Durante la última década, la industria de las baterías de iones de litio ha pasado de la automatización semiautomática a la independiente, y luego gradualmente hacia la automatización y la inteligencia completas. A lo largo de este proceso, ha habido cambios importantes mínimos en los procesos de fabricación de baterías. Sin embargo, con el crecimiento continuo y rápido de la demanda de baterías, que supera el 100% anual, y las actualizaciones continuas en los sistemas de materiales de baterías, es inevitable que los procesos de fabricación de baterías deban actualizarse para adaptarse a los cambios en la escala de fabricación y los sistemas de baterías. En consecuencia, los equipos de baterías, como la "gallina madre" de la industria de las baterías de iones de litio, también han encontrado nuevas oportunidades para los avances.
Tendencias de desarrollo de tecnología y equipos de fabricación
En el futuro, la tendencia de desarrollo de las baterías de almacenamiento de energía cambiará hacia una mayor capacidad de celdas pequeñas individuales. Los equipos de iones de litio deben garantizar la precisión en la fabricación de estas grandes celdas, una alta eficiencia de fabricación y mejorar la compatibilidad y la escalabilidad. Esto requiere mejoras correspondientes en la precisión de mecanizado de los componentes y la precisión de ensamblaje de los módulos.
Para abordar los desafíos de la fabricación de baterías de iones de litio a gran escala, es necesario mejorar la eficiencia de los equipos.La eficiencia de producción de los equipos de iones de litio se mejora principalmente desde dos aspectos. En primer lugar, aumentando la velocidad de producción de los equipos utilizando estructuras y métodos de control más rápidos y estables. En segundo lugar, reduciendo el tiempo consumido por los movimientos de los equipos, conocido como tiempo auxiliar.
Por ejemplo, la máquina de bobinado continuo para separadores desarrollada por Geesun Intelligent es un equipo típico. Anteriormente, cada celda aceleraba y se alimentaba a la velocidad de bobinado más alta, luego desaceleraba, se detenía, se cortaba el separador, se enhebraba la aguja y se pasaba al siguiente bobinado de la celda. Después de la mejora, el separador no se desacelera y se utiliza un mecanismo de corte volador para cortar el separador, lo que se hace con anticipación durante el proceso de desaceleración del electrodo. Esto reduce el tiempo consumido por el proceso de corte del electrodo y el separador, minimizando efectivamente el tiempo auxiliar a casi cero, lo que resulta en una mejora del tiempo del ciclo de producción general del 30-60% (dependiendo de la longitud del electrodo). Otro ejemplo es la máquina de corte de lengüetas de electrodos, que ha aumentado su velocidad de corte por láser de los 80-120 m/min anteriores a 200 m/min.
Desde esta perspectiva, el avance y la iteración de los equipos de fabricación de iones de litio se está moviendo hacia soluciones inteligentes a gran escala, de alta precisión, alta confiabilidad y totalmente integradas.
Desde la perspectiva de la optimización de los procesos de fabricación de iones de litio, los equipos integrados y totalmente inteligentes ofrecen una mayor estabilidad de producción, una mayor automatización y una mayor adaptabilidad a los procesos de fabricación. También ayuda a las empresas manufactureras a reducir los costos de mano de obra y espacio, acortar los enlaces de los procesos y minimizar el desperdicio de materiales, desempeñando un papel clave en la mejora de la eficiencia general.
Integración profunda de la tecnología de materiales y la tecnología de fabricación
A lo largo del proceso de fabricación de baterías, implica la transición de las operaciones de procesamiento de materiales a nanoescala a la producción y el procesamiento de dispositivos a escala métrica. En el pasado, la fabricación de iones de litio se centraba principalmente en controlar la eficiencia de fabricación, la calidad y el costo de los equipos basados en la mecánica newtoniana. Los principales parámetros controlados fueron las posiciones físicas, las velocidades, las aceleraciones, las inercias, la fricción y la resistencia de los materiales. Estos controles eran relativamente macroscópicos, y la visibilidad y observabilidad del proceso eran relativamente fáciles de gestionar.
Partiendo de la base de que las baterías implican la migración de iones bajo la influencia de un campo eléctrico interno, mientras que externamente, el proceso se refleja en la transferencia de electrones, es necesario controlar la producción y el uso de las baterías desde una perspectiva microscópica utilizando la mecánica cuántica. Esto implica considerar la evolución de la estructura y composición de la batería durante la producción y el ensamblaje, así como los comportamientos de transporte de electrones e iones, los problemas de interfaz y el efecto de la escala de rendimiento en las baterías. Los cambios en la interfaz durante el proceso de carga-descarga, las variaciones de rendimiento y escala, y los efectos de acoplamiento entre las moléculas internas y los iones, los efectos de la temperatura y los cambios en la forma y el volumen deben tenerse en cuenta para controlar la seguridad de la batería, la autodescarga, la vida útil, la densidad de energía y la densidad de potencia.
Esto requiere una mayor consideración de la termodinámica, la cinética (cinética de transporte de iones, cinética de transferencia de carga, cinética de reacción, cinética de transición de fase, etc.) y la estabilidad en el proceso de fabricación desde una perspectiva microscópica.
Sin embargo, el control de estos complejos procesos carece actualmente de un modelo teórico completo en el campo de la fabricación. Esto se debe a los desafíos inherentes al acoplamiento de campos multifísicos, los datos heterogéneos y multielementos, el control de formas a múltiples escalas, el control de las propiedades intrínsecas y la gestión de datos masivos. Los métodos que se pueden emplear incluyen el aprendizaje automático y el modelado de optimización basado en el análisis de tendencias cualitativas y el modelado de big data. Mediante el uso de la teoría de la mecánica cuántica para comprender los principios científicos intrínsecos dentro de las baterías, se puede lograr la optimización de procesos, la toma de decisiones y el control. Se pueden establecer métodos analíticos y técnicas de evaluación para lograr una fabricación de baterías reconfigurable, a gran escala y personalizada. En última instancia, este enfoque puede abordar problemas como la migración de iones, la generación y transferencia de calor, el control de la presión interna, la deformación del proceso, la formación de películas SEI y el control de dendritas de litio.
Integración de la fabricación y cambios en los principios de fabricación
La discusión anterior se centró en los aspectos microscópicos a tener en cuenta en la fabricación de baterías desde una perspectiva cuántica. En el contexto de las reacciones electroquímicas acopladas en las baterías de iones de litio, que involucran múltiples campos físicos, se puede lograr una cuantificación de los procesos electroquímicos de la batería utilizando variables de estado generalizadas como números adimensionales, densidad de partículas, densidad de defectos de red, velocidad de partículas, etc.
Mediante el empleo de técnicas de simulación numérica de dinámica de partículas lisas multidireccionales, se pueden desarrollar modelos numéricos que consideren la microestructura de mesoescala de los electrodos. Estos modelos pueden simular el campo de concentración de iones, el campo de potencial sólido-líquido, la densidad de la corriente de conversión y otros detalles microscópicos en la batería durante el proceso de descarga. Además, pueden analizar y revelar los mecanismos fisicoquímicos fundamentales de los procesos de carga-descarga de la batería y su correlación con el rendimiento macroscópico de la batería, incluidos factores como el voltaje de salida y el tamaño de partícula de los materiales activos sólidos que constituyen los electrodos.
La fabricación de electrodos secos, guiada por los principios de la dinámica de partículas a mesoescala, implica la integración de procesos como la fabricación de electrodos, la mezcla, la agitación, el recubrimiento, el secado y el laminado. La integración del corte y el bobinado por láser, así como el corte y el apilamiento por láser en un solo equipo, es una tendencia importante. En el futuro, prevemos que la producción de celdas de batería puede requerir solo tres tipos principales de equipos: equipos de producción de electrodos, equipos de ensamblaje y equipos de prueba. Sin embargo, este es un escenario ideal que requiere esfuerzos conjuntos y avances en materiales, procesos y equipos. No se puede lograr de la noche a la mañana, y requerirá los esfuerzos dedicados y la diligencia de los profesionales de la fabricación de baterías.
El proceso principal para la preparación de electrodos secos (también conocido como "recubrimiento seco") incluye la selección de aglutinantes no fibrados, el molienda de bolas de aglutinantes no fibrados para la granulación y la mezcla de aglutinantes no fibrados, aglutinantes fibrados y materiales activos de electrodos (cátodo/ánodo) antes del calandrado. Para garantizar la plasticidad de los materiales, la mezcla a menudo se calienta a temperaturas superiores a 100 °C durante el proceso de conformado.
Los aglutinantes no fibrosados utilizados por Maxwell incluyen fluoruro de polivinilideno y carboximetilcelulosa, mientras que el aglutinante fibradizado utilizado principalmente es el politetrafluoroetileno. El procesamiento paralelo se emplea comúnmente en sus procesos de fabricación. Consulte la figura a continuación para obtener una ilustración del proceso de fabricación de electrodos secos de Tesla.
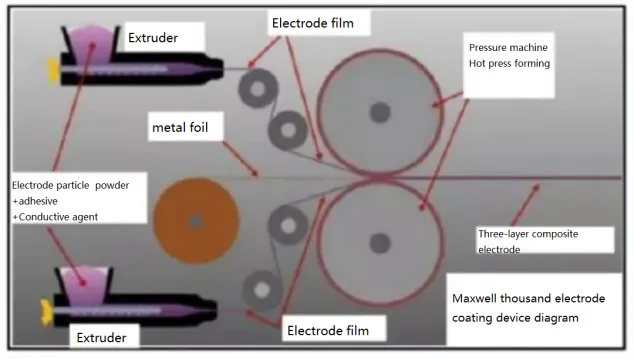
En comparación con los procesos tradicionales de electrodos húmedos, el proceso de electrodos secos utilizado por Tesla (Maxwell) ofrece varias ventajas. Sustituye la agitación por la molienda de bolas y el recubrimiento por calandrado, eliminando el proceso de secado después del recubrimiento húmedo. Este método puede ahorrar solventes, reducir el tiempo de procesamiento, evitar residuos de solventes y reducir la complejidad del equipo. Sin embargo, el proceso seco tiene sus limitaciones, particularmente para lograr una dispersión uniforme de los materiales activos, lo que es especialmente desafiante para los electrodos de batería de iones de litio en comparación con los materiales de los electrodos de supercondensador.
El proceso de electrodo seco de Tesla es aún más sencillo y no requiere el uso de disolventes. El proceso comienza con polvo de electrodo, donde se mezcla una pequeña cantidad (aproximadamente 5-8%) de aglutinante fino de politetrafluoroetileno (PTFE) con el polvo de cátodo. A continuación, la mezcla de polvo de cátodo y aglutinante se extruye para formar una tira fina de material de electrodo. Esta tira de material de electrodo extruido se lamina sobre un colector de corriente de lámina metálica para producir el electrodo final. El proceso seco mejora la eficiencia de la fabricación de electrodos, acorta los pasos de procesamiento y abre nuevas posibilidades para la producción a gran escala de baterías de almacenamiento de energía.
Proceso de fabricación y estructura de la batería simplificados
El equipo utilizado en cada proceso de fabricación de baterías de litio afecta significativamente el rendimiento de la batería. La longitud del flujo del proceso de la batería también afecta a la consistencia y la capacidad de control de la preparación de las celdas. La simplificación de los procesos de fabricación de electrodos y formación de células es un ejemplo exitoso. El desarrollo de equipos como máquinas integradas de calandrado y corte longitudinal, máquinas de corte y bobinado por láser, y máquinas de corte y apilamiento por láser ha simplificado los procesos y mejorado la capacidad de control de circuito cerrado. Esta simplificación no solo reduce el costo del transporte de materiales debido a las complejas rutas, sino que también ahorra mano de obra.
En el desarrollo futuro de la industria de las baterías, habrá cambios revolucionarios en la optimización del rendimiento de las baterías y las estructuras de fabricación. Esto incluye cambios en la forma, el tamaño y las conexiones de los electrodos de la carcasa de la batería en función de los requisitos de rendimiento, fabricación y conectividad. Los colectores de corriente internos y las conexiones de los electrodos también pueden cambiar para cumplir con los requisitos de reciclaje de la batería.
Tanto CATL como BYD han adoptado diferentes enfoques para agilizar sus procesos. Utilizan diferentes formas de CTP (Cell to Pack) para acortar el flujo del proceso. CTP se refiere a saltarse la etapa del módulo e integrar directamente las celdas de la batería en el paquete para aumentar la utilización del volumen. En el paquete de baterías CTP de CATL, hay varios módulos de batería, cada uno de los cuales contiene varias celdas y un marco para acomodar estas celdas. Han sustituido los módulos más pequeños por otros más grandes. El CTP de BYD, también conocido como GCTP (Blade Battery), logra niveles aún más altos de eliminación de módulos, donde el paquete de baterías blade solo usa un solo módulo grande. Consulte la tabla a continuación para ver una comparación de los procesos CATL-CTP y BYD-CTP.
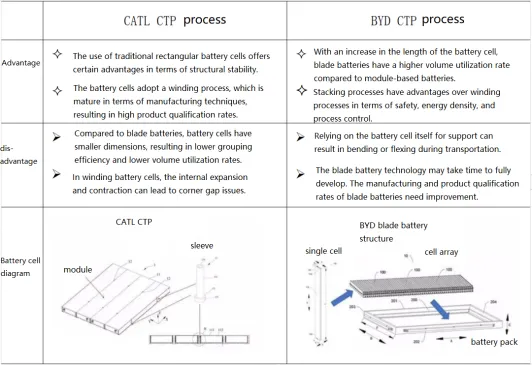
La demanda de baterías de iones de litio en el campo de las nuevas aplicaciones energéticas sigue creciendo. Las principales empresas de baterías de iones de litio tienen como objetivo lograr economías de escala y reducir los costos a través de la expansión continua de la capacidad. Tienen requisitos más altos para los procesos de la línea de producción, el rendimiento y la eficiencia de la producción. Los equipos de iones de litio desempeñan un papel crucial en la mejora de la eficiencia del proceso, las tasas de rendimiento y la eficiencia de la producción en la fabricación de iones de litio. La capacidad de innovación es la competencia central de los procesos de fabricación de baterías. La mejora continua y la iteración de los equipos de iones de litio, junto con nuevos avances en la tecnología de fabricación de iones de litio, requieren una estrecha colaboración.