リチウムイオン電池は通常、性能要件を満たすために直列または並列に組み合わされてパワー電池パックを形成します。個々のバッテリーの数が増えると、バッテリーの一貫性の問題がより顕著になります。バッテリーの不整合は、バッテリーの寿命の短縮、パフォーマンスの低下、バッテリーパックの安全性の低下など、さまざまな問題を引き起こす可能性があります。個々のバッテリーの不整合は、主に製造または保管プロセスと使用プロセスに起因します。
製造工程では、製造工程の精度を制御することで、不整合が間接的に減少することがよくあります。しかし、これでは初期パラメータの違いを最小限に抑えるだけで、完全に排除することはできません。電池の一貫性は、複数の相互作用する要因の影響を受けるため、推移性と累積性を示します。初期パラメータのわずかな違いでも、使用中に大幅に拡大する可能性があります。
この状況を改善するために、バッテリーの製造、バッテリーの選別、バッテリーバランス、パワーバッテリーパックの熱管理など、さまざまな側面から組み合わせたアプローチを取ることができます。この記事では、オールタブプリズム巻線リチウムイオンパワーバッテリーの製造工程のテストデータを共有し、それらの一貫性を分析します。
バッテリーの具体的な設計と製造プロセスは次のとおりです:バッテリーの正極材料は三元系を使用し、負極は人工黒鉛を使用します。バッテリーは巻き取り方式で組み立てられ、アルミニウムシェルに包まれています。電極シート、巻きゼリーロール、およびバッテリーの組み立てのプロセスを図1に示します。
オールタブ電池の巻線中、電極シートとセパレータの配置は図1の通りである。正極材(30)を塗布した際のコーティングなしの正極シート(15)の側端と、負極材(40)を塗布した負極シートのブランク面(14)は、それぞれ正負の集電体にイヤータブとして溶接されている。正極シートと負極シートはセパレータ(170)で分離されており、正負の集電体は巻線ゼリーロールの両側に露出しており、バッテリーの正極と負極に直接接続されています。
タブの視点から電力特性を改善することで、電流流距離が短くなり、高放電率で均一な電流密度分布が得られるため、高電力密度が可能となり、電極シートからの発熱が低減されます。
トップカバーを組み立てた後、ブランク集電体付きの正極タブを正のバスバーに溶接し、ブランク集電体付きの負極タブをレーザー溶接または抵抗溶接を使用して負のバスバーに溶接します。設計容量が大きい場合は、2つの巻きゼリーロールを並列に接続できます。溶接プロセス中に、複数の巻線ゼリーロールを最初に並列に接続してから一緒に溶接するか、各巻線ゼリーロールを個別に溶接し、レーザー溶接後に複数の巻線ゼリーロールを並列に接続することができます。
絶縁フィルムコーティングされた溶接タブを備えた巻線ゼリーロールをケーシングに挿入し、トップカバーとケーシングをレーザー溶接で溶接します。バッテリーが乾燥した後、電解液が充填され、予備充電されます。バッテリーの開口部をシーリングネイルで密閉し、アルミニウムシーリングプラグで覆い、シーリングプラグをバッテリーの上部カバーに溶接してセルを完全に密閉します。
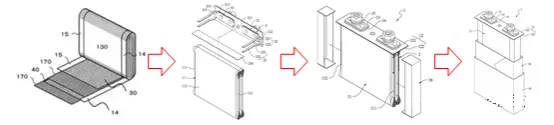
電極シート製造の一貫性
正極シートと負極シートは、スロットダイ押出コーティング技術を使用してコーティングされ、油圧サーボ圧延機を使用して一定のロールギャップモードカレンダーが塗布されます。
電極コーティングやカレンダー加工の工程では、長さ約500mの電極シートをロール状に集め、バッチとして初期検査と最終検査を行います。サンプラーで直径φ60mmの円形サンプルを切断し、電極シートの重量と厚さを測定します。電極シートの表面密度とコンパクト密度を算出し、1バッチあたり3つのサンプルを採取して試験とデータ計算を行います。
正極シートの試験データを図2と図3に示します。電極シートの両面の平均表面密度は36.89mg/cm2で、良好なコーティング安定性を示しています。電極シートのカレンダー加工は、電極シートの厚さを制御することにより、コーティングのコンパクト密度を決定します。カレンダー加工後、正極のコンパクト密度は3.00 g/cm3に制御され、厚さの変動は最小限に抑えられ、安定性は良好です。
正極シートの試験データを図2と図3に示します。電極シートの両面の平均表面密度は36.89mg/cm2で、良好なコーティング安定性を示しています。電極シートのカレンダー加工は、電極シートの厚さを制御することにより、コーティングのコンパクト密度を決定します。カレンダー加工後、正極のコンパクト密度は3.00 g/cm3に制御され、厚さの変動は最小限に抑えられ、安定性は良好です。
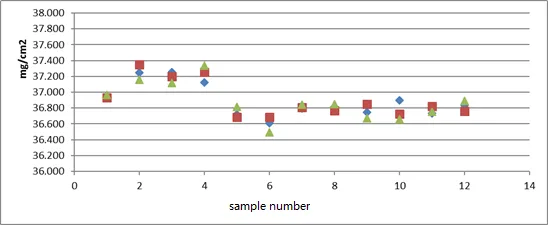
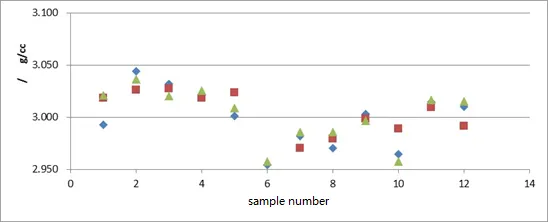
負極シートのテストデータを図4と図5に示します。電極シートの両面の平均表面密度は16.13mg/cm2で、良好なコーティング安定性を示しています。電極シートのカレンダー加工は、電極シートの厚さを制御することにより、コーティングのコンパクト密度を決定します。カレンダー加工後、負極のコンパクト密度は1.62 g/cm3に制御され、厚さの変動は最小限に抑えられ、安定性は良好です。最後に、正極シートと負極シートの両方の表面密度とコンパクト密度の範囲、平均、および標準偏差を表1にまとめます。

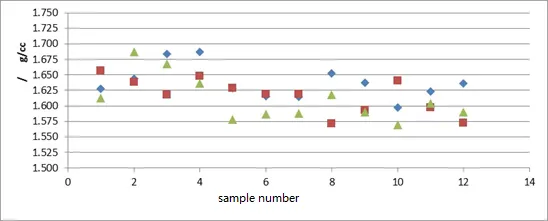
表1:正極シートと負極シートの表面密度とコンパクト密度
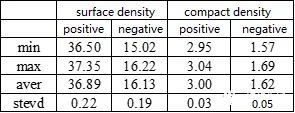
巻き取り後、ゼリーロールは製品の品質を確保するために、次のような広範なテストが必要です。
(1)高さ、幅、厚さ、テープの幅と位置、タブコレクターの配置などを含むセルの寸法。これらの寸法は直接測定でき、巻線プロセスと機器の精度に関連しています。
(2)電極シートとセパレーターの長さ。
(3)電極シートの幅。幅方向では、負極は正極を一定のマージンで超える必要があり、セパレータは負極を一定のマージンで超える必要があります。幅方向のアライメントは、巻線プロセスの精度によって直接決定されます。精度が高いと、マージン寸法が小さくなり、バッテリーのエネルギー密度が高くなります。ただし、バッテリーの安全マージンは減少するため、重大な安全リスクを回避するためにプロセスの精度を確保することが重要です。セル内の電極シートの各層の位置合わせは、通常、セルの四隅すべてのX線検査によって達成されます。正極と負極の間の相対幅寸法が要件を満たしていない場合、機器は自動的に警告を発し、不良品を拒否します。
(4)ゼリーロールの品質。
(5)電極シートのバリ。電極シートの切断に使用されるカッティングナイフは、時間の経過とともに摩耗し、切断品質に影響を与える可能性があります。そのため、カッティングナイフは寿命に合わせて管理する必要があり、バリを避けるために定期的なカッティング品質の検査を行う必要があります。バリを観察する一般的なプロセスは、切断された電極シートを取り、光学顕微鏡で切断面を調べてバリの存在を検出することです。バリの管理基準は、一般的にバリのサイズをセパレータの厚さの半分より小さくすることです。ただし、一部のメーカーでは、バリがコーティングを超えないように、より厳しい管理要件を設けています。
(6)ゼリーロールのその他の内部欠陥(電極シートの曲げ、コーティングの向き、異物など)。
ゼリーロールの品質選択の分析は、図6のデータヒストグラムに示されています。ヒストグラムは、収集したゼリーロールデータを使用して処理され、製品品質の分布を反映し、製品の品質と不適合率の評価と予測を可能にします。統計データを分析する場合、データは異なる範囲に基づいていくつかのグループに分割され、グループの数はビンの数と呼ばれます。ゼリーロールの品質分布は正規分布に従い、平均質量は179.86gです。177.955-178.155gの質量範囲内には、正規分布から逸脱した大量のゼリーロールがあります。
電極シートの加工では、片面コーティングや箔の露出などの問題がある不良シートにマーキングを施し、これらの不良シートを巻き取りながら取り除きます。しかし、それでもゼリーロールに不良シートが現れることがあります。ゼリーロールの品質検査を行い、不適合品を取り除くことで、製品の品質をさらに確保することができます。
品質検査結果の異常の主な原因は、電極シートの加工中に、コーティングのムラ、片面コーティング、電極シート上のテープ欠陥の存在など、不良シートの発生です。
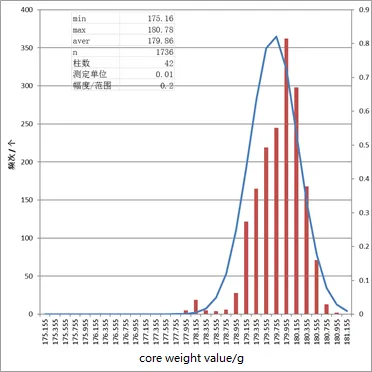
部分ゼリーロール分解破壊試験が行われ、主に正極、負極、およびセパレーターの長さデータを分析しました。具体的な結果を図7に示し、正極の長さは約2.20m、負極の長さは約2.37mです。正極からのリチウムイオンが拡散して負極格子に収容されるためには、負極が正極を一定のサイズのマージンで完全に囲む必要があります。さらに、短絡を防ぐために、セパレーターは負極をカプセル化する必要があります。巻線セルの長さ方向では、負極が正極と比較してマージンを持っていることを確認する必要があり、セパレーターは負極を囲む必要があります。電極シートの相対的な位置は、セパレーターの長さ、負極に対する相対寸法、正極と負極の間の相対位置などのパラメーターを含む非常に重要です。これらの寸法は、電極コーティング仕様、巻線プロセス、およびその他の要因の影響を受けます。
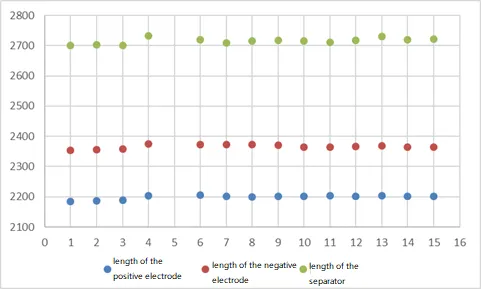
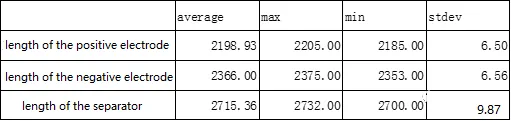
バッテリーを組み立てたら、充電と放電を行って、バッテリーの容量、DC内部抵抗、およびその他のパラメーターをテストします。容量分布は、バッテリーのすべてのプロセスに影響を与える要因の蓄積です。このパラメータを使用して、バッテリーの一貫性を分析し、すべてのプロセスのエラーを統合できます。バッテリー容量の分布を図8と表2に示します。プロセス能力とは、製品が定常状態にあるときに製品の品質を確保するプロセスの能力です。これは、オペレーター、機械設備、原材料、プロセス方法、プロセス内の作業環境などの要因によって包括的に影響を受け、制限されます。それは、製品の品質が安定しているかどうか、そして製品の品質精度が十分であるかどうかの2つの側面に反映されます。図9に示すように、バッテリー容量データに基づいて、バッテリー生産のプロセス能力が包括的に分析され、CP = 1.085、バッテリー生産能力は要件を満たしています。
工程能力の決定:
1.CP>1.33。Cp>1.33の場合、プロセス能力が十分であることを示します。このとき、プロセスの能力の大幅な変化を防ぐために、プロセスの安定性を制御する必要があります。プロセス能力が大きすぎると考えられる場合は、標準要件とプロセス条件を分析する必要があります。一方では、要件を下げて、機器の精度の無駄を避けることができます。一方、製品の品質を向上させるために規格を改訂することもできます。
2. 1.0
3. 0.67
4.CP≤0.67。工程能力指数が 0.67未満の場合は、工程能力が著しく不十分であり、必要に応じて修正のために作業を停止する必要があることを示しています。
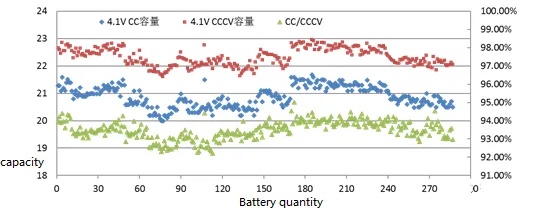
表2 バッテリー容量分布データ
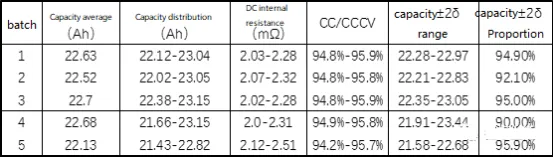
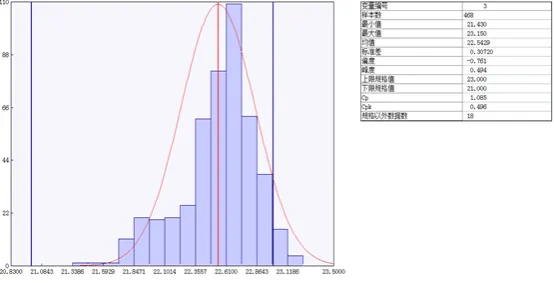