Le refendage, également connu sous le nom de refendage et de rembobinage, fait référence au processus de coupe longitudinale d’un film enduit de grande largeur en plusieurs bandes et de les rembobinage en rouleaux uniques supérieurs et inférieurs d’une certaine spécification de largeur. Les lames de refendage se composent principalement de lames de disque circulaires supérieures et inférieures, qui sont installées sur l’arbre du couteau de la machine à refendre et utilisent le principe de cisaillement par roulement pour fendre des produits tels que la feuille d’aluminium, la feuille de cuivre et les feuilles d’électrodes positives et négatives d’une épaisseur de 0,01 à 0,1 mm. La qualité des lames de refendage, l’angle de la lame et la tension du film sont les principaux facteurs affectant le processus de refendage. Après le refendage, les feuilles d’électrodes ne doivent pas présenter de plis ou de perte de poudre. Une grande précision est requise pour les dimensions de refendage et les bavures sur les bords des feuilles d’électrodes doivent être minimales. Sinon, les dendrites peuvent pénétrer dans le séparateur en raison des bavures, provoquant un court-circuit à l’intérieur de la batterie.
01 Indicateurs de l’équipement de refendage
Un dispositif de refendage, également connu sous le nom de découpeuse ou de découpeuse longitudinale, fait référence à un équipement de production qui coupe les électrodes de batterie lithium-ion, les feuilles d’électrode de batterie de batterie polymère, les feuilles d’électrode de batterie nickel-hydrure métallique, ainsi que les tôles ou bobines métalliques colorées, dans les spécifications de taille requises tout en maintenant une tension constante et en répondant à certaines exigences de processus. Le refendage des électrodes de batterie nécessite une grande précision dimensionnelle, et les bords des électrodes doivent présenter des bavures minimales. Sinon, les dendrites peuvent pénétrer dans le séparateur, provoquant un court-circuit à l’intérieur de la batterie. Les indicateurs de performance du dispositif de refendage comprennent principalement la précision de refendage, la précision de l’équipement de refendage et la gamme de réglages de la lame et de la matrice.
- Refendage exactitude
Après la refendage, les meules longitudinales de l’électrode doivent être de ≤7 μm et les meules transversales doivent être de ≤12 μm. Il ne doit pas y avoir de délamination ou de plis sur les bords coupés de l’électrode. Les dimensions géométriques doivent répondre aux exigences de tolérance linéaire des processus de fabrication des batteries. Il s’agit principalement de la tolérance de taille et du faux-rond de l’arbre du couteau et des lames de refendage, ainsi que de leur coaxialité.
- Précision de refendage et d’installation
La précision des rouleaux fous et du module de lame lors des essais à vide après le montage et le débogage de l’équipement de refendage se réfère principalement aux critères suivants :
Rugosité de surface du rouleau tendeur : Ra ≤ 0,4.
Cylindricité du galet tendeur : ≤ 0,03 mm.
Faux-rond total du galet tendeur après l’installation : ≤ 0,05 mm.
Faux-rond de l’ensemble du module de lame : ≤ 10μm.
- Plage de réglage de la lame
La plage de distance réglable entre les lames supérieure et inférieure de l’équipement de refendage au niveau de la section du matériau de coupe.
02 La composition et la structure clé de la machine à refendre
2.1 Composition de la machine à refendre
L’équipement de refendage se compose principalement d’un dispositif de déroulement, d’un contrôle de tension de déroulement, d’un contrôle d’alignement des bords de déroulement, d’un guidage de bande, d’un système de détection de défauts d’apparence CCD, d’un refendage, d’un système de détection de largeur post-refendage, d’un dépoussiérage, d’une détection de tension de rembobinage, d’un dispositif d’étiquetage, d’un dispositif de rembobinage et d’un système électrique.
La configuration standard d’un équipement de refendage de batterie au lithium entièrement automatique est montée verticalement sur le châssis. Il utilise un arbre différentiel à double glissement avec la même méthode d’enroulement central pour les rouleaux supérieur et inférieur. Le serrage du rembobinage et du déroulement, ainsi que les actions du module de lame et des rouleaux de pression, sont tous contrôlés pneumatiquement, ce qui rend l’opération simple et rapide. Il est entraîné par un seul moteur avec convertisseur de fréquence et transmission synchrone par courroie, assurant un fonctionnement fluide et fiable avec un faible bruit. Le déroulement est contrôlé par un frein à embrayage à poudre magnétique, qui offre une précision de contrôle de tension élevée, une réponse rapide et une large plage de réglage. La composition de l’équipement de refendage est indiquée ci-dessous.
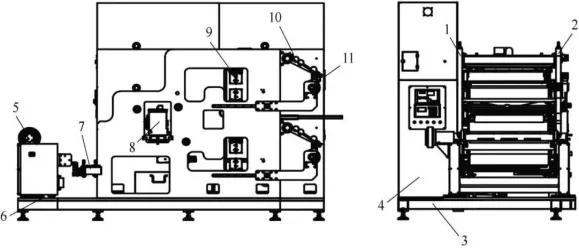
1 – Panneau mural arrière ;2 – Panneau mural avant ;3 – Base ;4 – Armoire électrique ;5 – Dispositif de déroulement ;6 – Dispositif d’alignement des bords ;7 – Plate-forme de guidage de la bande ;8 – Lame de refendage ;9 – Dispositif de brossage de poudre ;10 – Dispositif de bobinage à rouleau de pression ;11 – Dispositif d’arbre différentiel à glissement de rembobinage
- –Corps de la machine: Fabriqué en acier de construction au carbone de haute qualité, il est utilisé pour soutenir le cadre et l’armoire électrique de l’équipement de refendage. Les panneaux muraux avant et arrière sont reliés par des poutres de liaison et fixés verticalement sur la base.
- –Dispositif de déroulement: Le déroulement se fait à l’aide d’une méthode d’arbre d’expansion d’air. En connectant un frein à poudre magnétique à l’extrémité de l’arbre d’expansion de l’air de déroulement, une résistance contrôlable opposée à la direction de traction est appliquée pour obtenir une tension de déroulement.
- – Dispositif d’alignement des bords: Il adopte une seule sonde inductive de détection des bords pour l’alignement des bords. Un système d’alignement des bords de haute précision est utilisé avec une précision d’alignement de ±0,1 mm et une course d’alignement de ≥120 mm. Le mécanisme de réglage de la position du capteur est réglé à l’aide d’une vis et est équipé d’une échelle d’affichage numérique et d’un mécanisme de verrouillage de type poignée.
- Plate-forme d’alimentation à courroie :La largeur de l’espace de la plate-forme d’alimentation de la courroie est de 1 mm, avec une profondeur supérieure à 10 mm. La tige de pression pneumatique presse la plaque de contact. Une plaque d’acier noir de 5,0 mm est ajoutée à la plate-forme d’alimentation par courroie, ainsi qu’une règle à l’échelle. Le point de référence « 0 » sur l’échelle correspond à la largeur du manchon d’écart entre le point de référence de la matrice de découpe. Le processus d’assemblage des matériaux se fait manuellement. Il est nécessaire de s’assurer que la distance entre la plate-forme d’alimentation de la courroie et la barre de pression est de 10 mm lorsque la plaque de contact alimente correctement la courroie. Des mesures de sécurité supplémentaires sont mises en œuvre. Si la tige de pression est en position basse lors du démarrage de la machine, une alarme et une fonction d’invite doivent être activées et l’alarme doit être effacée avant que la machine puisse être démarrée.
- –Refendage Mourir:Le jeu entre la lame supérieure et la lame inférieure est commodément fixé. La matrice de coupe adopte un entraînement à axe unique. Les deux arbres principaux sont en matériau 40Cr, et la plaque de base et le support sont en acier S136. La surface est durcie avec une dureté de HRC50 ou plus. L’aspect général de la matrice de découpe doit être exempt de taches de rouille. L’indication de l’échelle sur le rouleau de réglage pour l’entrée de la matrice de découpe est requise. Le diamètre du rouleau d’alimentation est de φ50mm. Lorsque le point le plus bas du rouleau est à la même position horizontale que le point le plus haut de la lame inférieure, l’indication de l’échelle est nulle. Le réglage vers le haut est indiqué comme positif et le réglage vers le bas est indiqué comme négatif. L’échelle sur le rouleau de réglage de la matrice de découpe doit être réalisée avec une plage de ±5 mm. Le rouleau de réglage est en alliage d’aluminium et la surface est traitée avec une anodisation brune, avec une dureté non inférieure à HRB300. Les deux supports d’extrémité adoptent une structure à vis et peuvent être réglés de haut en bas. L’indication de l’échelle est zéro. Le réglage du rouleau de dérivation par rapport à la position zéro est indiqué par des angles positifs et négatifs, avec une plage de réglage de ±3°.
- – Appareil de brossage des poudres :L’appareil utilise un rouleau-brosse amovible avec une installation de type pince. Le trou de l’arbre est fixe et l’entraînement est réalisé par un mécanisme à goupille, ce qui facilite le montage et le démontage. Les poils du rouleau brosse sont en nylon souple pour éviter d’endommager la plaque de contact en raison d’une dureté excessive. Le rouleau brosse adopte un placement des poils de type enroulement, assurant une densité de poils élevée pour un dépoussiérage efficace. La brosse tourne dans le sens opposé au mouvement de la plaque de contact pour améliorer l’effet de dépoussiérage. Pendant le fonctionnement, les brosses gauche et droite du dispositif de dépoussiérage sont encastrées l’une dans l’autre pour assurer un contact efficace entre les poils et la plaque de contact, en appliquant une certaine pression tout en maintenant une élasticité suffisante pour assurer l’efficacité du dépoussiérage. La profondeur à laquelle les deux brosses sont encastrées l’une dans l’autre est de 2 à 3 mm (contrôlée en ajustant l’épaisseur du matériau d’étanchéité sur le bord de la boîte de dépoussiérage). La distance centrale entre les deux pinceaux doit être indiquée par une échelle. La brosse peut être ajustée de haut en bas de 50 mm pour faciliter l’enfilage, et il y a une position de réglage précise à 10 mm, ce qui est bénéfique pour ajuster l’effet de dépoussiérage. La vitesse de rotation de la brosse est réglable de 0 à 300r/min.
- – Dispositif de bobinage à rouleau de pression :Il existe un ensemble d’arbres de rembobinage supérieur et inférieur avec des mécanismes de rouleaux de pression. La surface des rouleaux de pression est chromée ou traitée avec un revêtement en céramique pour éviter le retournement des bords après la refendage.
- – Dispositif d’arbre différentiel à glissement de rembobinage :Il y a deux arbres de différentiel à glissement de rembobinage supérieur et inférieur, qui facilitent l’enroulement avec la vitesse différentielle. Il est équipé de plaques de couche intermédiaire et permet un réglage quantitatif de la tension multipliée par le nombre de bandes. Il ajuste automatiquement la base de tension en fonction des différentes largeurs de refendage et peut régler la base de tension par lui-même pour assurer une tension constante et stable, évitant ainsi la rupture de la courroie lors de la découpe continue.
2.2 Structures clés de la machine à refendre
Les composants clés de l’équipement de refendage comprennent le mécanisme de contrôle de tension constante pour le déroulement et le rembobinage, le mécanisme d’arbre différentiel à glissement et le mécanisme d’alignement des bords.
- Structure de contrôle de tension constante
(1) Principe de contrôle de tension constante.Le principe du contrôle constant de la tension est essentiel pour les processus de déroulement et de rembobinage dans les opérations de refendage. Au fur et à mesure que le diamètre de déroulement diminue et que le diamètre de rembobinage augmente, la tension change continuellement en raison du contrôle constant de la vitesse du moteur. Cette variation de tension peut entraîner des plis ou des ruptures de matériau si la tension est trop faible ou trop élevée, respectivement. Pour éviter ces problèmes, il est nécessaire de maintenir une tension constante pendant le processus de déroulement et de rembobinage.
L’essence du contrôle de tension constante est d’ajuster le couple de sortie du moteur en fonction de l’évolution du diamètre tout en maintenant la tension inchangée. Le contrôle du couple du moteur est réalisé par un convertisseur de fréquence et un moteur asynchrone triphasé. Le convertisseur de fréquence de la série Delta V fournit trois ports d’entrée analogiques : AUI, AVI et ACI. Ces ports peuvent être définis pour diverses fonctions, l’un servant de référence de couple et l’autre de limitation de vitesse.
Une plage de tension de 0 à 10 V correspond à une plage de sortie de 0 au couple nominal du moteur. En ajustant la tension dans la plage 0-10V, le contrôle de tension constante peut être obtenu.
- Calcul de la tension et du couple.D’après l’analyse cinétique de la figure ci-dessous :
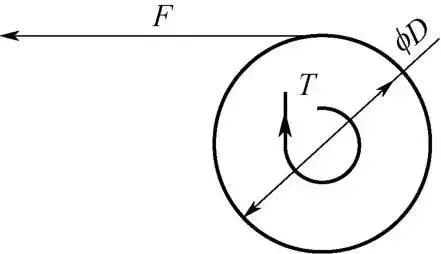
FD/2=Ti
Dans l’équation, F représente la tension, D représente le diamètre, T représente le couple du moteur et i représente le rapport de réduction de vitesse.
L’expression du couple nominal du moteur est la suivante :
T = 9550P/n
Dans l’équation, T représente le couple nominal du moteur en Newton-mètres (N·m),
P représente la puissance nominale du moteur en kilowatts (kW) et n représente la vitesse nominale du moteur en tours par minute (r/min).
(3) Calcul de la vitesse synchrone du moteur :
Le calcul de la vitesse synchrone du moteur est le suivant :
n = 60f/p = 60 × 2/2 = 60 r/min
Dans l’équation, f représente la fréquence d’alimentation en Hertz (Hz), n représente la vitesse du moteur de rembobinage en tours par minute (r/min) et p représente le nombre de paires de pôles du moteur.
(4) Vitesse opération.Lors de l’utilisation du contrôle de tension dans le système, il est nécessaire de limiter la vitesse de la machine à refendre pour éviter l’emballement. L’expression de la vitesse de fonctionnement V du rembobinage est la suivante :
V = πDn/i
Dans l’équation,V représente la vitesse de fonctionnement de la machine à refendre en mètres par minute (m/min),D représente le diamètre maximal du rembobinage en mètres (m),n représente la vitesse en tours par minute (r/min), et
(5)UnContrôleur de tension Utomatic.Le régulateur de tension automatique se compose principalement d’un capteur de tension, de convertisseurs A/N et N/A de haute précision, d’un microcontrôleur haute performance et d’autres composants. Ce régulateur automatique de tension constante fonctionne en comparant la tension mesurée du matériau de la bande à partir du capteur de tension avec la consigne de tension cible. Il utilise ensuite les calculs PID effectués par le microcontrôleur pour ajuster automatiquement la sortie N/A, modifiant ainsi le courant d’excitation de l’embrayage/frein à poudre magnétique ou le couple d’un servomoteur. Cela garantit une tension constante dans le matériau de la bande. Le régulateur de tension automatique peut être largement utilisé dans diverses applications qui nécessitent une mesure et un contrôle précis de la tension. Il offre une flexibilité de fonctionnement et dispose d’un large éventail d’applications. Il permet de basculer sans problème entre les modes automatique et manuel, ce qui permet aux opérateurs de passer d’un mode à l’autre en fonction de leurs besoins spécifiques.
(6) Rembobinage de la tension conique. Dans le processus de refendage et de rembobinage du film polarisant, la méthode de contrôle courante consiste à adopter un enroulement à tension constante. Cela signifie que la dérouleuse maintient une tension constante tout au long du processus, y compris le début du bobinage, le bobinage continu et la fin du bobinage. Cependant, lors de l’enroulement du matériau sur un noyau ou un mandrin, il y a une force réactive notable exercée par le noyau. Si un enroulement à tension constante est appliqué, il peut facilement entraîner le phénomène de dépassement du film au centre du rouleau, et cela peut même endommager l’équipement. Pour résoudre ce problème, un schéma de contrôle de la tension conique peut être utilisé. Cette approche atténue considérablement le problème susmentionné. La courbe de tension effilée, comme le montre la figure ci-dessous, ressemble à un cône avec un sommet pointu. Il crée une tension plus élevée au centre du rouleau et diminue progressivement la tension vers les couches extérieures à mesure que le diamètre du rouleau de matériau augmente. En contrôlant la tension, il est possible d’obtenir un enroulement du matériau « plus serré à l’intérieur, plus lâche à l’extérieur », répondant ainsi aux exigences du processus d’enroulement du matériau.
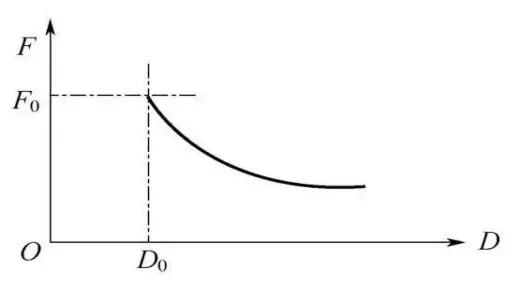
La formule de conicité de tension est exprimée comme suit :
F = F0 × [1 – K(1 – D0/D)]
Dans l’équation, F représente la tension de sortie réelle en Newtons (N), F0 représente la tension réglée en Newtons (N), K représente le coefficient de dénomination de la tension, D0 représente le diamètre minimum en mètres (m) et D représente le diamètre du courant en mètres (m).
2)UneCorrection de lignment
(1) Le phénomène de « déviation ».Au cours du processus de refendage et de rembobinage du film polarisant, divers facteurs tels qu’un revêtement inégal, une tension longitudinale inégale, des bords irréguliers du film, un désalignement entre les rouleaux de transport et un frottement excessif entre le film conique et la surface du rouleau peuvent entraîner une « déviation » du film pendant le transport. Pour éviter ce phénomène de déviation, une correction d’alignement des bords est installée sur l’équipement de refendage et de rembobinage.
(2)Méthodes de correction.Selon la position d’installation de l’équipement de correction, il peut être divisé en deux types : la correction bilatérale et la correction unilatérale.
DCorrection des bords UAL En particulier, pour polariser des films avec des bords inégaux, un désalignement ou une forme de tour, ou lorsqu’il est difficile d’aligner le film avec l’axe de la machine pendant le déroulement, les dispositifs de correction à double bord sont couramment utilisés sur les machines de déroulement. Il existe généralement deux formes de correction à double tranchant.
L’une d’entre elles est le système de tête à double détection, également connu sous le nom de contrôle de la position centrale (CPC), comme le montre la figure ci-dessous. Deux ensembles de têtes de détection sont positionnés symétriquement le long de l’axe de la machine. Ils sont entraînés par un moteur pas à pas à travers une vis-mère bidirectionnelle, permettant un mouvement synchrone vers l’intérieur ou vers l’extérieur. Lorsque le film entre dans la machine, les têtes de détection se déplacent vers l’intérieur. Si une seule des têtes détecte le bord du film, cela indique que le film a dévié dans cette direction, et un signal est envoyé pour déplacer la machine de déroulement et ajuster la position du film jusqu’à ce que les deux têtes de détection détectent les bords du film et émettent des signaux égaux. À ce stade, les têtes de détection et la machine de déroulement s’arrêtent de bouger et le film est en position centrale. L’avantage de cette méthode est qu’elle centre automatiquement le film pendant le processus de déroulement, sans qu’il soit nécessaire de tenir compte de la largeur du matériau.
L’autre méthode est le contrôle de la position des bords (EPC), qui contrôle la position des bords du film en les détectant. Le cadre de la tête de détection est monté du côté de la transmission de la machine. Les positions des têtes de détection sont préréglées en fonction de la largeur du matériau entrant. Lorsque le film de déroulement entre dans la machine, les têtes de détection envoient des signaux en fonction de l’étendue de la couverture (entièrement couverte, entièrement exposée ou partiellement couverte) par le film. La dérouleuse se déplace pour s’assurer qu’un côté du bord du film reste partiellement couvert par la tête de détection. L’avantage de cette méthode est qu’elle ne nécessite qu’une seule tête de détection, ce qui rend l’appareil relativement plus simple. Cependant, la position d’origine de la tête de détection doit être ajustée à l’avance en fonction des différentes largeurs du matériau avant l’utilisation.
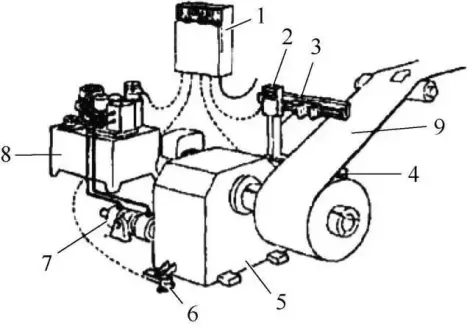
1—Armoire de commande ;2—Détecteur de contrôle de position ;3—Châssis en forme de C ;4—Source lumineuse émettrice ;5—Dérouleuse ;6—Détecteur de position centrale ;7—Vérin hydraulique en mouvement ;8—Station hydraulique/servovanne ;9—Film polarisant
Correction unilatérale:Pour les films polarisants avec des bords relativement réguliers, la correction à un seul bord est couramment utilisée. Les films à bords lisses sont moins susceptibles d’être endommagés pendant le transport et la manipulation. Pour obtenir un enroulement uniforme, un seul ensemble de têtes de détection est utilisé pour détecter les bords du film. Le détecteur de contrôle de position peut être monté sur un bras s’étendant de la dérouleuse, et il se déplace avec la machine de rembobinage. Alternativement, un support de tête séparé peut être installé près du rouleau de déviation de sortie de la machine. Un ensemble de vis-mères entraînées par un moteur pas à pas déplace la tête de détection ou l’ensemble du support de tête, qui comprend un capteur de position. Le processus de fonctionnement de ces deux méthodes est le suivant : lorsque le film est chargé sur le noyau d’enroulement et serré, la tête de détection se déplace jusqu’à ce qu’elle détecte que le bord du film recouvre partiellement la source lumineuse. Dans le même temps, le système de commande en boucle fermée est automatiquement engagé. Lorsque la position du bord du film change, la tête de détection continue de suivre et saisit la valeur de décalage dans le système de contrôle. Cela fait que le vérin hydraulique de correction des bords de la dérouleuse se déplace dans la même direction et à la même distance, ce qui permet d’obtenir un résultat de rembobinage uniforme.
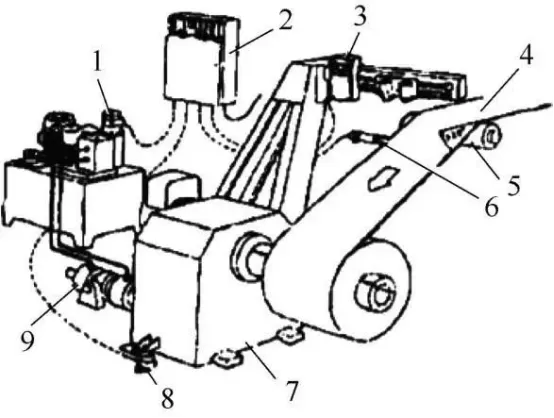
1—Station hydraulique/servovanne ;2—Armoire de commande ;3—Détecteur de contrôle de position ;4—Film polarisant ;5—Rouleau de déviation ;6—Source lumineuse émettrice ;7—Machine de rembobinage ;8—Détecteur de position centrale ;9—Cylindre hydraulique en mouvement
- Structure de refendage d’arbre coulissant
(1) Principe de fonctionnement.L’arbre de glissement est basé sur le principe du glissement de diverses bagues collectrices sur l’arbre pour maintenir l’équilibre de tension entre plusieurs rouleaux de matériau sur l’arbre, facilitant le processus de refendage et de rembobinage. L’objectif principal de l’arbre de glissement est d’ajuster la tension du matériau pendant le processus de rembobinage. En maintenant une tension appropriée sur tous les rouleaux pendant le fonctionnement de l’arbre, l’arbre coulissant améliore considérablement le rendement et réduit les coûts de production, en particulier dans l’application d’un film polarisant de batterie. C’est un composant important de la machine à refendre les batteries au lithium (refendeuse).
(2)Structure principale.L’arbre de glissement a une structure spéciale composée de plusieurs bagues collectrices. Pendant le fonctionnement, les bagues collectrices sont commandées pour glisser avec une certaine valeur de couple, compensant avec précision la différence de vitesse générée. Cela permet un contrôle précis de la tension de chaque rouleau de matériau, assurant un enroulement à tension constante et garantissant la qualité de l’enroulement. Il peut être appliqué dans une large gamme de tensions, de niveaux très faibles à élevés. L’arbre de glissement convient aux applications qui nécessitent des vitesses élevées, de grandes variations d’épaisseur de matériau, un contrôle de tension à plusieurs étages, un contrôle de tension de haute précision et un enroulement net de la face d’extrémité. Il est particulièrement bien adapté à une utilisation dans les machines de refendage à bobinage central à deux axes.
(3)Produits représentatifs.Les arbres de glissement Tōshin et Nishimura du Japon sont connus pour leur grande précision de contrôle, bien qu’ils aient un coût relativement plus élevé. L’unité principale de l’arbre de glissement est l’unité d’expansion pneumatique, qui se compose d’une chambre, d’une plaque inférieure inclinée, d’un piston, d’un joint d’air, de roulements, de ressorts et de plaques d’expansion. Chaque unité a une longueur de 40 mm, et les 18 unités peuvent être interchangées et remplacées indépendamment à n’importe quelle position, améliorant ainsi la durée de vie et la facilité d’entretien.
(4) Technologie matérielle.Le corps principal du produit est en acier moulé trempé et revenu ou en alliage d’aluminium avec revêtement anodisé dur. Les plaques d’expansion en caoutchouc sont fabriquées en polyuréthane résistant aux hautes températures et à l’usure et sont vulcanisées en conséquence, en fonction des exigences de tension maximales. Différentes tailles d’arbres coulissants peuvent être personnalisées en fonction d’exigences spécifiques, y compris des composants tels que l’arbre principal, l’unité d’expansion pneumatique, les plaques d’expansion, les ressorts et les joints universels.
(5)Mode d’emploi.L’arbre de glissement améliore considérablement la vitesse, la précision de rembobinage, le niveau d’automatisation, réduit le temps de configuration et améliore la facilité d’utilisation de la machine à refendre. L’application d’arbres de glissement dans le rembobinage améliore considérablement le rendement des produits de qualité et réduit les coûts de production. Notre arbre coulissant assure la plus haute qualité des rouleaux de matériau en maintenant une tension appropriée sur tous les rouleaux pendant le fonctionnement.
2.3 Quelle est la différence entre le refendage de feuilles d’électrodes et d’autres refendages de plaques métalliques ordinaires ?
Par rapport au processus de découpe des matériaux en tôle, la méthode de découpe des disques d’électrode de batterie au lithium présente des caractéristiques complètement différentes :
Lors de la coupe du disque d’électrode, les lames circulaires supérieure et inférieure ont un angle de coupe négatif, similaire aux lames des ciseaux, avec une très petite largeur de bord. Il n’y a pas d’espace horizontal entre les lames circulaires supérieure et inférieure (le paramètre c sur le schéma équivaut à une valeur négative), mais les lames supérieure et inférieure entrent en contact les unes avec les autres et exercent une pression latérale.
Dans la découpe de matériaux en feuille, il y a des rouleaux de support en caoutchouc au-dessus et en dessous, qui équilibrent la force de cisaillement et le couple de cisaillement générés pendant la coupe, évitant ainsi une déformation significative du matériau en feuille. Cependant, dans la coupe des disques d’électrodes, il n’y a pas de rouleaux de support supérieurs et inférieurs.
Le revêtement du disque d’électrode est un matériau composite composé de particules et a une faible capacité de déformation plastique. Lorsque la contrainte interne générée par les lames circulaires supérieure et inférieure dépasse la force de cohésion entre les particules de revêtement, des fissures se forment dans le revêtement et se propagent, conduisant à la séparation.
2.4 Quels sont les points clés du refendage ?
1. Influence des propriétés physiques et mécaniques des matériaux
En général, les matériaux ayant une bonne plasticité ont tendance à retarder l’apparition des fissures pendant le cisaillement, ce qui se traduit par une plus grande profondeur de matériau cisaillé et une plus grande proportion de zone de cisaillement brillante. D’autre part, les matériaux à faible plasticité sont plus sujets à la rupture dans les mêmes conditions de paramètres, ce qui entraîne une proportion plus élevée de zone de déchirure dans la surface de rupture et une zone de cisaillement brillante naturellement plus petite.
- L’influence des paires supérieure et inférieure sur la pression latérale de l’outil
Dans le processus de coupe des disques d’électrodes, la pression latérale exercée par l’outil est l’un des facteurs clés affectant la qualité de la coupe. Pendant le cisaillement, l’alignement des fissures supérieures et inférieures sur la surface de rupture et l’état de contrainte-déformation de la force de cisaillement sont étroitement liés à l’amplitude de la pression latérale. Si la pression latérale est trop faible, des défauts tels que des surfaces de coupe inégales et une perte de matériau peuvent survenir lors de la coupe des disques d’électrodes. À l’inverse, si la pression est trop élevée, l’outil est plus sujet à l’usure, ce qui entraîne une durée de vie plus courte.
- L’influence de la quantité de chevauchement des outils appariés supérieur et inférieur (paramètre δ dans la figure ci-dessus)
Le réglage de la quantité de chevauchement est principalement lié à l’épaisseur du disque d’électrode. Une quantité raisonnable de chevauchement est bénéfique pour l’engagement de l’outil et a un impact sur la qualité de la coupe, la taille des bavures et le taux d’usure du bord de l’outil.
- Influence de l’angle d’occlusion (paramètre α dans la figure ci-dessus)
Dans la découpe de disques, l’angle d’occlusion fait référence à l’angle entre le segment de coupe et l’axe de la tôle à couper. Au fur et à mesure que l’angle de morsure augmente, la composante horizontale de la force de coupe augmente également. Si la force horizontale dépasse la tension d’avance du disque d’électrode, le matériau en feuille peut glisser ou s’arquer devant la lame circulaire, ce qui rend impossible l’exécution de la coupe. D’autre part, la réduction de l’angle de morsure nécessite une augmentation du diamètre de la lame, ce qui nécessite à son tour des dimensions plus grandes pour la machine à refendre. Par conséquent, l’équilibrage de l’angle de morsure, du diamètre de la lame, de l’épaisseur de la feuille et de la quantité de chevauchement doit être déterminé en fonction des conditions de travail réelles.
2.5 Défauts
Les principaux défauts de la découpe des feuilles d’électrodes sont les suivants :
- Bardane
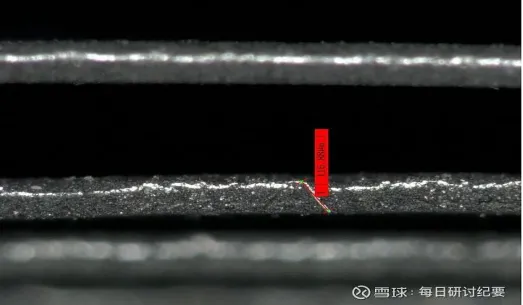
Les bavures, en particulier les bavures métalliques, présentent un risque important pour les batteries au lithium. Les plus grosses bavures métalliques peuvent pénétrer directement dans le séparateur, provoquant un court-circuit entre les électrodes positive et négative. Le processus de refendage des disques d’électrodes est la principale source de génération de bavures dans la fabrication de batteries lithium-ion. L’image ci-dessus montre la morphologie typique des bavures métalliques générées lors de la coupe des disques d’électrodes. En raison d’un contrôle instable de la tension pendant le refendage, un refendage secondaire se produit, ce qui entraîne des bavures de feuille d’aluminium de dimensions supérieures à 100 μm. Pour éviter cette situation, il est crucial de trouver la pression latérale et le chevauchement d’outil les plus appropriés en fonction des propriétés et de l’épaisseur du disque d’électrode lors du réglage de l’outil. De plus, le chanfreinage de la lame et le réglage de la tension de la bobine peuvent aider à améliorer la qualité du tranchant du disque d’électrode.
2. Bord ondulé
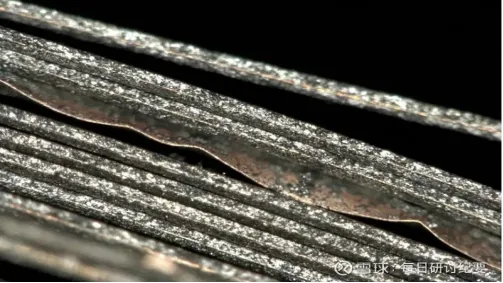
Lors de la refendage des disques d’électrodes, un chevauchement et une pression inappropriés des outils peuvent entraîner des bords ondulés et un délaminage du revêtement à la coupe. Lorsque des bords ondulés se produisent, il peut y avoir une déviation des bords et des vibrations lors de la refendage et de l’enroulement des disques d’électrodes, ce qui entraîne une diminution de la précision du processus. De plus, cela peut avoir un impact négatif sur l’épaisseur finale et l’apparence de la batterie.
03 Sélection et cas d’application de la machine à refendre
(1) Sélection de l’équipement :
Le choix d’une machine à refendre doit tenir compte de facteurs tels que la précision de coupe, la précision de l’équipement de refendage et la plage de réglage de la lame.
(2) Cas d’application :
Si l’on prend l’exemple de la machine à refendre ZY750-C600-C50 de Chaoyang Machinery Manufacturing Co., Ltd., il s’agit d’un équipement de refendage entièrement automatique par batterie au lithium de type C avec une largeur d’entrée maximale de 750 mm, un diamètre de rembobinage et de déroulement de φ600 mm, une largeur de refendage minimale de 30 mm et une vitesse de fonctionnement de 50 m/min. L’équipement est équipé d’un système de détection CCD pour détecter les problèmes tels que les dommages et les plis sur le disque d’électrode.
04 Utilisation et entretien de la machine à refendre
(1) Utilisation de la machine à refendre :
En prenant l’exemple de la machine à refendre le modèle 65 d’une certaine entreprise, l’utilisation de la machine à refendre est décrite. La figure ci-dessous montre l’interface principale du système. En cliquant sur « Entrer dans le système », vous pouvez accéder au système. L’interface des boutons de fonctionnement est illustrée dans la figure ci-dessous, et les explications de chaque bouton fonctionnel sont les suivantes.
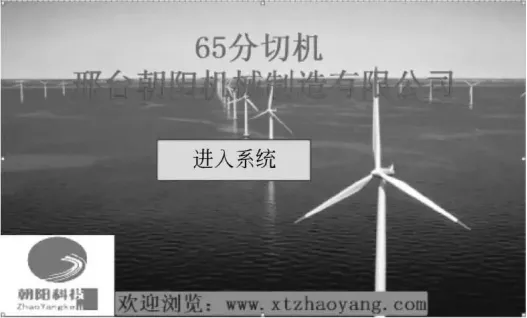
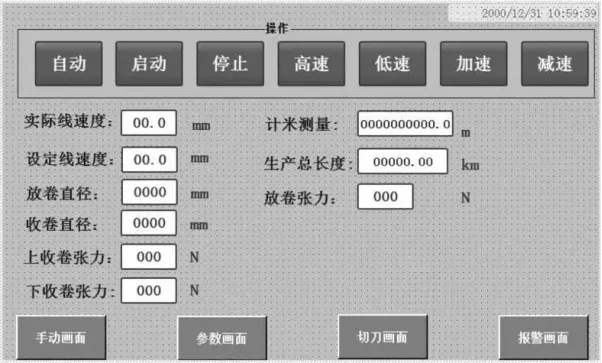
Mesure de la longueur : La longueur produite en mode de fonctionnement automatique peut être remise à zéro.
Longueur totale de production : La longueur accumulée en mode de fonctionnement automatique, qui ne peut pas être remise à zéro.
Régler la vitesse de ligne : La vitesse de fonctionnement actuelle définie par l’utilisateur via l’IHM (ou contrôleur de vitesse).
Vitesse de ligne réelle : vitesse en temps réel à laquelle la machine fonctionne actuellement.
Augmentation de la vitesse (+) : En appuyant sur ce bouton, la vitesse actuelle augmente de 1 m/min (la valeur d’incrément peut être réglée).
Diminution de la vitesse (-) : En appuyant sur ce bouton, la vitesse actuelle diminue de 1 m/min (la valeur de décrémentation peut être réglée).
Tension de déroulement : tension en temps réel détectée par le capteur de tension de déroulement.
Diamètre de rembobinage : Le diamètre en temps réel du matériau rembobiné.
Tension de rembobinage supérieur : tension en temps réel du rembobinage supérieur.
Tension de rembobinage inférieure : tension en temps réel du rembobinage inférieur.
Écran des paramètres : Accès à l’écran des paramètres pour définir des paramètres tels que la vitesse de traction, la tension de déroulement, la tension de rembobinage, le couple de traction, etc.
Écran de coupe : Accès à l’écran de coupe pour régler la longueur d’utilisation de la coupe, réinitialiser diverses valeurs de longueur et déterminer s’il faut activer la coupe.
Manuel : Accès à l’écran d’opération de débogage manuel pour contrôler manuellement des fonctions telles que le déroulement, le rembobinage, le brossage et l’arrêt/démarrage de la lame.
Auto : sélection du mode automatique.
Début : Démarrage de toute la ligne (valable en mode automatique).
Stop : Arrêt de toute la ligne (valable en mode automatique).
Haute vitesse : Faire fonctionner la machine à grande vitesse.
Basse vitesse : Faire fonctionner la machine à basse vitesse.
(2) Installation et mise en service de la machine à refendre :
Le fonctionnement de la machine à refendre comprend trois étapes : le réglage de la tension, le réglage de la correction de l’alignement de l’EPC et la mise en service de la vanne proportionnelle électrique de rembobinage. La mise en service de la vanne proportionnelle électrique est une étape critique, et la procédure est la suivante :
- Connectez l’alimentation 24V en fonction des exigences de câblage.
- Fournir de l’air comprimé à la vanne proportionnelle dans la plage de 0,5 à 0,65 MPa.
- Appuyez sur le bouton « Déverrouiller » ou « Verrouiller » et maintenez-le enfoncé pendant plus de 3 secondes jusqu’à ce que le voyant clignote.
- Appuyez par intermittence sur le bouton SET pour afficher GL.9/F01/F02 (F01 = limite inférieure, F02 = limite supérieure).
- Lorsque F01 s’affiche avec un nombre clignotant, appuyez sur le bouton de diminution ou d’augmentation pour diminuer ou augmenter le nombre. En général, F01 = 0,15-0,25.
- Lorsque F02 s’affiche avec un nombre clignotant, appuyez sur le bouton de diminution ou d’augmentation pour diminuer ou augmenter le nombre. En général, F02 = 0,45-0,50.
- Appuyez sur le bouton SET une fois le processus de débogage terminé.
(3) Précautions et entretien pour l’utilisation d’une machine à refendre :
1) Les opérateurs doivent recevoir une formation avant de commencer à travailler et être familiers avec le fonctionnement de la machine à refendre, les performances de l’équipement et les méthodes d’entretien générales. Le personnel qui n’est pas formé pour ce travail ne doit pas utiliser la machine.
2) Prenez les mesures de protection du travail nécessaires avant de démarrer la machine. Préparez les outils et le matériel auxiliaires (tels que les outils de réglage des couteaux, les cartons nécessaires, les tubes en papier, les couteaux de coupe, le ruban adhésif, etc.) et placez-les dans une position appropriée sur la machine.
3) Assurez-vous que l’équipement est dans un état sûr. Allumez l’interrupteur électrique, vérifiez qu’il n’y a pas de phases manquantes dans le circuit et assurez-vous que le circuit d’air n’est pas obstrué. Faites fonctionner la machine dans un essai et vérifiez si les équipements électriques, pneumatiques et mécaniques fonctionnent correctement.
4)Vérifiez si les dispositifs de sécurité mécaniques sont en place. Pendant le fonctionnement, évitez de vous écraser, de vous rayer ou de vous coincer dans les engrenages, les chaînes et les rouleaux en rotation.
5) Réglage du couteau : ajustez la distance du couteau avec précision en fonction des exigences du travail et faites attention à la direction de la lame. Si nécessaire, retirez le couteau inférieur et réorganisez-le. Réparez ou remplacez la lame si elle est endommagée ou si elle n’est pas tranchante.
6)Vérifiez la connexion du dispositif d’élimination de l’électricité statique et le fil de mise à la terre de la machine pour vous assurer que l’électricité statique est éliminée pendant le fonctionnement. Placez les vieux papiers sous la machine pour éviter l’accumulation de poussière.
7) Faites attention à la sécurité lors de l’alimentation des matériaux. Poussez le matériau dans la position appropriée pour le gonflage et faites attention au sens de rotation du matériau. Ne chargez pas le matériau en sens inverse.
8) Filetage du matériau et alignement des bords : Enfilez le matériau du déroulement au rembobinage selon la direction définie par l’équipement, ajustez l’alignement des bords et assurez-vous que les deux côtés du produit fini ont de l’adhésif. Faites attention à l’alignement des bords pendant l’alimentation. Il doit être aligné au milieu du trait d’alignement. Si le matériau ne peut pas être coupé jusqu’au bord lorsqu’il dépasse la course, prenez des mesures immédiates pour résoudre le problème.
9) Placez le tube de papier requis sur l’arbre de rembobinage et alignez le matériau. Si du ruban adhésif double face est nécessaire, assurez-vous qu’il est correctement appliqué. Ajustez la tension appropriée pour le rembobinage et le déroulement, et effectuez la coupe et le rembobinage des bords.
10) Pendant le processus de rembobinage, inspectez soigneusement la qualité du produit. Évitez de rouler dans des produits défectueux ou des déchets, de la saleté ou des garnitures de bord. Contrôlez strictement la longueur.
11) Après l’arrêt, coupez l’alimentation électrique et l’alimentation en air, et effectuez le nettoyage et l’entretien nécessaires sur la machine. Évitez d’utiliser un couteau pour gratter le rouleau de transfert. Nettoyez tout adhésif sur l’équipement avec un solvant.
12)En cas de problème pendant le fonctionnement, arrêtez la machine pour le dépannage. S’il n’est pas possible d’arrêter la machine, manipulez la situation avec prudence et réduisez la vitesse si nécessaire.