We all know that battery cells can be mainly categorized into three types: prismatic aluminum shell batteries, cylindrical batteries, and pouch batteries. Each of them has its own characteristics. Currently, prismatic batteries dominate the market for electric vehicle (EV) power batteries, while pouch batteries are primarily used in consumer electronics. Cylindrical batteries serve as a cost-effective option to occupy a share in the market. However, these three types of batteries have their advantages and disadvantages.
Cylindrical cell
Advantages: Cylindrical cells were one of the first mature industrialized lithium battery products. After over two decades of development, the production process of cylindrical lithium batteries has become mature. They have high production efficiency and relatively low costs. As a result, the cost of battery packs utilizing cylindrical cells is relatively low. Cylindrical batteries also have higher production yields compared to prismatic and pouch batteries. They exhibit good consistency and safety performance as well.
Disadvantage:Cylindrical cells, typically enclosed in steel casings, have higher safety levels but tend to be heavier, resulting in lower energy density compared to other types. The cylindrical shape also leads to lower space utilization and radial thermal conductivity issues, affecting temperature distribution. Due to the poor radial thermal performance of cylindrical batteries, the number of winding in a single cell is limited (typically around 20 windings for 18650 cells), resulting in smaller individual capacities. When used in electric vehicles, a large number of individual cells are required to form battery modules and packs, leading to increased connection losses and complexity in battery management system (BMS) management.
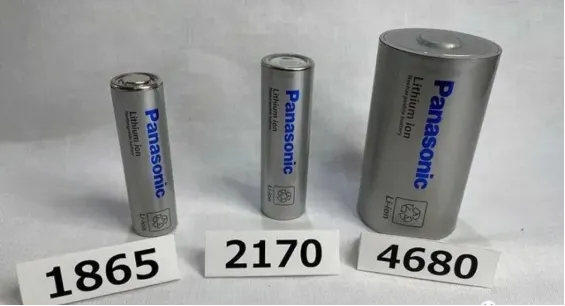
Prismatic cell
Advantages: Prismatic hard-shell batteries are typically made of materials such as aluminum alloy or stainless steel and employ winding or stacking processes internally. They provide better protection for the cell compared to aluminum-plastic film batteries (i.e., pouch batteries), and the safety of the cell has significantly improved compared to cylindrical batteries. However, prismatic hard-shell batteries have higher requirements for cooling system layout.
The adoption rate of prismatic batteries is high in China. With the rise of electric vehicle power batteries in recent years, the contradiction between vehicle range and battery capacity has become increasingly prominent. Domestic power battery manufacturers mostly use high-energy-density prismatic aluminum-shell batteries as the primary choice.
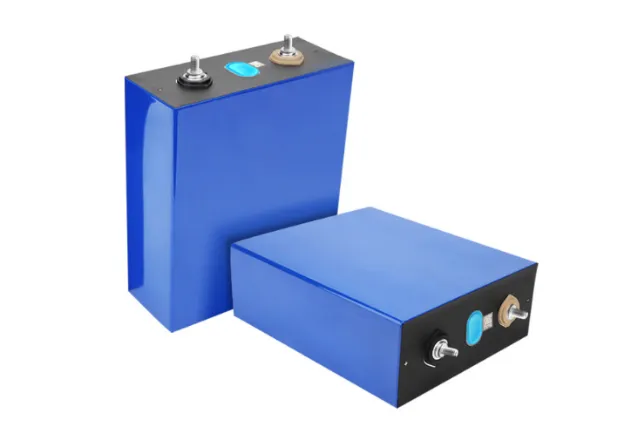
Advantages: The packaging of prismatic cells is mainly made of materials such as aluminum alloy and stainless steel, and the internal structure utilizes winding or stacking processes. This provides better protection for the cell compared to pouch lithium batteries. The safety of the cell is significantly improved compared to cylindrical lithium batteries. The structure of prismatic batteries is relatively simple. Unlike cylindrical batteries that require high-strength stainless steel casings and additional accessories such as explosion-proof safety valves, prismatic batteries have lighter overall accessory weight. They also have relatively higher energy density, which reduces the number of individual cells and lowers the requirements for the Battery Management System (BMS).
Disadvantages: The customization of prismatic battery packs according to product dimensions can lead to a wide variety of different models of prismatic batteries in the market. The abundance of different battery models makes it difficult to standardize the manufacturing process, resulting in lower levels of automation and significant variations in individual cells. This can potentially lead to battery packs composed of prismatic lithium batteries having a much lower lifespan than the individual batteries.
Pouch cell
The materials and processing techniques used in pouch batteries are not significantly different from traditional steel or aluminum shell batteries. The major difference lies in the use of flexible packaging materials, specifically the aluminum-plastic composite film, which is a key and highly challenging material in pouch lithium batteries. The flexible packaging material typically consists of three layers: an outer barrier layer (usually made of nylon BOPA or PET for protection), a barrier layer (aluminum foil in the middle), and an inner layer (a multi-functional high barrier layer).
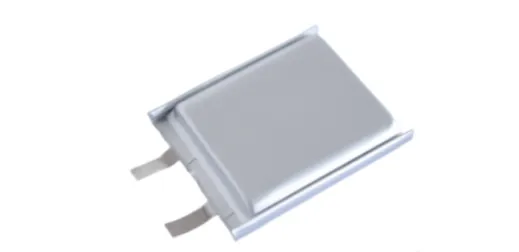
Advantages: Pouch lithium batteries have several advantages:
Pouch batteries have a lower risk of explosion compared to hard-shell batteries. The aluminum-plastic film packaging used in pouch batteries provides better protection and reduces the chances of a catastrophic failure.Pouch batteries offer a higher energy density. They are lighter than equivalent capacity steel-shell lithium batteries by approximately 40% and lighter than aluminum-shell batteries by approximately 20%. This allows for more energy storage in a smaller and lighter form factor.
Disadvantages: Pouch batteries currently need to solve problems such as standardization and high cost, heavy reliance on imports of aluminum-plastic films, and poor consistency.
Overall, cylindrical, prismatic, and pouch batteries each have their own advantages and disadvantages, and each type dominates in specific areas. The optimal packaging method can be determined based on the battery’s material characteristics, application field, and product requirements, taking into account the specific characteristics of each packaging form. Each packaging type has its own technological challenges, and good battery design involves complex issues in areas such as electrochemistry, thermal management, electrical engineering, and mechanical engineering. It places high demands on the overall design of the battery and system.
Safety performance is also a crucial concern for consumers. Regardless of the battery cell type, it is necessary to undergo a series of safety tests, such as external short circuit, overcharging, high and low-temperature exposure, explosion resistance, overdischarging, low-pressure resistance, temperature cycling, vibration, acceleration shock, dropping, compression, puncture, impact resistance, thermal abuse, combustion, and washing, in accordance with testing standards such as GB38031, GB31241, UN38.3, GB/T31485. A battery is considered qualified when it demonstrates resistance to fire, explosion, and leakage.
Taking a comprehensive comparison:
a. Cylindrical: Cylindrical batteries have good standardization, with only three main form factors: 18650, 2170, and 4680. They have a long history and mature manufacturing processes, originating from Sony’s invention in 1992 (the earliest commercial lithium battery). Cylindrical batteries have high automation levels, strong product consistency, and relatively low costs. However, they have limitations in radial heat dissipation, which restricts the number of winding layers and results in lower individual cell capacities. This means that hundreds or thousands of cells are required, along with advanced battery thermal management techniques. Additionally, the packaging efficiency is low during cell grouping, and the steel casing adds weight, resulting in a relatively lower energy density when grouped.
b. Prismatic: Prismatic batteries have a simpler manufacturing process and provide protection for the cells. They have less difficulty when grouped and offer higher energy density compared to cylindrical batteries. However, prismatic batteries lack standardization, with a wide range of models and challenges in achieving process uniformity. While prismatic batteries were traditionally manufactured using winding techniques, newer approaches such as stacked pouch cells are also being utilized.
c. Pouch: Pouch batteries offer a thin and flexible form factor, enabling higher energy density. However, they have lower mechanical strength and require more demanding manufacturing processes. They also have higher requirements for cell grouping.
The packaging form can also be divided into winding and lamination from another dimension. Among them: cylindrical cells can only be rolled, pouch packages can only be laminated, and prismatic cells can be both rolled and laminated. Comparing these three packages, it can be said that they are only half as good as each other, and they all fall into the category of usability and ease of use. Once a car company decides which package to use, it will not change it easily unless there is a drastic change in the packaging process pattern. Which packaging technology will develop well in the future mainly depends on which car company develops well.
For example, Tesla and Panasonic’s cylindrical batteries: Tesla has been using cylindrical batteries and continues to do so. Panasonic, closely associated with Tesla, has also focused on cylindrical batteries. In 2017, Panasonic held the world’s largest market share with 9.9 GWh of installed capacity, accounting for 16.7%.
Chinese new energy vehicles and prismatic batteries: China has a significant volume of new energy commercial vehicles (mainly used in urban buses), and they have shown a preference for prismatic batteries. Consequently, battery suppliers prioritize the production of prismatic batteries, which are then adopted by passenger vehicle manufacturers. Additionally, Germany also favors prismatic batteries. As a result, the majority of batteries used in China are currently prismatic, given the strong development of China’s new energy vehicle industry, making prismatic batteries the mainstream choice.