在过去的十年里,锂离子电池行业从半自动过渡到独立自动化,然后逐渐走向完全自动化和智能化。在整个过程中,电池制造工艺的重大变化很小。然而,随着电池需求的持续快速增长(每年超过100%)以及电池材料体系的不断升级,电池制造工艺不可避免地需要升级以适应制造规模和电池系统的变化。相应地,电池设备作为锂离子电池行业的“母鸡”,也遇到了新的突破机会。
制造技术及设备发展趋势
未来,储能电池的发展趋势将从单个小电池转向更大容量。锂离子设备需要确保制造这些大型电池的精度、高制造效率,并提高兼容性和可扩展性。这就要求对部件的加工精度和模块的装配精度进行相应的提高。
为了应对大规模锂离子电池制造的挑战,需要提高设备的效率。锂电设备的生产效率主要从两个方面进行提升。首先,通过使用更快、更稳定的结构和控制方法提高设备的生产速度。其次,通过减少设备移动所消耗的时间,称为辅助时间。
例如,吉阳智能开发的分离器连续收卷机就是典型的设备。以前,每个电池都会加速并被送入最高绕组速度,然后减速、停止、切断分离器、穿针,然后继续进行下一个电池绕组。改进后,隔膜不减速,使用飞切机构切割隔膜,这是在电极减速过程中提前完成的。这减少了电极和隔膜切割过程所消耗的时间,有效地将辅助时间缩短到几乎为零,从而使整体生产周期时间缩短了30-60%(取决于电极的长度)。另一个例子是电极片切割机,它将其激光切割速度从之前的80-120m/min提高到200m/min。
从这个角度来看,锂离子制造设备的进步和迭代正在朝着大规模、高精度、高可靠性、全集成智能解决方案的方向发展。
从优化锂离子制造工艺的角度来看,集成化和全智能化设备具有更高的生产稳定性、更高的自动化程度和对制造工艺的更大适应性。它还可以帮助制造公司降低劳动力和空间成本,缩短流程链接,并最大限度地减少材料浪费,在提高整体效率方面发挥着关键作用。
材料技术与制造技术的深度融合
在整个电池制造过程中,它涉及从纳米级材料加工操作过渡到米级器件生产和加工。过去,锂离子制造主要侧重于基于牛顿力学控制设备的制造效率、质量和成本。控制的主要参数是材料的物理位置、速度、加速度、惯性、摩擦和阻力。这些控制措施相对宏观,并且流程的可见性和可观察性相对容易管理。
基于电池在内部电场影响下涉及离子迁移,而在外部,该过程反映在电子转移上这一事实,因此有必要使用量子力学从微观角度控制电池的生产和使用。这需要考虑生产和组装过程中电池结构和成分的演变,以及电子和离子的传输行为、界面问题以及性能标度对电池的影响。必须考虑充放电过程中界面的变化、性能和规模变化、内部分子和离子之间的耦合效应、温度效应以及形状和体积的变化,以控制电池安全性、自放电、循环寿命、能量密度和功率密度。
这需要从微观角度更多地考虑制造过程中的热力学、动力学(离子传输动力学、电荷转移动力学、反应动力学、相变动力学等)和稳定性。
然而,目前在制造领域缺乏对这些复杂过程的控制,缺乏完整的理论模型。这是由于多物理场耦合、多元素和异构数据、多尺度形状控制、内在属性控制以及海量数据管理的固有挑战。可以采用的方法包括机器学习和基于定性趋势分析和大数据建模的优化建模。通过使用量子力学理论来理解电池内部的内在科学原理,可以实现过程优化、决策和控制。可以建立分析方法和评估技术,以实现可重构、大规模和定制的电池制造。最终,这种方法可以解决离子迁移、热量产生和传递、内部压力控制、工艺变形、SEI薄膜形成和锂枝晶控制等问题。
制造集成和制造原则的变化
前面的讨论侧重于从量子角度考虑电池制造中要考虑的微观方面。在锂离子电池中涉及多个物理场的耦合电化学反应的背景下,可以使用广义状态变量(如无量纲数、粒子密度、晶格缺陷密度、粒子速度等)实现电池电化学过程的量化。
通过采用多方向平滑粒子动力学数值模拟技术,可以开发考虑电极中尺度微观结构的数值模型。这些模型可以模拟电池在放电过程中的离子浓度场、固液势场、转换电流密度和其他微观细节。此外,它们还可以分析和揭示电池充放电过程的基本物理化学机制及其与电池宏观性能的相关性,包括输出电压和构成电极的固体活性材料的粒径等因素。
干电极制造以中尺度颗粒动力学原理为指导,涉及集成电极制造、混合、搅拌、涂层、干燥和轧制等过程。将激光切割和收卷以及激光切割和堆叠集成到一台设备中是一个重要的趋势。未来,我们设想电芯生产可能只需要三种主要类型的设备:电极生产设备、组装设备和检测设备。然而,这是一个理想的场景,需要在材料、流程和设备方面共同努力和进步。这不可能一蹴而就,需要电池制造专业人士的不懈努力和勤奋。
制备干电极(也称为“干涂层”)的主要过程包括选择非纤维化粘合剂、球磨非纤维化粘合剂进行造粒,以及在压延前混合非纤维化粘合剂、纤维化粘合剂和电极活性材料(阴极/阳极)。为了确保材料的可塑性,在成型过程中,混合物通常会被加热到100°C以上的温度。
Maxwell使用的非纤维化粘合剂包括聚偏二氟乙烯和羧甲基纤维素,而主要使用的纤维化粘合剂是聚四氟乙烯。并行加工通常用于他们的制造过程。请参阅下图,了解Tesla的干电极制造过程。
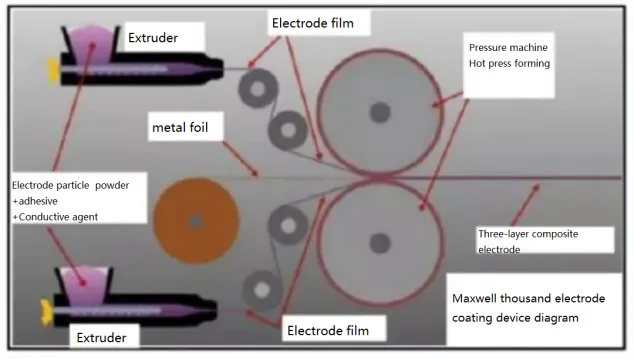
与传统的湿电极工艺相比,特斯拉(Maxwell)使用的干电极工艺具有多项优势。它用球磨代替搅拌,用压光代替涂层,消除了湿涂层后的干燥过程。这种方法可以节省溶剂,减少处理时间,避免溶剂残留,降低设备复杂性。然而,干法工艺有其局限性,特别是在实现活性材料的均匀分散方面,与超级电容器电极材料相比,这对锂离子电池电极来说尤其具有挑战性。
特斯拉的干电极工艺更简单,不需要使用溶剂。该过程从电极粉末开始,其中少量(约5-8%)精细的聚四氟乙烯(PTFE)粘合剂与阴极粉末混合。然后将阴极粉末和粘合剂的混合物挤出,形成薄的电极材料条。这种挤压的电极材料条层压到金属箔集流体上,以产生最终的电极。干法工艺提高了电极制造的效率,缩短了加工步骤,为储能电池的大规模生产开辟了新的可能性。
简化的制造工艺和电池结构
锂电池制造的各个过程中使用的设备都会显着影响电池性能。电池工艺流程的长度也会影响电池制备的一致性和可控性。电极制造和电池形成工艺的简化就是一个成功的例子。集成压延和分切机、激光切割和卷绕机以及激光切割和堆垛机等设备的发展简化了流程并增强了闭环控制能力。这种简化不仅降低了由于路线复杂而导致的物料运输成本,还节省了劳动力。
在电池行业的未来发展中,电池性能的优化和制造结构将发生革命性的变化。这包括根据性能、制造和连接要求更改电池外壳形状、尺寸和电极连接。内部集流体和电极连接也可能发生变化,以满足电池回收要求。
宁德时代和比亚迪都采用了不同的方法来简化他们的流程。他们利用不同形式的CTP(Cell to Pack)来缩短工艺流程。CTP是指跳过组件阶段,直接将电芯集成到电池组中,以提高体积利用率。在宁德时代的CTP电池组中,有多个电池模块,每个模块都包含多个电池单元和一个容纳这些电池单元的框架。他们用较大的模块取代了较小的模块。比亚迪的CTP,也称为GCTP(Blade Battery),实现了更高水平的模块消除,其中Blade电池组仅使用单个大型模块。CATL-CTP和BYD-CTP工艺的比较见下表。
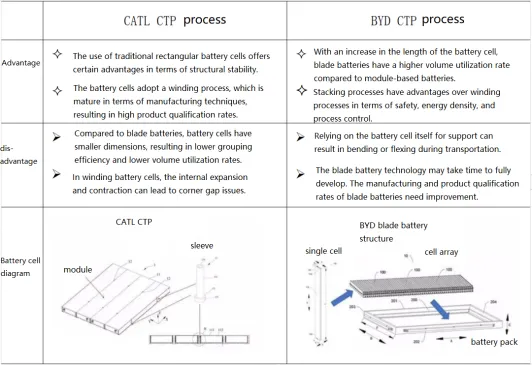
新能源应用领域对锂离子电池的需求不断扩大。领先的锂离子电池公司旨在通过持续的产能扩张来实现规模经济和降低成本。他们对生产线的流程、性能和生产效率有更高的要求。锂离子设备在提高锂离子制造的工艺效率、良率和生产效率方面发挥着至关重要的作用。创新能力是电池制造过程的核心竞争力。锂离子设备的持续改进和迭代,以及锂离子制造技术的进一步突破,都需要密切合作。