Les batteries lithium-ion sont généralement combinées en série ou en parallèle pour former une batterie d’alimentation afin de répondre aux exigences de performance. À mesure que le nombre de batteries individuelles augmente, la question de la cohérence des batteries devient plus importante. L’incohérence des batteries peut entraîner une série de problèmes tels que la réduction de la durée de vie de la batterie, la diminution des performances et la sécurité de la batterie. L’incohérence des batteries individuelles provient principalement du processus de fabrication ou de stockage ainsi que du processus d’utilisation.
Au cours du processus de production, les incohérences sont souvent indirectement réduites en contrôlant la précision du processus de fabrication. Cependant, cela ne peut que minimiser les différences de paramètres initiales et ne peut pas les éliminer complètement. La consistance des batteries présente une transitivité et une cumulativité, car elle est influencée par de multiples facteurs en interaction. Même de légères différences dans les paramètres initiaux peuvent être considérablement amplifiées pendant l’utilisation.
Pour améliorer cette situation, nous pouvons adopter une approche combinée de divers aspects tels que la production de batteries, le tri des batteries, l’équilibrage des batteries et la gestion thermique de la batterie d’alimentation. Cet article partage les données de test du processus de production des batteries lithium-ion à enroulement prismatique et analyse leur consistance.
La conception et le processus de production spécifiques de la batterie sont les suivants : le matériau de l’électrode positive de la batterie utilise un système ternaire, tandis que l’électrode négative utilise du graphite artificiel. La batterie est assemblée de manière enroulée et enfermée dans une coque en aluminium. Le processus de laminage des feuilles d’électrodes, de l’enroulement des rouleaux de gelée et de l’assemblage de la batterie est illustré à la figure 1.
Lors de l’enroulement de la batterie à languette toute, la disposition des feuilles d’électrodes et des séparateurs est comme le montre la figure 1. Les bords latéraux de la feuille d’électrode positive (15) sans revêtement lors de l’application du matériau d’électrode positive (30) et le côté vierge (14) de la feuille d’électrode négative lors de l’application d’un matériau d’électrode négative (40) sont respectivement soudés en tant qu’embouts auriculaires sur les collecteurs de courant positif et négatif. Les feuilles d’électrode positive et négative sont séparées par un séparateur (170), et les collecteurs de courant positif et négatif sont exposés des deux côtés du rouleau de gelée d’enroulement, directement connectés aux électrodes positive et négative de la batterie.
En améliorant les caractéristiques de puissance du point de vue des languettes, la distance de flux de courant est raccourcie, ce qui permet une distribution uniforme de la densité de courant à des taux de décharge élevés, ce qui permet une densité de puissance élevée et réduit la génération de chaleur à partir des feuilles d’électrodes.
Après avoir assemblé le capot supérieur, la languette d’électrode positive avec collecteur de courant vierge est soudée au jeu de barres positif, et la languette d’électrode négative avec collecteur de courant vierge est soudée au jeu de barres négatif à l’aide du soudage au laser ou du soudage par résistance. Lorsque la capacité nominale est grande, deux rouleaux de gelée d’enroulement peuvent être connectés en parallèle. Au cours du processus de soudage, plusieurs rouleaux de gelée d’enroulement peuvent d’abord être assemblés en parallèle, puis soudés ensemble, ou chaque rouleau de gelée d’enroulement peut être soudé individuellement, puis plusieurs rouleaux de gelée d’enroulement sont connectés en parallèle après le soudage au laser.
Les rouleaux de gelée d’enroulement avec des languettes soudées isolées recouvertes d’un film sont insérés dans le boîtier, et le couvercle supérieur et le boîtier sont soudés ensemble à l’aide d’un soudage laser. Une fois la batterie sèche, elle est remplie d’électrolyte et préchargée. L’ouverture de la batterie est scellée à l’aide d’un clou d’étanchéité, recouverte d’un bouchon d’étanchéité en aluminium, puis le bouchon d’étanchéité est soudé sur le couvercle supérieur de la batterie pour sceller complètement la cellule.
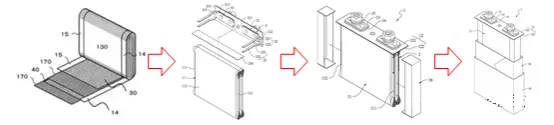
Cohérence dans la production de feuilles d’électrodes
Les feuilles d’électrodes positives et négatives sont revêtues à l’aide d’une technique de revêtement par extrusion de matrice à fente, avec un calandrage en mode d’écart de rouleau constant à l’aide d’un laminoir à servo hydraulique.
Au cours du processus de revêtement et de calandrage des électrodes, des feuilles d’électrodes d’une longueur d’environ 500 m sont collectées sous forme de rouleau et subissent des inspections initiales et finales en tant que lot. Un échantillonneur coupe des échantillons circulaires d’un diamètre de φ60 mm, et le poids et l’épaisseur des feuilles d’électrodes sont mesurés. La densité de surface et la densité compacte des feuilles d’électrodes sont calculées, avec 3 échantillons prélevés pour les tests et le calcul des données par lot.
Les données d’essai des feuilles d’électrodes positives sont illustrées à la figure 2 et à la figure 3. La densité de surface moyenne des feuilles d’électrodes des deux côtés est de 36,89 mg/cm2, ce qui indique une bonne stabilité du revêtement. Le calandrage des feuilles d’électrodes détermine la densité compacte du revêtement en contrôlant l’épaisseur des feuilles d’électrodes. Après le calandrage, la densité compacte de l’électrode positive est contrôlée à 3,00 g/cm3, avec des fluctuations d’épaisseur minimales et une bonne stabilité.
Les données d’essai des feuilles d’électrodes positives sont illustrées à la figure 2 et à la figure 3. La densité de surface moyenne des feuilles d’électrodes des deux côtés est de 36,89 mg/cm2, ce qui indique une bonne stabilité du revêtement. Le calandrage des feuilles d’électrodes détermine la densité compacte du revêtement en contrôlant l’épaisseur des feuilles d’électrodes. Après le calandrage, la densité compacte de l’électrode positive est contrôlée à 3,00 g/cm3, avec des fluctuations d’épaisseur minimales et une bonne stabilité.
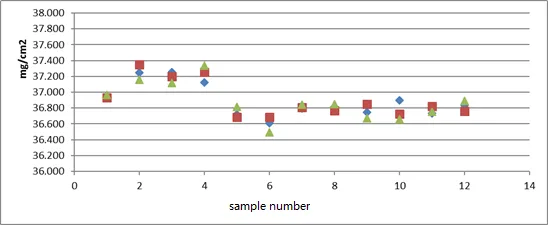
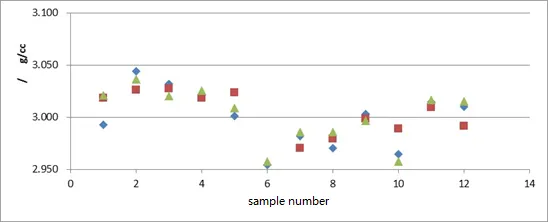
Les données d’essai des feuilles d’électrodes négatives sont illustrées à la figure 4 et à la figure 5. La densité moyenne de surface des feuilles d’électrodes des deux côtés est de 16,13 mg/cm2, ce qui indique une bonne stabilité du revêtement. Le calandrage des feuilles d’électrodes détermine la densité compacte du revêtement en contrôlant l’épaisseur des feuilles d’électrodes. Après calandrage, la densité compacte de l’électrode négative est contrôlée à 1,62 g/cm3, avec des fluctuations d’épaisseur minimales et une bonne stabilité. Enfin, les plages, les moyennes et les écarts-types de la densité de surface et de la densité compacte pour les feuilles d’électrodes positives et négatives sont résumés dans le tableau 1.

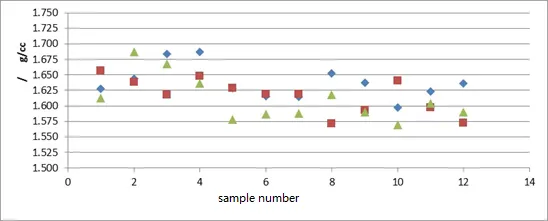
Tableau 1 : Densité de surface et densité compacte des feuilles d’électrodes positives et négatives
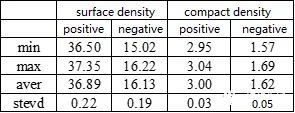
Après l’enroulement, le rouleau de gelée nécessite des tests approfondis pour garantir la qualité du produit, notamment :
(1) Dimensions des cellules, y compris la hauteur, la largeur, l’épaisseur, la largeur et la position du ruban, l’alignement des collecteurs d’onglets, etc. Ces dimensions peuvent être mesurées directement et sont liées au processus d’enroulement et à la précision de l’équipement.
(2) Longueur des feuilles d’électrodes et des séparateurs.
(3)Largeur des feuilles d’électrodes. Dans le sens de la largeur, l’électrode négative doit dépasser l’électrode positive d’une certaine marge, et le séparateur doit dépasser l’électrode négative d’une certaine marge. L’alignement dans le sens de la largeur est directement déterminé par la précision du processus d’enroulement. Lorsque la précision est élevée, les dimensions de la marge peuvent être plus petites, ce qui entraîne une densité d’énergie plus élevée de la batterie. Cependant, la marge de sécurité de la batterie diminue et il est crucial d’assurer la précision du processus pour éviter des risques de sécurité importants. L’alignement de chaque couche de feuilles d’électrodes dans la cellule est généralement réalisé par une inspection par rayons X des quatre coins de la cellule. Lorsque la dimension de largeur relative entre les électrodes positives et négatives ne répond pas aux exigences, l’équipement déclenche automatiquement l’alarme et rejette les produits défectueux.
(4) Qualité du rouleau de gelée.
(5) Meules sur les feuilles d’électrodes. Le couteau de coupe utilisé pour la découpe de feuilles d’électrodes peut subir une usure au fil du temps, affectant la qualité de coupe. Par conséquent, le couteau de coupe doit être géré pour sa durée de vie et des inspections régulières de la qualité de coupe doivent être effectuées pour éviter les bavures. Le processus typique d’observation des bavures consiste à prendre une feuille d’électrode coupée et à examiner la surface coupée au microscope optique pour détecter la présence de bavures. La norme de contrôle pour les bavures est généralement que la taille de la bavure doit être inférieure à la moitié de l’épaisseur du séparateur. Cependant, certains fabricants ont des exigences de contrôle plus strictes, où les bavures ne doivent pas dépasser le revêtement.
(6) Autres défauts internes dans le rouleau de gelée, tels que le pliage de la feuille d’électrode, l’orientation du revêtement, les corps étrangers, etc.
L’analyse de la sélection de la qualité des rouleaux de gelée est illustrée dans l’histogramme des données de la figure 6. L’histogramme est traité à l’aide des données collectées pour refléter la distribution de la qualité du produit, ce qui permet d’évaluer et de prédire la qualité du produit et les taux de non-conformité. Lors de l’analyse des données statistiques, les données sont divisées en plusieurs groupes en fonction de différentes plages, et le nombre de groupes est appelé nombre de groupes. La distribution de la qualité du jelly roll suit une distribution normale, avec une masse moyenne de 179,86 g. Il y a une plus grande quantité de rouleaux de gelée dans la gamme de masse de 177,955 à 178,155 g, s’écartant de la distribution normale.
Lors de l’usinage des feuilles d’électrodes, des marquages sont effectués sur des feuilles défectueuses présentant des problèmes tels qu’un revêtement unilatéral ou une feuille exposée, et ces feuilles défectueuses sont éliminées pendant le bobinage. Cependant, des feuilles défectueuses apparaissent encore occasionnellement dans le rouleau de gelée. La réalisation d’inspections de qualité sur les rouleaux de gelée et l’élimination des produits non conformes peuvent garantir davantage la qualité du produit.
La principale cause de résultats anormaux d’inspection de la qualité est la génération de feuilles défectueuses lors du traitement des feuilles d’électrodes, telles que des incohérences de revêtement, un revêtement unilatéral et la présence de défauts de ruban sur les feuilles d’électrodes.
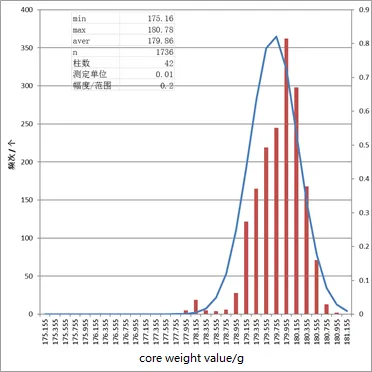
Des tests destructifs de démontage partiel ont été effectués, analysant principalement les données de longueur de l’électrode positive, de l’électrode négative et du séparateur. Les résultats spécifiques sont illustrés à la figure 7, avec une longueur d’électrode positive d’environ 2,20 m et une longueur d’électrode négative d’environ 2,37 m. Pour que les ions lithium de l’électrode positive se diffusent et soient logés dans le réseau d’électrode négative, l’électrode négative doit entourer entièrement l’électrode positive d’une certaine marge de taille. De plus, pour éviter les courts-circuits, le séparateur doit encapsuler l’électrode négative. Dans le sens de la longueur de la cellule enroulée, il est nécessaire de s’assurer que l’électrode négative a une marge par rapport à l’électrode positive, et le séparateur doit entourer l’électrode négative. Le positionnement relatif des feuilles d’électrode est crucial, y compris des paramètres tels que la longueur du séparateur, les dimensions relatives à l’électrode négative et le positionnement relatif entre les électrodes positives et négatives. Ces dimensions sont influencées par les spécifications de revêtement de l’électrode, les processus d’enroulement et d’autres facteurs.
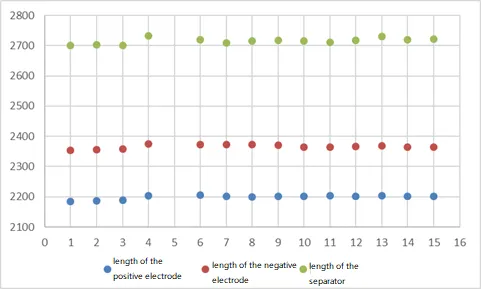
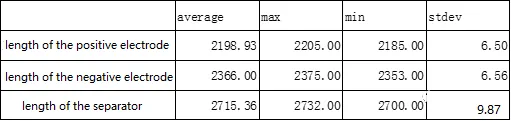
Une fois la batterie assemblée, chargez et déchargez pour tester la capacité de la batterie, la résistance interne CC et d’autres paramètres. La distribution de capacité est l’accumulation de tous les facteurs influençant le processus de la batterie. Ce paramètre peut être utilisé pour analyser la consistance de la batterie et intégrer les erreurs de tous les processus. La répartition de la capacité de la batterie est illustrée à la figure 8 et au tableau 2. La capabilité du processus est la capacité d’un processus à assurer la qualité du produit lorsqu’il est dans un état stable. Il est globalement affecté et limité par des facteurs tels que les opérateurs, les machines et les équipements, les matières premières, les méthodes de traitement et l’environnement de travail dans le processus. Cela se reflète dans deux aspects : si la qualité du produit est stable et si la précision de la qualité du produit est suffisante. Comme le montre la figure 9, sur la base des données de capacité de la batterie, la capacité de processus de production de batteries est analysée de manière exhaustive, CP = 1,085, et la capacité de production de la batterie répond aux exigences.
Détermination de la capabilité du processus :
1.Cp>1.33. Lorsque Cp>1.33, cela indique que la capabilité du processus est suffisante. À ce stade, il est nécessaire de contrôler la stabilité du procédé afin d’éviter des changements importants dans la capabilité du procédé. Si la capacité du processus est jugée trop importante, les exigences standard et les conditions du processus doivent être analysées. D’une part, les exigences peuvent être réduites pour éviter le gaspillage de la précision de l’équipement. D’autre part, les normes peuvent également être révisées pour améliorer la qualité des produits.
2. 1.0
3. 0,67
4.Cp≤0.67. Lorsque l’indice de capabilité du processus est inférieur à 0,67, cela indique que la capabilité du processus est gravement insuffisante et que le travail doit être arrêté pour être corrigé si nécessaire.
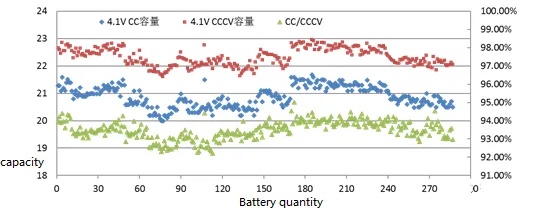
Tableau 2 Données de distribution de la capacité de la batterie
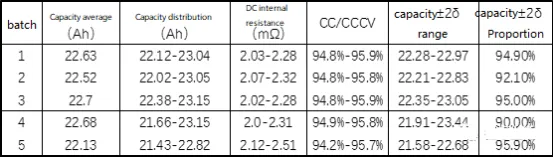
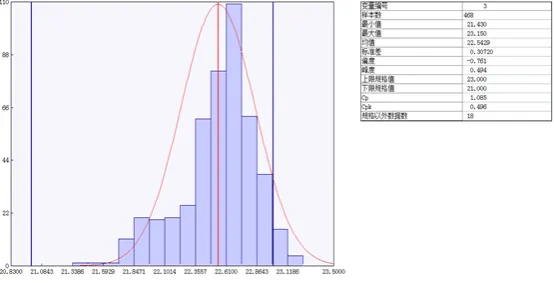