水分含有量はバッテリーの性能に大きな影響を与えるため、製造工程では厳密に管理する必要があります。バッテリーに水が存在すると、電解液が劣化したり、電解液と反応して有害ガスが発生したりして、バッテリー内の圧力が上昇したり変形したりする可能性があります。バッテリーの水分含有量が過剰になると、内部抵抗が大きくなり、自己放電が大きくなり、容量が小さくなり、サイクリング性能が低下し、さらには漏れが発生する可能性もあり、バッテリーの性能が大幅に低下します。したがって、リチウム電池の製造には乾燥プロセスが不可欠です。
01乾燥入門
乾燥とは、湿った材料にエネルギーを供給して気化させ、含まれている水分を取り除き、乾燥材料を生成する化学単位の操作です。現在、業界には多数の乾燥装置オプションがあり、それらはさまざまな方法で分類できます。運転モードに基づいて、乾燥装置は連続乾燥装置とバッチ(断続的)乾燥装置に分類できます。使用圧力により、大気乾燥装置と真空乾燥装置に分類できます。さらに、熱伝達法に基づいて、乾燥装置は、伝導乾燥装置、対流乾燥装置、放射線乾燥装置、誘電体乾燥装置などにさらに分類できます。
電池の水分含有量は、主に、正極シート、負極シート、セパレーター、電解質、その他の金属部品など、電池の原材料に存在する水分と、工場環境の水分に由来します。環境水分に対処するために、乾燥機が乾燥空気を生成し、乾燥室に連続的に供給される乾燥室を設置し、湿った空気を置換して環境水分を排除することができます。バッテリーの内部水分については、高い乾燥基準が必要であり、通常は(100-300)×10-6の間の水分含有量が要求されるため、水を除去するために真空乾燥装置が一般的に使用されます。乾燥後、バッテリーはベーキング要件を満たしていることを確認するためにテストされます。電池の製造では、電池電極粉末、正極巻線と負極巻線、電解液注入前のセル組み立てなど、複数のプロセスステップで真空乾燥が必要です。したがって、真空乾燥装置はバッテリー製造にとって非常に重要です。
02真空乾燥の原理
真空乾燥の原理は、水の沸点が異なる圧力環境下で変化するという事実に基づいています。圧力と沸点の関係を図に示します。
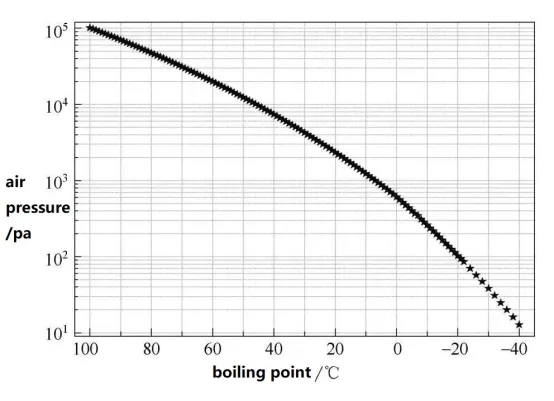
図からわかるように、常圧、つまり1気圧では水の沸点は100°Cですが、気圧が下がると水の沸点は下がり続けます。約100Paの真空環境では、水の沸点は約-20°Cまで下がっています。 これは、真空環境が乾燥プロセスを促進できるという基本原則です。
したがって、真空乾燥は、1つの標準大気圧未満の環境条件下で材料に含まれる水分を除去するプロセスです。真空乾燥の基本的な動力学原理は、熱と物質移動の理論です。真空乾燥の過程で、真空システムは乾燥する材料を排気しながら連続的に加熱するため、材料内部の水分は圧力差または濃度差を通じて表面に拡散します。水分子は、分子間の相互引力を克服するために、材料の表面で十分な運動エネルギーを得ます。真空チャンバーの低圧空間に飛び込み、真空ポンプに吸い込まれます。
真空乾燥プロセス中の水分損失率と、単位時間あたりの単位乾燥面積あたりの乾燥材料から気化および排出される水分の質量が乾燥速度、つまり
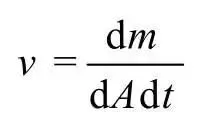
式では、v乾燥速度、g /(m2・h);m排出された水分量、g;乾燥エリア、m2;t乾燥時間、h。
バッテリーの乾燥では、一般的に水分の質よりも水分含有量により多くの注意が払われます。また、電池内の水分含有量が非常に少なく、蒸発した水分の質を測定するのが困難です。水分含有量の変化が単位面積あたりの水分量の変化を置き換えるために使用されることを考慮すると、上記の式は次のように変換できます。
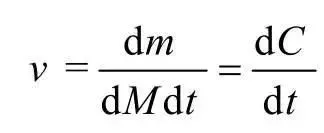
式では、v乾燥速度、mg /(kg・h);m排出水分量、mg;M総材料質量、kg;C含水率、mg / kg;t乾燥時間、h。
典型的な真空乾燥速度曲線を図に示します。水損失プロセスは、加速乾燥段階、定速乾燥段階、および減速乾燥段階の3つの段階に分けられます。セクションABは加速乾燥段階です。このとき、材料中の水分含有量は一定です。真空化と加熱により、材料は許容温度範囲内の対応する圧力で気化温度まで加熱され、大量に気化し、乾燥速度は増加し続けます。熱と物質移動特性の制限により、乾燥速度は最大値に達し、定速乾燥段階であるBCセクションに入ります。このとき、材料の温度は変化せず、加熱熱は気化の潜熱とさまざまな熱損失として使用され、気化蒸気は連続的に排出されます。蒸発面と空間の圧力差が維持され、乾燥を継続できます。材料の含水率が一定のレベルまで減少すると、蒸発した水分が減少し、蒸発面と空間との間の圧力差が減少します。減速乾燥段階であるCDセクションに入り、乾燥速度は徐々に低下し、ゼロに近づきます。
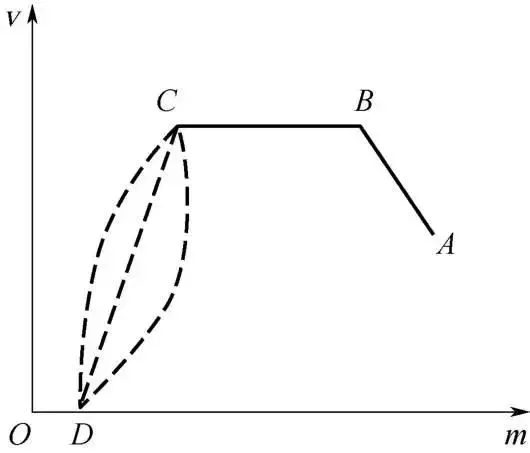
真空乾燥プロセス中の乾燥速度に影響を与える多くの要因があります。まず、乾燥させる材料の形状、サイズ、積み重ね方法、および材料自体の含水率、密度、その他の物理的特性が乾燥速度に影響します。第二に、乾燥装置の作動真空度は乾燥速度に影響を与えます。真空度が高いと、より低い温度で水分を気化させることができます。ただし、真空度が高いと熱伝導を助長せず、加熱効果が低下します。最後に、乾燥装置の構造形態、加熱方法、乾燥プロセスはすべて乾燥速度に影響します。そのため、乾燥時間や乾燥速度を計算することは非常に困難です。
現在、バッテリー乾燥中の水分変化を測定することは困難であるため、この分野での実験的研究は多くありません。しかし、電池の水分蒸発メカニズムを研究することは、電池の乾燥プロセスにとって重要な指針となります。Guan Yumingらは、計算流体力学(CFD)シミュレーションソフトウェアを使用して、バッテリーコア内の水の蒸発速度を解析しました。彼らは、フィックの法則によって計算されたバッテリーコア水分拡散関数コンパイル言語を読み込んでシミュレーション分析を完了し、バッテリーコア表面の水の蒸発速度が最速のベーキング時間は約10分であるのに対し、バッテリーコアの下部にある水の蒸発速度は最初は非常に低いことがわかりました。 また、図に示すように、最速の時間は約50分です。
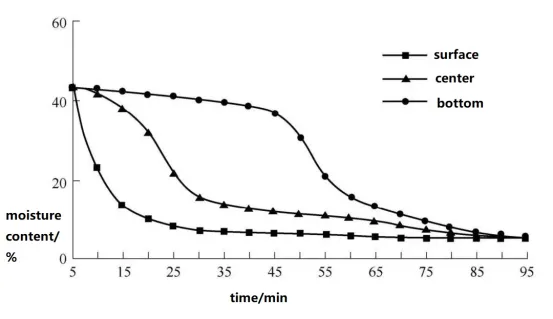
03 バッテリー真空乾燥プロセス
リチウム電池の製造工程では、スラリーの混合、コーティング、圧延、スリット、巻き取り/ラミネート、溶接、シーリング、液体注入、形成、体積分割、組み立てなど、いくつかの基本的なステップが必要です。最終製品の含水率を制御するには、生産プロセスのさまざまな主要ノードに水分制御ポイントを設定する必要があります。一般的な設計には、カソード粉末材料の水分制御、ポールロール/ポールシートの水分制御、そして最も重要なのは、バッテリー注入前の水分制御が含まれます。
リチウムイオン電池の製造工程では、通常、正極と負極の粉末材料をスラリーする前に水分を制御し、粉末製造の最終段階で同時に乾燥させる必要があります。スラリー混合プロセス中、負極は一般に水性スラリーであり、正極は一般に油性スラリーです。スラリーをコーティングした後、予備乾燥を行います。このステップの主な目的は、スラリー中の溶媒を除去し、微多孔質構造を持つバッテリーポールピースを形成することです。この乾燥ステップの後、ポールピースにはまだ多くの水分が残っています。残留水分を除去するための2つの主要な乾燥プロセスがあります。バッテリーを巻くかラミネートする前に、バッテリーのポールピースを真空乾燥します。一般的な乾燥温度は120~150°Cです。 バッテリーポールの部分は、多くの場合、ロールまたはパイルで乾燥されます。b.バッテリーを液体で満たす前に、組み立てたバッテリーを真空乾燥させてください。このとき、バッテリーにはセパレーターなどの部品が含まれているため、乾燥温度は一般的に60〜90°Cです。
乾燥温度の設定は恣意的なものではなく、リチウム電池が液体で満たされる前の固体材料中の水分の存在形態に関連しています。固体材料分子と水分子との間の力の性質と大きさに応じて、図に示すように、水には主に3つの形態があります。1つ目は水の付着で、これは単に材料の表面に機械的に付着します。2つ目は水の吸着であり、水は物理的または化学的吸着の形で固体と結合されます。3つ目は結合水であり、水は結晶水和物の形で材料と結合されます。組み合わせる。付着した水分の場合、常温常圧で自然に揮発する可能性があります。吸着した水分の場合、常圧下で約105°Cで蒸発する可能性があります。一方、複合水分の蒸発は通常、常圧で150°C以上に達する必要があります。真空環境では、水分除去温度を大幅に下げることができます。温度が高いほど水分除去効果は高くなりますが、リチウム電池のセパレーターのほとんどは高密度ポリエチレンや高密度ポリプロピレンなどのポリマー材料でできており、これらのポリマー材料は高温での使用には適していないため、温度が高すぎないようにする必要があります。高温で劣化し、深刻な安全上の問題を引き起こします。したがって、リチウム電池の乾燥温度を合理的に設定することは非常に重要な問題であり、特定の材料システムに応じて適切に調整する必要があります。
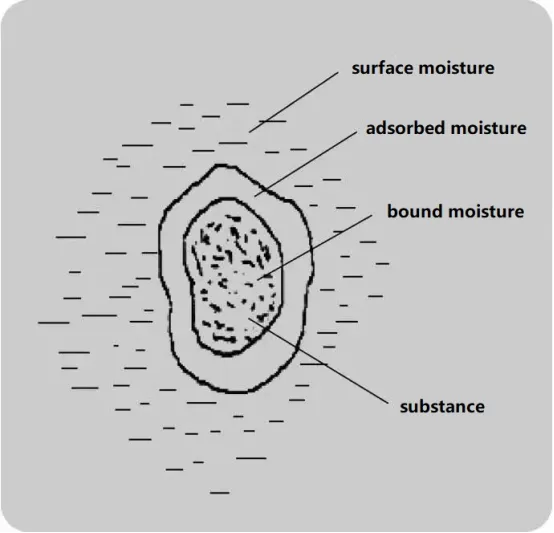
バッテリーの乾燥プロセスには、通常、予熱、真空乾燥、冷却の3つの段階が含まれます。真空部での熱伝達が遅いため、通常は常圧以上の圧力で予熱され、バッテリーは特定の温度に達した後に排気されます。乾燥後は水分を取り除き、室温まで冷やして、電池材料の酸化を防ぎます。乾燥したバッテリーは、大気環境との接触を避けるように努める必要があります。乾燥プロセス中の温度、真空度、予熱時間、真空メンテナンス時間などのプロセスパラメータは、乾燥結果に重要な影響を与えます。適切なプロセスパラメータを選択することで、乾燥効率の向上につながります。
04真空乾燥装置の基本構成と分類
現在、リチウム電池業界で使用されている真空乾燥装置は、基本的な全自動運転を実現しています。この装置の基本コンポーネントには、発熱体、真空システム、乾燥チャンバー、ローディングおよびアンローディングプラットフォーム、および中央制御システムが含まれます。
加熱部品は、乾燥装置に熱を供給するために使用されます。加熱コンポーネントは、さまざまな加熱源に応じて、電気加熱、電磁誘導加熱、マイクロ波加熱などに分けることができます。現在、バッテリー乾燥装置の最も一般的に使用されている方法は電気加熱です。電気加熱には、熱風循環加熱と接触加熱も含まれます。熱風循環加熱は、加熱装置とファンの組み合わせであり、乾燥チャンバー内の任意の位置を乾燥温度に到達させることができます。接触加熱は、加熱装置を使用してバッテリーに直接接触してバッテリーに熱を伝導するため、エネルギー利用効率が向上し、エネルギー消費を効果的に節約できます。加熱部品の主な設計要件は、加熱速度、温度安定性、温度均一性です。したがって、温度を制御および監視することは非常に重要です。加熱部品には、対応する温度制御部品と検出部品を装備する必要があります。
ポンプの有効ポンプ速度は次のように計算されます。
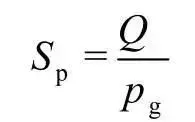
式では、Spポンプの有効ポンプ速度、m3 / s;PG真空チャンバーに必要な使用圧力、Pa;Q真空チャンバーの総ガス量、Pa・m3/s。
Q=1.3(Q1+Q2+Q3)
式では、Q1——真空プロセス中に発生するガスの量、Pa・m3/s;Q2真空チャンバーのガス放出量、Pa・m3/s;Q3真空チャンバーの総空気漏れ量Pa・m3/s。
ポンプの公称ポンプ速度は次のように計算されます。
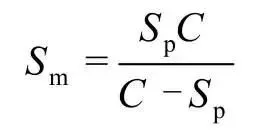
式では、Smはポンプの公称ポンプ速度、m3 / sです。Cは、真空チャンバー出口とユニット入口の間のパイプ接続、m3 / sです。
荷役台は、電池の組み立て(解体)や積み重ね(デスタッキング)、電池トレイなどのスキャン、NG状況への対応など、電池の積み下ろしに利用されます。自動化要件の改善に伴い、バッテリーのロードとアンロードは基本的に自動化され、手動の介入が少なくなりました。ローディングステーションでは、バーコードリーダーがバッテリーとパレットをスキャンします。NGコードをスキャンするバッテリーは、NGプラットフォームに置かれます。バッテリーロボットは、スキャンに成功したバッテリーをパレットにロードします。パレットがいっぱいになると、パレットロボットはパレットを上に積み重ねます。材料テーブルでは、ローディングテーブルが充填され、乾燥キャビティに入ります。乾燥が完了した後、バッテリーは乾燥キャビティから送り出され、パレットロボットはパレットを層ごとにデスタッカーします。その後、バッテリーロボットはパレットからバッテリーを取り出し、次のパレットに入ります。過程。
制御システムは、真空システム、発熱体、および乾燥システムのモーションコンポーネントの制御を担当します。しかし、ビッグデータとモノのインターネットの発展により、これらの機能は現在の生産要件を満たすのに十分ではなくなりました。乾燥装置にとって、ソフトウェアシステムの重要性はますます高まっています。ハードウェアの制御に加えて、ソフトウェアには次の機能が必要です。
1.機器の故障を診断し、現在および過去の故障を表示し、トラブルシューティング方法を提供する能力。
2.すべてのセンサーとアクチュエータの入力信号と出力信号、およびリアルタイムステータスを表示する機能。
3.24時間以内にリアルタイムの機器ステータスと機器ステータスとアラーム情報に関する統計を取得する機能。
4.材料の種類、バッチ、モデル、仕様などの情報を収集し、材料追跡システムを確立し、材料情報を追跡および追跡する能力。
5.生産プロセスを追跡および管理し、温度、真空レベルなど、材料乾燥中の関連ステーションのプロセスパラメータを収集する能力。
6.生産実行、機器の使用、プロセス制御などを含む履歴データを照会する機能
現在、バッテリー真空乾燥装置には統一規格はなく、さまざまな仕様や形態があります。チャンバーの形状により、円形チャンバー乾燥装置と角型チャンバー乾燥装置に分けることができます。加熱方法により、熱風循環加熱装置、接触加熱乾燥装置、誘導加熱装置などに分けることができます。バッテリー製造のさまざまな段階に基づいて、正極と負極の粉末乾燥装置、正と負の電極巻線乾燥装置、バッテリーセル乾燥装置などに分けることができます。乾燥装置の排出方法により、バッチ乾燥装置と連続乾燥装置に分けることができます。
05代表的な電池真空乾燥装置
5.1間欠真空乾燥装置
間欠真空乾燥装置は、従来の単一乾燥炉を複数組み合わせ、自動ローディングおよびアンローディングロボットと中央ディスパッチロボットを装備して大量生産を実現します。その構造図を図に示します。この乾燥装置は比較的高い柔軟性を持っています。各機器セットに装備されている乾燥オーブンの数と、各乾燥オーブンのキャビティの数は、特定のニーズに応じて構成できます。
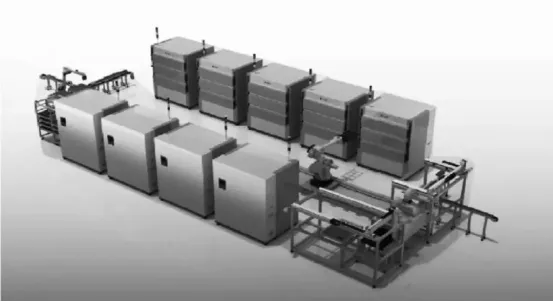
乾燥装置の荷台は、前工程の材料フローラインとドッキングされています。バッテリーセルは、前工程の材料フローラインからローディングプラットフォームに移送されます。その後、ローディングプラットフォームに位置決めして組み立てた後、対応する乾燥オーブンに移して乾燥させます。乾燥プロセスの後、セルはアンロードプラットフォームに移動され、分解と冷却が行われてから、次のプロセスの材料フローラインに入ります。乾燥オーブンの加熱方法は、熱風循環または接触加熱のいずれかです。プロセス全体は、中央制御システムによって制御されます。
単一乾燥炉は、断続的な真空乾燥装置の基礎およびコアユニットです。その構造には通常、真空乾燥チャンバー、全自動密閉ドア、ラック、外側のシーリングプレート、電気ボックス、真空パイプライン、窒素パイプライン、制御システムなどの基本ユニットが含まれます。空気駆動の暖房を使用する場合は、熱風循環パイプも含まれます。道路と暖房システム。
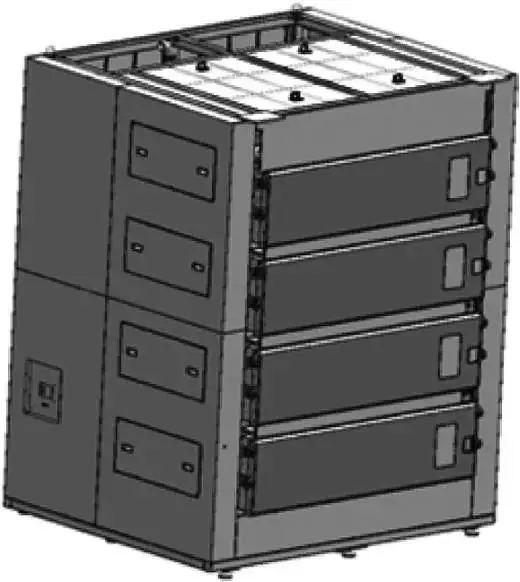
5.2連続真空乾燥装置
連続真空乾燥装置は、乾燥プロセスを予熱-真空乾燥-冷却などの複数のプロセスに分割し、異なるキャビティまたはワークステーションを使用して予熱-真空乾燥-冷却などのプロセスを実行します。これらのキャビティまたはワークステーションは、位置が密閉されたドアで接続されているため、乾燥が連続的なプロセスになります。さらに、自動ローディングおよびアンローディングプラットフォームとトランスミッションシステムを装備し、材料の連続乾燥を完了します。その構造図を図に示します。この乾燥装置は、エネルギー消費を大幅に節約でき、各装置セットのステーションの数は、特定のプロセス要件と生産能力に応じて構成できます。
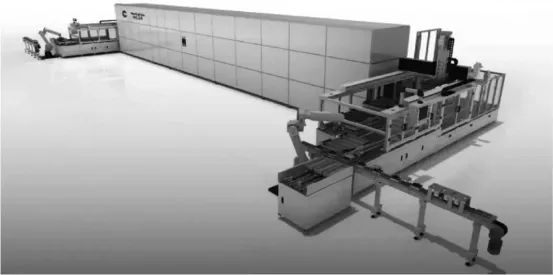
連続真空乾燥装置のプロセスフロー:バッテリーコアは、前のプロセスのロジスティクスラインからローディングプラットフォームに入ります。それらはローディングプラットフォームに配置され、メッキされ、積み重ねられた後、予熱のために予熱チャンバーに送られます。予熱後、乾燥トランジションキャビンを通過し、真空乾燥のために真空乾燥キャビンに入ります。乾燥後、冷却キャビンに入って冷却します。冷却後、荷降ろしプラットフォームに行き、デスタッキングとトレイの取り外しを行います。その後、セルは次のプロセスの物流ラインに入り、パレットは荷台に戻ります。プラットホーム。予熱キャビンの暖房方法は、熱風循環暖房または接触加熱であり得る。真空乾燥キャビンの暖房モードは、接触加熱または熱風循環加熱によって補完された放射加熱にすることができます。プロセス全体は、中央制御システムによって制御されます。
連続真空乾燥装置またはトンネル装置は、通常、予熱、真空乾燥、冷却といういくつかの基本的な段階に分けられます。典型的な予熱部の構造を図に示します。
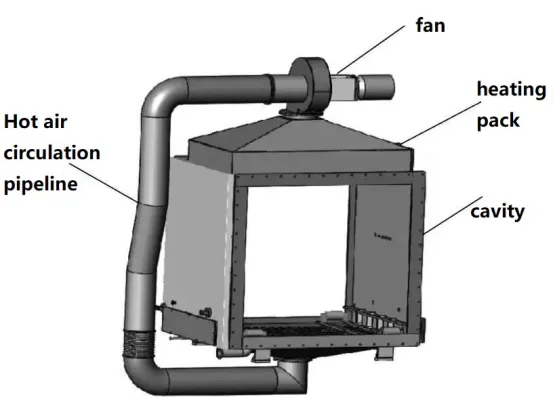
写真では、ファンが内部ガスを駆動して下向きに流れ、加熱パックによって加熱され、キャビティに入ってキャビティ内で乾燥する材料を加熱します。次に、底部の空気出口から循環パイプに入り、ファンに戻ってガス循環チャネルを形成します。予熱セクションの主な機能は、乾燥した材料を加熱して、真空乾燥に必要なプロセス温度にすばやく到達することです。したがって、予熱セクションの加熱速度と温度均一性がその主要なプロセス指標です。
乾燥した材料が設定温度に達した後、搬送装置を介して真空乾燥セクションに移されます。典型的な真空乾燥部の構造を図に示します。
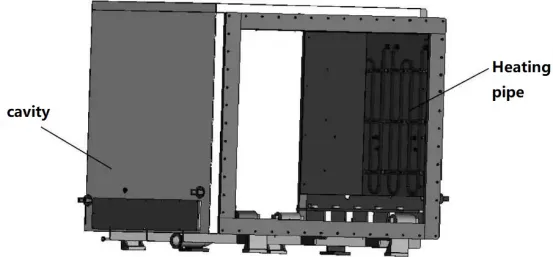
真空乾燥の真空度は通常約10~100Paです。真空環境にあり、媒体としてガスがないため、対流熱伝達は使用できません。真空セクションには通常、放射を通じて乾燥した材料にエネルギーを補充するために、キャビティの周りに配置された加熱システムがあります。
ポールピースの酸化を防ぐために、真空乾燥された材料は、装置を出て乾燥室に入る前に冷却する必要があります。したがって、連続真空乾燥装置の最後の機能セクションは冷却セクションです。典型的な冷却部の構造は、図の通りです。
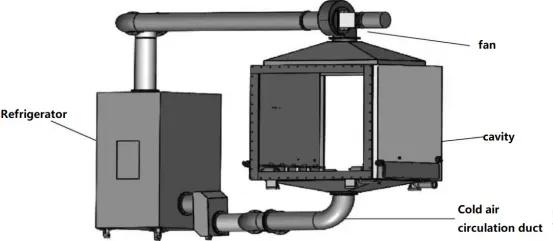
冷却セクションには通常、冷却不活性ガスを供給するための外部冷蔵庫が装備されています。ガスはファンを介してキャビティに入り、強制対流して材料を冷却および乾燥させ、冷気循環パイプを通って冷蔵庫に戻り、冷気循環チャネルを形成します。冷却部は、乾燥材料の温度を短時間で室温に近づけることができます。異なる冷凍システムとファンの流量を選択することで、異なる冷却曲線を達成することができます。
5.3加熱方法の異なる真空乾燥装置
温度は真空乾燥のコアパラメータであり、温度上昇プロセスは乾燥プロセスの重要な段階です。現在、機器には、空気駆動加熱と接触加熱の2つの一般的に使用されている加熱方法があります。風力駆動加熱は、空気やその他の不活性ガス媒体を加熱し、ファンやその他のデバイスを使用してキャビティ内を強制的に流すことで、強制対流によって熱を伝達する加熱方法です。これは、業界で最も一般的に使用されている加熱方法でもあります。精密な温度制御により、空気駆動加熱はキャビティ内の非常に均一な温度分布を達成し、それによって均一なバッテリー温度を得ることができます。
接触加熱は、近年徐々にその用途が拡大している別の真空乾燥加熱方法です。その基本原理は、バッテリーを加熱プレート上または加熱プレートの中央に配置し、熱伝導を使用してバッテリーを加熱することです。図に示すように、片面(底面)接点、両面(両面)接点、3面(底面プラス両面)接点の3つの接触加熱方法があります。
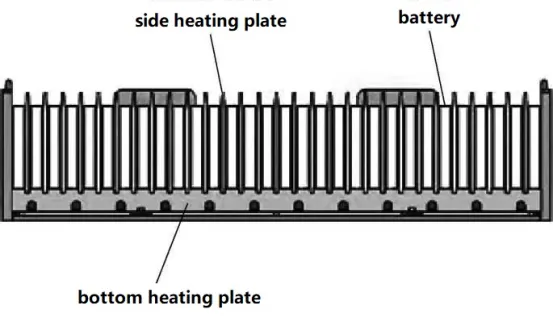
写真からわかるように、接触加熱されたバッテリートレイは通常通電されています。積み下ろしの際には、バッテリートレイを取り出して積み降ろし位置に置いて、バッテリーを出し入れします。真空乾燥時には、トレーを真空チャンバー中央の加熱位置まで上昇させ、弾性電気接点を介して電源供給と温度測定を行い、加熱プレートをリアルタイムに閉ループ制御します。バッテリーはホットタイドによって予熱され、真空乾燥段階では、ホットタイドガス媒体はバッテリー乾燥のためのエネルギーを連続的に補充できます。
空気駆動加熱と接触加熱の使用には、それぞれ独自の長所と短所があります。空気式加熱装置は、構造がシンプルで信頼性が高く、温度均一性に優れていますが、加熱時間が短いのが特徴です。接触加熱装置は、熱の力が温度勾配から来るため、温度均一性が悪く、温度平衡に達するまでに時間がかかるため、軽量です。同時に、接触加熱バッテリートレイとキャビティとの間の電気的接点は、通常、真空環境と接触している必要があるため、真空生産能力の問題を引き起こしやすく、生産への影響を増大させる可能性があります。コストの観点から、空気式暖房装置は、構造と温度制御の利点により、低コストです。一方、同じ生産能力を持つ接触式機器のコストは約30%から50%高くなります。
5.4 ロールツーロール真空乾燥装置
ロール・ツー・ロール真空乾燥装置は、バッテリー電極ロールの乾燥に特化して設計されています。電極ロールのサイズが大きいため、乾燥時間は一般に長くなり、ロールの内部と表面の間で水分含有量にばらつきが生じる可能性があります。乾燥効率を向上させ、一貫した水分含有量を達成するために、ロールツーロール乾燥装置が開発されました。ロール・ツー・ロール加工の概念は、コーティングなどのプロセスに端を発し、薄膜材料にとってより効率的な方法です。
ロールツーロール真空乾燥装置は、主に真空チャンバーと真空取得装置で構成されています。真空チャンバーには、ロールの巻き戻し、加熱、および巻き戻しのためのコンポーネントが含まれています。ロールツーロール真空乾燥装置の概略図を図に示します。ただし、ロールツーロール乾燥装置はまだ成熟した乾燥技術ではありません。市場には既存のデバイスはほとんどなく、そのような機器の工業規模の成功したアプリケーションはほとんど存在しません。
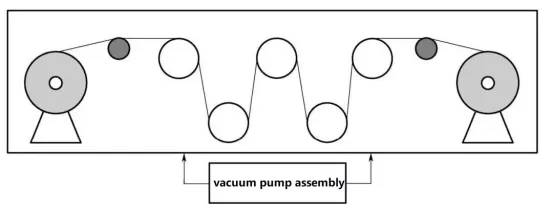
ロールツーロール乾燥のプロセスフローは比較的単純です:電極ロールは巻き戻しシャフトに配置され、電極フィルムはさまざまなシャフトと加熱ローラーを通過してから巻き戻しシャフトに巻き取られます。巻出軸と巻取軸が同時に回転し、電極ロールを加熱・乾燥させて水分を逃がし、加熱ローラーを通過します。すべてのプロセスは真空チャンバー内で行われます。乾燥終了後、電極ロールを巻き戻し軸から降ろします。
ロール・ツー・ロール処理方式は成熟していますが、ロール・ツー・ロール乾燥装置にはまだ多くの課題があります。まず、巻き戻しおよび巻き戻しコンポーネントは、市場で成熟したソリューションを持っています。ただし、乾燥効率を向上させるためには、巻き戻しおよび巻き戻し速度を高速化することが望まれます。このような軽量で薄い電極ロールの場合、速度を上げるとロールが破損する可能性があります。さらに、巻き戻しおよび巻き戻しコンポーネントは真空チャンバー内にあるため、伝送プロセス中のほこりによる汚染を防ぐための対策を講じる必要があります。最後に、電極ロールの高速伝送中に急速加熱、温度均一性制御、および検出を実現することは困難です。さらに、機器の真空レベルと温度要件は、以前の機器タイプと同等または同等である必要があります。
5.5物流保管真空乾燥装置
物流保管真空乾燥装置は、既存の物流システムを利用して、乾燥プロセスの効率と柔軟性を大幅に向上させます。このタイプの機器は、従来の大型乾燥室から逸脱し、代わりに乾燥スペースとしてカバー付きのパレットを使用し、カバー付きのバッテリートレイを保持するための保管ラックを備えています。各保管位置には、バッテリーを加熱してトレイ内に真空を作り出すための真空ドッキングシステムと加熱ドッキングシステムが装備されています。物流保管真空乾燥装置はまだ開発段階にあり、実用化には至っていません。その構造の概略図を図に示します。
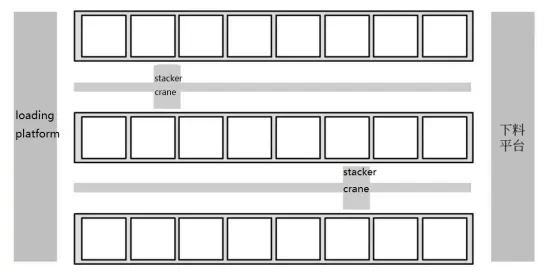
荷台では、ロボットがバッテリーをトレイに並べてカバーします。次に、スタッカークレーンは、バッテリーで組み立てられたトレイを保管ラックの対応する保管位置に置きます。ラック上の真空システムと加熱システムは、バッテリーを加熱および乾燥するためにトレイとドッキングされています。乾燥プロセスが完了すると、スタッカークレーンはバッテリーとトレイを荷降ろしプラットフォームに置き、そこでバッテリーを開梱して次のプロセスに進みます。
物流保管真空乾燥装置は、物流と保管の概念に依存しているため、高レベルの物流スケジューリングソフトウェアが必要です。さらに、バッテリーとトレイの取り扱いに使用されるスタッカークレーンは、機器の効率を確保するために特定の要件を満たす必要があります。トレイスペースを乾燥室として活用することで、チャンバーのサイズを小さくするとともに、柔軟性を大幅に向上させています。しかし、これはまた、各保管位置が加熱および真空ドッキング装置を備えている必要があることを意味し、これにより機器とメンテナンスのコストが増加します。この装置は、間欠真空乾燥装置と多くの類似点を共有しています。主な違いは、この装置のチャンバーが小さく、可動性が高いため、より柔軟でカスタマイズされた生産に適していることです。
06.リチウム電池真空乾燥装置の性能評価
6.1真空性能評価
真空乾燥装置の真空性能は、主に排気時間、到達真空度、チャンバーの真空シール能力などのパラメータに基づいて評価されます。真空性能の評価は、通常、無負荷条件下で行われます。テストセットアップには、真空ポンプ、真空バルブ、真空計、パイプ、真空計、タイマーが含まれます。
極限真空度とは、チャンバーが達成できる最低圧力を指します。到達真空度が低いほど、水分の蒸発には適していますが、機器に対する要求も高くなります。したがって、機器のコストと最終的な真空レベルとの間でバランスを取る必要があります。ほとんどのバッテリーの乾燥プロセスは、通常、数十から数百パスカル(Pa)の圧力で行われ、使用圧力が20〜1000 Paに低下することを考えると、約10 Paの究極の真空レベルで十分です。
連続ポンプ条件下では、機器のポンプ時間は、チャンバーが15分間開かれてから再び排気された後、究極の圧力値に達するのに必要な時間として定義されます。一般的には、排気時間は5分から10分程度とし、要件を満たせない場合は、要件を満たすために真空ポンプの交換を検討する必要があります。
真空チャンバーは、真空配管を介して真空ポンプの吸引入口に接続されており、真空システム全体が密閉されています。真空ポンプをONにし、真空レベルが到達圧力に達するとポンプをOFFにし、24時間圧力を維持します。時間と圧力曲線が記録され、圧力対時間曲線の線形セクションが特定されます。この線形セクションの傾きは、真空シール能力の値(つまり、1時間あたりの真空レベルの増加)を表します。真空シール能力は、一般的に5 Pa / h未満である必要があります。真空シール能力が要件を満たさない場合は、ヘリウムリークディテクターを使用してチャンバーをテストし、シール性能を向上させる必要があります。
6.2温度性能の評価
リチウム電池真空乾燥装置の温度性能は、主に加熱時間、温度変動、温度安定性、温度均一性などのパラメータに基づいて評価されます。温度性能の評価も、通常、無負荷条件下で行われます。温度性能のテストセットアップには、サーモレジスターや熱電対などの温度センサーと、温度レコーダーが含まれます。強制空気加熱の場合、温度測定点は通常、チャンバーの中心ですが、接触加熱の場合、加熱装置の中心です。
加熱時間とは、加熱装置が室温から最大電力で動作した場合に、機器がバッテリー乾燥のプロセス温度に達するのにかかる時間を指します。強制空気加熱の場合、加熱時間は90分を超えてはなりませんが、接触加熱の場合、10分を超えてはなりません。温度変動とは、乾燥過程で温度が安定してから規定の30分以内に測定地点の最高温度と最低温度の差が半分になったことと定義されます。バッテリー乾燥装置の温度変動は±1°Cを超えてはなりません。
温度安定性は、乾燥プロセス中に温度が安定してから24時間以内に異なる時間間隔で行われた複数の温度測定の平均温度と初期期間の平均温度の最大差によって決まります。バッテリー乾燥装置の温度安定性は2°Cを超えてはなりません。
温度均一性は、乾燥プロセス中に温度が安定した後、指定された時間間隔で、チャンバー内の任意の2点(強制空気加熱の場合)または加熱装置(接触加熱の場合)の平均温度の最大差の半分として定義されます。強制空気加熱の場合、温度測定ポイントにはチャンバーの中央と端に複数のポイントを含める必要がありますが、接触加熱の場合、ポイントには加熱装置の中心と端を含める必要があります。バッテリー乾燥装置の温度均一性は±3°Cを超えてはなりません。典型的な温度均一性試験曲線を図に示します。
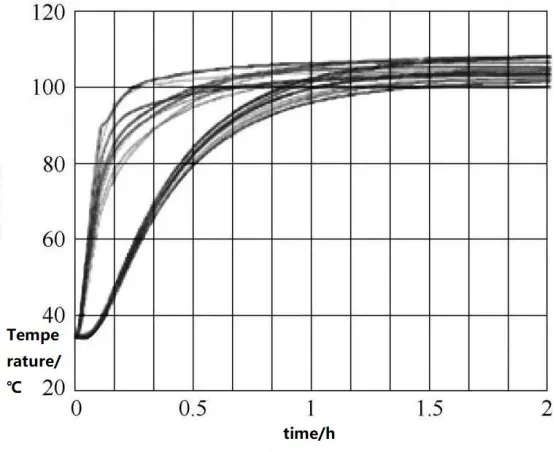
6.3乾燥後の水分評価
Niu Juntingらは、バッテリーポールピースの残留水分とバッテリー性能との関係について体系的な研究を行いました。正極シートの水分含有量が0.04%から0.05%のバッテリーは、良好なサイクル性能を発揮します。電流の充電と放電のサイクルを200サイクル繰り返した後でも、バッテリーの放電容量は初期容量の92.9%のままです。サイクルが進むと、正極シートの含水率が0.06%を超える電池の容量は急激に減少し、性能が劣化します。バッテリーポールピースの水分含有量が0.03%から0.06%の範囲のバッテリーは、放電比容量が高く、近くなります。放電率が増加すると、バッテリーポールピースの含水率は0.06%を超え、容量減衰率は増加します。水分が多すぎるとバッテリーの性能に大きな悪影響を与えるため、乾燥後のバッテリーの現在の水分含有量は一般に500mg / kg未満である必要があり、200~300mg / kgに減らすのが最善です。
乾燥後の電池の含水率は低く、一般的には1キログラムあたり数百ミリグラム程度であるため、簡単な方法では測定できません。カールフィッシャークーロン法は、一般に微量水分の試験に使用され、その原理は電気化学的法です。反応原理は、水がヨウ素と二酸化硫黄の酸化還元反応に関与するというものです。
上記の反応から、1molのヨウ素が1molの二酸化硫黄を酸化することがわかりますが、これには1molの水が必要です。したがって、ヨウ素を電気分解する力は、水を電気分解する力と同等です。1 molのヨウ素の電気分解には2×96493Cの電力が必要であり、1 mmolの水の電気分解には96493 mCの電力が必要です。測定された水分質量は、次の式に従って計算されます。
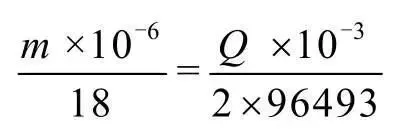
この式では、mは測定された水の質量μgです。Q電解質、mC;18水電解質。
測定された水分質量には、試験システム内の水分も含まれます。したがって、水分中の水分は、空のボトルの総水分質量損失(ブランク値)に基づいて測定する必要があり、水分値(ドリフト値)の影響を考慮する必要があります。ザ・水分中の水分含有量は次のように計算されます。
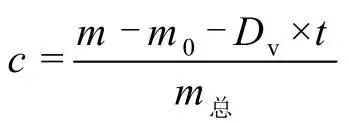
式では、cサンプルの水分含有量、μg / g;m0空のボトルの水分質量、μg;Dvドリフト値、μg / min;t抽出時間、分;m total – サンプルの総質量、g。
カールフィッシャークーロン水分計の構造図を図に示します。主にカールフィッシャー電解セルとサンプル加熱ユニットが含まれています。ポールピースサンプルを密封されたサンプルボトルに入れ、サンプルボトルを特定の温度で加熱します。電解セル内の水が蒸発し、乾燥ガスを使用して水蒸気を電解セルに送り込み、反応に参加し、電気分解プロセス中に発生する電気を測定して水分含有量を滴定します。
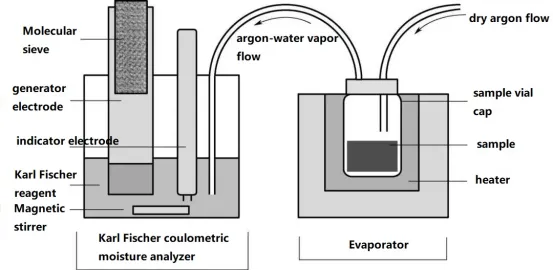
乾燥後にカールフィッシャー電量式水分計を使用してバッテリーサンプルの水分試験を行う際には、以下の点を考慮する必要があります。
ある。 サンプルバイアルは、サンプリング前に、通常は120〜160°Cで3〜6時間乾燥させる必要があります。取り外し後、すぐにキャップで密封する必要があります。サンプルバイアルのブランク水分含有量は10μg未満である必要があり、低いほど良いです。
b.サンプリングは、露点のある環境で行う必要があります。一般的に、露点は-40°C未満にすることをお勧めします。空のサンプルバイアルをブランクテストとして1〜2時間キャップを外しておきます。
c.電極プレートは、約0.5cmまたはサンプルバイアルの高さに沿って小片に切断できます。
d.分析用のサンプルサイズは、通常、0.5 g以上でなければなりません。
e.計量には、0.1 mgの分解能を持つ精密電子天びんを使用することをお勧めします。
f.正式なサンプルテストを実施する前に、電流ドリフトが20μg/min未満であり、大幅な上昇傾向や下降傾向がなく安定していることを確認してください。
g.サンプルが完成したら、サンプルの入ったバイアルをカールフィッシャーオーブンから取り出し、ドリフトボトルに戻し、装置を安定させてから次のサンプルに進みます。
h.カールフィッシャーオーブンの推奨温度は120〜180°Cです。温度が高すぎると、バッテリー内の一部の材料が揮発したり、副反応を起こしたりして、テスト結果が不正確になる可能性があります。試験温度が不明な場合は、グラジエント加熱法をカールフィッシャー水分計と併用して、リチウムイオン電池材料と電極プレートの水分含有量を分析できます。
07真空乾燥装置の開発ディレクション
7.1乾燥効率の継続的な改善
乾燥時間の短縮と乾燥効率の向上は、常に乾燥装置の目標でした。真空乾燥の効率を高めることで、製品コストを削減し、経済的利益を向上させることができます。現在、乾燥装置の自動化が進んでおり、これも乾燥効率の向上に貢献しています。将来的には、加熱効率を高めるための新しい加熱方法の開発、積み下ろし効率を向上させるための乾燥装置に合わせた物流システムの開発、エネルギー消費の少ない乾燥装置の作成、乾燥プロセスを最適化するためのバッテリー乾燥メカニズムの研究、プロセス制御を強化するためのソフトウェアと監視技術の活用、および機器の運用効率の向上が必要です。
7.2機器のモジュール式および標準化された設計
現在、市場に出回っているバッテリーの仕様が異なるため、バッテリー乾燥装置はカスタム設計されています。この標準化の欠如は、バッテリー乾燥装置の柔軟性を制限し、そのアップグレード性を妨げます。将来的には、バッテリーの仕様に対応する規格があり、乾燥装置の設計はこれらの規格に準拠する必要があります。これには、チャンバーのサイズ、真空ポンプの選択、加熱プレートの要件、真空計とバルブの設置位置などの側面が含まれます。また、電池のバッチ生産が求められるため、乾燥装置の大型化が進んでおり、現場での設置やデバッグには多大な人手、リソース、時間が必要になることが多くなっています。乾燥装置を設計する際には、モジュール化を考慮し、各モジュールに独立した機能を追加して、現場での設置とデバッグの時間を節約する必要があります。
7.3生産指導のための製造実行システム(MES)
バッテリー製造の自動化が進むにつれ、乾燥装置のソフトウェアシステムもアップグレードされています。現在、乾燥装置のソフトウェアは、基本的な要件であるエネルギー消費データの表示、製品情報の記録、およびプロセスデータを行うことができます。しかし、現在のMESは、乾燥データのトレーサビリティのためのデータ収集と保存に主眼を置いています。今後、MESはこれらの機能にとどまらず、ビッグデータなどの手法を活用して、バッテリーの乾燥プロセスの指導や改善を行い、機器のメンテナンスや乾燥効率の向上に貢献していく必要があります。
7.4 オンライン水分検出
前述のように、バッテリー乾燥後の水分試験では、バッテリーを破壊して水分含有量を評価し、その許容性を判断する必要があります。現在、効果的なリアルタイムの水分検出方法はありません。将来的には、破壊試験や乾燥後の水分分析を必要とせずに、乾燥プロセス中の水分含有量をリアルタイムで監視できる新しいバッテリー試験方法を開発するための研究を実施する必要があります。乾燥プロセス中に含水率が非準拠であることが判明した場合は、含水率が目的の基準を満たすまで、乾燥プロセスを即座に調整できます。新しい水分検出方法を開発するには、バッテリーの水分蒸発メカニズムと関連する影響要因についての詳細な研究が必要です。したがって、バッテリーの乾燥プロセスを研究することは、乾燥装置の進歩にとって非常に重要です。