卷绕是指将尺寸匹配的电极片、隔板和端子带切成条状,通过控制电极片的速度、张力、尺寸和偏差等因素,将其卷成果冻卷的生产过程。
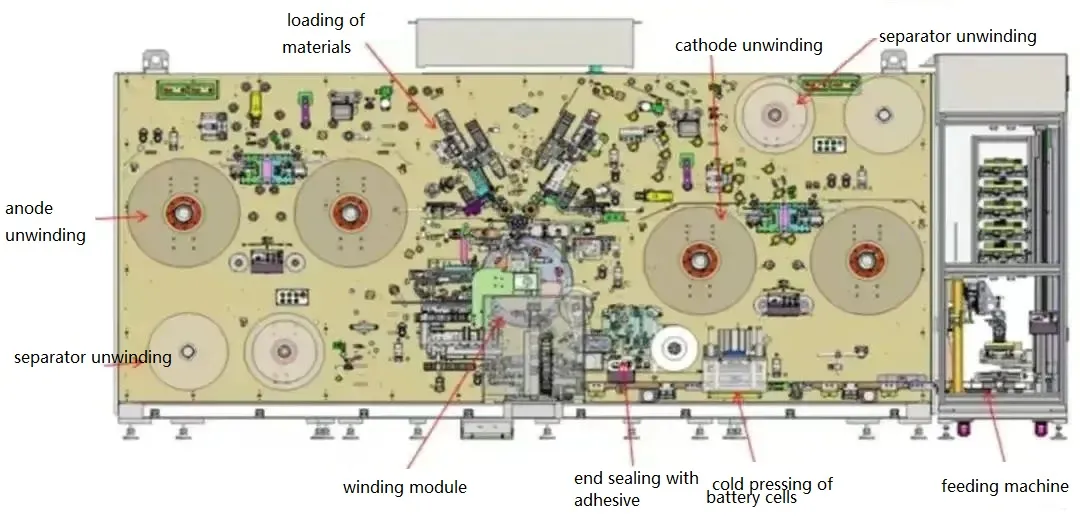
01.绕线设备分类概述
主流绕线机的分类
锂电池绕线机用于锂电池电芯的绕线,它们是将正极片、负极片和隔膜通过连续旋转组装成铁芯包的机器。绕线机由正负极送料装置组成,正负极隔膜缠绕在一起的部分称为绕线针。
根据绕线芯组形状的不同,绕线设备主要可分为棱柱形绕组和圆柱形绕组两大类。棱柱形绕线又可分为棱柱形自动绕线机和棱柱极耳绕线机。通过方形绕组生产的电池芯主要用于制造动力/储能方形电池、数字电池等。各种类型的电池卷绕设备如图所示。
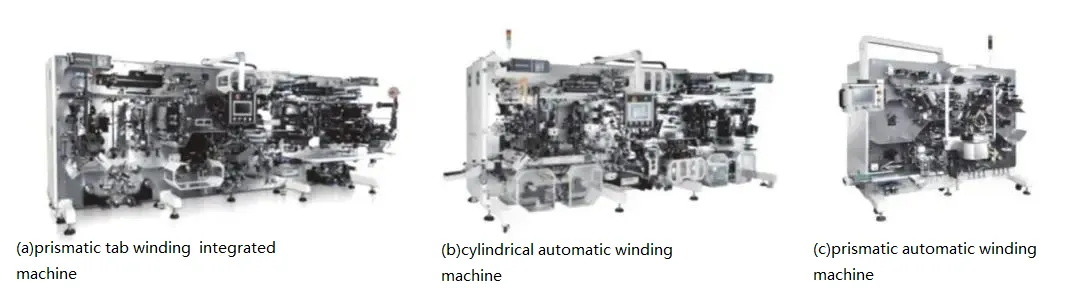
绕线机可以根据其自动化程度分为几类,例如手动、半自动、全自动和集成机器。它们还可以根据它们生产的核心包的大小进行分类,包括小、中、大和超大型。
表1:绕线机规格和芯组尺寸比较表

锂电池自动化生产设备的出现始于1990年日本公司Kaido成功开发的第一台方形锂电池卷绕机。1999年,韩国公司Koem成功开发锂电池卷绕机和组装机。随后,锂电池自动化生产设备的开发开始,日本和韩国仍然是该领域的领导者,由于其卓越的技术和声誉占据了主要的市场份额。中国的国产绕线制造设备始于2006年,最初是半自动圆形和棱柱形绕线机,然后是自动极耳制作和绕线集成机。
1.2绕组工艺发展的挑战
不可否认,基于多年的技术积累,绕线工艺在生产设备、工艺流程、效率和成本方面具有显著优势。然而,随着对标准化、高容量和大尺寸汽车级动力电池的需求不断增加,绕线工艺面临挑战和限制。
本文描述了缠绕单元的标准结构特征,两端都有圆角区域。在电池的充放电过程中,不一致的膨胀和收缩会导致电极板与隔膜之间的间隙增大。当电解液在该区域不足时,会影响容量性能,长期使用可能会带来与镀锂相关的安全问题。此外,随着对更高能量密度的需求不断增加,硅基负极材料正在逐渐被引入。然而,由于硅基负极的显着膨胀,绕线电极组件中存在内部电极板断裂的风险,这会影响电池的使用寿命并限制可以添加的硅材料的数量。
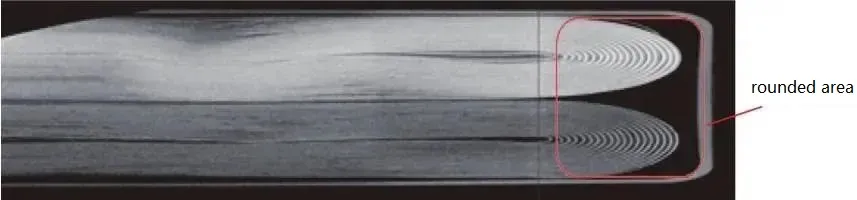
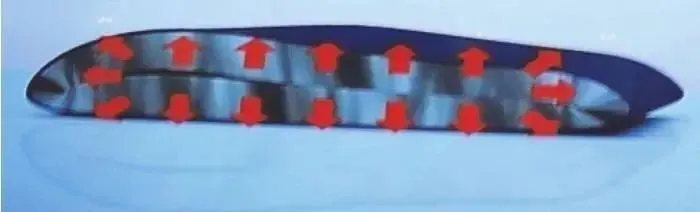

1.3绕线机的未来发展方向
(1)高速、高精度:绕线电极片的线速度将从目前的2-3m/s提高到5m/s,绕线电极片的对准精度将从目前的±0.3mm提高到±(0.1-0.2)mm。
(2)高合格率:CPK将从1.33提高到1.67,最终达到2.0以上,达到零缺陷水平。
(3)稳定性:增加平均故障间隔时间,从目前的几十或几百小时增加到几千或几万小时。
(4)设备数字化、智能化控制:在线监测绕组张力,电极片和隔板对位,绕组参数和最终电池性能参数闭环优化,提高绕组合格率。
(5)激光切割和收卷的集成:激光切割和收卷工艺的集成,实现设备集成。
(6)高速绕线机:分离器连续均匀运动技术的突破将使绕线效率翻倍。
02.设备原理、组成和关键结构
2.1绕线机原理
绕线机主要用于方形或圆柱形裸电池芯的自动绕线。设备采用两根或多根绕线针和单侧抽针的结构。正负极电极片和隔片主动展开,进行电极片-隔膜卷交换、自动对位校正、自动张力检测和控制。电极片通过夹紧辊驱动机构引入收卷段,并根据工艺要求与分离器自动卷绕在一起。绕线完成后,它会自动切换到下一个工位,切割分离器,并贴上端子胶带。成品裸电池单元自动卸载,进行预压和扫描,合格产品自动转移到托盘上,然后转移到后续流程中。有缺陷的裸电池单元会自动卸载到有缺陷的裸电池单元的收集区域。
2.2绕线机机构说明
(1)预卷:这是正负极电极片的初始进料过程。在此过程中,正负极电极片由电机以恒定速度供给。绕线针的转速需要与电极片的进料速度同步。此过程涉及六个电机。涉及两种类型的同步:分离器的放卷速度和卷绕针的速度之间的同步,以及电极片的进料速度和卷绕针的速度之间的同步。
(2)绕线过程:正负极电极片的初始进料过程完成后,隔板紧紧缠绕电极片,绕着绕线针绕一圈开始绕线过程。在此过程中,通过检测料卷的张力来调整电极片的进料速度。这种调整确保了卷绕过程中材料卷的恒定张力。
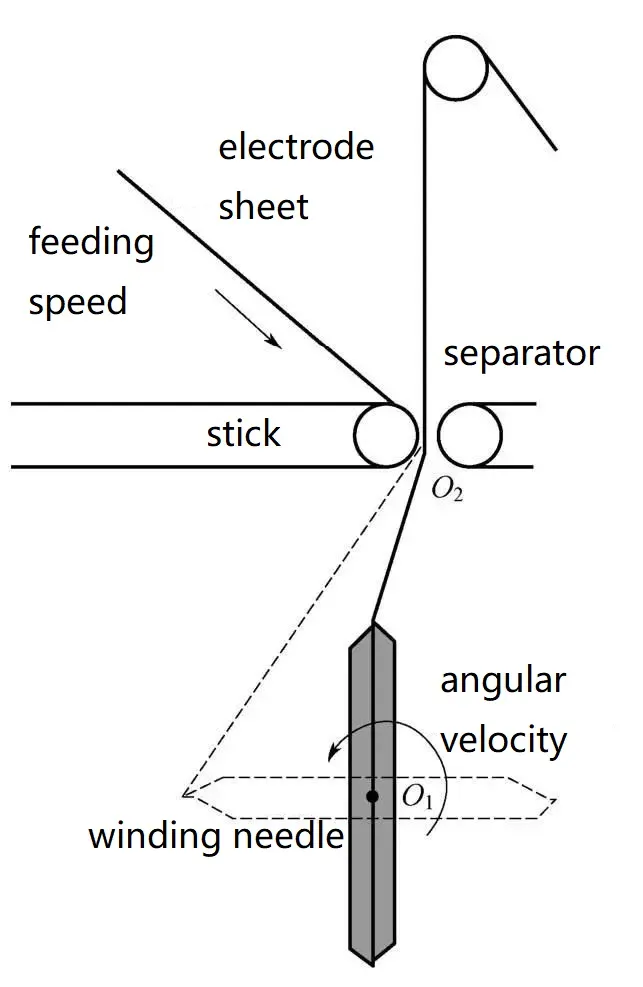
绕组过程示意图
绕线过程的示意图如图所示。此过程涉及六个电机。同步有两种类型:分离器的放卷速度与绕线针的速度同步,以及电极片的进料速度与绕线针的速度之间的同步。预绕组阶段的控制问题属于开环控制问题,因为两者之间没有真正同步的反馈校准。这就要求我们建立一个准确的绕线速度模型。在收卷过程中进行材料卷的张力测量,允许在控制过程中使用闭环反馈控制技术。
在收卷过程中,我们实际上控制着每个电机的旋转频率,而实际速度是料卷和收卷针半径的函数,它会随着时间的推移而动态变化。目前,在没有实际传感器进行测量的情况下,我们假设料卷在一次加载过程后中间半径的变化遵循阿基米德螺旋定律,而不考虑手动换卷的影响。此外,绕组材料的初始半径是在程序中预先确定的。
(3)绕线过程的动态建模:由于预绕线过程属于开环控制,因此准确的数学模型对于确定系统的成败至关重要。
2.3设备组成及关键结构
设备主要模块包括:电极/隔板自动放卷模块、电极/隔板换卷模块、自动对位校正模块、导辊模块、电极片导向压平模块、主驱动模块、张力控制模块、张力测量/显示及存储模块、电极进料模块、隔膜静电去除装置、电极片折叠/弯曲及电极损坏检测模块、 CCD在线检测模块、电极切割模块、除尘系统、不良电极和分离辊剔除模块、收卷头组件、分离器切割模块、分离器吸附模块、端子胶带应用模块、自动卸载模块、裸电池预压模块、出料模块、设备框架和主面板模块。
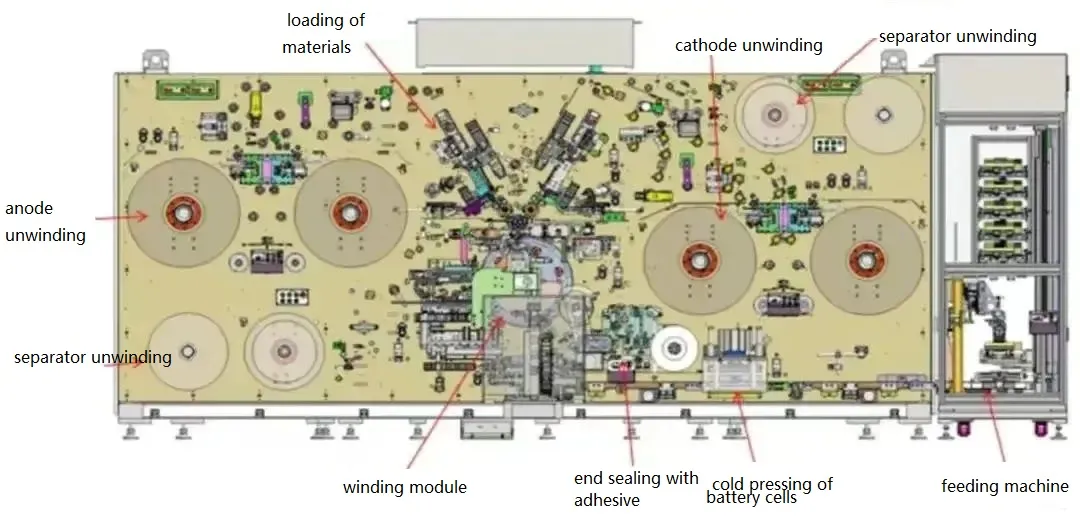
关键结构如下:
1.电极/分离器自动放卷系统:由电极/分离器自动放卷轴、皮带进料组件、放卷对中校正组成。它实现了电极/分离辊的固定、自动放卷和自动更换等功能。放卷轴采用机械或气动膨胀方式,辅助块和边缘检测机构便于快速定位。
2.自动纠边模块:由多级纠偏机构组成,可采用吊轴移动、导辊摆动、压区辊驱动等多种方式进行纠边。通过在皮带移动过程中实时检测、控制和显示材料边缘,它实现了对材料边缘的实时校正。传感器的定位旨在避免灰尘积聚,从而影响边缘值检测的准确性。主要参数包括±0.2mm的放卷对中精度和±0.1mm的过程中对中精度。
3.张力控制系统:由张力检测传感器、张力控制机构和显示/存储模块组成。张力控制机构可以包括直线电机、低摩擦气缸或伺服电机。张力检测机构的位置尽可能靠近卷绕针机构。通过有效控制皮带运动过程中材料的张力,它可以设置和调整每个卷绕周期的张力。为了实现精确控制,重要的是要防止裸电极因卷绕张力问题而变形。随着绕线过程中绕线直径逐渐增大,需要增加张力以保证电极的密封性。在每个绕线周期内,必须将张力的波动控制在一定范围内。
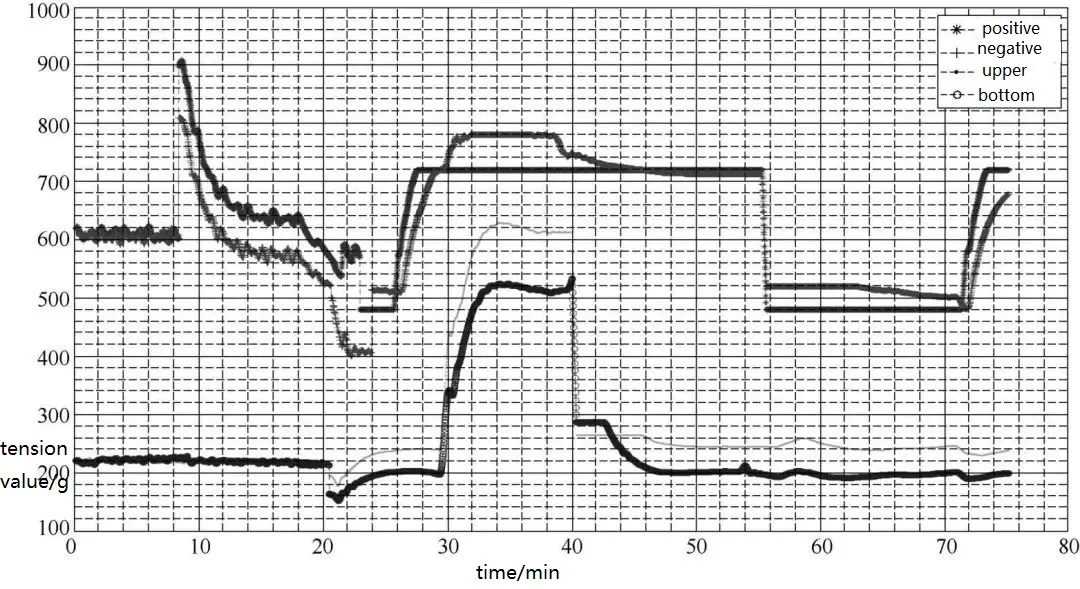
4、电极送料模块:由正负极压辊驱动机构和送料机构组成,负责收卷前对电极的送料。在收卷过程中,进料位置和材料的相对位置保持不变。进料压辊和电极在进料前的自由长度应尽可能短,同时确保适当的进料和拖尾。电极进料区具有吹气和导向功能,并带有数字压力监控功能。吹气和导向的方向是可调的,并配有角度刻度。此外,电极进料效率高、噪音低、无污染,并且可以轻松量化倾斜角度。
5.电极切割模块:由正负极压制和切割机构组成,能够自动检测电极末端的标记孔(由激光模切产生)。一旦达到设定的电极片数量或通过识别电极片之间的间距,模块就可以以预定长度切割电极。它还允许切割特定长度的电极。切割刀片建议采用钨钢等硬质材料制成,动刀片和固定刀片都有特定的角度。此外,切割区域应有隔离防护罩和警告标志,同时还要经过处理以防止粘附。
6.单线圈不良电极和隔膜去除模块:它由伺服电机、联轴器和线性导轨机构组成,并被编程为执行独立的去除功能。它可以在没有隔板的情况下单独移除有缺陷的正负极线圈。当在正极或负极检测到缺陷时,它可以自动将线圈与隔膜一起移除或单独移除。有缺陷的产品被排放到一个单独的机构中,并被收集在一个废品箱中。在移除没有隔膜的线圈的过程中,电极不会干扰或摩擦其他组件,确保不会影响下一种材料的对齐。
7.收卷模块:由双工位或多工位机构组成,配备双伺服电机或多个伺服电机驱动收卷机构。每组对应2个或多个上链针机构。它还配备了一个锁定和定位机构,用于在换站后旋转塔架。该模块可实现电池单元的绕线和不同绕线站之间的自动切换,同时在绕线过程中保持恒定的线速。它可以实现先绕组正极或负极,以及同时送入和绕组两个电极等功能。
在绕组过程中防止电池单元内产生内部折叠至关重要。在电池实际使用过程中,内部折叠会导致局部镀锂,构成重大的安全风险。
关于皱纹的产生,存在缠绕皱纹的规律:对于不同类型的缠绕针,缠绕芯的各层之间可能存在皱纹。起皱的原因是,随着电极在每次绕组匝中积累,电极的层间半径增加δ,电极的积累长度也增加。当电极累积圆周长度的增加速率不等于绕组半径的增加速率时,绕线针压紧纤芯后,内部电极出现皱纹。这被称为缠绕皱纹定律。
通常,菱形绕线针由于其结构特性,在绕线过程中会经历明显的电极张力波动。电极圆周的生长速率与半径的生长速率不一致,可导致层间皱纹的发生。相比之下,椭圆形、椭圆形和圆形的缠绕针没有皱纹的问题。
8.薄膜切割模块由热切刀机构和保护机构组成,可根据产品所需的长度对薄膜进行切割。切割部分需要有高温和刀片安全保护,并有警告标志,并应配备隔热装置。它具有吹气和使用旋转塔主轴将切割的膜压平等功能,防止膜起皱。膜切割后,需要立即吸吮,以防止膜因静电而卷曲,从而导致膜光洁度不佳。
9.端接胶带粘贴模块由自动编带机构、胶带标记孔传感器和胶带应用辊组成。卷带展开后,它会自动准备成所需的长度。该模块还会自动检测胶带标记孔,并将其应用于裸露电极芯的角落或末端。端接胶带粘贴机构设计为适应性强,允许根据裸露电极芯在绕线针上的位置调整胶带的位置。磁带放卷机构具有主动放卷能力,并包括防静电功能。
10.印前分切模块由裸电极芯卸料机构、裸电极芯预压装置、裸电极芯转移机构组成。它自动从绕线针上卸下裸电极芯,并在运输过程中对优质裸电极芯进行预压。预压后,扫描电极芯表面的二维码绑定信息,然后通过传送带将电极芯转移到切割机上。与裸电极芯接触的压力板经过处理,防止粘连,并配有预压压力传感器,以防止损坏裸电极芯。
11.除尘系统:由正重切纸机上的除尘装置、毛刷装置、静电去除组件、正重薄板/局部磁棒、单独的除尘罩和FFU系统组成。和裸电池表面,并防止环境进入裸电池。此外,除尘器的入口/出口管道由增强和防静电材料制成。管的内壁是光滑的。滤芯由防静电材料制成。进气管道应避免直角转弯。整体式封闭盖板采用隔离的透明盖板和隔板,隔离不同区域,即对接电极区、接触区、收卷区、卸料区,防止仓内混料和外混。同时,通过使用FFU系统来控制设备内部的气流,使其保持在略高于外部环境的正压。所有旋转连接器、紧固件、盖板和带子都应使用金属和非金属或完全非金属材料的组合。气动元件等部件应由不含铜和锌的材料制成,并应进行表面处理,以防止铜和锌粉尘的产生和污染。
负压吸入管道汇合到主吸入管道中,然后引出设备。整个气流场通过计算建模进行仿真。入口管道需要一定的风速,同时避免急剧弯曲。如果弯曲角度超过45度,则需要一个维护接入点。
12.电极过程检测系统由多套高分辨率工业相机、机器视觉光源、安装结构、工业计算机和显示器组成。视觉CCD相机可捕获阴极电极、阳极电极、上下隔膜的位置以及电池单元四个角的指定标记的图像。PC上的机器视觉软件分析材料边缘或边界与标记位置之间的二维距离。由计算机进行实时计算,确定阳极与上隔膜同一圆、阴极与阳极相同圆、阴极AT9与阳极相同圆、下隔膜与阴极同一圆、阴极前一圈与下阳极圆之间的位移值。这些值以散点图曲线和图层的形式实时显示在显示器或触摸屏上。此外,该系统还监控电池单元的排量值。
系统处理数据并计算每层裸电极芯之间的最大、最小和平均位移值。检测范围覆盖电芯第一圈到最后一圈,确保全面检查。
CCD检测示意图如图所示。检测系统安装在绕线机绕线针外侧附近,确保不会干扰绕线元件的运动和运行。与大板的角度和距离是连续可调的。结构构件需要具有较高的强度和牢固的安装,以免影响测量精度。相机和镜头均设计有碰撞保护功能,以防止任何可能导致结构部件移位或损坏的意外碰撞。
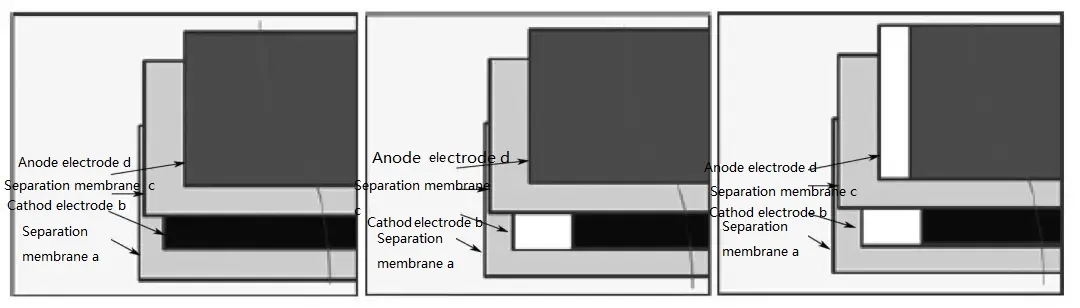
03.器件选型及应用案例
(1)明确来料流程
确认来料的兼容性要求,包括正负极片的宽度和厚度范围、波浪边缘、蛇形弯曲、线圈直径和卷筒内径等参数。
(2)明确产品规格
(1)确认裸电池规格的兼容性,包括电池厚度、宽度、高度等主要参数。
电池规格示例

如图所示的单元格尺寸
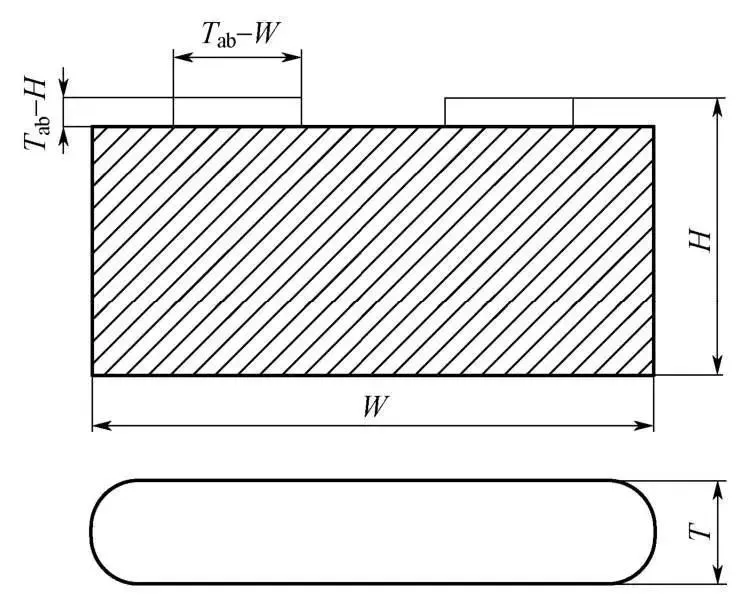
阐明胶粘剂应用过程,无论是使用单面胶粘剂还是双面胶粘剂。指定尺寸,例如胶带宽度和胶粘剂长度。
(3)明确设备配置
(1)功能配置:根据来料工艺和产品规格,确认整体设备配置需求。放卷配置包括具有自动换卷功能的正负极双放卷、分离膜双轴放卷和手动换卷。错位控制包括电极过程中的三个或更多级别的错位校正。绕线头采用直接驱动,绕线针的类型包括菱形、椭圆形或圆形针,可选择双针或三针配置。针式送料采用双夹持机构进行送料。细胞补料后,在后续补料过程之前进行预压。
(2)建立并执行机械、电气和信息系统的一般规范。