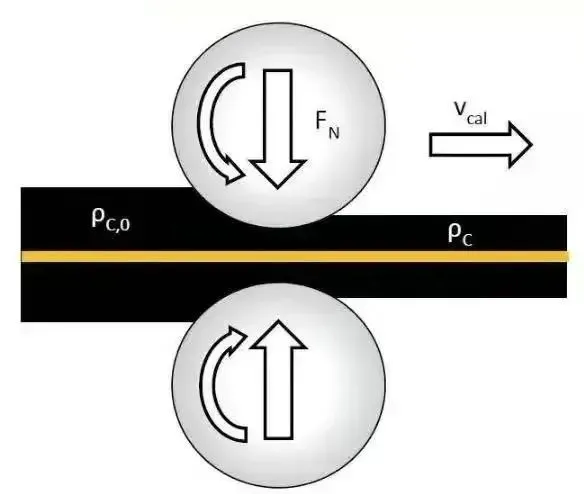
01転造品質の機能、原理、影響要因カレンダー加工機
- の機能カレンダー加工機
カレンダー加工は、コーティングされ部分的に乾燥したリチウム電池電極シートを圧縮するプロセスです。電極シートのカレンダー加工により、リチウム電池のエネルギー密度が増加し、電極材料が集電体にしっかりと取り付けられているため、サイクリング中の脱落による電池エネルギーの損失が防止されます。カレンダー加工の前に、コーティングされた電極シートをある程度乾燥させて、圧縮中にコーティングが剥がれるのを防ぐ必要があります。また、プロセス中の締固めレベルを制御することも重要です。過度の圧縮は、集電体近くの電極材料に影響を及ぼし、リチウムイオンの適切な挿入と抽出を妨げ、活物質が密着して集電体から容易に剥離する可能性があります。ひどい場合、電極シートの過度の可塑性は破損を引き起こし、圧縮後の巻線プロセスを妨げる可能性があります。カレンダー加工は、リチウム電池電極の製造において最も重要なプロセスの1つであり、その精度は電池の性能に大きく影響します。カレンダー加工の目的は、電極シートの滑らかで平らな表面を維持して、セパレーターに穴を開ける突起によって引き起こされる潜在的な短絡を防ぎ、バッテリーのエネルギー密度を向上させることです。また、圧縮プロセスにより電極シートの体積が減少するため、リチウム電池のエネルギー密度、サイクル寿命、安全性能が向上します。
- 電極シートの原理カレンダー
カレンダー加工の目的は、活物質と箔との間に、より緻密で均一に結合された接続を実現することです。ローラーの圧縮プロセスは、コーティングが完了し、電極シートが乾燥された後に実行する必要があります。そうしないと、圧縮中に粉末の脱落や層の層間剥離などの問題が発生する可能性があります。電池電極シートは、導電性ペースト粒子で両面に銅(またはアルミニウム)箔をコーティングしたものです。コーティングおよび乾燥プロセスを経た後、電極シートはローラー圧縮にかけられます。圧縮に先立ち、銅(またはアルミニウム)箔上の導電性ペーストのコーティングは、個々のまたは弱く結合した粒子またはクラスターで構成される半流動の半固体粒状媒体であり、特定の分散性と流動性を示します。導電性ペースト粒子の間には隙間があり、圧縮プロセス中に粒子が小さな変位を受けて隙間を埋め、圧縮下での相互位置決めを達成することができます。電池電極シートのカレンダー加工は、半固体の導電性ペースト粒子を非密封状態で連続的に圧縮するプロセスと考えることができます。導電性のペースト粒子は、銅(またはアルミニウム)箔の表面に付着し、摩擦力によってローラー間の隙間に連続的に引き込まれ、一定の密度で電極シートに圧縮されます。カレンダー加工の原理を図2 に示します。
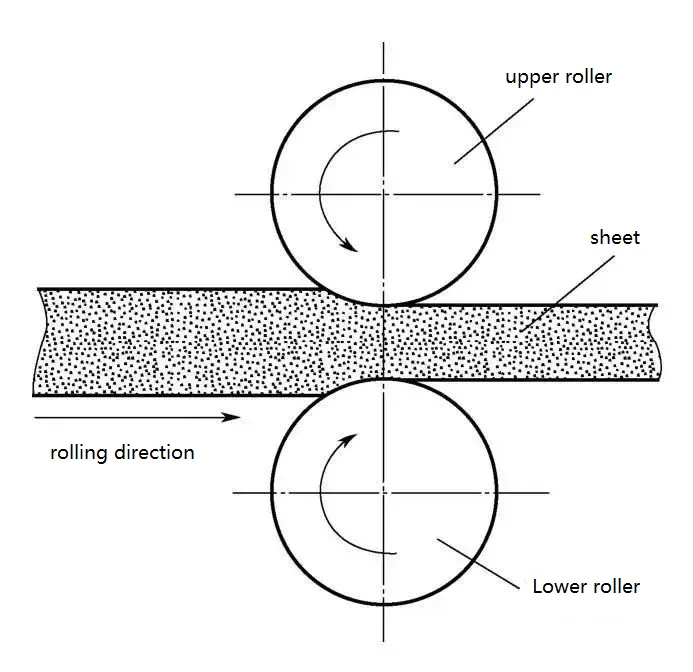
電池電極シートの圧延は、鋼の圧延とは大きく異なります。鋼が転造されるとき、ワークピースは外力を受けると最初に弾性変形を受けます。外力が一定の限界に達すると、ワークピースは塑性変形を経験し始めます。外力が増加すると、塑性変形が増加します。鋼材圧延における縦圧延の目的は、伸びを得ることです。鋼の圧延プロセス中、分子は縦方向に伸びて横方向に膨張するため、密度が変わることなくワークピースの厚さが減少します。
一方、バッテリー電極シートには、アルミホイルや銅箔などの基板にコンパウンドスラリーを塗布することが含まれます。電極シートのローラー圧縮は、シート上の導電性ペースト粒子を圧縮することを目的としています。その目的は、電極シートの圧縮密度を高めることです。適切な圧縮密度により、バッテリーの放電容量を高め、内部抵抗を減らし、バッテリーのサイクル寿命を延ばすことができます。導電性ペースト粒子は、圧縮プロセス中に圧力を受けると、変位と変形を受けます。電極シートの密度は、図3に示すように、圧力の変化に伴って特定のパターンに従います。
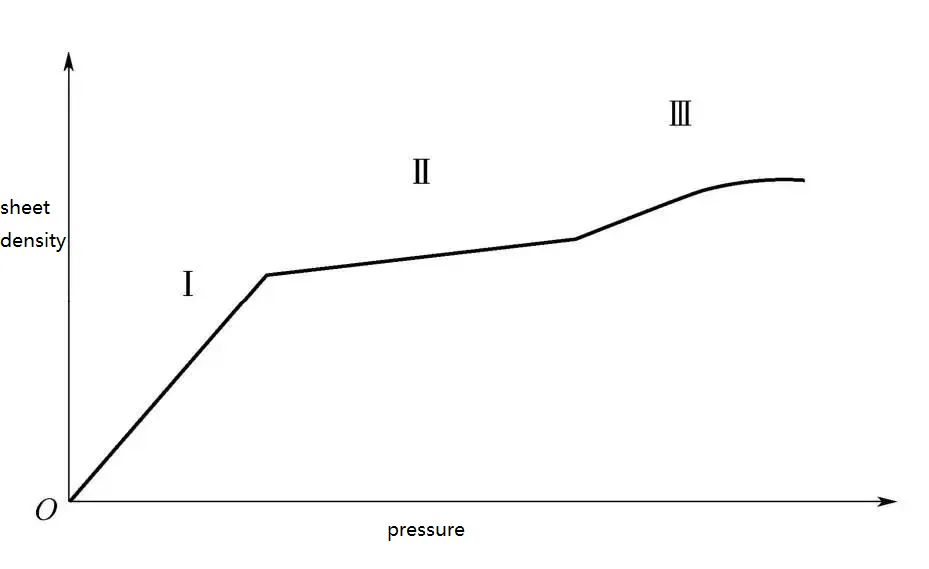
領域Iでは、接触圧力が増加すると、導電性ペースト粒子は小さな変位を受け始め、徐々に増加します。この段階では、ペースト粒子間の隙間が徐々に埋められ、電極シートの相対密度がゆっくりと増加します。
領域IIでは、ペースト粒子の密度が領域Iでわずかに増加した後、接触圧力がさらに増加すると、粒子間のギャップが継続的に充填されます。領域IIで圧縮が進行すると、粒子間のギャップが完全に圧縮され、電極シートの相対密度が急速に増加します。相対密度の増加率は領域Iよりもはるかに高く、この領域ではペースト粒子の変形がいくらか発生します。
領域IIIでは、ペースト粒子間のギャップが領域IIで完全に埋められた後、粒子はもはや変位を受けません。ただし、接触圧力が増加すると、ペースト粒子は大きな変形を受け始めます。この段階では、電極シートの相対密度は接触圧力の増加に伴って急速に増加しません。代わりに、電極シートは硬化し、相対密度の変化は緩やかな曲線になります。
- 圧延品質に影響を与える要因
カレンダー加工機によって引き起こされるバッテリー電極シートの品質問題は、主に圧延後のシートの厚さの不均一に現れます。厚さの不一致は、電極シートの圧縮密度のばらつきにつながり、これはバッテリー性能の一貫性に影響を与える重要な要因です。電極シートの厚さの均一性には、図4に示すように、横方向の厚さの均一性と縦方向の厚さの均一性の両方が含まれ、それぞれに異なる原因があります。
電極シートの横方向の厚さの不均一性に影響を与える主な要因には、ローリングロールの曲げ変形、機械フレームの剛性、主要な応力軸受部品の弾性変形、圧縮力、およびシートの幅が含まれます。カレンダー加工機の運転中、圧縮力によりローリングロールと機械フレームが変形し、最終的にロールのたわみ変形が発生します。これにより、シートは横方向の側面が中央で厚くなり、側面が薄くなるという現象につながります。
電極シートの縦方向の厚さの不均一性に影響を与える主な要因には、ローリングロール、ベアリング、およびベアリングシートの加工精度と取り付け精度が含まれます。重要な部品の加工誤差により、ロールが回転するときにシートに加えられる圧縮力が周期的に変動し、シートの長手方向の圧縮厚さが不均一になる可能性があります。
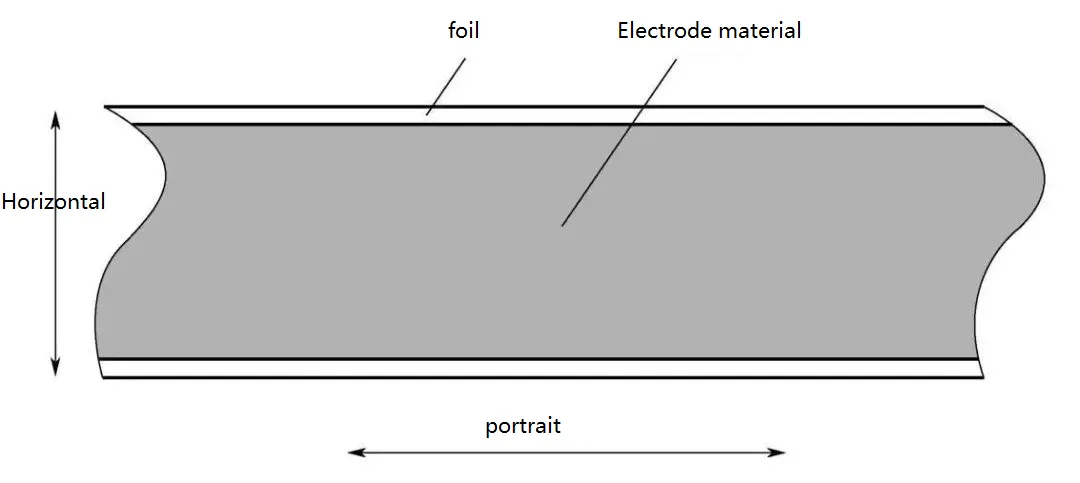
02構造構成と分類カレンダー加工機
2.1 の基本構造カレンダー加工機
電池電極シート用高精度カレンダー加工機は、2本のロールを水平に並べたH字型フレームを縦に取り付け、下に油圧シリンダーを取り付けて圧力を上向きにするという構造が標準です。ロールギャップはサーボモーター減速機によって調整され、機械は一体型ベースに取り付けられます。減速機のデュアル出力シャフトは、ユニバーサルカップリングを介して減速機に接続されています。この構成により、カレンダー加工工程で高い精度が保証されます。標準モデルのカレンダー加工機の概略図を図5に示します。
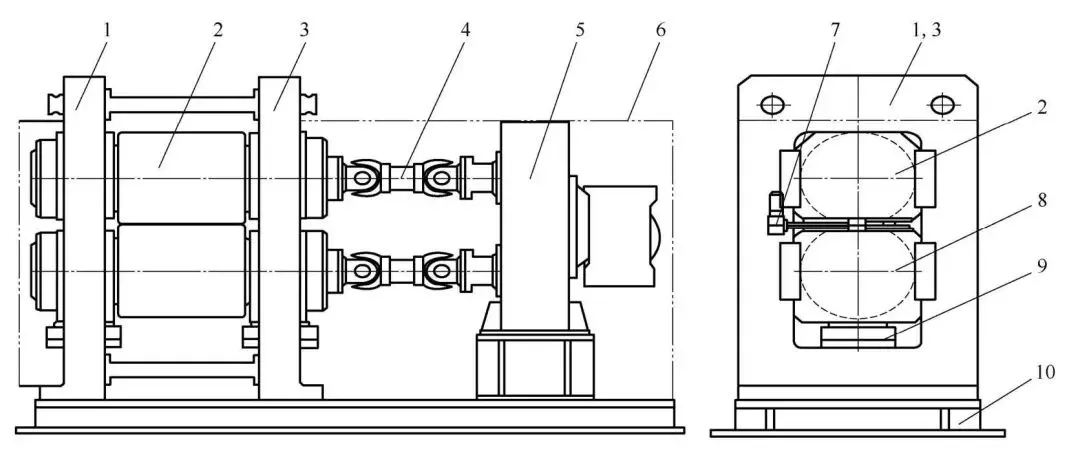
1 -左フレーム。2-アッパーロールシステム。3 -右フレーム。4-ユニバーサルカップリング。5-デュアル出力シャフト減速機。6—カバー;7-ロールギャップ調整機構。8-下部ロールシステム。9 -油圧シリンダー。10 - ベース。
図5に示すように、カレンダー加工機は主にフレーム、ロール、および主要なトランスミッションコンポーネントで構成されています。フレームはシステム全体の基盤として機能し、変形を最小限に抑えるために十分な剛性と強度を備えている必要があります。油圧装置は、ベアリングシートを介してロールに圧縮力を加えます。モーターと減速機により、2つのロールの同期回転が可能になり、ロールにトルクが供給され、連続的なカレンダー加工プロセスが保証されます。ロールギャップ調整機構は、2つのギャップ調整ウェッジで構成されており、2つのロール間のギャップを調整して、異なる電極シートの厚さ要件を満たすために使用されます。
2.2カレンダー機のメインマシンの構造形態
(1)ロールタイプによる分類。カレンダー加工機のメインロールは、図6に示すように、湾曲ロールとストレートロールの2つの形態に分けることができます。ストレートロール構造(標準モデル)は、メインベアリングのラジアルクリアランスを排除し、軸方向の位置決めを可能にする内部機構を備えたベアリングシートを備えています。湾曲したロールを備えた構造は、湾曲したロールシリンダーを使用して、メインベアリングのラジアルクリアランスを排除し、ロール表面のたわみ変形を低減または排除します。
圧縮された電極シートの幅が比較的狭い場合、ロール表面の幅とロールの表面直径の比率が1:1に近く、電極シートの圧縮中のたわみ変形を無視できる場合は、湾曲したロールのない標準モデルを使用することをお勧めします。
圧縮された電極シートの幅が比較的広く、ロール表面の幅とロールの表面直径の比率が1.2:1を超え、電極シートの圧縮中のたわみ変形が0.5μmを超える場合は、ロールが湾曲したモデルを使用することをお勧めします。
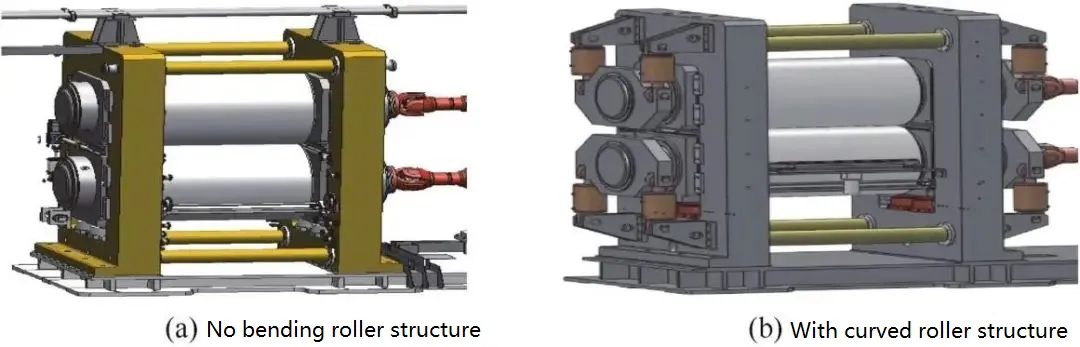
(2)運転モードによる分類。ローラー圧縮機は、図7に示すように、シングルモーター駆動構造とデュアルモーター駆動構造に分類できます。
シングルモーター駆動構造は、駆動モーター、減速機、減速機、ユニバーサルカップリング、およびロールトランスミッションを利用して、減速機を介してロールの機械的同期を実現します。
デュアルモーター駆動構造は、駆動モーター、減速機、ユニバーサルカップリング、ロールトランスミッションを採用しています。これは、ロールの機械的な同期を達成するために、電子機器によって制御される同期モーターを採用しています。
カレンダー加工機の駆動トルクは、カレンダー加工速度、ロール表面幅、ロール間圧力に比例します。ロール表面の幅と圧力が比較的一定のままである場合、速度を速くすると、より大きな駆動トルクとより大きなモーター出力が必要になります。高速で大きなモーター出力が必要な場合、カレンダー加工機は2つの同期モーターで駆動できます。
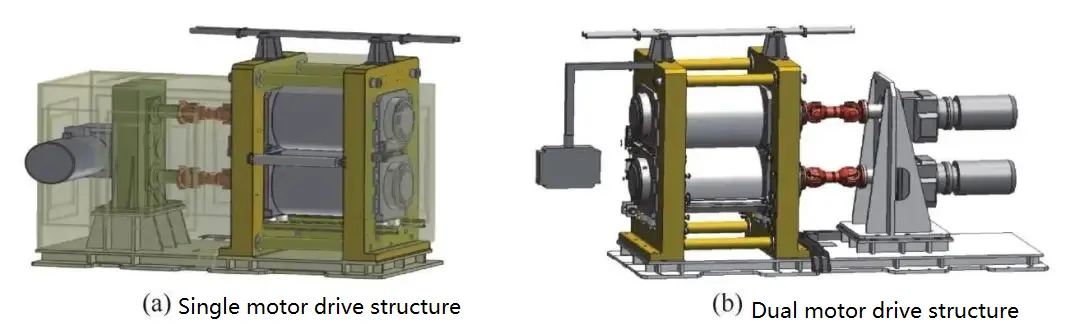
(3)プレス方法による分類。ローラー圧縮機は、図8に示すように、機械式ネジ締め構造と油圧シリンダー締め付け構造に分けることができます。
機械式ねじ締め構造は、ロールギャップ値を設定することにより、主に電極シート上のロールに圧力を加えます。追加の加圧装置は必要ありません。したがって、実際の圧力は一般に比較的小さく、ローラー圧縮中の電極シートの圧縮密度が制限されます。
油圧シリンダーの締め付け構造は、V字型フレームの内側、下部ロールシステムの両端にあるベアリングシートの下に油圧シリンダーを取り付けることを含みます。油圧シリンダーは、プランジャーシリンダーを使用して上向きに押し上げ、圧力を加えます。プランジャーシリンダーの作用により、下部ロールシステムが上方に移動し、ロール圧縮圧力がかかります。油圧シリンダを使用して圧力をかけることで、安定した圧力を得ることができ、より高い圧力をかけることができます。この方法は、現在主流のプレス方法として使用されています。
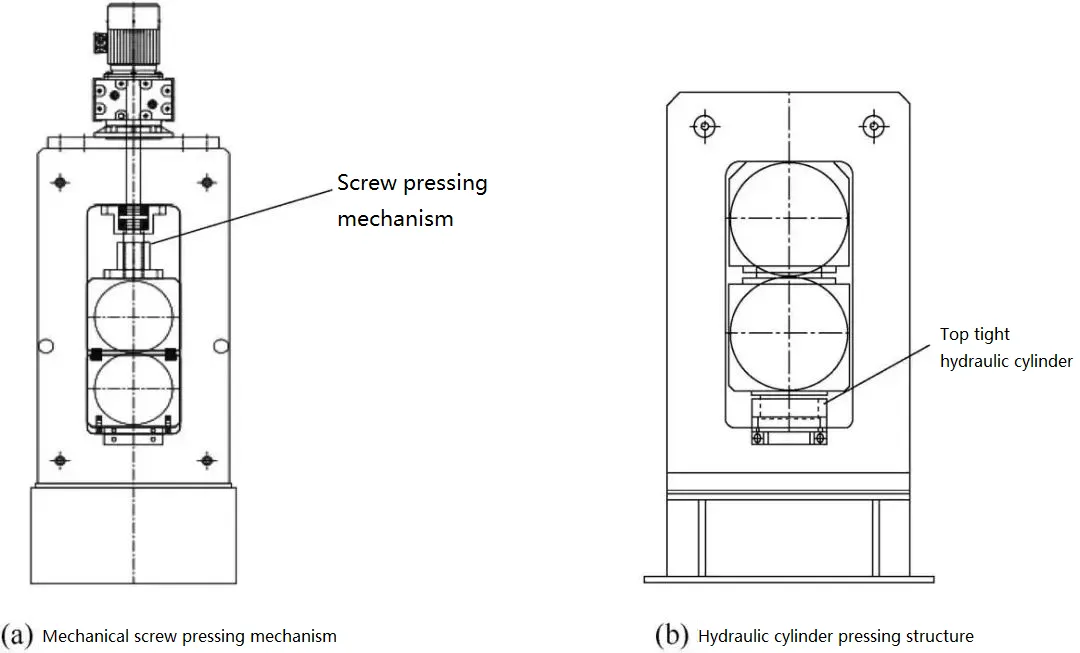
2.3中国では、リチウム電池電極シート用のカレンダー加工機のほとんどが室温で圧縮を行っています。圧縮プロセス中、電極シートは大きな反発を示すため、圧縮前に電極シートを特定の温度に予熱すると有益です。予熱の目的は次の通りです:電極シートを乾燥させて含水率を減らすため、圧縮後の電極シートの反発率を減らすため、圧縮後の電極シートの残留内部応力の一部を排除するため、および加熱によって電極シート表面のバインダーを柔らかくまたは溶融するため、 これにより、活物質と集電体との密着性が向上し、電解質の吸収が促進されます。電極シートを加熱するために、ローラー圧縮機の前に加熱ボックスを設置して電極シートを加熱します。加熱ボックス内の空気が加熱され、加熱された空気を使用して電極シートが加熱されます。しかし、この方法は、加熱ボックスとロールとの距離が長いため、加熱効率が低く、熱損失が急激に発生し、加熱が不十分になります。現在、広く使用されている方法はホットカレンダー機であり、機械のロールが最初に加熱され、次に加熱されたロールを使用してリチウム電池電極シートが圧縮されます。ロールの加熱は、外部加熱または内部加熱によって実現でき、いくつかの一般的な加熱方法は次のとおりです。
(1)電磁誘導によるロールの外部加熱。インダクションコイルはロールの外側に配置されます。コイルに通電すると、電磁誘導によりロール内部に渦電流が発生し、ロールが加熱されます。この加熱方法には、低エネルギー消費、高い熱変換率、および圧縮中のロール表面温度の正確な制御という利点があります。しかし、コストが高いことや、ロールの円周に沿った配線配置が難しいなど、いくつかの欠点もあります。
(2)外部加熱ボックスを使用してロールを加熱します。加熱ボックスはロールの上または下に配置され、高温の空気を使用してロールを外部から焼きます。熱は熱伝達媒体として空気を介してロールの作業面に伝達され、ロールを加熱する目的を達成します。しかし、この方法には深刻な問題があります:ロール表面の温度制御が困難である、ロール表面の温度分布が不均一である、局所的な高温はロールを損傷する可能性がある、そしてそれは大量のエネルギーを消費し、大きなエネルギー損失。
(3)抵抗線などの電子部品を使用してロールを内側から加熱します。通常、管状の発熱体または抵抗線は、作業ロールまたはサポートロールの内部部分に挿入されます。ロールの一端を電源に接続することにより、ロールが加熱されます。この加熱方法には、ロールの外部構造を損傷しない、単純、および実装が容易であるという利点があります。加熱プロセスはロールコアから始まり、熱はコアからロールの作業面に伝導されるため、中間優先の加熱アプローチになります。ただし、この方法では、加熱プロセス中にロールにかかる熱応力が増加します。大径のロールの場合、熱伝達時間が長いため、ロール表面温度の調整に敏感になりにくく、調整サイクルが長くなります。さらに、ベアリング位置で局所的な高温が発生し、潤滑が困難になります。
(4)伝熱油を使用してロールを加熱します。ロールを伝熱油で加熱することは、国内外で広く使用されている方法です。ロール内には内部油路が作られ、加熱された伝熱油がロータリージョイントを通じてロールに導入され、熱伝導によってロールが加熱されます。伝熱油は200°Cまでの温度で安定して運転できます。 この方法は安全で、環境に優しく、騒音が少ないです。伝熱油循環システムは高温精度を備えているため、伝熱油の入口温度を簡単に制御できます。入口での伝熱油の流量を制御することにより、伝熱油とロールの間に強制対流熱伝達が発生し、それらの間の対流熱伝達係数が増加し、それらの間の熱伝達が最大化されます。これにより、ロール表面は一定の温度範囲を維持し、良好な均一性を確保し、ほとんどのロールの温度要件を満たすことができます。