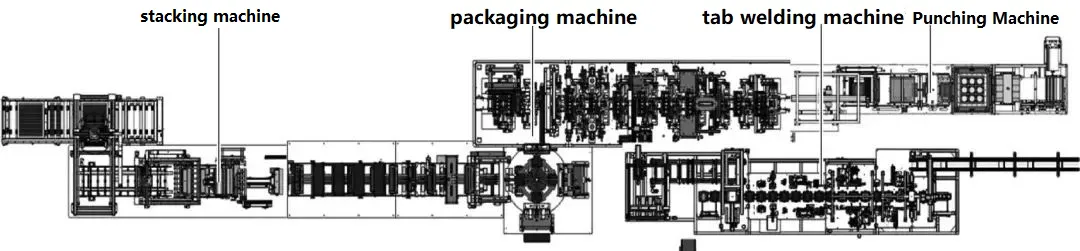
1.2集会線効率流通
建設ラインの設計プロセスでは、リズムの制御は主に各ステーション生産のボトルネックステーションの制限に依存します。例えば、実際の生産能力要件は8PPMです。機器の包括的な生産能力に関しては、実際の設計は一般的に10PPMに基づいており、限界作業制限は、溶接機セクションのタブプレ溶接における保護シート供給機構のようなマルチステーション方式で行われます。 タブ溶接のタブ送り機構、上部と下部のシール包装時間、包装機のサイドシール包装時間など。生産能力要件を比較した後、各ステーションに必要な処理時間を計算します。それが満たされない場合は、マルチステーション設計が必要です。たとえば、機器の効率要件が12PPMの場合、各バッテリーセルの処理時間と製造時間は5秒です。一部の顧客のパッケージング時間要件は、バッテリーセルステーションのスイッチング時間とパッケージングメカニズムの動作時間に加えて、4〜5秒に達します。、生産効率の要件を満たすことができないため、生産効率の要件を満たすために、このステーションのダブルワークステーションを設計する必要があります。他のワークステーションのビート分布は同じです。
1.3物流方法
バッテリーを組み立てるとき、ワークステーション間の移動と切り替えにロジスティクスを使用する必要があります。したがって、さまざまな州のバッテリーに対して合理的な物流方法を選択する必要があります。
(1)スタッキングマシンから排出される裸セルには、セルの輸送効率を確保し、セルの安全性を保護するために、通常、倍速チェーン+セルクランプの方法が使用されます。倍速チェーンは輸送効率が高く、長期生産に適しています。長距離輸送、大負荷、簡単なメンテナンスなどの利点があり、倍速チェーンプロファイルは、ストップやその他の補助構造の設置と調整を設定するための優れた柔軟性を備えています。デメリットは、倍速チェーンが摩擦を起こしやすく、粉塵が発生することです。バッテリーコアへのほこりの影響を避けるために、一部のメーカーは磁気浮上コンベヤーラインを使用して裸のバッテリーを輸送しますが、これは高価です。
(2)電気コアはスタッキングマシンから溶接機に運ばれます。溶接機の各ステーションには、電気コアの位置決め精度に対する高い要件があります。電気コアは溶接治具に装填され、段階的な輸送方法を採用しています。精度を確保するために、要件に応じて、ドライブはサーボモーター+シフトフォークの循環構造を採用しています。
(3)バッテリーコアを溶接機から降ろした後、サーボモーター+同期ベルト輸送方式が一般的に使用されます。これにより、バッテリーコアの輸送間隔が等くなり、ロボットの荷降ろしと積み込みのグラブ位置の精度が向上します。同様に、包装機の後にも同じ方法が採用されており、経済的で効率的です。
1.4 セルの位置決め方法と原理
バッテリーセルの組立ラインでは、バッテリーメーカーは、プロセスの観点からバッテリーセルに特定の寸法精度要件を設けています。したがって、バッテリーセルは、バッテリーが組立ラインに入る前に配置する必要があります。バッテリーセルは同じ基準で配置されています。後続の各ワークステーション調整もこれに基づいており、バッテリーアセンブリの一貫性を確保します。
バッテリーコア本体の形状は長方形なので、位置決めに関しては、通常、2つの側面を位置決め基準として使用し、他の2つの側面を押してバッテリーコアを位置決めします。また、バッテリー本体の中央位置決め方法を使用して、バッテリー本体を前後左右に同時に押すこともできます。位置決め方法の選択は、ベンチマークが一貫している限り、一般に、バッテリーコアのプロセスサイズ要件と構造設計の利便性に依存します。
1.5 ダストコントロール
バッテリーの製造工程で最も致命的な危険は、金属粉塵がバッテリー本体に侵入し、バッテリーの短絡や火災などの一連の問題を引き起こすことです。このような状況を避けるためには、組立ラインの粉塵の発生源を厳密に管理し、可能な限り除去する必要があります。粉塵を抑制するためには、まず粉塵の発生源を突き止め、的を絞った対策を講じる必要があります。
(1)ラミネート機コンベアライン(倍速チェーン)。輸送プロセス中、倍速チェーンは倍速チェーンプロファイルにこすれて大量の粉塵が発生します。この種の粉塵については、バッテリーコアに粉塵が落ちるのを防ぐために、倍速チェーンライン本体に防塵プレートを取り付ける必要があります。同時に、バッテリーコアクランプはできるだけ小さくする必要があります。コンベアは上下のクランプで搬送され、リターンライン上の空の固定具は固定点で粉塵が払われます。除塵方法は、ブロー+吸引で行います。ラインが比較的長いため、ホコリの溜まりなどを防ぐために手作業による清掃の頻度を増やす必要があります。
(2)組立ライン。組立ラインでバッテリーを循環させると、タブの事前はんだ付け、切断、タブ溶接、はんだスタンピングステーションなど、一部のワークステーション自体が粉塵を生成する可能性があります。切断ステーションまたは溶接ステーションがある限り、それらはインストールされます。特殊な除塵機構により、滞りなく集塵を行います。下の写真は、除塵ステーションの地図を示しています。
1.6品質管理
バッテリー製造品質の安定性と一貫性を確保するために、バッテリー製造のあらゆる側面で品質管理に対応する検出センサーがあります。組立ラインの場合、具体的な症状は次のとおりです。
(1)カラーセンサーは、主に手動介入後にバッテリーが逆放電するのを防ぐために、入力されるバッテリーコアの極性を検出するために使用されます。
(2)バッテリーコードをスキャンして、バッテリー情報がタイムリーにMESシステムにアップロードされていることを確認し、バッテリー製造情報の追跡を容易にします。
(3)バッテリーコアのX線検査は、バッテリーコアの位置合わせを検出するために使用され、その後の深刻な位置ずれのバッテリーの生成を防ぎます。
(4)溶接エラーを回避するためのタブ極性検出と正および負の検出。
(5)タブ溶接後の接着剤検出により、その後のパッケージング中にはんだ印刷物がアルミニウムプラスチックフィルムに直接接触するのを防ぎます。
(6)バッテリーコア生産のサイズの一貫性を確保するためのタブ溶接後のCCDサイズ検査。
(7)溶接後、バッテリーセルにHi-pot試験を行い、溶接セルの正極端子と負極端子の間に導電性がないことを確認します。
(8)アルミプラスチックフィルムのパンチング歩留まりを確保するためのアルミプラスチックフィルム偏差制御。
(9)パッケージ後のバッテリーのCCDサイズ検出により、バッテリーの外観とサイズの一貫性を確保します。
(10)カプセル化後、バッテリーでHi-potテストを実施して、カプセル化されたセルの正端子と負極の間に導電性がないことを確認します。
(11)封止後の電池の絶縁試験は、封止されたセルの正極端子と負極端子とアルミプラスチックフィルムとの間に導電性がないことを確認するために行われます。
(12)包装後のバッテリーシールの一貫性を確保するために、包装後のバッテリーのシールの厚さをテストします。
上記の一連の制御方法とポイントにより、組立ライン全体のバッテリーの品質を効果的に制御できます。
2.機器の主な機能と説明
リチウム電池は、負極材料としてリチウム金属またはリチウム合金を使用し、非水電解質溶液を使用する電池の一種です。リチウム電池の主なコンポーネントは、正極と負極、電解質、セパレーター、ケーシングです。ポーチパックリチウム電池は、液体リチウムイオン電池にポリマーシェルを配置し、アルミニウム-プラスチック複合フィルムでパッケージ化した電池です。円筒形電池とアルミシェル電池と比べると、電池の組成は同じですが、包装形態や電池の物理的構造が異なるため、パウチパック電池の組み立て形態や製造工程が異なります。パウチパック電池構造を図に示します。
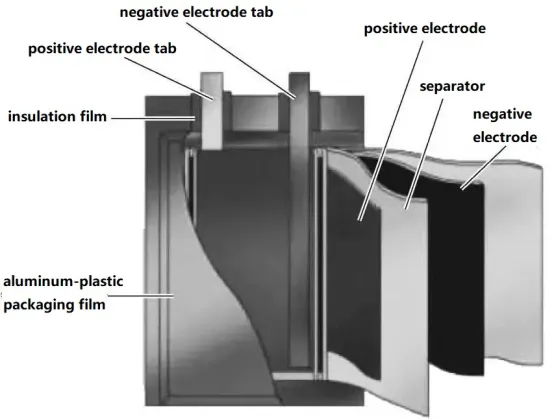
パウチセル構造
ポーチパックバッテリー組立ラインの製造プロセスは、最初の部分がタブ溶接部分、2番目の部分が包装機部分、3番目の部分がピットパンチングマシンの3つの部分に分けることができます
パウチセル組立ラインの主な技術指標は次のとおりです。
(1)製品認定率:≥99%
(2)ラインの全体的な生産効率:生産ラインの要件によって異なります。
(3)生産ラインに必要なオペレーター数:2人。
(4)総合設備稼働率:≥98%[計算式:(24時間-ダウンタイム-警報時間)/24×100%)]。
(5)包装機器認定率:≥98.8%
3.機器の構成と主要な構造
パウチセル組立ラインは、主に電極タブ溶接機、包装機、ポスト包装機で構成されています。
3.1タブ溶接機
タブ溶接機は、スタッキングマシンから受け取ったベアセルの銅またはアルミニウムタブを折り畳み、予備溶接する役割を果たします。タブの最終超音波溶接、溶接インプリントの平坦化、粉塵除去、接着剤塗布などのプロセスを実行して、アルミニウムプラスチックフィルムポケットにその後のカプセル化を準備します。電極タブ溶接機の主要な構造には、セルタブの事前溶接、タブ切断、セルタブの最終溶接、溶接インプリントの平坦化とダスト除去、および接着剤の塗布が含まれます。
タブ溶接機は、スタッキングマシンから受け取ったベアセルのタブの予備溶接と最終溶接を行います。その主要な構造には、タブ切断、タブ予備溶接、タブ間溶接、溶接インプリントの粉塵除去が含まれます。
タブの予備溶接では、セルの銅またはアルミニウムのタブを折りたたんで溶接し、最終的な溶接プロセスに備えます。この構造の構成要素には、プレ溶接機、溶接機ベース、折り畳み機構、および除塵機構が含まれます。タブプレ溶接の構造を図に示します。
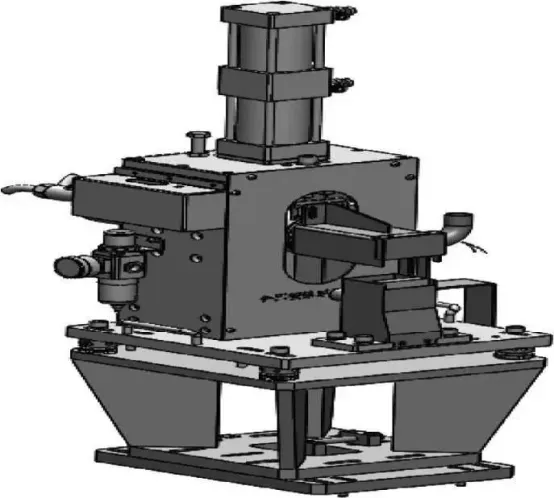
1)タブの事前はんだ付け
この構造の機能と動作は、タブの超音波予備溶接を実現するために使用されます。溶接機の下の溶接ヘッドは固定されています(溶接ヘッド、溶接ベース、およびベースの設計は、顧客とコミュニケーションをとる必要があります)。セルタブが所定の位置に配置された後、シリンダーが押されますパレットクランプは溶接前の作業高さに達し、溶接中にほこりが収集されます。そして、溶接中にタブが集められます。溶接されたバッテリーコアには、溶接スラグがバッテリーコアに落ちるのを防ぐための保護装置があります。下部溶接ヘッドにはダストカバーがあり、ダストカバーの内側には、溶接粉塵をきれいに吸収できるようにブロワー装置やダスト吸着装置などのダスト吸着装置があります。ダスト吸引風速は≥15m/sであることが求められます。
タブプレハンダ付けの溶接位置精度は、上下方向のずれが≤±0.2mm、左右方向のずれが≤±0.2mmであることが求められます。
備考:溶接包装ラインは、溶接機に応じてデータに接続する必要があり、主要な溶接パラメータ(溶接パラメータにはエネルギー、電力、時間、圧力などが含まれます)を収集でき、関連する溶接異常情報を受信し、異常なアラームを実行し、セルNGを放電できます。
2)タブカット
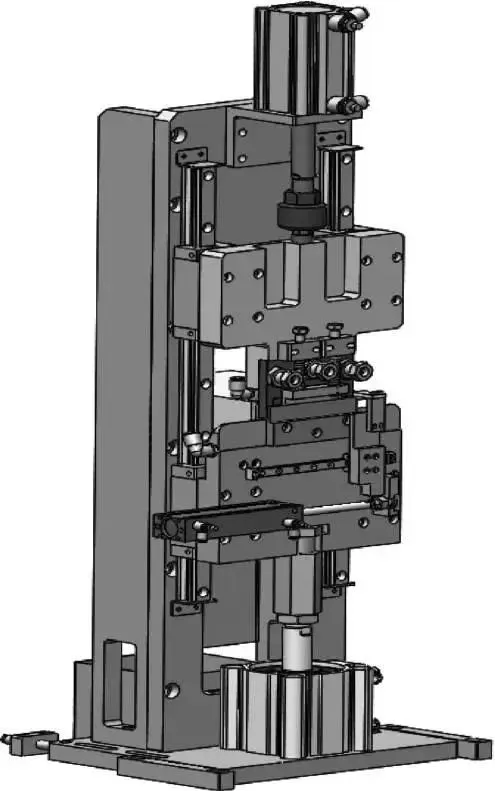
タブ切断構造は、主に溶接済みの銅とアルミニウムのタブをきれいに切断するために使用されます。上下のカッティングブレード、上下のカッティングブレードガイド機構、除塵機構、廃棄物ガイドシュート、上部シリンダー、下部シリンダー、およびその他のコンポーネントで構成されています。電極のタブカットの構造を図に示します。
この構造は、予備溶接後に正極タブの自動切断を実現するために使用されます。切削工具は、付着を防ぐためにダイヤモンドライクカーボンコーティングを施したSKD11を使用しています。バックアップツールは1対1のアプローチで使用され、タングステンカーバイド処理は顧客の要件に応じてSKD11に適用できます。切断位置を調整するためのデジタルマイクロメーターがあり、手動調整に便利で、溶接前の溶接インプリントに切断刃が切断されます。カットタブの長さの調整可能な範囲は0〜10mmで、カット精度は±0.1mmです。カッティングブレードの寿命要件は、最低300,000回使用でき(200,000回ごとに研ぐように注意してください)、10回以上再研ぐことができることです。カッティングブレードには防塵フードがあり、カッティングメカニズムを外部環境から隔離しています。防塵フードには粉塵吸着装置が付いており、切削くずやホコリを吸着して清潔さを確保しています。集塵気流速度の要件は≥15m / sです。切断機構内には、切断された箔材料を回収するための受け箱があります。カッティングプレートは凸型で、バネの力は調整可能です。切断する前に、保護フィルムが反り、その後のプロセスに影響を与えるのを防ぐために、両面の保護フィルムがプレスされます。
3.タブ最終溶接
タブの最終溶接プロセスは、正/負のタブ供給メカニズムと、正/負の電極タブの主な溶接プロセスで構成されています。
(1)正/負タブ送り機構:正/負のタブ送り機構は、タブマガジン式送り機構、サーボリフティング装置、タブ吸引機構、二次位置決め機構、マガジン機構検出センサーなどで構成されています。これは、正と負のタブの自動供給を実現するために使用されます。
ポジティブ/ネガティブタブ送り機構の主な機能は、タブ導電性ハンドルと事前にカットされたポジティブ/ネガティブタブを一緒に溶接する重要なプロセスです。実際の生産では、タブを連続的に供給する必要があります。機械を停止せずに材料交換を中断しないようにするには、メカニズムにタブバッファメカニズムを設計する必要があります。タブ回収ロボットには、タブの向きを間違えないように回転機能が必要です。タブの極性検出は、人間による誤った配置を防ぐために、正と負のタブの極性を検出することです。溶接時のセルタブとタブ間の位置精度のために、タブの位置決め機構が必要です。位置決め基準点は、お客様の要件に応じて、タブの側面とPP接着剤、またはタブの周囲にすることができます。タブの送り機構は、適切に配置されたタブをしっかりと保持し、最終溶接のために所定の位置に送ります。位置精度の要件により、駆動機構はサーボモーターとボールねじの組み合わせで精度を確保しています。正/負のタブ送りメカニズムを添付の図に示します。
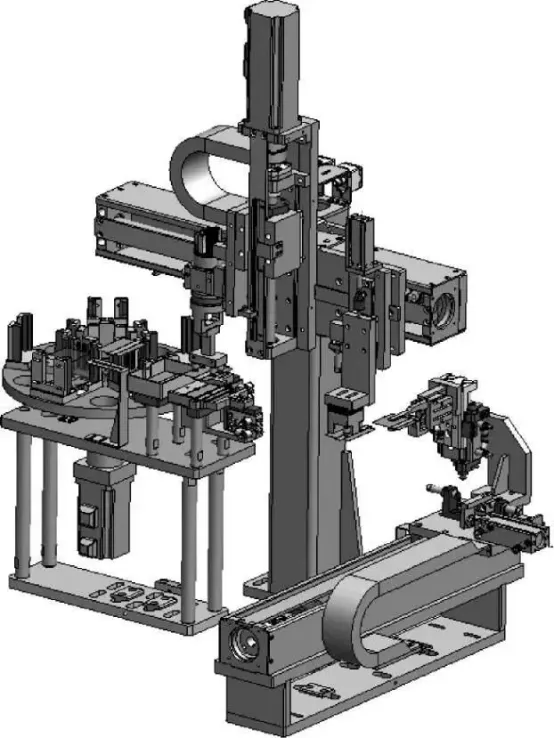
ポジティブ/ネガティブタブローディングメカニズムの機能とアクションは次のとおりです。
ある。マガジン機構には全部で5つのマガジンがあります。ポジティブマガジンとネガティブマガジンは、色とマーキングによって区別されます。1つのマガジンに一度に200個のタブを保持でき、1回の給餌で2時間以上連続して作業できます。
b.入力材料のTabの寸法精度:タブは、材料の受信中に手動でクリップに配置されます。バッテリーは、ブラッシング、エアブロー、および電気振とう手順を利用して複数のピースを防ぎ、100%の認定率を保証します。導電性ハンドルの位置の検出は、プラス面とマイナス面を識別するために使用されます。正と負の端子クランプは色で区別されます。6つのマガジンの転送はサーボで完了し、材料装填位置には材料の存在を検出するためのセンサーがあります。タブ耳の歪みの原因となる過度な位置決めオフセットを避けるため、サーボ回転を採用しています。
c. タブの位置決めでは、機械的な位置決めを使用して、導電性クリップとタブ接着剤の短辺を位置決めします。
d. クランプとローディングには、フィンガーシリンダーを使用して導電性ハンドルを最大領域にクランプし、導電性ハンドルの滑りを防ぎます。サーボ搬送方式により正確な送りを実現し、タブ位置決め精度は±0.2mmです。
(2)正極/負極タブの主溶接。ポジティブ/ネガティブタブの主な溶接の主なコンポーネントは、超音波溶接機、位置決め機構、検出システム、集塵システムなどです。ポジティブ/ネガティブタブの主な溶接は図の通りです。
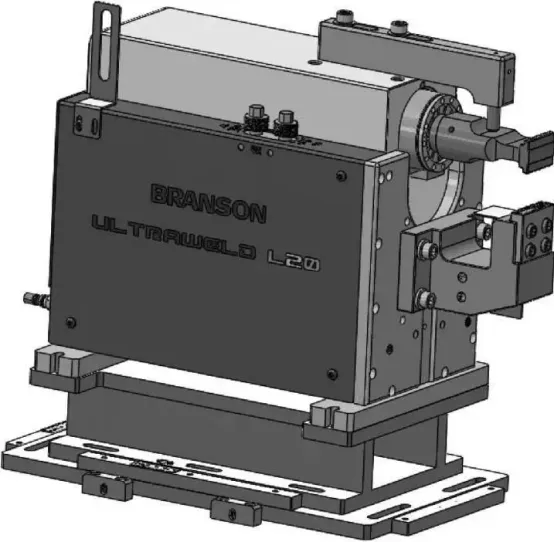
ポジティブ/ネガティブタブの主な溶接は、ポジティブタブとネガティブタブの超音波溶接を実現するために使用されます。このメカニズムの下部溶接ヘッドは固定されており、タブはバッテリータブの上に溶接されています。溶接機全体は、プロセス要件に適応するために水平に調整できます。
ポジティブ/ネガティブタブメイン溶接の技術的特徴は次のとおりです。
a.溶接チップ/ボトムダイのシングルユース寿命は≥50,000回で、1面で5回以上の再研磨が可能です。溶接チップ/ボトムダイとタブ溶接の層数との互換性は≤50層です。溶接チップ/ボトムダイとベースの設計は、パーティーAと通信する必要があります。
b.溶接後、タブが導電性ハンドルに溶接されているかどうかを検出する装置があります。システムはアラームを生成し、バッテリーに問題がある場合はNG(不良)デバイスをトリガーします。
溶接の主要なパラメータ(溶接パラメータには、エネルギー、電力、時間、圧力などが含まれます)は、上限と下限で設定できます。オンライン検出、異常アラーム、セルNG排除、上下溶接用の予約された導電性ハンドルの機能があります。
集塵処理:溶接されたバッテリーコアの側面には、溶接スラグがバッテリーコアに落ちるのを防ぐための保護装置があります。溶接ヘッドの動きに追従するようにダストカバーを作成し、超音波溶接中にダストをオンにします。粉塵吸引風速は20m / sで、金属粉塵を効果的に吸い取ることができます。
精度:タブの位置決め精度は±0.2mmです。溶接位置の精度は上下±0.2mm、左右±0.2mmです。
f.溶接パラメータにはローカルストレージがあり、MESと接続するためのインターフェース機能があります。手動の除塵ポートが追加され、溶接ステーションには溶接タブが存在するかどうかを確認し、溶接後にタブを検出する機能があります。
4)タブはんだ付けによるダスト除去
タブ溶接マークのほこり除去は、バッテリーコアの歩留まりと安全性能にとって重要です。主な理由は、超音波溶接プロセスが機械的な摩擦溶接であり、多くの金属粉塵が発生し、溶接マークに多くの鋭いバリが落ちることです。時には金属粉塵の原因にもなります。これらの金属粉塵がバッテリー本体に入ると、正極と負極の間のセパレーターを貫通し、バッテリーが短絡し、火災などの危険な事故を引き起こします。
タブの塵取り外しは2つの部分に分けられます:溶接押す平らにするメカニズムおよび溶接押す二次塵取り外しメカニズム。
(1)溶接・平坦化機構溶接スタンプの平坦化は、タブピースの最終溶接後にはんだ付けスタンプをスタンプして平らにすることです。その主な目的は、超音波溶接後にタブの表面のはんだ付けスタンプのバリを平らにするか、または除去して、はんだ付けスタンプの二次的なほこりの除去を容易にすることです。お仕事の準備も簡単です。また、この機構にはダスト吸引口があり、直接押し下げて吸い取りやすい溶接スラグのホコリを除去します。
溶接スタンピングおよび平坦化機構は、上部シリンダー移動機構、下部昇降機構、プレスブロック、真空カバーなどで構成されています。主にタブの溶接後の成形を実現するために使用され、成形圧力は≥500N、プレッシャープレートの材質はPEEKです。成形後の反りはなく、成形位置は調整可能で、溶接と平坦化のメカニズムは図の通りです。
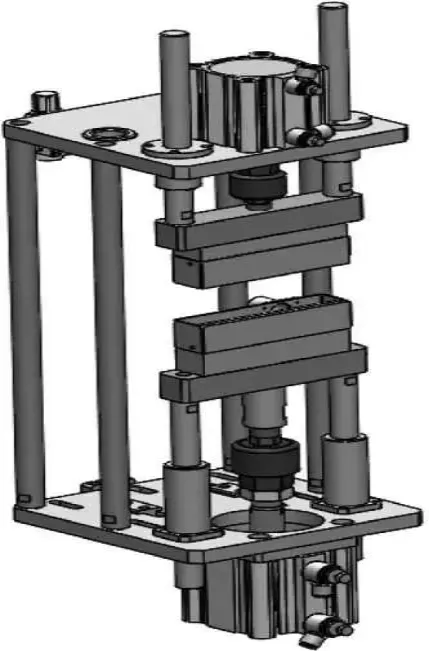
(2)溶接インプリント二次除塵機構。溶接インプリントの二次ダスト除去の目的は、溶接インプリントからダストを独立して除去し、平坦化機構によって除去されなかった金属ダストを徹底的に洗浄することです。
二次除塵機構は、主にシリンダー移動機構、密閉チャンバー、ブラシ機構などで構成されています。その機能と動作は次のとおりです:洗浄装置を使用して溶接領域を洗浄し、洗浄後に50μmを超える異物がないことを確認します。また、粉塵の徹底的な清掃を確実にするための粉塵吸着装置を備えており、集塵気流速度は≥20m/sです。クリーニングプロセスにより、バッテリーセルに二次汚染が発生したり、電極タブが損傷したりしてはなりません。溶接インプリントの二次除塵機構を添付の図に示します。
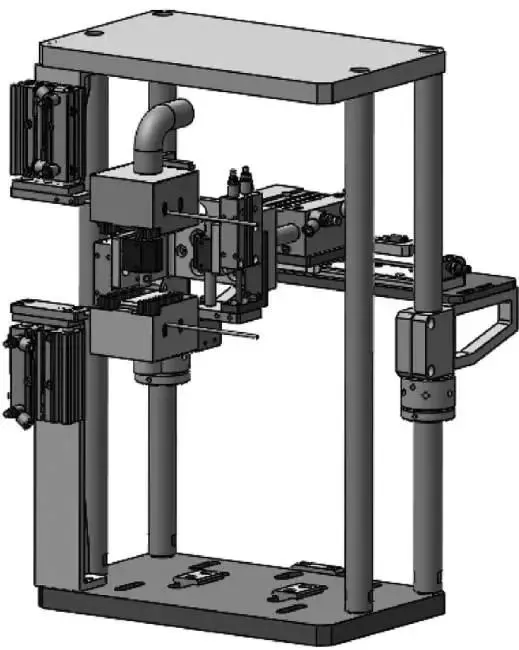
溶接インプリントの平坦化機構と二次除塵機構により、接着剤の塗布や包装などの後工程の滑らかさを確保し、熱風の融合も実現します。
5.タブの接着と検査
タブインプリントの接着は、その後の包装中にインプリントの凹凸のある表面がアルミニウムプラスチックフィルムに直接接触しないように粘着テープを貼ることによって達成され、PP接着剤に穴を開けてアルミニウム層に直接接触するリスクを回避します。
タブの接着と検査のプロセスは、タブの接着メカニズムとタブの接着検査メカニズムの2つの部分で構成されています。
(1)タブ接着機構:タブ接着機構は、粘着テープ供給機構、テンション機構、ガイド機構、自動切断機構、接着剤吸引機構などで構成されています。接着プロセスには、上部と下部の別々の接着メカニズムが含まれます。接着メカニズムは、上部接着メカニズムと下部接着メカニズムに分かれており、どちらも同じように機能します。粘着テープの長さは≤100mm、幅は≤25mmです。これにより、青い粘着テープがインプリントとタブの下端を完全に覆い、きちんとした接着で、導電性ハンドルのPP接着剤を押し下げることなく、きれいに接着します。接着機構では、引っ張りプロセス中の青い粘着テープの張力はスプリング張力によって制御され、接着後に青い粘着テープが跳ね返ったり、しわになったり、剥がれたりしないようにして、完全かつ適切な接着を実現します。粘着吸引ヘッドの材質は硬質アルマイトA6061で、タブを傷つけません。接着位置精度±0.2mm、垂直位置合わせ精度±0.2mm、切断精度±0.2mmを達成できます。タブ接着機構の図を添付図に示します。
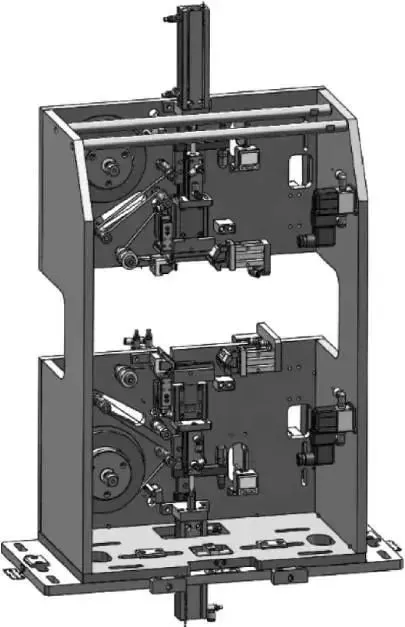
(2)タブ接着検査機構。タブ接着検査メカニズムの主な目的は、バッテリーセルのタブインプリントに粘着テープの存在を検出し、粘着テープを平らにすることです。
接着検査メカニズムは、主にシリンダー、圧力ブロック、プローブ、およびその他のコンポーネントで構成されています。タブインプリントの接着を検査するメカニズムを添付の図に示します。
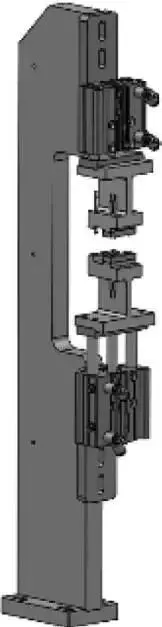
タブ接着機構と接着検査機構の処理後、アルミニウムプラスチックフィルム包装への溶接インプリントの影響が効果的に回避されます。
(2)アルミプラスチックフィルムパンチングマシン
アルミニウムプラスチックフィルムパンチングマシンは、アルミニウムプラスチックフィルムコイルを積極的に巻き戻し、バッテリーのサイズ要件を満たすためにアルミニウムプラスチックフィルムポケットを順番に打ち抜きます。アルミニウムプラスチックフィルムパンチングマシンの主要な構造には、主に巻き戻しおよび修正メカニズム、スリットメカニズム、パンチングメカニズム、切断メカニズムなどが含まれます。
(1)巻き戻しおよび修正メカニズム:巻き戻しおよび修正メカニズムは、アルミニウムプラスチックフィルムパンチングマシンの前部です。これは、アルミニウムプラスチックフィルムのロード、交換、巻き戻し、および通常の操作中のアルミニウムプラスチックフィルムのリアルタイム補正を担当します。
巻き戻しおよび修正機構は、空気膨張シャフト、アルミニウムプラスチックフィルム位置決め機構、アクティブ巻き戻し機構(モーター、減速機などを含む)、張力制御システム、材料受け入れプラットフォーム、補正システムなどで構成されています。その機能と動作は次のとおりです:手動ローディング、材料ロールのシリンダー位置決め、材料の存在の光電センサー検出、アルミニウムプラスチックフィルム切断ナイフとベルトプレスプレートを備えた手動ベルト供給プラットフォーム、およびベルト供給プラットフォームの下の負圧粉塵吸引装置。アルミニウムプラスチックフィルムの張力は、テンションコントローラーと磁性粉体ブレーキによって調整され、一定の張力と一貫した供給方向を維持します。これは、生産ライン全体のタイムリーな操作と効率を確保するために、二重巻き戻し構造を持っています。巻き戻しと修正のメカニズムを添付の図に示します。
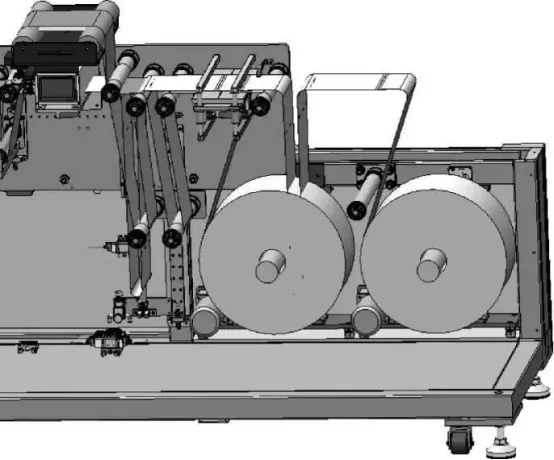
巻き戻しおよび修正メカニズムの関連する精度パラメータは次のとおりです。
張力範囲:0-100N
張力制御精度:±3N
ロール径検出:検出範囲≥400mm、検出精度要求±0.1mm
輸送中にアルミニウムプラスチックフィルムが損傷しないように、ガイドローラーには特別な処理と処理が施されています。ガイドローラーは黒色硬質アルマイトアルミニウム合金A6061でできており、コーティング厚は4μmを超え、表面粗さはRa0.8です。耐用年数は3年を超えることができます(機器の効率、稼働率、および製品の認定率を確保しながら)。ローラーシャフトには低摩擦ベアリングを採用し、回転抵抗を最小限に抑えています。
(2)スリット機構:スリット機構は、主にリニアベアリング、コラム、シリンダー、カッティングブレード、ブレード固定プレートで構成されています。その主な機能と動作は次のとおりです:ポケットを打ち抜く前に、アルミニウムプラスチックフィルムの2つの層の間にスリットを入れることにより応力を解放するために使用されます。カッティングブレードはアートナイフブレードを使用しており、調達や準備が容易です。材料が所定の位置にあると、プラットフォームの真空吸引が作動し、上部シリンダーが切断機構を駆動してフィルムをスリットします。切断機構にはダスト吸引カバーが付いており、切断プロセス中に発生するダストを負に吸い込むことができるため、カッティング廃棄物やホコリを効果的に除去できます。吸引気流速度の要件は≥15m / sです。プレカット位置精度は0.3mmで、必要に応じてカット長さの調整範囲を選択できます。スリット機構は添付の図に示します。
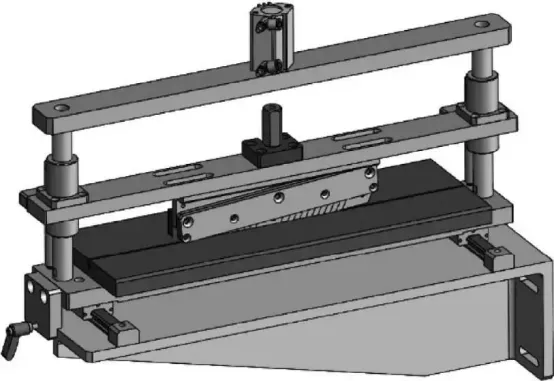
スリット機構は、アルミプラスチックフィルムにスリットを切開することで、アルミプラスチックフィルムの打ち抜きに備える機構です。
(3)ピットパンチ機構。パンチングメカニズムは、主にシェルパンチングモールド、サーボモーター、減速機、ボールねじ、シリンダー、ガイドシャフトなどで構成されています。
ピットパンチング機構は、複数のシリンダーを使用してアルミニウムプラスチックフィルムを圧縮し、サーボモーターでボールネジを駆動してピットをパンチします。奥行きはポーチウェアで自由に設定でき、設定範囲は2〜12mmです。アルミニウムプラスチックフィルムのプレス力はサーボによって調整されます。金型には位置決め穴を開ける機能があります。ダブルピットパンチング方式を採用しています。パンチングシェルの寸法精度は±0.1mm以内に制御できます。位置決めピン穴はシリンダーで穴を開けており、打ち抜き精度が高いです。±0.1mm、下部モールドプレートの両側からピンホールの老廃物が排出されます。装置パンチングモールドの両側には、グレーチング(ベルト搬送方向に垂直)が装備されています。異物が検出されると、アラームが鳴り、機械が停止します。メンテナンスには、メンテナンス担当者が金型に引っかかるのを防ぐための安全保護機能が装備されています。害。
パンチングメカニズムには金型交換の要件があるため、各パンチングマシンには金型交換を容易にするための金型トロリーが装備されています。
打ち抜き機構は何度も使われるため、素材選びがとても重要です。主に次の材料タイプがあります:底板45#強化+ニッケルメッキ、天板45#強化+ニッケルメッキ、メインコラム45#強化+クロムメッキ、上部テンプレートSKD11 +焼入れ+窒化、凹型SKD11 +焼入れ+窒化、パンチKD11 +焼入れ+窒化、パンチ固定プレート45#+ニッケルメッキ。ピットパンチング機構を図に示します。
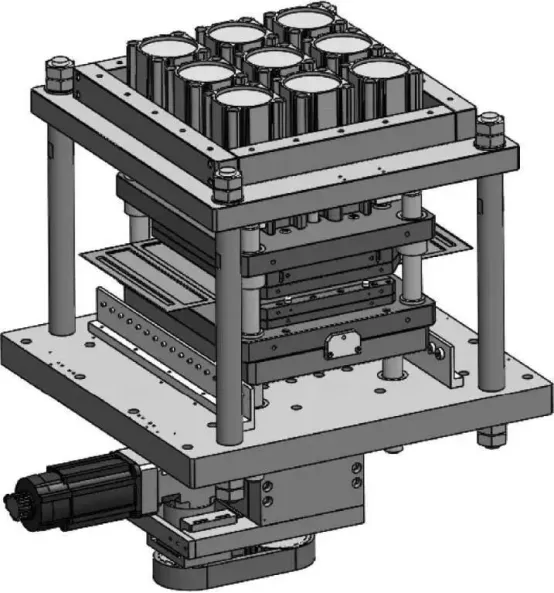
(4)切断機構。切断機構は、主にガイドロッド、切断刃、刃固定シート、上部シリンダー、下部シリンダー、除塵機構などで構成されています。その機能と動作は、切断中に除塵装置を使用して、アルミニウムプラスチックフィルムを固定長に切断することです。カッティングブレードの寿命は通常300,000〜500,000カット(寿命リマインダーアラーム付き)で、10回以上研ぐことができます。刃先には、切断時のダスト吸引システムが装備されています。吸引気流速度の要件は≥20m / sで、アルミニウムプラスチックシェルの切断精度は±0.2mmです。切断機構は添付の図に示されています。
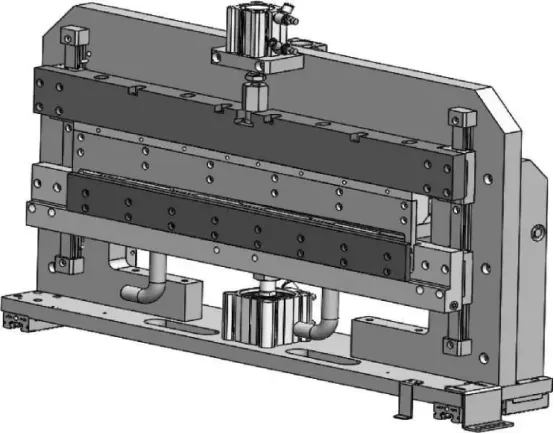
(3)包装機
包装機は、タブ溶接機で溶接されたバッテリーコアとパンチングマシンでプレスされたアルミニウムプラスチックフィルムを予備バッテリーフォームに組み立てます。包装機の主要な構造には、主に包装機クランプ、折り畳み機構、切断機構、上面/側面シール機構などが含まれます。
(1)包装機固定具。包装機の固定具は、アルミニウムプラスチックフィルムとバッテリーセルを組み立ててさまざまなプロセスを完了するための重要なキャリアです。ギアラック、アンギュラベアリング、上部キャビティ、下部キャビティ、吸盤、位置決めブロックなどで構成されています。その動作原理は、下部キャビティがブラケットに固定され、真空吸盤が合理的に分散されていることです。上部キャビティは、ラックとピニオンを介してフィクスチャ反転機構によって反転され、開閉、保守の3つの位置要件を達成でき、真空吸盤は合理的に分散されています。アルミフィルム金型キャビティに入れられた後、真空吸盤はアルミフィルムの位置を決定するために機能し、各ステーションの流れ中にアルミフィルムの位置は変わりません。アルミプラスチックフィルムはポーチ本体であるため、アルミプラスチックフィルムピットとバッテリーコアの間の相対的なサイズ位置を確保するために、バッテリーコアの外形寸法をコピーして上下のキャビティを加工し、加工精度は±0.2mmに達することができますクランプを可能な限り軽量にし、強度要件を確保するために、材料は一般的にA6061で、表面は酸化されており、耐久性があります。折り畳み後、アルミフィルムのエッジアライメントは±0.2mmです。図に示すように包装機の固定具。
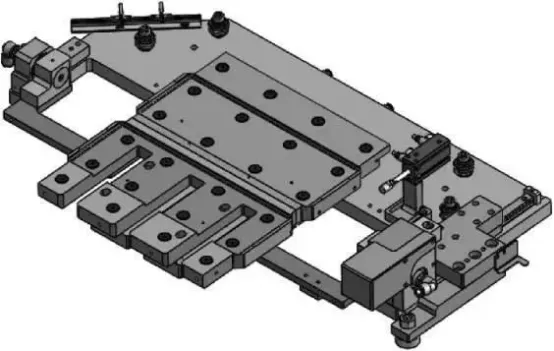
折り畳み機構は、主にリフティングシリンダー、前進/収縮シリンダー、リニアガイド、折り畳みプレートなどで構成されています。その主な機能と動作は次のとおりです:リフティングシリンダーはトップ位置に留まり、前進/収縮サーボは折り板をアルミフィルムの折り線の真上の位置に押します。次に、リフティングシリンダーが下向きに移動してアルミニウムフィルムをプレスし、折り板の端をフィルムの折り線に合わせます。回転固定具が閉じ、前進/格納シリンダーが折り畳みプレートを引き出し、アルミニウムフィルムを完全に折り畳み、次のワークステーションに移動します。この段階では、アルミニウムプラスチックフィルムの内部にバッテリーセルはありません。折り畳み機構の全体的な精度は±0.2mmに達することができます。折り畳み機構は添付の図に示されています。
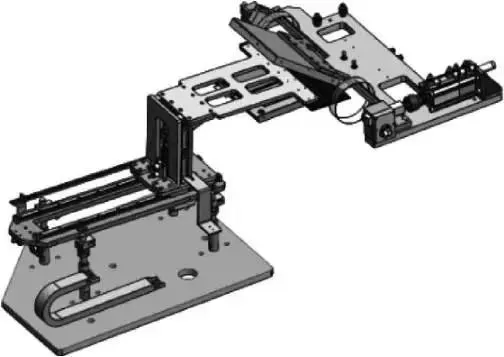
(3)切断機構。切断機構は、主に包装機のアルミニウムプラスチックフィルムを切断するために使用されます。主に上部カッター駆動シリンダー、下部カッター駆動シリンダー、上部カッター、下部カッター、プレス機構、リニアガイドレール、除塵機構、圧力調整器で構成されています。バルブなどで構成されており、切断位置にマイクロメーターがあり、手動での調整を容易にします。機能と動作は次のとおりです:ターンテーブルが1つのステーションを回転させ、下部シリンダーが移動し、下部ナイフが持ち上げられ、上部シリンダーが移動し、スプリングプレッシャープレートがアルミニウムプラスチックフィルムに接触し、次にアルミニウムプラスチックフィルムを切断し、シリンダーが同時にリセットされます。切断機構を図に示します。
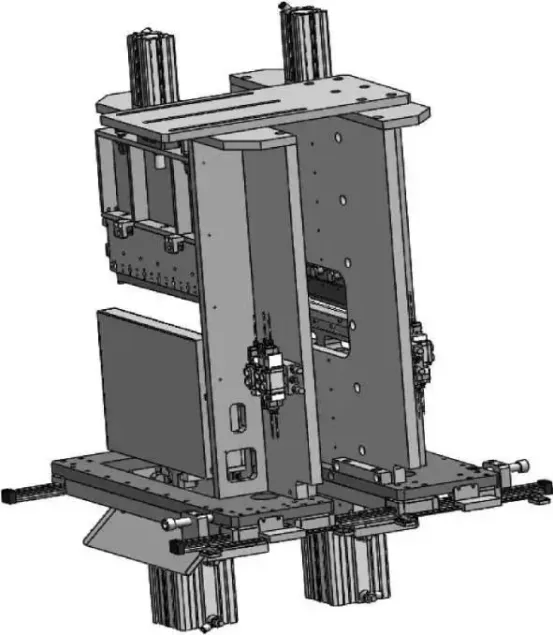
切断機構の下部切断機構には、切断されたアルミニウムプラスチックフィルムを回収するための材料受入ボックスが含まれています。切断機構には、切断プロセス中に切断領域を外部環境から隔離する防塵カバーが装備されています。防塵カバーには、ブロー装置や負圧除塵装置などの集塵装置が内蔵されており、切削屑や粉塵を効果的に回収することができます。ダスト吸引気流速度の要件は≥20m / sです。上端の切断精度は≤0.2mmで、切断後の上端の位置合わせ精度も≤0.2mmです。カッティングブレードの寿命は30万〜50万カット(刃研ぎのリマインダー付き)で、10回以上研ぐことができます。デジタルマイクロメータを採用し、0.01mmの調整精度を確保しています。
(4)トップ/サイドシール機構。上面/側面シール機構は、主にバッテリーの上部または側面のシールに使用されます。主に、サーボモーター、ボールねじ、リニアガイド、バッファリング機構、タブ位置決め機構、微調整機構、NAK80シーリングヘッド、温度コントローラー、加熱管、熱電対、およびその他のコンポーネントで構成されています。機能と動作は次のとおりです:シーリングヘッドは電気加熱を使用して加熱され、シーリングヘッドの温度は室温から250°Cまで調整できます。機器運転中、シーリングヘッドの全体的な温度偏差は±3°C未満です。加熱管の電力は1500Wで、寿命は1年です。温度制御精度は≤5°Cです。室温から200°Cまで加熱するのに10分もかかりません。シーリングヘッドヒーティングシートは、温度補償用の断熱プレートで設計されており、高速シーリング中も温度が必要な範囲内に留まるようにします。バッテリーがこのワークステーションに回転した後、上部と下部のサーボモーターが同時にボールねじを駆動して、サーマルシール用の上部と下部のシーリングヘッドを閉じます。シール圧力調整範囲は0〜20kgf/cm2です。シーリングヘッドはタブスロットで設計されています。バッテリー本体とシーリングヘッドの間のギャップは調整可能で、調整用のデジタルマイクロメーターがあります。シール時間は0秒から8秒まで調整可能で、調整精度は0.1秒です。タブエリアのシール精度は±20μm、ノンタブエリアでは±15μmです。上面/側面のシール機構を添付の図に示します。
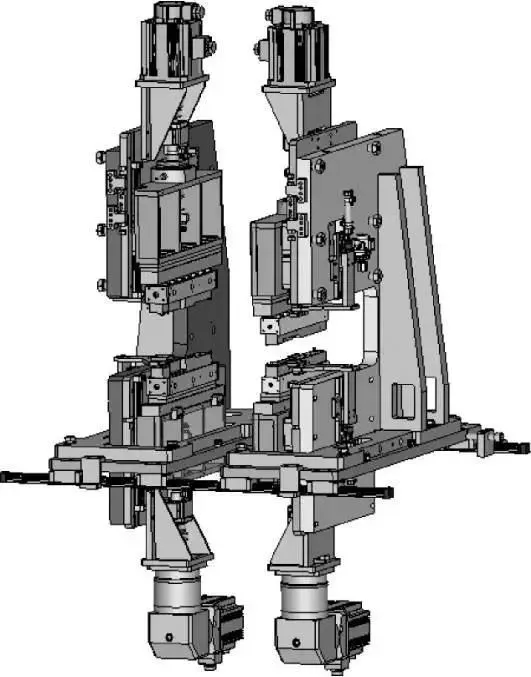