Water content has a significant impact on battery performance and must be strictly controlled during the manufacturing process. The presence of water in batteries can cause degradation of the electrolyte, or react with the electrolyte to produce harmful gases, leading to increased pressure and deformation within the battery. Excessive water content in batteries can also result in high internal resistance, high self-discharge, low capacity, poor cycling performance, and even leakage, greatly degrading battery performance. Therefore, a drying process is essential in lithium battery production.
01 Introduction to Drying
Drying is a chemical unit operation that involves providing energy to moist materials to vaporize and remove the contained moisture, resulting in the production of dried materials. Currently, there are numerous drying equipment options in the industry, and they can be classified using different methods. Based on the operating mode, drying equipment can be categorized as continuous drying equipment and batch (intermittent) drying equipment. According to the operating pressure, it can be classified as atmospheric drying equipment and vacuum drying equipment. Furthermore, based on the heat transfer method, drying equipment can be further classified into conduction drying equipment, convection drying equipment, radiation drying equipment, and dielectric drying equipment, among others.
The water content in batteries primarily originates from moisture present in the battery’s raw materials, including the positive and negative electrode sheets, separator, electrolyte, and other metal components, as well as from the moisture in the factory environment. To address environmental moisture, a dry room can be established, where a drying machine generates dry air that is continuously supplied to the dry room, displacing the humid air and eliminating environmental moisture. For internal moisture in the battery, due to the high drying standards required, typically demanding a moisture content between (100-300)×10-6, vacuum drying equipment is generally employed to remove water. After drying, the batteries are tested to ensure they meet the baking requirements. Multiple process steps in the production of batteries require vacuum drying, such as for battery electrode powders, positive and negative electrode winding, and cell assembly before electrolyte injection. Therefore, vacuum drying equipment is crucial for battery manufacturing.
02 Principle of Vacuum Drying
The principle of vacuum drying is based on the fact that the boiling point of water changes under different pressure environments. The relationship between pressure and boiling point is depicted in Figure.
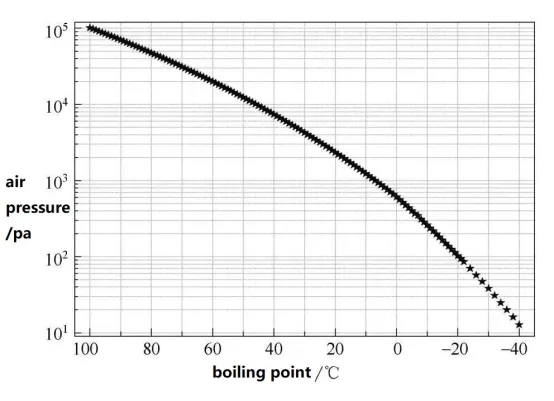
It can be seen from the figure that under normal pressure, that is, one atmospheric pressure, the boiling point of water is 100°C, but as the air pressure decreases, the boiling point of water continues to decrease. In a vacuum environment of about 100Pa, the boiling point of water has dropped to about -20°C. This is the basic principle that a vacuum environment can promote the drying process.
Therefore, vacuum drying is the process of removing moisture contained in materials under environmental conditions below one standard atmospheric pressure. The basic kinetic principle of vacuum drying is the heat and mass transfer theory. During the process of vacuum drying, the vacuum system continuously heats the material to be dried while evacuation, so that the moisture inside the material diffuses to the surface through the pressure difference or concentration difference. The water molecules obtain sufficient kinetic energy on the surface of the material to overcome the mutual attraction between molecules. Fly into the low-pressure space of the vacuum chamber and be sucked away by the vacuum pump.
The rate of moisture loss during the vacuum drying process and the mass of moisture vaporized and discharged from the dry material per unit drying area per unit time are the drying speed, that is
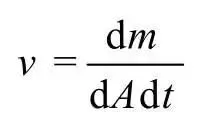
In the formula, v drying speed, g/(m2·h); m discharged moisture mass, g; A drying area, m2; t drying time, h.
In the drying of batteries, more attention is generally paid to the moisture content rather than the moisture quality. Moreover, the moisture content in the battery is extremely small, and the evaporated moisture quality is difficult to measure. Considering that the change in moisture content is used to replace the change in moisture mass per unit area, the above formula can be transformed into:
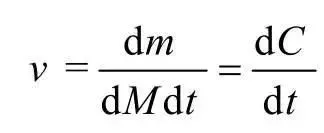
In the formula, v drying speed, mg/(kg·h); m discharged moisture mass, mg; M total material mass, kg; C moisture content, mg/kg; t drying time, h.
A typical vacuum drying speed curve is shown in the figure. The water loss process is divided into three stages: accelerated drying stage, constant speed drying stage, and decelerated drying stage. Section AB is the accelerated drying stage. At this time, the moisture content in the material is constant. Due to vacuuming and heating, the material is heated to the vaporization temperature under the corresponding pressure within the allowable temperature range and vaporizes in large quantities, and the drying speed continues to increase. Due to the limitation of heat and mass transfer characteristics, the drying speed reaches the maximum value and enters the BC section, which is the constant speed drying stage. At this time, the temperature of the material remains unchanged, the heating heat is used as the latent heat of vaporization and various heat losses, and the vaporization steam is continuously discharged. The pressure difference between the evaporation surface and the space is maintained, allowing drying to continue. When the moisture content of the material is reduced to a certain level, the evaporated moisture is reduced, and the pressure difference between the evaporation surface and the space is reduced. It enters the CD section, which is the deceleration drying stage, and the drying speed gradually decreases and approaches zero.
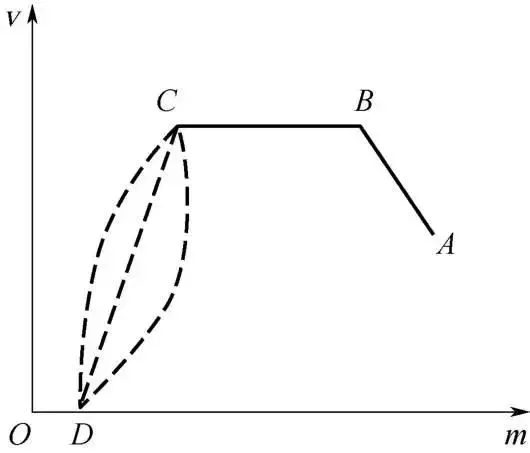
There are many factors that affect the drying speed during the vacuum drying process. First of all, the shape, size and stacking method of the material to be dried, as well as the moisture content, density and other physical properties of the material itself will affect the drying speed. Secondly, the working vacuum degree of the drying equipment will affect the drying speed. If the vacuum degree is high, the moisture can be vaporized at a lower temperature. However, the high vacuum degree is not conducive to heat conduction and will reduce the heating effect. Finally, the structural form, heating method and drying process of the drying equipment will all affect the drying speed. Therefore, it is very difficult to calculate drying time and drying speed.
At present, it is difficult to measure the moisture changes during battery drying, so there are not many experimental studies in this area. However, studying the water evaporation mechanism in batteries has important guiding significance for the battery drying process. Guan Yuming et al. used computational fluid dynamics (CFD) simulation software to analyze the water evaporation rate in the battery core. They completed the simulation analysis by loading the battery core moisture diffusion function compiled language calculated by Fick’s law and found that the water evaporation rate on the battery core surface was The fastest baking time is about 10 minutes, while the water evaporation rate at the bottom of the battery core is very low at the beginning, and the fastest time is about 50 minutes, as shown in Figure .
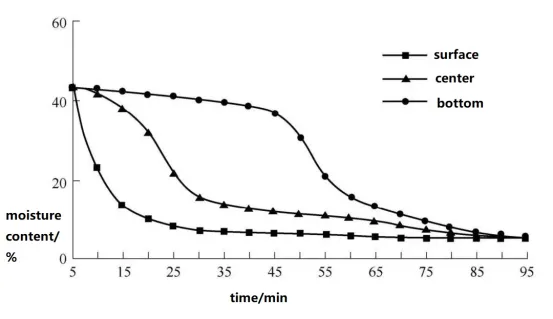
03 Battery vacuum drying process
In the production process of lithium batteries, several basic steps such as slurry mixing, coating, rolling, slitting, winding/lamination, welding, sealing, liquid injection, formation, volume division and assembly are required. In order to control the moisture content of the final product, moisture control points must be set at different key nodes of the production process. Typical designs include moisture control of cathode powder materials, moisture control of pole rolls/pole sheets, and most importantly, moisture control before battery injection.
In the production process of lithium-ion batteries, the positive and negative electrode powder materials generally need to be moisture controlled before slurrying, and dried simultaneously through the final stage of powder manufacturing. During the slurry mixing process, the negative electrode is generally a water-based slurry, and the positive electrode is generally an oil-based slurry. After the slurry is coated, a preliminary drying is performed. The main purpose of this step is to remove the solvent in the slurry and form a battery pole piece with a microporous structure. After this step of drying, there is still a lot of moisture remaining in the pole piece. There are two main drying processes to remove the residual moisture: a. Before the battery is rolled or laminated, the battery pole pieces are vacuum dried. The general drying temperature is 120~150°C. The battery pole pieces are often dried in rolls or piles; b. Before filling the battery with liquid, vacuum dry the assembled battery. Since the battery contains components such as separators at this time, the drying temperature is generally 60 to 90°C.
The setting of the drying temperature is not arbitrary, it is related to the existence form of moisture in the solid material before the lithium battery is filled with liquid. According to the nature and size of the force between solid material molecules and water molecules, there are three main forms of water, as shown in the figure. The first is water adhesion, which is simply mechanically attached to the surface of the material; the second is adsorption of water, in which water is combined with solid matter in the form of physical or chemical adsorption; the third is combined water, in which water is combined with material in the form of crystal hydrates. combine. For attached moisture, it can naturally volatilize at normal temperature and pressure; for adsorbed moisture, it can evaporate at around 105°C under normal pressure; while the evaporation of compound moisture usually needs to reach above 150°C under normal pressure. In a vacuum environment, the moisture removal temperature can be significantly reduced. The higher the temperature, the better the moisture removal effect, but the temperature should not be too high, because most of the lithium battery separators are made of polymer materials, such as high-density polyethylene and high-density polypropylene, and these polymer materials are not suitable for use at high temperatures. It will degrade at high temperatures, causing serious safety issues. Therefore, setting the drying temperature of lithium batteries reasonably is an extremely important issue and needs to be adjusted appropriately according to the specific material system.
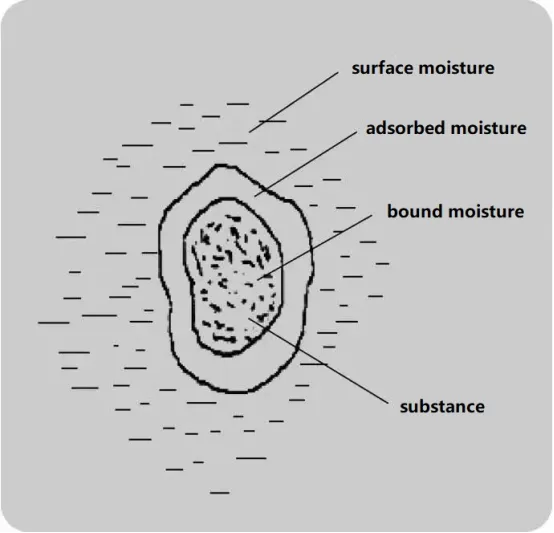
The drying process of the battery generally includes three stages: preheating, vacuum drying, and cooling. Since the heat transfer in the vacuum section is slow, it is generally preheated at normal pressure or higher pressure, and then the battery is evacuated after it reaches a certain temperature. Remove moisture and cool to room temperature after drying to avoid oxidation of battery materials. The dried battery should try to avoid contact with the atmospheric environment. Process parameters such as temperature, vacuum degree, preheating time, and vacuum maintenance time during the drying process have an important impact on the drying results. Choosing appropriate process parameters is conducive to improving drying efficiency.
04 Basic composition and classification of vacuum drying equipment
Currently, the vacuum drying equipment used in the lithium battery industry has achieved basic fully automatic operation. The equipment’s basic components include heating elements, vacuum systems, drying chambers, loading and unloading platforms, and a central control system.
The heating component is used to supply heat to the drying equipment. Heating components can be divided into electric heating, electromagnetic induction heating, microwave heating, etc. according to different heating sources. At present, the most commonly used method of battery drying equipment is electric heating. Electric heating also includes hot air circulation heating and contact heating. Hot air circulation heating is a combination of heating device and fan, which can make any position in the drying chamber reach the drying temperature. Contact heating uses the heating device to directly contact the battery to conduct heat to the battery, which improves energy utilization efficiency and can effectively save energy consumption. The main design requirements for heating components are heating rate, temperature stability and temperature uniformity. Therefore, it is very important to control and monitor temperature. The heating components need to be equipped with corresponding temperature control components and detection components.
The effective pumping speed of the pump is calculated as follows:
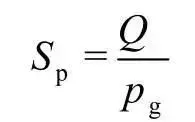
In the formula, the effective pumping speed of Sp pump, m3/s; the working pressure required by pg vacuum chamber, Pa; the total gas volume of Q vacuum chamber, Pa・m3/s.
Q=1.3(Q1+Q2+Q3)
In the formula, Q1——the amount of gas generated during the vacuum process, Pa・m3/s; the outgassing amount of Q2 vacuum chamber, Pa・m3/s; the total air leakage amount of Q3 vacuum chamber, Pa・m3/s.
The nominal pumping speed of the pump is calculated as follows:
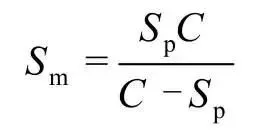
In the formula, Sm is the nominal pumping speed of the pump, m3/s; C is the pipe connection between the vacuum chamber outlet and the unit inlet, m3/s.
The loading and unloading platform is used for loading and unloading batteries, including assembling (dismantling) and stacking (de-stacking) batteries, scanning battery trays, etc., and handling NG situations, etc. With the improvement of automation requirements, battery loading and unloading has been basically automated, requiring less manual intervention. At the loading station, the barcode reader scans the battery and pallet. The battery that scans the NG code is placed on the NG platform. The battery robot loads the successfully scanned battery into the pallet. When the pallet is full, the pallet robot stacks the pallet to the top. At the material table, the loading table is filled and enters the drying cavity; after drying is completed, the batteries are sent out from the drying cavity, and the pallet robot destackers the pallets layer by layer. The battery robot then takes the batteries out of the pallet and enters the next one. process.
The control system is responsible for controlling the vacuum system, heating elements, and motion components of the drying system. However, with the development of big data and the Internet of Things, these functions are no longer sufficient to meet current production requirements. Software systems have become increasingly important for drying equipment. In addition to controlling the hardware, the software needs to have the following functionalities:
1.Ability to diagnose equipment faults, display current and historical faults, and provide troubleshooting methods.
2.Ability to display input and output signals and real-time status of all sensors and actuators.
3.Ability to obtain real-time equipment status and statistics on equipment status and alarm information within 24 hours.
4.Ability to collect information such as material types, batches, models, and specifications, establish a material tracking system, and track and trace material information.
5.Ability to track and manage the production process, collect process parameters of relevant stations during material drying, including temperature, vacuum level, etc.
6.Ability to query historical data, including production execution, equipment usage, process control, etc.
Currently, there is no unified standard for battery vacuum drying equipment, and there are various specifications and forms. Based on the chamber shape, it can be divided into circular chamber drying equipment and square chamber drying equipment. Based on the heating method, it can be divided into hot air circulation heating equipment, contact heating drying equipment, induction heating equipment, etc. Based on the different stages of battery production, it can be divided into positive and negative electrode powder drying equipment, positive and negative electrode winding drying equipment, battery cell drying equipment, etc. Based on the discharge method of the drying equipment, it can be divided into batch drying equipment and continuous drying equipment.
05 Typical battery vacuum drying equipment
5.1 Intermittent vacuum drying equipment
Intermittent vacuum drying equipment combines multiple traditional single drying furnaces and is equipped with automated loading and unloading robots and central dispatching robots to achieve mass production. Its structural diagram is shown in the figure. This drying equipment has relatively high flexibility. The number of drying ovens equipped in each set of equipment and the number of cavities in each drying oven can be configured according to specific needs.
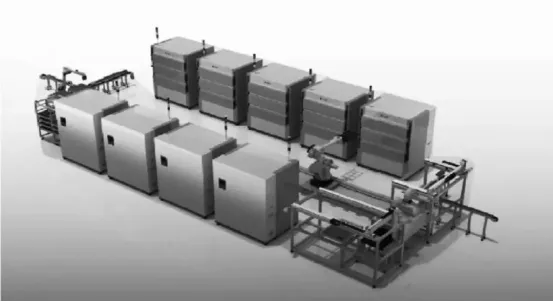
The loading platform of the drying equipment is docked with the previous process’s material flow line. The battery cells are transferred from the previous process’s material flow line to the loading platform. They are then positioned and assembled on the loading platform before being transferred to the corresponding drying oven for drying. After the drying process, the cells are moved to the unloading platform for disassembly and cooling before entering the next process’s material flow line. The heating method of the drying oven can be either hot air circulation or contact heating. The entire process is controlled by a central control system.
The single drying furnace is the basis and core unit of intermittent vacuum drying equipment. Its structure usually includes basic units such as a vacuum drying chamber, a fully automatic sealed door, a rack, an outer sealing plate, an electrical box, a vacuum pipeline, a nitrogen pipeline, a control system, etc. If air-driven heating is used, it will also include a hot air circulation pipe. roads and heating systems.
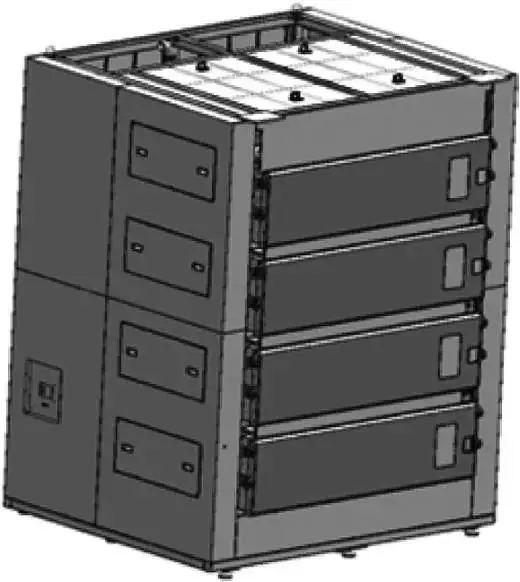
5.2 Continuous vacuum drying equipment
Continuous vacuum drying equipment divides the drying process into multiple processes such as preheating-vacuum drying-cooling, etc., and uses different cavities or work stations to perform preheating-vacuum drying-cooling and other processes. These cavities or work stations are The positions are connected with sealed doors, making drying a continuous process. In addition, it is equipped with an automated loading and unloading platform and transmission system to complete the continuous drying of materials. Its structural diagram is shown in the figure. This drying equipment can save energy consumption to a great extent, and the number of stations in each set of equipment can be configured according to specific process requirements and production capacity.
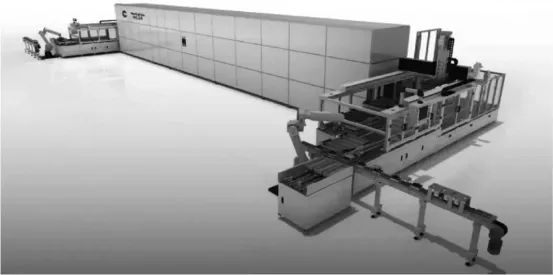
Continuous vacuum drying equipment process flow: The battery cores enter the loading platform from the logistics line of the previous process. They are positioned, plated and stacked on the loading platform, and then sent to the preheating chamber for preheating. After preheating, they pass through The drying transition cabin enters the vacuum drying cabin for vacuum drying. After drying, it enters the cooling cabin for cooling. After cooling, it goes to the unloading platform for destacking and tray removal. After that, the cells enter the logistics line of the next process, and the pallets return to the loading platform. platform. The heating method of the preheating cabin can be hot air circulation heating or contact heating. The heating mode of the vacuum drying cabin can be contact heating or radiant heating supplemented by hot air circulation heating. The entire process is controlled by a central control system.
Continuous vacuum drying equipment or tunnel equipment is usually divided into several basic stages: preheating, vacuum drying, and cooling. The structure of a typical preheating section is shown in the figure.
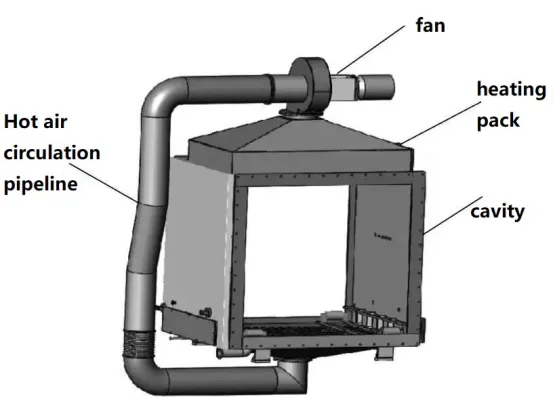
In the picture, the fan drives the internal gas to flow downward, is heated by the heating pack, and then enters the cavity to heat the materials to be dried in the cavity. Then it enters the circulation pipe through the bottom air outlet and returns to the fan to form a gas circulation channel. The main function of the preheating section is to heat the dry materials to quickly reach the process temperature required for vacuum drying. Therefore, the heating rate and temperature uniformity of the preheating section are its main process indicators.
After the dried material reaches the preset temperature, it is transferred to the vacuum drying section through the conveying device. The typical vacuum drying section structure is shown in the figure.
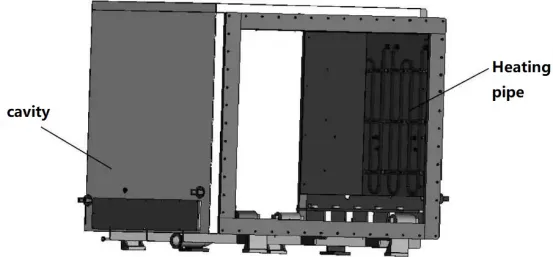
The vacuum degree of vacuum drying is usually around 10~100Pa. Since it is in a vacuum environment and there is no gas as a medium, convection heat transfer cannot be used. The vacuum section usually has a heating system arranged around the cavity to replenish energy to the dry materials through radiation.
In order to prevent the oxidation of the pole piece, the vacuum-dried material needs to be cooled before leaving the equipment and entering the drying room. Therefore, the last functional section of the continuous vacuum drying equipment is the cooling section. The typical cooling section structure is as shown in the figure.
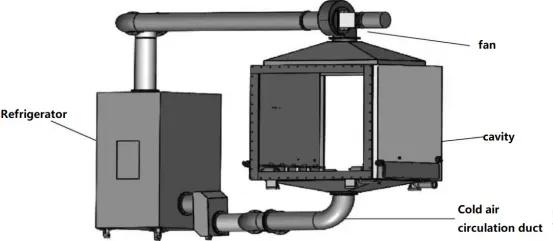
The cooling section is usually equipped with an external refrigerator to provide cooling inert gas. The gas enters the cavity through the fan, forced convection to cool and dry the material, and then returns to the refrigerator through the cold air circulation pipe to form a cold air circulation channel. The cooling section can reduce the temperature of dry materials to close to room temperature in a short period of time. Different cooling curves can be achieved by selecting different refrigeration systems and fan flow rates.
5.3 Vacuum drying equipment with different heating methods
Temperature is a core parameter of vacuum drying, and the temperature rise process is an important stage of the drying process. Currently, there are two commonly used heating methods on equipment: air-driven heating and contact heating. Wind-driven heating is a heating method that heats air or other inert gas media and uses fans and other devices to force it to flow in the cavity, thereby transferring heat through forced convection. This is also the most commonly used heating method in industry. Through precise temperature control, air-driven heating can achieve a very uniform temperature distribution in the cavity, thereby obtaining a uniform battery temperature.
Contact heating is another vacuum drying heating method that has gradually expanded its application in recent years. Its basic principle is to place the battery on the heating plate or in the middle of the heating plate, and use heat conduction to heat the battery. As shown in the figure, there are three contact heating methods: single-sided (bottom) contact, two-sided (both sides) contact, and three-sided (bottom plus both sides) contact.
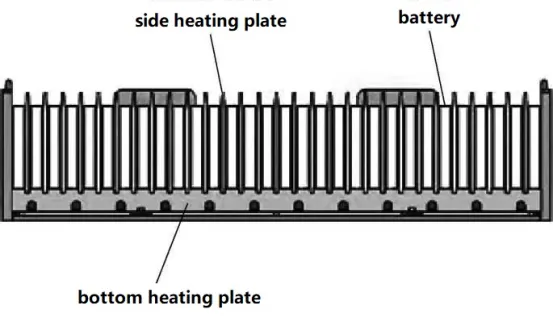
As you can see from the picture, contact heated battery trays are usually energized. When loading and unloading, the battery tray is taken out and placed in the loading and unloading position to put in and take out the battery; during vacuum drying, the tray is raised to the heating position in the center of the vacuum chamber, and power supply and temperature measurement are performed through elastic electrical contacts, and the heating plate is Perform real-time closed-loop control. The battery is preheated by hot tide, and during the vacuum drying stage, the hot tide gas medium can continuously replenish energy for battery drying.
The use of air-driven heating and contact heating each has its own advantages and disadvantages. The air-operated heating equipment has a simple structure, high reliability, and good temperature uniformity, but requires a short heating time. The contact heating equipment is lighter because the power of heat comes from the temperature gradient, so the temperature uniformity is poor and it takes time to reach temperature equilibrium. At the same time, the electrical contacts between the contact heating battery tray and the cavity must usually be in contact with a vacuum environment, which can easily cause vacuum production capacity problems and increase the impact on production. From a cost perspective, air-operated heating equipment has lower costs due to its advantages in structure and temperature control; while the cost of contact-type equipment with the same production capacity will be about 30% to 50% higher.
5.4 Roll-to-Roll Vacuum Drying Equipment
Roll-to-roll vacuum drying equipment is specifically designed for drying battery electrode rolls. Due to the large size of the electrode rolls, the drying time is generally longer, and there can be variations in moisture content between the interior and surface of the rolls. In order to improve drying efficiency and achieve consistent moisture content, roll-to-roll drying equipment has been developed. The concept of roll-to-roll processing originated from coating and other processes, and it is a more efficient method for thin film materials.
Roll-to-roll vacuum drying equipment mainly consists of a vacuum chamber and vacuum acquisition devices. The vacuum chamber includes components for unwinding the rolls, heating, and rewinding. The schematic diagram of roll-to-roll vacuum drying equipment is shown in the diagram. However, roll-to-roll drying equipment is not yet a mature drying technology. There are very few existing devices on the market, and industrial-scale successful applications of such equipment are almost non-existent.
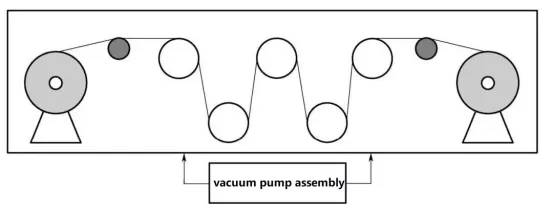
The process flow of roll-to-roll drying is relatively simple: the electrode roll is placed on the unwinding shaft, and the electrode film passes through various shafts and heating rollers before winding onto the rewinding shaft. The unwinding and rewinding shafts rotate simultaneously, and the electrode roll is heated and dried to remove moisture as it passes through the heating rollers. The entire process takes place within a vacuum chamber. After drying is complete, the electrode roll is unloaded from the rewinding shaft.
The roll-to-roll processing scheme is mature, but there are still many challenges to be addressed in roll-to-roll drying equipment. Firstly, the unwinding and rewinding components have mature solutions in the market. However, to improve drying efficiency, higher unwinding and rewinding speeds are desirable. For such lightweight and thin electrode rolls, increasing the speed can lead to roll breakage. Additionally, as the unwinding and rewinding components are located within the vacuum chamber, measures need to be taken to prevent contamination from dust during the transmission process. Lastly, achieving rapid heating, temperature uniformity control, and detection during the high-speed transmission of the electrode roll pose difficulties. Furthermore, the equipment’s vacuum level and temperature requirements should be similar to or on par with those of previous equipment types.
5.5 Logistics Storage Vacuum Drying Equipment
Logistics storage vacuum drying equipment utilizes existing logistics systems to significantly improve the efficiency and flexibility of the drying process. This type of equipment deviates from the traditional large drying chamber and instead uses pallets with covers as drying spaces, with storage racks for holding the covered battery trays. Each storage position is equipped with a vacuum docking system and a heating docking system for heating the batteries and creating a vacuum within the trays. The logistics storage vacuum drying equipment is still in the developmental stage and has not been implemented in practical applications. The schematic diagram of its structure is shown in the diagram.
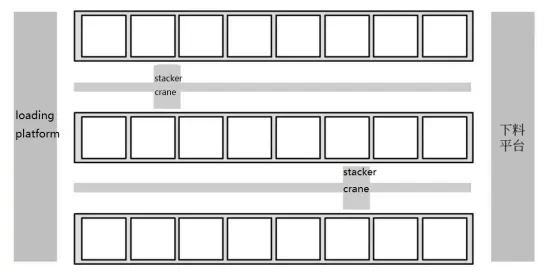
At the loading platform, a robot arranges the batteries into trays and covers them. The stacker crane then places the assembled trays with batteries onto the corresponding storage positions on the storage racks. The vacuum system and heating system on the racks are docked with the trays to heat and dry the batteries. Once the drying process is complete, the stacker crane places the batteries and trays onto the unloading platform, where the batteries are unpacked and proceed to the next process.
Logistics storage vacuum drying equipment relies on the concept of logistics and storage, thus requiring a high level of logistics scheduling software. Additionally, the stacker crane used for handling the batteries and trays must meet specific requirements to ensure the equipment’s efficiency. By utilizing the tray space as the drying chamber, the equipment reduces the chamber’s size while significantly improving flexibility. However, this also means that each storage position must have heating and vacuum docking devices, which increases the equipment and maintenance costs. This equipment shares many similarities with intermittent vacuum drying equipment. The main difference lies in the smaller and more mobile chamber of this equipment, making it more flexible and suitable for customized production.
06. Evaluation of Lithium Battery Vacuum Drying Equipment Performance
6.1 Vacuum Performance Evaluation
The vacuum performance of a vacuum drying equipment is primarily evaluated based on parameters such as the pumping time, ultimate vacuum level, and vacuum sealing capability of the chamber. The evaluation of vacuum performance is typically conducted under unloaded conditions. The testing setup includes a vacuum pump, vacuum valves, vacuum gauge, pipes, as well as a vacuum meter and timer.
The ultimate vacuum level refers to the lowest pressure that the chamber can achieve. A lower ultimate vacuum level is favorable for moisture evaporation, but it also imposes higher requirements on the equipment. Therefore, a balance needs to be struck between equipment cost and ultimate vacuum level. Considering that the drying process for most batteries is typically carried out at pressures of several tens to a few hundred pascals (Pa), with the working pressure falling between 20 to 1000 Pa, an ultimate vacuum level of around 10 Pa is sufficient.
Under continuous pumping conditions, the pumping time of the equipment is defined as the time required to reach the ultimate pressure value after the chamber has been opened for 15 minutes and then evacuated again. Generally, the pumping time should be around 5 to 10 minutes, and if the requirement cannot be met, consideration should be given to replacing the vacuum pump to meet the requirements.
The vacuum chamber is connected to the suction inlet of the vacuum pump through vacuum piping to ensure the entire vacuum system is sealed. The vacuum pump is turned on, and when the vacuum level reaches the ultimate pressure, the pump is turned off, and the pressure is maintained for 24 hours. The time and pressure curve are recorded, and the linear section of the pressure versus time curve is identified. The slope of this linear section represents the value of vacuum sealing capability (i.e., the increase in vacuum level per hour). The vacuum sealing capability should generally be less than 5 Pa/h. If the vacuum sealing capability does not meet the requirements, a helium leak detector should be used to test the chamber and improve its sealing performance.
6.2 Evaluation of Temperature Performance
The temperature performance of lithium battery vacuum drying equipment is primarily assessed based on parameters such as heating time, temperature fluctuation, temperature stability, and temperature uniformity. The evaluation of temperature performance is also typically conducted under unloaded conditions. The testing setup for temperature performance includes temperature sensors such as thermoresistors and thermocouples, as well as a temperature recorder. For forced air heating, the temperature measurement point is typically the center of the chamber, while for contact heating, it is the center of the heating device.
Heating time refers to the time it takes for the equipment to reach the process temperature for battery drying when the heating device is operated at maximum power from room temperature. For forced air heating, the heating time should not exceed 90 minutes, while for contact heating, it should not exceed 10 minutes. Temperature fluctuation is defined as half of the difference between the highest and lowest temperatures at the measurement point within a specified 30-minute period after the temperature stabilizes during the drying process. The temperature fluctuation of the battery drying equipment should not exceed ±1°C.
Temperature stability is determined by the maximum difference between the average temperature of multiple temperature measurements taken at different time intervals within 24 hours after the temperature stabilizes during the drying process and the average temperature during the initial period. The temperature stability of the battery drying equipment should not exceed 2°C.
Temperature uniformity is defined as half of the maximum difference between the average temperatures at any two points within the chamber (for forced air heating) or on the heating device (for contact heating) during a specified time interval after the temperature stabilizes during the drying process. For forced air heating, temperature measurement points should include multiple points at the center and edges of the chamber, while for contact heating, points should include the center and edges of the heating device. The temperature uniformity of the battery drying equipment should not exceed ±3°C. A typical temperature uniformity test curve is shown in the figure.
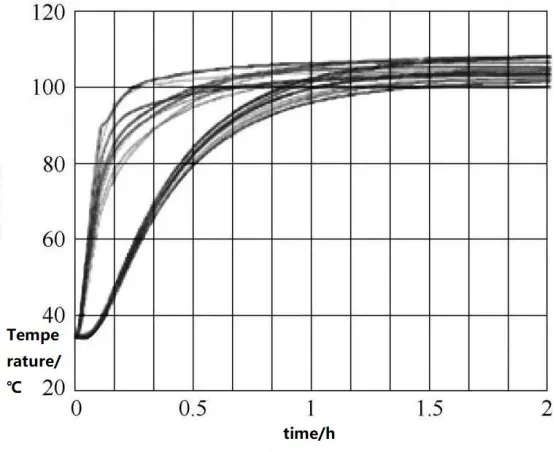
6.3 Moisture assessment after drying
Niu Junting et al. conducted a systematic study on the relationship between residual moisture in battery pole pieces and battery performance. Batteries with a positive electrode sheet moisture content between 0.04% and 0.05% have good cycle performance. After 200 cycles of current charge and discharge cycles, the battery discharge capacity still remains at 92.9% of the initial capacity. As the cycle proceeds, the capacity of batteries with a moisture content of more than 0.06% in the positive electrode sheet rapidly decreases and the performance deteriorates. Batteries with a moisture content in the battery pole piece in the range of 0.03% to 0.06% have a high and close discharge specific capacity. As the discharge rate increases, the moisture content of the battery pole piece exceeds 0.06%, and the capacity attenuation rate increases. Since excessive moisture has a great negative impact on battery performance, the current moisture content of the battery after drying is generally required to be below 500mg/kg, and it is best to reduce it to 200~300mg/kg.
Since the moisture content of the battery is low after drying, generally only a few hundred milligrams per kilogram, it cannot be measured by a simple method. The Karl Fischer-Coulomb method is generally used to test trace moisture, and its principle is an electrochemical method. The reaction principle is that water participates in the redox reaction of iodine and sulfur dioxide.
It can be seen from the above reaction that 1 mol of iodine oxidizes 1 mol of sulfur dioxide, which requires 1 mol of water. Therefore, the power of electrolyzing iodine is equivalent to the power of electrolyzing water. The electrolysis of 1 mol of iodine requires 2×96493C of power, and the electrolysis of 1 mmol of water requires 96493 mC of power. The measured moisture mass is calculated according to the following formula:
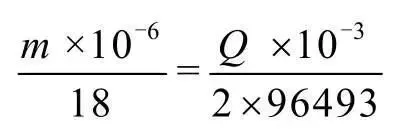
In the formula, m is the measured mass of water, μg; Q electrolyte, mC; 18 water electrolyte.
The measured moisture mass also includes the moisture in the test system. Therefore, the moisture in the moisture should be measured based on the total moisture mass loss of the empty bottle (blank value), and the influence of the moisture value (drift value) should be considered. The moisture in the moisture The content is calculated as follows:
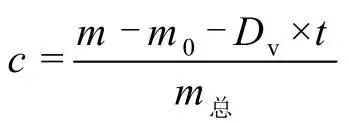
In the formula, c sample moisture content, μg/g; m0 empty bottle moisture mass, μg; Dv drift value, μg/min; t extraction time, min; m total – total sample mass, g.
The structural diagram of the Karl Fischer-Coulomb moisture tester is shown in Figure. It mainly includes a Karl Fischer electrolytic cell and a sample heating unit. The pole piece sample is placed in a sealed sample bottle, and then the sample bottle is heated at a certain temperature. The water in the electrolytic cell evaporates, and then dry gas is used to send the water vapor into the electrolytic cell to participate in the reaction, and then the electricity generated during the electrolysis process is measured to titrate the water content.
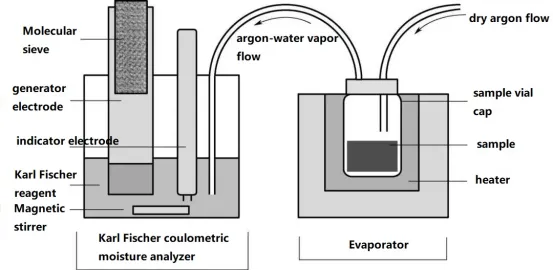
When performing moisture testing on battery samples using a Karl Fischer coulometric moisture analyzer after drying, the following points should be taken into consideration:
a. The sample vial must be dried before sampling, typically at 120-160°C for 3-6 hours. After removal, it should be immediately sealed with a cap. The blank moisture content of the sample vial should be less than 10 μg, and the lower the better.
b. Sampling should be conducted in an environment with a dew point. It is generally recommended to have a dew point lower than -40°C. Leave the empty sample vial uncapped for 1-2 hours as a blank test.
c. The electrode plate can be cut into small pieces around 0.5 cm or along the height of the sample vial.
d. The sample size for analysis should generally not be less than 0.5 g.
e. It is recommended to use a precision electronic balance with a resolution of 0.1 mg for weighing.
f. Before conducting formal sample testing, ensure that the current drift is less than 20 μg/min and stable without significant upward or downward trends.
g. After completing a sample, remove the vial with the sample from the Karl Fischer oven, insert it back into the drift bottle, and let the instrument stabilize before proceeding to the next sample.
h. The recommended temperature for the Karl Fischer oven is 120-180°C. Excessive temperature can cause volatilization or side reactions of some materials in the battery, leading to inaccurate test results. When unsure about the testing temperature, the gradient heating method can be used with the Karl Fischer moisture analyzer to analyze the moisture content of lithium-ion battery materials and electrode plates.
07 Development direction of vacuum drying equipment
7.1 Continuous Improvement of Drying Efficiency
Shortening drying time and improving drying efficiency has always been a goal of drying equipment. Enhancing the efficiency of vacuum drying helps to reduce product costs and improve economic benefits. Currently, drying equipment is becoming increasingly automated, which also contributes to improved drying efficiency. In the future, it is necessary to develop new heating methods to enhance heating efficiency, develop logistics systems tailored to drying equipment to improve loading and unloading efficiency, create low-energy-consumption drying equipment, conduct research on battery drying mechanisms to optimize drying processes, utilize software and monitoring techniques to enhance process control, and improve the operational efficiency of the equipment.
7.2 Modular and Standardized Design of Equipment
Currently, battery drying equipment is custom-designed due to the varying specifications of batteries in the market. This lack of standardization limits the flexibility of battery drying equipment and hinders its upgradability. In the future, there should be corresponding standards for battery specifications, and the design of drying equipment should adhere to these standards. This includes aspects such as chamber size, selection of vacuum pumps, requirements for heating plates, and installation positions of vacuum gauges and valves. Additionally, due to the demand for batch production of batteries, drying equipment is becoming larger in size, and on-site installation and debugging often require significant manpower, resources, and time. When designing drying equipment, modularization should be considered, with each module having independent functionality to save on-site installation and debugging time.
7.3 Manufacturing Execution System (MES) for Production Guidance
With the increasing automation in battery production, the software systems of drying equipment are also being upgraded. Currently, the software of drying equipment can display energy consumption data, record product information, and process data, which are basic requirements. However, the current MES primarily focuses on data collection and storage for traceability of drying data. In the future, MES should go beyond these functions and utilize techniques such as big data to provide guidance and improvement in battery drying processes, assisting in equipment maintenance and enhancing drying efficiency.
7.4 Online Moisture Detection
As mentioned earlier, moisture testing after battery drying requires the destruction of batteries to assess their moisture content and determine their acceptability. Currently, there is no effective real-time moisture detection method available. In the future, research should be conducted to develop new battery testing methods that can monitor moisture content during the drying process in real-time, without the need for destructive testing or post-drying moisture analysis. If the moisture content is found to be non-compliant during the drying process, immediate adjustments can be made to the drying process until the moisture content meets the desired standards. Developing new moisture detection methods requires in-depth research on the moisture evaporation mechanism of batteries and the relevant influencing factors. Therefore, studying the battery drying process is of significant importance for the advancement of drying equipment.