DeLIDIANBIJI
01 Introducción al proceso de fabricación de pulpa
1.1 La importancia del proceso de fabricación de pulpa
El límite de rendimiento de las baterías de iones de litio está determinado por el sistema químico utilizado, incluidos los materiales activos para el cátodo y el ánodo, así como el electrolito. Sin embargo, el rendimiento real depende fundamentalmente de la microestructura del electrodo, que está determinada principalmente por la microestructura de la lechada y el proceso de recubrimiento. En este contexto, la microestructura del purín desempeña un papel dominante. Por lo tanto, existe una afirmación ampliamente reconocida de que la influencia del proceso de fabricación en el rendimiento de las baterías de iones de litio es de al menos el 70% en los procesos de etapa inicial, y dentro de estos procesos, el impacto del proceso de fabricación de pulpa por sí solo representa al menos el 70%. En otras palabras, el proceso de fabricación de pulpa contribuye a aproximadamente la mitad de la influencia general.
1.2 Composición de la suspensión y estado ideal de dispersión de cada componente
Los materiales de los electrodos de las baterías de iones de litio constan de tres componentes principales: materiales activos, aditivos conductores y aglutinantes. Entre ellos, el material activo constituye la gran mayoría del peso total, que generalmente oscila entre el 90% y el 98%, mientras que las proporciones de aditivos conductores y aglutinantes son relativamente pequeñas, generalmente entre el 1% y el 5%. Estos componentes principales difieren significativamente en sus propiedades físicas y tamaños. Las partículas del material activo suelen oscilar entre 1 y 20 μm, mientras que la mayoría de los aditivos conductores son materiales de nanocarbono. Por ejemplo, el negro de humo de uso común tiene diámetros de partícula primarios en el rango de decenas de nanómetros, y los nanotubos de carbono tienen diámetros generalmente inferiores a 30 nm. El aglutinante es un material polimérico que puede disolverse en disolventes o formar microemulsiones en disolventes.
El electrodo de una batería de iones de litio debe lograr un buen transporte de electrones e iones, lo que requiere que el estado de distribución del material activo, los aditivos conductores y los aglutinantes cumplan con ciertos requisitos. El estado de distribución ideal de cada material en el electrodo se ilustra en la figura, donde el material activo está completamente disperso, los aditivos conductores están completamente dispersos y en suficiente contacto con el material activo, formando una buena red conductora electrónica, y el aglutinante se distribuye uniformemente en el electrodo, uniendo el material activo y los aditivos conductores para formar un electrodo cohesivo.
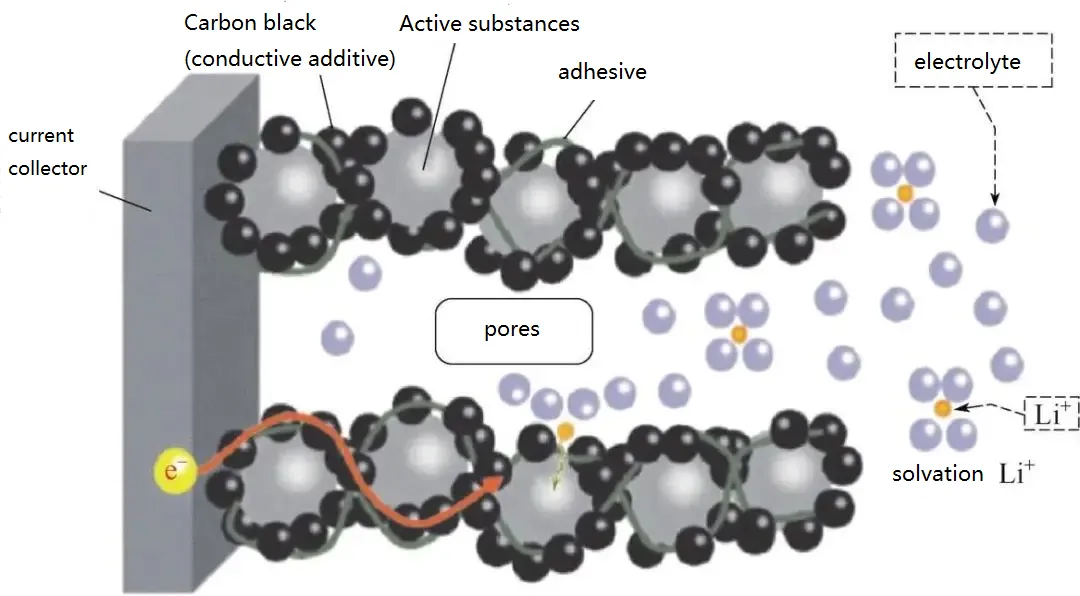
Para lograr la microestructura deseada del electrodo, es necesario obtener una lechada con la microestructura correspondiente durante el proceso de fabricación de pulpa. Esto significa que el material activo, los aditivos conductores y los aglutinantes en la suspensión deben estar completamente dispersos, y debe haber una buena unión entre los aditivos conductores y el material activo, así como entre el aglutinante y los aditivos conductores/material activo. Además, el estado de dispersión de cada componente en el lodo debe ser estable. La suspensión es esencialmente una suspensión donde las partículas sólidas se dispersan en un líquido. Varias fuerzas actúan entre las partículas en la suspensión, y las fuerzas de atracción entre las partículas formadas por las interacciones de van der Waals son la causa principal de la agregación de partículas. Para evitar esta agregación, es necesario tener un cierto nivel de repulsión entre las partículas. Los tipos comunes de repulsión incluyen la repulsión electrostática y el obstáculo estérico causado por las cadenas poliméricas. La teoría DLVO (teoría de Deryaguin-Landau-Verwey-Overbeek) es una teoría clásica utilizada para describir la estabilidad de las dispersiones coloidales. Considera los efectos combinados de la repulsión electrostática y la atracción de van der Waals. Como se muestra en la figura, la energía total formada por la repulsión electrostática y las fuerzas de van der Waals alcanza un valor máximo (Gmax) a una cierta distancia. Este valor máximo forma una barrera de energía, evitando que las partículas se acerquen más y formen gprimaria.
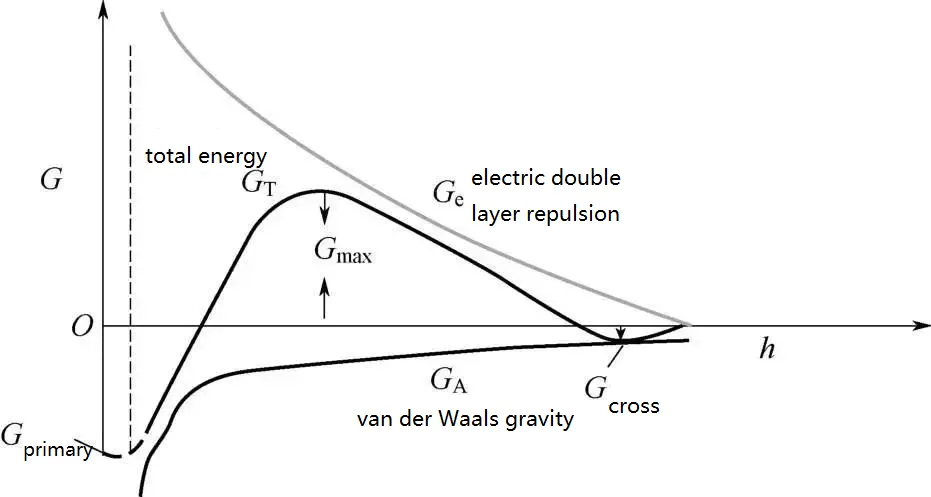
En la suspensión de las baterías de iones de litio, el obstáculo estérico formado por la adsorción de cadenas de polímeros aglutinantes en las superficies de las partículas juega un papel crucial en la estabilidad de la suspensión. Cuando las moléculas aglutinantes se adsorben en las superficies de las partículas para formar una capa de adsorción, las capas de adsorción de dos superficies de partículas se acercan entre sí. Debido al obstáculo estérico, se genera una energía de interacción. La fuerza de obstáculo estérico, junto con la repulsión electrostática y la atracción de van der Waals, constituye la energía total de interacción entre las partículas, como se muestra en la figura.
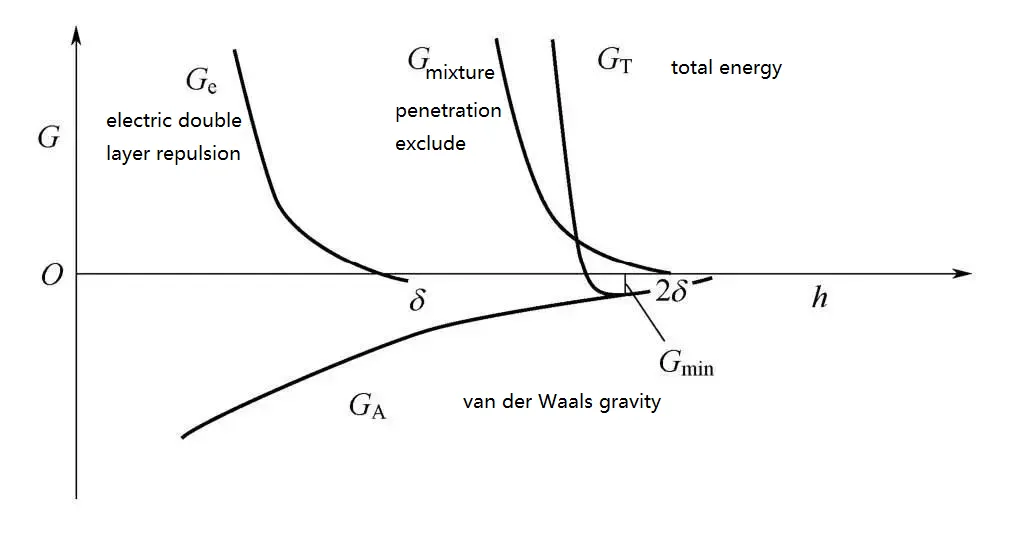
Por lo tanto, para evitar la agregación de partículas en la suspensión, es necesario que las cadenas poliméricas del aglutinante se adsorban en las superficies de las partículas, creando un cierto nivel de obstáculo estérico. Esto permite que el estado de dispersión de la lechada permanezca estable durante un período prolongado de tiempo.
1.3 El proceso microscópico de fabricación de pulpa
El proceso de fabricación de pulpa en la fabricación de baterías de iones de litio implica la dispersión uniforme de materiales activos y aditivos conductores en un solvente, formando una suspensión estable bajo la influencia de cadenas de polímeros aglutinantes. Desde una perspectiva microscópica, este proceso suele incluir tres etapas principales: humectación, dispersión y estabilización, como se ilustra en la figura.
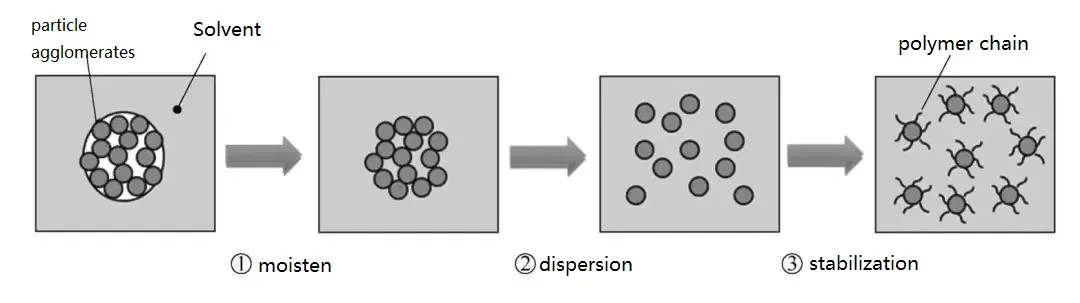
La etapa de humectación es el proceso de lograr un contacto suficiente entre el solvente y las superficies de las partículas. Consiste en desplazar el aire de los aglomerados de partículas y sustituirlo por el disolvente. La velocidad y la eficacia de esta etapa dependen de la afinidad entre las superficies de las partículas y el disolvente, así como del equipo y el proceso de fabricación de pulpa.
La etapa de dispersión es el proceso de ruptura de los aglomerados de partículas. La velocidad y la eficacia de esta etapa están influenciadas por las características del material, como el tamaño de partícula, el área de superficie específica y las fuerzas entre partículas. Además, la intensidad de la dispersión y el proceso de dispersión están estrechamente relacionados con la eficiencia de esta etapa.
La etapa de estabilización implica la adsorción de cadenas poliméricas en las superficies de las partículas para evitar la reagregación entre partículas. La velocidad y la eficacia de esta etapa dependen de las características del material, la formulación, así como del equipo y el proceso de fabricación de pulpa.
Hay que tener en cuenta que no todos los materiales pasan por las tres etapas simultáneamente a lo largo de todo el proceso de fabricación de la pulpa. Diferentes partes de la suspensión pueden estar en diferentes etapas. Por ejemplo, algunas partes de la lechada pueden haber entrado en la etapa de estabilización, mientras que otras aún están en la etapa de humectación. Esta situación es bastante común y contribuye a la complejidad y dificultad en el control del proceso de fabricación de pulpa.
1.4 Equipos y procesos de dispersión de lodos
El equipo utilizado para la dispersión de lodos se puede clasificar en dos tipos. El primer tipo involucra dispositivos que utilizan fuerzas de cizallamiento generadas por el movimiento del fluido para dispersar aglomerados de partículas. Esto incluye varios tipos de mezcladoras y amasadoras equipadas con diferentes tipos de cuchillas de agitación. También incluye fresadoras de tres ejes y molinos de discos. El segundo tipo involucra equipos que utilizan perlas de molienda para impactar los aglomerados de partículas y lograr la dispersión, como los molinos agitados. Además, existen algunos dispositivos de dispersión especializados, como los dispersores ultrasónicos, que utilizan la cavitación y los microchorros instantáneos generados por ultrasonidos para dispersar los aglomerados de partículas. Estos diferentes tipos de equipos de dispersión se ilustran en la figura.
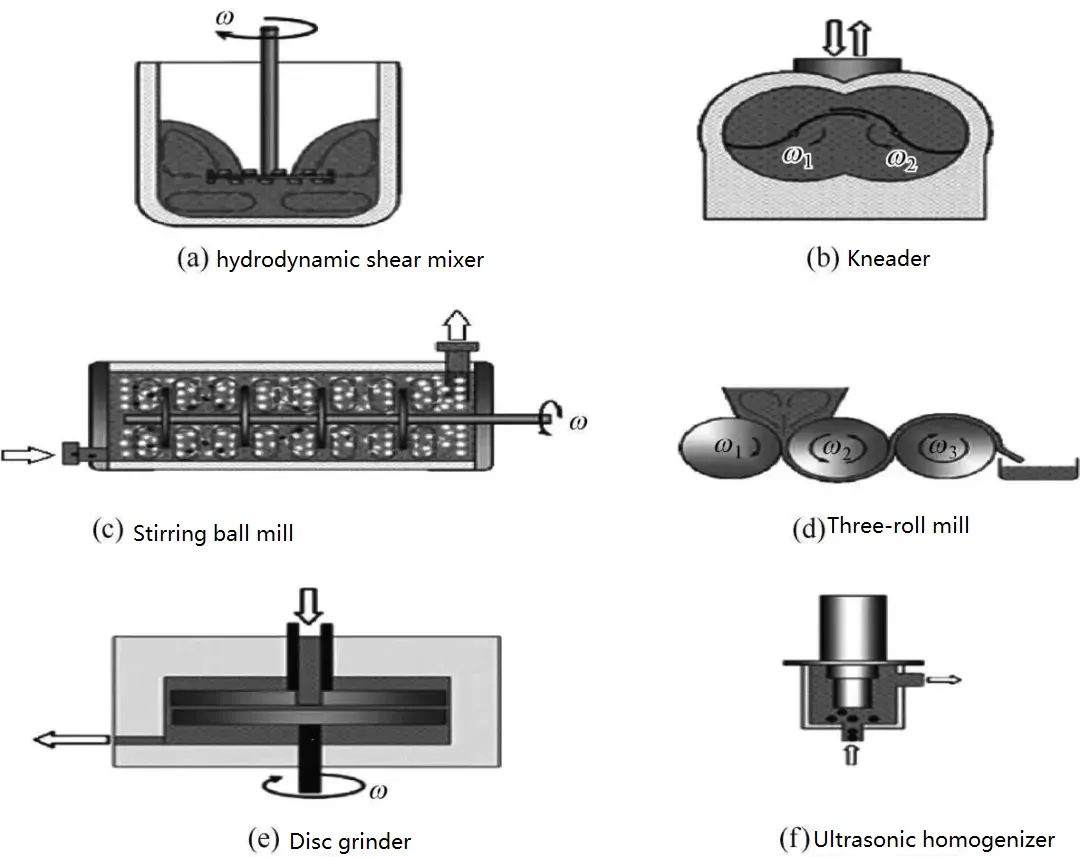
No todos los equipos de dispersión mencionados anteriormente son adecuados para la producción de lodos en baterías de iones de litio. Por ejemplo, el uso de cordones de molienda en molinos agitados genera fuerzas de impacto significativas, que pueden dañar el recubrimiento superficial de algunos materiales activos e incluso provocar su fragmentación. Como resultado, los molinos agitados rara vez se utilizan en la producción de lodos para baterías de iones de litio. Los dispositivos de dispersión ultrasónica tampoco son adecuados para lodos de alto contenido de sólidos y alta viscosidad. Sin embargo, los lodos para baterías de iones de litio suelen tener un alto contenido de sólidos (60% a 80% para los lodos de electrodos positivos, 40% a 60% para los lodos de electrodos negativos) y una alta viscosidad (20 a 200 Pa·s), lo que los hace inadecuados para la dispersión mediante dispersores ultrasónicos.
En la práctica, el equipo utilizado para la producción de lodos en baterías de iones de litio se basa en fuerzas de cizallamiento generadas por el movimiento del fluido para la dispersión. Esto incluye mezcladores, amasadoras, y el equipo más típico, el mezclador Twin planet, que se detallará en la Sección 2. El proceso de producción de lodos también tiene un impacto significativo en las propiedades de los lodos de baterías de iones de litio. Por ejemplo, las propiedades de la suspensión pueden variar mucho según el orden de adición de diferentes materiales. Los informes de la literatura han demostrado que el uso de dos secuencias de alimentación diferentes para preparar lodos para materiales de electrodos positivos ternarios de níquel-cobalto-manganeso da como resultado diferencias significativas en las características de la suspensión y el rendimiento del electrodo. La segunda secuencia de alimentación produce una suspensión con mayor contenido de sólidos, con una resistencia al pelado y una conductividad del electrodo mucho mayores. Esto se debe a que la premezcla de los aditivos conductores con el material principal permite que los aditivos conductores recubran la superficie del material principal, reduciendo los aditivos conductores libres. Esto, a su vez, reduce la viscosidad de la lechada y minimiza la agregación de los aditivos conductores durante el secado, lo que facilita la formación de una buena red conductora.
Actualmente, existen dos tipos principales de procesos de producción de lodos comúnmente utilizados en la industria de las baterías de litio, conocidos como proceso húmedo y proceso seco. La principal diferencia entre ellos radica en el contenido sólido inicial de la lechada. El proceso húmedo implica un menor contenido de sólidos inicial de la lechada, mientras que el proceso seco implica un mayor contenido de sólidos iniciales de la lechada.
El flujo del proceso para la producción de lodos húmedos implica primero mezclar y dispersar los aditivos conductores y aglutinantes. Después de lograr una dispersión completa, los materiales activos se agregan y se mezclan y dispersan aún más. Finalmente, se agrega una cantidad adecuada de solvente para ajustar la viscosidad con fines de recubrimiento. El aglutinante puede existir en forma líquida o en polvo. La preparación del aglutinante como solución facilita su eficacia, aunque algunas empresas también utilizan directamente aglutinantes en polvo. Debe tenerse en cuenta que cuando el aglutinante tiene un alto peso molecular y un tamaño de partícula grande, puede tardar más tiempo en disolverse. En tales casos, es necesario preparar el aglutinante como solución.
El flujo del proceso para la producción de lodos secos implica primero la premezcla de materiales en polvo, como materiales activos y aditivos conductores. A continuación, se añade una parte de la solución aglutinante o del disolvente, y la mezcla se agita o amasa en condiciones de alto contenido de sólidos y alta viscosidad. Posteriormente, la solución aglutinante o disolvente restante se añade gradualmente para su dilución y dispersión. Finalmente, se agrega una cantidad adecuada de solvente para ajustar la viscosidad con fines de recubrimiento.
La característica del proceso de producción de lodos secos es que en la etapa inicial, la mezcla y la dispersión (amasado) se realizan en condiciones de alto contenido de sólidos y alta viscosidad. En esta etapa, el material se encuentra en un estado de suspensión espeso y pastoso, y la fuerza mecánica aplicada por la paleta de agitación es fuerte. Además, existe una importante fricción interna entre las partículas, lo que favorece la humectación y la dispersión, lo que resulta en un alto grado de dispersión. Por lo tanto, el proceso de producción de lodos secos puede acortar el tiempo de producción de lodos, y el lodo obtenido tiene una viscosidad más baja, lo que permite un mayor contenido de sólidos en comparación con el proceso de producción de lodos húmedos.
Sin embargo, es un desafío controlar el estado óptimo del material en el proceso de producción de lodos secos. Cuando hay cambios en el tamaño de partícula, el área superficial específica y otras propiedades físicas de las materias primas, es necesario ajustar los parámetros del proceso, como el contenido de sólidos intermedios, para lograr el estado de dispersión óptimo. Esto puede afectar a la eficiencia de la producción y a la coherencia de un lote a otro.
02 Estado actual de los equipos de fabricación de pasta
2.1 Equipo de fabricación de pasta tradicional – Mezclador Twin Planet
Actualmente, la producción nacional e internacional de baterías de iones de litio emplea comúnmente procesos de agitación tradicionales para la producción de lodos, a menudo utilizando mezcladores de planetas gemelos. El principio de funcionamiento de un tWin Planet Mixer implica el movimiento combinado de 2 a 3 cuchillas de agitación de baja velocidad, que giran y giran simultáneamente. Este movimiento permite que las cuchillas cubran todo el espacio dentro del tambor de mezcla, como se muestra en el diagrama.
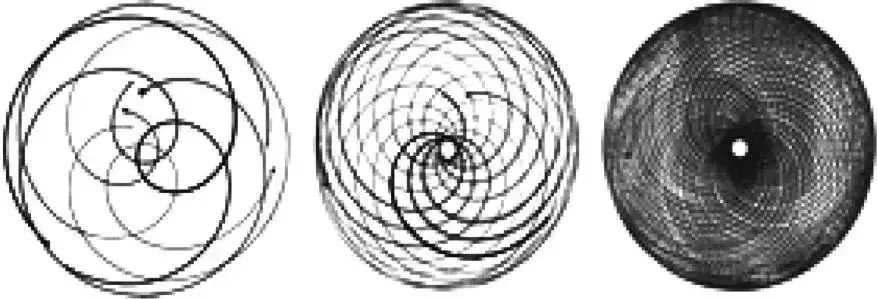
Con los avances tecnológicos, ha habido más mejoras en los equipos de producción de lodos. Además de las cuchillas de agitación de baja velocidad existentes, se han añadido cuchillas de dispersión de alta velocidad. Estas cuchillas dispersas de alta velocidad utilizan la rotación rápida del disco dentado para generar fuertes fuerzas de cizallamiento. Esto permite una mayor dispersión de la suspensión premezclada, como se muestra en el diagrama.
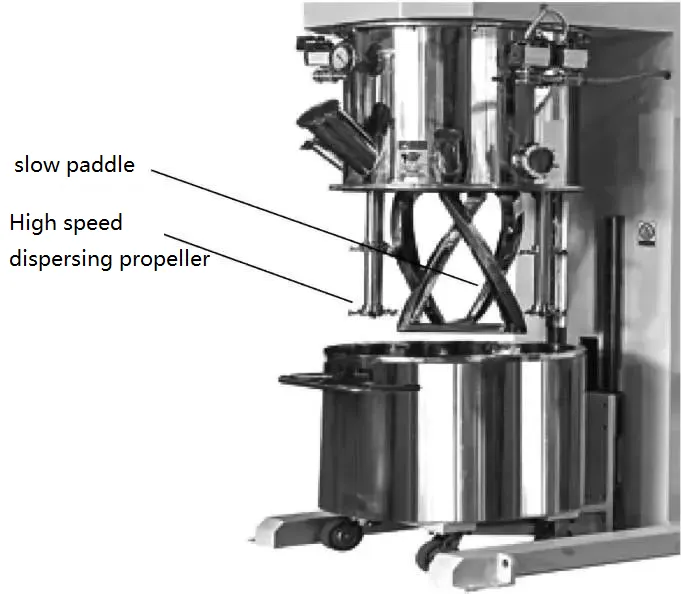
El mezclador de doble planeta tiene la ventaja destacada de ajustar fácilmente los parámetros del proceso, como la secuencia de alimentación, la velocidad y el tiempo, para adaptarse a las diferentes características del material. También permite un fácil retrabajo cuando las propiedades de la lechada no cumplen con los requisitos, exhibiendo una gran adaptabilidad y flexibilidad. Además, durante los cambios de producto, especialmente para mezcladores a pequeña escala, la limpieza es relativamente sencilla.
En el mezclador de planetas gemelos, la interacción del material con las cuchillas de agitación sigue una distribución de probabilidad, lo que requiere un largo tiempo de mezcla para garantizar una mezcla y dispersión completas de todos los materiales. En las primeras etapas, la preparación de la suspensión podía llevar más de 10 horas. Con las continuas mejoras del proceso, especialmente la introducción de técnicas de producción de lodos secos, el tiempo de producción se ha acortado a 3-4 horas. Sin embargo, debido a las limitaciones inherentes, es un desafío reducir aún más el tiempo de producción de lodo con el mezclador de dos planetas. La eficiencia de la producción de lodos es relativamente baja y el consumo de energía por unidad es mayor.
A medida que aumenta el volumen del tambor de mezcla, se hace más difícil lograr una dispersión uniforme. Actualmente, el volumen máximo de los mezcladores de dos planetas utilizados para la producción de lodos de baterías de iones de litio no supera los 2000 litros, con un tamaño máximo de lote de aproximadamente 1200 litros de lodo.
Los principales fabricantes de mezcladores de planetas gemelos incluyen Ross de los Estados Unidos, Asada Iron Works e Inoue Mfg. de Japón, y Hongyun Mixing Equipment de China. La tecnología del mezclador de planetas gemelos es muy madura.
2.2 Se introduce el dispersor de alta velocidad de película delgada, un nuevo tipo de equipo de dispersión de lodos, para complementar la limitada capacidad de dispersión del mezclador de doble planeta. Cuando se trata de materiales difíciles de dispersar, como el fosfato de hierro y litio del tamaño de una partícula pequeña y el negro de humo conductor de área superficial alta específica, el mezclador planetario dual puede tener dificultades para lograr una dispersión efectiva. Por lo tanto, se requiere un equipo de dispersión más eficiente, y el dispersor de alta velocidad de película delgada, desarrollado por PRIMIX en Japón, es una excelente opción para la dispersión de lodos.
El principio de funcionamiento del dispersor de alta velocidad de película delgada es el siguiente: la lechada ingresa al recipiente de dispersión desde el fondo y gira a alta velocidad junto con la rueda de dispersión. Bajo la fuerza centrífuga, la lechada se lanza contra la pared interna del recipiente de dispersión, formando un anillo de suspensión. Además, la lechada, influenciada por la fuerza centrífuga, se separa rápidamente de la pared exterior de la rueda de dispersión e impacta en las paredes del recipiente de dispersión. Simultáneamente, se forma un vacío momentáneo en la superficie de la rueda, lo que facilita que la lechada pase a través de los orificios de dispersión de la rueda, lo que da como resultado la trayectoria que se muestra en el diagrama.
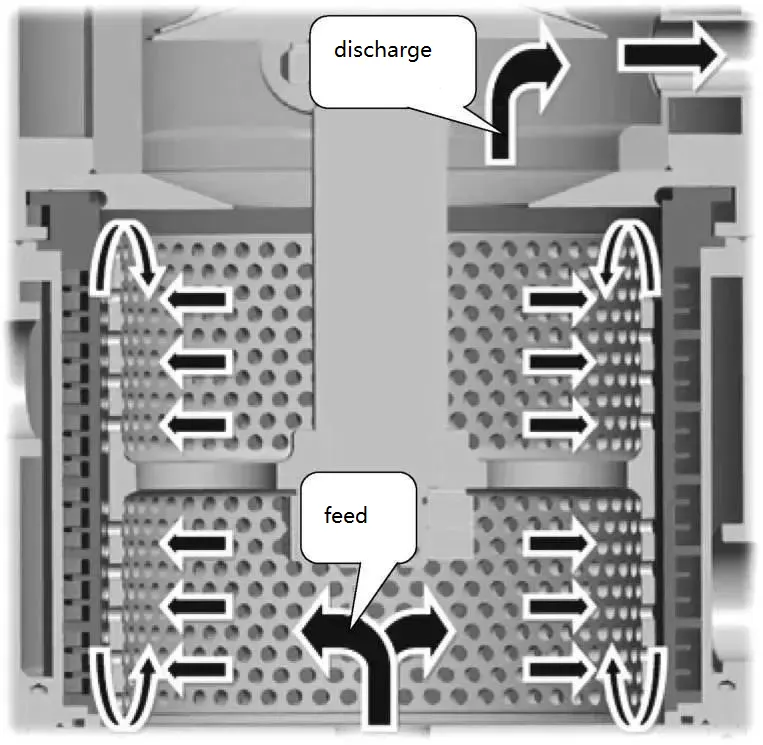
Además, debido al estrecho espacio de solo 2 mm entre la rueda de dispersión y la pared del recipiente, cuando la rueda de dispersión gira a alta velocidad (con una velocidad lineal de hasta 30-50 m/s), el lodo experimenta fuerzas de cizallamiento uniformes e intensas dentro de este pequeño espacio. El purín tiene un tiempo de residencia de aproximadamente 30 segundos dentro del dispersor. Durante este tiempo, la lechada se somete a una circulación continua y a una dispersión de cizallamiento dentro del dispersor, lo que da como resultado un efecto de dispersión ideal. El diagrama ilustra una comparación de la intensidad y frecuencia de las fuerzas de cizallamiento que actúan sobre la lechada tanto en el mezclador de planetas gemelos como en el dispersor de alta velocidad de película delgada, obtenida a través de cálculos de simulación. A partir del diagrama, es evidente que en el mezclador de planetas gemelos, la lechada solo experimenta fuertes fuerzas de cizallamiento en la región final de las cuchillas de agitación, lo que resulta en una baja frecuencia de alta acción de cizallamiento en la lechada. Por el contrario, en el dispersor de alta velocidad de película delgada, la lechada experimenta fuertes fuerzas de cizallamiento en toda la región, lo que conduce a una alta frecuencia de acción de alto cizallamiento en la lechada. Esto mejora significativamente el efecto de dispersión y la eficiencia de la lechada.
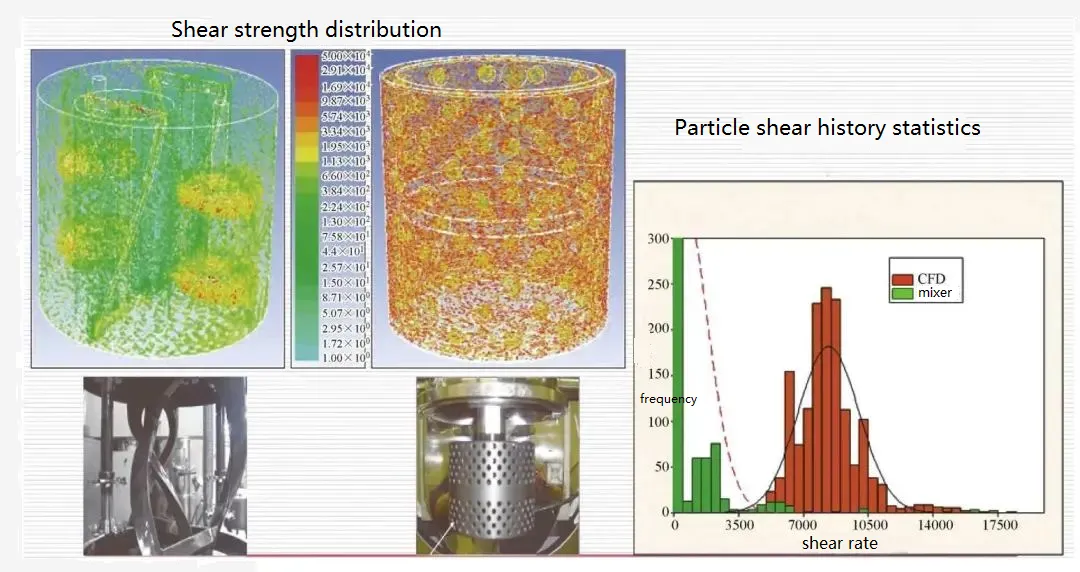
El dispersor de película delgada y alta velocidad, iniciado por PRIMIX en Japón, ha sido adoptado por algunos fabricantes de baterías de iones de litio en Corea del Sur y China. SHANGSHUI fue el primero en introducirlo en el país, y el rendimiento de sus productos ha alcanzado el mismo nivel que los productos de PRIMIX. Cabe señalar que este dispersor de alta velocidad de película delgada no se puede utilizar de forma independiente para la producción de lodos. Requiere una mezcla previa de materiales en polvo y líquidos para formar una lechada utilizando equipos como un mezclador de planetas gemelos antes de una mayor dispersión utilizando el dispersor de alta velocidad de película delgada. Por lo tanto, la aplicación de este equipo tiene ciertas limitaciones y generalmente se usa junto con mezcladores de planetas gemelos para la producción de materiales difíciles de dispersar.
2.3 Nuevo equipo de fabricación de pulpa: máquina de pulpa de doble tornillo
Para abordar el problema de la baja eficiencia en los mezcladores de planetas gemelos, algunos fabricantes han introducido nuevos procesos y equipos de producción de lodos. Uno de esos desarrollos que ha atraído una atención significativa es el sistema de pulpa continua, que cuenta con una extrusora de doble tornillo como equipo principal. Brueckner, de Alemania, es una de las empresas que ha introducido este sistema, que ha sido ampliamente adoptado.
Originalmente utilizada en industrias como el procesamiento de plásticos, la extrusora de doble tornillo es adecuada para mezclar y dispersar materiales de alta viscosidad. Brueckner ha introducido este equipo en el campo de la producción de lodos de baterías de iones de litio. El sistema permite la preparación continua de la lechada mediante la introducción de polvo y líquido en diferentes posiciones a lo largo de los tornillos.
El proceso específico es el siguiente: el polvo de materiales activos y agentes conductores se introduce primero en el extremo delantero de los tornillos. A medida que los tornillos transportan los materiales hacia la parte trasera, se añaden disolventes o adhesivos secuencialmente en diferentes secciones de los tornillos. Se utilizan varios elementos de tornillo para lograr procesos como amasado, dilución, dispersión y desaireación. Al final de los tornillos, la salida es la lechada terminada.
En la máquina de pulpa de doble tornillo, la dispersión de la lechada se produce principalmente durante la etapa de amasado. Durante esta etapa, la lechada tiene una alta viscosidad y se generan intensas fuerzas de cizallamiento por la acción de los elementos del tornillo. Esto permite una dispersión eficiente de la lechada.。
El proceso de fabricación de pulpa en la máquina de doble tornillo implica la mezcla continua de materias primas en polvo y líquidas, lo que mejora significativamente la eficiencia de la mezcla macroscópica. Además, los elementos de amasado de la máquina proporcionan una dispersión de cizallamiento de alta intensidad para lodos de alto contenido de sólidos y alta viscosidad, lo que mejora en gran medida la eficiencia de dispersión. Como resultado, la máquina de pulpa de doble tornillo ofrece ventajas notables como alta eficiencia y bajo consumo de energía.
Sin embargo, el uso de máquinas de pulpa de doble tornillo para la producción de lodos de baterías de iones de litio también tiene algunas deficiencias notables. En primer lugar, debido a la larga longitud de los tornillos en la máquina de pulpa de doble tornillo y la necesidad de reducir el desgaste y prolongar el tiempo de residencia, la velocidad de rotación no puede ser demasiado alta. Normalmente, la velocidad lineal en el extremo de los elementos del tornillo está entre 2 y 3 m/s. La generación de fuertes fuerzas de cizallamiento a una velocidad lineal tan baja requiere minimizar las holguras mínimas entre los elementos del tornillo y entre los elementos del tornillo y la pared del cañón. Actualmente, la holgura mínima en las máquinas de pulpa de doble tornillo es de alrededor de 0,2 a 0,3 mm. Un espacio libre tan pequeño requiere una alta precisión en el procesamiento y la instalación, y puede provocar el desgaste de los elementos de tornillo. Las partículas metálicas desgastadas resultantes pueden suponer graves riesgos para la seguridad de los productos de baterías de iones de litio.
En segundo lugar, el modo de fabricación continua de pulpa de la máquina de doble tornillo requiere una dosificación dinámica precisa de las materias primas en polvo y líquidas para garantizar velocidades de alimentación precisas y estables para todos los materiales. Cualquier fluctuación en la velocidad de alimentación de un material en particular puede causar fluctuaciones en la proporción de ingredientes de la suspensión. Si estas fluctuaciones superan el rango aceptable, puede resultar en el rechazo de una parte de la lechada o incluso causar pérdidas imprevistas en procesos posteriores. Por lo tanto, este sistema de fabricación continua de pulpa debe estar equipado con un sistema de dosificación y alimentación de materia prima de alta precisión, lo que aumenta significativamente el costo total del sistema. En la producción práctica, para evitar que las fluctuaciones en las velocidades de alimentación causen anomalías, a menudo se instala un gran tanque intermedio con agitación después de la extrusora de doble tornillo. La lechada producida por la extrusora se homogeneiza parcialmente en el tanque intermedio para eliminar el impacto de las fluctuaciones instantáneas en las velocidades de alimentación. Sin embargo, este enfoque hace que el sistema se parezca un poco a un sistema de pulpa por lotes.
Además, la máquina de pulpa de doble tornillo es sensible a las fluctuaciones en la calidad de la materia prima. Si los parámetros de la lechada no cumplen debido a las fluctuaciones en la calidad de la materia prima, no es posible volver a trabajar. Además, al cambiar entre diferentes variantes de productos, puede ser necesario cambiar algunos elementos de tornillo para adaptarse a nuevos materiales y formulaciones, lo que resulta en una mala adaptabilidad.
Actualmente, el principal proveedor de máquinas de pulpa de doble tornillo es Brueckner de Alemania. Algunos fabricantes nacionales en China también ofrecen equipos similares. Este sistema de fabricación continua de pulpa ha sido adoptado por las fábricas nacionales de baterías de energía en China.
2.4 Nuevo equipo de fabricación de pulpa: máquina de circulación de pasta
Dadas las fortalezas y debilidades de los sistemas de pulpa continua, algunos fabricantes han introducido sistemas de pulpa semicontinuos. Shangshui Intelligent, por ejemplo, ha desarrollado una máquina de fabricación de pasta de alta eficiencia que combina las ventajas de los sistemas de fabricación de pasta continua y por lotes. Este sistema utiliza la medición de lotes, la alimentación continua para la fabricación de pulpa y la dispersión circulante para lograr una preparación eficiente de la lechada y una dispersión uniforme de todo el lote. Ha sido adoptado por fábricas de baterías de energía doméstica de alta gama. La estructura básica de la máquina de pulpa circulante de Shangshui Intelligent se muestra en la Figura 14.
El principio básico de funcionamiento consiste en mezclar primero el polvo y alimentarlo continuamente en la máquina de fabricación de pasta a través del módulo de alimentación de polvo a un caudal predeterminado. Bajo la presión negativa formada durante la descarga de la máquina de fabricación de pulpa, el polvo libera algo de gas y se dispersa en un estado similar al humo por el dispositivo de dispersión de polvo giratorio de alta velocidad. A continuación, se introduce en el líquido que fluye rápidamente, se sumerge y se dispersa en el líquido. A medida que la lechada fluye hacia abajo en el módulo de dispersión debajo del impulsor, experimenta intensas fuerzas de cizallamiento del impulsor giratorio de alta velocidad y el estator fijo en la cámara, formando una estructura rotor-estator. Esto logra un buen estado de dispersión, y la lechada es acelerada por el impulsor y descargada a través de la salida tangencial.
03 Tendencias futuras de desarrollo de equipos de fabricación de pasta
El mezclador tradicional sigue siendo el equipo de fabricación de pasta convencional hasta ahora, y su ventaja radica en su gran adaptabilidad, particularmente adecuada para la producción de baterías de iones de litio con cambios frecuentes de variedad y tamaños de lote pequeños. Sin embargo, en el campo de la fabricación de baterías de potencia con cambios de variedad menos frecuentes y tamaños de lote más grandes, las desventajas de la baja capacidad de una sola máquina y el alto consumo de energía de los mezcladores hacen que sean reemplazados gradualmente por nuevos equipos de pulpa con mayor eficiencia de dispersión. Por ejemplo, la máquina de pulpa circulante de SHANGSHUI ha sido gradualmente aceptada y adoptada por los fabricantes de baterías de alta gama en China.
Además, la investigación de nuevos dispersantes y la reducción de la dependencia de los equipos de dispersión de alta intensidad es también una de las futuras direcciones de desarrollo en la industria.