Las baterías de iones de litio generalmente se combinan en serie o en paralelo para formar un paquete de baterías de energía con el fin de cumplir con los requisitos de rendimiento. A medida que aumenta el número de baterías individuales, el problema de la consistencia de la batería se vuelve más prominente. La inconsistencia en las baterías puede provocar una serie de problemas, como la reducción de la vida útil de la batería, la disminución del rendimiento y el compromiso de la seguridad del paquete de baterías. La inconsistencia de las baterías individuales se deriva principalmente del proceso de fabricación o almacenamiento, así como del proceso de uso.
Durante el proceso de producción, la inconsistencia a menudo se reduce indirectamente mediante el control de la precisión del proceso de fabricación. Sin embargo, esto solo puede minimizar las diferencias de parámetros iniciales y no puede eliminarlas por completo. La consistencia de las baterías exhibe transitividad y acumulatividad, ya que está influenciada por múltiples factores que interactúan. Incluso las ligeras diferencias en los parámetros iniciales pueden magnificarse en gran medida durante el uso.
Para mejorar esta situación, podemos adoptar un enfoque combinado de varios aspectos, como la producción de baterías, la clasificación de baterías, el equilibrio de baterías y la gestión térmica del paquete de baterías de energía. Este artículo comparte los datos de prueba del proceso de producción de baterías de iones de litio de bobinado prismático de todas las lengüetas y analiza su consistencia.
El diseño específico y el proceso de producción de la batería son los siguientes: El material del electrodo positivo de la batería utiliza un sistema ternario, mientras que el electrodo negativo utiliza grafito artificial. La batería se ensambla de manera bobinada y está encerrada en una carcasa de aluminio. En la Figura 1 se muestra el proceso de las láminas de electrodos, el bobinado de rollos de gelatina y el ensamblaje de la batería.
Durante el bobinado de la batería de lengüetas, la disposición de las láminas de electrodos y los separadores es la que se muestra en la Figura 1. Los bordes laterales de la lámina de electrodo positivo (15) sin recubrimiento durante la aplicación de material de electrodo positivo (30) y el lado en blanco (14) de la lámina de electrodo negativo mientras se aplica material de electrodo negativo (40) se sueldan respectivamente como lengüetas de oreja en los colectores de corriente positiva y negativa. Las láminas de electrodos positivo y negativo están separadas por un separador (170), y los colectores de corriente positiva y negativa están expuestos a ambos lados del rollo de gelatina de bobinado, conectados directamente a los electrodos positivo y negativo de la batería.
Al mejorar las características de potencia desde la perspectiva de las pestañas, la distancia del flujo de corriente se acorta, lo que da como resultado una distribución uniforme de la densidad de corriente a altas tasas de descarga, lo que permite una alta densidad de potencia y reduce la generación de calor de las láminas de electrodos.
Después de ensamblar la cubierta superior, la lengüeta del electrodo positivo con colector de corriente en blanco se suelda a la barra colectora positiva, y la lengüeta del electrodo negativo con colector de corriente en blanco se suelda a la barra colectora negativa mediante soldadura láser o soldadura por resistencia. Cuando la capacidad de diseño es grande, se pueden conectar dos rollos de gelatina de bobinado en paralelo. Durante el proceso de soldadura, primero se pueden conectar varios rollos de gelatina de bobinado en paralelo y luego soldarlos juntos, o cada rollo de gelatina de bobinado se puede soldar individualmente y luego se conectan varios rollos de gelatina de bobinado en paralelo después de la soldadura láser.
Los rollos de gelatina de bobinado con lengüetas soldadas recubiertas de película aislada se insertan en la carcasa, y la cubierta superior y la carcasa se sueldan mediante soldadura láser. Una vez que la batería se seca, se llena de electrolito y se precarga. La abertura de la batería se sella con un clavo de sellado, se cubre con un tapón de sellado de aluminio, y luego el tapón de sellado se suelda a la cubierta superior de la batería para sellar la celda por completo.
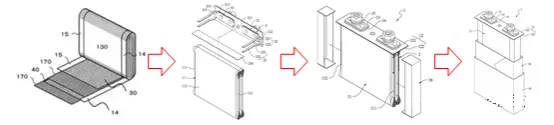
Consistencia en la producción de láminas de electrodos
Las láminas de electrodos positivos y negativos se recubren mediante una técnica de recubrimiento de extrusión de matriz ranurada, con calandrado en modo de espacio entre rodillos constante mediante un servolaminador hidráulico.
Durante el proceso de recubrimiento y calandrado de electrodos, las láminas de electrodos con una longitud de aproximadamente 500 m se recogen en forma de rollo y se someten a inspecciones iniciales y finales en lotes. Un muestreador corta muestras circulares con un diámetro de φ60 mm, y se mide el peso y el grosor de las láminas de electrodos. Se calcula la densidad superficial y la densidad compacta de las láminas de electrodos, con 3 muestras tomadas para pruebas y cálculo de datos por lote.
Los datos de prueba para las láminas de electrodos positivos se muestran en la Figura 2 y la Figura 3. La densidad superficial media de las láminas de electrodos en ambos lados es de 36,89 mg/cm2, lo que indica una buena estabilidad del recubrimiento. El calandrado de las láminas de electrodos determina la densidad compacta del recubrimiento controlando el grosor de las láminas de electrodos. Después del calandrado, la densidad compacta del electrodo positivo se controla a 3,00 g/cm3, con fluctuaciones mínimas de espesor y buena estabilidad.
Los datos de prueba para las láminas de electrodos positivos se muestran en la Figura 2 y la Figura 3. La densidad superficial media de las láminas de electrodos en ambos lados es de 36,89 mg/cm2, lo que indica una buena estabilidad del recubrimiento. El calandrado de las láminas de electrodos determina la densidad compacta del recubrimiento controlando el grosor de las láminas de electrodos. Después del calandrado, la densidad compacta del electrodo positivo se controla a 3,00 g/cm3, con fluctuaciones mínimas de espesor y buena estabilidad.
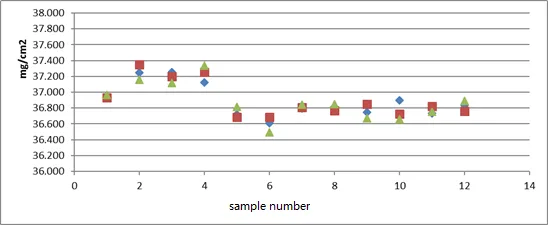
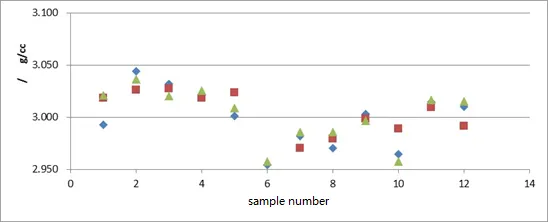
Los datos de prueba para las láminas de electrodos negativos se muestran en la Figura 4 y la Figura 5. La densidad superficial media de las láminas de electrodos en ambos lados es de 16,13 mg/cm2, lo que indica una buena estabilidad del recubrimiento. El calandrado de las láminas de electrodos determina la densidad compacta del recubrimiento controlando el grosor de las láminas de electrodos. Después del calandrado, la densidad compacta del electrodo negativo se controla a 1,62 g/cm3, con fluctuaciones mínimas de espesor y buena estabilidad. Por último, en la Tabla 1 se resumen los rangos, promedios y desviaciones estándar de la densidad superficial y la densidad compacta para láminas de electrodos positivos y negativos.

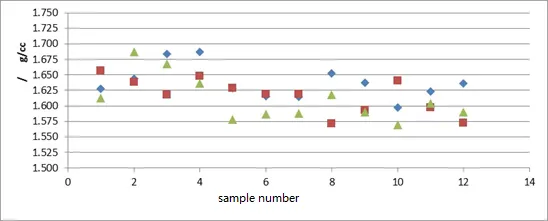
Tabla 1: Densidad superficial y densidad compacta de láminas de electrodos positivos y negativos
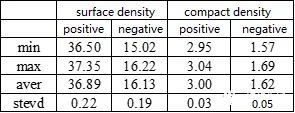
Después de enrollarse, el rollo de gelatina requiere pruebas exhaustivas para garantizar la calidad del producto, que incluyen:
(1) Dimensiones de la celda, incluida la altura, el ancho, el grosor, el ancho y la posición de la cinta, la alineación de los colectores de pestañas, etc. Estas dimensiones se pueden medir directamente y están relacionadas con el proceso de bobinado y la precisión del equipo.
(2) Longitud de las láminas de electrodos y separadores.
(3)Anchura de las láminas de electrodos. En la dirección del ancho, el electrodo negativo debe exceder el electrodo positivo por un cierto margen, y el separador debe exceder el electrodo negativo por un cierto margen. La alineación en la dirección del ancho está directamente determinada por la precisión del proceso de bobinado. Cuando la precisión es alta, las dimensiones del margen pueden ser más pequeñas, lo que resulta en una mayor densidad de energía de la batería. Sin embargo, el margen de seguridad de la batería disminuye y es crucial garantizar la precisión del proceso para evitar riesgos de seguridad significativos. La alineación de cada capa de láminas de electrodos en la celda generalmente se logra mediante inspección de rayos X de las cuatro esquinas de la celda. Cuando la dimensión del ancho relativo entre los electrodos positivo y negativo no cumple con los requisitos, el equipo emite automáticamente una alarma y rechaza los productos defectuosos.
(4) calidad del rollo de gelatina.
(5) Rebabas en láminas de electrodos. La cuchilla de corte utilizada para el corte de láminas de electrodos puede experimentar desgaste con el tiempo, lo que afecta la calidad del corte. Por lo tanto, la cuchilla de corte debe administrarse durante su vida útil y se deben realizar inspecciones periódicas de la calidad del corte para evitar rebabas. El proceso típico para observar rebabas es tomar una lámina de electrodo cortada y examinar la superficie cortada bajo un microscopio óptico para detectar la presencia de rebabas. El estándar de control para las rebabas es generalmente que el tamaño de las rebabas debe ser menor que la mitad del grosor del separador. Sin embargo, algunos fabricantes tienen requisitos de control más estrictos, donde las rebabas no deben exceder el recubrimiento.
(6) Otros defectos internos en el rodillo de gelatina, como flexión de la lámina del electrodo, orientación del recubrimiento, objetos extraños, etc.
El análisis de la selección de la calidad de los rollos de gelatina se muestra en el histograma de datos de la Figura 6. El histograma se procesa utilizando los datos recopilados de rollos de gelatina para reflejar la distribución de la calidad del producto, lo que permite la evaluación y predicción de la calidad del producto y las tasas de no conformidad. Al analizar datos estadísticos, los datos se dividen en varios grupos en función de diferentes rangos, y el número de grupos se denomina número de bins. La distribución de la calidad de los rollos de gelatina sigue una distribución normal, con una masa media de 179,86 g. Hay una mayor cantidad de rollos de gelatina dentro del rango de masa de 177,955-178,155 g, desviándose de la distribución normal.
Durante el procesamiento de láminas de electrodos, se realizan marcas en láminas defectuosas con problemas como recubrimiento de una sola cara o lámina expuesta, y estas láminas defectuosas se eliminan durante el bobinado. Sin embargo, las hojas defectuosas todavía aparecen ocasionalmente en el rollo de gelatina. La realización de inspecciones de calidad en los rollos de gelatina y la eliminación de productos no conformes pueden garantizar aún más la calidad del producto.
La causa principal de los resultados anormales de la inspección de calidad es la generación de láminas defectuosas durante el procesamiento de la lámina de electrodos, como inconsistencias en el recubrimiento, recubrimiento de una sola cara y la presencia de defectos de cinta en las láminas de electrodos.
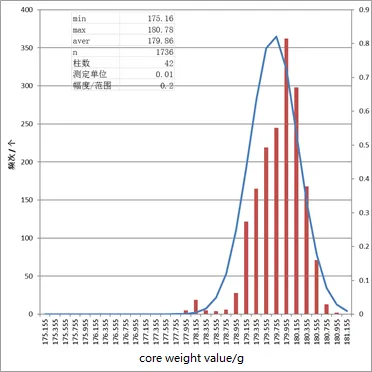
Se realizaron pruebas destructivas de desmontaje parcial de rollos de gelatina, analizando principalmente los datos de longitud del electrodo positivo, el electrodo negativo y el separador. Los resultados específicos se muestran en la Figura 7, con la longitud del electrodo positivo de aproximadamente 2,20 m y la longitud del electrodo negativo de aproximadamente 2,37 m. Para que los iones de litio del electrodo positivo se difundan y se acomoden en la red del electrodo negativo, el electrodo negativo debe encerrar completamente el electrodo positivo con un margen de cierto tamaño. Además, para evitar cortocircuitos, el separador debe encapsular el electrodo negativo. En la dirección de la longitud de la celda enrollada, es necesario asegurarse de que el electrodo negativo tenga un margen en comparación con el electrodo positivo, y el separador debe encerrar el electrodo negativo. El posicionamiento relativo de las láminas de electrodos es crucial, incluidos parámetros como la longitud del separador, las dimensiones relativas al electrodo negativo y el posicionamiento relativo entre los electrodos positivo y negativo. Estas dimensiones están influenciadas por las especificaciones de recubrimiento del electrodo, los procesos de bobinado y otros factores.
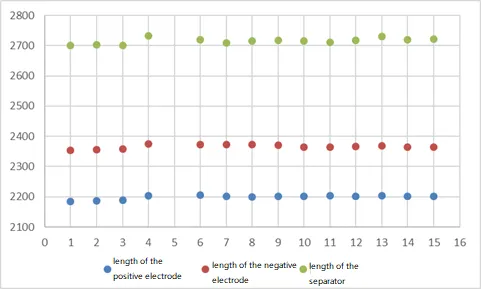
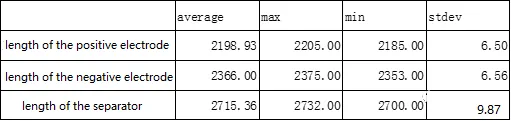
Después de ensamblar la batería, cargue y descargue para probar la capacidad de la batería, la resistencia interna de CC y otros parámetros. La distribución de la capacidad es la acumulación de todos los factores que influyen en el proceso de la batería. Este parámetro se puede utilizar para analizar la consistencia de la batería e integrar los errores de todos los procesos. La distribución de la capacidad de la batería se muestra en la Figura 8 y la Tabla 2. La capacidad del proceso es la capacidad de un proceso para garantizar la calidad del producto cuando se encuentra en un estado estacionario. Se ve afectado y restringido de manera integral por factores como los operadores, la maquinaria y el equipo, las materias primas, los métodos de proceso y el entorno de trabajo en el proceso. Se refleja en dos aspectos: si la calidad del producto es estable y si la precisión de la calidad del producto es suficiente. Como se muestra en la Figura 9, según los datos de capacidad de la batería, se analiza exhaustivamente la capacidad del proceso de producción de baterías, CP = 1.085, y la capacidad de producción de la batería cumple con los requisitos.
Determinación de la capacidad del proceso:
1.Cp>1.33. Cuando Cp>1.33, indica que la capacidad del proceso es suficiente. En este momento, es necesario controlar la estabilidad del proceso para evitar cambios significativos en la capacidad del proceso. Si se considera que la capacidad del proceso es demasiado grande, se deben analizar los requisitos estándar y las condiciones del proceso. Por un lado, los requisitos se pueden reducir para evitar el desperdicio de precisión del equipo. Por otro lado, las normas también pueden ser revisadas para mejorar la calidad del producto.
2. 1.0
3. 0,67
4.Cp≤0.67. Cuando el índice de capacidad del proceso es inferior a 0,67, indica que la capacidad del proceso es gravemente insuficiente y el trabajo debe detenerse para su rectificación si es necesario.
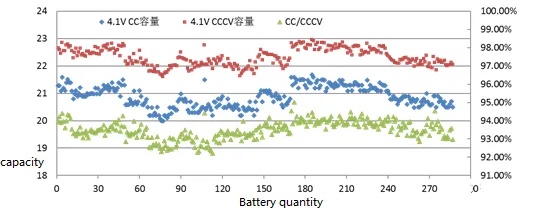
Tabla 2 Datos de distribución de la capacidad de la batería
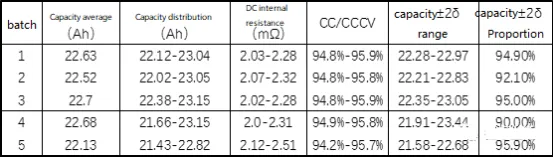
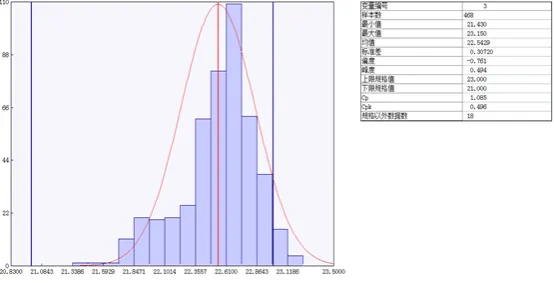