La teneur en eau a un impact significatif sur les performances de la batterie et doit être strictement contrôlée pendant le processus de fabrication. La présence d’eau dans les batteries peut provoquer la dégradation de l’électrolyte ou réagir avec l’électrolyte pour produire des gaz nocifs, entraînant une augmentation de la pression et une déformation à l’intérieur de la batterie. Une teneur excessive en eau dans les batteries peut également entraîner une résistance interne élevée, une autodécharge élevée, une faible capacité, de mauvaises performances de cyclage et même des fuites, dégradant considérablement les performances de la batterie. Par conséquent, un processus de séchage est essentiel dans la production de batteries au lithium.
01 Introduction au séchage
Le séchage est une opération d’unité chimique qui consiste à fournir de l’énergie aux matériaux humides pour les vaporiser et éliminer l’humidité contenue, ce qui entraîne la production de matériaux séchés. Actuellement, il existe de nombreuses options d’équipements de séchage dans l’industrie, et elles peuvent être classées à l’aide de différentes méthodes. En fonction du mode de fonctionnement, l’équipement de séchage peut être classé en équipement de séchage continu et équipement de séchage par lots (intermittent). Selon la pression de fonctionnement, il peut être classé comme équipement de séchage atmosphérique et équipement de séchage sous vide. De plus, sur la base de la méthode de transfert de chaleur, les équipements de séchage peuvent être classés en équipements de séchage par conduction, équipements de séchage par convection, équipements de séchage par rayonnement et équipements de séchage diélectrique, entre autres.
La teneur en eau des batteries provient principalement de l’humidité présente dans les matières premières de la batterie, y compris les feuilles d’électrodes positives et négatives, le séparateur, l’électrolyte et d’autres composants métalliques, ainsi que de l’humidité de l’environnement de l’usine. Pour traiter l’humidité ambiante, une salle sèche peut être établie, où une machine à sécher génère de l’air sec qui est fourni en permanence à la pièce sèche, déplaçant l’air humide et éliminant l’humidité ambiante. Pour l’humidité interne dans la batterie, en raison des normes de séchage élevées requises, exigeant généralement une teneur en humidité comprise entre (100-300)×10-6, un équipement de séchage sous vide est généralement utilisé pour éliminer l’eau. Après séchage, les batteries sont testées pour s’assurer qu’elles répondent aux exigences de cuisson. Plusieurs étapes du processus de production des batteries nécessitent un séchage sous vide, comme pour les poudres d’électrodes de batterie, l’enroulement d’électrodes positives et négatives et l’assemblage des cellules avant l’injection d’électrolyte. Par conséquent, l’équipement de séchage sous vide est crucial pour la fabrication de batteries.
02 Principe du séchage sous vide
Le principe du séchage sous vide est basé sur le fait que le point d’ébullition de l’eau change sous différents environnements de pression. La relation entre la pression et le point d’ébullition est représentée sur la figure.
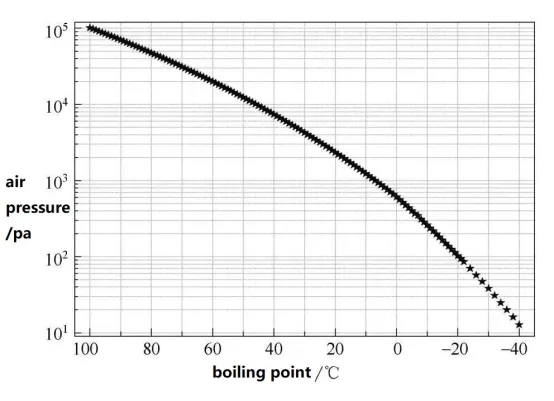
On peut voir sur la figure qu’à une pression normale, c’est-à-dire une pression atmosphérique, le point d’ébullition de l’eau est de 100°C, mais à mesure que la pression atmosphérique diminue, le point d’ébullition de l’eau continue de diminuer. Dans un environnement sous vide d’environ 100 Pa, le point d’ébullition de l’eau est descendu à environ -20 °C. C’est le principe de base qu’un environnement sous vide peut favoriser le processus de séchage.
Par conséquent, le séchage sous vide est le processus d’élimination de l’humidité contenue dans les matériaux dans des conditions environnementales inférieures à une pression atmosphérique standard. Le principe cinétique de base du séchage sous vide est la théorie du transfert de chaleur et de masse. Pendant le processus de séchage sous vide, le système de vide chauffe en continu le matériau à sécher pendant l’évacuation, de sorte que l’humidité à l’intérieur du matériau se diffuse à la surface par la différence de pression ou la différence de concentration. Les molécules d’eau obtiennent suffisamment d’énergie cinétique à la surface du matériau pour surmonter l’attraction mutuelle entre les molécules. Volez dans l’espace basse pression de la chambre à vide et soyez aspiré par la pompe à vide.
Le taux de perte d’humidité pendant le processus de séchage sous vide et la masse d’humidité vaporisée et évacuée du matériau sec par unité de surface de séchage par unité de temps sont la vitesse de séchage, c’est-à-dire
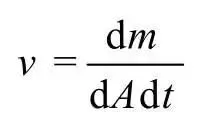
Dans la formule, v vitesse de séchage, g/(m2·h) ; m masse d’humidité évacuée, g ; Une zone de séchage, m2 ; t temps de séchage, h.
Lors du séchage des batteries, on accorde généralement plus d’attention à la teneur en humidité qu’à la qualité de l’humidité. De plus, la teneur en humidité de la batterie est extrêmement faible et la qualité de l’humidité évaporée est difficile à mesurer. Étant donné que la variation de la teneur en humidité est utilisée pour remplacer la variation de la masse d’humidité par unité de surface, la formule ci-dessus peut être transformée en :
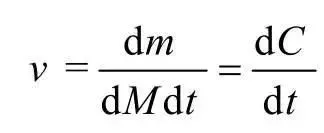
Dans la formule, v vitesse de séchage, mg/(kg·h) ; m masse d’humidité évacuée, mg ; M masse totale du matériau, kg ; C teneur en humidité, mg/kg ; t temps de séchage, h.
Une courbe de vitesse de séchage sous vide typique est illustrée sur la figure. Le processus de perte d’eau est divisé en trois étapes : l’étape de séchage accélérée, l’étape de séchage à vitesse constante et l’étape de séchage décélérée. La section AB est l’étape de séchage accéléré. À ce moment, la teneur en humidité du matériau est constante. En raison de l’aspiration et du chauffage, le matériau est chauffé à la température de vaporisation sous la pression correspondante dans la plage de température autorisée et se vaporise en grandes quantités, et la vitesse de séchage continue d’augmenter. En raison de la limitation des caractéristiques de transfert de chaleur et de masse, la vitesse de séchage atteint la valeur maximale et entre dans la section BC, qui est l’étape de séchage à vitesse constante. À ce moment, la température du matériau reste inchangée, la chaleur de chauffage est utilisée comme chaleur latente de vaporisation et de diverses pertes de chaleur, et la vapeur de vaporisation est déchargée en continu. La différence de pression entre la surface d’évaporation et l’espace est maintenue, ce qui permet au séchage de se poursuivre. Lorsque la teneur en humidité du matériau est réduite à un certain niveau, l’humidité évaporée est réduite et la différence de pression entre la surface d’évaporation et l’espace est réduite. Il entre dans la section CD, qui est l’étape de séchage par décélération, et la vitesse de séchage diminue progressivement et se rapproche de zéro.
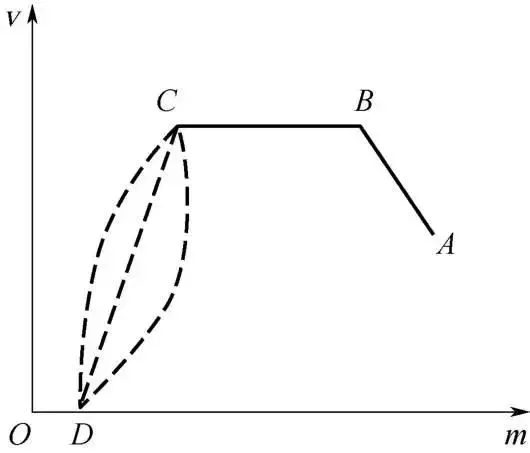
De nombreux facteurs affectent la vitesse de séchage pendant le processus de séchage sous vide. Tout d’abord, la forme, la taille et la méthode d’empilement du matériau à sécher, ainsi que la teneur en humidité, la densité et d’autres propriétés physiques du matériau lui-même affecteront la vitesse de séchage. Deuxièmement, le degré de vide de travail de l’équipement de séchage affectera la vitesse de séchage. Si le degré de vide est élevé, l’humidité peut être vaporisée à une température plus basse. Cependant, le degré de vide élevé n’est pas propice à la conduction de la chaleur et réduira l’effet de chauffage. Enfin, la forme structurelle, la méthode de chauffage et le processus de séchage de l’équipement de séchage affecteront tous la vitesse de séchage. Par conséquent, il est très difficile de calculer le temps de séchage et la vitesse de séchage.
À l’heure actuelle, il est difficile de mesurer les changements d’humidité pendant le séchage des batteries, il n’y a donc pas beaucoup d’études expérimentales dans ce domaine. Cependant, l’étude du mécanisme d’évaporation de l’eau dans les batteries a une importance directrice importante pour le processus de séchage des batteries. Guan Yuming et al. ont utilisé un logiciel de simulation de dynamique des fluides numérique (CFD) pour analyser le taux d’évaporation de l’eau dans le cœur de la batterie. Ils ont terminé l’analyse de simulation en chargeant la fonction de diffusion de l’humidité du cœur de la batterie a compilé le langage calculé selon la loi de Fick et ont constaté que le taux d’évaporation de l’eau à la surface du cœur de la batterie était Le temps de cuisson le plus rapide est d’environ 10 minutes, tandis que le taux d’évaporation de l’eau au bas du noyau de la batterie est très faible au début, et le temps le plus rapide est d’environ 50 minutes, comme le montre la figure .
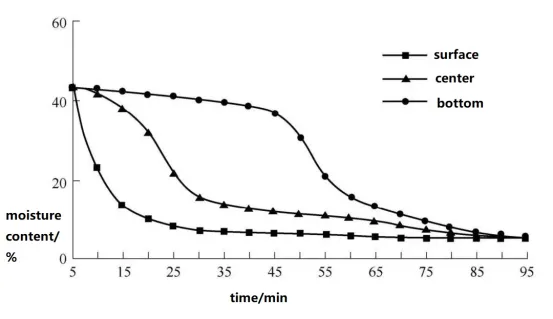
03 Processus de séchage sous vide de la batterie
Dans le processus de production des batteries au lithium, plusieurs étapes de base telles que le mélange de boue, le revêtement, le laminage, le refendage, l’enroulement/laminage, le soudage, l’étanchéité, l’injection de liquide, la formation, la division du volume et l’assemblage sont nécessaires. Afin de contrôler la teneur en humidité du produit final, des points de contrôle de l’humidité doivent être définis à différents nœuds clés du processus de production. Les conceptions typiques incluent le contrôle de l’humidité des matériaux en poudre de cathode, le contrôle de l’humidité des rouleaux de poteaux/feuilles de poteau et, surtout, le contrôle de l’humidité avant l’injection de la batterie.
Dans le processus de production des batteries lithium-ion, les matériaux en poudre d’électrode positive et négative doivent généralement être contrôlés à l’humidité avant la suspension et séchés simultanément jusqu’à l’étape finale de la fabrication de la poudre. Au cours du processus de mélange de boue, l’électrode négative est généralement une boue à base d’eau et l’électrode positive est généralement une boue à base d’huile. Une fois la boue enrobée, un séchage préliminaire est effectué. L’objectif principal de cette étape est d’éliminer le solvant dans la boue et de former une pièce polaire de batterie avec une structure microporeuse. Après cette étape de séchage, il reste encore beaucoup d’humidité dans la pièce polaire. Il existe deux principaux procédés de séchage pour éliminer l’humidité résiduelle : a. Avant que la batterie ne soit roulée ou laminée, les pièces polaires de la batterie sont séchées sous vide. La température générale de séchage est de 120 ~ 150 °C. Les pièces polaires de la batterie sont souvent séchées en rouleaux ou en tas ; b. Avant de remplir la batterie de liquide, séchez la batterie assemblée sous vide. Étant donné que la batterie contient à ce moment des composants tels que des séparateurs, la température de séchage est généralement de 60 à 90 °C.
Le réglage de la température de séchage n’est pas arbitraire, il est lié à l’existence d’une forme d’humidité dans le matériau solide avant que la batterie au lithium ne soit remplie de liquide. Selon la nature et la taille de la force entre les molécules de matériau solide et les molécules d’eau, il existe trois formes principales d’eau, comme le montre la figure. La première est l’adhérence de l’eau, qui est simplement fixée mécaniquement à la surface du matériau ; la seconde est l’adsorption de l’eau, dans laquelle l’eau est combinée avec de la matière solide sous forme d’adsorption physique ou chimique ; le troisième est l’eau combinée, dans laquelle l’eau est combinée avec un matériau sous forme d’hydrates de cristal. combiner. Pour l’humidité fixée, il peut se volatiliser naturellement à une température et une pression normales ; pour l’humidité adsorbée, il peut s’évaporer à environ 105 °C sous pression normale ; tandis que l’évaporation de l’humidité composée doit généralement atteindre plus de 150 °C sous pression normale. Dans un environnement sous vide, la température d’élimination de l’humidité peut être considérablement réduite. Plus la température est élevée, meilleur est l’effet d’élimination de l’humidité, mais la température ne doit pas être trop élevée, car la plupart des séparateurs de batteries au lithium sont fabriqués à partir de matériaux polymères, tels que le polyéthylène haute densité et le polypropylène haute densité, et ces matériaux polymères ne conviennent pas à une utilisation à des températures élevées. Il se dégradera à des températures élevées, causant de graves problèmes de sécurité. Par conséquent, le réglage raisonnable de la température de séchage des batteries au lithium est une question extrêmement importante et doit être ajusté de manière appropriée en fonction du système de matériaux spécifique.
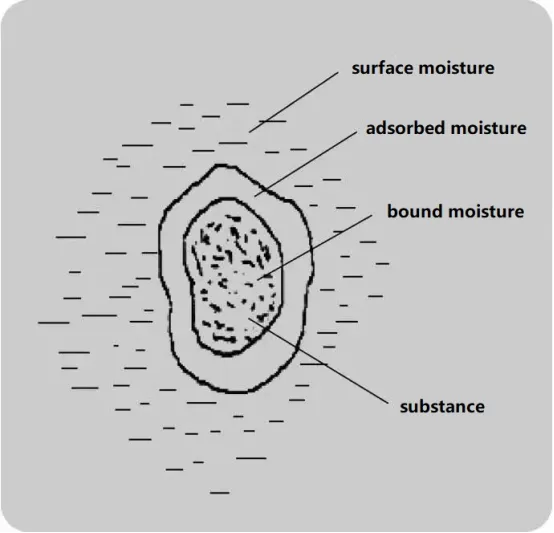
Le processus de séchage de la batterie comprend généralement trois étapes : le préchauffage, le séchage sous vide et le refroidissement. Étant donné que le transfert de chaleur dans la section de vide est lent, il est généralement préchauffé à une pression normale ou à une pression plus élevée, puis la batterie est évacuée une fois qu’elle a atteint une certaine température. Évacuez l’humidité et laissez refroidir à température ambiante après séchage pour éviter l’oxydation des matériaux de la batterie. La batterie séchée doit essayer d’éviter tout contact avec l’environnement atmosphérique. Les paramètres de processus tels que la température, le degré de vide, le temps de préchauffage et le temps de maintenance du vide pendant le processus de séchage ont un impact important sur les résultats de séchage. Le choix des paramètres de processus appropriés est propice à l’amélioration de l’efficacité du séchage.
04 Composition de base et classification de l’équipement de séchage sous vide
Actuellement, l’équipement de séchage sous vide utilisé dans l’industrie des batteries au lithium a atteint un fonctionnement de base entièrement automatique. Les composants de base de l’équipement comprennent des éléments chauffants, des systèmes de vide, des chambres de séchage, des plates-formes de chargement et de déchargement et un système de contrôle central.
Le composant chauffant est utilisé pour fournir de la chaleur à l’équipement de séchage. Les composants de chauffage peuvent être divisés en chauffage électrique, chauffage par induction électromagnétique, chauffage par micro-ondes, etc. selon différentes sources de chaleur. À l’heure actuelle, la méthode la plus couramment utilisée pour les équipements de séchage de batterie est le chauffage électrique. Le chauffage électrique comprend également le chauffage à circulation d’air chaud et le chauffage par contact. Le chauffage par circulation d’air chaud est une combinaison d’un dispositif de chauffage et d’un ventilateur, qui peut faire en sorte que n’importe quelle position dans la chambre de séchage atteigne la température de séchage. Le chauffage par contact utilise le dispositif de chauffage pour entrer en contact direct avec la batterie afin de conduire la chaleur vers la batterie, ce qui améliore l’efficacité de l’utilisation de l’énergie et permet d’économiser efficacement la consommation d’énergie. Les principales exigences de conception des composants chauffants sont la vitesse de chauffage, la stabilité de la température et l’uniformité de la température. Par conséquent, il est très important de contrôler et de surveiller la température. Les composants chauffants doivent être équipés de composants de contrôle de température et de composants de détection correspondants.
La vitesse de pompage effective de la pompe est calculée comme suit :
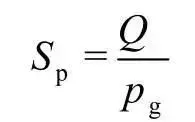
Dans la formule, la vitesse de pompage effective de la pompe Sp, m3/s ; la pression de travail requise par la chambre à vide pg, Pa ; le volume total de gaz de la chambre à vide Q, Pa・m3/s.
Q=1.3(Q1+Q2+Q3)
Dans la formule, Q1——la quantité de gaz générée pendant le processus de vide, Pa・m3/s ; la quantité de dégazage de la chambre à vide Q2, Pa・m3/s ; la quantité totale de fuite d’air de la chambre à vide Q3, Pa・m3/s.
La vitesse nominale de pompage de la pompe est calculée comme suit :
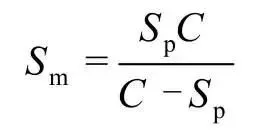
Dans la formule, Sm est la vitesse nominale de pompage de la pompe, m3/s ; C est le raccord du tuyau entre la sortie de la chambre à vide et l’entrée de l’unité, m3/s.
La plate-forme de chargement et de déchargement est utilisée pour le chargement et le déchargement des batteries, y compris l’assemblage (démontage) et l’empilage (désempilage) des batteries, le balayage des plateaux de batteries, etc., et la gestion des situations NG, etc. Avec l’amélioration des exigences d’automatisation, le chargement et le déchargement des batteries ont été essentiellement automatisés, nécessitant moins d’interventions manuelles. Au poste de chargement, le lecteur de codes-barres scanne la batterie et la palette. La batterie qui scanne le code NG est placée sur la plate-forme NG. Le robot de batterie charge la batterie scannée avec succès dans la palette. Lorsque la palette est pleine, le robot à palettes empile la palette jusqu’en haut. Sur la table des matériaux, la table de chargement est remplie et entre dans la cavité de séchage ; Une fois le séchage terminé, les batteries sont envoyées de la cavité de séchage et le robot de palettes dépilage les palettes couche par couche. Le robot de batterie sort ensuite les batteries de la palette et entre dans la suivante. processus.
Le système de contrôle est responsable du contrôle du système de vide, des éléments chauffants et des composants de mouvement du système de séchage. Cependant, avec le développement du big data et de l’Internet des objets, ces fonctions ne suffisent plus à répondre aux besoins de production actuels. Les systèmes logiciels sont devenus de plus en plus importants pour les équipements de séchage. En plus de contrôler le matériel, le logiciel doit disposer des fonctionnalités suivantes :
1. Capacité à diagnostiquer les défauts de l’équipement, à afficher les défauts actuels et historiques et à fournir des méthodes de dépannage.
2. Possibilité d’afficher les signaux d’entrée et de sortie et l’état en temps réel de tous les capteurs et actionneurs.
3. Possibilité d’obtenir l’état de l’équipement en temps réel et des statistiques sur l’état de l’équipement et des informations d’alarme dans les 24 heures.
4. Capacité à collecter des informations telles que les types de matériaux, les lots, les modèles et les spécifications, à établir un système de suivi des matériaux et à suivre et tracer les informations sur les matériaux.
5. Capacité à suivre et à gérer le processus de production, à collecter les paramètres de processus des stations pertinentes pendant le séchage des matériaux, y compris la température, le niveau de vide, etc.
6. Possibilité d’interroger les données historiques, y compris l’exécution de la production, l’utilisation de l’équipement, le contrôle des processus, etc.
Actuellement, il n’existe pas de norme unifiée pour les équipements de séchage sous vide sur batterie, et il existe diverses spécifications et formes. En fonction de la forme de la chambre, il peut être divisé en équipement de séchage à chambre circulaire et équipement de séchage à chambre carrée. En fonction de la méthode de chauffage, il peut être divisé en équipement de chauffage à circulation d’air chaud, équipement de séchage à chauffage par contact, équipement de chauffage par induction, etc. Sur la base des différentes étapes de la production de la batterie, il peut être divisé en équipement de séchage de poudre à électrode positive et négative, équipement de séchage à enroulement d’électrode positive et négative, équipement de séchage de cellule de batterie, etc. Sur la base de la méthode de décharge de l’équipement de séchage, il peut être divisé en équipement de séchage par lots et équipement de séchage continu.
05 Équipement typique de séchage sous vide sur batterie
5.1 Équipement de séchage sous vide intermittent
L’équipement de séchage sous vide intermittent combine plusieurs fours de séchage simples traditionnels et est équipé de robots de chargement et de déchargement automatisés et de robots de répartition centralisés pour réaliser une production de masse. Son schéma structurel est illustré sur la figure. Cet équipement de séchage a une flexibilité relativement élevée. Le nombre de fours de séchage équipés dans chaque ensemble d’équipements et le nombre de cavités dans chaque four de séchage peuvent être configurés en fonction des besoins spécifiques.
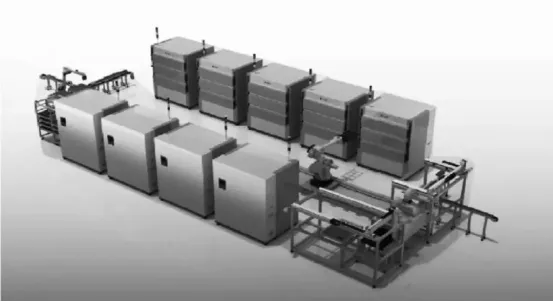
La plate-forme de chargement de l’équipement de séchage est amarrée à la ligne d’écoulement de matériau du processus précédent. Les cellules de la batterie sont transférées de la ligne de flux de matériaux du processus précédent vers la plate-forme de chargement. Ils sont ensuite positionnés et assemblés sur la plate-forme de chargement avant d’être transférés dans l’étuve de séchage correspondante pour le séchage. Après le processus de séchage, les cellules sont déplacées vers la plate-forme de déchargement pour le démontage et le refroidissement avant d’entrer dans la ligne de flux de matériaux du processus suivant. La méthode de chauffage de l’étuve de séchage peut être soit la circulation d’air chaud, soit le chauffage par contact. L’ensemble du processus est contrôlé par un système de contrôle central.
Le four de séchage unique est la base et l’unité centrale des équipements de séchage sous vide intermittent. Sa structure comprend généralement des unités de base telles qu’une chambre de séchage sous vide, une porte étanche entièrement automatique, un rack, une plaque d’étanchéité extérieure, un boîtier électrique, une canalisation sous vide, une canalisation d’azote, un système de contrôle, etc. Si un chauffage à air est utilisé, il comprendra également un tuyau de circulation d’air chaud. routes et systèmes de chauffage.
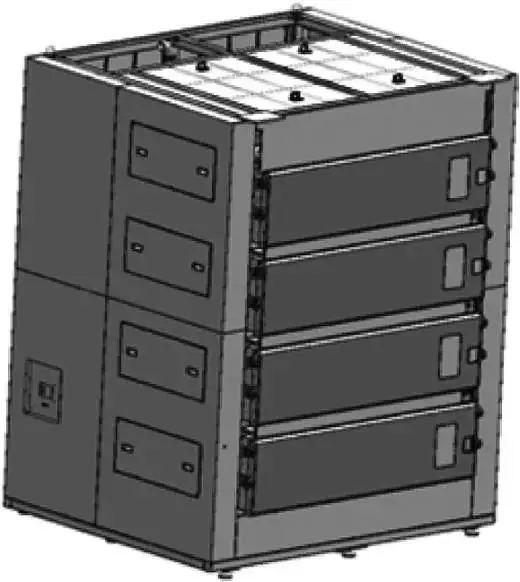
5.2 Équipement de séchage sous vide continu
L’équipement de séchage sous vide continu divise le processus de séchage en plusieurs processus tels que le préchauffage-le vide, le séchage-refroidissement, etc., et utilise différentes cavités ou postes de travail pour effectuer le préchauffage-vide, le séchage-refroidissement et d’autres processus. Ces cavités ou postes de travail sont Les positions sont reliées par des portes scellées, faisant du séchage un processus continu. De plus, il est équipé d’une plate-forme de chargement et de déchargement automatisée et d’un système de transmission pour compléter le séchage continu des matériaux. Son schéma structurel est illustré sur la figure. Cet équipement de séchage permet d’économiser considérablement la consommation d’énergie, et le nombre de stations dans chaque ensemble d’équipements peut être configuré en fonction des exigences spécifiques du processus et de la capacité de production.
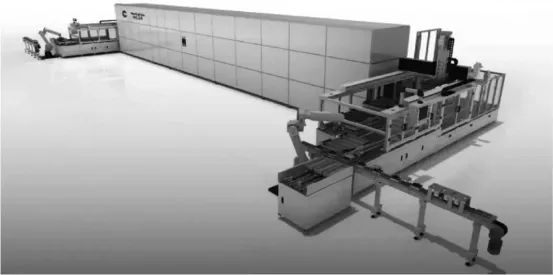
Flux de processus de l’équipement de séchage sous vide continu : Les noyaux de batterie entrent dans la plate-forme de chargement à partir de la ligne logistique du processus précédent. Ils sont positionnés, plaqués et empilés sur la plate-forme de chargement, puis envoyés dans la chambre de préchauffage pour le préchauffage. Après le préchauffage, ils passent à travers La cabine de transition de séchage entre dans la cabine de séchage sous vide pour le séchage sous vide. Après séchage, il entre dans la cabine de refroidissement pour le refroidissement. Après refroidissement, il passe à la plate-forme de déchargement pour le désempilage et le retrait des plateaux. Après cela, les cellules entrent dans la ligne logistique du processus suivant et les palettes retournent à la plate-forme de chargement. plateforme. La méthode de chauffage de la cabine de préchauffage peut être le chauffage à circulation d’air chaud ou le chauffage par contact. Le mode de chauffage de la cabine de séchage sous vide peut être le chauffage par contact ou le chauffage par rayonnement complété par un chauffage par circulation d’air chaud. L’ensemble du processus est contrôlé par un système de contrôle central.
L’équipement de séchage sous vide continu ou l’équipement de tunnel est généralement divisé en plusieurs étapes de base : préchauffage, séchage sous vide et refroidissement. La structure d’une section de préchauffage typique est illustrée sur la figure.
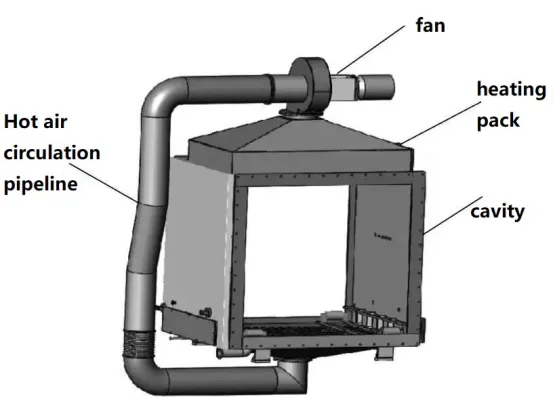
Sur l’image, le ventilateur entraîne le gaz interne pour qu’il s’écoule vers le bas, est chauffé par le pack chauffant, puis pénètre dans la cavité pour chauffer les matériaux à sécher dans la cavité. Ensuite, il pénètre dans le tuyau de circulation par la sortie d’air inférieure et retourne au ventilateur pour former un canal de circulation de gaz. La fonction principale de la section de préchauffage est de chauffer les matériaux secs pour atteindre rapidement la température de processus requise pour le séchage sous vide. Par conséquent, la vitesse de chauffage et l’uniformité de la température de la section de préchauffage sont ses principaux indicateurs de processus.
Une fois que le matériau séché a atteint la température prédéfinie, il est transféré dans la section de séchage sous vide par le dispositif de transport. La structure typique de la section de séchage sous vide est illustrée sur la figure.
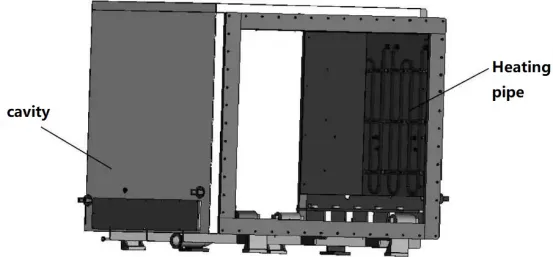
Le degré de vide du séchage sous vide est généralement d’environ 10 ~ 100Pa. Comme il se trouve dans un environnement sous vide et qu’il n’y a pas de gaz comme fluide, le transfert de chaleur par convection ne peut pas être utilisé. La section à vide dispose généralement d’un système de chauffage disposé autour de la cavité pour reconstituer l’énergie des matériaux secs par rayonnement.
Afin d’éviter l’oxydation de la pièce polaire, le matériau séché sous vide doit être refroidi avant de quitter l’équipement et d’entrer dans la salle de séchage. Par conséquent, la dernière section fonctionnelle de l’équipement de séchage sous vide continu est la section de refroidissement. La structure typique de la section de refroidissement est celle illustrée sur la figure.
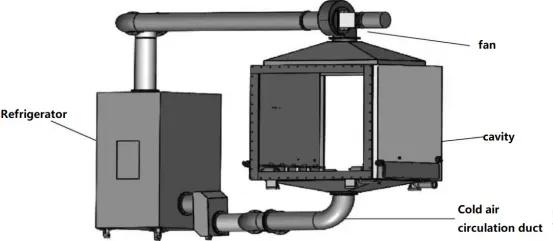
La section de refroidissement est généralement équipée d’un réfrigérateur externe pour fournir un refroidissement au gaz inerte. Le gaz pénètre dans la cavité par le ventilateur, force la convection pour refroidir et sécher le matériau, puis retourne au réfrigérateur par le tuyau de circulation d’air froid pour former un canal de circulation d’air froid. La section de refroidissement peut réduire la température des matériaux secs à un niveau proche de la température ambiante en peu de temps. Différentes courbes de refroidissement peuvent être obtenues en sélectionnant différents systèmes de réfrigération et débits de ventilateur.
5.3 Équipement de séchage sous vide avec différentes méthodes de chauffage
La température est un paramètre central du séchage sous vide, et le processus d’élévation de la température est une étape importante du processus de séchage. À l’heure actuelle, il existe deux méthodes de chauffage couramment utilisées sur les équipements : le chauffage par air et le chauffage par contact. Le chauffage par le vent est une méthode de chauffage qui chauffe l’air ou d’autres gaz inertes et utilise des ventilateurs et d’autres dispositifs pour le forcer à s’écouler dans la cavité, transférant ainsi la chaleur par convection forcée. C’est aussi la méthode de chauffage la plus utilisée dans l’industrie. Grâce à un contrôle précis de la température, le chauffage par air peut obtenir une répartition très uniforme de la température dans la cavité, obtenant ainsi une température de batterie uniforme.
Le chauffage par contact est une autre méthode de chauffage par séchage sous vide qui a progressivement élargi son application ces dernières années. Son principe de base est de placer la batterie sur la plaque chauffante ou au milieu de la plaque chauffante, et d’utiliser la conduction thermique pour chauffer la batterie. Comme le montre la figure, il existe trois méthodes de chauffage par contact : le contact unilatéral (en bas), le contact bilatéral (des deux côtés) et le contact à trois côtés (en bas plus des deux côtés).
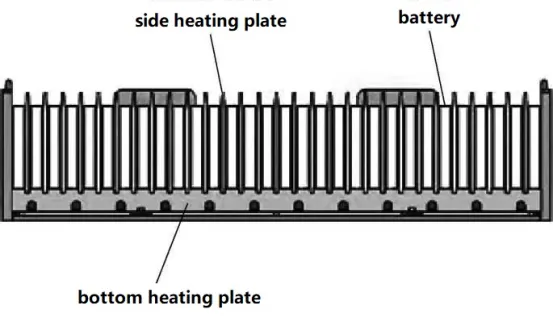
Comme vous pouvez le voir sur l’image, les plateaux de batterie chauffés par contact sont généralement sous tension. Lors du chargement et du déchargement, le plateau de batterie est retiré et placé en position de chargement et de déchargement pour mettre et retirer la batterie ; pendant le séchage sous vide, le plateau est élevé à la position de chauffage au centre de la chambre à vide, et l’alimentation électrique et la mesure de la température sont effectuées par des contacts électriques élastiques, et la plaque chauffante est Effectuer un contrôle en boucle fermée en temps réel. La batterie est préchauffée par marée chaude et, pendant l’étape de séchage sous vide, le gaz de marée chaude peut continuellement reconstituer l’énergie pour le séchage de la batterie.
L’utilisation du chauffage pneumatique et du chauffage par contact présente chacune ses propres avantages et inconvénients. L’équipement de chauffage pneumatique a une structure simple, une grande fiabilité et une bonne uniformité de température, mais nécessite un temps de chauffage court. L’équipement de chauffage par contact est plus léger car la puissance de la chaleur provient du gradient de température, de sorte que l’uniformité de la température est faible et qu’il faut du temps pour atteindre l’équilibre de température. Dans le même temps, les contacts électriques entre le plateau de batterie de chauffage par contact et la cavité doivent généralement être en contact avec un environnement sous vide, ce qui peut facilement causer des problèmes de capacité de production de vide et augmenter l’impact sur la production. Du point de vue des coûts, les équipements de chauffage pneumatiques ont des coûts inférieurs en raison de leurs avantages en termes de structure et de contrôle de la température ; tandis que le coût des équipements de type contact avec la même capacité de production sera d’environ 30 à 50 % plus élevé.
5.4 Équipement de séchage sous vide rouleau à rouleau
L’équipement de séchage sous vide rouleau à rouleau est spécialement conçu pour le séchage des rouleaux d’électrodes de batterie. En raison de la grande taille des rouleaux d’électrodes, le temps de séchage est généralement plus long et il peut y avoir des variations de teneur en humidité entre l’intérieur et la surface des rouleaux. Afin d’améliorer l’efficacité du séchage et d’obtenir une teneur en humidité constante, des équipements de séchage rouleau à rouleau ont été développés. Le concept de traitement rouleau à rouleau provient du revêtement et d’autres processus, et il s’agit d’une méthode plus efficace pour les matériaux à couche mince.
L’équipement de séchage sous vide rouleau à rouleau se compose principalement d’une chambre à vide et de dispositifs d’acquisition de vide. La chambre à vide comprend des composants pour le déroulement des rouleaux, le chauffage et le rembobinage. Le schéma de principe de l’équipement de séchage sous vide rouleau à rouleau est illustré dans le diagramme. Cependant, l’équipement de séchage rouleau à rouleau n’est pas encore une technologie de séchage mature. Il existe très peu d’appareils sur le marché, et les applications réussies à l’échelle industrielle de ces équipements sont presque inexistantes.
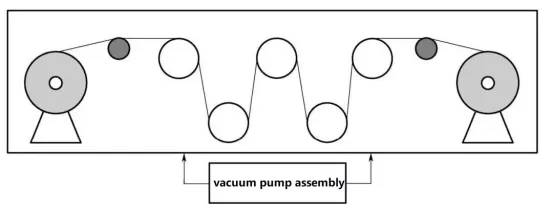
Le déroulement du séchage rouleau à rouleau est relativement simple : le rouleau d’électrode est placé sur l’arbre de déroulement et le film d’électrode passe à travers différents arbres et rouleaux chauffants avant de s’enrouler sur l’arbre de rembobinage. Les arbres de déroulement et de rembobinage tournent simultanément, et le rouleau d’électrode est chauffé et séché pour éliminer l’humidité lorsqu’elle passe à travers les rouleaux chauffants. L’ensemble du processus se déroule dans une chambre à vide. Une fois le séchage terminé, le rouleau d’électrode est déchargé de l’arbre de rembobinage.
Le schéma de traitement rouleau à rouleau est mature, mais il reste encore de nombreux défis à relever dans les équipements de séchage rouleau à rouleau. Tout d’abord, les composants de déroulement et de rembobinage ont des solutions matures sur le marché. Cependant, pour améliorer l’efficacité du séchage, des vitesses de déroulement et de rembobinage plus élevées sont souhaitables. Pour des rouleaux d’électrodes aussi légers et minces, l’augmentation de la vitesse peut entraîner la rupture du rouleau. De plus, comme les composants de déroulement et de rembobinage sont situés à l’intérieur de la chambre à vide, des mesures doivent être prises pour éviter la contamination par la poussière pendant le processus de transmission. Enfin, l’obtention d’un chauffage rapide, le contrôle de l’uniformité de la température et la détection lors de la transmission à grande vitesse du rouleau d’électrode posent des difficultés. De plus, les exigences en matière de niveau de vide et de température de l’équipement doivent être similaires ou équivalentes à celles des types d’équipement précédents.
5.5 Équipement de séchage sous vide pour le stockage logistique
L’équipement de séchage sous vide utilise les systèmes logistiques existants pour améliorer considérablement l’efficacité et la flexibilité du processus de séchage. Ce type d’équipement s’écarte de la grande chambre de séchage traditionnelle et utilise à la place des palettes avec des couvercles comme espaces de séchage, avec des racks de stockage pour contenir les plateaux de batteries couverts. Chaque poste de stockage est équipé d’un système d’amarrage sous vide et d’un système d’amarrage chauffant pour chauffer les batteries et créer un vide à l’intérieur des plateaux. L’équipement de séchage sous vide de stockage logistique est encore en phase de développement et n’a pas été mis en œuvre dans des applications pratiques. Le schéma de sa structure est illustré dans le diagramme.
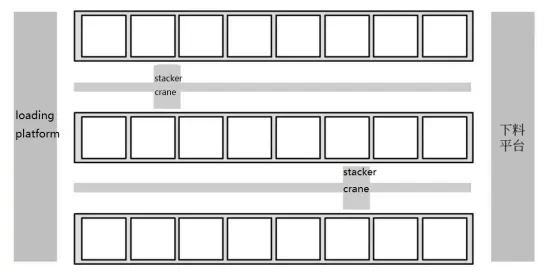
Sur la plate-forme de chargement, un robot dispose les batteries dans des plateaux et les recouvre. Le transstockeur place ensuite les plateaux assemblés avec les batteries sur les positions de stockage correspondantes sur les rayonnages de stockage. Le système d’aspiration et le système de chauffage sur les racks sont reliés aux plateaux pour chauffer et sécher les batteries. Une fois le processus de séchage terminé, le transstockeur place les batteries et les plateaux sur la plate-forme de déchargement, où les batteries sont déballées et passent au processus suivant.
L’équipement de séchage sous vide de stockage logistique repose sur le concept de logistique et de stockage, nécessitant ainsi un logiciel de planification logistique de haut niveau. De plus, le transstockeur utilisé pour la manutention des batteries et des plateaux doit répondre à des exigences spécifiques pour garantir l’efficacité de l’équipement. En utilisant l’espace du plateau comme chambre de séchage, l’équipement réduit la taille de la chambre tout en améliorant considérablement la flexibilité. Cependant, cela signifie également que chaque position de stockage doit être équipée de dispositifs de chauffage et d’amarrage sous vide, ce qui augmente les coûts d’équipement et de maintenance. Cet équipement présente de nombreuses similitudes avec les équipements de séchage sous vide intermittent. La principale différence réside dans la chambre plus petite et plus mobile de cet équipement, ce qui le rend plus flexible et adapté à la production personnalisée.
06.Évaluation des performances de l’équipement de séchage sous vide des batteries au lithium
6.1 Évaluation des performances du vide
Les performances de vide d’un équipement de séchage sous vide sont principalement évaluées en fonction de paramètres tels que le temps de pompage, le niveau de vide ultime et la capacité d’étanchéité sous vide de la chambre. L’évaluation de la performance du vide est généralement effectuée dans des conditions non chargées. La configuration de test comprend une pompe à vide, des soupapes à vide, un vacuomètre, des tuyaux, ainsi qu’un vacuomètre et une minuterie.
Le niveau de vide ultime fait référence à la pression la plus basse que la chambre peut atteindre. Un niveau de vide ultime inférieur est favorable à l’évaporation de l’humidité, mais il impose également des exigences plus élevées à l’équipement. Par conséquent, il faut trouver un équilibre entre le coût de l’équipement et le niveau de vide final. Étant donné que le processus de séchage de la plupart des batteries est généralement effectué à des pressions de quelques dizaines à quelques centaines de pascals (Pa), avec une pression de service comprise entre 20 et 1000 Pa, un niveau de vide ultime d’environ 10 Pa est suffisant.
Dans des conditions de pompage continu, le temps de pompage de l’équipement est défini comme le temps nécessaire pour atteindre la valeur de pression ultime après ouverture de la chambre pendant 15 minutes, puis évacuation à nouveau. En général, le temps de pompage doit être d’environ 5 à 10 minutes, et si l’exigence ne peut pas être satisfaite, il faut envisager de remplacer la pompe à vide pour répondre aux exigences.
La chambre à vide est reliée à l’entrée d’aspiration de la pompe à vide par une tuyauterie à vide pour garantir l’étanchéité de l’ensemble du système de vide. La pompe à vide est mise en marche et, lorsque le niveau de vide atteint la pression finale, la pompe est arrêtée et la pression est maintenue pendant 24 heures. La courbe de temps et de pression est enregistrée, et la section linéaire de la courbe de pression en fonction du temps est identifiée. La pente de cette section linéaire représente la valeur de la capacité de scellage sous vide (c’est-à-dire l’augmentation du niveau de vide par heure). La capacité de scellage sous vide doit généralement être inférieure à 5 Pa/h. Si la capacité d’étanchéité sous vide ne répond pas aux exigences, un détecteur de fuite d’hélium doit être utilisé pour tester la chambre et améliorer ses performances d’étanchéité.
6.2 Évaluation de la performance en température
Les performances thermiques des équipements de séchage sous vide des batteries au lithium sont principalement évaluées en fonction de paramètres tels que le temps de chauffage, la fluctuation de la température, la stabilité de la température et l’uniformité de la température. L’évaluation de la performance en température est également généralement effectuée dans des conditions non chargées. La configuration de test des performances thermiques comprend des capteurs de température tels que des thermorésistances et des thermocouples, ainsi qu’un enregistreur de température. Pour le chauffage à air pulsé, le point de mesure de la température est généralement le centre de la chambre, tandis que pour le chauffage par contact, c’est le centre de l’appareil de chauffage.
Le temps de chauffage fait référence au temps qu’il faut à l’équipement pour atteindre la température de processus pour le séchage de la batterie lorsque l’appareil de chauffage fonctionne à la puissance maximale à partir de la température ambiante. Pour le chauffage à air pulsé, le temps de chauffage ne doit pas dépasser 90 minutes, tandis que pour le chauffage par contact, il ne doit pas dépasser 10 minutes. La fluctuation de température est définie comme la moitié de la différence entre les températures les plus élevées et les plus basses au point de mesure dans un délai spécifié de 30 minutes après que la température s’est stabilisée pendant le processus de séchage. La fluctuation de température de l’équipement de séchage de la batterie ne doit pas dépasser ±1°C.
La stabilité de la température est déterminée par la différence maximale entre la température moyenne de plusieurs mesures de température prises à différents intervalles de temps dans les 24 heures suivant la stabilisation de la température pendant le processus de séchage et la température moyenne pendant la période initiale. La stabilité de la température de l’équipement de séchage de la batterie ne doit pas dépasser 2°C.
L’uniformité de la température est définie comme la moitié de la différence maximale entre les températures moyennes en deux points quelconques de la chambre (pour le chauffage à air pulsé) ou sur le dispositif de chauffage (pour le chauffage par contact) pendant un intervalle de temps spécifié après que la température s’est stabilisée pendant le processus de séchage. Pour le chauffage à air pulsé, les points de mesure de la température doivent inclure plusieurs points au centre et sur les bords de la chambre, tandis que pour le chauffage par contact, les points doivent inclure le centre et les bords de l’appareil de chauffage. L’uniformité de la température de l’équipement de séchage de la batterie ne doit pas dépasser ±3°C. Une courbe typique d’essai d’uniformité de la température est illustrée sur la figure.
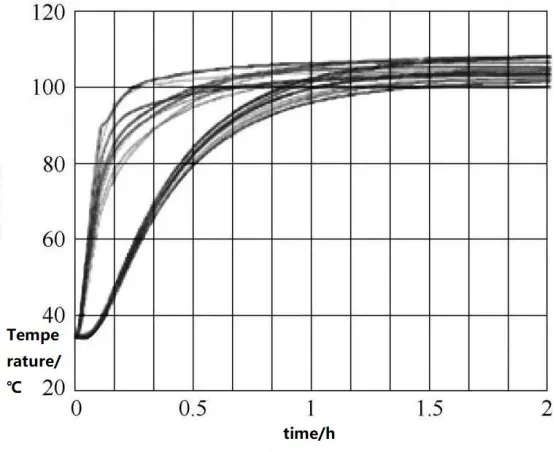
6.3 Évaluation de l’humidité après séchage
Niu Junting et al. ont mené une étude systématique sur la relation entre l’humidité résiduelle dans les pièces polaires de la batterie et les performances de la batterie. Les batteries avec une teneur en humidité positive de la feuille d’électrode comprise entre 0,04 % et 0,05 % ont de bonnes performances de cycle. Après 200 cycles de charge et de décharge actuels, la capacité de décharge de la batterie reste toujours à 92,9 % de la capacité initiale. Au fur et à mesure que le cycle avance, la capacité des batteries avec une teneur en humidité supérieure à 0,06 % dans la feuille d’électrode positive diminue rapidement et les performances se détériorent. Les batteries dont la teneur en humidité dans la pièce polaire de la batterie est comprise entre 0,03 % et 0,06 % ont une capacité spécifique de décharge élevée et rapprochée. À mesure que le taux de décharge augmente, la teneur en humidité de la pièce polaire de la batterie dépasse 0,06 % et le taux d’atténuation de la capacité augmente. Étant donné qu’une humidité excessive a un impact négatif important sur les performances de la batterie, la teneur en humidité actuelle de la batterie après séchage doit généralement être inférieure à 500 mg / kg, et il est préférable de la réduire à 200 ~ 300 mg / kg.
Étant donné que la teneur en humidité de la batterie est faible après séchage, généralement seulement quelques centaines de milligrammes par kilogramme, elle ne peut pas être mesurée par une méthode simple. La méthode Karl Fischer-Coulomb est généralement utilisée pour tester l’humidité à l’état de traces, et son principe est une méthode électrochimique. Le principe de réaction est que l’eau participe à la réaction redox de l’iode et du dioxyde de soufre.
On peut voir à partir de la réaction ci-dessus que 1 mol d’iode oxyde 1 mol de dioxyde de soufre, ce qui nécessite 1 mole d’eau. Par conséquent, la puissance d’électrolyse de l’iode est équivalente à la puissance d’électrolyse de l’eau. L’électrolyse de 1 mol d’iode nécessite 2×96493C de puissance, et l’électrolyse de 1 mmol d’eau nécessite 96493 mC de puissance. La masse d’humidité mesurée est calculée selon la formule suivante :
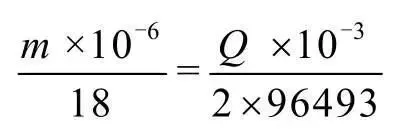
Dans la formule, m est la masse d’eau mesurée, μg ; Électrolyte Q, mC ; 18 électrolyte d’eau.
La masse d’humidité mesurée comprend également l’humidité dans le système d’essai. Par conséquent, l’humidité dans l’humidité doit être mesurée sur la base de la perte totale de masse d’humidité de la bouteille vide (valeur à blanc), et l’influence de la valeur d’humidité (valeur de dérive) doit être prise en compte. L’humidité dans l’humidité La teneur est calculée comme suit :
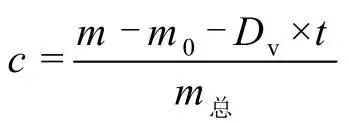
Dans la formule, c teneur en humidité de l’échantillon, μg/g ; m0 masse d’humidité de la bouteille vide, μg ; valeur de dérive Dv, μg/min ; t temps d’extraction, min ; m total – masse totale de l’échantillon, g.
Le schéma structurel du testeur d’humidité Karl Fischer-Coulomb est illustré à la figure. Il comprend principalement une cellule électrolytique Karl Fischer et une unité de chauffage d’échantillons. L’échantillon de pièce polaire est placé dans une bouteille d’échantillon scellée, puis la bouteille d’échantillon est chauffée à une certaine température. L’eau dans la cellule électrolytique s’évapore, puis le gaz sec est utilisé pour envoyer la vapeur d’eau dans la cellule électrolytique pour participer à la réaction, puis l’électricité générée pendant le processus d’électrolyse est mesurée pour titrer la teneur en eau.
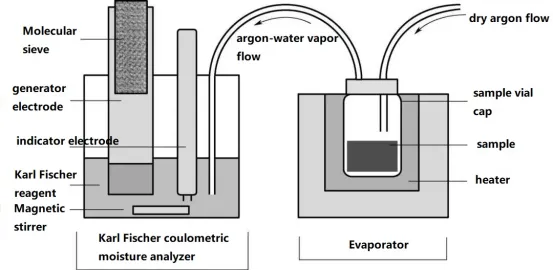
Lors de la réalisation d’un test d’humidité sur des échantillons de batterie à l’aide d’un dessiccateur coulométrique Karl Fischer après séchage, les points suivants doivent être pris en compte :
un. Le flacon d’échantillon doit être séché avant l’échantillonnage, généralement à 120-160°C pendant 3 à 6 heures. Après le retrait, il doit être immédiatement scellé avec un bouchon. La teneur en humidité du flacon d’échantillon doit être inférieure à 10 μg, et plus elle est basse, mieux c’est.
b. L’échantillonnage doit être effectué dans un environnement où le point de rosée est atteint. Il est généralement recommandé d’avoir un point de rosée inférieur à -40°C. Laissez le flacon d’échantillon vide non bouché pendant 1 à 2 heures comme test à blanc.
c. La plaque d’électrode peut être coupée en petits morceaux d’environ 0,5 cm ou sur la hauteur du flacon d’échantillon.
d. La taille de l’échantillon pour l’analyse ne doit généralement pas être inférieure à 0,5 g.
e. Il est recommandé d’utiliser une balance électronique de précision avec une résolution de 0,1 mg pour le pesage.
f. Avant d’effectuer des tests formels sur l’échantillon, assurez-vous que la dérive du courant est inférieure à 20 μg/min et stable sans tendances significatives à la hausse ou à la baisse.
g. Une fois l’échantillon terminé, retirez le flacon contenant l’échantillon du four Karl Fischer, réinsérez-le dans la bouteille de dérive et laissez l’instrument se stabiliser avant de passer à l’échantillon suivant.
h. La température recommandée pour le four Karl Fischer est de 120-180°C. Une température excessive peut provoquer une volatilisation ou des réactions secondaires de certains matériaux dans la batterie, entraînant des résultats de test inexacts. En cas de doute sur la température d’essai, la méthode de chauffage par gradient peut être utilisée avec le dessiccateur Karl Fischer pour analyser la teneur en humidité des matériaux des batteries lithium-ion et des plaques d’électrodes.
07 Direction du développement de l’équipement de séchage sous vide
7.1 Amélioration continue de l’efficacité du séchage
Réduire le temps de séchage et améliorer l’efficacité du séchage a toujours été un objectif des équipements de séchage. L’amélioration de l’efficacité du séchage sous vide permet de réduire les coûts des produits et d’améliorer les avantages économiques. Actuellement, les équipements de séchage sont de plus en plus automatisés, ce qui contribue également à améliorer l’efficacité du séchage. À l’avenir, il est nécessaire de développer de nouvelles méthodes de chauffage pour améliorer l’efficacité du chauffage, de développer des systèmes logistiques adaptés aux équipements de séchage pour améliorer l’efficacité du chargement et du déchargement, de créer des équipements de séchage à faible consommation d’énergie, de mener des recherches sur les mécanismes de séchage des batteries pour optimiser les processus de séchage, d’utiliser des logiciels et des techniques de surveillance pour améliorer le contrôle des processus et d’améliorer l’efficacité opérationnelle de l’équipement.
7.2 Conception modulaire et normalisée de l’équipement
Actuellement, les équipements de séchage des batteries sont conçus sur mesure en raison des différentes spécifications des batteries sur le marché. Ce manque de standardisation limite la flexibilité des équipements de séchage des batteries et entrave leur évolutivité. À l’avenir, il devrait y avoir des normes correspondantes pour les spécifications des batteries, et la conception de l’équipement de séchage devrait respecter ces normes. Cela inclut des aspects tels que la taille de la chambre, le choix des pompes à vide, les exigences relatives aux plaques chauffantes et les positions d’installation des vacuomètres et des vannes. De plus, en raison de la demande de production par lots de batteries, les équipements de séchage deviennent de plus en plus volumineux, et l’installation et le débogage sur site nécessitent souvent beaucoup de main-d’œuvre, de ressources et de temps. Lors de la conception d’un équipement de séchage, la modularisation doit être prise en compte, chaque module disposant de fonctionnalités indépendantes pour économiser le temps d’installation et de débogage sur site.
7.3 Système d’exécution de la fabrication (MES) pour l’orientation de la production
Avec l’automatisation croissante de la production de batteries, les systèmes logiciels des équipements de séchage sont également mis à niveau. Actuellement, le logiciel de l’équipement de séchage peut afficher les données de consommation d’énergie, enregistrer des informations sur le produit et les données de processus, qui sont des exigences de base. Cependant, le MES actuel se concentre principalement sur la collecte et le stockage des données pour la traçabilité des données de séchage. À l’avenir, le MES devrait aller au-delà de ces fonctions et utiliser des techniques telles que le big data pour fournir des conseils et améliorer les processus de séchage des batteries, aider à la maintenance des équipements et améliorer l’efficacité du séchage.
7.4 Détection d’humidité en ligne
Comme mentionné précédemment, les tests d’humidité après le séchage des batteries nécessitent la destruction des batteries pour évaluer leur teneur en humidité et déterminer leur acceptabilité. À l’heure actuelle, il n’existe aucune méthode efficace de détection de l’humidité en temps réel. À l’avenir, des recherches devraient être menées pour développer de nouvelles méthodes de test des batteries capables de surveiller la teneur en humidité pendant le processus de séchage en temps réel, sans qu’il soit nécessaire de procéder à des tests destructifs ou à une analyse de l’humidité après le séchage. Si la teneur en humidité s’avère non conforme pendant le processus de séchage, des ajustements immédiats peuvent être apportés au processus de séchage jusqu’à ce que la teneur en humidité réponde aux normes souhaitées. Le développement de nouvelles méthodes de détection de l’humidité nécessite des recherches approfondies sur le mécanisme d’évaporation de l’humidité des batteries et les facteurs d’influence pertinents. Par conséquent, l’étude du processus de séchage des batteries est d’une importance significative pour l’avancement des équipements de séchage.