El contenido de agua tiene un impacto significativo en el rendimiento de la batería y debe controlarse estrictamente durante el proceso de fabricación. La presencia de agua en las baterías puede causar la degradación del electrolito o reaccionar con el electrolito para producir gases nocivos, lo que provoca un aumento de la presión y la deformación dentro de la batería. El contenido excesivo de agua en las baterías también puede resultar en una alta resistencia interna, alta autodescarga, baja capacidad, bajo rendimiento de ciclo e incluso fugas, lo que degrada en gran medida el rendimiento de la batería. Por lo tanto, un proceso de secado es esencial en la producción de baterías de litio.
01 Introducción al secado
El secado es una operación de unidad química que consiste en proporcionar energía a los materiales húmedos para vaporizar y eliminar la humedad contenida, lo que resulta en la producción de materiales secos. Actualmente, existen numerosas opciones de equipos de secado en la industria, y se pueden clasificar utilizando diferentes métodos. Según el modo de funcionamiento, el equipo de secado se puede clasificar como equipo de secado continuo y equipo de secado por lotes (intermitente). De acuerdo con la presión de funcionamiento, se puede clasificar como equipo de secado atmosférico y equipo de secado al vacío. Además, según el método de transferencia de calor, los equipos de secado se pueden clasificar en equipos de secado por conducción, equipos de secado por convección, equipos de secado por radiación y equipos de secado dieléctrico, entre otros.
El contenido de agua en las baterías se origina principalmente en la humedad presente en las materias primas de la batería, incluidas las láminas de electrodos positivos y negativos, el separador, el electrolito y otros componentes metálicos, así como de la humedad en el entorno de la fábrica. Para hacer frente a la humedad ambiental, se puede establecer una sala seca, donde una secadora genera aire seco que se suministra continuamente a la sala seca, desplazando el aire húmedo y eliminando la humedad ambiental. Para la humedad interna en la batería, debido a los altos estándares de secado requeridos, que generalmente exigen un contenido de humedad entre (100-300)×10-6, generalmente se emplea un equipo de secado al vacío para eliminar el agua. Después del secado, las baterías se prueban para asegurarse de que cumplen con los requisitos de horneado. Múltiples pasos del proceso en la producción de baterías requieren un secado al vacío, como en el caso de los polvos de los electrodos de las baterías, el devanado de los electrodos positivos y negativos y el montaje de las celdas antes de la inyección de electrolitos. Por lo tanto, los equipos de secado al vacío son cruciales para la fabricación de baterías.
02 Principio del secado al vacío
El principio del secado al vacío se basa en el hecho de que el punto de ebullición del agua cambia en diferentes entornos de presión. La relación entre la presión y el punto de ebullición se muestra en la figura.
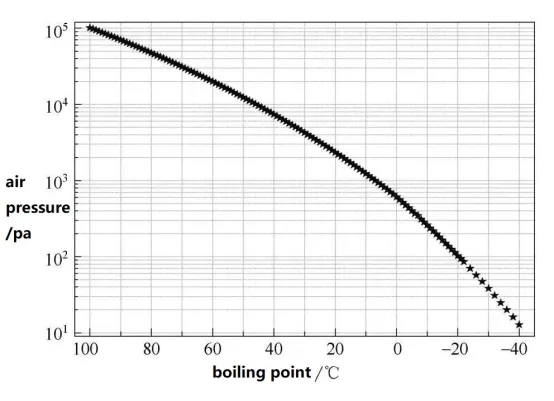
Se puede ver en la figura que a presión normal, es decir, una presión atmosférica, el punto de ebullición del agua es de 100 °C, pero a medida que disminuye la presión del aire, el punto de ebullición del agua continúa disminuyendo. En un entorno de vacío de unos 100 Pa, el punto de ebullición del agua ha descendido a unos -20 °C. Este es el principio básico de que un entorno de vacío puede promover el proceso de secado.
Por lo tanto, el secado al vacío es el proceso de eliminar la humedad contenida en los materiales en condiciones ambientales por debajo de una presión atmosférica estándar. El principio cinético básico del secado al vacío es la teoría de la transferencia de calor y masa. Durante el proceso de secado al vacío, el sistema de vacío calienta continuamente el material a secar durante la evacuación, de modo que la humedad dentro del material se difunde a la superficie a través de la diferencia de presión o la diferencia de concentración. Las moléculas de agua obtienen suficiente energía cinética en la superficie del material para superar la atracción mutua entre moléculas. Vuele hacia el espacio de baja presión de la cámara de vacío y sea aspirado por la bomba de vacío.
La tasa de pérdida de humedad durante el proceso de secado al vacío y la masa de humedad vaporizada y descargada del material seco por unidad de área de secado por unidad de tiempo son la velocidad de secado, es decir,
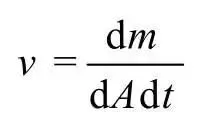
En la fórmula, v velocidad de secado, g/(m2·h); m masa de humedad descargada, g; Una zona de secado, m2; t tiempo de secado, h.
En el secado de las baterías, generalmente se presta más atención al contenido de humedad que a la calidad de la humedad. Además, el contenido de humedad en la batería es extremadamente pequeño y la calidad de la humedad evaporada es difícil de medir. Teniendo en cuenta que el cambio en el contenido de humedad se utiliza para reemplazar el cambio en la masa de humedad por unidad de área, la fórmula anterior se puede transformar en:
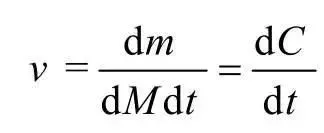
En la fórmula, v velocidad de secado, mg/(kg·h); m masa de humedad descargada, mg; M masa total del material, kg; C contenido de humedad, mg/kg; t tiempo de secado, h.
En la figura se muestra una curva típica de velocidad de secado al vacío. El proceso de pérdida de agua se divide en tres etapas: etapa de secado acelerado, etapa de secado a velocidad constante y etapa de secado desacelerado. La sección AB es la etapa de secado acelerado. En este momento, el contenido de humedad en el material es constante. Debido al aspirado y al calentamiento, el material se calienta a la temperatura de vaporización bajo la presión correspondiente dentro del rango de temperatura permitido y se vaporiza en grandes cantidades, y la velocidad de secado continúa aumentando. Debido a la limitación de las características de transferencia de calor y masa, la velocidad de secado alcanza el valor máximo e ingresa a la sección BC, que es la etapa de secado de velocidad constante. En este momento, la temperatura del material permanece sin cambios, el calor de calentamiento se utiliza como calor latente de vaporización y diversas pérdidas de calor, y el vapor de vaporización se descarga continuamente. La diferencia de presión entre la superficie de evaporación y el espacio se mantiene, permitiendo que el secado continúe. Cuando el contenido de humedad del material se reduce a un cierto nivel, la humedad evaporada se reduce y la diferencia de presión entre la superficie de evaporación y el espacio se reduce. Ingresa a la sección CD, que es la etapa de secado por desaceleración, y la velocidad de secado disminuye gradualmente y se acerca a cero.
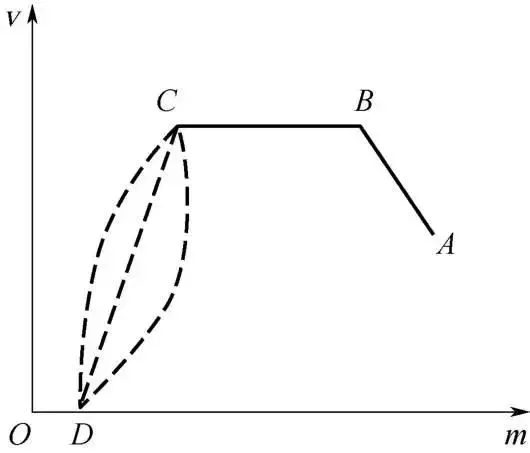
Hay muchos factores que afectan la velocidad de secado durante el proceso de secado al vacío. En primer lugar, la forma, el tamaño y el método de apilamiento del material a secar, así como el contenido de humedad, la densidad y otras propiedades físicas del propio material afectarán a la velocidad de secado. En segundo lugar, el grado de vacío de trabajo del equipo de secado afectará la velocidad de secado. Si el grado de vacío es alto, la humedad se puede vaporizar a una temperatura más baja. Sin embargo, el alto grado de vacío no es propicio para la conducción de calor y reducirá el efecto de calentamiento. Finalmente, la forma estructural, el método de calentamiento y el proceso de secado del equipo de secado afectarán la velocidad de secado. Por lo tanto, es muy difícil calcular el tiempo de secado y la velocidad de secado.
En la actualidad, es difícil medir los cambios de humedad durante el secado de la batería, por lo que no hay muchos estudios experimentales en esta área. Sin embargo, el estudio del mecanismo de evaporación del agua en las baterías tiene una importante importancia orientativa para el proceso de secado de las baterías. Guan Yuming et al. utilizaron software de simulación de dinámica de fluidos computacional (CFD) para analizar la tasa de evaporación del agua en el núcleo de la batería. Completaron el análisis de simulación cargando el lenguaje compilado de la función de difusión de humedad del núcleo de la batería calculado por la ley de Fick y encontraron que la tasa de evaporación del agua en la superficie del núcleo de la batería fue El tiempo de horneado más rápido es de aproximadamente 10 minutos, mientras que la tasa de evaporación del agua en la parte inferior del núcleo de la batería es muy baja al principio, y el tiempo más rápido es de unos 50 minutos, como se muestra en la Figura .
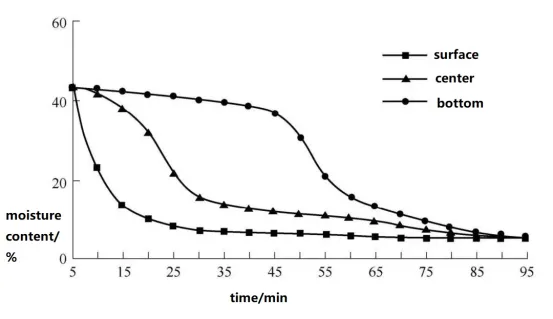
03 Proceso de secado al vacío de la batería
En el proceso de producción de baterías de litio, se requieren varios pasos básicos, como la mezcla de lechada, el recubrimiento, el laminado, el corte, el bobinado / laminación, la soldadura, el sellado, la inyección de líquidos, la formación, la división de volumen y el ensamblaje. Para controlar el contenido de humedad del producto final, se deben establecer puntos de control de humedad en diferentes nodos clave del proceso de producción. Los diseños típicos incluyen el control de la humedad de los materiales de polvo catódico, el control de la humedad de los rodillos de polos/láminas de los polos y, lo que es más importante, el control de la humedad antes de la inyección de la batería.
En el proceso de producción de baterías de iones de litio, los materiales de polvo de electrodos positivos y negativos generalmente deben controlarse la humedad antes de la suspensión y secarse simultáneamente durante la etapa final de fabricación de polvo. Durante el proceso de mezcla de lodo, el electrodo negativo es generalmente una suspensión a base de agua, y el electrodo positivo es generalmente una suspensión a base de aceite. Después de recubrir la lechada, se realiza un secado preliminar. El objetivo principal de este paso es eliminar el disolvente de la lechada y formar una pieza polar de la batería con una estructura microporosa. Después de este paso de secado, todavía queda mucha humedad en la pieza polar. Hay dos procesos principales de secado para eliminar la humedad residual: a. Antes de enrollar o laminar la batería, las piezas polares de la batería se secan al vacío. La temperatura general de secado es de 120 ~ 150 °C. Las piezas polares de la batería a menudo se secan en rollos o pilas; b. Antes de llenar la batería con líquido, seque al vacío la batería ensamblada. Dado que la batería contiene componentes como separadores en este momento, la temperatura de secado suele ser de 60 a 90 °C.
El ajuste de la temperatura de secado no es arbitrario, está relacionado con la existencia de humedad en el material sólido antes de que la batería de litio se llene de líquido. De acuerdo con la naturaleza y el tamaño de la fuerza entre las moléculas de material sólido y las moléculas de agua, hay tres formas principales de agua, como se muestra en la figura. La primera es la adhesión al agua, que simplemente se adhiere mecánicamente a la superficie del material; la segunda es la adsorción de agua, en la que el agua se combina con la materia sólida en forma de adsorción física o química; El tercero es el agua combinada, en la que el agua se combina con material en forma de hidratos cristalinos. combinar. Para la humedad adherida, puede volatilizarse naturalmente a temperatura y presión normales; para la humedad adsorbida, puede evaporarse a alrededor de 105 ° C bajo presión normal; mientras que la evaporación de la humedad compuesta generalmente debe superar los 150 °C a presión normal. En un entorno de vacío, la temperatura de eliminación de humedad se puede reducir significativamente. Cuanto mayor sea la temperatura, mejor será el efecto de eliminación de humedad, pero la temperatura no debe ser demasiado alta, porque la mayoría de los separadores de baterías de litio están hechos de materiales poliméricos, como polietileno de alta densidad y polipropileno de alta densidad, y estos materiales poliméricos no son adecuados para su uso a altas temperaturas. Se degradará a altas temperaturas, causando graves problemas de seguridad. Por lo tanto, establecer razonablemente la temperatura de secado de las baterías de litio es un tema extremadamente importante y debe ajustarse adecuadamente de acuerdo con el sistema de material específico.
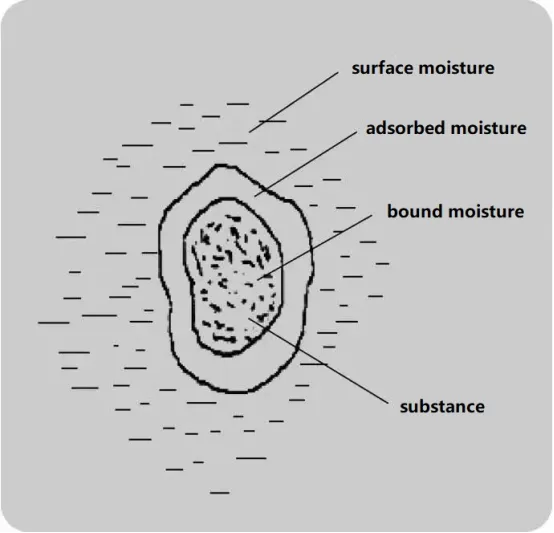
El proceso de secado de la batería generalmente incluye tres etapas: precalentamiento, secado al vacío y enfriamiento. Dado que la transferencia de calor en la sección de vacío es lenta, generalmente se precalienta a presión normal o a presión más alta, y luego la batería se evacua después de que alcanza una cierta temperatura. Elimine la humedad y enfríe a temperatura ambiente después del secado para evitar la oxidación de los materiales de la batería. La batería seca debe tratar de evitar el contacto con el ambiente atmosférico. Los parámetros del proceso, como la temperatura, el grado de vacío, el tiempo de precalentamiento y el tiempo de mantenimiento del vacío durante el proceso de secado, tienen un impacto importante en los resultados del secado. La elección de los parámetros de proceso adecuados es propicia para mejorar la eficiencia del secado.
04 Composición básica y clasificación de los equipos de secado al vacío
Actualmente, el equipo de secado al vacío utilizado en la industria de las baterías de litio ha logrado un funcionamiento básico totalmente automático. Los componentes básicos del equipo incluyen elementos calefactores, sistemas de vacío, cámaras de secado, plataformas de carga y descarga y un sistema de control central.
El componente calefactor se utiliza para suministrar calor al equipo de secado. Los componentes de calefacción se pueden dividir en calefacción eléctrica, calefacción por inducción electromagnética, calefacción por microondas, etc. según las diferentes fuentes de calentamiento. En la actualidad, el método más utilizado para el secado de equipos de batería es el calentamiento eléctrico. La calefacción eléctrica también incluye calefacción por circulación de aire caliente y calefacción por contacto. La calefacción por circulación de aire caliente es una combinación de dispositivo de calefacción y ventilador, que puede hacer que cualquier posición de la cámara de secado alcance la temperatura de secado. El calentamiento por contacto utiliza el dispositivo de calentamiento para entrar en contacto directamente con la batería para conducir el calor a la batería, lo que mejora la eficiencia de la utilización de la energía y puede ahorrar efectivamente el consumo de energía. Los principales requisitos de diseño para los componentes de calefacción son la velocidad de calentamiento, la estabilidad de la temperatura y la uniformidad de la temperatura. Por lo tanto, es muy importante controlar y monitorear la temperatura. Los componentes de calefacción deben estar equipados con los correspondientes componentes de control de temperatura y componentes de detección.
La velocidad de bombeo efectiva de la bomba se calcula de la siguiente manera:
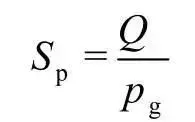
En la fórmula, la velocidad de bombeo efectiva de la bomba Sp, m3/s; la presión de trabajo requerida por la cámara de vacío pg, Pa; el volumen total de gas de la cámara de vacío Q, Pa・m3/s.
Q = 1.3 (Q1 + Q2 + Q3)
En la fórmula, Q1——la cantidad de gas generado durante el proceso de vacío, Pa・m3/s; la cantidad de desgasificación de la cámara de vacío Q2, Pa・m3/s; la cantidad total de fuga de aire de la cámara de vacío Q3, Pa・m3 / s.
La velocidad nominal de bombeo de la bomba se calcula de la siguiente manera:
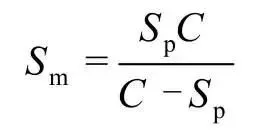
En la fórmula, Sm es la velocidad nominal de bombeo de la bomba, m3/s; C es la conexión de la tubería entre la salida de la cámara de vacío y la entrada de la unidad, m3/s.
La plataforma de carga y descarga se utiliza para cargar y descargar baterías, incluido el montaje (desmontaje) y el apilamiento (desapilado) de baterías, el escaneo de bandejas de baterías, etc., y el manejo de situaciones de NG, etc. Con la mejora de los requisitos de automatización, la carga y descarga de la batería se ha automatizado básicamente, requiriendo menos intervención manual. En la estación de carga, el lector de códigos de barras escanea la batería y el palé. La batería que escanea el código NG se coloca en la plataforma NG. El robot de batería carga la batería escaneada con éxito en el palé. Cuando el palé está lleno, el robot de palets apila el palé hasta la parte superior. En la mesa de materiales, la mesa de carga se llena y entra en la cavidad de secado; Una vez completado el secado, las baterías se envían desde la cavidad de secado y el robot de palets desapilar los palets capa por capa. A continuación, el robot de baterías saca las baterías del palé y entra en el siguiente. proceso.
El sistema de control es responsable de controlar el sistema de vacío, los elementos calefactores y los componentes de movimiento del sistema de secado. Sin embargo, con el desarrollo del big data y el Internet de las cosas, estas funciones ya no son suficientes para satisfacer los requisitos de producción actuales. Los sistemas de software se han vuelto cada vez más importantes para los equipos de secado. Además de controlar el hardware, el software debe tener las siguientes funcionalidades:
1. Capacidad para diagnosticar fallas de equipos, mostrar fallas actuales e históricas y proporcionar métodos de solución de problemas.
2. Capacidad para mostrar señales de entrada y salida y el estado en tiempo real de todos los sensores y actuadores.
3. Capacidad para obtener el estado del equipo en tiempo real y estadísticas sobre el estado del equipo e información de alarma dentro de las 24 horas.
4. Capacidad para recopilar información como tipos de materiales, lotes, modelos y especificaciones, establecer un sistema de seguimiento de materiales y rastrear y rastrear información de materiales.
5. Capacidad para rastrear y administrar el proceso de producción, recopilar parámetros de proceso de estaciones relevantes durante el secado del material, incluida la temperatura, el nivel de vacío, etc.
6. Capacidad para consultar datos históricos, incluida la ejecución de la producción, el uso del equipo, el control de procesos, etc.
Actualmente, no existe un estándar unificado para los equipos de secado al vacío con baterías, y existen varias especificaciones y formularios. Según la forma de la cámara, se puede dividir en equipos de secado de cámara circular y equipos de secado de cámara cuadrada. Según el método de calentamiento, se puede dividir en equipo de calefacción por circulación de aire caliente, equipo de secado por contacto, equipo de calentamiento por inducción, etc. Según las diferentes etapas de la producción de baterías, se puede dividir en equipos de secado de polvo de electrodos positivos y negativos, equipos de secado de bobinado de electrodos positivos y negativos, equipos de secado de celdas de batería, etc. Según el método de descarga del equipo de secado, se puede dividir en equipo de secado por lotes y equipo de secado continuo.
05 Equipo típico de secado al vacío con batería
5.1 Equipos de secado al vacío intermitente
El equipo de secado al vacío intermitente combina múltiples hornos de secado individuales tradicionales y está equipado con robots de carga y descarga automatizados y robots de despacho central para lograr la producción en masa. Su diagrama estructural se muestra en la figura. Este equipo de secado tiene una flexibilidad relativamente alta. El número de hornos de secado equipados en cada conjunto de equipos y el número de cavidades en cada horno de secado se pueden configurar según las necesidades específicas.
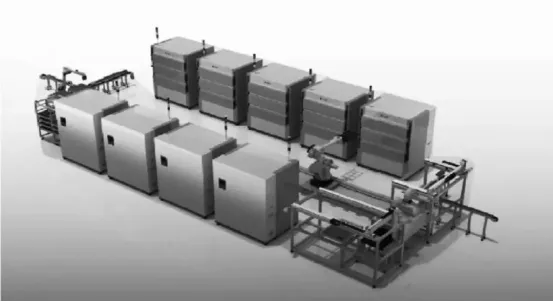
La plataforma de carga del equipo de secado está acoplada a la línea de flujo de material del proceso anterior. Las celdas de la batería se transfieren desde la línea de flujo de material del proceso anterior a la plataforma de carga. A continuación, se colocan y ensamblan en la plataforma de carga antes de ser transferidos al horno de secado correspondiente para su secado. Después del proceso de secado, las celdas se trasladan a la plataforma de descarga para su desmontaje y enfriamiento antes de ingresar a la línea de flujo de material del siguiente proceso. El método de calentamiento del horno de secado puede ser circulación de aire caliente o calentamiento por contacto. Todo el proceso está controlado por un sistema de control central.
El horno de secado único es la base y la unidad central de los equipos de secado al vacío intermitente. Su estructura suele incluir unidades básicas como una cámara de secado al vacío, una puerta sellada totalmente automática, un rack, una placa de sellado exterior, una caja eléctrica, una tubería de vacío, una tubería de nitrógeno, un sistema de control, etc. Si se utiliza calefacción por aire, también incluirá una tubería de circulación de aire caliente. carreteras y sistemas de calefacción.
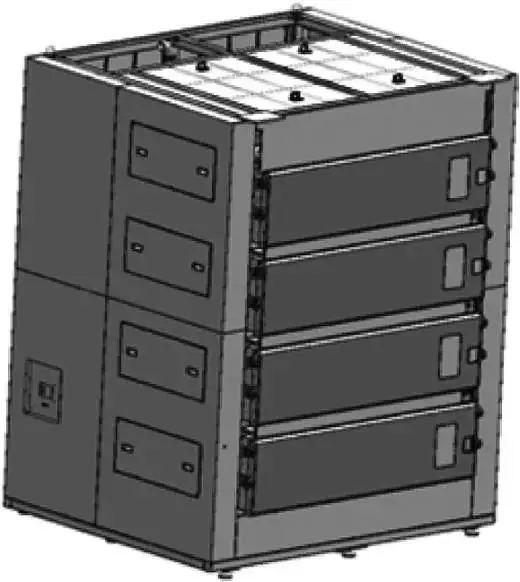
5.2 Equipos de secado continuo al vacío
Los equipos de secado al vacío continuo dividen el proceso de secado en múltiples procesos, como precalentamiento-secado al vacío-enfriamiento, etc., y utilizan diferentes cavidades o estaciones de trabajo para realizar precalentamiento-secado al vacío-enfriamiento y otros procesos. Estas cavidades o estaciones de trabajo son Las posiciones están conectadas con puertas selladas, lo que hace que el secado sea un proceso continuo. Además, está equipado con una plataforma de carga y descarga automatizada y un sistema de transmisión para completar el secado continuo de los materiales. Su diagrama estructural se muestra en la figura. Este equipo de secado puede ahorrar mucho en el consumo de energía, y el número de estaciones en cada conjunto de equipos se puede configurar de acuerdo con los requisitos específicos del proceso y la capacidad de producción.
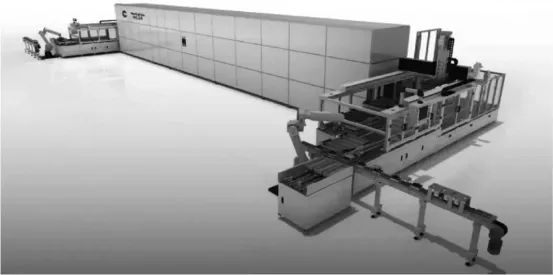
Flujo de proceso del equipo de secado al vacío continuo: Los núcleos de la batería ingresan a la plataforma de carga desde la línea logística del proceso anterior. Se colocan, se enchapan y se apilan en la plataforma de carga, y luego se envían a la cámara de precalentamiento para su precalentamiento. Después del precalentamiento, pasan a través de La cabina de transición de secado ingresa a la cabina de secado al vacío para el secado al vacío. Después del secado, ingresa a la cabina de enfriamiento para enfriarse. Después de enfriarse, pasa a la plataforma de descarga para desapilarlo y retirar la bandeja. Después de eso, las celdas ingresan a la línea logística del siguiente proceso y los palets regresan a la plataforma de carga. plataforma. El método de calentamiento de la cabina de precalentamiento puede ser calefacción por circulación de aire caliente o calefacción por contacto. El modo de calefacción de la cabina de secado al vacío puede ser calefacción por contacto o calefacción radiante complementada por calefacción por circulación de aire caliente. Todo el proceso está controlado por un sistema de control central.
Los equipos de secado continuo al vacío o los equipos de túnel suelen dividirse en varias etapas básicas: precalentamiento, secado al vacío y enfriamiento. La estructura de una sección de precalentamiento típica se muestra en la figura.
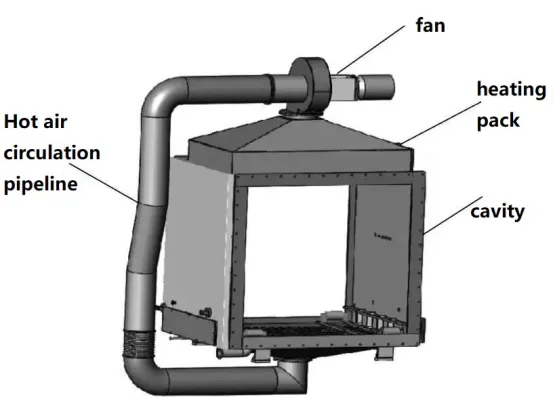
En la imagen, el ventilador impulsa el gas interno para que fluya hacia abajo, es calentado por el paquete calefactor y luego ingresa a la cavidad para calentar los materiales que se van a secar en la cavidad. Luego ingresa al tubo de circulación a través de la salida de aire inferior y regresa al ventilador para formar un canal de circulación de gas. La función principal de la sección de precalentamiento es calentar los materiales secos para alcanzar rápidamente la temperatura de proceso requerida para el secado al vacío. Por lo tanto, la velocidad de calentamiento y la uniformidad de la temperatura de la sección de precalentamiento son sus principales indicadores de proceso.
Una vez que el material seco alcanza la temperatura preestablecida, se transfiere a la sección de secado al vacío a través del dispositivo de transporte. La estructura típica de la sección de secado al vacío se muestra en la figura.
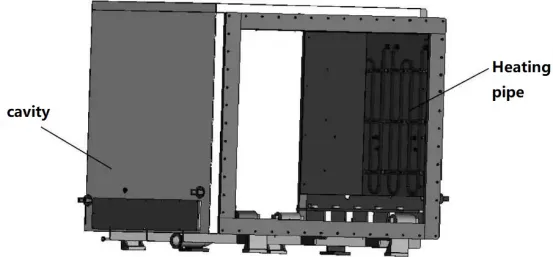
El grado de vacío de secado al vacío suele ser de alrededor de 10 ~ 100Pa. Dado que se encuentra en un entorno de vacío y no hay gas como medio, no se puede utilizar la transferencia de calor por convección. La sección de vacío generalmente tiene un sistema de calentamiento dispuesto alrededor de la cavidad para reponer energía a los materiales secos a través de la radiación.
Para evitar la oxidación de la pieza polar, el material secado al vacío debe enfriarse antes de salir del equipo e ingresar a la sala de secado. Por lo tanto, la última sección funcional del equipo de secado continuo al vacío es la sección de enfriamiento. La estructura típica de la sección de enfriamiento es la que se muestra en la figura.
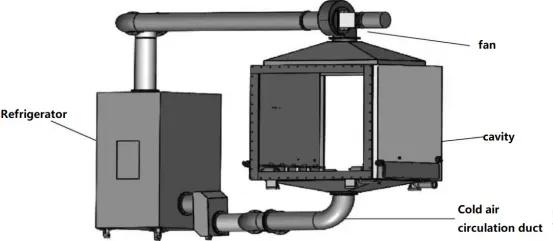
La sección de enfriamiento generalmente está equipada con un refrigerador externo para proporcionar gas inerte de enfriamiento. El gas ingresa a la cavidad a través del ventilador, convección forzada para enfriar y secar el material, y luego regresa al refrigerador a través del tubo de circulación de aire frío para formar un canal de circulación de aire frío. La sección de enfriamiento puede reducir la temperatura de los materiales secos a casi la temperatura ambiente en un corto período de tiempo. Se pueden lograr diferentes curvas de enfriamiento seleccionando diferentes sistemas de refrigeración y caudales de ventilador.
5.3 Equipos de secado al vacío con diferentes métodos de calentamiento
La temperatura es un parámetro central del secado al vacío, y el proceso de aumento de temperatura es una etapa importante del proceso de secado. Actualmente, hay dos métodos de calentamiento comúnmente utilizados en los equipos: calentamiento impulsado por aire y calentamiento por contacto. El calentamiento impulsado por el viento es un método de calentamiento que calienta el aire u otros medios de gas inerte y utiliza ventiladores y otros dispositivos para forzarlo a fluir en la cavidad, transfiriendo así el calor a través de la convección forzada. Este es también el método de calentamiento más utilizado en la industria. A través de un control preciso de la temperatura, el calentamiento impulsado por aire puede lograr una distribución de temperatura muy uniforme en la cavidad, obteniendo así una temperatura uniforme de la batería.
El calentamiento por contacto es otro método de calentamiento por secado al vacío que ha ampliado gradualmente su aplicación en los últimos años. Su principio básico es colocar la batería en la placa calefactora o en el centro de la placa calefactora, y utilizar la conducción de calor para calentar la batería. Como se muestra en la figura, hay tres métodos de calentamiento por contacto: contacto de un solo lado (inferior), contacto de dos lados (ambos lados) y contacto de tres lados (inferior más ambos lados).
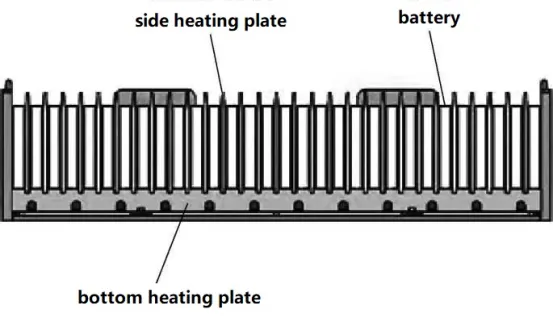
Como puede ver en la imagen, las bandejas de batería calentadas por contacto generalmente están energizadas. Al cargar y descargar, la bandeja de la batería se saca y se coloca en la posición de carga y descarga para colocar y sacar la batería; durante el secado al vacío, la bandeja se eleva a la posición de calentamiento en el centro de la cámara de vacío, y la fuente de alimentación y la medición de la temperatura se realizan a través de contactos eléctricos elásticos, y la placa calefactora se realiza un control de circuito cerrado en tiempo real. La batería se precalienta con la marea caliente, y durante la etapa de secado al vacío, el medio de gas de marea caliente puede reponer continuamente la energía para el secado de la batería.
El uso de la calefacción por aire y la calefacción por contacto tiene sus propias ventajas y desventajas. El equipo de calefacción accionado por aire tiene una estructura simple, alta confiabilidad y buena uniformidad de temperatura, pero requiere un tiempo de calentamiento corto. El equipo de calentamiento por contacto es más liviano porque la potencia del calor proviene del gradiente de temperatura, por lo que la uniformidad de la temperatura es pobre y lleva tiempo alcanzar el equilibrio de temperatura. Al mismo tiempo, los contactos eléctricos entre la bandeja de la batería de calentamiento por contacto y la cavidad generalmente deben estar en contacto con un entorno de vacío, lo que puede causar fácilmente problemas de capacidad de producción de vacío y aumentar el impacto en la producción. Desde el punto de vista de los costos, los equipos de calefacción accionados por aire tienen costos más bajos debido a sus ventajas en la estructura y el control de la temperatura; mientras que el costo de los equipos de tipo contacto con la misma capacidad de producción será entre un 30% y un 50% más alto.
5.4 Equipo de secado al vacío rollo a rollo
El equipo de secado al vacío rollo a rollo está diseñado específicamente para secar rollos de electrodos de batería. Debido al gran tamaño de los rodillos de electrodos, el tiempo de secado es generalmente más largo y puede haber variaciones en el contenido de humedad entre el interior y la superficie de los rodillos. Con el fin de mejorar la eficiencia del secado y lograr un contenido de humedad constante, se ha desarrollado un equipo de secado rollo a rollo. El concepto de procesamiento de rollo a rollo se originó a partir del recubrimiento y otros procesos, y es un método más eficiente para materiales de película delgada.
El equipo de secado al vacío rollo a rollo consta principalmente de una cámara de vacío y dispositivos de adquisición de vacío. La cámara de vacío incluye componentes para desenrollar los rollos, calentar y rebobinar. El diagrama esquemático del equipo de secado al vacío rollo a rollo se muestra en el diagrama. Sin embargo, el equipo de secado rollo a rollo aún no es una tecnología de secado madura. Hay muy pocos dispositivos existentes en el mercado, y las aplicaciones exitosas a escala industrial de dichos equipos son casi inexistentes.
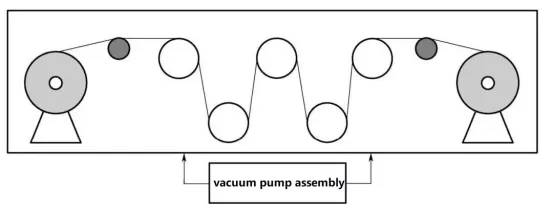
El flujo del proceso de secado rollo a rollo es relativamente simple: el rodillo de electrodo se coloca en el eje de desenrollado y la película de electrodos pasa a través de varios ejes y rodillos de calentamiento antes de enrollarse en el eje de rebobinado. Los ejes de desenrollado y rebobinado giran simultáneamente, y el rodillo de electrodos se calienta y seca para eliminar la humedad a medida que pasa a través de los rodillos de calentamiento. Todo el proceso se lleva a cabo dentro de una cámara de vacío. Una vez finalizado el secado, el rodillo de electrodos se descarga del eje de rebobinado.
El esquema de procesamiento de rollo a rollo está maduro, pero todavía hay muchos desafíos que deben abordarse en los equipos de secado de rollo a rollo. En primer lugar, los componentes de desbobinado y rebobinado tienen soluciones maduras en el mercado. Sin embargo, para mejorar la eficiencia del secado, es deseable velocidades de desenrollado y rebobinado más altas. Para rodillos de electrodos tan ligeros y delgados, el aumento de la velocidad puede provocar la rotura del rodillo. Además, dado que los componentes de desenrollado y rebobinado se encuentran dentro de la cámara de vacío, se deben tomar medidas para evitar la contaminación por polvo durante el proceso de transmisión. Por último, lograr un calentamiento rápido, el control de la uniformidad de la temperatura y la detección durante la transmisión a alta velocidad del rodillo de electrodos plantean dificultades. Además, el nivel de vacío y los requisitos de temperatura del equipo deben ser similares o iguales a los de los tipos de equipos anteriores.
5.5 Logística Almacenamiento Equipos de secado al vacío
El equipo de secado al vacío de almacenamiento logístico utiliza los sistemas logísticos existentes para mejorar significativamente la eficiencia y la flexibilidad del proceso de secado. Este tipo de equipo se desvía de la tradicional gran cámara de secado y en su lugar utiliza palets con cubiertas como espacios de secado, con estantes de almacenamiento para sujetar las bandejas de batería cubiertas. Cada posición de almacenamiento está equipada con un sistema de acoplamiento por vacío y un sistema de acoplamiento por calefacción para calentar las baterías y crear un vacío dentro de las bandejas. El equipo de secado al vacío de almacenamiento logístico aún se encuentra en etapa de desarrollo y no se ha implementado en aplicaciones prácticas. El diagrama esquemático de su estructura se muestra en el diagrama.
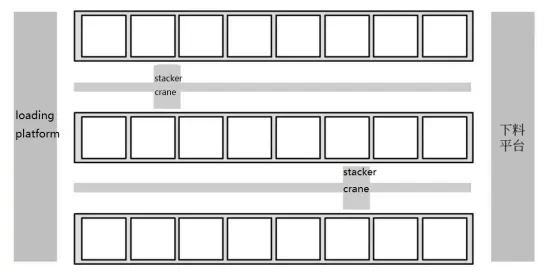
En la plataforma de carga, un robot coloca las baterías en bandejas y las cubre. A continuación, el transelevador coloca las bandejas montadas con baterías en las posiciones de almacenamiento correspondientes en las estanterías de almacenamiento. El sistema de vacío y el sistema de calefacción de los bastidores están acoplados a las bandejas para calentar y secar las baterías. Una vez finalizado el proceso de secado, el transelevador coloca las baterías y las bandejas en la plataforma de descarga, donde se desembalan las baterías y se pasa al siguiente proceso.
Los equipos de secado al vacío de almacenamiento logístico se basan en el concepto de logística y almacenamiento, por lo que requieren un alto nivel de software de programación logística. Además, el transelevador utilizado para la manipulación de las baterías y bandejas debe cumplir unos requisitos específicos para garantizar la eficiencia del equipo. Al utilizar el espacio de la bandeja como cámara de secado, el equipo reduce el tamaño de la cámara y mejora significativamente la flexibilidad. Sin embargo, esto también significa que cada posición de almacenamiento debe tener dispositivos de calentamiento y acoplamiento al vacío, lo que aumenta los costos de equipo y mantenimiento. Este equipo comparte muchas similitudes con el equipo de secado al vacío intermitente. La principal diferencia radica en la cámara más pequeña y móvil de este equipo, lo que lo hace más flexible y adecuado para la producción personalizada.
06.Evaluación del rendimiento del equipo de secado al vacío con batería de litio
6.1 Evaluación del rendimiento del vacío
El rendimiento al vacío de un equipo de secado al vacío se evalúa principalmente en función de parámetros como el tiempo de bombeo, el nivel de vacío final y la capacidad de sellado al vacío de la cámara. La evaluación del rendimiento del vacío se lleva a cabo normalmente en condiciones de descarga. La configuración de la prueba incluye una bomba de vacío, válvulas de vacío, manómetro de vacío, tuberías, así como un medidor de vacío y un temporizador.
El nivel de vacío final se refiere a la presión más baja que puede alcanzar la cámara. Un nivel de vacío final más bajo es favorable para la evaporación de la humedad, pero también impone requisitos más altos al equipo. Por lo tanto, es necesario lograr un equilibrio entre el costo del equipo y el nivel de vacío final. Teniendo en cuenta que el proceso de secado de la mayoría de las baterías se lleva a cabo normalmente a presiones de varias decenas a unos pocos cientos de pascales (Pa), con una presión de trabajo que oscila entre 20 y 1000 Pa, un nivel de vacío final de alrededor de 10 Pa es suficiente.
En condiciones de bombeo continuo, el tiempo de bombeo del equipo se define como el tiempo necesario para alcanzar el valor de presión final después de que la cámara se haya abierto durante 15 minutos y luego se haya evacuado nuevamente. Generalmente, el tiempo de bombeo debe ser de alrededor de 5 a 10 minutos, y si no se puede cumplir con el requisito, se debe considerar reemplazar la bomba de vacío para cumplir con los requisitos.
La cámara de vacío está conectada a la entrada de succión de la bomba de vacío a través de tuberías de vacío para garantizar que todo el sistema de vacío esté sellado. La bomba de vacío se enciende y, cuando el nivel de vacío alcanza la presión máxima, la bomba se apaga y la presión se mantiene durante 24 horas. Se registra la curva de tiempo y presión, y se identifica la sección lineal de la curva de presión frente al tiempo. La pendiente de esta sección lineal representa el valor de la capacidad de sellado al vacío (es decir, el aumento del nivel de vacío por hora). La capacidad de sellado al vacío generalmente debe ser inferior a 5 Pa/h. Si la capacidad de sellado al vacío no cumple con los requisitos, se debe usar un detector de fugas de helio para probar la cámara y mejorar su rendimiento de sellado.
6.2 Evaluación del rendimiento de la temperatura
El rendimiento de la temperatura del equipo de secado al vacío con batería de litio se evalúa principalmente en función de parámetros como el tiempo de calentamiento, la fluctuación de la temperatura, la estabilidad de la temperatura y la uniformidad de la temperatura. La evaluación del rendimiento de la temperatura también se lleva a cabo normalmente en condiciones de descarga. La configuración de prueba para el rendimiento de la temperatura incluye sensores de temperatura como termorresistencias y termopares, así como un registrador de temperatura. Para el calentamiento por aire forzado, el punto de medición de temperatura suele ser el centro de la cámara, mientras que para el calentamiento por contacto, es el centro del dispositivo de calentamiento.
El tiempo de calentamiento se refiere al tiempo que tarda el equipo en alcanzar la temperatura de proceso para el secado de la batería cuando el dispositivo de calentamiento funciona a máxima potencia desde la temperatura ambiente. Para el calentamiento por aire forzado, el tiempo de calentamiento no debe exceder los 90 minutos, mientras que para el calentamiento por contacto, no debe exceder los 10 minutos. La fluctuación de la temperatura se define como la mitad de la diferencia entre las temperaturas más alta y más baja en el punto de medición dentro de un período específico de 30 minutos después de que la temperatura se estabiliza durante el proceso de secado. La fluctuación de temperatura del equipo de secado de la batería no debe exceder los ±1 °C.
La estabilidad de la temperatura está determinada por la diferencia máxima entre la temperatura promedio de múltiples mediciones de temperatura tomadas en diferentes intervalos de tiempo dentro de las 24 horas posteriores a la estabilización de la temperatura durante el proceso de secado y la temperatura promedio durante el período inicial. La estabilidad de la temperatura del equipo de secado de la batería no debe exceder los 2 °C.
La uniformidad de la temperatura se define como la mitad de la diferencia máxima entre las temperaturas medias en dos puntos cualesquiera dentro de la cámara (para el calentamiento por aire forzado) o en el dispositivo de calefacción (para el calentamiento por contacto) durante un intervalo de tiempo especificado después de que la temperatura se estabiliza durante el proceso de secado. Para el calentamiento por aire forzado, los puntos de medición de temperatura deben incluir múltiples puntos en el centro y los bordes de la cámara, mientras que para el calentamiento por contacto, los puntos deben incluir el centro y los bordes del dispositivo de calentamiento. La uniformidad de la temperatura del equipo de secado de la batería no debe exceder los ±3 °C. En la figura se muestra una curva de prueba de uniformidad de temperatura típica.
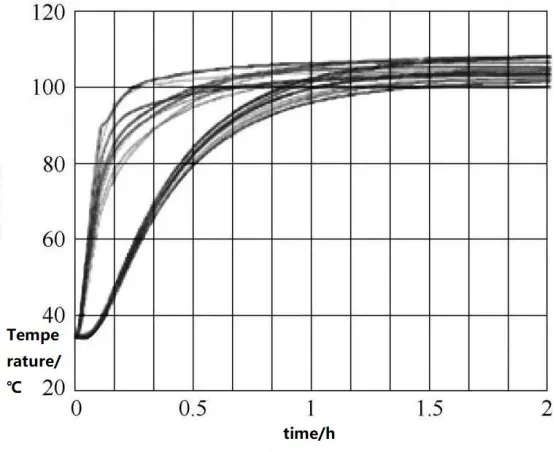
6.3 Evaluación de la humedad después del secado
Niu Junting et al. realizaron un estudio sistemático sobre la relación entre la humedad residual en las piezas polares de la batería y el rendimiento de la batería. Las baterías con un contenido de humedad de la lámina de electrodos positivo entre 0,04% y 0,05% tienen un buen rendimiento de ciclo. Después de 200 ciclos de carga y descarga actuales, la capacidad de descarga de la batería sigue siendo del 92,9% de la capacidad inicial. A medida que avanza el ciclo, la capacidad de las baterías con un contenido de humedad de más del 0,06% en la lámina de electrodos positivos disminuye rápidamente y el rendimiento se deteriora. Las baterías con un contenido de humedad en la pieza polar de la batería en el rango de 0.03% a 0.06% tienen una capacidad específica de descarga alta y cercana. A medida que aumenta la tasa de descarga, el contenido de humedad de la pieza polar de la batería supera el 0,06% y la tasa de atenuación de la capacidad aumenta. Dado que la humedad excesiva tiene un gran impacto negativo en el rendimiento de la batería, generalmente se requiere que el contenido de humedad actual de la batería después del secado sea inferior a 500 mg / kg, y es mejor reducirlo a 200 ~ 300 mg / kg.
Dado que el contenido de humedad de la batería es bajo después del secado, generalmente solo unos pocos cientos de miligramos por kilogramo, no se puede medir con un método simple. El método de Karl Fischer-Coulomb se usa generalmente para probar trazas de humedad, y su principio es un método electroquímico. El principio de reacción es que el agua participa en la reacción redox del yodo y el dióxido de azufre.
Se puede ver en la reacción anterior que 1 mol de yodo oxida 1 mol de dióxido de azufre, lo que requiere 1 mol de agua. Por lo tanto, el poder de electrolizar el yodo es equivalente al poder de electrolizar el agua. La electrólisis de 1 mol de yodo requiere 2×96493C de potencia, y la electrólisis de 1 mmol de agua requiere 96493 mC de potencia. La masa de humedad medida se calcula de acuerdo con la siguiente fórmula:
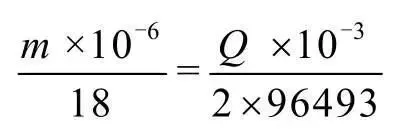
En la fórmula, m es la masa medida de agua, μg; Electrolito Q, mC; 18 electrolito de agua.
La masa de humedad medida también incluye la humedad en el sistema de prueba. Por lo tanto, la humedad en la humedad debe medirse en función de la pérdida total de masa de humedad de la botella vacía (valor en blanco), y se debe considerar la influencia del valor de humedad (valor de deriva). La humedad en el contenido de humedad se calcula de la siguiente manera:
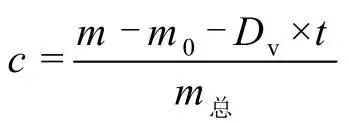
En la fórmula, c contenido de humedad de la muestra, μg/g; m0 masa de humedad de la botella vacía, μg; Valor de deriva dv, μg/min; t tiempo de extracción, min; m total – masa total de la muestra, g.
El diagrama estructural del medidor de humedad Karl Fischer-Coulomb se muestra en la figura. Incluye principalmente una celda electrolítica Karl Fischer y una unidad de calentamiento de muestras. La muestra de la pieza polar se coloca en una botella de muestra sellada y, a continuación, la botella de muestra se calienta a una temperatura determinada. El agua en la celda electrolítica se evapora, y luego se usa gas seco para enviar el vapor de agua a la celda electrolítica para participar en la reacción, y luego se mide la electricidad generada durante el proceso de electrólisis para valorar el contenido de agua.
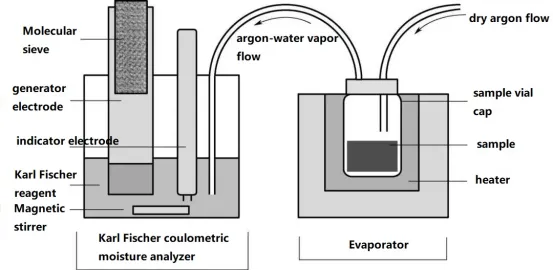
Al realizar pruebas de humedad en muestras de baterías con un analizador de humedad coulométrico Karl Fischer después del secado, se deben tener en cuenta los siguientes puntos:
un. El vial de muestra debe secarse antes de la toma de muestras, normalmente a 120-160 °C durante 3-6 horas. Después de retirarlo, debe sellarse inmediatamente con una tapa. El contenido de humedad en blanco del vial de muestra debe ser inferior a 10 μg, y cuanto más bajo, mejor.
b. El muestreo debe realizarse en un entorno con un punto de rocío. Por lo general, se recomienda tener un punto de rocío inferior a -40 °C. Deje el frasco de muestra vacío sin tapar durante 1-2 horas como una prueba en blanco.
c. La placa de electrodos se puede cortar en trozos pequeños de alrededor de 0,5 cm o a lo largo de la altura del vial de muestra.
d. El tamaño de la muestra para el análisis generalmente no debe ser inferior a 0,5 g.
e. Se recomienda utilizar una balanza electrónica de precisión con una resolución de 0,1 mg para el pesaje.
f. Antes de realizar una prueba formal de muestra, asegúrese de que la deriva de corriente sea inferior a 20 μg/min y estable sin tendencias significativas al alza o a la baja.
g. Después de completar una muestra, retire el frasco con la muestra del horno Karl Fischer, insértelo nuevamente en la botella de deriva y deje que el instrumento se estabilice antes de pasar a la siguiente muestra.
h. La temperatura recomendada para el horno Karl Fischer es de 120-180°C. Una temperatura excesiva puede causar volatilización o reacciones secundarias de algunos materiales en la batería, lo que lleva a resultados de prueba inexactos. Cuando no está seguro de la temperatura de prueba, el método de calentamiento de gradiente se puede utilizar con el analizador de humedad Karl Fischer para analizar el contenido de humedad de los materiales de las baterías de iones de litio y las placas de electrodos.
07 Dirección de desarrollo de equipos de secado al vacío
7.1 Mejora continua de la eficiencia de secado
Acortar el tiempo de secado y mejorar la eficiencia del secado siempre ha sido un objetivo de los equipos de secado. Mejorar la eficiencia del secado al vacío ayuda a reducir los costos del producto y mejorar los beneficios económicos. Actualmente, los equipos de secado están cada vez más automatizados, lo que también contribuye a mejorar la eficiencia del secado. En el futuro, es necesario desarrollar nuevos métodos de calentamiento para mejorar la eficiencia de la calefacción, desarrollar sistemas logísticos adaptados a los equipos de secado para mejorar la eficiencia de carga y descarga, crear equipos de secado de bajo consumo de energía, realizar investigaciones sobre mecanismos de secado de baterías para optimizar los procesos de secado, utilizar software y técnicas de monitoreo para mejorar el control del proceso y mejorar la eficiencia operativa del equipo.
7.2 Diseño modular y estandarizado de equipos
Actualmente, los equipos de secado de baterías se diseñan a medida debido a las diferentes especificaciones de las baterías en el mercado. Esta falta de estandarización limita la flexibilidad de los equipos de secado de baterías y dificulta su capacidad de actualización. En el futuro, debería haber estándares correspondientes para las especificaciones de las baterías, y el diseño del equipo de secado debería cumplir con estos estándares. Esto incluye aspectos como el tamaño de la cámara, la selección de las bombas de vacío, los requisitos de las placas calefactoras y las posiciones de instalación de los vacuómetros y las válvulas. Además, debido a la demanda de producción por lotes de baterías, los equipos de secado son cada vez más grandes, y la instalación y depuración in situ a menudo requieren una cantidad significativa de mano de obra, recursos y tiempo. Al diseñar el equipo de secado, se debe considerar la modularización, con cada módulo con una funcionalidad independiente para ahorrar tiempo de instalación y depuración en el sitio.
7.3 Sistema de Ejecución de Manufactura (MES) para la Guía de Producción
Con la creciente automatización en la producción de baterías, también se están actualizando los sistemas de software de los equipos de secado. Actualmente, el software del equipo de secado puede mostrar datos de consumo de energía, registrar información del producto y datos de proceso, que son requisitos básicos. Sin embargo, la ETM actual se centra principalmente en la recopilación y el almacenamiento de datos para la trazabilidad de los datos de secado. En el futuro, MES debería ir más allá de estas funciones y utilizar técnicas como el big data para proporcionar orientación y mejora en los procesos de secado de baterías, ayudando en el mantenimiento de los equipos y mejorando la eficiencia del secado.
7.4 Detección de humedad en línea
Como se mencionó anteriormente, las pruebas de humedad después del secado de la batería requieren la destrucción de las baterías para evaluar su contenido de humedad y determinar su aceptabilidad. Actualmente, no existe un método eficaz de detección de humedad en tiempo real disponible. En el futuro, se deben realizar investigaciones para desarrollar nuevos métodos de prueba de baterías que puedan monitorear el contenido de humedad durante el proceso de secado en tiempo real, sin la necesidad de pruebas destructivas o análisis de humedad posteriores al secado. Si se determina que el contenido de humedad no cumple con los requisitos durante el proceso de secado, se pueden realizar ajustes inmediatos en el proceso de secado hasta que el contenido de humedad cumpla con los estándares deseados. El desarrollo de nuevos métodos de detección de humedad requiere una investigación en profundidad sobre el mecanismo de evaporación de la humedad de las baterías y los factores influyentes relevantes. Por lo tanto, el estudio del proceso de secado de la batería es de gran importancia para el avance de los equipos de secado.