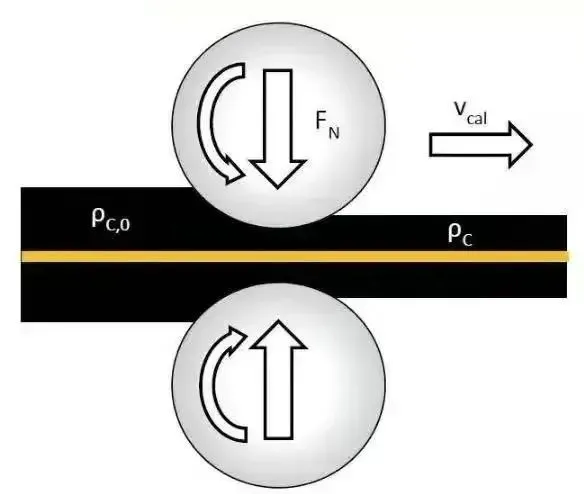
01 Funciones, principios y factores que influyen en la calidad de laminación de máquina de calandrado
- Funciones demáquina de calandrado
El calandrado es un proceso en el que se compactan las láminas de electrodos de la batería de litio recubiertas y parcialmente secas. El calandrado de las láminas de electrodos aumenta la densidad de energía de las baterías de litio y garantiza que los materiales de los electrodos estén firmemente unidos al colector de corriente, evitando la pérdida de energía de la batería causada por el desprendimiento durante el ciclo. Antes del calandrado, las láminas de electrodos recubiertas deben secarse hasta cierto punto para evitar que el recubrimiento se despegue durante la compactación. También es importante controlar el nivel de compactación durante el proceso. La compactación excesiva puede afectar a los materiales de los electrodos cerca del colector de corriente, dificultando la correcta inserción y extracción de los iones de litio y haciendo que los materiales activos se adhieran firmemente entre sí, lo que facilita el desprendimiento del colector de corriente. En casos graves, la plasticidad excesiva de las láminas de electrodos puede provocar roturas y dificultar el proceso de bobinado después de la compactación. El calandrado es uno de los procesos más críticos en la fabricación de electrodos de batería de litio y su precisión afecta significativamente el rendimiento de la batería. Los objetivos del calandrado incluyen mantener una superficie lisa y plana de las láminas de electrodos para evitar posibles cortocircuitos causados por protuberancias que perforan el separador y mejorar la densidad de energía de las baterías. El proceso de compactación también reduce el volumen de las láminas de electrodos, mejorando así la densidad de energía, el ciclo de vida y el rendimiento de seguridad de las baterías de litio.
- Principio de la lámina de electrodosCalandrado
El propósito del calandrado es lograr una unión más densa y uniforme entre el material activo y la lámina. El proceso de compactación del rodillo debe llevarse a cabo después de que se complete el recubrimiento y se sequen las láminas de electrodos. De lo contrario, pueden producirse problemas como el desprendimiento de polvo y la delaminación de la capa durante la compactación. Las láminas de electrodos de la batería consisten en papel de cobre (o aluminio) recubierto por ambos lados con partículas de pasta conductoras de electricidad. Después de someterse a los procesos de recubrimiento y secado, las láminas de electrodos se someten a una compactación con rodillos. Antes de la compactación, el recubrimiento de pasta conductora de electricidad sobre la lámina de cobre (o aluminio) es un medio granular semifluido y semisólido compuesto por partículas o grupos individuales o débilmente conectados, que exhibe cierta dispersabilidad y fluidez. Hay espacios entre las partículas de pasta conductoras de electricidad, lo que garantiza que durante el proceso de compactación, las partículas puedan sufrir pequeños desplazamientos para llenar los espacios y lograr un posicionamiento mutuo bajo compactación. El calandrado de las láminas de electrodos de la batería puede considerarse como un proceso de compactación continuo de partículas semisólidas de pasta conductora de electricidad en un estado no sellado. Las partículas de pasta conductoras de electricidad se adhieren a la superficie de la lámina de cobre (o aluminio), siendo arrastradas continuamente hacia el espacio entre los rodillos por la fuerza de fricción y compactadas en láminas de electrodos con una cierta densidad. El principio de calandrado se ilustra en la Figura 2.
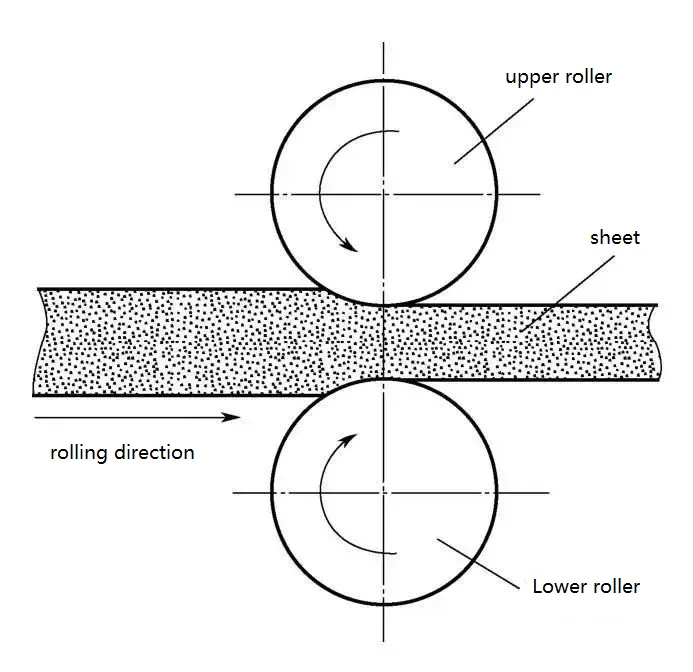
El laminado de las láminas de electrodos de la batería difiere significativamente del laminado del acero. Cuando el acero está laminado, la pieza de trabajo sufre una deformación elástica inicialmente cuando se somete a fuerzas externas. Cuando la fuerza externa alcanza un cierto límite, la pieza de trabajo comienza a experimentar una deformación plástica. A medida que aumenta la fuerza externa, aumenta la deformación plástica. El propósito del laminado longitudinal en el laminado de acero es obtener elongación. Durante el proceso de laminación de acero, las moléculas se extienden longitudinalmente y se expanden lateralmente, lo que resulta en una reducción en el espesor de la pieza de trabajo sin un cambio en la densidad.
Por otro lado, las láminas de electrodos de batería implican la aplicación de lechada compuesta sobre sustratos como papel de aluminio o papel de cobre. La compactación con rodillo de las láminas de electrodos tiene como objetivo compactar las partículas de pasta conductoras de electricidad en las láminas. Su propósito es aumentar la densidad compactada de las láminas de electrodos. La densidad compactada adecuada puede mejorar la capacidad de descarga de la batería, reducir la resistencia interna y prolongar el ciclo de vida de la batería. Las partículas de pasta conductoras de electricidad sufren desplazamiento y deformación cuando se someten a presión durante el proceso de compactación. La densidad de la lámina de electrodos sigue un cierto patrón con la variación de la presión, como se muestra en la Figura 3.
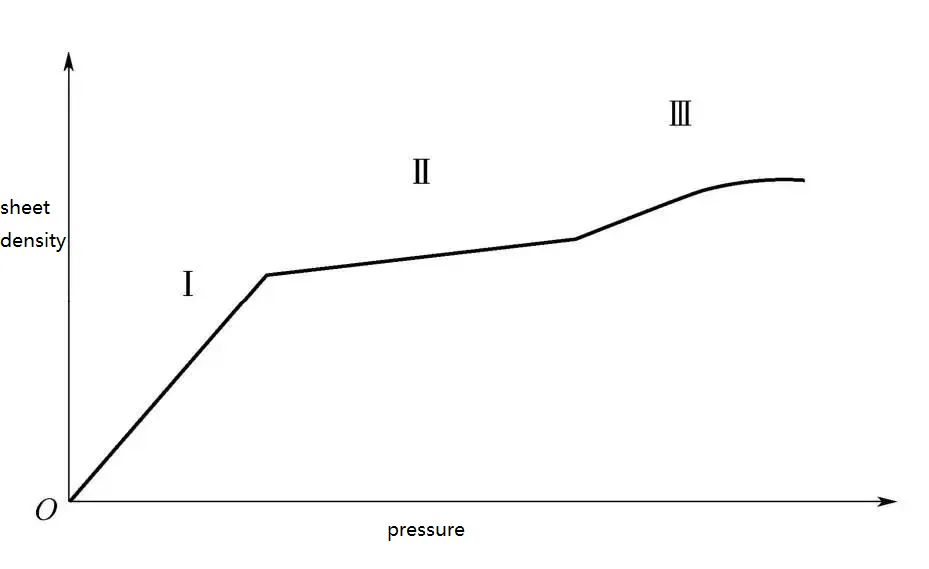
En la Región I, a medida que aumenta la presión de contacto, las partículas de pasta conductoras de electricidad comienzan a sufrir un desplazamiento a pequeña escala, que aumenta gradualmente. En esta etapa, los espacios entre las partículas de pasta se llenan gradualmente, lo que resulta en un aumento lento en la densidad relativa de la lámina de electrodos.
En la Región II, después de que la densidad de las partículas de pasta ha aumentado ligeramente en la Región I, un mayor aumento en la presión de contacto conduce a un llenado continuo de los espacios entre las partículas. A medida que la compactación avanza en la Región II, los espacios entre las partículas se comprimen por completo, lo que resulta en un rápido aumento en la densidad relativa de la lámina de electrodos. La tasa de aumento de la densidad relativa es mucho mayor que la de la Región I, y en esta región se produce cierta deformación de las partículas en pasta.
En la Región III, una vez que los espacios entre las partículas de pasta se han llenado por completo en la Región II, las partículas ya no experimentan desplazamiento. Sin embargo, a medida que aumenta la presión de contacto, las partículas de pasta comienzan a sufrir una deformación significativa. En esta etapa, la densidad relativa de la lámina de electrodos no aumenta rápidamente con el aumento de la presión de contacto. En cambio, la lámina del electrodo se endurece y el cambio en la densidad relativa se convierte en una curva suave.
- Factores que afectan a la calidad de laminación
Los problemas de calidad de las láminas de electrodos de batería causados por la máquina calandradora se manifiestan principalmente en el grosor desigual de las láminas después del laminado. La inconsistencia en el grosor conduce a variaciones en la densidad compactada de las láminas de electrodos, que es un factor crítico que afecta la consistencia del rendimiento de la batería. La uniformidad del espesor de la lámina de electrodo incluye tanto la uniformidad del espesor transversal como la uniformidad del espesor longitudinal, como se muestra en la Figura 4, y tienen diferentes causas.
Los principales factores que influyen en la falta de uniformidad del espesor transversal de la lámina de electrodos incluyen la deformación por flexión de los rodillos rodantes, la rigidez del bastidor de la máquina, la deformación elástica de los principales componentes del soporte de tensión, la fuerza de compactación y el ancho de la lámina. Durante el funcionamiento de la máquina calandradora, la fuerza de compactación provoca deformación en los rodillos y en el bastidor de la máquina, lo que en última instancia resulta en una deformación por deflexión de los rodillos. Esto conduce al fenómeno de que la hoja es más gruesa en el medio y más delgada en los lados en la dirección transversal.
Los principales factores que influyen en la falta de uniformidad del espesor longitudinal de la lámina de electrodos incluyen la precisión del procesamiento y la precisión de la instalación de los rodillos rodantes, los cojinetes y los asientos de los cojinetes. Los errores de mecanizado de los componentes críticos pueden causar fluctuaciones periódicas en la fuerza de compactación aplicada a la hoja a medida que giran los rodillos, lo que resulta en un espesor compactado no uniforme en la dirección longitudinal de la lámina.
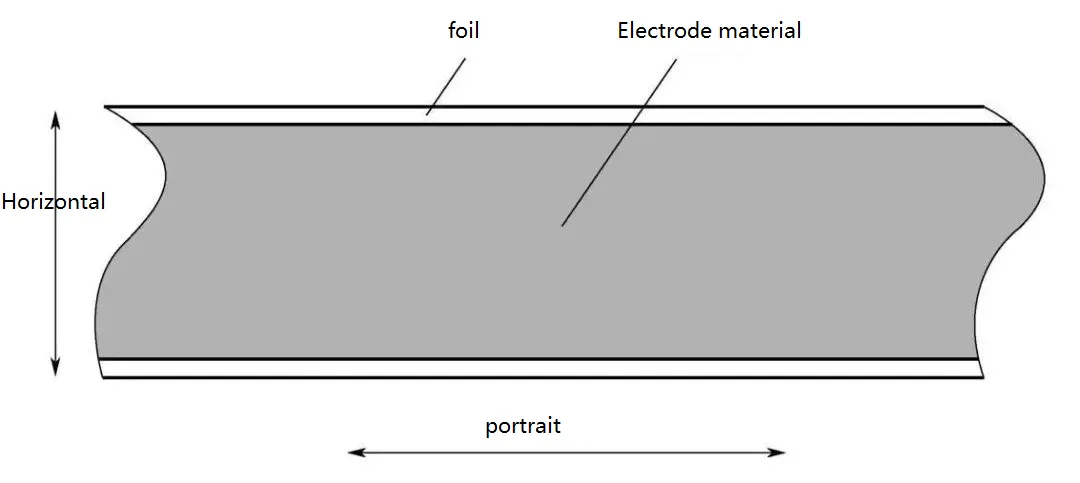
02 Composición estructural y clasificación demáquina de calandrado
2.1 Estructura básica demáquina de calandrado
La configuración estándar de una máquina calandradora de alta precisión para láminas de electrodos de batería consta de un marco en forma de H montado verticalmente, con dos rodillos dispuestos horizontalmente, y un cilindro hidráulico montado debajo que aplica presión hacia arriba. El espacio entre rodillos se ajusta mediante un reductor de servomotor y la máquina está montada sobre una base integral. Los ejes de salida dobles del reductor están conectados al reductor de velocidad a través de un acoplamiento universal. Esta configuración garantiza una alta precisión en el proceso de calandrado. El diagrama esquemático de la máquina calandradora modelo estándar se muestra en la Figura 5.
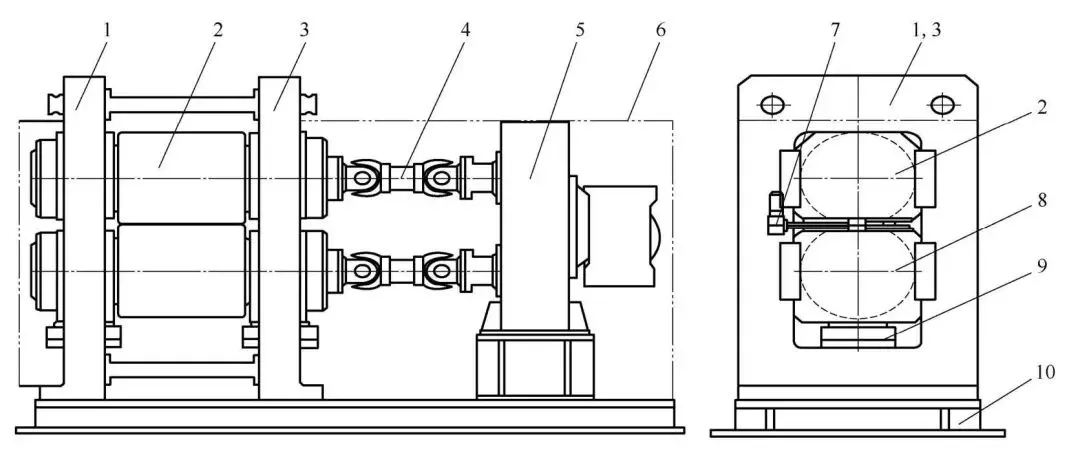
1—Marco izquierdo; 2—Sistema de balanceo superior; 3—Marco derecho; 4—Acoplamiento universal; 5—Reductor de velocidad de eje de salida doble; 6—Cubierta; 7—Mecanismo de ajuste de espacio entre rodillos; 8—Sistema de balanceo inferior; 9—Cilindro hidráulico; 10—Base.
Como se muestra en la Figura 5, la máquina calandradora consta principalmente del bastidor, los rodillos y los componentes principales de la transmisión. El marco sirve como base de todo el sistema y debe tener suficiente rigidez y resistencia para minimizar la deformación. El dispositivo hidráulico aplica la fuerza de compactación a los rodillos a través de los asientos de los cojinetes. El motor y el reductor permiten la rotación sincrónica de los dos rodillos, proporcionando par a los rodillos y asegurando un proceso de calandrado continuo. El mecanismo de ajuste del espacio entre rodillos consta de dos cuñas de ajuste del espacio, que se utilizan para ajustar el espacio entre los dos rodillos para cumplir con los requisitos de espesor de diferentes láminas de electrodos.
2.2 Forma estructural de la máquina principal de la máquina calandradora
(1) Clasificación basada en el tipo de rollo. Los rodillos principales de la máquina calandradora se pueden dividir en dos formas: rodillos curvos y rodillos rectos, como se muestra en la Figura 6. La estructura con rodillos rectos (modelo estándar) tiene un asiento de rodamiento con mecanismos internos para eliminar el juego radial de los rodamientos principales y proporcionar posicionamiento axial. La estructura con rodillos curvos utiliza un cilindro de rodillos curvos para eliminar el juego radial de los rodamientos principales y reducir o eliminar la deformación por deflexión de la superficie del rodillo.
Cuando el ancho de la lámina de electrodo compactada es relativamente estrecho, la relación entre el ancho de la superficie del rodillo y el diámetro de la superficie del rodillo es cercana a 1:1, y se puede descuidar la deformación por deflexión durante la compactación de la lámina de electrodo, se recomienda utilizar el modelo estándar sin rodillos curvos.
Cuando el ancho de la lámina de electrodo compactado es relativamente amplio, la relación entre el ancho de la superficie del rodillo y el diámetro de la superficie del rodillo es superior a 1,2:1 y la deformación por deflexión durante la compactación de la lámina de electrodos es superior a 0,5 μm, se recomienda utilizar un modelo con rodillos curvos.
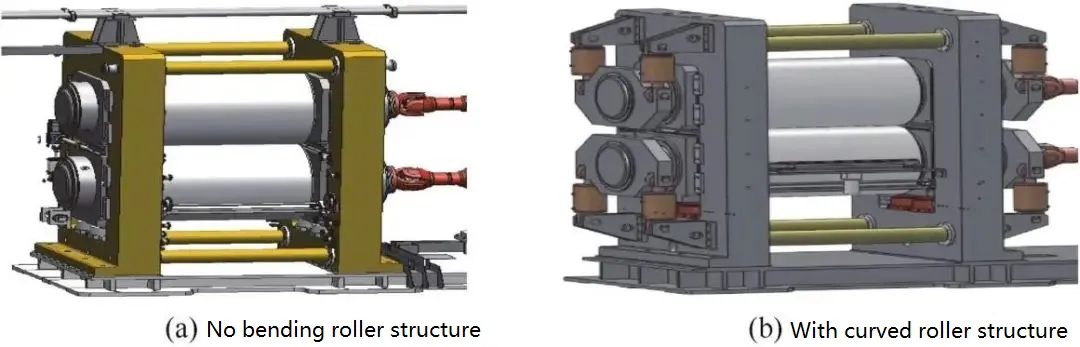
(2) Clasificación basada en el modo de conducción. La máquina compactadora de rodillos se puede clasificar en estructura de accionamiento de un solo motor y estructura de accionamiento de doble motor, como se muestra en la Figura 7.
La estructura de accionamiento de un solo motor utiliza un motor de accionamiento, un reductor, un reductor de velocidad, un acoplamiento universal y una transmisión de rodillos para lograr la sincronización mecánica de los rodillos a través del reductor de velocidad.
La estructura de accionamiento de doble motor adopta un motor de accionamiento, un reductor, un acoplamiento universal y una transmisión de balanceo. Emplea motores síncronos controlados por electrónica para lograr la sincronización mecánica de los rodillos.
El par motor de la máquina calandradora es proporcional a la velocidad de calandrado, el ancho de la superficie del rodillo y la presión entre rodillos. Cuando el ancho de la superficie del rodillo y la presión permanecen relativamente constantes, una velocidad más alta requiere un mayor par de accionamiento y una mayor potencia del motor. En los casos en que se requiere una alta velocidad y una potencia de motor significativa, la máquina calandradora puede ser accionada por dos motores síncronos.
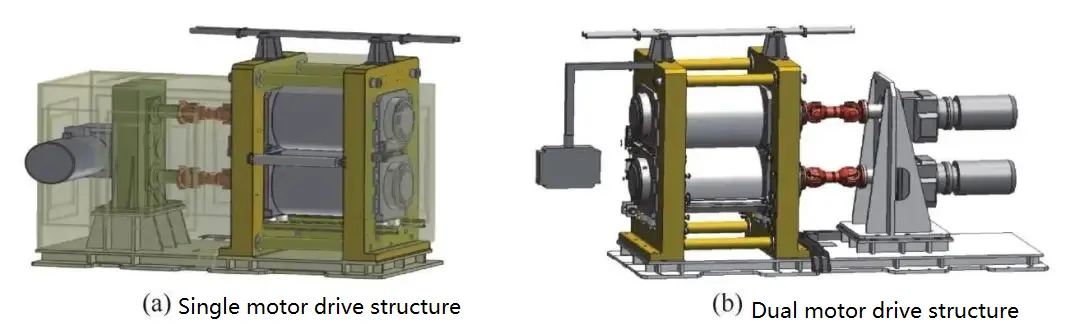
(3) Clasificación basada en el método de prensado. La máquina compactadora de rodillos se puede dividir en una estructura de apriete de tornillo mecánico y una estructura de apriete de cilindro hidráulico, como se muestra en la Figura 8.
La estructura mecánica de apriete de tornillos aplica presión principalmente a los rodillos en la lámina de electrodos ajustando el valor del espacio entre rodillos. No requiere dispositivos de presurización adicionales. Por lo tanto, la presión real es generalmente relativamente pequeña, lo que limita la densidad de compactación de la lámina de electrodos durante la compactación con rodillos.
La estructura de apriete del cilindro hidráulico implica el montaje de cilindros hidráulicos debajo de los asientos de los cojinetes en ambos extremos del sistema de rodillos inferiores, dentro del bastidor en forma de V. Los cilindros hidráulicos utilizan cilindros de émbolo para empujar hacia arriba y aplicar presión. Bajo la acción de los cilindros de émbolo, el sistema de rodillo inferior se mueve hacia arriba y ejerce presión de compactación del rodillo. Al aplicar presión con los cilindros hidráulicos, se puede lograr una presión estable y se pueden ejercer presiones más altas. Este método es actualmente el principal método de prensado utilizado.
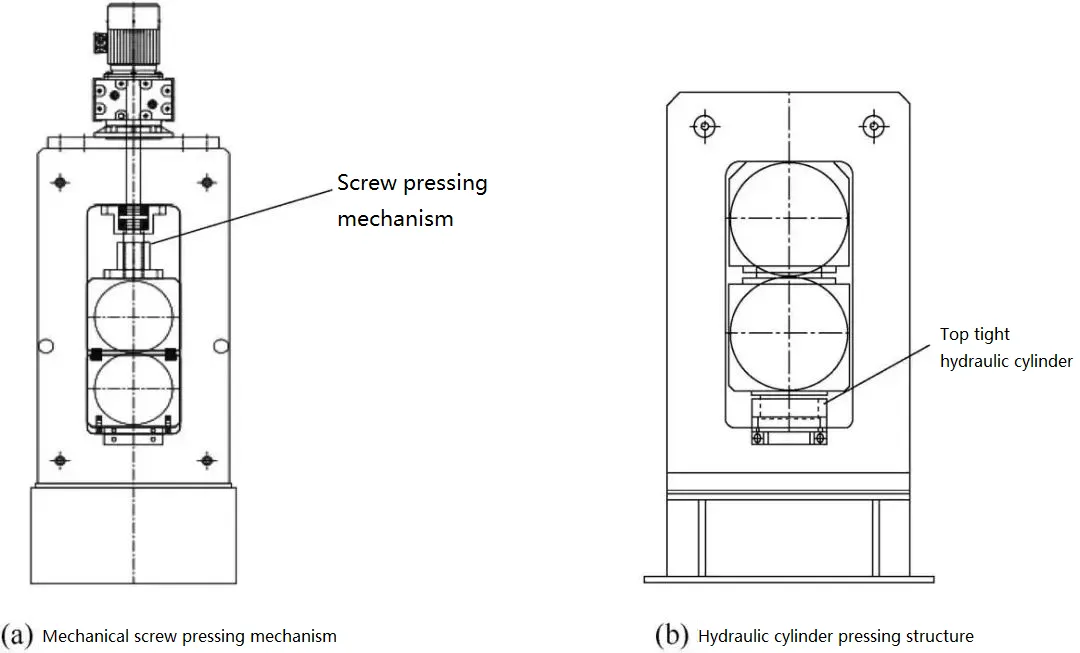
2.3 En China, la mayoría de las máquinas calandradoras para láminas de electrodos de baterías de litio realizan la compactación a temperatura ambiente. Durante el proceso de compactación, la lámina de electrodos exhibe un rebote significativo, por lo que es beneficioso precalentar la lámina de electrodos a una cierta temperatura antes de la compactación. El propósito del precalentamiento es el siguiente: secar la lámina de electrodo y reducir su contenido de humedad, reducir la tasa de rebote de la lámina de electrodo después de la compactación, eliminar parte de la tensión interna residual en la lámina de electrodo después de la compactación y ablandar o derretir el aglutinante en la superficie de la lámina de electrodo mediante calentamiento, lo que mejora la adherencia entre el material activo y el colector de corriente, facilitando una mejor absorción de electrolitos. Para calentar la lámina de electrodos, se instala una caja de calentamiento antes de la máquina compactadora de rodillos para calentar la lámina de electrodos. El aire dentro de la caja de calentamiento se calienta y luego el aire calentado se usa para calentar la lámina de electrodos. Sin embargo, este método tiene una baja eficiencia de calentamiento debido a la distancia entre la caja de calentamiento y los rollos, lo que resulta en una rápida pérdida de calor y un calentamiento ineficaz. Actualmente, el método ampliamente utilizado es la máquina calandradora en caliente, donde los rodillos de la máquina se calientan primero y luego los rodillos calentados se utilizan para compactar la lámina de electrodo de la batería de litio. El calentamiento de los rollos se puede lograr a través de un calentamiento externo o un calentamiento interno, y varios métodos de calentamiento comunes se describen a continuación:
(1) Calentamiento externo de los rodillos mediante inducción electromagnética. Las bobinas de inducción se colocan fuera de los rodillos. Cuando las bobinas están energizadas, la inducción electromagnética genera corrientes de Foucault dentro de los rodillos, calentando así los rollos. Este método de calentamiento tiene las ventajas de un bajo consumo de energía, una alta tasa de conversión térmica y un control preciso de la temperatura de la superficie del rodillo durante la compactación. Sin embargo, también tiene algunos inconvenientes, como el alto costo y las dificultades para organizar el cableado a lo largo de la circunferencia de los rollos.
(2) Calentar los rollos con una caja de calentamiento externa. La caja de calentamiento se coloca por encima o por debajo de los panecillos, y se utiliza aire a alta temperatura para hornear los panecillos desde el exterior. El calor se transfiere a la superficie de trabajo de los rodillos a través del aire como medio de transferencia de calor, logrando el propósito de calentar los rodillos. Sin embargo, este método tiene serios problemas: es difícil controlar la temperatura de la superficie del rodillo, la distribución de la temperatura en la superficie del rodillo es desigual, las altas temperaturas localizadas pueden dañar los rodillos y consume una gran cantidad de energía con una pérdida de energía significativa.
(3) Calentar los rollos desde el interior utilizando componentes electrónicos como cables de resistencia. Por lo general, los elementos calefactores tubulares o los cables de resistencia se insertan en la parte interna de los rodillos de trabajo o rodillos de soporte. Al conectar un extremo de los rollos a una fuente de alimentación, los rollos se calientan. Este método de calentamiento tiene las ventajas de no dañar la estructura externa de los rodillos, simplicidad y facilidad de implementación. El proceso de calentamiento comienza desde el núcleo del rodillo y el calor se conduce desde el núcleo hasta la superficie de trabajo de los rodillos, lo que da como resultado un enfoque de calentamiento intermedio primero. Sin embargo, este método aumenta el estrés térmico en los rodillos durante el proceso de calentamiento. Para rodillos de mayor diámetro, el tiempo de transferencia de calor es largo, lo que lo hace menos sensible al ajuste de la temperatura de la superficie del rodillo y requiere ciclos de ajuste más largos. Además, se producen altas temperaturas localizadas en las posiciones de los rodamientos, lo que provoca dificultades en la lubricación.
(4) Calentar los panecillos con aceite de transferencia de calor. Calentar los rollos con aceite de transferencia de calor es un método ampliamente utilizado tanto a nivel nacional como internacional. Se crean conductos internos de aceite dentro de los rodillos, y el aceite de transferencia de calor calentado se introduce en los rodillos a través de juntas giratorias, calentando los rodillos a través de la conducción térmica. El aceite de transferencia de calor puede funcionar de manera estable a temperaturas de hasta 200 °C. Este método es seguro, respetuoso con el medio ambiente y tiene poco ruido. El sistema de circulación de aceite de transferencia de calor tiene una precisión de alta temperatura, lo que facilita el control de la temperatura de entrada del aceite de transferencia de calor. Al controlar el caudal del aceite de transferencia de calor en la entrada, se produce una transferencia de calor por convección forzada entre el aceite de transferencia de calor y los rodillos, aumentando el coeficiente de transferencia de calor convectivo entre ellos y maximizando la transferencia de calor entre ellos. Esto asegura que la superficie del rollo mantenga un rango de temperatura constante y tenga una buena uniformidad, cumpliendo con los requisitos de temperatura para la mayoría de los rollos.