Au cours de la dernière décennie, l’industrie des batteries lithium-ion est passée d’une automatisation semi-automatique à une automatisation autonome, puis progressivement à une automatisation et une intelligence complètes. Tout au long de ce processus, il y a eu peu de changements majeurs dans les processus de fabrication des batteries. Cependant, avec la croissance continue et rapide de la demande de batteries, dépassant 100 % par an, et les mises à niveau continues des systèmes de matériaux de batterie, les processus de fabrication des batteries doivent inévitablement être mis à niveau pour s’adapter aux changements dans l’échelle de fabrication et les systèmes de batteries. En conséquence, les équipements de batterie, en tant que « poule mère » de l’industrie des batteries lithium-ion, ont également rencontré de nouvelles opportunités de percées.
Tendances en matière de technologie de fabrication et de développement d’équipements
À l’avenir, la tendance au développement des batteries de stockage d’énergie s’orientera vers une plus grande capacité à partir de petites cellules individuelles. Les équipements lithium-ion doivent garantir la précision de la fabrication de ces grandes cellules, une efficacité de fabrication élevée et améliorer la compatibilité et l’évolutivité. Cela nécessite des améliorations correspondantes de la précision d’usinage des composants et de la précision d’assemblage des modules.
Pour relever les défis de la fabrication de batteries lithium-ion à grande échelle, l’efficacité des équipements doit être améliorée.L’efficacité de production des équipements lithium-ion est principalement améliorée de deux côtés. Tout d’abord, en augmentant la vitesse de production de l’équipement à l’aide de structures et de méthodes de contrôle plus rapides et plus stables. Deuxièmement, en réduisant le temps consommé par les mouvements d’équipements, ce que l’on appelle le temps auxiliaire.
À titre d’exemple, la machine d’enroulement continu pour séparateurs développée par Geesun Intelligent est un équipement typique. Auparavant, chaque cellule accélérait et était alimentée à la vitesse d’enroulement la plus élevée, puis décélérait, s’arrêtait, coupait le séparateur, enfilait l’aiguille et passait à l’enroulement de la cellule suivante. Après amélioration, le séparateur ne ralentit pas et un mécanisme de coupe volant est utilisé pour couper le séparateur, ce qui est fait à l’avance pendant le processus de décélération de l’électrode. Cela réduit le temps consommé par le processus de coupe de l’électrode et du séparateur, minimisant efficacement le temps auxiliaire à près de zéro, ce qui entraîne une amélioration globale du temps de cycle de production de 30 à 60 % (selon la longueur de l’électrode). Un autre exemple est la machine de découpe de languettes d’électrodes, qui a augmenté sa vitesse de découpe laser de 80-120 m/min à 200 m/min.
De ce point de vue, l’avancement et l’itération des équipements de fabrication au lithium-ion s’orientent vers des solutions intelligentes à grande échelle, de haute précision, de haute fiabilité et entièrement intégrées.
Du point de vue de l’optimisation des processus de fabrication lithium-ion, les équipements intégrés et entièrement intelligents offrent une plus grande stabilité de production, une automatisation accrue et une plus grande adaptabilité aux processus de fabrication. Il aide également les entreprises manufacturières à réduire les coûts de main-d’œuvre et d’espace, à raccourcir les liens entre les processus et à minimiser le gaspillage de matériaux, jouant ainsi un rôle clé dans l’amélioration de l’efficacité globale.
Intégration poussée de la technologie des matériaux et de la technologie de fabrication
Tout au long du processus de fabrication des batteries, il s’agit de passer d’opérations de traitement de matériaux à l’échelle nanométrique à la production et au traitement de dispositifs à l’échelle du mètre. Dans le passé, la fabrication au lithium-ion se concentrait principalement sur le contrôle de l’efficacité de fabrication, de la qualité et du coût des équipements basés sur la mécanique newtonienne. Les principaux paramètres contrôlés étaient les positions physiques, les vitesses, les accélérations, les inerties, le frottement et la résistance des matériaux. Ces contrôles étaient relativement macroscopiques, et la visibilité et l’observabilité du processus étaient relativement faciles à gérer.
Sur la base du fait que les batteries impliquent la migration d’ions sous l’influence d’un champ électrique interne, tandis qu’en externe, le processus se reflète dans le transfert d’électrons, il est nécessaire de contrôler la production et l’utilisation des batteries d’un point de vue microscopique en utilisant la mécanique quantique. Cela implique de prendre en compte l’évolution de la structure et de la composition des batteries pendant la production et l’assemblage, ainsi que les comportements de transport des électrons et des ions, les problèmes d’interface et l’effet de l’échelle de performance sur les batteries. Les changements à l’interface pendant le processus de charge-décharge, les variations de performance et d’échelle, ainsi que les effets de couplage entre les molécules internes et les ions, les effets de température et les changements de forme et de volume doivent être pris en compte pour contrôler la sécurité de la batterie, l’autodécharge, la durée de vie, la densité d’énergie et la densité de puissance.
Cela nécessite une plus grande prise en compte de la thermodynamique, de la cinétique (cinétique de transport d’ions, cinétique de transfert de charge, cinétique de réaction, cinétique de transition de phase, etc.) et de la stabilité du processus de fabrication d’un point de vue microscopique.
Cependant, la maîtrise de ces processus complexes manque actuellement d’un modèle théorique complet dans le domaine manufacturier. Cela est dû aux défis inhérents au couplage de champs multi-physiques, aux données multi-éléments et hétérogènes, au contrôle de forme multi-échelle, au contrôle des propriétés intrinsèques et à la gestion des données massives. Les méthodes qui peuvent être employées comprennent l’apprentissage automatique et la modélisation d’optimisation basée sur l’analyse qualitative des tendances et la modélisation du big data. En utilisant la théorie de la mécanique quantique pour comprendre les principes scientifiques intrinsèques aux batteries, l’optimisation des processus, la prise de décision et le contrôle peuvent être réalisés. Des méthodes analytiques et des techniques d’évaluation peuvent être établies pour réaliser une fabrication de batteries reconfigurables, à grande échelle et personnalisées. En fin de compte, cette approche peut résoudre des problèmes tels que la migration d’ions, la génération et le transfert de chaleur, le contrôle de la pression interne, la déformation du procédé, la formation de films SEI et le contrôle de la dendrite de lithium.
Intégration de la fabrication et modifications des principes de fabrication
La discussion précédente s’est concentrée sur les aspects microscopiques à considérer dans la fabrication de batteries d’un point de vue quantique. Dans le contexte des réactions électrochimiques couplées dans les batteries lithium-ion, qui impliquent plusieurs champs physiques, une quantification des processus électrochimiques de la batterie peut être réalisée à l’aide de variables d’état généralisées telles que les nombres sans dimension, la densité des particules, la densité des défauts du réseau, la vitesse des particules, etc.
En utilisant des techniques de simulation numérique multidirectionnelle de dynamique des particules lisses, il est possible de développer des modèles numériques qui prennent en compte la microstructure à méso-échelle des électrodes. Ces modèles peuvent simuler le champ de concentration ionique, le champ de potentiel solide-liquide, la densité de courant de conversion et d’autres détails microscopiques dans la batterie pendant le processus de décharge. De plus, ils peuvent analyser et révéler les mécanismes physicochimiques fondamentaux des processus de charge-décharge de la batterie et leur corrélation avec les performances macroscopiques de la batterie, y compris des facteurs tels que la tension de sortie et la taille des particules des matériaux actifs solides constituant les électrodes.
La fabrication d’électrodes sèches, guidée par les principes de la dynamique des particules à méso-échelle, implique l’intégration de processus tels que la fabrication, le mélange, l’agitation, l’enrobage, le séchage et le laminage des électrodes. L’intégration de la découpe et de l’enroulement laser ainsi que de la découpe et de l’empilage laser dans un seul équipement est une tendance importante. À l’avenir, nous prévoyons que la production de cellules de batterie ne nécessitera que trois principaux types d’équipements : l’équipement de production d’électrodes, l’équipement d’assemblage et l’équipement de test. Cependant, il s’agit d’un scénario idéal qui nécessite des efforts conjoints et des progrès dans les matériaux, les processus et les équipements. Cela ne peut pas être réalisé du jour au lendemain, et cela nécessitera les efforts dévoués et la diligence des professionnels de la fabrication de batteries.
Le processus principal de préparation des électrodes sèches (également connu sous le nom de « revêtement sec ») comprend la sélection de liants non fibrés, le broyage à billes de liants non fibrés pour la granulation et le mélange de liants non fibrés, de liants fibrés et de matériaux actifs d’électrode (cathode/anode) avant le calandrage. Pour garantir la plasticité des matériaux, le mélange est souvent chauffé à des températures supérieures à 100°C pendant le processus de formage.
Les liants non fibrés utilisés par Maxwell comprennent le fluorure de polyvinylidène et la carboxyméthylcellulose, tandis que le liant fibré principalement utilisé est le polytétrafluoroéthylène. Le traitement parallèle est couramment utilisé dans leurs processus de fabrication. Veuillez vous référer à la figure ci-dessous pour une illustration du processus de fabrication des électrodes sèches de Tesla.
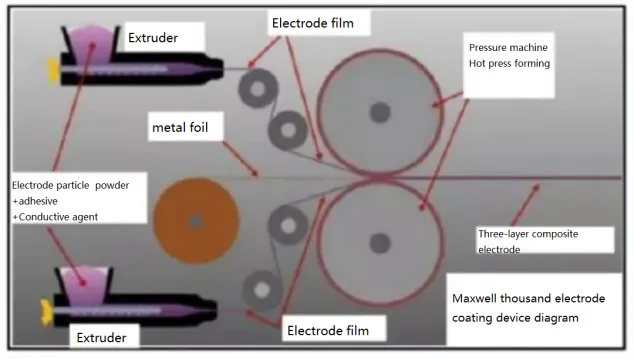
Par rapport aux procédés traditionnels d’électrode humide, le procédé d’électrode sèche utilisé par Tesla (Maxwell) offre plusieurs avantages. Il remplace l’agitation par le broyage à billes et l’enrobage par le calandrage, éliminant ainsi le processus de séchage après l’enrobage humide. Cette méthode permet d’économiser des solvants, de réduire le temps de traitement, d’éviter les résidus de solvants et de réduire la complexité de l’équipement. Cependant, le processus sec a ses limites, en particulier pour obtenir une dispersion uniforme des matériaux actifs, ce qui est particulièrement difficile pour les électrodes de batterie lithium-ion par rapport aux matériaux d’électrode de supercondensateur.
Le processus d’électrode sèche de Tesla est encore plus simple et ne nécessite pas l’utilisation de solvants. Le processus commence avec de la poudre d’électrode, où une petite quantité (environ 5 à 8 %) de liant fin de polytétrafluoroéthylène (PTFE) est mélangée à la poudre de cathode. Le mélange de poudre de cathode et de liant est ensuite extrudé pour former une fine bande de matériau d’électrode. Cette bande de matériau d’électrode extrudé est laminée sur un collecteur de courant à feuille métallique pour produire l’électrode finale. Le procédé à sec améliore l’efficacité de la fabrication des électrodes, raccourcit les étapes de traitement et ouvre de nouvelles possibilités pour la production à grande échelle de batteries de stockage d’énergie.
Processus de fabrication et structure de batterie simplifiés
L’équipement utilisé dans chaque processus de fabrication de batteries au lithium affecte considérablement les performances de la batterie. La longueur du flux de processus de la batterie a également un impact sur la cohérence et la contrôlabilité de la préparation des cellules. La simplification des processus de fabrication d’électrodes et de formage de cellules en est un exemple réussi. Le développement d’équipements tels que des machines intégrées de calandrage et de refendage, des machines de découpe et d’enroulement laser, ainsi que des machines de découpe et d’empilage laser a rationalisé les processus et amélioré la capacité de contrôle en boucle fermée. Cette simplification permet non seulement de réduire le coût du transport des matériaux en raison d’itinéraires complexes, mais aussi d’économiser de la main-d’œuvre.
Dans le développement futur de l’industrie des batteries, il y aura des changements révolutionnaires dans l’optimisation des performances des batteries et des structures de fabrication. Cela inclut les modifications de la forme, de la taille et des connexions des électrodes du boîtier de la batterie en fonction des performances, de la fabrication et des exigences de connectivité. Les collecteurs de courant internes et les connexions des électrodes peuvent également être modifiés pour répondre aux exigences de recyclage des batteries.
CATL et BYD ont adopté des approches différentes pour rationaliser leurs processus. Ils utilisent différentes formes de CTP (Cell to Pack) pour raccourcir le flux de processus. Le CTP consiste à sauter l’étape du module et à intégrer directement les cellules de la batterie dans le pack pour augmenter l’utilisation du volume. Dans la batterie CTP de CATL, il y a plusieurs modules de batterie, chacun contenant plusieurs cellules et un cadre pour accueillir ces cellules. Ils ont remplacé les petits modules par des plus grands. Le CTP de BYD, également connu sous le nom de GCTP (Blade Battery), atteint des niveaux d’élimination de module encore plus élevés, où la batterie de lame n’utilise qu’un seul grand module. Voir le tableau ci-dessous pour une comparaison des processus CATL-CTP et BYD-CTP.
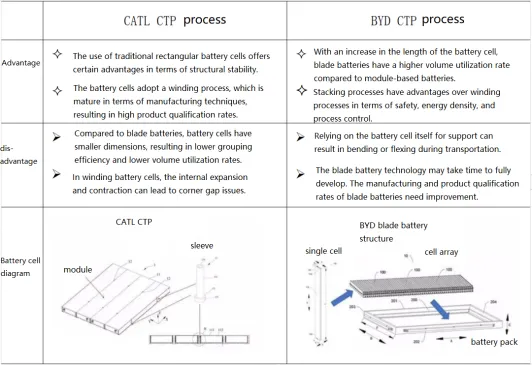
La demande de batteries lithium-ion dans le domaine des nouvelles applications énergétiques ne cesse de croître. Les principales entreprises de batteries lithium-ion visent à réaliser des économies d’échelle et à réduire les coûts grâce à une expansion continue de leur capacité. Ils ont des exigences plus élevées en matière de processus de chaîne de production, de performances et d’efficacité de la production. Les équipements lithium-ion jouent un rôle crucial dans l’amélioration de l’efficacité des processus, des taux de rendement et de l’efficacité de la production dans la fabrication lithium-ion. La capacité d’innovation est la compétence essentielle des processus de fabrication de batteries. L’amélioration et l’itération continues des équipements lithium-ion, ainsi que d’autres percées dans la technologie de fabrication lithium-ion, nécessitent une collaboration étroite.