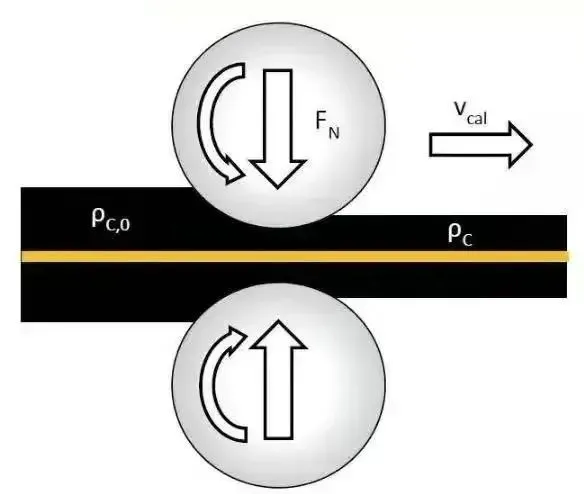
01 Fonctions, principes et facteurs d’influence de la qualité de laminage machine à calandrer
- Fonctions demachine à calandrer
Le calandrage est un processus dans lequel les feuilles d’électrodes de batterie au lithium revêtues et partiellement séchées sont compactées. Le calandrage des feuilles d’électrodes augmente la densité énergétique des batteries au lithium et garantit que les matériaux des électrodes sont fermement fixés au collecteur de courant, évitant ainsi la perte d’énergie de la batterie causée par le détachement pendant le cyclage. Avant le calandrage, les feuilles d’électrodes revêtues doivent être séchées dans une certaine mesure pour éviter que le revêtement ne se décolle pendant le compactage. Il est également important de contrôler le niveau de compactage pendant le processus. Un compactage excessif peut affecter les matériaux d’électrode à proximité du collecteur de courant, entravant l’insertion et l’extraction correctes des ions lithium et provoquant une adhérence étroite des matériaux actifs, conduisant à un détachement facile du collecteur de courant. Dans les cas graves, une plasticité excessive des feuilles d’électrodes peut entraîner une rupture et entraver le processus d’enroulement après compactage. Le calandrage est l’un des processus les plus critiques dans la fabrication des électrodes de batterie au lithium, et sa précision a un impact significatif sur les performances de la batterie. Les objectifs du calandrage comprennent le maintien d’une surface lisse et plane des feuilles d’électrodes afin d’éviter les courts-circuits potentiels causés par les saillies perforant le séparateur et l’amélioration de la densité énergétique des batteries. Le processus de compactage réduit également le volume des feuilles d’électrodes, améliorant ainsi la densité énergétique, la durée de vie et les performances de sécurité des batteries au lithium.
- Principe de la feuille d’électrodeCalandre
Le but du calandrage est d’obtenir une liaison plus dense et plus uniforme entre le matériau actif et la feuille. Le processus de compactage des rouleaux doit être effectué une fois le revêtement terminé et les feuilles d’électrodes séchées. Sinon, des problèmes tels que la perte de poudre et le délaminage de la couche peuvent survenir pendant le compactage. Les feuilles d’électrode de la batterie sont constituées d’une feuille de cuivre (ou d’aluminium) recouverte des deux côtés de particules de pâte conductrices d’électricité. Après avoir subi les processus de revêtement et de séchage, les feuilles d’électrodes sont soumises à un compactage au rouleau. Avant le compactage, le revêtement d’une pâte conductrice d’électricité sur la feuille de cuivre (ou d’aluminium) est un milieu granulaire semi-fluide et semi-solide composé de particules ou d’amas individuels ou faiblement connectés, présentant une certaine dispersibilité et fluidité. Il y a des espaces entre les particules de pâte conductrices d’électricité, ce qui garantit que pendant le processus de compactage, les particules peuvent subir de petits déplacements pour combler les espaces et obtenir un positionnement mutuel sous compactage. Le calandrage des feuilles d’électrodes de batterie peut être considéré comme un processus de compactage continu de particules de pâte semi-solides conductrices d’électricité à l’état non scellé. Les particules de pâte conductrices d’électricité adhèrent à la surface de la feuille de cuivre (ou d’aluminium), étant continuellement aspirées dans l’espace entre les rouleaux par la force de frottement et compactées en feuilles d’électrodes d’une certaine densité. Le principe du calandrage est illustré à la figure 2.
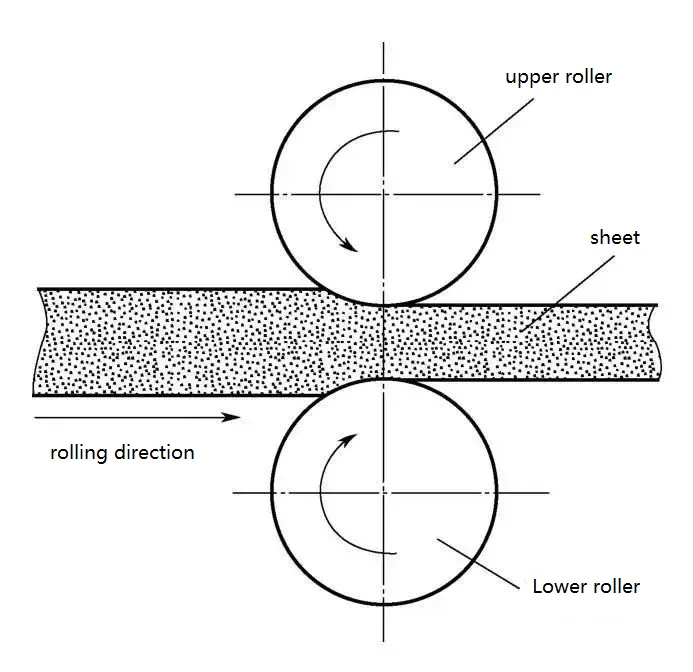
Le laminage des feuilles d’électrodes de batterie diffère considérablement du laminage de l’acier. Lorsque l’acier est laminé, la pièce subit d’abord une déformation élastique lorsqu’elle est soumise à des forces externes. Lorsque la force externe atteint une certaine limite, la pièce commence à subir une déformation plastique. À mesure que la force externe augmente, la déformation plastique augmente. Le but du laminage longitudinal dans le laminage de l’acier est d’obtenir un allongement. Au cours du processus de laminage de l’acier, les molécules s’étendent longitudinalement et latéralement, ce qui entraîne une réduction de l’épaisseur de la pièce sans changement de densité.
D’autre part, les feuilles d’électrode de batterie impliquent l’application d’une boue composée sur des substrats tels que des feuilles d’aluminium ou de cuivre. Le compactage à rouleaux des feuilles d’électrodes vise à compacter les particules de pâte conductrices d’électricité sur les feuilles. Son but est d’augmenter la densité compactée des feuilles d’électrodes. La densité compactée appropriée peut améliorer la capacité de décharge de la batterie, réduire la résistance interne et prolonger la durée de vie de la batterie. Les particules de pâte conductrices d’électricité subissent un déplacement et une déformation lorsqu’elles sont soumises à la pression pendant le processus de compactage. La densité de la feuille d’électrode suit un certain schéma avec la variation de pression, comme le montre la figure 3.
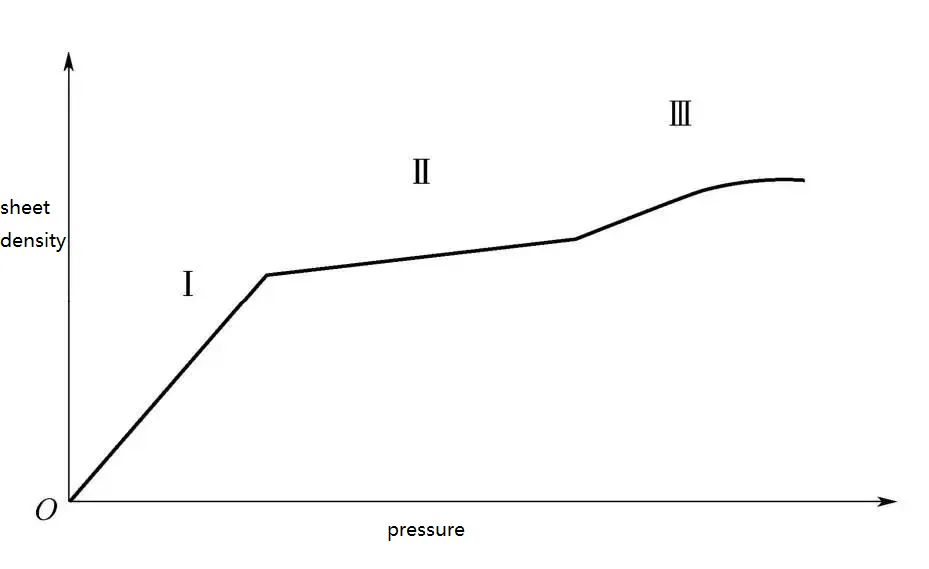
Dans la Région I, à mesure que la pression de contact augmente, les particules de pâte conductrices d’électricité commencent à subir un déplacement à petite échelle, qui augmente progressivement. À ce stade, les espaces entre les particules de pâte sont progressivement remplis, ce qui entraîne une augmentation lente de la densité relative de la feuille d’électrode.
Dans la Région II, après que la densité des particules de pâte a été légèrement augmentée dans la Région I, une nouvelle augmentation de la pression de contact conduit à un remplissage continu des espaces entre les particules. Au fur et à mesure que le compactage progresse dans la Région II, les espaces entre les particules sont entièrement comprimés, ce qui entraîne une augmentation rapide de la densité relative de la feuille d’électrode. Le taux d’augmentation de la densité relative est beaucoup plus élevé que dans la Région I, et une certaine déformation des particules de pâte se produit dans cette région.
Dans la Région III, une fois que les espaces entre les particules de pâte ont été complètement remplis dans la Région II, les particules ne subissent plus de déplacement. Cependant, à mesure que la pression de contact augmente, les particules de pâte commencent à subir une déformation importante. À ce stade, la densité relative de la feuille d’électrode n’augmente pas rapidement avec l’augmentation de la pression de contact. Au lieu de cela, la feuille d’électrode subit un durcissement et le changement de densité relative devient une courbe douce.
- Facteurs affectant la qualité du laminage
Les problèmes de qualité des feuilles d’électrodes de batterie causés par la machine à calandrer se manifestent principalement par l’épaisseur inégale des feuilles après le laminage. L’incohérence de l’épaisseur entraîne des variations dans la densité compactée des feuilles d’électrodes, ce qui est un facteur critique affectant la constance des performances de la batterie. L’uniformité de l’épaisseur de la feuille d’électrode comprend à la fois l’uniformité de l’épaisseur transversale et l’uniformité de l’épaisseur longitudinale, comme le montre la figure 4, et elles ont des causes différentes.
Les principaux facteurs influençant la non-uniformité de l’épaisseur transversale de la feuille d’électrode comprennent la déformation en flexion des rouleaux de laminage, la rigidité du châssis de la machine, la déformation élastique des principaux composants porteurs de contraintes, la force de compactage et la largeur de la feuille. Pendant le fonctionnement de la machine de calandrage, la force de compactage provoque une déformation des rouleaux de laminage et du châssis de la machine, ce qui entraîne finalement une déformation par déflexion des rouleaux. Cela conduit au phénomène de la feuille plus épaisse au milieu et plus mince sur les côtés dans le sens transversal.
Les principaux facteurs influençant la non-uniformité de l’épaisseur longitudinale de la feuille d’électrode comprennent la précision de traitement et la précision d’installation des rouleaux de roulement, des roulements et des sièges de roulement. Les erreurs d’usinage des composants critiques peuvent provoquer des fluctuations périodiques de la force de compactage appliquée à la tôle lorsque les rouleaux tournent, ce qui entraîne une épaisseur compactée non uniforme dans le sens longitudinal de la tôle.
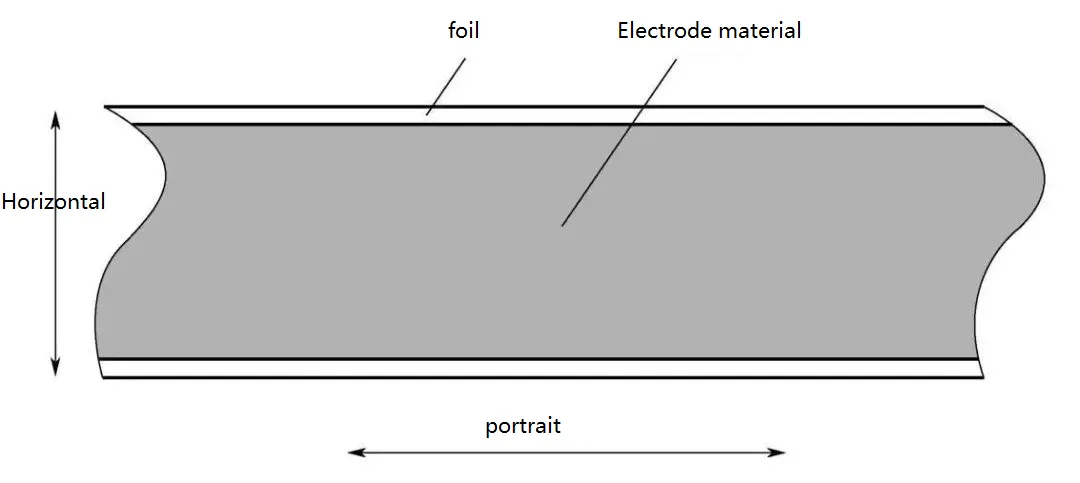
02 Composition structurelle et classificationmachine à calandrer
2.1 Structure de base demachine à calandrer
La configuration standard d’une machine de calandrage de haute précision pour les feuilles d’électrodes de batterie se compose d’un cadre en forme de H monté verticalement, avec deux rouleaux disposés horizontalement, et d’un vérin hydraulique monté en dessous appliquant une pression vers le haut. L’écartement des rouleaux est ajusté par un réducteur de servomoteur, et la machine est montée sur une base intégrée. Les deux arbres de sortie du réducteur sont reliés au réducteur de vitesse par un accouplement universel. Cette configuration garantit une grande précision dans le processus de calandrage. Le schéma de principe de la calandreuse modèle standard est illustré à la figure 5.
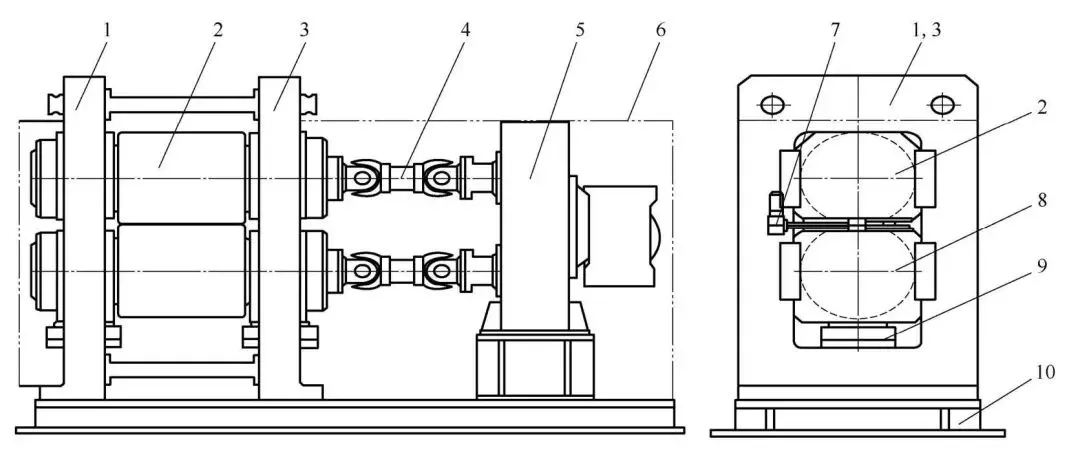
1—Cadre gauche ; 2—Système de roulis supérieur ; 3—Cadre droit ; 4—Accouplement universel ; 5—Réducteur de vitesse à double arbre de sortie ; 6—Couvrir ; 7—Mécanisme de réglage de l’écart de roulis ; 8—Système de roulis inférieur ; 9—Cylindre hydraulique ; 10—Base.
Comme le montre la figure 5, la machine de calandrage se compose principalement du châssis, des rouleaux et des principaux composants de transmission. Le cadre sert de base à l’ensemble du système et doit avoir une rigidité et une résistance suffisantes pour minimiser la déformation. Le dispositif hydraulique applique la force de compactage aux rouleaux à travers les sièges de roulement. Le moteur et le réducteur permettent une rotation synchrone des deux rouleaux, fournissant du couple aux rouleaux et assurant un processus de calandrage continu. Le mécanisme de réglage de l’écartement des rouleaux se compose de deux cales de réglage de l’écartement, qui sont utilisées pour ajuster l’écart entre les deux rouleaux afin de répondre aux exigences d’épaisseur des différentes feuilles d’électrodes.
2.2 Forme structurelle de la machine principale de la machine de calandrage
(1) Classification basée sur le type de rouleau. Les rouleaux principaux de la machine à calandrer peuvent être divisés en deux formes : les rouleaux courbes et les rouleaux droits, comme le montre la figure 6. La structure à rouleaux droits (modèle standard) dispose d’un siège de roulement avec des mécanismes internes pour éliminer le jeu radial des roulements principaux et assurer un positionnement axial. La structure à rouleaux incurvés utilise un cylindre de rouleau incurvé pour éliminer le jeu radial des roulements principaux et réduire ou éliminer la déformation de déflexion de la surface du rouleau.
Lorsque la largeur de la feuille d’électrode compactée est relativement étroite, que le rapport entre la largeur de la surface du rouleau et le diamètre de la surface du rouleau est proche de 1:1 et que la déformation de déflexion lors du compactage de la feuille d’électrode peut être négligée, il est recommandé d’utiliser le modèle standard sans rouleaux incurvés.
Lorsque la largeur de la feuille d’électrode compactée est relativement large, que le rapport entre la largeur de la surface du rouleau et le diamètre de la surface du rouleau est supérieur à 1,2:1 et que la déformation de déflexion lors du compactage de la feuille d’électrode est supérieure à 0,5 μm, il est recommandé d’utiliser un modèle avec des rouleaux incurvés.
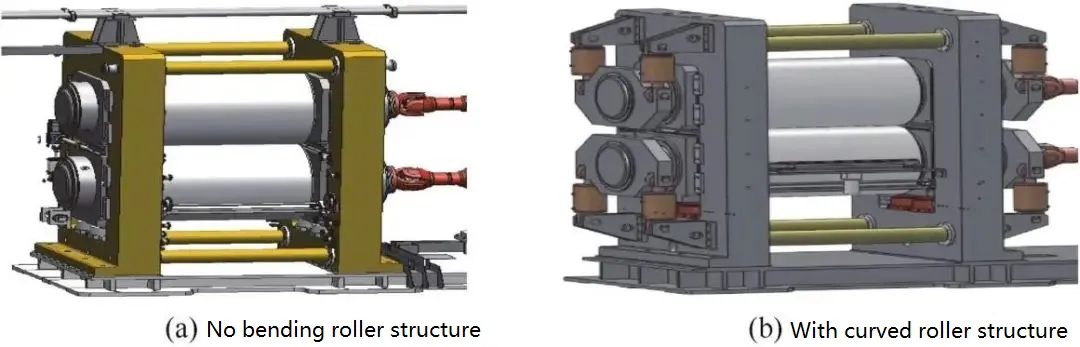
(2) Classification basée sur le mode de conduite. La machine de compactage à rouleaux peut être classée en structure d’entraînement à moteur unique et structure d’entraînement à deux moteurs, comme le montre la figure 7.
La structure d’entraînement à moteur unique utilise un moteur d’entraînement, un réducteur, un réducteur de vitesse, un accouplement universel et une transmission de roulis pour réaliser la synchronisation mécanique des rouleaux à travers le réducteur de vitesse.
La structure d’entraînement à double moteur adopte un moteur d’entraînement, un réducteur, un accouplement universel et une transmission de roulis. Il utilise des moteurs synchrones contrôlés par l’électronique pour réaliser la synchronisation mécanique des rouleaux.
Le couple d’entraînement de la machine à calandrer est proportionnel à la vitesse de calandrage, à la largeur de la surface du rouleau et à la pression entre les rouleaux. Lorsque la largeur de la surface du rouleau et la pression restent relativement constantes, une vitesse plus élevée nécessite un couple d’entraînement plus important et une puissance moteur plus importante. Dans les cas où une vitesse élevée et une puissance moteur importante sont requises, la calandreuse peut être entraînée par deux moteurs synchrones.
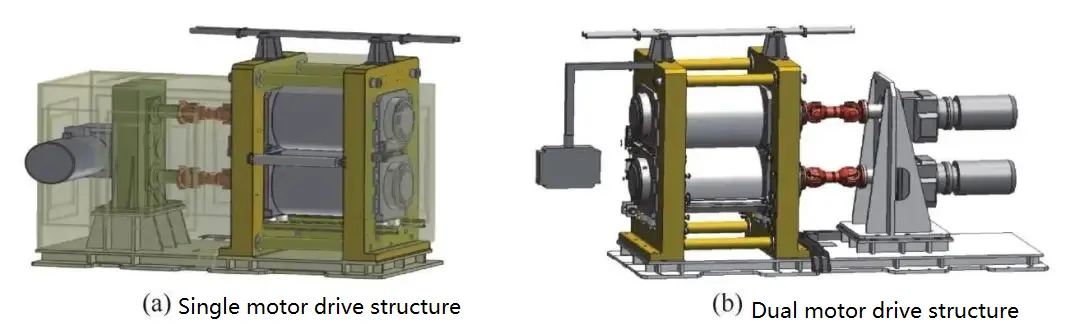
(3) Classification basée sur la méthode de pressage. La machine de compactage à rouleaux peut être divisée en structure de serrage à vis mécanique et structure de serrage à vérin hydraulique, comme le montre la figure 8.
La structure mécanique de serrage par vis exerce principalement une pression sur les rouleaux sur la feuille d’électrode en réglant la valeur de l’écart entre les rouleaux. Il ne nécessite pas de dispositifs de pressurisation supplémentaires. Par conséquent, la pression réelle est généralement relativement faible, ce qui limite la densité de compactage de la feuille d’électrode lors du compactage du rouleau.
La structure de serrage des vérins hydrauliques consiste à monter des vérins hydrauliques sous les sièges de roulement aux deux extrémités du système de roulement inférieur, à l’intérieur du cadre en forme de V. Les vérins hydrauliques utilisent des vérins à piston pour pousser vers le haut et appliquer une pression. Sous l’action des cylindres à piston, le système de rouleau inférieur se déplace vers le haut et exerce une pression de compactage du rouleau. En appliquant une pression à l’aide des vérins hydrauliques, une pression stable peut être obtenue et des pressions plus élevées peuvent être exercées. Cette méthode est actuellement la méthode de pressage la plus couramment utilisée.
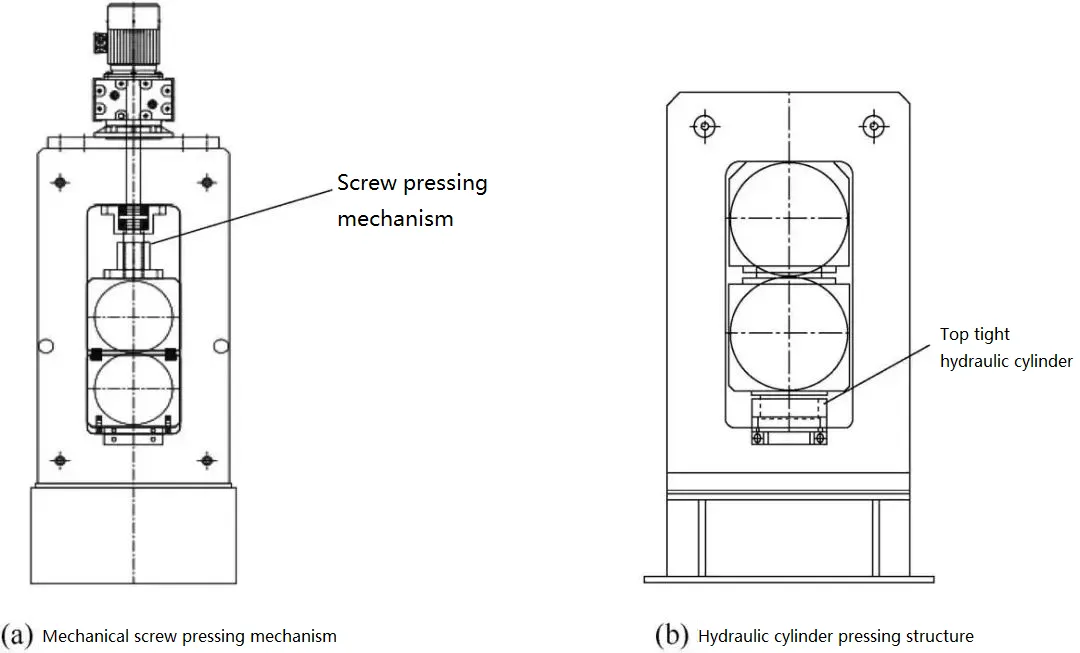
2.3 En Chine, la plupart des machines de calandrage pour les feuilles d’électrodes de batterie au lithium effectuent un compactage à température ambiante. Au cours du processus de compactage, la feuille d’électrode présente un rebond significatif, il est donc avantageux de préchauffer la feuille d’électrode à une certaine température avant le compactage. Le but du préchauffage est le suivant : sécher la feuille d’électrode et réduire sa teneur en humidité, réduire le taux de rebond de la feuille d’électrode après compactage, éliminer une partie de la contrainte interne résiduelle dans la feuille d’électrode après compactage, et ramollir ou fondre le liant à la surface de la feuille d’électrode par chauffage, ce qui améliore l’adhérence entre le matériau actif et le collecteur de courant, facilitant une meilleure absorption de l’électrolyte. Pour chauffer la feuille d’électrodes, un caisson chauffant est installé avant la machine de compactage à rouleaux pour chauffer la feuille d’électrodes. L’air à l’intérieur de la boîte chauffante est chauffé, puis l’air chauffé est utilisé pour chauffer la feuille d’électrodes. Cependant, cette méthode a une faible efficacité de chauffage en raison de la distance entre le caisson de chauffage et les rouleaux, ce qui entraîne une perte de chaleur rapide et un chauffage inefficace. Actuellement, la méthode largement utilisée est la machine de calandrage à chaud, où les rouleaux de la machine sont d’abord chauffés, puis les rouleaux chauffés sont utilisés pour compacter la feuille d’électrode de batterie au lithium. Le chauffage des rouleaux peut être réalisé par chauffage externe ou chauffage interne, et plusieurs méthodes de chauffage courantes sont décrites ci-dessous :
(1) Chauffage externe des rouleaux par induction électromagnétique. Les bobines d’induction sont placées à l’extérieur des rouleaux. Lorsque les bobines sont alimentées, l’induction électromagnétique génère des courants de Foucault à l’intérieur des rouleaux, chauffant ainsi les rouleaux. Cette méthode de chauffage présente les avantages d’une faible consommation d’énergie, d’un taux de conversion thermique élevé et d’un contrôle précis de la température de surface du rouleau pendant le compactage. Cependant, il présente également quelques inconvénients, tels que le coût élevé et les difficultés à organiser le câblage le long de la circonférence des rouleaux.
(2) Chauffage des rouleaux à l’aide d’une boîte de chauffage externe. La boîte chauffante est positionnée au-dessus ou en dessous des rouleaux, et de l’air à haute température est utilisé pour cuire les rouleaux de l’extérieur. La chaleur est transférée à la surface de travail des rouleaux par l’air en tant que fluide caloporteur, ce qui permet de chauffer les rouleaux. Cependant, cette méthode présente de sérieux problèmes : il est difficile de contrôler la température de la surface du rouleau, la répartition de la température sur la surface du rouleau est inégale, des températures élevées localisées peuvent endommager les rouleaux et elle consomme une grande quantité d’énergie avec une perte d’énergie importante.
(3) Chauffage des rouleaux de l’intérieur à l’aide de composants électroniques tels que des fils de résistance. En règle générale, des éléments chauffants tubulaires ou des fils de résistance sont insérés dans la partie interne des rouleaux de travail ou des rouleaux de support. En connectant une extrémité des rouleaux à une source d’alimentation, les rouleaux sont chauffés. Cette méthode de chauffage présente les avantages de ne pas endommager la structure externe des rouleaux, la simplicité et la facilité de mise en œuvre. Le processus de chauffage commence à partir du noyau du rouleau, et la chaleur est conduite du noyau à la surface de travail des rouleaux, ce qui entraîne une approche de chauffage intermédiaire. Cependant, cette méthode augmente la contrainte thermique sur les rouleaux pendant le processus de chauffage. Pour les rouleaux de plus grand diamètre, le temps de transfert de chaleur est long, ce qui les rend moins sensibles à l’ajustement de la température de surface du rouleau et nécessite des cycles de réglage plus longs. De plus, des températures élevées localisées se produisent aux positions des roulements, ce qui entraîne des difficultés de lubrification.
(4) Chauffage des rouleaux à l’aide d’huile de transfert de chaleur. Le chauffage des rouleaux avec de l’huile de transfert de chaleur est une méthode largement utilisée tant au niveau national qu’international. Des passages d’huile internes sont créés à l’intérieur des rouleaux, et de l’huile de transfert de chaleur chauffée est introduite dans les rouleaux par des joints rotatifs, chauffant les rouleaux par conduction thermique. L’huile caloporteuse peut fonctionner de manière stable à des températures allant jusqu’à 200 °C. Cette méthode est sûre, respectueuse de l’environnement et peu bruyante. Le système de circulation de l’huile caloporteur a une grande précision de température, ce qui facilite le contrôle de la température d’entrée de l’huile caloporteuse. En contrôlant le débit de l’huile caloporteuse à l’entrée, un transfert de chaleur par convection forcée se produit entre l’huile caloporteuse et les rouleaux, augmentant le coefficient de transfert de chaleur convectif entre eux et maximisant le transfert de chaleur entre eux. Cela garantit que la surface du rouleau maintient une plage de température constante et a une bonne uniformité, répondant aux exigences de température de la plupart des rouleaux.