What is battery thermal management?
Batteries have similar characteristics to humans in that they cannot tolerate extreme heat or cold, and their optimum operating temperature is typically between 15-40°C. However, the working environment of a car can vary widely, with temperatures ranging from -20°C to 55°C being common. So, what can be done in such cases? One solution is to equip the battery with a cooling system to achieve three functions of thermal management: cooling, heating, and temperature consistency.
Cooling: When the temperature is too high, the battery’s lifespan (capacity degradation) is reduced, and the risk of thermal runaway (overheating) increases. Therefore, cooling is necessary when the temperature is too high.
Heating: When the temperature is too low, the battery’s lifespan (capacity degradation) is reduced, its performance weakens, and if charging occurs, there is a risk of thermal runaway due to lithium plating causing internal short circuits. Therefore, heating (or insulation) is necessary when the temperature is too low.
Temperature consistency: Do you remember the air conditioners we used to have at home when we were young? They would start with a blast of cold air and then take a break. However, modern air conditioners often have variable frequency and surround airflow functions to maintain temperature consistency in both time and space. Similarly, power batteries need to minimize temperature differences in space as much as possible (to ensure that the temperature difference within the battery cells is as small as possible).
The impact of low temperature on vehicles and batteries is well known. The power battery is the most critical component of an electric vehicle and affects its performance in every aspect: how far it can travel, maximum acceleration, lifespan, and, of course, safety. Many factors influence the performance of a power battery, with temperature being the most significant one. Electric vehicle owners in northern regions especially have experienced the challenges posed by low temperatures. Many early electric vehicles would see their range reduced to only 70% in winter. Some people hesitated to turn on the heating to avoid affecting the driving range.
In reality, low temperatures also reduce the battery’s discharge capability. Lower battery temperatures completely suppress the battery’s discharge ability, affecting not only the driving range but also the vehicle’s power output and energy recovery, among other things. Let’s take the common lithium-ion battery as an example: the working principle of a lithium-ion battery is essentially the redox reaction between the internal positive and negative electrodes and the electrolyte. At low temperatures, the reaction rate of lithium intercalation into the surface active material of the electrode slows down, the concentration of lithium ions inside the active material decreases, which leads to a decrease in the battery’s balanced potential, an increase in internal resistance, a decrease in discharge capacity, and in extreme low-temperature conditions, phenomena such as electrolyte freezing and the inability of the battery to discharge can occur. This greatly affects the low-temperature performance of the battery system in electric vehicles, resulting in decreased power output performance and reduced driving range. Additionally, in low-temperature environments, lithium deposition is more likely to occur on the negative electrode surface during charging, and the accumulation of metallic lithium on the negative electrode surface can puncture the battery separator, causing a short circuit between the positive and negative electrodes, posing a safety risk. The safety issues associated with low-temperature charging in electric vehicle battery systems are significant constraints to the promotion of electric vehicles in cold regions.
Is there a technology that can alleviate the above problem?
Based on the information provided, it is evident that the lack of battery thermal management or poor thermal management in electric vehicles can have a significant impact on their performance. However, with technological advancements, most modern electric cars are equipped with battery thermal management systems. The ultimate goal of these systems is to maintain the battery temperature within the optimal operating range.
Battery thermal management is necessary depending on the type of battery used in the vehicle, as well as the heat generation rate, energy efficiency, and temperature sensitivity of the battery. Thermal management includes both heating and cooling and is equally important. Preheating technology is an important component of battery thermal management, aiming to quickly raise the battery temperature to the optimal operating temperature when it is low. There are several mainstream battery heating methods, including:
- Battery self-heating: This method utilizes the heat generated during battery operation, discharge, or charging to increase the battery temperature. However, this method has a slow heating effect and is often insufficient to raise the battery temperature before the vehicle is used. It is no longer commonly used in mainstream vehicles and is more prevalent in early models or low-cost vehicles.
- Air blowing heating: To be honest, air-cooled battery packs are not commonly seen in the market. It has been reported that BYD has developed air-cooled battery packs. This method involves using external air conditioning to blow hot or cold air into the battery pack to control the temperature. However, this technology requires strict design of the air ducts within the battery pack, and the heating effect on the battery temperature rise is relatively slow. Moreover, if not well-designed, it can easily lead to localized overheating.
- Heating equipment inside the battery pack: The heating system mainly consists of heating elements and circuits, with the heating elements being the most important part. Common heating elements include variable resistance heating elements and constant resistance heating elements. The former is often referred to as PTC (positive temperature coefficient), while the latter is typically made up of a heating film composed of metal heating wires, such as silicone heating film or flexible electric heating film. PTC or heating film methods generally provide good heating effects and faster heating speeds. However, there may be uneven temperature rise in the battery, with the cells closer to the heat source experiencing significantly higher temperature increases compared to those farther away. This is especially the case with heating films that are in direct contact with the surface of the battery module, requiring certain requirements for the heat dissipation structure within the battery pack.
PTC is widely used due to its safety, high thermal conversion efficiency, rapid heating, absence of open flames, and automatic temperature control. It has a lower cost, which is advantageous for current high-priced power batteries. However, PTC heating elements have a larger volume, occupying a significant space within the battery system. Insulated flexible heating films are another type of heater that can be bent to match the shape of the object being heated, ensuring close contact and maximum heat transfer. Silicone heating films are flexible thin surface heating elements, but they require complete contact with the heated object, and their safety is somewhat inferior to PTC.
- hydronic heating: Liquid-cooled battery packs have gained popularity in current designs due to their effective heating, uniform heat dissipation, and reliable safety characteristics. In the internal structure of the battery pack, water channels or pathways are typically designed to facilitate heat dissipation, ensuring even distribution of heat throughout the battery pack and achieving uniform temperature rise.
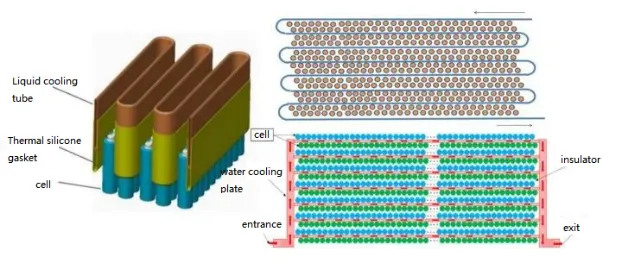
This is the principle of battery heating. Additionally, I can share some insider information with you. The upcoming Xpeng P7, which is currently under development, will feature a novel one-click navigation charging station pre-heating function. It allows your vehicle to pre-heat the battery while en route to a supercharging station. The heating power is adjusted based on the distance provided by the navigation system. This ensures that the battery is at the optimal temperature when arriving at the charging station, ready for supercharging.
The main scenarios and characteristics of battery pre-heating are primarily focused on winter in northern cities. The main usage scenarios include both discharging and charging situations. When a vehicle is parked in a cold environment for a period of time and then started, the battery temperature is typically low, which significantly affects the driving experience. If the vehicle then proceeds to a charging station for charging, it also greatly impacts charging efficiency. Therefore, detailed temperature calibration is required for the start and stop strategies of battery pre-heating to achieve optimal results without wasting resources while meeting customer usage scenarios. This also tests the integration and matching capabilities of the automaker.
The “barrel effect” of the power battery, where the performance and reliability of the battery system depend on the weakest cell, and the safety of the system depends on the least stable cell, determines that only battery packs with better temperature consistency can demonstrate the best performance. This is why most battery packs are designed with liquid cooling.
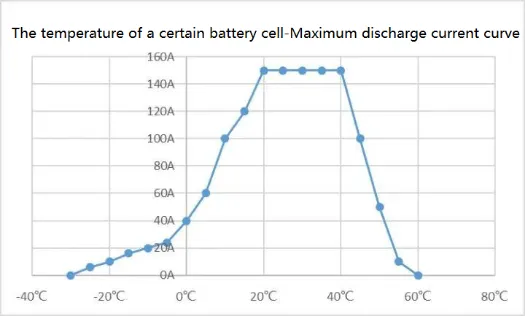
Indeed, there are many more details and points to explore regarding battery pre-heating technology. Some examples include heat dissipation for square-shaped batteries, optimal operating temperature ranges for different cell materials, the integration of passenger compartment thermal management with battery thermal management, optimization of battery pack structure, and so on. Each of these topics is worthy of in-depth research.