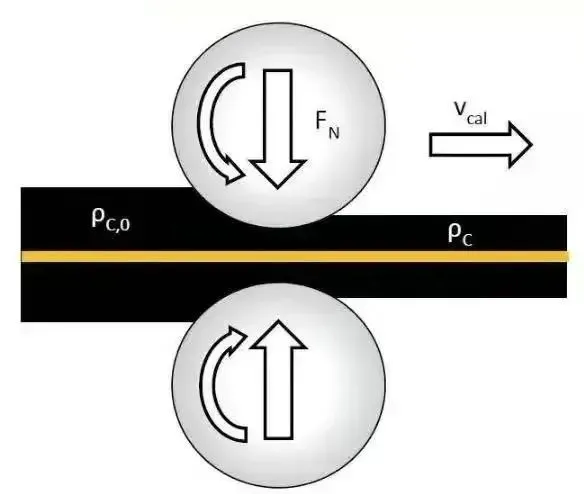
01轧制质量的作用、原理及影响因素压光机
- 的功能压光机
压延是将涂覆和部分干燥的锂电池电极片压实的过程。电极片的压延提高了锂电池的能量密度,并确保电极材料牢固地附着在集流体上,防止了循环过程中因脱落而造成的电池能量损失。在压延之前,需要将涂布的电极片干燥到一定程度,以防止涂层在压实过程中剥落。在此过程中控制压实程度也很重要。过度压实会影响集流体附近的电极材料,阻碍锂离子的正确插入和提取,导致活性材料紧密粘附在一起,导致容易从集流体上脱落。在严重的情况下,电极片的过度可塑性会导致破损并阻碍压实后的卷绕过程。压延是锂电池电极制造中最关键的工艺之一,其精度会显著影响电池性能。压延的目标包括保持电极片的光滑和平坦表面,以防止因突起刺穿隔膜而引起的潜在短路,以及提高电池的能量密度。压实过程还减少了电极片的体积,从而提高了锂电池的能量密度、循环寿命和安全性能。
- 电极片的原理压延
压延的目的是在活性材料和箔之间实现更致密、更均匀的粘合连接。辊压制过程应在涂层完成并且电极片干燥后进行。否则,在压实过程中可能会出现粉末脱落和层分层等问题。电池电极片由两面涂有导电浆料颗粒的铜(或铝)箔组成。在经过涂层和干燥过程后,电极片经过辊压。在压实之前,铜(或铝)箔上的导电浆料涂层是由单个或弱连接的颗粒或簇组成的半流体、半固体颗粒介质,表现出一定的分散性和流动性。导电浆料颗粒之间存在间隙,这保证了在压实过程中,颗粒可以发生小位移以填充间隙,并在压实时实现相互定位。电池电极片的压延可以看作是半固体导电浆料颗粒在未密封状态下的连续压实过程。导电浆料颗粒粘附在铜(或铝)箔的表面,在摩擦力的作用下不断被吸入辊之间的间隙中,并压制成一定密度的电极片。压延的原理如图2所示。
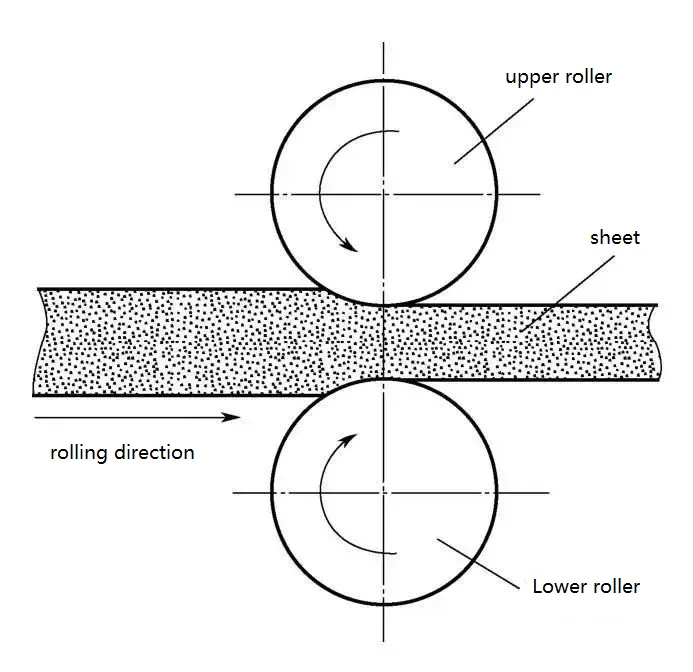
电池电极片的轧制与钢的轧制有很大不同。当钢材被轧制时,工件最初在受到外力时会发生弹性变形。当外力达到一定限度时,工件开始发生塑性变形。随着外力的增加,塑性变形增加。钢轧制纵向轧制的目的是获得伸长率。在轧钢过程中,分子纵向延伸和横向膨胀,导致工件厚度减小,而密度没有变化。
另一方面,电池电极片涉及将复合浆料涂覆在铝箔或铜箔等基材上。电极片的滚筒压实旨在压实电极片上的导电浆料颗粒。其目的是增加电极片的压实密度。适当的压实密度可以提高电池的放电容量,降低内阻,延长电池的循环寿命。导电浆料颗粒在压实过程中受到压力时会发生位移和变形。电极片的密度随压力的变化而遵循一定的模式,如图3所示。
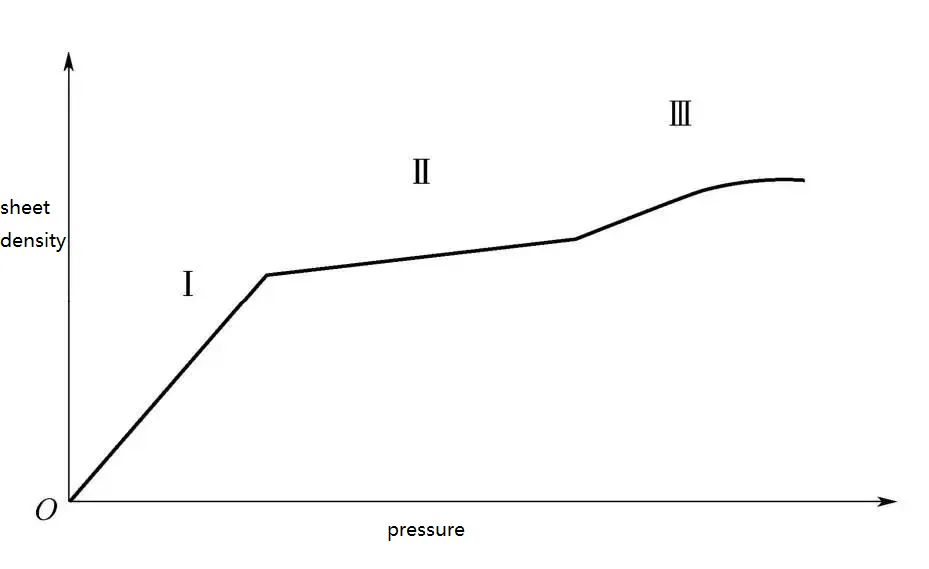
在区域I中,随着接触压力的增加,导电浆料颗粒开始发生小规模的位移,并逐渐增加。在这个阶段,浆料颗粒之间的间隙逐渐填充,导致电极片的相对密度缓慢增加。
在区域II中,在区域I中糊状颗粒的密度略微增加后,接触压力的进一步增加导致颗粒之间的间隙继续填充。随着区域II的压实进行,颗粒之间的间隙被完全压缩,导致电极片的相对密度迅速增加。相对密度的增加速率远高于区域I中的速率,并且浆体颗粒在该区域发生一些变形。
在区域III中,在区域II中,糊状颗粒之间的间隙完全填充后,颗粒不再发生位移。然而,随着接触压力的增加,浆料颗粒开始发生明显的变形。在这个阶段,电极片的相对密度不会随着接触压力的增加而迅速增加。相反,电极片发生硬化,相对密度的变化变成平缓的曲线。
- 影响轧制质量的因素
压延机引起的电池电极片的质量问题主要表现在轧制后片材厚度不均匀。厚度的不一致会导致电极片的压实密度发生变化,这是影响电池性能一致性的关键因素。电极片厚度的均匀性包括横向厚度均匀性和纵向厚度均匀性,如图4所示,它们有不同的原因。
影响电极片横向厚度不均匀性的主要因素包括轧辊的弯曲变形、机架的刚度、主要受力构件的弹性变形、压实力和板材的宽度。压光机运行过程中,压实力使轧辊和机架变形,最终导致轧辊偏转变形。这导致板材在横向上中间较厚而侧面较薄的现象。
影响电极片纵向厚度不均匀性的主要因素包括轧辊、轴承和轴承座的加工精度和安装精度。当辊子旋转时,关键部件的加工误差会导致施加在板材上的压实力出现周期性波动,从而导致板材纵向的压实厚度不均匀。
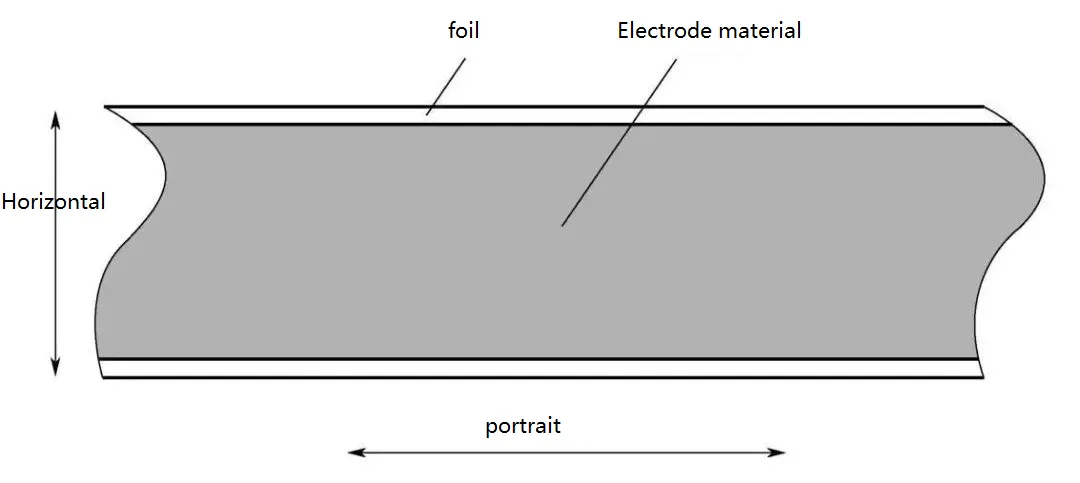
02结构组成及分类压光机
2.1基本结构压光机
用于电池电极片的高精度压延机的标准配置包括一个垂直安装的H形框架,两个辊子水平排列,以及一个安装在下方向上施加压力的液压缸。辊隙由伺服电机减速器调节,机器安装在整体式底座上。减速机的双输出轴通过万向联轴器连接到减速机。这种配置确保了压延过程的高精度。标准型号压光机的示意图如图5所示。
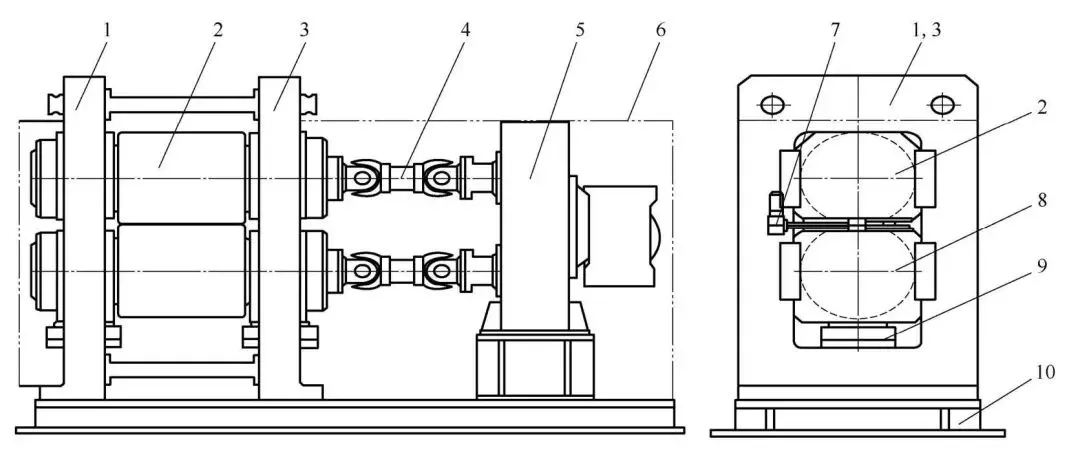
1 -左框架;2—上辊系统;3 -右框架;4—万向联轴器;5—双输出轴减速机;6 -掩护;7—辊隙调节机构;8—下辊系统;9—液压缸;10 -基座。
如图5所示,压光机主要由机架、辊子和主要传动部件组成。框架是整个系统的基础,需要具有足够的刚度和强度,以最大限度地减少变形。液压装置通过轴承座将压实力施加到辊子上。电机和减速器使两个辊子同步旋转,为辊子提供扭矩并确保连续的压光过程。辊间隙调整机构由两个间隙调整楔块组成,用于调整两个辊之间的间隙,以满足不同电极片的厚度要求。
2.2压延机主机的结构形式
(1)按卷筒类型分类。压光机的主辊可分为两种形式:弯辊和直辊,如图6所示。直辊结构(标准型号)具有带内部机构的轴承座,以消除主轴承的径向游隙并提供轴向定位。带弯曲辊的结构采用弯曲辊筒,以消除主轴承的径向游隙,减少或消除辊面的偏转变形。
当压实后的电极片宽度较窄,辊面宽度与辊面直径之比接近1:1,且可以忽略电极片压实过程中的偏转变形时,建议使用无弯曲辊的标准机型。
当压实后的电极片宽度较宽,辊面宽度与辊面直径之比大于1.2:1,且电极片压实过程中的挠度变形大于0.5μm时,建议使用弯曲辊的型号。
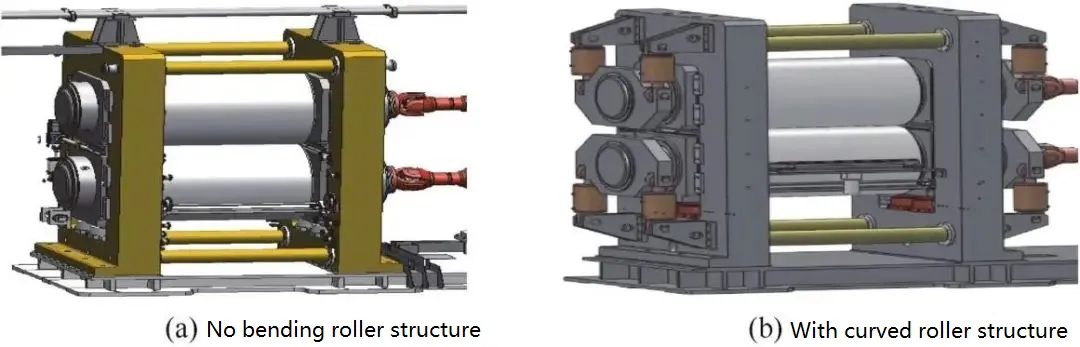
(2)基于驾驶模式的分类。压路机可分为单电机驱动结构和双电机驱动结构,如图7所示。
单电机驱动结构利用驱动电机、减速器、减速器、万向联轴器、辊子传动装置,通过减速器实现辊子的机械同步。
双电机驱动结构采用驱动电机、减速器、万向联轴器、滚动传动。它采用由电子元件控制的同步电机,以实现辊子的机械同步。
压光机的驱动扭矩与压光速度、辊面宽度和辊间压力成正比。当辊面宽度和压力保持相对恒定时,更高的速度需要更大的驱动扭矩和更大的电机功率。在需要高速和大电机功率的情况下,压延机可以由两个同步电机驱动。
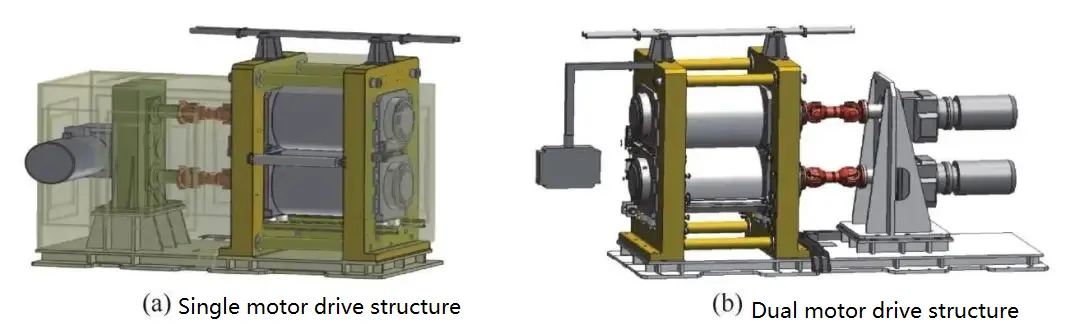
(3)按压制方式分类。压路机可分为机械螺丝拧紧结构和液压缸拧紧结构,如图8所示。
机械螺丝拧紧结构主要通过设置辊间隙值对电极片上的辊子施加压力。它不需要额外的加压装置。因此,实际压力一般比较小,限制了辊压时电极片的压实密度。
液压缸拧紧结构包括将液压缸安装在下辊系统两端的轴承座下方,在V形框架内。液压缸使用柱塞缸向上推并施加压力。在柱塞气缸的作用下,下辊系统向上移动并施加辊压实压力。通过使用液压缸施加压力,可以实现稳定的压力,并可以施加更高的压力。这种方法是目前使用的主流压制方法。
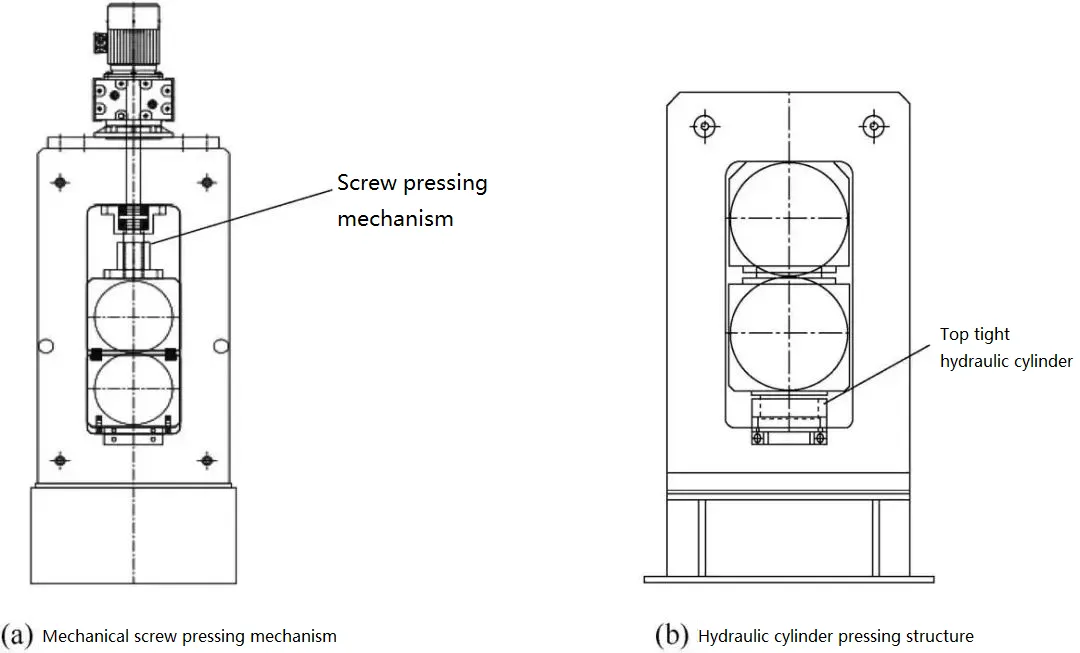
2.3在中国,大多数用于锂电池电极片的压延机在室温下进行压实。在压实过程中,电极片表现出明显的反弹,因此在压实前将电极片预热到一定温度是有益的。预热的目的如下:使电极片干燥并降低其水分含量,降低压实后电极片的回弹率,消除压实后电极片内的一些残余内应力,并通过加热软化或熔化电极片表面的粘结剂,这增强了活性材料和集流体之间的粘附力,促进了更好的电解液吸收。为了加热电极片,在辊压机之前安装了一个加热箱来加热电极片。加热箱内的空气被加热,然后用加热的空气加热电极片。但是,由于加热箱与辊子之间的距离,这种方法加热效率低,导致热量损失迅速,加热无效。目前,广泛使用的方法是热压延机,先将机器的辊子加热,然后用加热的辊子压实锂电池电极片。辊子的加热可以通过外部加热或内部加热来实现,几种常见的加热方法说明如下:
(1)采用电磁感应对辊子进行外部加热。感应线圈放置在辊子外部。当线圈通电时,电磁感应会在辊子内部产生涡流,从而加热辊子。这种加热方式具有能耗低、热转化率高、压实时辊子表面温度精确控制等优点。但是,它也有一些缺点,例如成本高和难以沿卷筒圆周布置布线。
(2)使用外部加热箱加热辊子。加热箱位于卷材的上方或下方,并使用高温空气从外部烘烤卷材。热量通过空气作为传热介质传递到轧辊的工作表面,达到加热轧辊的目的。但是,这种方法存在严重的问题:难以控制辊面的温度,辊面的温度分布不均匀,局部高温会损坏辊子,消耗大量能量,能量损失明显。
(3)使用电阻丝等电子元件从内部加热辊子。通常,管状加热元件或电阻丝插入工作辊或支撑辊的内部。通过将卷筒的一端连接到电源,对卷筒进行加热。这种加热方法的优点是不会损坏辊子的外部结构,简单且易于实施。加热过程从辊芯开始,热量从辊芯传导到辊子的工作表面,从而形成中间优先加热方法。然而,这种方法在加热过程中增加了辊子上的热应力。对于较大直径的辊子,传热时间很长,因此对调整辊子表面温度不太敏感,需要更长的调整周期。此外,轴承位置会出现局部高温,导致润滑困难。
(4)使用导热油加热辊子。用导热油加热辊子是国内外广泛使用的方法。在辊子内形成内部油道,加热的导热油通过旋转接头引入辊子中,通过热传导加热辊子。导热油可在高达200°C的温度下稳定运行。这种方法安全、环保、噪音低。导热油循环系统具有高温精度,易于控制导热油的入口温度。通过控制导热油在入口处的流速,导热油和辊子之间发生强制对流传热,从而增加它们之间的对流传热系数并最大限度地提高它们之间的传热。这确保了辊子表面保持恒定的温度范围并具有良好的均匀性,满足大多数辊子的温度要求。