锂离子电池通常串联或并联组合成一个动力电池组,以满足性能要求。随着单个电池数量的增加,电池一致性问题变得更加突出。电池的不一致会导致一系列问题,例如电池寿命缩短、性能下降和电池组安全性受损。单个电池的不一致主要源于制造或储存过程以及使用过程。
在生产过程中,通常通过控制制造过程的准确性来间接减少不一致。但是,这只能最小化初始参数差异,而不能完全消除它们。电池的一致性表现出传递性和累积性,因为它受多种相互作用因素的影响。在使用过程中,即使是初始参数的微小差异也会被大大放大。
为了改善这种情况,我们可以从电池生产、电池分类、电池平衡和动力电池组的热管理等各个方面采取综合方法。本文分享了全极耳棱柱绕组锂离子动力电池生产过程的测试数据,并分析了它们的一致性。
电池的具体设计和生产工艺如下:电池的正极材料采用三元系统,而负极采用人造石墨。电池以绕组方式组装并封装在铝制外壳中。电极片、缠绕果冻卷和电池组装的过程如图1所示。
在全极耳电池的绕组过程中,电极片和隔膜的布置如图1所示。在施加正极材料(30)时未涂层的正极片(15)的侧边和在施加负极材料(40)时负极片的空白面(14)分别焊接在正负集流体上作为耳片。正负极片由隔板(170)隔开,正负极集流体暴露在卷绕果冻卷的两侧,直接连接到电池的正负极。
通过从极耳的角度改善功率特性,缩短了电流流距离,从而在高放电倍率下实现均匀的电流密度分布,从而实现高功率密度并减少电极片的发热。
组装顶盖后,将带空白集流体的正极片焊接到正母线上,将带空白集流体的负极片用激光焊接或电阻焊到负极母线上。当设计容量较大时,可并联两个收卷果冻卷。在焊接过程中,可以先将多个收卷果冻卷并联,然后再焊接在一起,也可以将每个收卷果冻卷单独焊接,然后在激光焊接后将多个收卷果冻卷并联。
将带有绝缘涂膜焊接片的卷绕果冻卷插入外壳中,并使用激光焊接将顶盖和外壳焊接在一起。电池干燥后,加注电解液并预充电。电池的开口用密封钉密封,盖上铝密封塞,然后将密封塞焊接到电池顶盖上,使电芯完全密封。
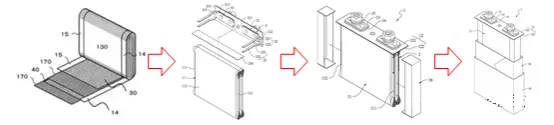
电极片生产的一致性
正极和负极片材采用狭缝模头挤压涂布技术进行涂布,使用液压伺服轧机进行恒定辊隙模式压延。
在电极涂布和压延过程中,将长度约为500m的电极片收集成卷,并作为批次进行初步和最终检查。采样器切割直径为φ60mm的圆形样品,并测量电极片的重量和厚度。计算电极片的表面密度和致密密度,每批次采集3个样品进行测试和数据计算。
正极片的测试数据如图2和图3所示。电极片两侧的平均表面密度为36.89 mg/cm2,表明涂层稳定性良好。电极片的压延通过控制电极片的厚度来确定涂层的致密密度。压延后,正极的致密密度控制在3.00 g/cm3,厚度波动最小,稳定性好。
正极片的测试数据如图2和图3所示。电极片两侧的平均表面密度为36.89 mg/cm2,表明涂层稳定性良好。电极片的压延通过控制电极片的厚度来确定涂层的致密密度。压延后,正极的致密密度控制在3.00 g/cm3,厚度波动最小,稳定性好。
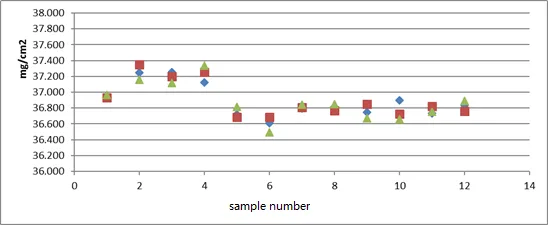
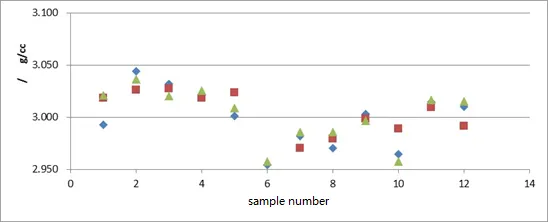
负极片的测试数据如图4和图5所示。电极片两侧的平均表面密度为16.13 mg/cm2,表明涂层稳定性良好。电极片的压延通过控制电极片的厚度来确定涂层的致密密度。压延后,负极的致密密度控制在1.62 g/cm3,厚度波动最小,稳定性好。最后,表1总结了正极和负极片的表面密度和致密密度的范围、平均值和标准偏差。

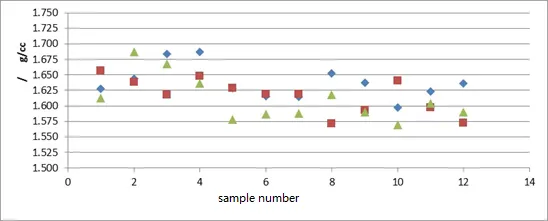
表1:正负极片的表面密度和紧凑密度
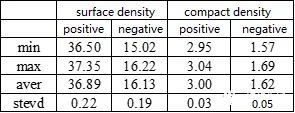
收卷后,果冻卷需要进行广泛的测试以确保产品质量,包括:
(1)电芯尺寸,包括高度、宽度、厚度、磁带宽度和位置、极耳收集器对齐等。这些尺寸可以直接测量,与绕线工艺和设备精度有关。
(2)电极片和隔板的长度。
(3)电极片的宽度。在宽度方向上,负极需要超过正极一定的幅度,隔膜需要超过负极一定的幅度。宽度方向的对齐方式直接由卷绕过程的精度决定。当精度较高时,裕量尺寸可以更小,从而使电池的能量密度更高。然而,电池的安全裕度会降低,因此确保工艺精度以避免重大安全风险至关重要。电池中每一层电极片的对齐通常是通过对电池的所有四个角进行X射线检查来实现的。当正负极之间的相对宽度尺寸不符合要求时,设备会自动报警并剔除不良品。
(4)果冻卷质量。
(5)电极片上的毛刺。用于电极片切割的切割刀会随着时间的推移而磨损,从而影响切割质量。因此,需要对切割刀的使用寿命进行管理,并需要定期检查切割质量以避免毛刺。观察毛刺的典型过程是取切割电极片,在光学显微镜下检查切割表面,以检测毛刺的存在。毛刺的控制标准一般是毛刺尺寸应小于分离器厚度的一半。但是,一些制造商有更严格的控制要求,其中毛刺不应超过涂层。
(6)果冻卷中的其他内部缺陷,如电极片弯曲、涂层取向、异物等。
果冻卷质量选择的分析如图6中的数据直方图所示。使用收集的果冻卷数据处理直方图,以反映产品质量的分布,从而可以评估和预测产品质量和不合格率。在分析统计数据时,根据不同的范围将数据分为几组,组数称为bin数。果冻卷质量分布呈正态分布,平均质量为179.86g。在177.955-178.155g的质量范围内有较多的果冻卷,偏离正态分布。
在电极片的加工过程中,会在有缺陷的片材上进行标记,例如单面涂层或外露的箔片,并在卷绕过程中去除这些有缺陷的片材。然而,有缺陷的片材仍然偶尔会出现在果冻卷中。对果冻卷进行质量检查并去除不合格产品可以进一步确保产品质量。
质量检查结果异常的主要原因是在电极片加工过程中产生不良片材,例如涂层不一致、单面涂层以及电极片上存在胶带缺陷。
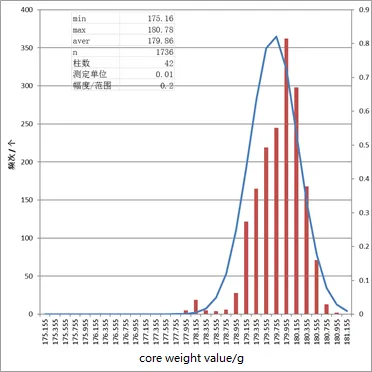
进行了部分果冻卷拆解破坏性试验,主要分析了正极、负极和隔膜的长度数据。具体结果如图7所示,正极长度约为2.20 m,负极长度约为2.37 m。为了使来自正极的锂离子扩散并容纳在负极晶格中,负极必须以一定大小的余量完全包围正极。此外,为了防止短路,隔膜必须封装负极。在绕线电池的长度方向上,必须确保负极与正极相比具有余量,并且隔膜必须包围负极。电极片的相对位置至关重要,包括隔膜长度、与负极的相对尺寸以及正负极之间的相对位置等参数。这些尺寸受电极涂层规格、绕组工艺和其他因素的影响。
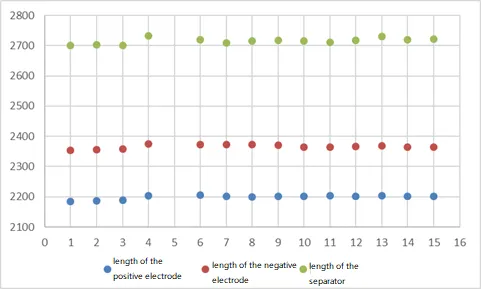
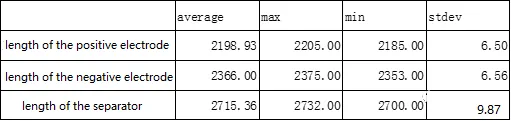
电池组装好后,进行充放电测试电池的容量、直流内阻等参数。容量分布是电池所有过程影响因素的累积。该参数可用于分析电池的一致性,并整合所有过程的误差。电池容量分布如图8和表2所示。过程能力是过程在稳定状态下保证产品质量的能力。它受到操作人员、机器设备、原材料、工艺方法、过程中工作环境等因素的综合影响和制约。体现在产品质量是否稳定和产品质量精度是否足够两个方面。如图9所示,基于电池容量数据,综合分析电池生产过程能力,CP=1.085,电池产能满足要求。
工艺能力测定:
1.CP>1.33.当Cp>1.33时,表示过程能力足够。此时,需要控制工艺的稳定性,以防止工艺能力发生重大变化。如果认为工艺能力过大,则应分析标准要求和工艺条件。一方面可以降低要求,避免设备精度的浪费。另一方面,也可以修订标准以提高产品质量。
2. 1.0
3. 0.67
4.Cp≤0.67.当过程能力指数小于0.67时,表明过程能力严重不足,必要时必须停止工作进行整改。
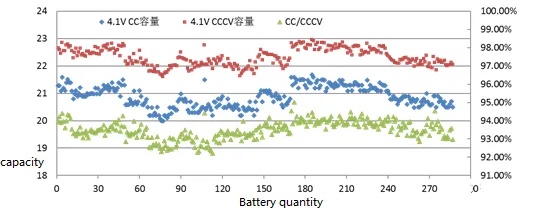
表2电池容量分布数据
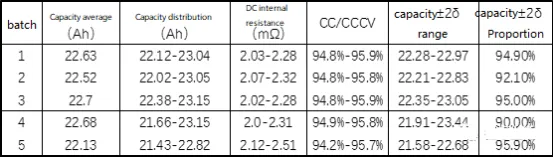
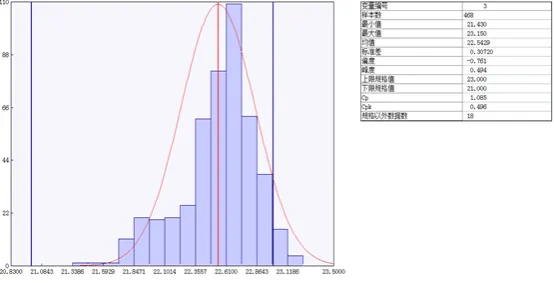